Catalytic Partial Oxidation in Novel Non-Premixed Counter-Flow Reactor Configurations
Total Page:16
File Type:pdf, Size:1020Kb
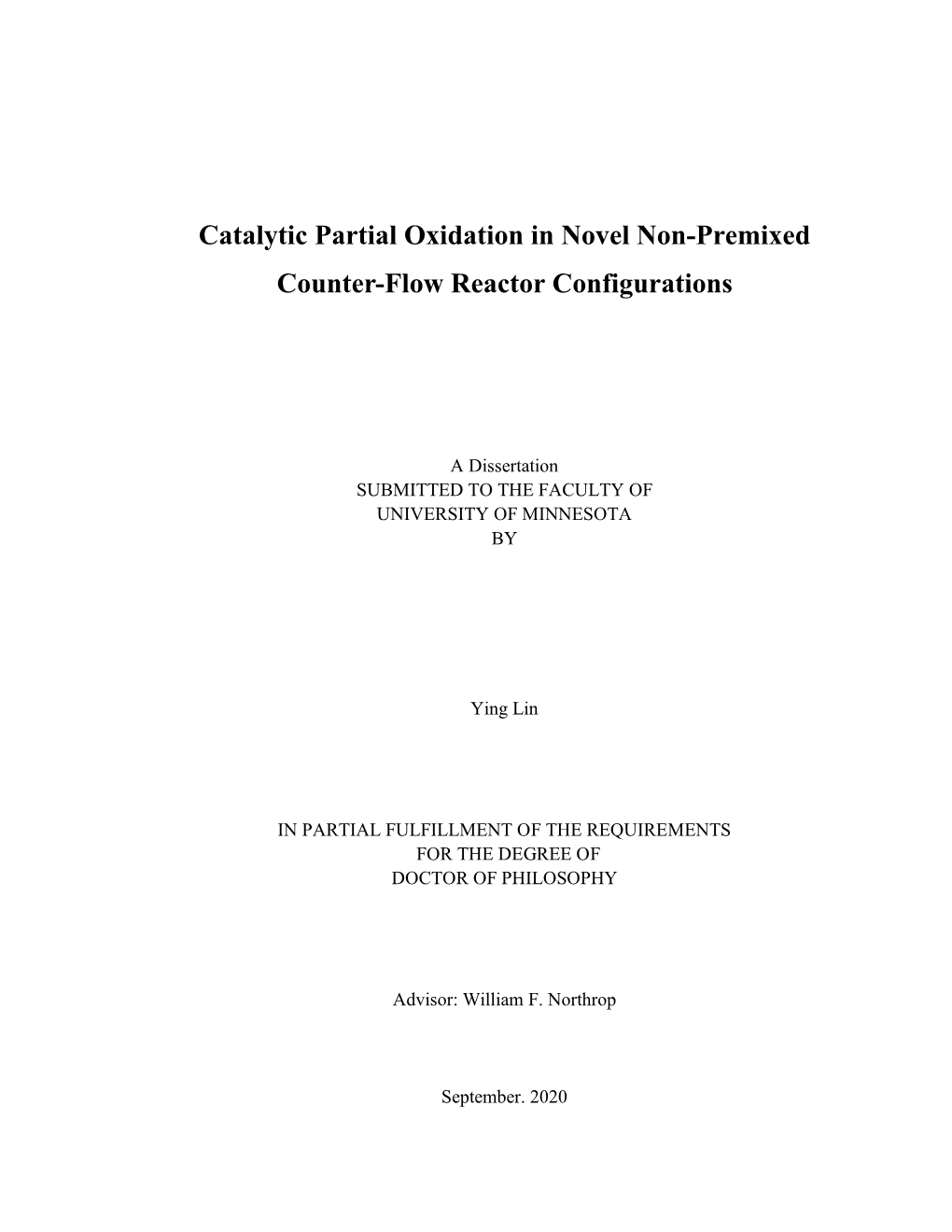
Load more
Recommended publications
-
Handbook of Hydrogen Energy Reformation of Hydrocarbon Fuels
This article was downloaded by: 10.3.98.104 On: 27 Sep 2021 Access details: subscription number Publisher: CRC Press Informa Ltd Registered in England and Wales Registered Number: 1072954 Registered office: 5 Howick Place, London SW1P 1WG, UK Handbook of Hydrogen Energy S.A. Sherif, D. Yogi Goswami, Elias K. Stefanakos, Aldo Steinfeld Reformation of Hydrocarbon Fuels Publication details https://www.routledgehandbooks.com/doi/10.1201/b17226-6 Paul A. Erickson, Hong-Yue (Ray) Tang, David R. Vernon Published online on: 29 Jul 2014 How to cite :- Paul A. Erickson, Hong-Yue (Ray) Tang, David R. Vernon. 29 Jul 2014, Reformation of Hydrocarbon Fuels from: Handbook of Hydrogen Energy CRC Press Accessed on: 27 Sep 2021 https://www.routledgehandbooks.com/doi/10.1201/b17226-6 PLEASE SCROLL DOWN FOR DOCUMENT Full terms and conditions of use: https://www.routledgehandbooks.com/legal-notices/terms This Document PDF may be used for research, teaching and private study purposes. Any substantial or systematic reproductions, re-distribution, re-selling, loan or sub-licensing, systematic supply or distribution in any form to anyone is expressly forbidden. The publisher does not give any warranty express or implied or make any representation that the contents will be complete or accurate or up to date. The publisher shall not be liable for an loss, actions, claims, proceedings, demand or costs or damages whatsoever or howsoever caused arising directly or indirectly in connection with or arising out of the use of this material. 3 Reformation of Hydrocarbon Fuels Paul A. Erickson University of California, Davis Hong-Yue (Ray) Tang University of California, Davis David R. -
Hydrogen Production by Partial Oxidation Reforming of Methane Over Ni Catalysts Supported on High and Low Surface Area Alumina and Zirconia
processes Article Hydrogen Production by Partial Oxidation Reforming of Methane over Ni Catalysts Supported on High and Low Surface Area Alumina and Zirconia Anis Fakeeha 1,2, Ahmed A. Ibrahim 1, Hesham Aljuraywi 1, Yazeed Alqahtani 1, Ahmad Alkhodair 1, Suliman Alswaidan 1, Ahmed E. Abasaeed 1 , Samsudeen O. Kasim 1 , Sofiu Mahmud 1 and Ahmed S. Al-Fatesh 1,* 1 Chemical Engineering Department, College of Engineering, King Saud University, P.O. Box 800, Riyadh 11421, Saudi Arabia; [email protected] (A.F.); [email protected] (A.A.I.); [email protected] (H.A.); [email protected] (Y.A.); [email protected] (A.A.); [email protected] (S.A.); [email protected] (A.E.A.); [email protected] (S.O.K.); mahmudsofi[email protected] (S.M.) 2 King Abdullah City for Atomic and Renewable Energy, (K.A. CARE) Energy Research and Innovation Center at Riyadh, Riyadh 11421, Saudi Arabia * Correspondence: [email protected]; Tel.: +966-11-46-76859 Received: 7 March 2020; Accepted: 9 April 2020; Published: 25 April 2020 Abstract: The catalytic activity of the partial oxidation reforming reaction for hydrogen production over 10% Ni supported on high and low surface area alumina and zirconia was investigated. The reforming reactions, under atmospheric pressure, were performed with a feed molar ratio of CH4/O2 = 2.0. The reaction temperature was set to 450–650 ◦C. The catalytic activity, stability, and carbon formation were determined via TGA, TPO, Raman, and H2 yield. The catalysts were calcined at 600 and 800 ◦C. The catalysts were prepared via the wet-impregnation method. -
Combined Steam Reforming and Partial Oxidation of Methane to Synthesis Gas Under Electrical Discharge
Combined Steam Reforming and Partial Oxidation of Methane to Synthesis Gas under Electrical Discharge Korada Supat† and Sumaeth Chavadej‡ The Petroleum and Petrochemical College, Chulalongkorn University, Bangkok 10330, Thailand Lance L. Lobban§ and Richard G. Mallinson* School of Chemical Engineering and Materials Science, University of Oklahoma, Norman, Oklahoma 73019 An experimental study of synthesis gas production from simultaneous steam reforming and partial oxidation of methane using an ac corona discharge was conducted. The benefits of the combination of the two reactions reduce the pure oxygen requirement in the system and increase the thermal efficiency by transferring heat between the exothermic and endothermic reactions. The results show that the addition of water vapor greatly enhanced the conversions of methane and oxygen and improved the energy efficiency in an oxygen-lean system. The energy consumed to convert a methane molecule decreased dramatically from 68 to 13 eV/mc with an increase in the percentage of water vapor from 0 to 50% at a CH4/O2 ratio of 5. At the conditions studied, input power had more influence on the methane and oxygen conversions than applied frequency. Introduction a higher H2O/CH4 ratio than the stoichiometric value. This results in higher H2/CO ratios (in the range of 3.4- Synthesis gas, consisting of hydrogen and carbon 5.0) than those required for Fischer-Tropsch synthesis monoxide, is an important raw material in chemical - and methanol production, and the high ratio of H2/CO manufacture such as, Fischer Tropsch synthesis to also would limit the carbon chain growth in Fischer- produce higher hydrocarbons (reaction 1), methanol 5,6 1 Tropsch synthesis. -
Evaluation of a Detailed Reaction Mechanism for Partial and Total
Evaluation of a Detailed Reaction Mechanism for Partial and Total Oxidation of C1 - C4 Alkanes DISSERTATION Submitted to the Faculty of Chemistry of the Rupertus-Carola University of Heidelberg, Germany For the degree of Doctor of Natural Sciences Presented by Raúl Quiceno González Born in Medellín, Colombia Examiners: Prof. Dr. Dr. h. c. Jürgen Warnatz Prof. Dr. Olaf Deutschmann Heidelberg, November 16, 2007 Interdisziplinäres Zentrum für Wissenschaftliches Rechnen Ruprecht – Karls – Universität Heidelberg 2007 DISSERTATION Submitted to the Faculty of Chemistry of the Rupertus-Carola University of Heidelberg, Germany For the degree of Doctor of Natural Sciences Presented by Raúl Quiceno González, Ms, Sciences Born in Medellín, Colombia Heidelberg, November 16, 2007 Title Evaluation of a Detailed Reaction Mechanism for Partial and Total Oxidation of C1 - C4 Alkanes Examiners: Prof. Dr. Dr. h. c. Jürgen Warnatz Prof. Dr. Olaf Deutschmann ACKNOWLEDGMENTS I would like to acknowledge to all the people who helped me directly or indirectly to accomplish this dissertation: First and foremost, I would like to express all my gratitude towards Prof. Dr. Dr. h. c. Jürgen Warnatz for giving the opportunity to share an unforgettable time in his group in Heidelberg. To Prof. Dr. Olaf Deutschmann and his family, for his support during my time in Heidelberg, for the useful comments and great support in the development of my work and for his friendship during difficult moments. To Farid Chejne, my former tutor in Colombia, for his tireless compromise with all of us, for being more than a tutor, a friend. I am also thankful to my colleagues at IWR: Ingrid for her collaboration with all the administrative details, to Barbara for her unvaluable help, to Jürgen Moldenhauer, Till Katzenmeier, Volker Karbach, Shaik and all my coworkers for their help and understanding. -
Production of Hydrogen
Production of Hydrogen RJ Allam Air Products Why Hydrogen? H2 + ½ O2 → H2O ∆H -57.8 kcal/mole z H2 is an energy vector, is converted to water which has minimal environmental impact. z H2 is a non-polluting fuel for transportation vehicles and power production z Currently road vehicles emit about the same quantity of CO2 as power production. z H2 can be produced from fossil fuels with CO2 capture and storage or from renewables 3 Production of Hydrogen Options Method Characteristics Photolysis catalytic-water splitting Electrolysis water Power for electrolyser ambient → high temperature ambient → high pressure Thermal splitting water high temperature ≡m conc as function of temp freeze equilibrium Fossil fuel Conversion Heat, water, oxygen, catalytic Far Future Non fossil fuel alternatives based on sunlight, renewables and nuclear Present Fossil fuels 4 Carbon Containing Fuels Coal Lignite → Anthracite Natural gas Refined Hydrocarbons Ethane → Fuel Oil Heavy refinery waste Tar → Petcoke Biomass 5 Reactions Reforming With Steam - Catalytic Natural gas and light CH4 + H2O ↔ CO + 3H2 + ∆H hydrocarbons CO + H2O ↔ H2 + CO2 - ∆H Partial Oxidation - Non Catalytic Any hydrocarbon or C + ½O2 → CO - ∆H carbonaceous feedstock CO + H2O ↔ CO2 + H2 - ∆H Thermal Decomposition Only limited application as co- CH4 → 2H2 + C +∆H product in carbon black manufacture 6 General Arrangement For CO2- free Hydrogen Production Steam Export Steam CO2 Fuel Syngas Heat Shift H2 purification / Oxygen H2 Generation Recovery reactors CO2 separation Waste Fuel Gas 7 CO2 Separation -
The Potential of Gas Switching Partial Oxidation Using Advanced Oxygen Carriers for Efficient H2 Production with Inherent CO2 Capture
applied sciences Article The Potential of Gas Switching Partial Oxidation Using Advanced Oxygen Carriers for Efficient H2 Production with Inherent CO2 Capture Carlos Arnaiz del Pozo 1,*, Schalk Cloete 2, Ángel Jiménez Álvaro 1 , Felix Donat 3 and Shahriar Amini 4 1 Departamento de Ingeniería Energética, Escuela Técnica Superior de Ingenieros Industriales (ETSII) c/ José Gutiérrez Abascal nº2, Universidad Politécnica de Madrid, 28006 Madrid, Spain; [email protected] 2 Flow Technology Research Group, SINTEF Industry, 7465 Trondheim, Norway; [email protected] 3 Department of Mechanical and Process Engineering, Institute of Energy and Process Engineering, Eidgenössische Technische Hochschule ETH Zurich, 8092 Zürich, Switzerland; [email protected] 4 Department of Mechanical Engineering, South Engineering Research Center, University of Alabama, Tuscaloosa, AL 35487, USA; [email protected] * Correspondence: [email protected] Abstract: The hydrogen economy has received resurging interest in recent years, as more countries commit to net-zero CO2 emissions around the mid-century. “Blue” hydrogen from natural gas with CO2 capture and storage (CCS) is one promising sustainable hydrogen supply option. Although conventional CO2 capture imposes a large energy penalty, advanced process concepts using the chemical looping principle can produce blue hydrogen at efficiencies even exceeding the conventional steam methane reforming (SMR) process without CCS. One such configuration is gas switching reforming (GSR), which uses a Ni-based oxygen carrier material to catalyze the SMR reaction and Citation: Arnaiz del Pozo, C.; Cloete, efficiently supply the required process heat by combusting an off-gas fuel with integrated CO2 capture. S.; Jiménez Álvaro, Á.; Donat, F.; The present study investigates the potential of advanced La-Fe-based oxygen carrier materials to Amini, S. -
Production of Hydrogen by Superadiabatic Decomposition of Hydrogen Sulfide
Proceedings of the 2002 U.S. DOE Hydrogen Program Review NREL/CP-610-32405 PRODUCTION OF HYDROGEN BY SUPERADIABATIC DECOMPOSITION OF HYDROGEN SULFIDE Rachid B. Slimane, Francis S. Lau, Remon J. Dihu, and Mark Khinkis Gas Technology Institute, Des Plaines, Illinois 60018 Phone: (847) 768-0592; e-mail: [email protected] Jacques Bingue, Alexei Saveliev, Alexander Fridman, and Lawrence Kennedy University of Illinois at Chicago, Chicago, IL Abstract The Gas Technology Institute, in collaboration with the University of Illinois at Chicago and industrial partners, including UOP, has been developing an innovative noncatalytic, thermochemical process for the production of hydrogen and elemental sulfur from hydrogen sulfide in H2S-containing waste gases. The key feature of this process is the superadiabatic reactor, where partial oxidation of H2S in the feed gas is carried out in a cylindrical vessel packed with a porous ceramic medium with a high thermal capacity. The intensive heat exchange between the filtrating and burning gas mixture, and the porous medium through the highly developed internal surfaces permits the accumulation of combustion energy in the solid matrix. As a result, flame temperatures can be significantly higher than the adiabatic temperature for the mixture. This process has potential to produce economically viable quantities of hydrogen through the superadiabatic partial oxidation of H2S in the feed at very high temperatures, which can be achieved without the input of external energy, and with no additional carbon dioxide (CO2) emissions. GTI has envisioned a process comprising the superadiabatic H2S decomposition reactor, product/byproduct separation schemes, hydrogen purification, and tail gas cleanup. With funding from the U.S. -
Supercritical Water Partial Oxidation
Proceedings of the 2002 U.S. DOE Hydrogen Program Review NREL/CP-610-32405 SUPERCRITICAL WATER PARTIAL OXIDATION G.T. Hong and M.H. Spritzer General Atomics 3550 General Atomics Court San Diego, CA 92121-1122 Abstract General Atomics is developing Supercritical Water Partial Oxidation (SWPO), a gasification process involving oxidative reactions in a supercritical water environment – akin to high- pressure steam – in the presence of substoichiometric quantities of oxidant. The key potential advantage of the SWPO process is the use of partial oxidation in-situ to rapidly heat the gasification medium, resulting in less char formation and improved hydrogen yield. Another major advantage is that the high-pressure, high-density aqueous environment is ideal for reacting and gasifying organics. The high water content of the medium should encourage formation of hydrogen and hydrogen-rich products and is highly compatible with high water content feeds such as biomass materials. By the same token, the high water content of the medium is effective for gasification of hydrogen-poor materials such as coal. A versatile pilot plant for exploring gasification in supercritical water has been established at the General Atomics’ facility in San Diego. Preliminary testing of the SWPO process has found hydrogen yields of about 10 grams per 100 grams of feed, comparable to those found in prior laboratory- scale work carried out at the University of Hawaii. As in that prior work, a significant amount of the hydrogen found in the gas phase products is derived from the water/steam matrix. Introduction General Atomics is developing Supercritical Water Partial Oxidation (SWPO) for the efficient and environmentally advantageous gasification and hydrogen production from low-grade fuels such as biomass, municipal/solid waste (MSW) and high-sulfur coal. -
Steam and Partial Oxidation Reforming Options for Hydrogen Production from Fossil Fuels for PEM Fuel Cells
Alexandria Engineering Journal (2012) 51,69–75 Alexandria University Alexandria Engineering Journal www.elsevier.com/locate/aej www.sciencedirect.com Steam and partial oxidation reforming options for hydrogen production from fossil fuels for PEM fuel cells Yousri M.A. Welaya, Mohamed M. El Gohary 1, Nader R. Ammar * Naval Arch. & Marine Eng. Dept., Faculty of Engineering, Alexandria University, Egypt Received 28 June 2011; revised 13 February 2012; accepted 22 March 2012 Available online 24 April 2012 KEYWORDS Abstract Proton exchange membrane fuel cell (PEM) generates electrical power from air and from PEMFC; hydrogen or hydrogen rich gas mixtures. Therefore, there is an increasing interest in converting cur- Hydrogen production; rent hydrocarbon based marine fuels such as natural gas, gasoline, and diesel into hydrogen rich Steam reforming; gases acceptable to the PEM fuel cells on board ships. Using chemical flow sheeting software, Partial oxidation the total system efficiency has been calculated. Natural gas appears to be the best fuel for hydrogen rich gas production due to its favorable composition of lower molecular weight compounds. This paper presents a study for a 250 kW net electrical power PEM fuel cell system utilizing a partial oxidation in one case study and steam reformers in the second. This study has shown that steam-reforming process is the most competitive fuel processing option in terms of fuel processing efficiency. Partial oxidation process has proved to posses the lowest fuel processing efficiency. Among the options studied, the highest fuel processing efficiency is achieved with natural gas steam reforming system. ª 2012 Faculty of Engineering, Alexandria University. -
Two-Section Reactor Model for Autothermal Reforming of Methane to Synthesis Gas
Two-section reactor model for autothermal reforming of methane to synthesis gas P. Maarten Biesheuvel and Gert Jan Kramer Shell Global Solutions International B.V., Badhuisweg 3, 1031 CM, Amsterdam, The Netherlands. Abstract A one-dimensional and stationary reactor model is presented to describe the catalytic conversion of a gaseous hydrocarbon fuel with air and steam to synthesis gas by autothermal reforming (ATR) and catalytic partial oxidation (CPO). The model defines two subsequent sections in the reactor, namely an upstream oxidation section, and a downstream reforming section. In the oxidation section all of the oxygen is converted, with partial conversion of the fuel. An empirical fuel utilization ratio is used to quantify which part of the fuel is converted in the oxidation section as function of the relative flows of air and steam. In the oxidation section, the gas temperature rapidly increases toward the toptemperature at the intersection with the reforming section. In this section the temperature decreases while the fuel is further converted with water and CO 2 as oxidant. For methane as fuel, simulation results are presented and compared with experiments. For multicomponent fuels such as natural gas and naphtha, it is described how the two-section model can be applied. Introduction Hydrogen is manufactured industrially from hydrocarbon fuels either by steam reforming or by gasification (Rostrup-Nielsen, 1993). In steam reforming, the fuel (in most cases, natural gas) reacts with steam toward synthesis gas over a Ni-based heterogeneous catalyst. Due to the endothermicity of the steam reforming reaction, heat must be supplied to the reactor through the reactor tube walls. -
Advances in Reforming and Partial Oxidation of Hydrocarbons for Hydrogen MARK Production and Fuel Cell Applications
Renewable and Sustainable Energy Reviews 82 (2018) 761–780 Contents lists available at ScienceDirect Renewable and Sustainable Energy Reviews journal homepage: www.elsevier.com/locate/rser Advances in reforming and partial oxidation of hydrocarbons for hydrogen MARK production and fuel cell applications Sivaprakash Sengodana, Rong Lana, John Humphreysa, Dongwei Dua, Wei Xua, Huanting Wangb, ⁎ Shanwen Taoa,b, a School of Engineering, University of Warwick, Coventry CV4 7AL, UK b Department of Chemical Engineering, Monash University, Clayton, Victoria 3800, Australia ARTICLE INFO ABSTRACT Keywords: One of the most attractive routes for the production of hydrogen or syngas for use in fuel cell applications is the Hydrogen production reforming and partial oxidation of hydrocarbons. The use of hydrocarbons in high temperature fuel cells is Catalyst achieved through either external or internal reforming. Reforming and partial oxidation catalysis to convert Reforming hydrocarbons to hydrogen rich syngas plays an important role in fuel processing technology. The current re- Partial oxidation search in the area of reforming and partial oxidation of methane, methanol and ethanol includes catalysts for Fuel cells reforming and oxidation, methods of catalyst synthesis, and the effective utilization of fuel for both external and internal reforming processes. In this paper the recent progress in these areas of research is reviewed along with the reforming of liquid hydrocarbons, from this an overview of the current best performing catalysts for the reforming and partial oxidizing of hydrocarbons for hydrogen production is summarized. 1. Introduction The development of converting hydrocarbon fuels to hydrogen-rich gas products generally fall in one of following processes: steam re- Fuel cells are electrochemical energy conversion devices that are forming (SR), auto thermal reforming (ATR), dry reforming (DR), par- used to convert the chemical energy stored in chemical fuels directly to tial oxidation (POX) or a combination of two or more [27]. -
Review of Small Stationary Reformers for Hydrogen Production
IEA/H2/TR-02/002 REVIEW OF SMALL STATIONARY REFORMERS FOR HYDROGEN PRODUCTION Dr. Joan M. Ogden Research scientist Center for Energy and Environmental Studies Princeton University Princeton, NJ 08544 Phone: (609) 258-5470 Email: [email protected] A report for the International Energy Agency Agreement on the Production and Utilization of Hydrogen Task 16, Hydrogen from Carbon-Containing Materials Preface The following report was prepared in support of efforts to develop a new International Energy Agency (IEA) task on the production of hydrogen from carbon-containing materials. The draft report was completed and the results presented during a Task Development Workshop in March 2001. The discussion in this report is based on technology developments that had been reported or were known prior to March 2001. No updates have been made to reflect advancements that have taken place since that time. An update to this report will be a likely outcome of the new IEA Agreement on the Production and Utilization of Hydrogen Task 16, Hydrogen from Carbon-Containing Materials, which officially began in April 2002 and will be active for three years. REVIEW OF SMALL STATIONARY REFORMERS FOR HYDROGEN PRODUCTION TABLE OF CONTENTS I. INTRODUCTION ............................................................................................................. 1 II. HYDROGEN SUPPLY OPTIONS FOR THE TRAN SPORTATION SECTOR ............. 3 A. MOTIVATION FOR HYDROGEN AS A TRANSPORTATION FUEL: ENVIRONMENTAL AND ENERGY SUPPLY CHALLENGES FACING THE TRANSPORTATION SECTOR .................................... 3 B. REVIEW OF PAST STUDIES OF HYDROGEN REFUELING INFRASTRUCTURE .................... 4 C. HYDROGEN INFRASTRUCTURE DEMONSTRATIONS........................................................ 6 D. DISTRIBUTED VERSUS CENTRALIZED HYDROGEN PRODUCTION ................................... 6 E. ROLES FOR SMALL REFORMERS IN DEVELOPMENT OF A HYDROGEN ENERGY SYSTEM 6 III.