Cimdata Cpdm Late-Breaking News
Total Page:16
File Type:pdf, Size:1020Kb
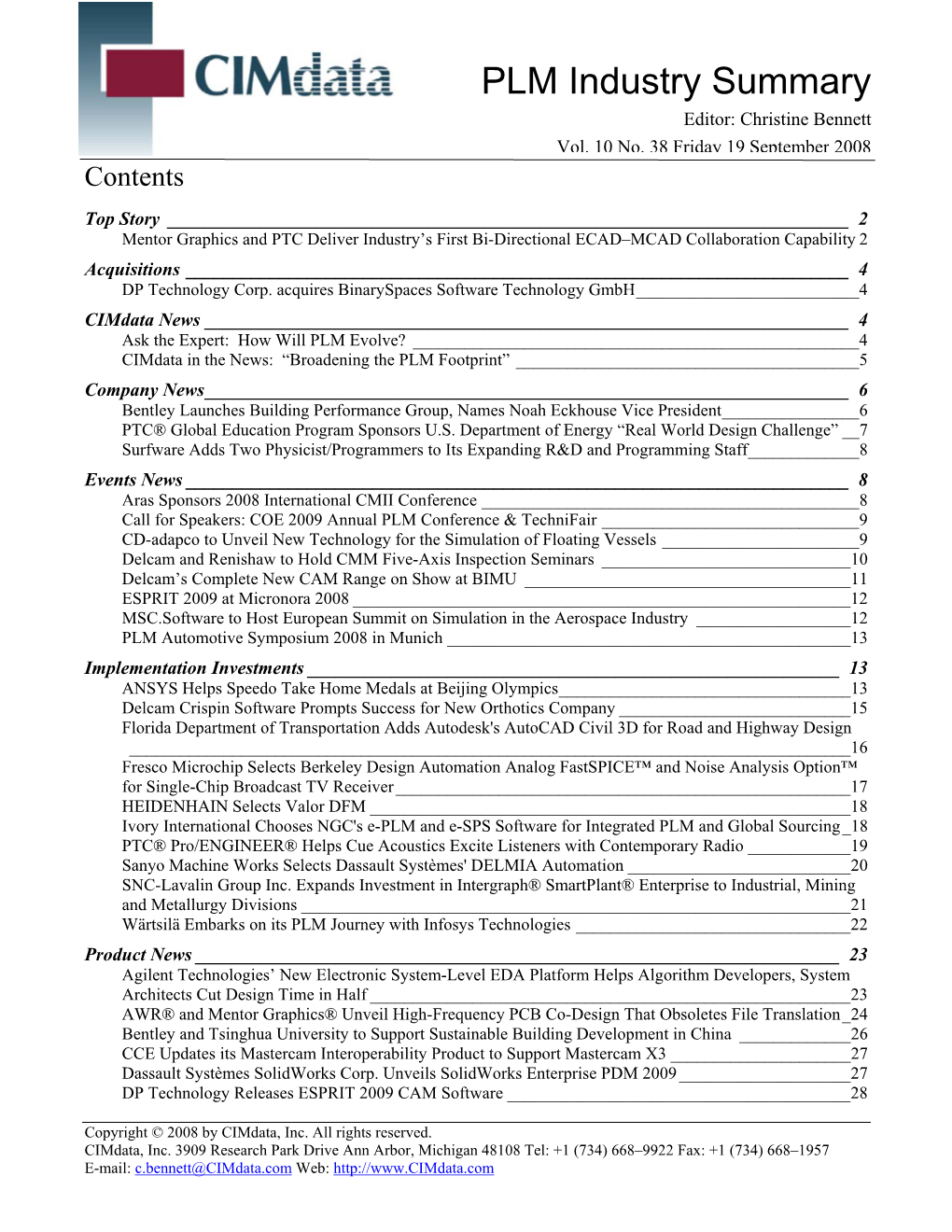
Load more
Recommended publications
-
4 Chapter Four Modelling of Lspmsm Using Jmag ( Fem
© ABDULAZIZ SALEH MILHEM 2017 iii This Thesis is dedicated to The soul of my Father My Dear Mother My Wife My Children Shahd, Omar and Noor My Holy Homeland Palestine iv ACKNOWLEDGMENTS All praise and glory to Allah the most merciful, the most beneficent, who gave me the health, strength, and courage to complete my Master’s degree. I would like to express my deep appreciation to my advisor Prof. Zakariya Al-Hamouz for giving me the opportunity to become one of his students. I thank him for his efficient and constant support, help, motivation, and immense knowledge. His precious advices and thorough guidance played a critical role in completing this thesis. I also would like to extend my appreciation to my dissertation committee members Prof. Mohammed Abido and Prof. Ibrahim El-Amin for their insightful comments, support, and profitable questions which incented me to enhance my work. I would like to thank our research group members supervised by Prof. Zakariya Al- Hamouz, they include Mr. Luqman Marraba for his massive support and help, Mr. Khalid Baradiah and Mr. Ibrahim Hussein. I am very grateful to Mr. Osama Hussain the General Manager and Mr. Samir Al-Hourani the Procurement Manager from Al-Osais Contracting Co. for their continuous support and understanding during the study period. I am thankful to the King Fahd University of Petroleum and Minerals (KFUPM) for providing me with the research facilities, precious resources and an environment conducive to intellectual growth for my master research v TABLE OF CONTENTS ACKNOWLEDGMENTS ........................................................................................................ V TABLE OF CONTENTS ........................................................................................................ VI LIST OF TABLES.................................................................................................................. -
Comparison of Main Magnetic Force Computation Methods for Noise and Vibration Assessment in Electrical Machines
JOURNAL OF LATEX CLASS FILES, VOL. 14, NO. 8, SEPTEMBER 2017 1 Comparison of main magnetic force computation methods for noise and vibration assessment in electrical machines Raphael¨ PILE13, Emile DEVILLERS23, Jean LE BESNERAIS3 1 Universite´ de Toulouse, UPS, INSA, INP, ISAE, UT1, UTM, LAAS, ITAV, F-31077 Toulouse Cedex 4, France 2 L2EP, Ecole Centrale de Lille, Villeneuve d’Ascq 59651, France 3 EOMYS ENGINEERING, Lille-Hellemmes 59260, France (www.eomys.com) In the vibro-acoustic analysis of electrical machines, the Maxwell Tensor in the air-gap is widely used to compute the magnetic forces applying on the stator. In this paper, the Maxwell magnetic forces experienced by each tooth are compared with different calculation methods such as the Virtual Work Principle based nodal forces (VWP) or the Maxwell Tensor magnetic pressure (MT) following the stator surface. Moreover, the paper focuses on a Surface Permanent Magnet Synchronous Machine (SPMSM). Firstly, the magnetic saturation in iron cores is neglected (linear B-H curve). The saturation effect will be considered in a second part. Homogeneous media are considered and all simulations are performed in 2D. The technique of equivalent force per tooth is justified by finding similar resultant force harmonics between VWP and MT in the linear case for the particular topology of this paper. The link between slot’s magnetic flux and tangential force harmonics is also highlighted. The results of the saturated case are provided at the end of the paper. Index Terms—Electromagnetic forces, Maxwell Tensor, Virtual Work Principle, Electrical Machines. I. INTRODUCTION TABLE I MAGNETO-MECHANICAL COUPLING AMONG SOFTWARE FOR N electrical machines, the study of noise and vibrations due VIBRO-ACOUSTIC I to magnetic forces first requires the accurate calculation of EM Soft Struct. -
Gpu-Accelerated Applications
GPU-ACCELERATED APPLICATIONS Test Drive the World’s Fastest Accelerator – Free! Take the GPU Test Drive, a free and easy way to experience accelerated computing on GPUs. You can run your own application or try one of the preloaded ones, all running on a remote cluster. Try it today. www.nvidia.com/gputestdrive GPU-ACCELERATED APPLICATIONS Accelerated computing has revolutionized a broad range of industries with over five hundred applications optimized for GPUs to help you accelerate your work. CONTENTS 1 Computational Finance 2 Climate, Weather and Ocean Modeling 2 Data Science and Analytics 4 Deep Learning and Machine Learning 7 Federal, Defense and Intelligence 8 Manufacturing/AEC: CAD and CAE COMPUTATIONAL FLUID DYNAMICS COMPUTATIONAL STRUCTURAL MECHANICS DESIGN AND VISUALIZATION ELECTRONIC DESIGN AUTOMATION 15 Media and Entertainment ANIMATION, MODELING AND RENDERING COLOR CORRECTION AND GRAIN MANAGEMENT COMPOSITING, FINISHING AND EFFECTS EDITING ENCODING AND DIGITAL DISTRIBUTION ON-AIR GRAPHICS ON-SET, REVIEW AND STEREO TOOLS WEATHER GRAPHICS 22 Medical Imaging 22 Oil and Gas 23 Research: Higher Education and Supercomputing COMPUTATIONAL CHEMISTRY AND BIOLOGY NUMERICAL ANALYTICS PHYSICS SCIENTIFIC VISUALIZATION 33 Safety & Security 35 Tools and Management Computational Finance APPLICATION NAME COMPANY/DEVELOPER PRODUCT DESCRIPTION SUPPORTED FEATURES GPU SCALING Accelerated Elsen Secure, accessible, and accelerated back- * Web-like API with Native bindings for Multi-GPU Computing Engine testing, scenario analysis, risk analytics Python, R, Scala, C Single Node and real-time trading designed for easy * Custom models and data streams are integration and rapid development. easy to add Adaptiv Analytics SunGard A flexible and extensible engine for fast * Existing models code in C# supported Multi-GPU calculations of a wide variety of pricing transparently, with minimal code Single Node and risk measures on a broad range of changes asset classes and derivatives. -
Loads, Load Factors and Load Combinations
Overall Outline 1000. Introduction 4000. Federal Regulations, Guides, and Reports Training Course on 3000. Site Investigation Civil/Structural Codes and Inspection 4000. Loads, Load Factors, and Load Combinations 5000. Concrete Structures and Construction 6000. Steel Structures and Construction 7000. General Construction Methods BMA Engineering, Inc. 8000. Exams and Course Evaluation 9000. References and Sources BMA Engineering, Inc. – 4000 1 BMA Engineering, Inc. – 4000 2 4000. Loads, Load Factors, and Load Scope: Primary Documents Covered Combinations • Objective and Scope • Minimum Design Loads for Buildings and – Introduce loads, load factors, and load Other Structures [ASCE Standard 7‐05] combinations for nuclear‐related civil & structural •Seismic Analysis of Safety‐Related Nuclear design and construction Structures and Commentary [ASCE – Present and discuss Standard 4‐98] • Types of loads and their computational principles • Load factors •Design Loads on Structures During • Load combinations Construction [ASCE Standard 37‐02] • Focus on seismic loads • Computer aided analysis and design (brief) BMA Engineering, Inc. – 4000 3 BMA Engineering, Inc. – 4000 4 Load Types (ASCE 7‐05) Load Types (ASCE 7‐05) • D = dead load • Lr = roof live load • Di = weight of ice • R = rain load • E = earthquake load • S = snow load • F = load due to fluids with well‐defined pressures and • T = self‐straining force maximum heights • W = wind load • F = flood load a • Wi = wind‐on‐ice loads • H = ldload due to lllateral earth pressure, ground water pressure, -
4.1 Standard Interfaces and Exchange Formats – Baseline
D4.1: Standard interfaces and exchange formats – baseline Author, company: Marc Eheim, IILS Jürgen Freund, University of Stuttgart Roland Weil, IILS Stephan Rudolph, University of Stuttgart Kjell Bentsson, Jotne Maarten Nelissen, KE-works Erwin Moerland, DLR Roberto d’Ippolito, NOESIS Martin Motzer, DRÄXLMAIER Kevin van Hoogdalem, KE-works Jochen Haenisch, Jotne Version: 1.02 Date: August 14, 2015 Status: Final / Released Confidentiality: Public Copyright IDEALISM Consortium 2/36 Document: Standard interfaces and exchange formats – baseline Version: 1.02 Date: August 14, 2015 CHANGE LOG Vers. Date Author Description 0.1 16.06.2015 Marc Eheim Initial Document 0.2 18.06.2015 Marc Eheim Added thoughts of Freund (U of Stuttgart) 0.3 19.06.2015 Marc Eheim Added chapter 3 contributed by Weil (IILS) 0.4 22.06.2015 Stephan Rudolph Major rework of Sections 2.1 and 2.2 0.5 30.06.2015 Kjell Bentsson Added section 3.4 “STEP” 0.6 09.07.2015 Marc Eheim Moved chapter 3 to 4; added new chapter 3: Inventory list of used standards 0.7 10.07.2015 Marc Eheim Added conclusions chapter 0.8 10.07.2015 Maarten Nelissen Added section about BPMN 0.9 15.07.2015 Erwin Moerland Major review of chapters 1 and 2, added information on task 4.3, added DLR contribution to inventory list of used standards in chapter 3, added information concerning section 4.4 “CPACS” (*) extensions were based on version 0.5, used comparison tool of MS word to insert changes made revisions 0.6-0.8. Some revisions are therefore marked inserted by Moerland, Erwin but are made by Marc Eheim and Maarten Nelissen 0.10 17.07.2015 Roberto d’Ippolito Added section about OWL 0.11 21.07.2015 Roland Weil Revised amendments/comments by Erwin, cleaned up document, document ready for feview 0.12 23.07.2015 Roland Weil Minor changes/fixes 0.13 24.07.2015 Martin Motzer Review 0.14 27.07.2015 Kevin van Hoogdalem Review 0.15 28.07.2015 Roland Weil Solved major issues of reviews 0.16 30.07.2015 Jochen Haenisch Revised all sections related to STEP and Jotne. -
FEA Newsletter April 2017
Volume 6, Issue 04, April 2017 www.feainformation.com www.feaiej.com www.feapublications.com T. Yasuki - Received The Arnold W. Siegel International Transportation Safety Award New features of 3D adaptivity W. Hu New Feature: Defining Hardening Curve X. Zhu, L. Zhang, Y. Xiao ESI releases IC.IDO 11 Terrabyte CAE Solutions Rescale - How Cloud HPC is Changing the Predictive Engineering CAE Project Timeline FEA Information Engineering Solutions Page 1 FEA Information Inc. A publishing company founded April 2000 – published monthly since October 2000. The publication’s focus is engineering technical solutions/information. FEA Information Inc. publishes: FEA Information Engineering Solutions www.feapublications.com Contact: [email protected] FEA Information Engineering Journal www.feaiej.com Contact: [email protected] FEA Information China Engineering Solutions Simplified and Traditional Chinese To receive this publication contact [email protected] FEA Information Engineering Solutions Page 2 logo courtesy - Lancemore FEA Information Engineering Solutions Page 3 logo courtesy - Lancemore FEA Information Engineering Solutions Page 4 FEA Information News Sections 02 FEA Information Inc. Profile 03 Platinum Participants 05 TOC 06 Announcements Articles – Blogs – News 07 OASYS SHELL 08 ESI ESI IC.IDO 11, Placing Virtual Reality at the Core of Industrial Engineering 10 Terrabyte Terrabyte CAE Solution and Consulting Services 11 Predictive Predictive Engineering – LS-DYNA Training Class Offered in May 12 ETA Engineering Technology -
Vysoké Učení Technické V Brně Brno University of Technology
VYSOKÉ UČENÍ TECHNICKÉ V BRNĚ BRNO UNIVERSITY OF TECHNOLOGY FAKULTA STROJNÍHO INŽENÝRSTVÍ ÚSTAV MECHANIKY TĚLES, MECHATRONIKY A BIOMECHANIKY FACULTY OF MECHANICAL ENGINEERING INSTITUTE OF SOLID MECHANICS, MECHATRONICS AND BIOMECHANICS DEFORMAČNĚ-NAPĚŤOVÁ ANALÝZA PRUTOVÝCH SOUSTAV METODOU KONEČNÝCH PRVKŮ STRESS-STRAIN ANALYSIS OF A BAR SYSTEMS USING FINITE ELEMENT METHOD BAKALÁŘSKÁ PRÁCE BACHELOR´S THESIS AUTOR PRÁCE JÁN FODOR AUTHOR VEDOUCÍ PRÁCE Ing. TOMÁŠ NÁVRAT, Ph.D SUPERVISOR BRNO 2015 Vysoké učení technické v Brně, Fakulta strojního inženýrství Ústav mechaniky těles, mechatroniky a biomechaniky Akademický rok: 2014/2015 ZADÁNÍ BAKALÁŘSKÉ PRÁCE student(ka): Ján Fodor který/která studuje v bakalářském studijním programu obor: Základy strojního inženýrství (2341R006) Ředitel ústavu Vám v souladu se zákonem č.111/1998 o vysokých školách a se Studijním a zkušebním řádem VUT v Brně určuje následující téma bakalářské práce: Deformačně-napěťová analýza prutových soustav metodou konečných prvků v anglickém jazyce: Stress-strain analysis of a bar systems using finite element method Stručná charakteristika problematiky úkolu: Cílem práce je naprogramovat algoritmus metody konečných prvků pro řešení prutových soustav. Pro řešení primárně využít volně dostupné prostředky (Python, knihovny NumPy, SciPy, překladač Fortranu, apod.). Ověření funkčnosti realizovat výpočtem v programu ANSYS. Cíle bakalářské práce: 1. Přehled používaných MKP programů se stručným popisem jejich možností. 2. Možnost využití volně dostupných prostředků pro vědecké výpočty. 3. Naprogramovat algoritmus MKP pro prutovou soustavu. 4. Verifikovat vypočtené výsledky s výsledky získanými v programu ANSYS. Seznam odborné literatury: 1. Zienkiewicz, O., C., Taylor, R. L.: The finite element method, 5th ed., Arnold Publishers, London, 2000 2. Kolář, V., Kratochvíl, J., Leitner, F., Ženíšek, A.: Výpočet plošných a prostorových konstrukcí metodou konečných prvků, SNTL Praha, 1979 3. -
Download Download
https://doi.org/10.3311/PPee.17144 Creative Commons Attribution b |113 Periodica Polytechnica Electrical Engineering and Computer Science, 65(2), pp. 113–122, 2021 Performance Analysis of FEM Solvers on Practical Electromagnetic Problems Gergely Máté Kiss1, Jan Kaska2, Roberto André Henrique de Oliveira3, Olena Rubanenko4*, Balázs Tóth5 1 AVL List GmbH, Alte Poststraße 152, 8020 Graz, Austria 2 Department of Theory of Electrical Engineering, Faculty of Electrical Engineering, University of West Bohemia, Univerzitní 2732/8, 301 00 Pilsen, Czech Republic 3 Department of Electrical and Computer Engineering, Faculdade de Ciências e Tecnologia, New University of Lisbon, Largo da Torre, 2825-149 Caparica, Portugal 4 Research and Innovation Centre for Electrical Engineering, Faculty of Electrical Engineering, University of West Bohemia, Univerzitní 2732/8, 301 00 Pilsen, Czech Republic 5 Department of Mechanics, Institute of Applied Mechanics, University of Miskolc, Faculty of Mechanical Engineering and Informatics, Miskolc-Egyetemváros, H-3515 Miskolc, Hungary * Corresponding author, e-mail: [email protected] Received: 03 September 2020, Accepted: 02 November 2020, Published online: 25 March 2021 Abstract The paper presents a comparative analysis of different commercial and academic software. The comparison aims to examine how the integrated adaptive grid refinement methodologies can deal with challenging, electromagnetic-field related problems. For this comparison, two bench-mark problems were examined in the paper. The first example is a solution of an L-shape domain like test problem, which has a singularity at a certain point in the geometry. The second problem is an induction heated aluminum rod, which accurate solution needs to solve non-linear, coupled physical fields. -
HEAT TRANSFER in ELECTRIC MACHINES Overview of Cooling and Simulation Techniques in Electric Machines
HEAT TRANSFER IN ELECTRIC MACHINES Overview of cooling and simulation techniques in electric machines JANDAUD Pierre-Olivier LE BESNERAIS Jean 20th September 2017 www.eomys.com [email protected] 1 PRESENTATION OF EOMYS • Innovative Company created in may 2013 in Lille, North of France (1 h from Paris) • Activity: engineering consultancy / applied research • R&D Engineers in electrical engineering, vibro-acoustics, heat transfer, scientific computing • 80% of export turnover in transportation (railway, automotive, marine, aeronautics), energy (wind, hydro), home appliances, industry 2 EOMYS SERVICES & PRODUCTS • Diagnosis and problem solving including both simulation & measurements • Multi-physical design optimization of electrical systems • Technical trainings on vibroacoustics of electrical systems • MANATEE fast simulation software for the electromagnetic, vibro-acoustic and heat transfer design optimization of electric machines EOMYS can be involved both at design stage & after manufacturing of electric machines 3 WEBINAR SUMMARY • INTRODUCTION • TYPES OF COOLING TOPOLOGIES • SIMULATION TECHNIQUES • CONCLUSION 4 INTRODUCTION • Why is heat management important in an electric machine? • General introduction to Heat Transfer & Fluid Mechanics • Types of Losses 5 Why is heat management important? • Temperature levels impact directly on the lifetime of a machine • High temperature increases the fatigue of a material • Each machine has an insulation class for its windings based on the nature of the insulation material • Basic rule of thumb: -
COUPLING ENVIRONMENT Using Taitherm and STAR-CCM+
FRAUNHOFER INSTITUTE FOR ALGORITHMS AND SCIENTIFIC COMPUTING SCAI 1 2 1 Automotive thermal management COUPLING ENVIRONMENT using TAITherm and STAR-CCM+. 2 Thermal loads on a ceramic impeller – Vendor Neutral Interface for Coupled Simulation Abaqus coupled with FINE Turbo Multiphysics Modelling Computational Fluid Dynamics (CFD) Fraunhofer Institute for Algorithms • ANSYS ICEPAK and Scientific Computing SCAI MpCCI is a vendor neutral interface for co- • ANSYS Fluent simulation. MpCCI offers advanced features • FINE / Open Schloss Birlinghoven for multi-physics modelling: • FINE / Turbo 53754 Sankt Augustin, Germany • Accurate and robust neighbourhood • OpenFOAM calculation and mapping algorithms • STAR-CCM+ Contact • Various synchronisation schemes • STAR-CD Klaus Wolf • Predefined setups for typical applications Phone +49 2241 14-2557 • Open programming interface Electro Magnetic Modelling [email protected] • Quasi-Newton relaxation method • ANSYS Emag www.mpcci.de for fluid-structure interaction (FSI) • FLUX applications with incompressible fluids, • JMAG Distributed by moving walls and light solids scapos AG • FSI coupling with rotating parts modelled Radiation Phone +49 2241 14-2819 in different reference frames RadTherm / TAITherm www.scapos.com System Models www.scai.fraunhofer.de / mp Supported Codes • Flowmaster / FloMASTER • MATLAB Structural Analysis • MSC.Adams • Abaqus • SIMPACK MpCCI • ANSYS Mechanical • FMI / EAS-Master (on request) CouplingEnvironment • MSC.Nastran • MSC.Marc 1 2 1 Vehicle dynamic dimulation using Abaqus and MSC.Adams. 2 Electric arc running in a busbar system (ANSYS Emag & ANSYS Fluent). Aeroelasticity and Fluid-Structure-Interaction Wading Simulation for Off-Road Vehicles Vehicle wading refers to situations where vehicles traverse through Wing and Spoiler Design water at different speed. One of the major challenge is computing The deformation and dynamic fl utter of aircraft wings or racecar the inertial fi eld of the vehicle while wading. -
JMAG GPU Solution for Electromechanical Design | GTC
× JMAG Powered by GPU: A Novel Solution for Electromechanical Design March 2013 David Farnia JSOL Corporation [email protected] Copyright © 2012 JSOL Corp. All Rights Reserved http://www.jmag-international.com/ 0 Contents × What is JMAG? Electromagnetic Solver vs Structural Solver Customer Example Multiple GPUs vs CPUs Future JMAG Development Copyright © 2012 JSOL Corp. All Rights Reserved http://www.jmag-international.com/ 1 What is JMAG? × JMAG is… Finite Element Analysis (FEA) software for electromechanical design. Copyright © 2012 JSOL Corp. All Rights Reserved http://www.jmag-international.com/ 2 About JMAG and JMAG-RT × JMAG Designer is the nucleus around which all other JMAG tools function JMAG RT can generate high fidelity 1D models for system simulations based on JMAG Designer analyzes This combination of power and speed allows customers to analyze a wide range of electromagnetic phenomena . Analysis Functions Magnetic field analysis Electric field analysis Structural analysis Thermal analysis and coupled analysis Copyright © 2012 JSOL Corp. All Rights Reserved http://www.jmag-international.com/ 3 × Copyright © 2012 JSOL Corp. All Rights Reserved http://www.jmag-international.com/ 4 JMAG Group × Vietnam Europe POWERSYS New System Vietnam Co., Ltd. China IDAJ India ProSIM R&D Center Pvt. Ltd. North America Powersys Solutions Oceania Impakt-Pro Ltd. Korea EMDYNE Inc Taiwan FLOTREND CORPORATION Thailand Singapore/Malaysia JSIM Co.,Ltd PD Solutions Copyright © 2012 JSOL Corp. All Rights Reserved http://www.jmag-international.com/ 5 Technical Partners × CAD/CAE HILS Dassault Systems (CATIA, Abaqus, dSPACE SolidWorks) National Instruments (LabVIEW) PTC (Pro/E) OPAL-RT LMS International (Virtual.Lab) Fujitsu Altair Engineering (AcuSolve) Toyota Technical Development Co. -
2014 09 2014年9月号 Jmagのマルチフィジックス解析への取り組み 特集
JMAG Newsletter 2014年9月号 Simulation Technology for Electromechanical Design http://www.jmag-international.com 目次 [1] ソリューション JMAGのマルチフィジックス解析への取り組み [2] ソリューション 電磁弁解析ソリューション [3] WEB JMAG動画による機能紹介 [4] JMAGを100%使いこなそう よくある問い合わせの中から [5] イベント情報 - JMAGユーザー会in Germany 開催案内 - - 2014年9月~10月のイベント紹介 - - JMAGイチオシセミナー紹介 - - 2014年6月~8月のイベントレポート - [6] 定期開催セミナーの御案内 エンジニアリングビジネス事業部 〒104-0053 東京都中央区晴海2丁目5番24号 晴海センタービル7階 TEL : 03-5859-6020 FAX : 03-5859-6035 〒460-0002 名古屋市中区丸の内2丁目18番25号 丸の内KSビル17階 TEL : 052-202-8181 FAX : 052-202-8172 〒550-0001 大阪市西区土佐堀2丁目2番4号 土佐堀ダイビル11階 TEL : 06-4803-5820 FAX : 06-6225-3517 [email protected] 2 JMAG Newsletter(September,2014) JMAG Newsletter 9 月号のみどころ 熱帯夜も終わりを告げ、すっかり秋めいてきた今日この頃、皆様お変わりなくお過ごしでしょうか。JMAG Newsletter 9 月号をお 送りします。 「ソリューション」では、7 月 31 日に開催したマルチフィジックスセミナーで紹介した内容とあわせて、活用事例を紹介いたしま す。 「イベント情報」では、9 月に開催する JMAG-Express ワークショップと、ここまでできる MBD のための JMAG-RT 活用セミナーを 紹介しております。モータ設計に関わる方、モデルベース開発を実施されている方はぜひ参加ください。皆様の参加をお待ちして おります。 JMAG Newsletter は、JMAG をご利用中の方はもちろんのこと、JMAG をまだお使いでない方々や JMAG を使い始めた方にも 読んでいただきたいと思っております。お近くに JMAG 初心者の方がいらっしゃいましたらぜひ御紹介ください。 今回も盛りだくさんの内容でお届けします。どうぞ最後まで御覧ください。 株式会社 JSOL エンジニアリングビジネス事業部 電磁場技術グループ 3 JMAG Newsletter(September,2014) ソリューション JMAG のマルチフィジックス解析への取り組み JMAG は電気機器設計のための解析高度化に応えるべく、10 年以上前から電磁界解析に加えて、熱解析、構造解析およ びそれらを組み合わせたマルチフィジックス解析の機能開発を行ってきました。近年では、他の CAE ソフトウェアとの連携解 析を行うために、多目的ファイル入出力ツールの開発および STAR-CCM+や Abaqus などとの連携解析にも力を入れていま す。本稿では、7 月 31 日に行った「電気機器設計のための構造、流体、電磁界連携ソリューションセミナー」の内容について 報告します。 はじめに マルチフィジックス解析には大きく三つのタイプがあ JMAG は 1995 年頃から、熱解析、構造解析および ります。一つは、例えば試作が困難な大型機の設計を