Analysis of Alternatives for the Use of Trichloroethylene As an Extraction
Total Page:16
File Type:pdf, Size:1020Kb
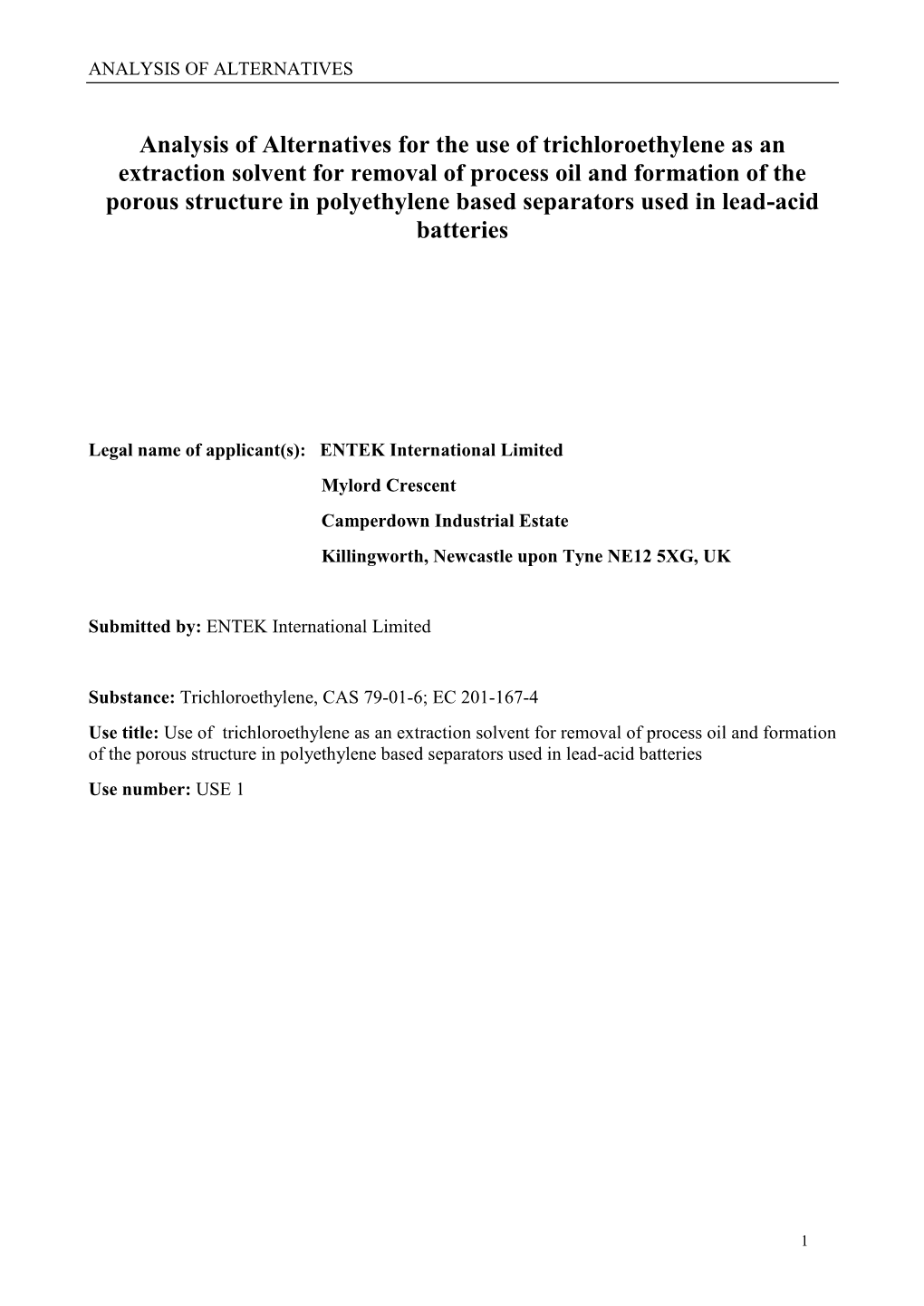
Load more
Recommended publications
-
Packet of Wiser Reports on Acetone Acetonitrile
Ac&tone ^Hazmat - NFPA Hazard Classification Page 1 of Acetone CAS RN: 67-64-1 Hazmat - NFPA Hazard Classification SOMS DocID 2085807 Health: 1 (Slight) Materials that, on exposure, would cause significant irritation, but only minor residual injury, including those requiring the use of an approved air-purifying respirator. These materials are only slightly hazardous to health and only breathing protection is needed. Flammability: 3 (Severe) rhis degree includes Class IB and 1C flammable liquids and materials that can be easily ignited under almost all normal temperature conditions. Water may be ineffective in controlling or extinguishing fires in such materials. Instability: 0 (Minimal) This degree includes materials that are normally stable, even under fire exposure conditions, and that do not react with water.- Norma lire fighting procedures may be used. Printed by WISER for Windows (v2.3.231, database v2.108) HHS/NIH, National Library of Medicine AR000018 iile://C:\Documents and Settings\Gham\Application Data\National Library of Medicine\WISER\2.3.231.628... 9/27/20 Acetone ^Key Info Page 1 of Acetone CAS RN: 67-64-1 Key Info FLAMMABLE LIQUIDS (Polar / Water-Miscible) • HIGHLY FLAMMABLE: Easily ignited by heat, sparks or flames • CAUTION: Very low flash point; use of water spray when fighting fire may be inefficient Printed by WISER for Windows (v2.3.231, database v2.108) HHS/NIH, National Library of Medicine AR000019 file://C:\Documents and Settings\Gham\Application Data\National Library of Medicine\WISER\2.3.231.628../ 9/27/20 Acetone - -Hazmat - Explosive Limits / Potential Page 1 of Acetone CAS RIM: 67-64-1 Hazmat - Explosive Limits / Potential Highly flammable liquid. -
AP-42 Vol. I CH1.6 Wood Residue Combustion in Boilers
1.6 Wood Residue Combustion In Boilers 1.6.1 General1-6 The burning of wood residue in boilers is mostly confined to those industries where it is available as a byproduct. It is burned both to obtain heat energy and to alleviate possible solid residue disposal problems. In boilers, wood residue is normally burned in the form of hogged wood, bark, sawdust, shavings, chips, mill rejects, sanderdust, or wood trim. Heating values for this residue range from about 4,500 British thermal units/pound (Btu/lb) of fuel on a wet, as-fired basis, to about 8,000 Btu/lb for dry wood. The moisture content of as-fired wood is typically near 50 weight percent for the pulp, paper and lumber industries and is typically 10 to 15 percent for the furniture industry. However, moisture contents may vary from 5 to 75 weight percent depending on the residue type and storage operations. Generally, bark is the major type of residue burned in pulp mills; either a mixture of wood and bark residue or wood residue alone is burned most frequently in the lumber, furniture, and plywood industries. 1.6.2 Firing Practices5, 7, 8 Various boiler firing configurations are used for burning wood residue. One common type of boiler used in smaller operations is the Dutch oven. This unit is widely used because it can burn fuels with very high moisture content. Fuel is fed into the oven through an opening in the top of a refractory-lined furnace. The fuel accumulates in a cone-shaped pile on a flat or sloping grate. -
Dichloromethane; CASRN 75-09-2
Integrated Risk Information System (IRIS) U.S. Environmental Protection Agency Chemical Assessment Summary National Center for Environmental Assessment Dichloromethane; CASRN 75-09-2 Human health assessment information on a chemical substance is included in the IRIS database only after a comprehensive review of toxicity data, as outlined in the IRIS assessment development process. Sections I (Health Hazard Assessments for Noncarcinogenic Effects) and II (Carcinogenicity Assessment for Lifetime Exposure) present the conclusions that were reached during the assessment development process. Supporting information and explanations of the methods used to derive the values given in IRIS are provided in the guidance documents located on the IRIS website. STATUS OF DATA FOR Dichloromethane File First On-Line 01/31/1987 Category (section) Assessment Available? Last Revised Oral RfD (I.A.) Yes 11/18/2011 Inhalation RfC (I.B.) Yes 11/18/2011 Carcinogenicity Assessment (II.) Yes 11/18/2011 I. Chronic Health Hazard Assessments for Noncarcinogenic Effects I.A. Reference Dose for Chronic Oral Exposure (RfD) Substance Name — Dichloromethane CASRN — 75-09-2 Section I.A. Last Revised — 11/18/2011 The RfD is an estimate (with uncertainty spanning perhaps an order of magnitude) of a daily oral exposure to the human population (including sensitive subgroups) that is likely to be without an appreciable risk of deleterious effects during a lifetime. The RfD is intended for use in risk assessments for health effects known or assumed to be produced through a nonlinear (presumed threshold) mode of action. It is expressed in units of mg/kg-day. Please refer to the guidance documents for an elaboration of these concepts. -
NMR Chemical Shifts of Common Laboratory Solvents As Trace Impurities
7512 J. Org. Chem. 1997, 62, 7512-7515 NMR Chemical Shifts of Common Laboratory Solvents as Trace Impurities Hugo E. Gottlieb,* Vadim Kotlyar, and Abraham Nudelman* Department of Chemistry, Bar-Ilan University, Ramat-Gan 52900, Israel Received June 27, 1997 In the course of the routine use of NMR as an aid for organic chemistry, a day-to-day problem is the identifica- tion of signals deriving from common contaminants (water, solvents, stabilizers, oils) in less-than-analyti- cally-pure samples. This data may be available in the literature, but the time involved in searching for it may be considerable. Another issue is the concentration dependence of chemical shifts (especially 1H); results obtained two or three decades ago usually refer to much Figure 1. Chemical shift of HDO as a function of tempera- more concentrated samples, and run at lower magnetic ture. fields, than today’s practice. 1 13 We therefore decided to collect H and C chemical dependent (vide infra). Also, any potential hydrogen- shifts of what are, in our experience, the most popular bond acceptor will tend to shift the water signal down- “extra peaks” in a variety of commonly used NMR field; this is particularly true for nonpolar solvents. In solvents, in the hope that this will be of assistance to contrast, in e.g. DMSO the water is already strongly the practicing chemist. hydrogen-bonded to the solvent, and solutes have only a negligible effect on its chemical shift. This is also true Experimental Section for D2O; the chemical shift of the residual HDO is very NMR spectra were taken in a Bruker DPX-300 instrument temperature-dependent (vide infra) but, maybe counter- (300.1 and 75.5 MHz for 1H and 13C, respectively). -
Alberta Environment
Chemical Fact Sheets Manganese, Mn CAS No. 7439-96-5 WHAT IS MANGANESE? Manganese is a gray-pink metal. USES Manganese is used in the manufacture of ceramics, matches, glass, dyes and welding rods. It is a component of steel, steel alloys, cast iron, superalloys & nonferrous alloys, as well as a chemical intermediate for high purity salts. Manganese is used as a purifying & scavenging agent in metal production. SOURCES Manganese is a naturally occurring substance found in many types of rock; it is ubiquitous in the environment and found in low levels in water air, soil, and food. It is commonly found in the environment as a result of its use in the manufacture of the above-noted materials. ENVIRONMENTAL LEVELS AND EXPOSURE Exposure to manganese might include: • Inhaling it in ambient air, particularly near industries involved in the manufacture of manganese-containing materials. Occupational exposure via inhalation is most common. Ambient air concentrations of manganese were not reported in 1997 or 1998 in Alberta. ENVIRONMENTAL FATE AND BEHAVIOUR • Manganese, as an aerosol, may dissolve upon contact with water on a time scale of a few minutes. TOXICITY • Manganese is an element considered essential to human health. • Inhalation of manganese compounds in aerosols or fine dusts may cause "metal fume fever”. MANGANESE Page 1 of 2 • Early symptoms of chronic manganese poisoning may include languor, sleepiness and weakness in the legs. Emotional disturbances such as uncontrollable laughter and a spastic gait with tendency to fall in walking are common in more advanced cases. • Chronic manganese poisoning is not a fatal disease. -
A Functional Nitric Oxide Reductase Model
A functional nitric oxide reductase model James P. Collman*, Ying Yang, Abhishek Dey, Richard A. Decre´ au, Somdatta Ghosh, Takehiro Ohta, and Edward I. Solomon Department of Chemistry, Stanford University, Stanford, CA 94305 Contributed by James P. Collman, September 2, 2008 (sent for review August 7, 2008) A functional heme/nonheme nitric oxide reductase (NOR) model is presented. The fully reduced diiron compound reacts with two equivalents of NO leading to the formation of one equivalent of N2O and the bis-ferric product. NO binds to both heme Fe and nonheme Fe complexes forming individual ferrous nitrosyl species. The mixed-valence species with an oxidized heme and a reduced nonheme FeB does not show NO reduction activity. These results are consistent with a so-called ‘‘trans’’ mechanism for the reduc- tion of NO by bacterial NOR. functional model ͉ NO reduction ͉ N2O ͉ “trans” mechanism Fig. 1. Schematic representation of the bimetallic active sites of NOR and itric oxide reductase (NOR) is a membrane-bound enzyme CcO. Nthat catalyzes the 2eϪ reduction of nitric oxide (NO) to nitrous oxide (N2O), an obligatory step involved in the sequen- Ϫ tial reduction of nitrate to dinitrogen known as bacterial deni- FTIR reveals a heme ferric nitrosyl band at 1,924 cm 1 that shifts trification. The active site of NOR consists of a monohistidine to 1,887 cmϪ1 when 15NO is used, whereas the EPR spectrum ligated five-coordinate heme and a trisimidazole ligated non- manifests a low-spin ferric signal that is assigned to the nonheme heme FeB. This structure strongly resembles the active site of FeB because a ferric heme nitrosyl would be EPR silent. -
Dichloromethane
Version 6.11 SAFETY DATA SHEET Revision Date 06/14/2021 Print Date 09/25/2021 SECTION 1: Identification of the substance/mixture and of the company/undertaking 1.1 Product identifiers Product name : Dichloromethane Product Number : 270997 Brand : Sigma-Aldrich Index-No. : 602-004-00-3 CAS-No. : 75-09-2 1.2 Relevant identified uses of the substance or mixture and uses advised against Identified uses : This chemical/product is not and cannot be distributed in commerce (as defined in TSCA section 3(5)) or processed (as defined in TSCA section 3(13)) for consumer paint or coating removal. 1.3 Details of the supplier of the safety data sheet Company : Sigma-Aldrich Inc. 3050 SPRUCE ST ST. LOUIS MO 63103 UNITED STATES Telephone : +1 314 771-5765 Fax : +1 800 325-5052 1.4 Emergency telephone Emergency Phone # : 800-424-9300 CHEMTREC (USA) +1-703- 527-3887 CHEMTREC (International) 24 Hours/day; 7 Days/week SECTION 2: Hazards identification 2.1 Classification of the substance or mixture GHS Classification in accordance with 29 CFR 1910 (OSHA HCS) Skin irritation (Category 2), H315 Eye irritation (Category 2A), H319 Carcinogenicity (Category 2), H351 Specific target organ toxicity - single exposure (Category 3), Central nervous system, H336 For the full text of the H-Statements mentioned in this Section, see Section 16. 2.2 GHS Label elements, including precautionary statements Pictogram Sigma-Aldrich - 270997 Page 1 of 12 The life science business of Merck KGaA, Darmstadt, Germany operates as MilliporeSigma in the US and Canada Signal word Warning Hazard statement(s) H315 Causes skin irritation. -
A Cu4s Model for the Nitrous Oxide Reductase Active Sites Supported Only by Nitrogen Ligands Brittany J
Marquette University e-Publications@Marquette Chemistry Faculty Research and Publications Chemistry, Department of 1-1-2015 A Cu4S Model for the Nitrous Oxide Reductase Active Sites Supported Only by Nitrogen Ligands Brittany J. Johnson University of Illinois at Chicago William E. Antholine Medical College of Wisconsin Sergey V. Lindeman Marquette University, [email protected] Neal P. Mankad University of Illinois at Chicago Accepted version. Chemical Communications, Vol. 51 (2015): 11860-11863. DOI. © 2015 The Royal Society of Chemistry. Used with permission. NOT THE PUBLISHED VERSION; this is the author’s final, peer-reviewed manuscript. The published version may be accessed by following the link in the citation at the bottom of the page. A Cu4S Model for the Nitrous Oxide Reductase Active Sites Supported Only by Nitrogen Ligands Brittany J. Johnson Department of Chemistry, University of Illinois at Chicago, Chicago, IL William E. Antholine Department of Biophysics, Medical College of Wisconsin, Milwaukee, WI Sergey V. Lindeman Department of Chemistry, Marquette University, Milwaukee, WI Neal P. Mankad Department of Chemistry, University of Illinois at Chicago, Chicago, IL Abstract: To model the (His)7Cu4Sn (n = 1 or 2) active sites of nitrous oxide reductase, the first Cu4(μ4-S) cluster supported only by nitrogen donors has been prepared using amidinate supporting ligands. Structural, magnetic, spectroscopic, and computational characterization is reported. Electrochemical Chemical Communications, Vol 51 (2015): pg. 11860-11863. DOI. This article is © Royal Society of Chemistry and permission has been granted for this version to appear in e-Publications@Marquette. Royal Society of Chemistry does not grant permission for this article to be further copied/distributed or hosted elsewhere without the express permission from Royal Society of Chemistry. -
1, 3-Bis(2, 4, 6-Trinitrophenylaminooxy) Propane
CEJC 1(2003)53{64 1,3-bis(2,4,6-trinitrophenylaminooxy)propane andits 4-cyano-2,6-dinitrophenylCongener: Synthesisand Prop erties. Irina C. Covaci 1,PetreIonita 1,MironT. Caproiu 2,RaduSocoteanu 1, Titus Constantinescu 1,AlexandruT. Balaban 3;4 1 RoumanianA cademy,Institute ofPhysical Chemistry \I.G.Murgulescu", Laboratoryof Supramolecular Chemistry and Interphase Processes, SplaiulIndependentei 202, 77408, Bucharest, Roumania 2 RoumanianA cademy,Institute \C.D. Nenitzescu" ofOrganic Chemistry, SplaiulIndependentei 202B, 77408, Bucharest, Roumania 3 University \Polytechnica",Faculty of Industrial Chemistry, Departmentof Organic Chemistry, Bucharest, Roumania 4 TexasA&M University atGalveston, Galveston,TX 77553-1675,USA Received 4October 2002;revised 24December 2002 Abstract: Starting fromN-hydroxyphthalimide (5) and1,3-dibromopropane (6) weobtained 1,3-bis(phthalimidooxy)propane (7) which led to 1,3-bis(aminooxy)propane dihydrochloride (8). Fromits reaction with picryl chloride or4-cyano-2,6-dinitrochlorobenzene, the twotitle compounds(4b, 4a)were obtained. 1H-NMR and 13C-NMRspectra arepresented. Forcomparisonwith the analogousN-methoxy- 2,6-dinitro-4-R-anilines 1a,1b (R=CNorR=NO 2), wereport the hydrophobic characteristics (by RPTLC), electronic spectra for the neutral compoundsand their anions, pK a values, andthe behavior towardsoxidizers (DPPH, PbO 2;Pb(CH3COO)4, KMnO4 and Ag2O); DPPH converts compounds1a, 1b and 4a, 4b into betainic structures 2a,2b respectively. c Central EuropeanScience Journals. All rights reserved. ® Keywords:N-alkoxyaryl derivatives; RPTLC; pK a;NMR;oxidation 1Introduction It was shown in previous papers [1- 10]that compounds of type 1present interesting properties when substituents are strong electron acceptors (e.g.1a, 1b). Among these properties, the generation of N-alkoxyaminylfree radicals on oxidation [4- 8]allowed a 54 A.T.Balaban et al. -
6. the Top Eight Causes of Accidents in Recent Years
6. The Top Eight Causes of Accidents in Recent Years Accidents with alkali metals Here you can see that the reactivity level and risks of alkali metals increases in this direction, with Lithium being the least reactive and Caesium having the strongest reaction. As you can see here, the reactivity level of Caesium is much stronger than that of Lithium. 19.11.19 ca. 15.15h: In a practicum laboratory a fire suddenly broke out in a fume hood. Accident object: Distillation apparatus containing alkali metals. The aim of this distillation apparatus was to dry heptane with alkali metal. reservoir vessel = distilled dry heptane receiver flask containing alkali metals and heptane The following concatenations led to the accident: - The N2 gas supply hose of a distillation apparatus containing alkali metals in a fume hood was damaged by a student. - The pressure drop caused a over boiling in the distillation apparatus. The heptane with the alkali metal splashed inside the distillation apparatus up. - The assistant decided to clean the distillation apparatus after this incident. - The assistant instructed the student to clean the reservoir vessel, he took care of the receiver flask. - The student tried to flush out the residue in the reservoir vessel with an acetone squirt bottle. It reacted with smoke formation. - In another fume hood, where among other things hazardous waste was stored, the student rinsed the reservoir vessel with isopropanol. However, he could not satisfactorily clean the residues contained in the reservoir vessel. - The student then attempted to rinse the residue with a methylene chloride spray bottle; at this point, deflagration occurred and the fire broke out. -
General Remarks
SOME CHEMICALS USED AS SOLVENTS AND IN POLYMER MANUFACTURE VOLUME 110 This publication represents the views and expert opinions of an IARC Working Group on the Evaluation of Carcinogenic Risks to Humans, which met in Lyon, 3–10 June 2014 LYON, FRANCE - 2017 IARC MONOGRAPHS ON THE EVALUATION OF CARCINOGENIC RISKS TO HUMANS GENERAL REMARKS This one-hundred-and-tenth volume of the IARC Monographs contains evaluations of the carcinogenic hazard to humans of perfluorooctanoic acid, tetrafluoroethylene, 1,2-dichlo- ropropane, dichloromethane, and 1,3-propane sultone. Exposure measurements and biomonitoring studies have shown that workers and the general population are exposed to these agents. All except one of these agents, perfluorooctanoic acid, were evaluated previously in Volume 71 of the IARC Monographs (IARC, 1999), when the Working Group classified three (tetrafluoroethylene, dichloromethane, and 1,3-propane sultone) as possibly carcinogenic to humans (Group 2B) and one (1,2-dichloropropane) as not classifiable as to its carcinogenicity to humans (Group 3). Since the previous evaluations, new data have become available, and the Preamble to the IARC Monographs has been modified to permit more explicit consideration of mechanistic data. A summary of the findings of this volume appears in The Lancet Oncology (Benbrahim-Tallaa et al., 2014). Perfluorooctanoic acid perturbation of these pathways and increased risk of cancer, with respect to human testicular Interference with steroidogenic enzymes is a cancer in general, as well as perfluorooctanoic -
II.1.6 Chloroform and Dichloromethane by Kanako Watanabe
1.6 II.1.6 Chloroform and dichloromethane by Kanako Watanabe Introduction Chloroform exerts a suppressing eff ect on the central nervous system. It had been used as a general anaesthetic since the 19th century, but it disappeared, because of its hepatotoxicity and arrhythmia-inducing eff ects. It is now being used for industrial purposes, such as a solvent, extracting reagent, refrigerant and chemical material. Chloroform poisoning can be seen in accidental, suicidal [1] and homicidal cases. Dichloromethane (methylene dichloride, methylene chloride) is also being widely used in industries as a solvent and refrigerant like chloroform, and causing many poisoning cases due to accidents and suicides [2]. Recently, dichloromethane has become of interest as a substitute of chlorofl uorocarbon, because the latter was found to accelerate the depletion of the ozone layer and is in the line of being abolished completely. Since both chloroform and dichloromethane are volatile compounds, their analysis is usu- ally made by the headspace extraction and GC detection. In this chapter, a simple headspace GC method, using dichloromethane as internal standard (IS) for assays of chloroform and vice versa, is presented [3]. Reagent and their preparation i. Reagents Chloroform, dichloromethane and methanol of special grade can be purchased from Wako Pure Chemical Industries, Ltd., Osaka, Japan and many other manufacturers. ii. Preparation A 337-µL volume of chloroform and a 377-µL volume of dichloromethane are separately dis- solved in methanol to prepare each 100 mL solution as stock solutions. Each solution is diluted 5-fold with methanol; a 10-µL volume containing 10 µg of each compound is added to 0.5 mL whole blood as IS and mixed well.