Pump Control Systems
Total Page:16
File Type:pdf, Size:1020Kb
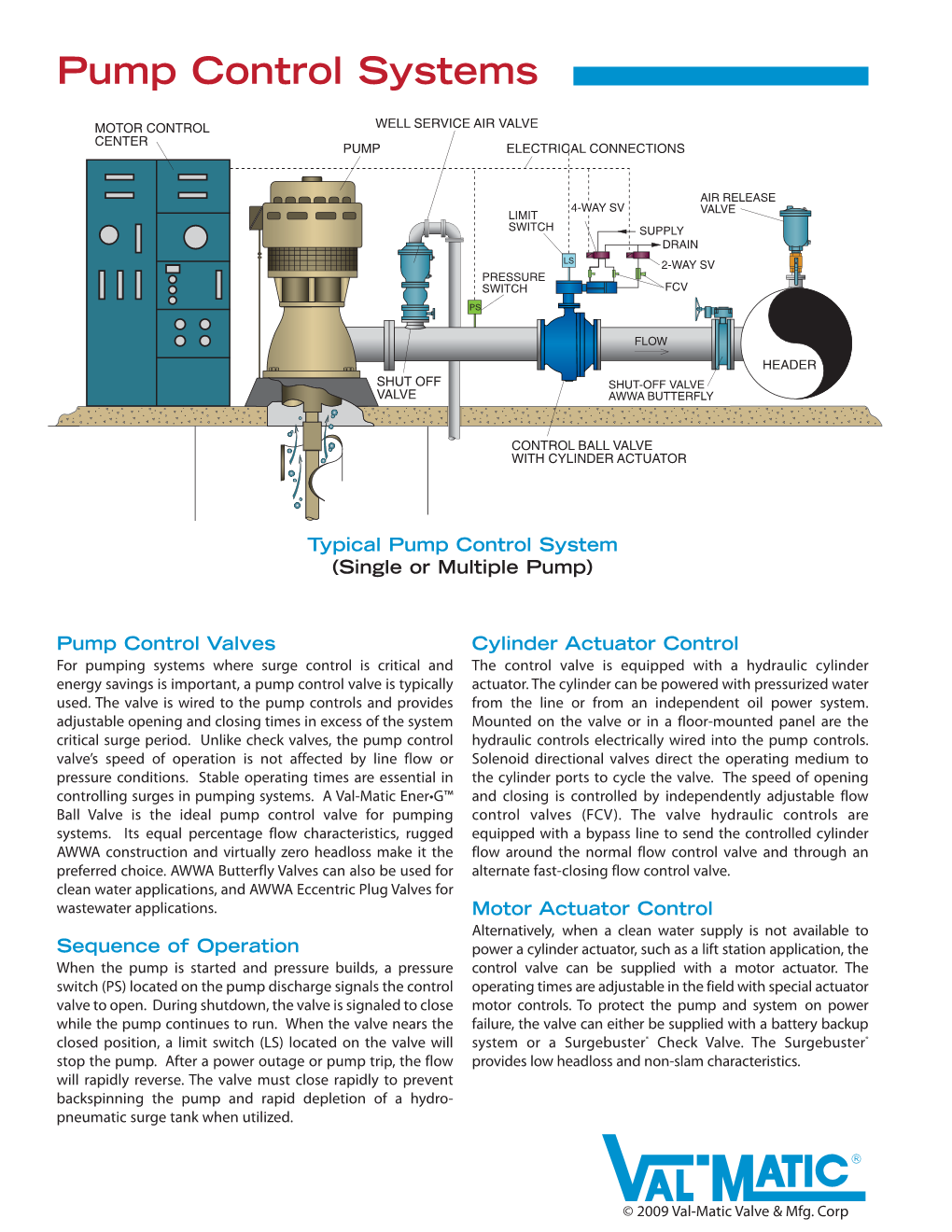
Load more
Recommended publications
-
Automatic Flow Control Valves 6
Automatic Flow Form No.: F143.6 Control Valves Date: 8.06 Guide Specifications Supersedes: F143.5 5.99 Guide Specifications A. Manufacturers: 5. For 2 1/2” and larger flanged connections: 1. Flow Design, Inc., Autoflow or approved equal. Ductile-iron body suitable for mounting wafer Models YR, AC, MC, WG, WS, WB, WR style between standard 150# or 300# flanges. or WT. The long flange bolts and nuts shall be provided with each control valve. Flow Design Model WS B. Design: or equal. 1. The GPM for the automatic flow control valves 6. All valves shall be factory leak tested at 100 psi shall be factory set and shall automatically limit air. the rate of flow to within 5% of the specified D. Minimum ratings: GPM over at least 95 percent of the control 1. 1/2” through 2” pipe size: 400 PSIG at 250°F range. 2. 2 1/2” through 14” pipe size: 600 PSIG at 250°F 2. For 1/2” - 2“, the flow cartridge shall be 3. 16” through 30” pipe size: 250 PSIG at 250°F removable from the Y- body housing without the use of special tools to provide access for E. Flow Verification (choose one): regulator change-out, inspection and cleaning 1. The differential pressure across the Automatic without breaking the main piping. (Access shall Flow Control Valve shall be measured for flow be similar to that provided for removal of a verification and to determine the amount of Y-strainer screen). system over heading or under pumping. 3. PUMP HEAD REQUIREMENT: 2. -
Hydraulic Valve Remote Control System
HYDRAULIC VALVE REMOTE CONTROL SYSTEM OVERVIEW Nordic Flow Control’s compact design for our Hydraulic Valve Remote Control Systems does not compromise on power. Our systems operate at a higher torque level even with our smaller actuators. Submerged applications are available, and maintenance is possible even during operation. By having a hand pump in a deck box with solenoid valves, manual operations are now possible. Our Hydraulic Valve Remote Control Systems are tried and tested in the harshest conditions. The system consists of the hydraulic actuator, a power unit, solenoid valve cabinet, and the control station with operating system. Our actuators and control systems are able to match and operate valves with no limitations. BENEFITS • Able to operate bigger size valves with smaller actuators • Able to use for submerged applications • Cost efficient • Reliable • Able to operate at hazardous areas • Simplicity of design and control Nordic Flow Control Valve Remote Control Systems 1 COMPONENTS ACTUATORS Nordic Flow Control’s actuators are manufactured using sophisticated machinery in our own production plant. They convert hydraulic energy directly into a mechanical rotating movement by using the rack and pinion principle, elimi- nating cost from intensive servicing, maintenance and the sensitivity of transmission elements. Our actuators are created for durability, performance and cost effectiveness. Our new NRA series actuators are now more compact and provide higher torque at even smaller sizes. They have a longer life span, with higher efficiency. Polymer bearings for smaller actuators and ball bearings for bigger actuators are used to reduce friction between the parts. Mounting is according to ISO5211 standards, but can be customised to meet other requirements. -
UFGS 23 09 13 Instrumentation and Control Devices for HVAC
************************************************************************** USACE / NAVFAC / AFCEC / NASA UFGS-23 09 13 (November 2015) Change 2 - 05/21 ------------------------------------ Preparing Activity: USACE Superseding UFGS-23 09 23 (May 2011) UFGS-23 09 23.13 20 (August 2009) UNIFIED FACILITIES GUIDE SPECIFICATIONS References are in agreement with UMRL dated July 2021 ************************************************************************** SECTION TABLE OF CONTENTS DIVISION 23 - HEATING, VENTILATING, AND AIR CONDITIONING (HVAC) SECTION 23 09 13 INSTRUMENTATION AND CONTROL DEVICES FOR HVAC 11/15, CHG 2: 05/21 PART 1 GENERAL 1.1 SUMMARY 1.1.1 Verification of Dimensions 1.1.2 Drawings 1.2 RELATED SECTIONS 1.3 REFERENCES 1.4 SUBMITTALS 1.5 DELIVERY AND STORAGE 1.6 INPUT MEASUREMENT ACCURACY 1.7 SUBCONTRACTOR SPECIAL REQUIREMENTS PART 2 PRODUCTS 2.1 EQUIPMENT 2.1.1 General Requirements 2.1.2 Operation Environment Requirements 2.1.2.1 Pressure 2.1.2.2 Vibration 2.1.2.3 Temperature 2.1.2.4 Humidity 2.2 WEATHERSHIELDS 2.3 TUBING 2.3.1 Copper 2.3.2 Stainless Steel 2.3.3 Plastic 2.3.4 Polyethylene Tubing 2.4 WIRE AND CABLE 2.4.1 Terminal Blocks 2.4.2 Control Wiring for Binary Signals 2.4.3 Control Wiring for Analog Signals 2.4.4 Power Wiring for Control Devices 2.4.5 Transformers 2.5 AUTOMATIC CONTROL VALVES SECTION 23 09 13 Page 1 2.5.1 Valve Type 2.5.1.1 Liquid Service 150 Degrees F or Less 2.5.1.2 Liquid Service Above 150 Degrees F 2.5.1.3 Steam Service 2.5.2 Valve Flow Coefficient and Flow Characteristic 2.5.2.1 Two-Way Modulating -
Capillary Tube Thermal Mass Flow Meters & Controllers: a User's Guide
Capillary Tube Thermal Mass Flow Meters & Controllers A User’s Guide By John G. Olin, Ph.D., Sierra Instruments, Inc. / 9.24.13 A SIERRA WHITEPAPER www.sierrainstruments.com NORTH AMERICA 5 Harris Court, Building L / Monterey, CA 93940 / USA 800.866.0200 / 831.373.0200 / fx 831.373.4402 EUROPE Bijlmansweid2 / 1934RE Egmond aan den Hoef The Netherlands +31 72 5071400 / fx +31 72 5071401 ASIA-PACIFIC Second Floor Building 5 / Senpu Industrial Park 25 Hangdu Road Hangtou Town / Pu Dong New District Shanghai, P.R. China Post Code 201316 +8621 5879 8521/22 / fx +8621 5879 8586 © 2013 Sierra Instruments, Inc. / All rights reserved. A USER’S GUIDE TO CAPILLARY TUBE THERMAL MASS FLOW METERS AND CONTROLLERS John G. Olin(1) Abstract Capillary tube thermal mass flow meters directly measure the mass flow rate of clean gases and gas mixtures in lower flow ranges. A capillary tube thermal mass flow controller adds an integrally mounted flow control valve to the flow body of the mass flow meter and both monitors the mass flow rate and controls it to be equal to a set-point value selected by the user. This paper describes capillary tube mass flow meters and controllers for use in general purpose industrial and laboratory applications and in the fabrication of semiconductor devices. It provides a detailed description of the major components-- -flow body, flow conditioner, bypass, capillary sensor tube, control valve, and electronics. Flow ranges and specifications for which this technology is best suited are presented. The paper explains the principle of operation; describes gas conversion factors that provide Fig. -
Flow Control Valves
Flow Control Valves Overview Needle Valves Flow Control Valves DV, DVE & DVP Series (see page 43) DRV & DRVP Series (see page 47) Pressure Compensated Flow Control Valves Check Valves SRVR Series (see page 51) RV & RVP Series (see page 53) Stainless Steel Flow Control Valves DV, DRV & RV Series (see page 55) 41 INNOVATIVE FLUID POWER Flow Control Valves Flow Control Valve Design Features and Options Color 1 2 Coded 3 4 Safety Screw Flow 5 and Spindle Indicator Knob Threaded Spindle Locking Housing for Panel Set Screw Mounting Kit Slotted BA Spindle NPT, SAE or BSPP Ports Guided Poppet Introduction Product Features Our complete line of flow control valves are designed and • Phosphate coated steel valve body manufactured by our ISO 9001 certified FLUTEC Division. • FPM (Fluoroelastomer) seals • Slotted control spindle for precise and linear flow adjustments Description • Exclusive safety spindle design • Color coded spindle for accurate flow control • The HYDAC family of flow control valves permit safe, simple and • Guided poppets for smoother, chatter free operation repeatable control of hydraulic fluids at operating pressures to 5000 psi. • The standard slotted control spindle allows for a wide range Available Options of infinitely variable flow adjustments with excellent flow • Panel mounting kit characteristics. • 25 and 65 PSI cracking pressure springs (7 psi standard) • Precise adjustment of flow is achieved by a micrometer style • Zinc Plated Body. Consult HYDAC for price and delivery adjustment knob featuring a color coded flow indicator for accurate, easy-to read visual flow reference. • Design modifications and special materials are available for corrosive fluids such as phosphate ester, acids and caustics. -
Hydraulic Accessories Valves, Clamps & Reservoir Accessories
Hydraulic Accessories Valves, Clamps & Reservoir Accessories PN#02080105 / 01.17 / ACC1603-1753 Components, Systems and Service. All from one Company. Our fluid engineering solutions are defined by the scope and complexity of our customers’ requirements. Our products range from individually designed components in the fields of fluid engineering, hydraulics and electronics right up to complete systems for specific functions. All components and systems are conceived and designed in-house. Experienced industrial and product specialists develop innovative products and efficient solutions for high-quality, cost-effective production. Throughout the globe, our production facilities share one common goal: quality. We take great pride in both our products and solutions. Industries and Applications Pulp & Paper Mobile Hydraulics Wind Power Power Industry Agriculture Off Shore/Marine Industrial PN#02080105 / 01.17 / ACC1603-1753 TABLE OF CONTENTS Section: Valves Overview - A-1; Quick Reference Guide - A-2; Compatibility List - A-4; Materials Summary - A-7 A High Pressure Ball Valves Standard Ball Valve Design Features and Options [KHB, KHM, KHP, KHB3K] - A1-2; Engineering Data - A1-3; 2-way Ball Valve with SAE & NPT Connections [KHB & KHM] - A1-4; 2-way Ball Valves with BSP & Metric Tube Connections [KHB & KHM] - A1-6; 2-way Ball Valves with Split Flange Connections [KHB & KHM] - A1-8; Direct Mount SAE Flange 1/2” to 2” [KHF3/6] - A1-10; A1 Direct Mount SAE Flange 2 1/2” to 4” [KHF3] - A1-11; 2-way Manifold Mounted Ball Valves [KHP] - A1-12; 3 Piece -
Armstrong Steam
Distributed by: M&M Control Service, Inc. www.mmcontrol.com/Armstrong.php 800-876-0036 847-356-0566 Bulletin ALW-200-D Thermostatic, Electronic and Digital Water Temperature Control Solutions Distributed by: M&M Control Service, Inc. www.mmcontrol.com/Armstrong.php 800-876-0036 847-356-0566 Introduction Armstrong offers both a complete system and a modular component solution to mixed water temperature control across the entire Institutional and Industrial hot water distribution network. From mechanical room based digital recirculation system control with integral BAS interface to traditional thermostatic control at distribution points within the system to revolutionary digital point of use control solutions, Armstrong products place user safety and legionella risk reduction at the forefront of hot water system design operation and maintenance. Armstrong defines its range of mixed water temperature controls within the following classifications: • Water Temperature Control-Single Point of Use-Thermostatic • Water Temperature Control-Single Point of Use-Digital • Water Temperature Control-Groups of Fixtures-Thermostatic • Water Temperature Control-Recirculation Systems-Thermostatic • Water Temperature Control-Recirculation Systems-Electronic • Water Temperature Control-Recirculation Systems-Digital • Water Temperature Control-Emergency Fixtures-Thermostatic Individual product data sheets, written specifications, certified submittal drawings, IOM guides, online installation site tours and other product and system support information and documentation can be located at Armstrong’s web site. Please visit www.armstronginternational.com. Table of Contents Water Temperature Control - Single Point of Use . .4-17 Thermostatic Rada 110 . .6 Rada 215 . .7 Digital BrainWave™ DMV-1 for Lavatory . .10-11 BrainWave™ DMV-2 for Individual Shower . .12-13 Brain Wave™ DMV-3 for Individual Bath . -
TECHNICAL DATA CONTROL ASSEMBLY (Maximum 250 PSI WWP)
July 23, 2001 533 a MODEL A-1 SPEED TECHNICAL DATA CONTROL ASSEMBLY (Maximum 250 PSI WWP) 1. PRODUCT NAME Water Working Pressure Rating: VIKING MODEL A-1 For use up to 250 PSIG (1 724 SPEED CONTROL ASSEMBLY kPa) Part No. 08780 Galvanized Factory Assembled Part No. 11181 Brass Shipping Weight: Approximately 6.8 Part No. 11192 Stainless Steel lbs (3,1 kg) For use with Viking Deluge Valves Material Specifications: Refer to and Flow Control Valves Chart in Figure 2 2. MANUFACTURED 5. OPERATION (Refer to Figure 2.) THE VIKING CORPORATION 210 N. Industrial Park Road The Viking Model A-1 Speed Con- Hastings, MI 49058 U.S.A. trol Assembly consists of a Telephone: (616) 945-9501 pre-assembled galvanized or brass (877) 384-5464 pipe loop for installation between Fax: (616) 945-9599 the priming chamber and trim of the e-mail: [email protected] Viking Deluge or Flow Control Valve used. 3. PRODUCT DESCRIPTION One leg of the loop is equipped with The Viking Speed Control Assembly a check valve to allow flow into the provides adjustment of the opening priming chamber only. The other leg speed of Viking Deluge Valves, and is equipped with a check valve that adjustment of both the opening and only allows flow out of the priming closing speed of Viking Flow Control chamber. Valves. Water hammer, which may Speed Control Assembly result from the opening of a Deluge Both legs are equipped with a spe- Figure 1 Valve or opening and closing of a cial needle valve to adjust flow into Flow Control Valve, may be reduced or out of the priming chamber. -
Control & Automation Valves Q Profix.FH11
Control & Automation Valves Q_profix.FH11 Tue Mar 11 15:02:55 2008 Page 1 C M Y CM MY CY CMY K BULLETIN B-412 INCH CONTROL & AUTOMATION Composite Control & Automation Valves Q_profix.FH11 Tue Mar 11 15:02:55 2008 Page 2 C M Y CM MY CY CMY K CONTROL & AUTOMATION Introduction Habonim has extended its range to meet industrial demands for flow control systems that are accurate, flexible, cost efficient and maintenance friendly. Many complex requirements come into play when designing flow process operations, and no other valve design available today offers a more cost effective solution without compromising flow control functionality. ProfiX provides excellent performance, even in the harshest environments, offering a compact lightweight design solution; step-less characterized control of pressure and flow for fast response times, wide rangeability and bubble- tight shutoff for increased valve longevity even in the most demanding conditions. Critical features include high pressure drop capacity with straight- through flow, high Cv, and large exhaust capacity with added design features for ease of maintenance and zero backlash. Habonim provides world-class technical expertise in design, tech-support, sales, project management, QA, and every phase of manufacturing. All Habonim products are comprised of quality components throughout, to insure reliability, stability and design flexibility for a range of applications including; power generation, oil and gas production, petrochemical, chemical, pulp and paper, medical and pharmaceutical, and general industrial. 2 CONTROL & AUTOMATION Composite Control & Automation Valves Q_profix.FH11 Tue Mar 11 15:02:55 2008 Page 3 C M Y CM MY CY CMY K V-Port & V-Ball Valve Solutions to resist abrasion and galling. -
Flow Control: Thermoplastic Valves
Flow Control: Thermoplastic Valves | Actuation & Controls | Strainers | Filters | Instrumentation | Pumps | Bulkhead Fittings & Tank Accessories Flow Control For more than 80 years, Hayward Flow Control’s thermoplastic fluid handling products and solutions have proven to excel in the harshest environments. Thousands of customers worldwide have installed our products in aggressive and corrosive systems, as well as delicate life support systems where the strictest chemical balance is required. We understand the rigorous demands of industrial piping and are committed to offering advantageous products for your application that will keep your systems working. Hayward Flow Control has solutions ready for the demanding needs of mineral extraction. Our products and solutions are designed and suitable for use in key piping systems and applications such as: • Electro-winning solutions • Chemical handling, production and distribution • Mineral extraction • Water treatment, transmission and disposal Hayward Flow Control products carry an industry leading, full two-year warranty. An an ISO 9001:2015 certified manufacturing company, we strive for the highest quality product for use in a wide range of demanding applications. Buy American 2 TBH Series True Union Ball Valves 1/2” to 2” DN8-DN50 PVC, CPVC MATERIALS KEY FEATURES OPTIONS 2 1/2” to 6” DN65-DN150 PVC, CPVC* • System2™ Sealing Technology provides • Z-Ball - Drilled Ball for Sodium *Available Late 2019 longer cycle life Hypochlorite applications with MINING MARKET GUIDE PVC • 250 PSI / 16 Bar, -
Dome-Loaded Back Pressure Regulator Improves Mass Flow Controller Calibration Process
Dome‐loaded Back Pressure Regulator improves Mass Flow Controller calibration process by Jeff Jennings, PE Thermal mass flow meters and mass flow controllers are widely used throughout laboratories and industry in situations requiring precise control of gas flow rate.. As shown in the Figure 2, mass flow controllers are often used to supply inert and other gases into laboratory reactors and vessels. Fig 1: Thermal mass flow controller In order to calibrate these devices precisely, it is accepted good practice to showing flow control valve on outlet control the outlet pressure of the devices in the same range as the application pressure. This article describes how a sensitive dome‐loaded back pressure regulator can improve the quality and efficiency of the MFC and MFM calibration process. Thermal mass flow meters Thermal mass flow meters (MFM’s) are the dominant method Fig. 2: Mass flow controllers supplying multiple gases into of measuring gas flow in laboratory and small scale a research reactor. The back pressure regulator is used applications. MFMs sense mass flow by measuring the to control the overall reaction pressure. amount of heat transferred by the gas flow in a thin hot tube in the gas stream. They can use either a constant temperature method (variable power input), or a constant power method (variable temperature). For all but the smallest MFMs, the flow sensor is situated in a small side stream of the overall stream flow, and a laminar flow divider is typically used to provide reliable scaling from the small side‐stream flow sensor to the overall flow meter stream (see Fig. -
Valves & Flow Controls
$5.00$1.50 U.S.U.S. valves & ow controls Quality Assurance Lab Our trained Quality Assurance Personnel follow a rigid inspection program to ensure that our fittings meet or surpass the strictest requirements of SAE. Engineering Optical Comparator Pressure Test Stand We design our products to the strictest requirements of SAE, and improve our designs as we solve problems or reflect the latest changes in SAE design. We can also design custom fittings to fit your needs. Precision Instruments All equipment is calibrated at regularly scheduled intervals. Records and instrument serial numbers are kept on file to guarantee the accuracy of every inspection. Our Glastonbury Southern “The Corrective Preventive Gage trained personnel Action program you’ve setup use only certified instru- at Pressure Connections is mentation and equipment top notch. It is one of the in the quality process best I’ve seen.” giving you leak free perfor- ISO 9001:2000 ISO Auditor mance. Audit W.J. Davis Quality Assurance Systems Inc. Coordinate Measuring Machine (CMM) Only a CMM can verify that “How can an OFS fitting leak?” an OFS groove is manufac- The Answer: Grooves that are too small or too tured to exact SAE J1453 large don’t apply the correct pressure on the O-ring specifications. We use a to seal properly. state-of-the-art CMM to measure the latest OFS “dovetail” and standard OFS groove designs. Quality Symbol Quality Assurance Points Coordinate Measuring Machine - CMM Male O-Ring Face Seal Groove Diameters: The CMM is the only way to identify and discard out of spec OFS grooves that To Guarantee the Accuracy will not give the correct Fill & Squeeze (1) for the O-ring to seal properly.