PDF File Generated From
Total Page:16
File Type:pdf, Size:1020Kb
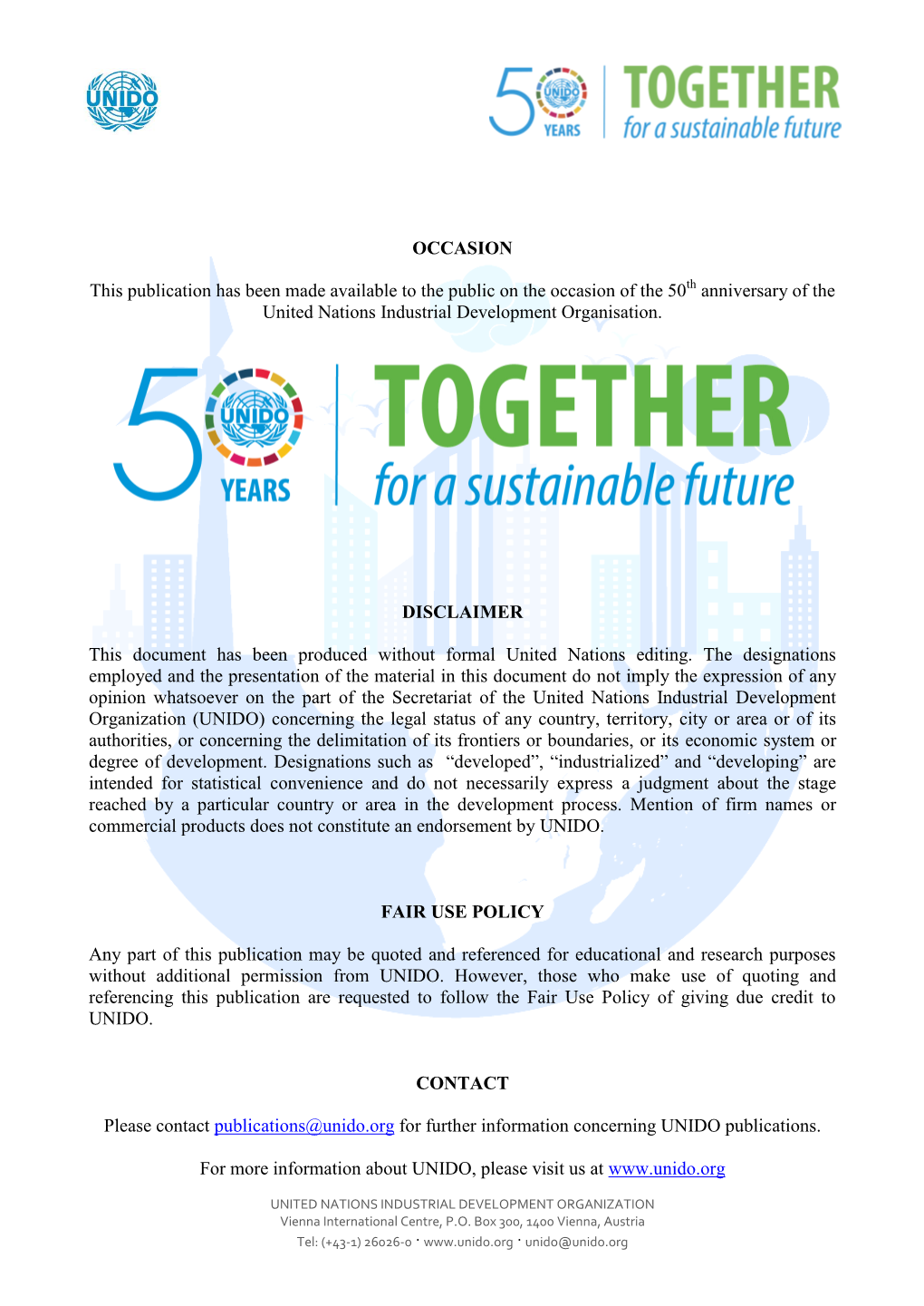
Load more
Recommended publications
-
Biomass Drying: Experimental and Numerical Investigations
archives of thermodynamics Vol. 39(2018), No. 1, 39–73 DOI: 10.1515/aoter-2018-0003 Biomass drying: Experimental and numerical investigations JACEK ŻABSKIa∗ PIOTR LAMPARTa STANISŁAW GUMKOWSKIb a Institute of Fluid Flow Machinery, Polish Academy of Sciences, 80-231 Gdańsk, Fiszera 14, Poland b Gdańsk School of Higher Education, 80-875 Gdańsk, Biskupia 24B Abstract Results of experimental and numerical investigations of wood chips drying are described in the paper. Experiments are carried out on two test facilities: a small laboratory rig and a larger pre-prototype dryer. Both facilities are thorough-circulation convective air dryers. The first one is a batch dryer, whereas the second one is a continuous dryer with wood chips flowing down by gravity from a charging hopper to a gutter with the aid of screw-conveyor. The latter is considered a half scale model (pre- prototype) for professional drying installations. A low feeding rate of wood chips into the pre-prototype dryer makes the process quasi-stationary and the difference between it and a batch drying is negligible. So, most exper- iments at this facility were carried out as batch dryers with non-agitated packed beds. The investigations exhibit the same linear correlation between the mass of evaporated water from the packed bed and the drying air veloc- ity for both facilities. Numerical analysis of the drying process is conducted using the Ansys Fluent software enriched in drying capabilities by means of self-written procedures – user defined functions. Simulations confirmed a phenomenon of a drying front observed in the small laboratory rig. A thin layer of wood chips comprises the whole heat exchange and moisture evap- oration phenomenon. -
METHODS of ACCELERATING WOOD DRYING by Leif D
METHODS OF ACCELERATING WOOD DRYING by Leif D. Espenas Oregon Forest Products Laboratory, Corvallis, Oregon Introduction Methods of accelerating the drying of wood have always been the subject of keen interest by the wood industries. Rapid drying methods are potentially low cost drying methods and the conveniences inherent in short drying periods provide ad- ditional attractions. Unfortunately, some of the methods proposed are not cheaper methods but may be even more costly than the current air drying on kiln drying methods. Others hold little or no promise of being capable of doing a reasonably good job of drying and there are a few proposed methods that do not in fact reduce drying time. Within modern times, kiln drying, which had its start almost a century ago, has been the most successful method of accelerating drying. Despite the fact that there are some few persons who are still skeptical of the merits of kiln drying, there can be little doubt about its success. Current research in drying is largely directed to- wards improvement of kiln drying methods. These efforts, however, along with more fundamental studies of the seasoning of wood, may sometime result in even greater success either by- kiln drying or by some other method. Basic Theory of Wood Drying The basic concepts of the drying of wood involve knowledge of the structure of wood and of moisture diffusion, neither of which are as yet completely understood. Botanists, anatomists, wood technologists and chemists have long been studying wood structure, but theories and studies of the movement of moisture in wood as it dries are about as new as the development of the internal fan dry kiln. -
Heat Sterilization of Wood Xiping Wang, Research Forest Products Technologist
CHAPTER 20 Heat Sterilization of Wood Xiping Wang, Research Forest Products Technologist Insects and other pests can travel between countries in pal- lets and other wood packaging materials through interna- Contents tional trade. Because these pests can cause significant eco- Heat Treatment Standards 20–1 logical damage, their invasion into non-native countries is Factors Affecting Heating Times 20–2 undesirable. Heat sterilization is currently the most practical and environmentally friendly treatment to kill pests in solid Energy Source 20–2 wood materials and prevent their transfer between conti- Heating Medium 20–2 nents and regions. Consequently, regulations requiring heat Air Circulation 20–2 sterilization are becoming more and more common. Size and Configuration of Wood 20–2 Two important questions should be considered in heat steril- Species 20–2 izing solid wood materials: First, what temperature–time Stacking Methods 20–2 regime is required to kill a particular pest? Second, how much time is required to heat the center of any wood con- Heating Times for Wood in Various Forms 20–4 figuration to the kill temperature? The entomology research Methods for Estimating Heating Times 20–5 on the first question has facilitated the development of in- MacLean Equations 20–5 ternational standards for heat sterilization of various solid Multiple Regression Models 20–7 wood materials. This chapter primarily addresses the second question. It focuses on various factors that should be con- American Lumber Standard Committee (ALSC) sidered when planning and implementing a heat treatment Enforcement Regulations 20–9 process, discusses experimentally derived heating times for Quality Mark 20–11 commonly used wood products, and presents analytical and Other Considerations 20–11 empirical methods for estimating heating times that can be Literature Cited 20–13 used as starting points in the development of heat treatment schedules. -
Dry Kiln Operator's Manual
United States Department of Agriculture Dry Kiln Forest Service Operator's Forest Products Laboratory Manual Madison, Wisconsin Agriculture Handbook No. 188 Dry Kiln Operator’s Manual Edited by William T. Simpson, Research Forest Products Technologist United States Department of Agriculture Forest Service Forest Products Laboratory 1 Madison, Wisconsin Revised August 1991 Agriculture Handbook 188 1The Forest Products Laboratory is maintained in cooperation with the University of Wisconsin. This publication reports research involving pesticides. It does not contain recommendations for their use, nor does it imply that the uses discussed here have been registered. All uses of pesticides must be registered by appropriate State and/or Federal agencies before they can be recommended. CAUTION, Pesticides can be injurious to humans, domestic animals, desirable plants, and fish or other wildlife-if they are not handled or applied properly. Use all pesticides selectively and carefully. Follow recommended practices for the disposal of surplus pesticides aand pesticide containers. Preface Acknowledgments The purpose of this manual is to describe both the ba- Many people helped in the revision. We visited many sic and practical aspects of kiln drying lumber. The mills to make sure we understood current and develop- manual is intended for several types of audiences. ing kiln-drying technology as practiced in industry, and First and foremost, it is a practical guide for the kiln we thank all the people who allowed us to visit. Pro- operator-a reference manual to turn to when questions fessor John L. Hill of the University of New Hampshire arise. It is also intended for mill managers, so that they provided the background for the section of chapter 6 can see the importance and complexity of lumber dry- on the statistical basis for kiln samples. -
Dimensional Stability of Waterlogged Scots Pine Wood Treated with PEG and Dried Using an Alternative Approach
Article Dimensional Stability of Waterlogged Scots Pine Wood Treated with PEG and Dried Using an Alternative Approach Mariusz Fejfer 1,2 , Jerzy Majka 3,* and Magdalena Zborowska 1 1 Department of Chemical Wood Technology, Faculty of Forestry and Wood Technology, Pozna´nUniversity of Life Sciences, Wojska Polskiego 38/42, 60-637 Pozna´n,Poland; [email protected] (M.F.); [email protected] (M.Z.) 2 Archaeological Museum in Biskupin. Biskupin 17, 88-410 G ˛asawa,Poland 3 Department of Wood Science and Thermal Technics, Faculty of Forestry and Wood Technology, Pozna´nUniversity of Life Sciences, Wojska Polskiego 38/42, 60-637 Pozna´n,Poland * Correspondence: [email protected]; Tel.: +48-61-848-7442 Received: 21 October 2020; Accepted: 24 November 2020; Published: 26 November 2020 Abstract: Low-intensity drying is widely believed to protect waterlogged archeological wood against the adverse effects of dimensional alteration and cracking. However, slow drying generates substantial costs for the conservation process. This study compares the effects on conservation of highly-degraded sapwood (SW) and slightly-degraded heartwood (HW) from waterlogged archeological Scots pine wood treated with polyethylene glycol either as a mixture of polyethylene glycol (PEG) 400/4000 or PEG 2000 solution and air-dried using different approaches. The reference air-drying approach, using gradually decreasing air relative humidity (RH), i.e., 96, 86, 75, 66, and finally 44% (multi-stage schedule), was compared to an alternative approach, using constant RH of 44% (single-stage schedule). The Fourier-transform infrared spectroscopy (FTIR) analysis confirmed the decomposition of hydrophilic chemical wood components and revealed differences in the degree of degradation of waterlogged SW and HW. -
Drying Eastern Hardwood Lumber
DRYING EASTERN HARDWOOD LUMBER AGRICULTURE HANDBOOK NO. 528 FOREST SERVICE U. S. DEPARTMENT OF AGRICULTURE DRYING EASTERN HARDWOOD LUMBER By JOHN M. MCMILLEN and EUGENE M. WENGERT Forest Products Laboratory Forest Service U. S. Department of Agriculture (Maintained at Madison, Wisconsin, in cooperation with the University of Wisconsin) AGRICULTURE HANDBOOK NO. 528 September 1978 Library of Congress Catalog No. 77-600073 McMILLEN, JOHN M. and WENGERT, EUGENE M. 1977. Drying eastern hardwood lumber. U.S. Dep. Agrie, Ag- rie. Handb. 528, 104 p. Presents recommendations based on recent research and industry practice for drying eastern hardwood lumber, in- cluding dimension items. Accent is on comparing methods for energy-saving management decisions, but practical guid- ance is also given to wood drying personnel. Air drying, accelerated air drying, and kiln drying are covered. KEYWORDS: Hardwoods, drying, air drying, kiln drying, forced-air drying, high-temperature drying, steaming, de- humidifier drying, cost accounting, energy saving, degrade reduction. ABOUT THE AUTHORS . JOHN M. McMILLEN is a forest products technologist who has specialized in the drying of wood for more than three decades at the Forest Products Laboratory. EUGENE M. WENGERT, formerly a member of the wood dry- ing group at the Laboratory, is now extension specialist in wood technology at Virginia Polytechnic Institute and State University, Blacksburg, Va. For sale by the Superintendent of Documents U.S. Government Printing Office Washington, D.C. 20402 Stock Number 001-000-03761-7 11 PREFACE Interest in broader utilization of hardwoods has been spurred by shortages of softwoods and an apparent surplus of hardwoods. However, to greatly increase use of hardwoods will require simphfied drying procedures. -
WATER ADSORPTION of PARTICLEBOARD and FLAKEBOARD' Benedito R
WATER ADSORPTION OF PARTICLEBOARD AND FLAKEBOARD' Benedito R. Vital2 Graduate Research Assistant and James B. Wilson Associate Professor Department of Forest Products, School of Forestry, Oregon State University, Corvallis, OR 97331 (Received 14 February 1980) ABSTRACT The amount of water adsorption (WA) determines the dimensional stability of particleboard and flakeboard. Regression models showed that WA is a function of relative humidity, resin type, and board specific gravity, as well as the thickness and slenderness ratio of the wood furnish. Those factors explained 95% of all variation in WA. Keywords: Water adsorption, particleboard, flakeboard, regression models, dimensional stability, urea- and phenol-formaldehyde resin. INTRODUCTION Particleboard is the generic term for a panel manufactured from lignocellulosic materials. Wood-based particleboard is made from dry wood particles that have been coated with resin, formed into a mat, and pressed under heat; flakeboard is a particleboard composed of flakes. Processing parameters-wood species, reduction of solid wood to particles or flakes, drying temperature, amount and kind of resin and wax, moisture content of the mat, compression ratio, and press- ing conditions-markedly affect the properties of the finished panels. For example, because wood particleboard and flakeboard are hygroscopic, their response to changes in relative humidity is complex. The environmental moisture affects the moisture content of the board, measurably changing linear expansion in the plane of the panel and thickness swelling perpendicular to the plane. The amounts of linear expansion and thickness swelling depend on the processing parameters, which also affect water adsorption (W,4) and equilibrium moisture content at different relative humidities. In turn, WA and exposure conditions directly affect the amount of linear expansion and thickness swelling. -
Chapter 1 Properties of Wood Related to Drying
Chapter 1 Properties of Wood Related to Drying Commercial wood species 1 Lumber drying is one of the most time- and energy- Hardwoods and softwoods 2 consuming steps in processing wood products. The Structural features of wood 2 anatomical structure of wood limits how rapidly wa- Sapwood and heartwood 4 ter can move through and out of wood. In addition, Pith 4 the sensitivity of the structure to stresses set up in dry- Annual growth rings 4 ing limits the drying rate; rapid drying causes defects Wood rays 4 such as surface and internal checks, collapse, splits, Grain and texture 5 and warp. Drying time and susceptibility to many dry- Color 5 ing defects increase at a rate that is more than pro- Variations in structure 5 portional to wood thickness. The variability of wood Commercial lumber grades 6 properties further complicates drying. Each species has Hardwood lumber grades 6 different properties, and even within species, variability Softwood lumber grades 6 in drying rate and sensitivity to drying defects impose Wood-moisture relations 7 limitations on the development of standard drying pro- Free and bound water 8 cedures. The interactions of wood, water, heat, and Fiber saturation point 8 stress during drying are complex. The purpose of this Equilibrium moisture content 8 chapter is to describe some of the fundamental prop- How wood dries 9 erties of wood that are relevant to lumber drying. We Forces that move water 9 will discuss commercial wood species, wood structure, Factors that influence drying rate 10 lumber grades, water movement in wood, how wood Lumber thickness 10 dries, specific gravity and weight of wood, wood shrink- Specific gravity and weight of wood 10 age, stress development during drying, and electrical Shrinkage of wood 11 and thermal properties of wood. -
Principles and Practices of Drying Lumber
Principles and Practices of Drying Lumber Eugene M. Wengert, Extension Specialist Brooks Forest Products Center Virginia Polytechnic Institute and State University Blacksburg, Virginia Copyright © 2006 Lignomat USA Ltd. All Rights Reserved. Table of Contents Why Dry Wood? ............................................................................................................................5 How Dry Should Wood Be? ..........................................................................................................6 Wood Drying Methods ..................................................................................................................8 Air Drying..................................................................................................................................8 Forced-Air Air-Drying (or Fan Shed Drying) ...........................................................................9 Low Temperature Warehouse Predrying...................................................................................9 Low Temperature Dehumidification Drying .............................................................................9 Normal Temperature or Conventional Temperature Kiln Drying .............................................9 Drying Systems........................................................................................................................10 Degrade....................................................................................................................................10 Air Drying -
MDF): Theory and Experiment
Chemical Engineering Science 59 (2004) 735–745 www.elsevier.com/locate/ces High frequency heating of medium density ÿberboard (MDF): theory and experiment Celeste M.C. Pereiraa, Calixte Blanchardb, Luisa M.H. Carvalhoa, Carlos A.V. Costaa;∗ aLEP, Laboratory of Process, Environment and Energy Engineering, Faculdade de Engenharia, Depto de Engenharia Quimica, Universidade do Porto, Rua Dr Roberto Frias s/n, 4200-465 Porto, Portugal bCTBA, Centre Technique du Bois et d’Ameublement, 33028 Bordeaux, Cedex, France Received 22 February 2002; received in revised form 15 July 2003; accepted 14 September 2003 Abstract Medium-density ÿberboard (MDF) is a wood-based panel manufactured from wood ÿbers with a synthetic adhesive through the conduction ofheat fromthe hot platens. One alternative is the use ofhigh-frequency(HF) heating, which has the advantage ofreducing the press cycle, the platens temperature and the post-curing time, with constancy ofresin formulation.For this approach, an electromagnetic (EM) heating model was developed and coupled with a three-dimensional model for heat and mass transfer and resin polymerization already existent. A solution ofthe Maxwell equations is used to determine the spatial distribution ofthe electric ÿeld inside the material and the absorbed power. MDF mat was assumed as a porous and homogeneous material at macroscopic level and a dielectric mixture at microscopic level (volume ofcontrol). The mat dielectric properties (wood ÿbers/particles and UF resin) were estimated using a “rule of mixture” and depend on local temperature and moisture content during the heating process. This dynamic model was used to predict the evolution ofthe local variables related to heat and mass transfer(temperature and moisture content), as well as the variable connected to the EM behavior (dielectric properties ofthe mat). -
Design Is in the Details Ensuring Durability in Wood Construction Sponsored by Rethink Wood, American Wood Council, and US Woodworks | by Layne Evans
1 Photo courtesy of WG Clark Construction; Architect: Ankrom Moisan Architects Campus housing under construction EDUCATION CONTINUING Project: Mercer Court, University of Washington, Washington State Design Is in the Details Ensuring durability in wood construction Sponsored by reThink Wood, American Wood Council, and US WoodWorks | By Layne Evans rchitects specify wood for many reasons, even 20 years ago. Glued laminated timber CONTINUING EDUCATION including cost, ease and efficiency of (glulam), cross laminated timber (CLT), and a A construction, design versatility, and variety of structural composite lumber products EARN 0.1 ICC sustainability—as well as its beauty and the are enabling increased dimensional stability and CONTINUING innate appeal of nature and natural materials. strength, and greater long-span capabilities. EDUCATION UNIT Innovative new technologies and building These innovations are leading to taller, highly (CEU) systems are also leading to the increased use of innovative wood buildings. Examples include the Learning Objectives wood as a structural material, not only in houses, eight-story Limnologen in Sweden, the nine-story After reading this article, you should be able schools, and other traditional applications, but in Stadthaus in the UK, and the 10-story Forté in to: larger, taller, and more visionary wood buildings. Australia, currently the world’s tallest modern 1. Analyze factors contributing to the long But even as the use of wood is expanding, one residential wood building.1 Although durability is term durability of wood buildings. significant characteristic of wood buildings important in every structure, a long future takes 2. Implement effective design strategies for is often underestimated: their durability. -
Technical Specifications Requirements for Containerized Wood Drying Kiln and Related Items
DOCUMENT TO BE USED FOR ILLIUSTRATION PURPOSES ONLY United Nations Industrial Development Organization Technical Specifications Requirements for Containerized Wood Drying Kiln and Related Items UNIDO ID: SAP130067 I. GENERAL BACKGROUND INFORMATION: The purpose of this procurement is to purchase of materials for the fabrication of a containerized wood drying kiln and related items for the implementation of UNIDO activities under its Strengthening Forestry Training Centres for Green Employment in the SADC Region project. II. THE SCOPE OF SUPPLY: UNIDO REQUIREMENTS TO BE COMPLETED BY THE INVITEE Name and Required Parameter Total Item Unit Price QTY Price Compliance / Remarks / Photo Reference Item (USD) Containerized Wood Kiln (USD) 40' Last Run Inter-Modal Shipping Container o Dry Storage Type shipping Container o Robust steel sheet construction with eight (8) reinforced ISO corner castings; o Should have a Last Conformity Certificate or equivalent of Last Trip; o Dimensional Type Definition: 40 ft. (12m x 2.4m x 2.6m) o Container Flooring Type: Plywood with a thickness of between 25mm and 30mm; o Verifiable ISO 6346 Reporting Mark 1 1 o Approx weight 2000kg o Minimum inside dimension: H: 2359mm W: 2330mm o Constructed with Forklift Slots/Pockets between bottom/floor steel cross members o Length: 5867mm o Door inside height/width: 2261mm/2286mm o Doors open at end with secure closing system, robust hinges, and easy lock design o Max stacking rating: three (3) containers high DOCUMENT TO BE USED FOR ILLIUSTRATION PURPOSES ONLY Foam Board