(12) Patent Application Publication (10) Pub. No.: US 2005/0252141 A1 Kerkar Et Al
Total Page:16
File Type:pdf, Size:1020Kb
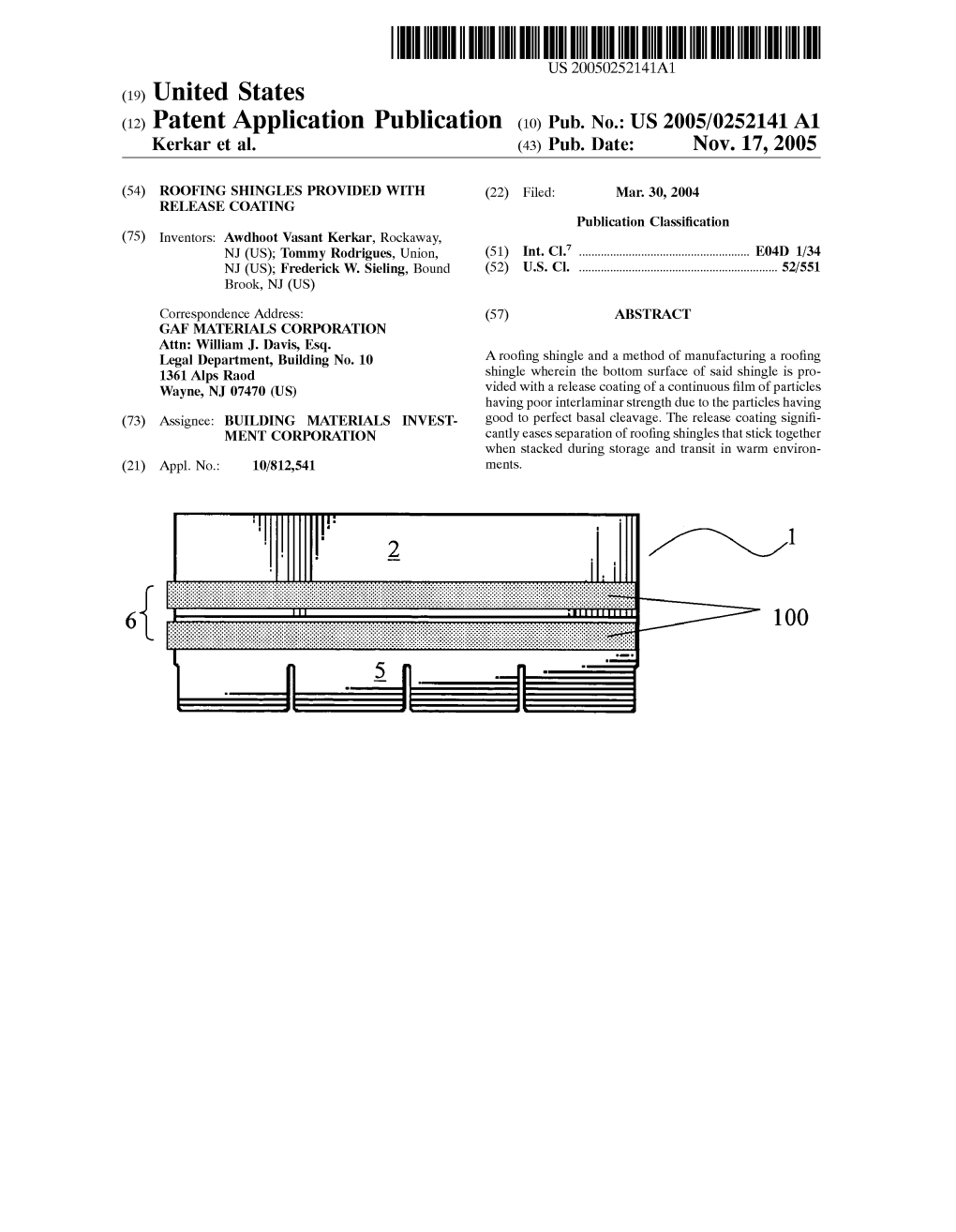
Load more
Recommended publications
-
Mineral Processing
Mineral Processing Foundations of theory and practice of minerallurgy 1st English edition JAN DRZYMALA, C. Eng., Ph.D., D.Sc. Member of the Polish Mineral Processing Society Wroclaw University of Technology 2007 Translation: J. Drzymala, A. Swatek Reviewer: A. Luszczkiewicz Published as supplied by the author ©Copyright by Jan Drzymala, Wroclaw 2007 Computer typesetting: Danuta Szyszka Cover design: Danuta Szyszka Cover photo: Sebastian Bożek Oficyna Wydawnicza Politechniki Wrocławskiej Wybrzeze Wyspianskiego 27 50-370 Wroclaw Any part of this publication can be used in any form by any means provided that the usage is acknowledged by the citation: Drzymala, J., Mineral Processing, Foundations of theory and practice of minerallurgy, Oficyna Wydawnicza PWr., 2007, www.ig.pwr.wroc.pl/minproc ISBN 978-83-7493-362-9 Contents Introduction ....................................................................................................................9 Part I Introduction to mineral processing .....................................................................13 1. From the Big Bang to mineral processing................................................................14 1.1. The formation of matter ...................................................................................14 1.2. Elementary particles.........................................................................................16 1.3. Molecules .........................................................................................................18 1.4. Solids................................................................................................................19 -
51St Annual Franklin-Sterling Gem and Mineral Show
ANNUAL Franklin - Sterling GEM & MINERAL SHOW SATURDAY & SUNDAY SEPTEMBER 29th & 30th, 2007 Sponsored By ;FRANKLIN. MI M I ; I' N 1 S F E R i U A i ■ N I I, '.--...., - Franklin, New Jersey The Fluorescent Mineral Capital Of The World STERLING HILL MINING MUSEUM 30 PLANT STREET OGDENSBURG, NJ 07439-1126 Welcome to The Sterling Hill Mine in Ogdensburg, NJ UNDERGROUND MINE TOURS • • • PASSAIC & NOBLE PIT • • COLLECTING OPEN TO THE PUBLIC • • • • During the Franklin-Sterling Hill Mineral Show, Sept. 30, 2007 • • Open Sunday, 9 AM to 3 PM • Admission: $5.00 per person, $1.50 per pound for anything taken • • • • • • STERLING HILL GARAGE SALE • • • • September 29th and 30th • Saturday and Sunday, from 11 AM to 3 PM • FRANKLIN MINE TOUR ADMISSION Citi N a. ADULT 10.00 CHILDREN (UNDER 12) 7.50 SENIOR CITIZEN (65+) 9.00 HOURS STERLING HILL OPEN 7 DAYS A WEEK MINING MUSEUM NEW YORK HOURS 10 AM TO 3 PM TOURS AT 1:00 PM DAILY OGDENSBURG & OTHER TIMES BY CHANCE I OR APPOINTMENT (:) GREEN THUMB FROM APRIL 1 TO NOV. 30 NURSERY MARCH AND DEC., WEEKENDS ONLY OTHER TIMES BY APPOINTMENT SPARTA JAN AND FEB., WEEKENDS ONLY FRANKLIN OTHER TIMES BY APPOINTMENT EXIT Nite Collecting Sat. Sept. 29th from 6-11 PM GROUP RATES AVAILABLE EXIT 34B For information call DOVER (973)209-7212 COLLECTING AVAILABLE FAX 973-209-8505 7 Days A Week, April to Nov. 10 AM to 3 PM www.sterlinghill.org MINERAL SPECIES FOUND AT FRANKLIN-STERLING HILL, NJ (Revised by FOMS Mineral List Committee September 2007) Acanthite Birnessite Cuprite Actinolite Bornite Cuprostibite Adamite Bostwickite -
Thirty-Seventh List of New Mineral Names. Part 1" A-L
Thirty-seventh list of new mineral names. Part 1" A-L A. M. CLARK Department of Mineralogy, The Natural History Museum, Cromwell Road, London SW7 5BD, UK AND V. D. C. DALTRYt Department of Geology and Mineralogy, University of Natal, Private Bag XO1, Scottsville, Pietermaritzburg 3209, South Africa THE present list is divided into two sections; the pegmatites at Mount Alluaiv, Lovozero section M-Z will follow in the next issue. Those Complex, Kola Peninsula, Russia. names representing valid species, accredited by the Na19(Ca,Mn)6(Ti,Nb)3Si26074C1.H20. Trigonal, IMA Commission on New Minerals and Mineral space group R3m, a 14.046, c 60.60 A, Z = 6. Names, are shown in bold type. Dmeas' 2.76, Dc~ac. 2.78 g/cm3, co 1.618, ~ 1.626. Named for the locality. Abenakiite-(Ce). A.M. McDonald, G.Y. Chat and Altisite. A.P. Khomyakov, G.N. Nechelyustov, G. J.D. Grice. 1994. Can. Min. 32, 843. Poudrette Ferraris and G. Ivalgi, 1994. Zap. Vses. Min. Quarry, Mont Saint-Hilaire, Quebec, Canada. Obschch., 123, 82 [Russian]. Frpm peralkaline Na26REE(SiO3)6(P04)6(C03)6(S02)O. Trigonal, pegmatites at Oleny Stream, SE Khibina alkaline a 16.018, c 19.761 A, Z = 3. Named after the massif, Kola Peninsula, Russia. Monoclinic, a Abenaki Indian tribe. 10.37, b 16.32, c 9.16 ,~, l~ 105.6 ~ Z= 2. Named Abswurmbachite. T. Reinecke, E. Tillmanns and for the chemical elements A1, Ti and Si. H.-J. Bernhardt, 1991. Neues Jahrb. Min. Abh., Ankangite. M. Xiong, Z.-S. -
Editpad Classic
Here is a text file containing the list of all species found at Franklin-Sterling Hill, the identification of the fluorescent species, a bibliography, and hotels in the area. This is a LONG text file! Best regards, Jeff W and Don H ---------------------------------------------------------------------------------------- The species list More than 340 minerals, some 80 of them fluorescent under ultraviolet light, are known from the Franklin-Sterling district -- a world's record. The current list of verified mineral species for the Franklin Sterling area is shown below. This list is updated annually and published in the bulletin for the Franklin Mineral Show, held each autumn in Franklin New Jersey. A Acanthite Actinolite Adamite Adelite Aegirine Akrochordite Albite Allactite Allanite-(Ce) Alleghanyite Almandine Analcime Anandite Anatase Andradite Anglesite Anhydrite Annabergite Anorthite Anorthoclase Antlerite Aragonite Arsenic Arseniosiderite Arsenopyrite Atacamite Augite Aurichalcite Aurorite Austinite Azurite B Bakerite Bannisterite Barite Barium-pharmacosiderite Barylite Barysilite Bassanite Baumhauerite Bementite Berthierite Bianchite Biotite Birnessite Bornite Bostwickite Brandtite Breithauptite Brochantite Brookite Brucite Bultfonteinite Bustamite C Cahnite Calcite Canavesite Carrollite Caryopilite Celestine Celsian Cerussite Chabazite Chalcocite Chalcophanite Chalcopyrite Chamosite Charlesite Chloritoid Chlorophoenicite Chondrodite Chrysocolla Cianciulliite Clinochlore Clinochrysotile Clinoclase Clinohedrite Clinohumite Clinozoisite -
JRS-16-Web.Pdf
JOURNAL OF The Russell Society Volume 16, 2013 www.russellsoc.org JOURNAL OF THE RUSSELL SOCIETY The journal of British Isles topographical mineralogy EDITOR Norman Moles School of Environment and Technology, University of Brighton, Cockcroft Building, Lewes Road, Brighton, BN2 4GJ JOURNAL MANAGER Frank Ince 78 Leconfield Road, Loughborough, Leicestershire, LE11 3SQ EDITORIAL BOARD R.E. Bevins, Cardiff, U.K. I.R. Plimer, Parkville, Australia R.S.W. Braithwaite, Manchester, U.K. M.T. Price, OUMNH, Oxford, U.K T.E. Bridges, Ovington, U.K. R.E. Starkey, Bromsgrove, U.K A. Dyer, Hoddleston, Darwin, U.K. R.F. Symes, Sidmouth, U.K. N.J. Elton, St Austell, U.K. P.A. Williams, Kingswood, Australia A.D. Hart, NHM, London, U.K. Aims and Scope: The Journal publishes refereed articles by both amateur and professional mineralogists dealing with all aspects of mineralogy relating to the British Isles. Contributions are welcome from both members and non-members of the Russell Society. Notes for contributors can be found at the back of this issue, on the Society website (www.russellsoc.org) or obtained from the Editor or Journal Manager. Subscription rates: The Journal is free to members of the Russell Society. The subscription rate for non-members is £13 (including P&P) for this volume. Enquiries should be made to the Journal Manager at the above address. Back numbers of the Journal may also be ordered through the Journal Manager. The Russell Society, named after the eminent amateur mineralogist Sir Arthur Russell (1878–1964), is a society of amateur and professional mineralogists which encourages the study, recording and conservation of mineralogical sites and material. -
(12) United States Patent (10) Patent No.: US 8,480,729 B2 Atanasoska Et Al
US008480729B2 (12) United States Patent (10) Patent No.: US 8,480,729 B2 Atanasoska et al. (45) Date of Patent: Jul. 9, 2013 (54) MEDICAL DEVICES CONTAINING SILICATE 2003/0093107 A1 5/2003 Parsonage et al. AND CARBON PARTICLES 2003. O133865 A1 7/2003 Smalley et al. 2003/0143350 A1* 7/2003 Jimenez ....................... 428,352 2003/0171257 A1 9, 2003 Stirblet al. (75) Inventors: Liliana Atanasoska, Edina, MN (US); 2003. O180472 A1 9, 2003 Zhou et al. Jan Weber, Maastrichet (NL); John 2003/0185985 A1 10, 2003 Bronikowski et al. Jianhua Chen, Plymouth, MN (US); 2003/0236514 A1 12/2003 Schwarz 2004/003.8007 A1 2/2004 Kotov et al. Daniel J. Horn, Shoreview, MN (US) 2004/OO73251 A1 4/2004 Weber 2004/O136896 A1 7/2004 Liu et al. (73) Assignee: Boston Science Scimed, Inc., Maple 2004/0266063 Al 12/2004 Montgomery et al. Grove, MN (US) 2005, OO38498 A1 2/2005 Dubrow et al. 2005, 0124976 A1* 6/2005 Devens et al. ................ 604,523 (*) Notice: Subject to any disclaimer, the term of this 2005, 0140261 A1 6, 2005 Gilad patent is extended or adjusted under 35 2005/0152891 A1* 7/2005 Toone et al. .................. 424,125 2005, 0181015 A1 8/2005 Zhong U.S.C. 154(b) by 954 days. 2005/0208100 A1 9, 2005 Weber et al. 2005/0260355 A1 11/2005 Weber et al. (21) Appl. No.: 12/205,647 2006/0051535 A1 3/2006 Arney et al. 2007/O154513 A1 7/2007 Atanasoska et al. (22) Filed: Sep. 5, 2008 2007/02O7182 A1 9, 2007 Weber 2009/0104386 A1* 4/2009 Barrera et al. -
The Picking Table Volume 34, No. 1
THE PICKIMG TABLE JOURMAL OF THE FRAMKLIM-OGDEMSBURG MIMERALOGICAL SOCIETY, IMC. VOLUME 34 MUMBER 1 SPRIMG/SUMMER 1993 The contents of The Picking Table are licensed under a Creative Commons Attribution-NonCommercial 4.0 International License. THE PRAMKLIM-OGDEMSBURG MlMERALOGICAL SOCIETY, IhC. OFFICERS AHD STAFF PRESIDENT Chester S. Lemanski, Jr. 309 Massachusetts Avenue, Browns Mills, NJ 08015 FIRST VICE PRESIDENT Lee Lowell 53 Foxtail Lane, Hamburg, NJ 07419 SECOND VICE PRESIDENT George Elling 758 Charnwood Drive, Wykoff, NJ 07481 SECRETARY Maureen E. Woods RD #2, Box 440J, Branchville, NJ 07826 TREASURER John Cianciulli 60 Alpine Road, Sussex, NJ 07461 ASSISTANT TREASURER Stephen C. Misiur 309 Fernwood Terrace, Linden, NJ 07036 SLIDE COLLECTION CUSTODIAN Edward H. Wilk 202 Boiling Springs Avenue, East Rutherford, NJ 07073 TRUSTEES COMMITTEE CHAIRPERSONS John L. Baum (1994) Auditing William J. Trost Philip P. Betancourt (1994) Banquet Maureen E. Woods Richard C. Bostwick (1993) Field Trip Edward H. Wilk, Warren Joseph Cilen (1993)) Cummings (assistant) John C.Ebner (1993) Historical John L. Baum William Kroth (1994) Identification Richard C. Bostwick Steven M. Kuitems (1993) Mineral Exchange Richard C. Bostwick Warren A. Langill (1994) Nominating Philip P. Betancourt Edward H. Wilk (1994) Program Lee Lowell Spring Swap & Sell Chester S. Lemanski, Jr. LIAISON WITH THE EASTERN FEDERATION OF MINERAL AND LAPIDARY SOCIETIES (EFMLS) Delegate Philip P. Betancourt Alternates Richard C. Bostwick and Omer S. Dean MEMBERSHIP INFORMATION: Anyone interested in the minerals, mines, or mining history of the Franklin- Ogdensburg, New Jersey area is invited to join the Franklin-Ogdensburg Miner- alogicalSociety, Inc. Membership includes scheduled meetings, lectures and field trips; as well as a subscription to The Picking Table. -
ISBN 5 900395 50 2 UDK 549 New Data on Minerals. Moscow
#00_firstPpages_en_0727:#00_firstPpages_en_0727.qxd 21.05.2009 19:38 Page 2 ISBN 5900395502 UDK 549 New Data on Minerals. Moscow.: Ocean Pictures, 2003. volume 38, 172 pages, 66 color photos. Articles of the volume are devoted to mineralogy, including descriptions of new mineral species (telyushenkoite – a new caesium mineral of the leifite group, neskevaaraite-Fe – a new mineral of the labuntsovite group) and new finds of min- erals (pabstite from the moraine of the Dara-i-Pioz glacier, Tadjikistan, germanocolusite from Kipushi, Katanga, min- erals of the hilairite group from Khibiny and Lovozero massifs). Results of study of mineral associations in gold-sulfide- tellyride ore of the Kairagach deposit, Uzbekistan are presented. Features of rare germanite structure are revealed. The cavitation model is proposed for the formation of mineral microspherulas. Problems of isomorphism in the stannite family minerals and additivity of optical properties in minerals of the humite series are considered. The section Mineralogical Museums and Collections includes articles devoted to the description and history of Museum collections (article of the Kolyvan grinding factory, P.A.Kochubey's collection, new acquisitions) and the geographical location of mineral type localities is discussed in this section. The section Mineralogical Notes includes the article about photo- graphing minerals and Reminiscences of the veteran research worker of the Fersman Mineralogical Museum, Doctor in Science M.D. Dorfman about meetings with known mineralogists and geochemists – N.A. Smoltaninov, P.P. Pilipenko, Yu.A. Bilibin. The volume is of interest for mineralogists, geochemists, geologists, and to museum curators, collectors and amateurs of minerals. EditorinChief Margarita I .Novgorodova, Doctor in Science, Professor EditorinChief of the volume: Elena A.Borisova, Ph.D Editorial Board Moisei D. -
Download the Scanned
American Mi neralogist,Volume78, pagesI 350-1359, 1993 SUBJECT INDEX, VOLUME 78, 1993 AlzO:-SiOz-H20,285 Analysis, chemical(mineral), cont. Analysis, chemical(mineral), cont. Ar, 1135 columbite,419 samarskite,419 Au,877 cordierite,1041 sanidine,601 Auqa-ssHge-rz,1108 diamond,753 serendibite,195 a-B qtartz,694 diaphorite,85 smectite,l2l7 Abhurite,233 &avite, 265 sodium-potassiummica, 782 Aeschynite,419 Fe-Pt,178 spinel,873, 1002 Alaska, 143, LO66 Fe2O3-FeTiO3,941 staurolite,345, 988, 1041 Alberta,225, 230 fangite, 1096 taikanire,1088 Algebraicanalysis, 1257 feldspar,158 tengerite-(Y),425 Alkali feldspar,952 fergusonite,419 tourmaline,1299 Almandine,405 fluid inclusions,657, 804 tremolite-richteite, 23 Aluminosilicate,594, 9ll foitire, 1299 tschernichite,822 Aluminum silicate,298 forsterite+ monticellite,42 vaninite, 1262 Alumotantite,845 galena,85 widgiemoolthalite,819 Amazonite,500 garnet,113, 132, 158,338,345, zircon, 36 Amorphoussilica, 1066 826 [erratum],988,1002, 1041 Analysis, chemical(rock) Amphibole,96, 405, 733, 746, 968, gedrite,511 amphibolite,988 t1r7 halogen,641 basalt, 794 Amphiboleactivities, 1174 hornblende,968 basanite,1230 Amphibolite, 988 ilmenite, 113, 826 lerratum] lunar rocks, 360 Analcime,225,230 jacobsite,1304 magnesio-arfvedsonite,96 Analysis,chemical (mineral) kaersutite,968, 1230 manganesecummingtonite, 96 aeschynite,419 kosnarite,653 microspheres,873 algebraicanalysis, 1257 lindqvistite, I304 pelite, 158, 345 amphibole,96,'133, 746, 968 lizardite, 391, 844 [erratum] PIXE,893 analcime,225,230 lunar rocks, 360 -
53Rd Annual Franklin-Sterling Gem and Mineral Show
Franklin - Sterling GEM & MINERAL SHOW SATURDAY & SUNDAY SEPTEMBER 26th & 27th, 2009 Sponsored By ;FRANKLIN,. t 1 1; A N't Franklin, New Jersey The Fluorescent Mineral Capital Of The World DEDICATION Steven Phillips The Franklin Mineral Museum Show Committee is pleased to dedicate the 2009 Franklin-Sterling Gem & Mineral Show to Steven Phillips. Steven was born and raised in Sussex County and was introduced to the Franklin mining area as a child when his father, Amos, purchased the Trot- ter and Buckwheat mine properties. Both areas are located across the street from the Franklin Mineral Mu- seum. The Trotter property was used as a collecting site for years and was managed under the watchful eye of Nick Zipco. The Buckwheat pit area Photo by Tema J. Hecht was developed into a family recrea- tional site. Steven developed an interest in the Franklin-Sterling Hill rocks and minerals in 1990 after his business, Phillips Enterprises, became one of the investors in the purchase of the Sterling Hill mine property. In 1988, the town of Og- densburg had foreclosed on the New Jersey Zinc Company mine property. Steven's interest in the area's unique mineralogy was the impetus for his be- coming involved with the Franklin Mineralogy Museum. He served on the Mu- seum board for several years and in 1999 was elected president. Under his guidance, the Museum made significant improvements to the physical facili- ties. These included designing and installing a new ramp into the Buckwheat dump collecting area and erecting an open-air pavilion for school and event use. -
IMA–CNMNC Approved Mineral Symbols
Mineralogical Magazine (2021), 85, 291–320 doi:10.1180/mgm.2021.43 Article IMA–CNMNC approved mineral symbols Laurence N. Warr* Institute of Geography and Geology, University of Greifswald, 17487 Greifswald, Germany Abstract Several text symbol lists for common rock-forming minerals have been published over the last 40 years, but no internationally agreed standard has yet been established. This contribution presents the first International Mineralogical Association (IMA) Commission on New Minerals, Nomenclature and Classification (CNMNC) approved collection of 5744 mineral name abbreviations by combining four methods of nomenclature based on the Kretz symbol approach. The collection incorporates 991 previously defined abbreviations for mineral groups and species and presents a further 4753 new symbols that cover all currently listed IMA minerals. Adopting IMA– CNMNC approved symbols is considered a necessary step in standardising abbreviations by employing a system compatible with that used for symbolising the chemical elements. Keywords: nomenclature, mineral names, symbols, abbreviations, groups, species, elements, IMA, CNMNC (Received 28 November 2020; accepted 14 May 2021; Accepted Manuscript published online: 18 May 2021; Associate Editor: Anthony R Kampf) Introduction used collection proposed by Whitney and Evans (2010). Despite the availability of recommended abbreviations for the commonly Using text symbols for abbreviating the scientific names of the studied mineral species, to date < 18% of mineral names recog- chemical elements -
Ernie New.Fp5
IMA/CNMNC List of Mineral Names compiled by Ernest H. Nickel & Monte C. Nichols Supplied through the courtesy of Materials Data, Inc. (http://www.MaterialsData.com) and based on the database MINERAL, which MDI makes available as a free download to the mineralogical community Status* Name CNMMC Approved Formula Strunz Classification Best, Most Recent or Most Complete reference. A Abelsonite NiC£¡H£¢N¤ 10.CA.20 American Mineralogist 63 (1978) 930 A Abenakiite-(Ce) Na¢¦Ce¦(SiO£)¦(PO¤)¦(CO£)¦(SO¢)O 9.CK.10 Canadian Mineralogist 32 (1994), 843 G Abernathyite K(UO¢)AsO¤•3H¢O 8.EB.15 American Mineralogist 41 (1956), 82 A Abhurite (SnÀÈ)¢¡Cl¡¦(OH)¡¤O¦ 3.DA.30 Canadian Mineralogist 23 (1985), 233 D Abkhazite Ca¢Mg¥Si¨O¢¢(OH)¢ American Mineralogist 63 (1978), 1023 D Abrazite K,Ca,Al,Si,O,H¢O Canadian Mineralogist 35 (1997), 1571 D Abriachanite Na¢(Fe,Mg)£(FeÁÈ)¢Si¨O¢¢(OH)¢ American Mineralogist 63 (1978), 1023 D Absite (U,Ca,Y,Ce)(Ti,Fe)¢O¦ Zapiski Vsesoyuznogo Mineralogicheskogo Obshchestva 92 (1963), 113 A Abswurmbachite CuÀÈ(MnÁÈ)¦O¨(SiO¤) 9.AG.05 Neues Jahrbuch für Mineralogie, Abhandlungen 163 (1991), 117 D Abukumalite (Ca,Ce)¢Y£(SiO¤,PO¤)£(O,OH,F) American Mineralogist 51 (1966), 152 D Acadialite (Ca,K,Na)(Si,Al)£O¦•3H¢O Canadian Mineralogist 35 (1997), 1571 G Acanthite Ag¢S 2.BA.35 Handbook of Mineralogy (Anthony et al.), 1 (1990), 1 A Acetamide CH£CONH¢ 10.AA.20 Zapiski Vsesoyuznogo Mineralogicheskogo Obshchestva 104 (1975), 326 G Achavalite FeSe 2.CC.05 Neues Jahrbuch für Mineralogie, Monatshefte (1972), 276 D Achiardite (Na,K,Ca)¥(Si,Al)¢¤O¤¨•14H¢O Canadian Mineralogist 35 (1997), 1571 D Achlusite Na,K,Al,Si,O(?) Canadian Mineralogist 36 (1998), 905 D Achrematite Pb,Mo,As,O,Cl American Mineralogist 62 (1977), 170 * A = Approved by CNMNC, D = Discredited by CNMNC, G = Grandfathered (original description preceded the establishment of the CNMNC in 1959, and generally regarded as a valid species) , GROUP = A name used to designate a group of species, H = Hypothetical mineral (synthetic, anthropogenic, etc.), I = Intermediate member of a solid-solution series (e.g.