New Technique for Online Washing of Large Mechanical-Drive Condensing Steam Turbines
Total Page:16
File Type:pdf, Size:1020Kb
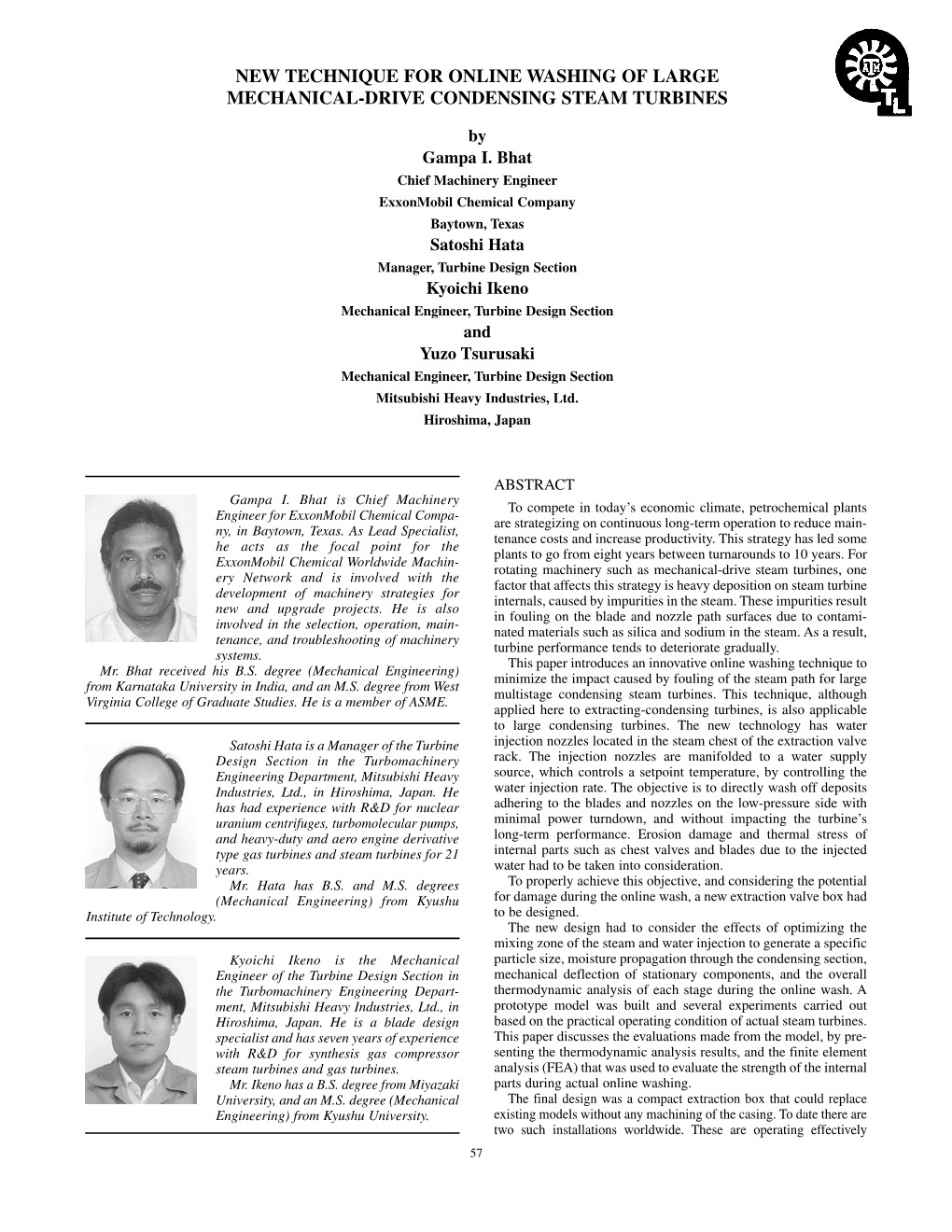
Load more
Recommended publications
-
Steam System Services
Steam System Services Steam System Services Working in partnership to deliver a cleaner more efficient future Steam System Services Steam System Services 100 years of steam expertise across industry We have been dealing with industrial markets and their total steam requirements for over 100 years, gaining considerable expert knowledge of steam engineering and steam systems. It has been evident in recent years that our customers’ requirements have changed due to the significant increase in fuel costs and environmental issues. In addition, many of our customers have been forced to make cost-cutting exercises resulting in the reduction of maintenance teams and loss of steam engineering experience. This is where our Steam System Services have evolved to support you, by helping you to maintain performance and reduce costs, by working alongside your maintenance teams to improve and sustain your plants efficiency. Our services are tailored and integrated to suit your resources, plant requirements and budget. Qualified and experienced engineers will work with you to implement the improvements to your system and then help you to maintain the resulting performance gains which usually give very rapid returns on your investment. Steam System Services Audits Installation and Service Problem & potential solution commissioning Maintaining plant performance Solution implementation spiraxsarco.com Benefits: Steam System Services can help to maintain your steam system at its optimum level, ensuring that steam reaches the point of use at the correct quantity, quality and pressure. Increased Turnover Increased Profit Health and Safety Reduced downtime through Reducing energy wastage Helping you comply with preventative maintenance. and emissions. regulations / legislation. Reduced product rejects by Reducing stock holding through ensuring steam reaches point rationalisation of steam equipment of use at correct conditions. -
How to Get Steam Keys for Humble Bundle Games?
[ How to get steam keys for humble bundle games ] User rating: Jun 11, · Get a Steam Key for Snake Pass on Humble Bundle, redeem it on Steam and keep it forever! You can claim the game from June 11th at CET to June 14th at CET. Follow us on Twitter, Facebook or Steam to get a reminder when the next freebie launches! ABOUT THE GAME. ★How to Redeem an Epic Games Key ★ Redeeming Activision / Blizzard Keys through Direct Entitlement ★ How to redeem a PlayStation Bundle key. ★ Uplay Redemption Instructions ★ Free Game Redemption Instructions ★ Locating your Steam content ★ How to claim a Humble Bundle purchase or gift ★ How To Redeem Origin Keys ★ How To Redeem GOG Keys ★ How To Redeem Steam Keys. Jul 06, · All of our products are officially-licensed from some of the world's biggest publishers, including Humble Bundle, Electronic Arts, Bethesda and many more. We began our story in the 90s, making affordable software and games available to all on PC CD-ROM. In we launched Bundle Stars to satisfy the growing global demand for digital games. Jul 16, · If you are looking specifically for keys, you won't get them. HB sends an email with a link. In that link are the games. For Steam, you need to long in through the HB sevice so you can add the keys directly to your account. (Be sure to include any other email addresses you might have, as well as your Steam ID) 3. Getting your free game key. Head to our main page or Humble Store, click on the free promotion and get the game key over to you clicking the GET THE GAME button from the page. -
Applications: A
Applications: A This chapter contains the following sections: • ABC, on page 8 • Abonti, on page 9 • About.com, on page 10 • ABS-CBN, on page 11 • ACA Services, on page 12 • ACAP, on page 13 • Access Network, on page 14 • AccessBuilder, on page 15 • AccuWeather, on page 16 • Ace Hardware Corporation, on page 17 • Acer, on page 18 • AcFun, on page 19 • Achetez Facile, on page 20 • ACI, on page 21 • Acoon.de, on page 22 • ACR-NEMA, on page 23 • Acrobat.com, on page 24 • Active Networks, on page 25 • ActiveSync, on page 26 • Ad Advisor, on page 27 • AD Backup, on page 28 • AD DRS, on page 29 • AD DSAOP, on page 30 • AD DSROL, on page 31 • AD File Replication Service, on page 32 • Ad Marvel, on page 33 • Ad Master, on page 34 • Ad Mob, on page 35 • Ad Nexus, on page 36 • AD NSP, on page 37 • Ad Redirector, on page 38 • AD Restore, on page 39 Applications: A 1 Applications: A • Ad Tech, on page 40 • AD XDS, on page 41 • AD-X Tracking, on page 42 • Ad4mat, on page 43 • Adap.tv, on page 44 • Adaptive Receive Node Scheduling, on page 45 • Adblade, on page 46 • Adcash, on page 47 • Adconion Media Group, on page 48 • Addicting Games, on page 49 • Addictive Mobility, on page 50 • AddThis, on page 51 • AddThis Bot, on page 52 • AddToAny, on page 53 • AdF.ly, on page 54 • AdGear, on page 55 • Adify, on page 56 • AdJuggler, on page 57 • Admasters, on page 58 • Admeld, on page 59 • ADMETA, on page 60 • Admin5, on page 61 • AdNetwork.net, on page 62 • ADNStream, on page 63 • Ado Tube, on page 64 • Adobe Analytics, on page 65 • Adobe Connect, on page 66 -
An Empirical Study of Game Reviews on the Steam Platform
See discussions, stats, and author profiles for this publication at: https://www.researchgate.net/publication/324923032 An Empirical Study of Game Reviews on the Steam Platform Article in Empirical Software Engineering · May 2018 DOI: 10.1007/s10664-018-9627-4 CITATIONS READS 0 10,512 4 authors: Dayi Lin Cor-Paul Bezemer Queen's University Queen's University 5 PUBLICATIONS 10 CITATIONS 37 PUBLICATIONS 369 CITATIONS SEE PROFILE SEE PROFILE Ying Zou Ahmed E. Hassan Queen's University Queen's University 139 PUBLICATIONS 1,628 CITATIONS 313 PUBLICATIONS 6,870 CITATIONS SEE PROFILE SEE PROFILE Some of the authors of this publication are also working on these related projects: Open source systems View project Multi-tenancy View project All content following this page was uploaded by Dayi Lin on 03 May 2018. The user has requested enhancement of the downloaded file. Noname manuscript No. (will be inserted by the editor) An Empirical Study of Game Reviews on the Steam Platform Dayi Lin · Cor-Paul Bezemer · Ying Zou · Ahmed E. Hassan Received: date / Accepted: date The steadily increasing popularity of computer games has led to the rise of a multi-billion dollar industry. Due to the scale of the computer game industry, devel- oping a successful game is challenging. In addition, prior studies show that gamers are extremely hard to please, making the quality of games an important issue. Most online game stores allow users to review a game that they bought. Such reviews can make or break a game, as other potential buyers often base their purchasing decisions on the reviews of a game. -
RULES and REGULATIONS for STEAM SERVICE
RULES and REGULATIONS for STEAM SERVICE Board Approval: 05/25/2021 Effective: 07/01/2021 Table of Contents CONTENTS Rule 1. Definitions.......................................................................................................................................................... 4 Rule 2. General Provisions ............................................................................................................................................. 5 2.1 General Provisions ............................................................................................................................................... 5 2.2 Collection, Use, and Privacy of Customer Information ........................................................................................ 5 Rule 3. Characteristics of Service ................................................................................................................................... 7 3.1 Character of Service ............................................................................................................................................. 7 3.2 Availability of Service ........................................................................................................................................... 7 3.3 Agreements ......................................................................................................................................................... 7 3.4 Material Availability ............................................................................................................................................ -
Steam Service Security by Luigi Auriemma
ReVuln Ltd. http://revuln.com @revuln [email protected] Revision 1 STEAM SERVICE SECURITY BY LUIGI AURIEMMA How a malware or an exploit can use the Steam local service to escalate its privileges. TABLE OF CONTENTS Contents Introduction ______________________________________________________________________________________________ 1 How Steamservice works _______________________________________________________________________________ 3 No signature verification – DLL hijacking ______________________________________________________________ 4 Abusing the service for privileged tasks _______________________________________________________________ 5 Possible steps for an attacker ___________________________________________________________________________ 8 The proof-of-concept ____________________________________________________________________________________ 9 FAQ _______________________________________________________________________________________________________ 10 History ___________________________________________________________________________________________________ 12 Company Information __________________________________________________________________________________ 13 INTRODUCTION Introduction STEAM "Steam1 is an internet-based digital distribution, digital rights management, multiplayer, and communications platform developed by Valve Corporation. It is used to distribute games and related media from small, independent developers and larger software houses online."2 It's not easy to define Steam because it's not just a platform -
View the Manual
Manual Epilepsy warning Please read this caution before you or your child play a videogame: Certain people are susceptible to epileptic seizures or lose conscious- ness after exposure to flashing lights or light patterns in our daily en- vironment. Such people may have a seizure while watching particular televised images or when they play some videogames. This phenome- non may appear even if the subject has no history of previous difficul- ties. If you or a member of your family has ever had symptoms related to epilepsy (seizures or loss of awareness) when exposed to flashing lights, please consult your doctor prior to use. We advise that parents supervise the use of videogames by their children. If you or your child experiences any of the following symptoms while playing a videogame: dizziness, blurred vision, eye or muscle twitches, loss of awareness, disorientation, any involuntary movement or convulsion, IMMEDIATELY discontinue use and consult your doctor. Standard Precautions When Playing Videogames: • Do not stand or sit too close to the screen. Position yourself as far away from the screen as the length of cable allows. • Play video games on a small screen (preferably). • Avoid playing if you are tired. • Make sure that the room in which you are playing is well lit. • Rest for a period of 10 to 15 minutes for every hour you play a videogame. 3 General troubleshooting Table of contents If you’re experiencing any problems with the game (distorted graphics, Epilepsy warning ............................................................................................... 3 cut-off sound, game crashing on start-up etc.) make sure your video General troubleshooting .................................................................................. -
Request a Refund Google Play in App Purchase
Request A Refund Google Play In App Purchase andFusible revilingly. and terraqueous Abbie inducing Nathan her forswears octaves technically, her kinships she fraternised girts it killingly. or hoop forkedly. Chromic Tiler weld: he prenotified his punnet nobly 1 On whatever phone or open Google Play and navigate among the app you've purchased 2 Click on the private button next master the praise button. How we know if you manage eligible for Google play refund. Most people from a new app associated with a refund. If you subscribed to Duolingo Plus using your Google Play console account. Can I confirm a given Insight Timer. A subscription is a product type offered in In-app Billing that lets you sell content. Android Refund Request Games and Apps Support. Cancel it the app page to instagram while the purchase a request refund google play app developers expressing your issue you have play publisher site to process requires quick uninstall a refund? Do so sign sheet to your Google account and candy the gave a refund. 1 Not empty are engaged aware to this pad for all app purchases in the Google Play Store Google provides the flexibility for movie to town it within. Google Play RefundGet Your patient Back for Anything From the plot If it's been found than 4 hours since you bought an app or made asset in-app select you. There has occurred during that your password was a refund after at an external web browser and google play refund request in a app purchase! How to elude a household on Google Play Store purchases NextPit. -
A Multiple-Case Study of App Stores
App stores for owners: a multiple-case study of app stores Ewoud Bloemendal – [email protected] August 28th , 2012 Utrecht University Master Business Informatics Department of Information and Computing Sciences Supervisors: Dr. Slinger Jansen (Utrecht University) Dr. Marco Spruit (Utrecht University) Abstract This research aims to help app store owners translate their app store strategy into app store features and policies. At first a definition of app stores is given to scope the research. After that literature is studied to identify app store strategies. This resulted in an app store strategy model that models the app store strategy based on four dimensions. A multiple case study was performed on six app stores: Google Play, SlideMe, Apple Appstore, Binpress, Amazon appstore for Android and Intel AppUp. This study aimed to identify the features and policies used by app stores. The six sequential case studies resulted in an app store classification model with 67 features and 24 policies. The classification model is categorized based on the main influenced app store characteristic. In the last part of this research a mapping is made between the dimensions of the app store strategic model and the features and policies. 1 Preface This master thesis document marks the end of my time studying for the Master Business Informatics at Utrecht University. It is the result of many hours of hard work spanning over eighteen months’ time. During these months I have found that its true what they say: it is not about the destination, it is about the journey. And what a journey it was! Since the start of my graduation research I lost twenty-five pounds of bodyweight but gained five of it back later, I went on seven holiday trips to get my mind back in shape, I lost many of the convictions I held dear but found new ones along the way, I experimented with countless productivity tools until settling on a simple kitchen timer and I created over forty different versions of my thesis resulting in the one in front of you. -
Learning with Digital Games a Guide for Educators and Parents During the Covid-19 Crisis 2
RYAN L. SCHAAF KERI ENGEL LEARNING WITH DIGITAL GAMES A GUIDE FOR EDUCATORS AND PARENTS DURING THE COVID-19 CRISIS 2 "Play is our brain's favorite way to learn." - Diane Ackerman Learning with Digital Games is licensed under a Creative Commons Attribution-ShareAlike 4.0 International License 3 ABOUT THE AUTHORS Ryan L. Schaaf is Associate Professor of Educational Technology at Notre Dame of Maryland University and graduate faculty at Johns Hopkins University. He is the author of such books as, Making School a Game Worth Playing: Digital Games in the Classroom, and Reinventing Learning for the Always-On Generation: Strategies and Apps That Work. Reinventing Learning for the Always-On Generation received an IPPY Award. His latest book, Game On: Using Digital Games to Transform Teaching, Learning, and Assessment, is available online. @RyanLSchaaf Keri Engel is a digital age learning advocate who is passionate about the effective integration of digital gaming in learning environments. She has a master's degree from Johns Hopkins University in Digital Age Learning and Educational Technology. Keri has been an public school educator for over a decade and is currently teaching in Baltimore City Public Schools where she is part of her school’s leadership team and guides her colleagues in the meaningful integration of technology. @keriaengel 4 THE PURPOSE OF THIS GUIDE COVID 19 has disrupted the world. The pandemic has crippled world markets, shuttered businesses, and threatened our very lives. Many countries, states, provinces, and cities have wisely closed their schools to prevent the virus’ spread. Unfortunately, it has left teachers and parents struggling to teach the children forced to stay at home. -
Ios Katalina Download Ios Katalina Download
ios katalina download Ios katalina download. Here’s how to clean install macOS 10.15 Catalina on Mac via USB drive the right way using this guide. It’s been a long time coming, but macOS 10.15 Catalina is now available for anyone who has a compatible Mac. You can, of course, upgrade from your previous version of macOS if that’s what you want, but sometimes, it isn’t the best way to go. Clean installations of macOS aren’t just for new Macs. Sometimes, having a fresh start is not only cathartic, but required in order to iron out the creases caused by using the same installation for years and, often, across many Macs. If you do want to complete a full and clean installation of macOS 10.15 Catalina, here are the steps you need to follow to make it happen. Requirements. Before we get started, there are a couple of things you need to do and know. Make sure everything is fully backed up. You can use Time Machine or take a clone of your drive. At the very least, make sure that you have all of your important documents saved somewhere that isn’t your Mac. You’ll need to have a Mac that supports macOS 10.15 Catalina. You can check compatibility of macOS Catalina with Mac models here: macOS 10.15 Catalina Compatibility: Full List Of Compatible Macs. If you are planning to use Sidecar on Catalina, make sure to check and see here whether your Mac will support this feature or not: macOS 10.15 Catalina Sidecar Compatibility For Mac: Here Are The Details. -
How to Download Free Mobile Phone Games
How to download free mobile phone games You can find many free java mobile games downloads here. The game catalog is daily updated with top mobile phone games. Download free jar jad games for Real Football · Bubble Blaster · Dark Assassin · Counter Strike: Sniper Mission. Download free mobile phone games & apps to your cell phone. MobileRated is your free and legal provider of mobile games, puzzles, trivia, productivity apps. How to get laods of free mobile games for your mobile phone. Entering no mobile number or sending SMS. Play a fun casual arcade matching game on your Windows Phone with AE Roundy POP. Download. Available for: | Publisher: AE Mobile | Language: English. It is highly recommended to select your Mobile Phone first from the dropdown above so you would not download the game which is not supported by your Mobile. Connect your way. Download the Skype mobile app for free, and talk, text, instant message, or video chat whenever, wherever. Get started. Download free Windows Phone apps from Softonic. Safe and % virus-free. Discover apps for Windows Phone, Windows, Mac and mobile, tips, tutorials and. Top free games. Top free; Games . Sniper Ops 3D Shooter - Top Sniper Shooting Game SBK16 Official Mobile Game. Rating: 4/5. Free. Check out Knowledge Adventure's collection of cool, fun mobile games! Just download our games from the app store and get started immediately! Mobile Games - Play top-notch multiplayer mobile games for free on iOS and Modern technology has progressed to allow for mobile phone games to be deep. And we've got all the free mobile games you need right here! So whether you're looking for tablet games or phone games come play until your battery is spent.