Intersections of Music and Science in Experimental Violins of the Nineteenth Century Sarah M
Total Page:16
File Type:pdf, Size:1020Kb
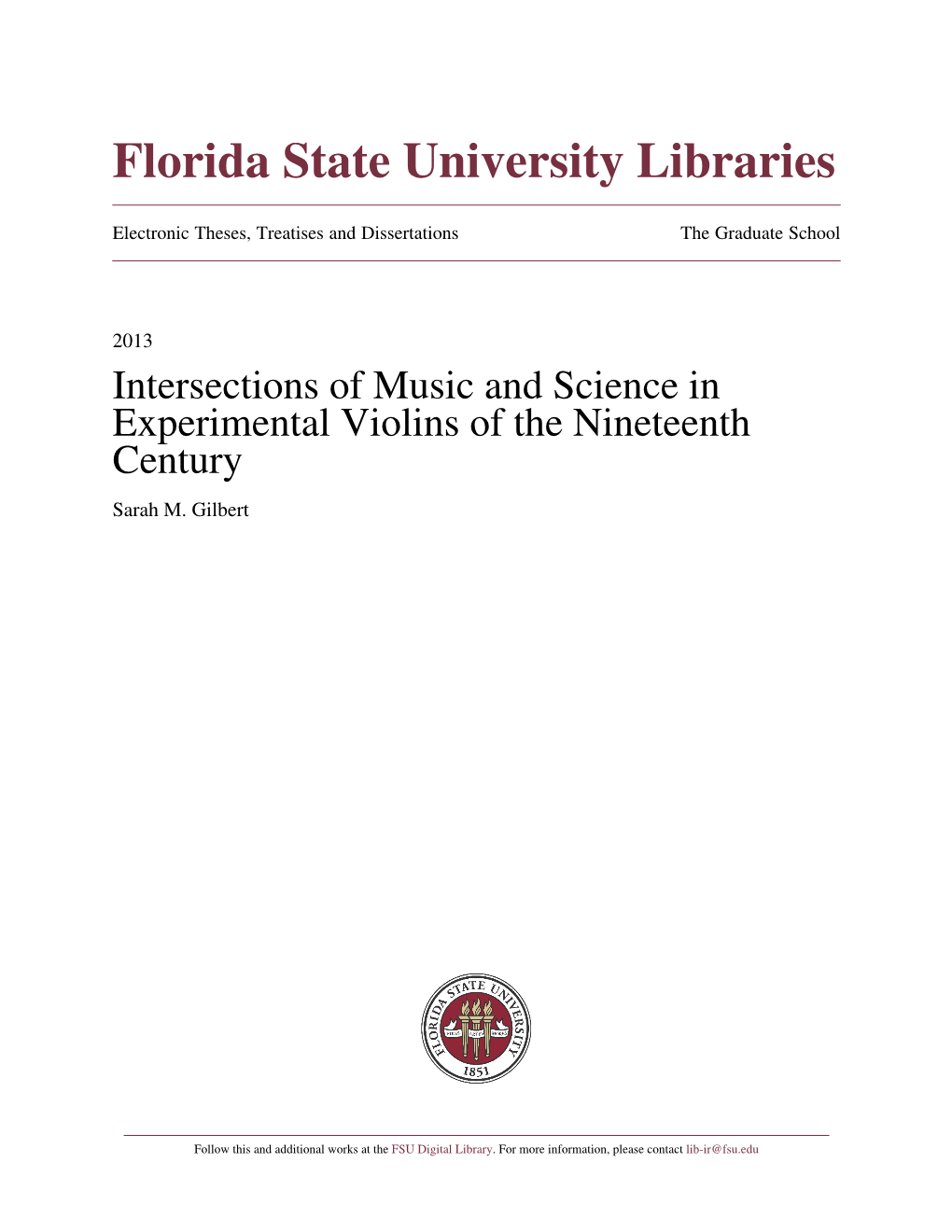
Load more
Recommended publications
-
Messiah Notes.Indd
Take One... The Messiah Violin Teacher guidance notes The Messiah Violin is on display in A zoomable image of the violin is available Gallery 39, Music and Tapestry. on our website. Visit www.ashmolean.org/education/ Starting Questions The following questions may be useful as a starting point for thinking about the Messiah violin and developing speaking and listening skills with your class. • What materials do you think this violin is made from? • Why do you think this violin is in a museum? • Where do you think it might come from? • What kind of person do you think would have owned this violin? • Who could have made it? • Does the violin look like it has been played a lot or does it look brand new? • How old do you think the violin could be? • If I told you that nobody is allowed to play this violin do you feel about that? These guidance notes are designed to help you use the Ashmolean’s Messiah violin as a focus for cross-curricular teaching and learning. A visit to the Ashmolean Museum to see your chosen object offers your class the perfect ‘learning outside the classroom’ opportunity. Background Information Italy - a town that was already famous for its master violin makers. The new styles of violins and cellos that The Object he developed were remarkable for their excellent tonal quality and became the basic design for many TThe Messiah violin dates from Stradivari’s ‘golden modern versions of the instruments. period’ of around 1700 - 1725. The violin owes Stradivari’s violins are regarded as the fi nest ever its fame chiefl y to its fresh appearance due to the made. -
B&F Magazine Issue 31
No. 31 A VIOLIN BY PIETRO GIOVANNI GUARNERI, MANTUA, 1709 superb instruments loaned to them by the Arrisons, gave spectacular performances and received standing ovations. Our profound thanks go to Karen and Clement Arrison for their dedication to preserving our classical music traditions and helping rising stars launch their careers over many years. Our feature is on page 11. Violinist William Hagen Wins Third Prize at the Queen Elisabeth International Dear Friends, Competition With a very productive summer coming to a close, I am Bravo to Bein & Fushi customer delighted to be able to tell you about a few of our recent and dear friend William Hagen for notable sales. The exquisite “Posselt, Philipp” Giuseppe being awarded third prize at the Guarneri del Gesù of 1732 is one of very few instruments Queen Elisabeth Competition in named after women: American virtuoso Ruth Posselt (1911- Belgium. He is the highest ranking 2007) and amateur violinist Renee Philipp of Rotterdam, American winner since 1980. who acquired the violin in 1918. And exceptional violins by Hagen was the second prize winner Camillo Camilli and Santo Serafin along with a marvelous of the Fritz Kreisler International viola bow by Dominique Peccatte are now in the very gifted Music Competition in 2014. He has hands of discerning artists. I am so proud of our sales staff’s Photo: Richard Busath attended the Colburn School where amazing ability to help musicians find their ideal match in an he studied with Robert Lipsett and Juilliardilli d wherehh he was instrument or bow. a student of Itzhak Perlman and Catherine Cho. -
A Violin by Giuseppe Giovanni Battista Guarneri
141 A VIOLIN BY GIUSEPPE GIOVANNI BATTISTA GUARNERI Roger Hargrave, who has also researched and drawn the enclosed poster, discusses an outstanding example of the work of a member of the Guarneri family known as `Joseph Guarneri filius Andrea'. Andrea Guarneri was the first He may never have many details of instruments by of the Guarneri family of violin reached the heights of his Joseph filius at this period recall makers and an apprentice of contemporary, the Amati school, this type of Nicola Amati (he was actually varnish, in combination with registered as living in the house Antonio Stradivarius, but he the freer hand of Joseph, gives of Nicola Amati in 1641). Andrea's does rank as one of the the instruments a visual impact youngest son, whose work is il - greatest makers of all time. never achieved by an Amati or , lustrated here, was called. We should not forget he with the exception of Stradi - Giuseppe. Because several of the sired and trained the great vari, by any other classical Guarneri family bear the same del Gesu' maker before this time. christian names, individuals have traditionally been identified by a It should be said, however, suffix attached to their names. that the varnish of Joseph filius Thus, Giuseppe's brother is known as `Peter Guarneri varies considerably. It is not always of such out - of Mantua' to distinguish him from Giuseppe's son, standing quality the same can be said of Joseph's pro - who is known as `Peter Guarneri of Venice'. duction in general. If I were asked to describe the instruments of a few of the great Cremonese makers Giuseppe himself is called 'Giuseppe Guarneri filius in a single word, I would say that Amatis (all of them) Andrea' or, more simply, `Joseph filius' to distinguish are `refined', Stradivaris are `stately', del Gesus are him from his other son, the illustrious 'Giuseppe `rebellious' and the instruments of Joseph filius An - Guarneri del Gesu'. -
The Baroque Cello and Its Performance Marc Vanscheeuwijck
Performance Practice Review Volume 9 Article 7 Number 1 Spring The aB roque Cello and Its Performance Marc Vanscheeuwijck Follow this and additional works at: http://scholarship.claremont.edu/ppr Part of the Music Practice Commons Vanscheeuwijck, Marc (1996) "The aB roque Cello and Its Performance," Performance Practice Review: Vol. 9: No. 1, Article 7. DOI: 10.5642/perfpr.199609.01.07 Available at: http://scholarship.claremont.edu/ppr/vol9/iss1/7 This Article is brought to you for free and open access by the Journals at Claremont at Scholarship @ Claremont. It has been accepted for inclusion in Performance Practice Review by an authorized administrator of Scholarship @ Claremont. For more information, please contact [email protected]. Baroque Instruments The Baroque Cello and Its Performance Marc Vanscheeuwijck The instrument we now call a cello (or violoncello) apparently deve- loped during the first decades of the 16th century from a combina- tion of various string instruments of popular European origin (espe- cially the rebecs) and the vielle. Although nothing precludes our hypothesizing that the bass of the violins appeared at the same time as the other members of that family, the earliest evidence of its existence is to be found in the treatises of Agricola,1 Gerle,2 Lanfranco,3 and Jambe de Fer.4 Also significant is a fresco (1540- 42) attributed to Giulio Cesare Luini in Varallo Sesia in northern Italy, in which an early cello is represented (see Fig. 1). 1 Martin Agricola, Musica instrumentalis deudsch (Wittenberg, 1529; enlarged 5th ed., 1545), f. XLVIr., f. XLVIIIr., and f. -
The Science of String Instruments
The Science of String Instruments Thomas D. Rossing Editor The Science of String Instruments Editor Thomas D. Rossing Stanford University Center for Computer Research in Music and Acoustics (CCRMA) Stanford, CA 94302-8180, USA [email protected] ISBN 978-1-4419-7109-8 e-ISBN 978-1-4419-7110-4 DOI 10.1007/978-1-4419-7110-4 Springer New York Dordrecht Heidelberg London # Springer Science+Business Media, LLC 2010 All rights reserved. This work may not be translated or copied in whole or in part without the written permission of the publisher (Springer Science+Business Media, LLC, 233 Spring Street, New York, NY 10013, USA), except for brief excerpts in connection with reviews or scholarly analysis. Use in connection with any form of information storage and retrieval, electronic adaptation, computer software, or by similar or dissimilar methodology now known or hereafter developed is forbidden. The use in this publication of trade names, trademarks, service marks, and similar terms, even if they are not identified as such, is not to be taken as an expression of opinion as to whether or not they are subject to proprietary rights. Printed on acid-free paper Springer is part of Springer ScienceþBusiness Media (www.springer.com) Contents 1 Introduction............................................................... 1 Thomas D. Rossing 2 Plucked Strings ........................................................... 11 Thomas D. Rossing 3 Guitars and Lutes ........................................................ 19 Thomas D. Rossing and Graham Caldersmith 4 Portuguese Guitar ........................................................ 47 Octavio Inacio 5 Banjo ...................................................................... 59 James Rae 6 Mandolin Family Instruments........................................... 77 David J. Cohen and Thomas D. Rossing 7 Psalteries and Zithers .................................................... 99 Andres Peekna and Thomas D. -
Significance of Beating Observed in Earthquake Responses of Buildings
SIGNIFICANCE OF BEATING OBSERVED IN EARTHQUAKE RESPONSES OF BUILDINGS Mehmet Çelebi1, S. Farid Ghahari2, and Ertuğrul Taciroǧlu2 U.S. Geological Survey1 and University of California, Los Angeles2 Menlo Park, California, USA1 and Los Angeles, California, USA2 Abstract The beating phenomenon observed in the recorded responses of a tall building in Japan and another in the U.S. are examined in this paper. Beating is a periodic vibrational behavior caused by distinctive coupling between translational and torsional modes that typically have close frequencies. Beating is prominent in the prolonged resonant responses of lightly damped structures. Resonances caused by site effects also contribute to accentuating the beating effect. Spectral analyses and system identification techniques are used herein to quantify the periods and amplitudes of the beating effects from the strong motion recordings of the two buildings. Quantification of beating effects is a first step towards determining remedial actions to improve resilient building performance to strong earthquake induced shaking. Introduction In a cursory survey of several textbooks on structural dynamics, it can be seen that beating effects have not been included in their scopes. On the other hand, as more earthquake response records from instrumented buildings became available, it also became evident that the beating phenomenon is common. As modern digital equipment routinely provide recordings of prolonged responses of structures, we were prompted to visit the subject of beating, since such response characteristics may impact the instantaneous and long-term shaking performances of buildings during large or small earthquakes. The main purpose in deploying seismic instruments in buildings (and other structures) is to record their responses during seismic events to facilitate studies understanding and assessing their behavior and performances during and future strong shaking events. -
Echo Eliminator Ceiling & Wall Panels
Echo Eliminator Ceiling & Wall Panels Echo Eliminator, or Bonded Acoustical Cotton (B.A.C.), is the most cost-effective acoustical absorbing material on the market. It is a high-performance panel manufactured from recycled cotton, and is ideal for noise control applications. Echo Eliminator can easily be installed as acoustical wall panels or hanging baffles. • No VOCs (Volatile Organic Compounds) • No formaldehyde, requires no warning labels • Fungi-, mold-, and mildew-resistant • Class A Fire Rated (Non-flammable per ASTM E-84) ACOUSTICAL SURFACES, INC. CELEBRATING 35 YEARS – SOUNDPROOFING, ACOUSTICS, NOISE & VIBRATION SPECIALISTS! ™ 952.448.5300 • 800.448.0121 • [email protected] • www.acousticalsurfaces.com Echo Eliminator APPLICATIONS Residential, commercial, industrial; schools, restaurants, classrooms, Ceiling & Wall Panels houses of worship, community centers, offices, conference rooms, music rooms, recording studios, theaters, public spaces, medical facilities, audi- toriums, arenas/stadiums, warehouses, manufacturing plants, and more. Acoustics and Expected Performance: Absorbing sound and reducing echo / reverberation can be challeng- ing. Echo Eliminator offers a high Noise Reduction Coefficient (NRC) to reduce the amount of sound within a room. One-inch thick panels are appropriate for areas wher e the main issue is understanding speech. Rooms with more mid-and-low frequency noise, or where music is present, benefit from using two-inch thick panels. SIZES & OPTIONS Standard Size: 24" x 48" (minimum quantities apply, call for details); options: 12" x 12", 24" x 24", 48" x 48", 48" x 96". Note: All sizes are nominal and subject to manufacturing tolerances that may vary +/- 1/8". Thickness/Density: 1" thick / 3 lb. per cubic foot (pcf); 1" thick/6 lb. -
Jan. 6, 1970 M
Jan. 6, 1970 M. TANSKY 3,487,740 VIOLIN WITH TIMBRE BASS BAR Filed May 9, 1968 c?????? NivENTOR NA CA E TANSKY’ AORNEYS 3,487,740 United States Patent Office Patented Jan. 6, 1. 970 2 Still further objects and advantages of the present in 3,487,740 VIOLIN WITH TEMBRE BASSBAR Vention will readily become apparent to those skilled in the Michael Tansky, 541 Olive Ave., art to which the invention pertains on reference to the Long Beach, Calif. 90812 following detailed description. Filed May 9, 1968, Ser. No. 727,774 5 Description of the drawing ? . , Int. CI. G10d 1/02 0 The description refers to the accompanying drawing in U.S. C. 84-276 6 Claims which like reference characters refer to like parts through out the several views in which: FIGURE 1 is a longitudinal sectional view of the sound ABSTRACT OF THE DISCLOSURE O box of a violin showing the bass bar embodying my in A violin having an elongated, internally mounted bass vention; , ; bar with a continuous series of conical cavities extending FIGURE 2 is a view of the preferred bass bar, sepa along its inner longitudinal edge and facing the back of rated from the instrument as along one of its longitudinal the instrument. The bass bar results in the violin pro edges; w ` ? - . ducing pure, limpid tones while the cavities reduce the FIGURE3 is a view of the opposite longitudinal edge weight of the bass bar. Y. of the preferred bass bar; and : ... TSSSLSLSSSSLLLLL SLLS0L0LSLSTM SM FIGURE 4 is a fragmentary perspective view of the Background of the invention mid-section of the preferred bass bar. -
Alison Rabinovici
A web of connections The orchestral ledger in the Louise Hanson-Dyer Music Library Alison Rabinovici One of the treasures of the Louise Hanson-Dyer Music Library is a ledger which documents the library’s holdings of orchestral music, and records the loans of those scores and parts for a period of nearly 50 years, from 1910 to 1954. It is, perhaps, the only extant—and complete— document of its kind in Australia. The ledger was produced by E. Whitehead & Co., of 238 Collins Street, Melbourne, and is dated ‘27/8/1910’. It is an impressive document in its own right, consisting of nearly 900 pages held between two massive linen-covered compressed cardboard covers. Nearly 100 years later, it was showing the combined effects of age, insect and water damage, and neglect. The ledger contains within its pages a view into aspects of the and further afield. Until the recent Evelyn Portek, Music Librarian of the history of music education at the conservation of the ledger, Louise Hanson-Dyer Music Library, University of Melbourne. It gives at information contained within it was represented the library’s interests in least a partial view of programming inaccessible. the project, while Jude Fraser, and performance, and hence the A fieldwork placement in the Grimwade Conservator at the reception, of music in Melbourne in subject ‘History in the Field’ with University’s Centre for Cultural the first half of the 20th century. As a Dr Andrew Brown-May and Dr June Materials Conservation, provided record of loans of orchestral music to Senyard in 2006 offered -
Reconstructing Lost Instruments Praetorius’S Syntagma Musicum and the Violin Family C
Prejeto / received: 3. 5. 2019. Odobreno / accepted: 12. 9. 2019. doi: 10.3986/dmd15.1-2.07 RECONSTRUCTING LOST INSTRUMENTS Praetorius’S Syntagma musicum and the Violin Family C. 1619 Matthew Zeller Duke University Izvleček: Knjigi De organographia in Theatrum Abstract: Michael Praetorius’s De organographia instrumentorum Michaela Praetoriusa vsebujeta and Theatrum instrumentorum provide valuable dragocene namige, ki pomagajo pri poznavanju clues that contribute to a new understanding glasbil iz družine violin okoli leta 1619; številna of the violin family c. 1619, many surviving ex- preživela glasbila so manjša, kot so bili izvirniki amples of which are reduced in size from their v 16. in 17. stoletju. Podatki o preživelih glas- sixteenth- and seventeenth-century dimensions. bilih – predvsem izdelki družine Amati – skupaj The record of surviving instruments – especially z metrologijo, sekundarno dokumentacijo in those of the Amati family – alongside metrologic, ikonografskim gradivom kažejo na to, da je documentary and iconographic evidence shows Michael Praetorius opisal veliko glasbilo, po that Michael Praetorius describes a large in- velikosti izjemno podobno violončelu (basso strument conforming remarkably well to the da braccio),kar je odličen primer predstavitve original dimensions of the basso da braccio glasbila iz družine violin in točne uglasitve, kot (violoncello), as well as furnishing an excellent so jih poznali v času izida Praetoriusovega dela. scale representation of the violin family as it was at the time of these works’ -
Artikelverzeichnis
Artikelverzeichnis A B Aa, Michel van der Bacewicz, Grazyna˙ Abaco, Evaristo Felice Dall’ Bach-Bogen Abel, Jenny Bach, Carl Philipp Emanuel Abstrich, Aufstrich Bach, Johann Sebastian Accardo, Salvatore Badings, Henk Herman Accolaÿ, Jean-Baptiste Baillot, Pierre (Marie François de Sales) Accordatura Balestrieri, Tommaso Achron, Joseph Baltzar, Thomas Adams, John (Coolidge) Banks, Benjamin Adern Einlagen Bariolage Akkordspiel Barockvioline Alard, Jean-Delphin Barthélémon, François-Hippolyte Alban, Matthias Bartók, Béla (Viktor János) Albicastro, Henrico Bartók-Pizzicato Albinoni, Tomaso Giovanni Baryton Amati (Famile) Bass, Bassgeige Amoyal, Pierre Bassani, Giovanni Battista Antoniazzi (Familie) Bassbalken Antonii, Pietro degli Bassett Halbbass Applicatura, Applikatur Basso continuo Arányi, Jelly d’ Batiashvili, Lisa archet Bauch arco Bax, Arnold (Edward Trevor) arco normale Bazzini, Antonio Arditti, Irvine Bearbeitung Arpeggio, arpeggiando Bebung Arpeggione Beethoven, Ludwig van Arrangement Bearbeitung Bell, Joshua (David) Artesono-Violine Benda, Franz Artikulation Bennewitz, Antonín Asmussen, Svend Bereifung ASTA Berg, Alban (Maria Johannes) au chevalet sul ponticello Bergonzi (Familie) Auer, Leopold (von) Berio, Luciano Aufführungspraxis Bériot, Charles-Auguste de Aufstrich Abstrich Berlioz (Louis) Hector Aulin, Tor (Bernhard Vilhelm) Bernardel (Familie) AUSTA Bertolotti, Gasparo Gasparo da Salò Ayo, Félix Berwald, Franz (Adolf) Betts, John Edward 18 Artikelverzeichnis Beyer, Amandine Carter, Elliott (Cook) Bezug Cartier, Jean-Baptiste -
Syrinx (Debussy) Body and Soul (Johnny Green)
Sound of Music How It Works Session 5 Musical Instruments OLLI at Illinois Hurrian Hymn from Ancient Mesopotamian Spring 2020 Musical Fragment c. 1440 BCE D. H. Tracy Sound of Music How It Works Session 5 Musical Instruments OLLI at Illinois Shadow of the Ziggurat Assyrian Hammered Lyre Spring 2020 (Replica) D. H. Tracy Sound of Music How It Works Session 5 Musical Instruments OLLI at Illinois Hymn to Horus Replica Ancient Lyre Spring 2020 Based on Trad. Eqyptian Folk Melody D. H. Tracy Sound of Music How It Works Session 5 Musical Instruments OLLI at Illinois Roman Banquet Replica Kithara Spring 2020 Orig Composition in Hypophrygian Mode D. H. Tracy Sound of Music How It Works Session 5 Musical Instruments OLLI at Illinois Spring 2020 D. H. Tracy If You Missed a Session…. • PDF’s of previous presentations – Also other handout materials are on the OLLI Course website: http://olli.illinois.edu/downloads/courses/ The Sound of Music Syllabus.pdf References for Sound of Music OLLI Course Spring 2020.pdf Smartphone Apps for Sound of Music.pdf Musical Scale Cheat Sheet.pdf OLLI Musical Scale Slider Tool.pdf SoundOfMusic_1 handout.pdf SoM_2_handout.pdf SoM_3 handout.pdf SoM_4 handout.pdf 2/25/20 Sound of Music 5 6 Course Outline 1. Building Blocks: Some basic concepts 2. Resonance: Building Sounds 3. Hearing and the Ear 4. Musical Scales 5. Musical Instruments 6. Singing and Musical Notation 7. Harmony and Dissonance; Chords 8. Combining the Elements of Music 2/25/20 Sound of Music 5 7 Chicago Symphony Orchestra (2015) 2/25/20 Sound of Music