Study on Connection of Crossbeams in Rationalized Plate-Girder Bridges
Total Page:16
File Type:pdf, Size:1020Kb
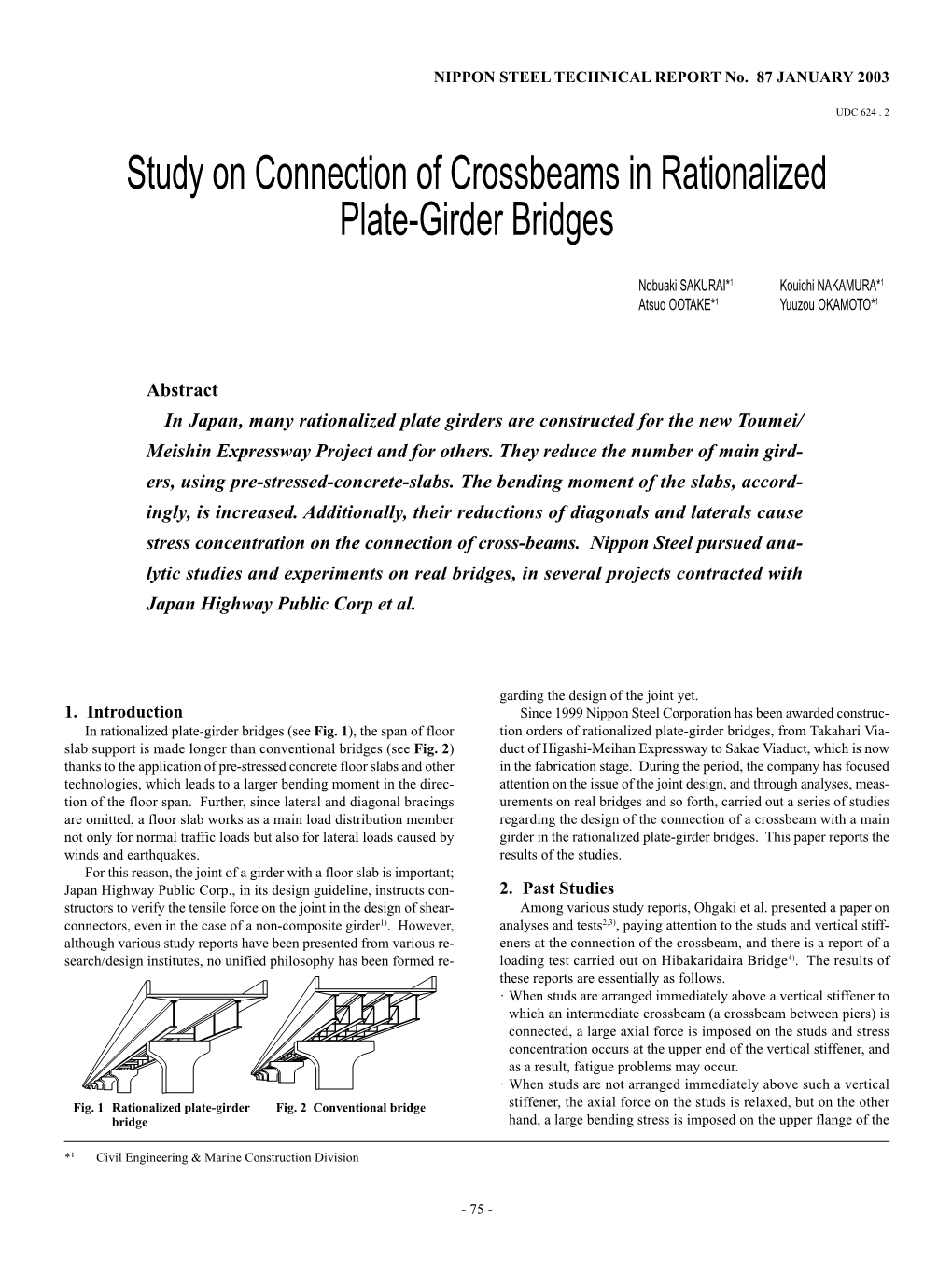
Load more
Recommended publications
-
Modern Steel Construction 2009
Reprinted from 2009 MSC Steel Bridges 2009 Welcome to Steel Bridges 2009! This publication contains all bridge related information collected from Modern Steel Construction magazine in 2009. These articles have been combined into one organized document for our readership to access quickly and easily. Within this publication, readers will find information about Accelerated Bridge Construction (ABC), short span steel bridge solutions, NSBA Prize Bridge winners, and advancement in coatings technologies among many other interesting topics. Readers may also download any and all of these articles (free of charge) in electronic format by visiting www.modernsteel.org. The National Steel Bridge Alliance would like to thank everyone for their strong dedication to improving our nation’s infrastructure, and we look forward to what the future holds! Sincerely, Marketing Director National Steel Bridge Alliance Table of Contents March 2009: Up and Running in No Time........................................................................................... 3 March 2009: Twice as Nice .................................................................................................................. 6 March 2009: Wide River ..................................................................................................................... 8 March 2009: Over the Rails in the Other Kansas City ........................................................................ 10 July 2009: Full House ....................................................................................................................... -
Ch. 407 Structural Steel
2012 INDIANA DEPARTMENT OF TRANSPORTATION—2012 DESIGN MANUAL CHAPTER 407 Steel Structure NOTE: References to material in 2011 Design Manual have been highlighted in blue throughout this document. 2012 TABLE OF CONTENTS Table of Contents ............................................................................................................................ 2 List of Figures ................................................................................................................................. 5 407-1A Plate Thicknesses ........................................................................................................ 5 407-1B Flange Grouping for Fabrication ................................................................................ 5 407-1C Girder Weld Splice Details ......................................................................................... 5 407-1D Safety Handrail Details ............................................................................................... 5 407-1E Bearing Restraints ....................................................................................................... 5 407-2A Weathering Steel (Paint Limits) .................................................................................. 5 407-2B Drip Bar Details .......................................................................................................... 5 407-4A Annual Traffic Growth Rates ...................................................................................... 5 407-4B Schematic of Top Flange -
Steel Bridge Design Handbook Vol. 13
U.S. Department of Transportation Federal Highway Administration Steel Bridge Design Handbook Bracing System Design Publication No. FHWA-HIF-16-002 - Vol. 13 December 2015 FOREWORD This handbook covers a full range of topics and design examples intended to provide bridge engineers with the information needed to make knowledgeable decisions regarding the selection, design, fabrication, and construction of steel bridges. Upon completion of the latest update, the handbook is based on the Seventh Edition of the AASHTO LRFD Bridge Design Specifications. The hard and competent work of the National Steel Bridge Alliance (NSBA) and prime consultant, HDR, Inc., and their sub-consultants, in producing and maintaining this handbook is gratefully acknowledged. The topics and design examples of the handbook are published separately for ease of use, and available for free download at the NSBA and FHWA websites: http://www.steelbridges.org, and http://www.fhwa.dot.gov/bridge, respectively. The contributions and constructive review comments received during the preparation of the handbook from many bridge engineering processionals across the country are very much appreciated. In particular, I would like to recognize the contributions of Bryan Kulesza with ArcelorMittal, Jeff Carlson with NSBA, Shane Beabes with AECOM, Rob Connor with Purdue University, Ryan Wisch with DeLong’s, Inc., Bob Cisneros with High Steel Structures, Inc., Mike Culmo with CME Associates, Inc., Mike Grubb with M.A. Grubb & Associates, LLC, Don White with Georgia Institute of Technology, Jamie Farris with Texas Department of Transportation, and Bill McEleney with NSBA. Joseph L. Hartmann, PhD, P.E. Director, Office of Bridges and Structures Notice This document is disseminated under the sponsorship of the U.S. -
Over Jones Falls. This Bridge Was Originally No
The same eastbound movement from Rockland crosses Bridge 1.19 (miles west of Hollins) over Jones Falls. This bridge was originally no. 1 on the Green Spring Branch in the Northern Central numbering scheme. PHOTO BY MARTIN K VAN HORN, MARCH 1961 /COLLECTION OF ROBERT L. WILLIAMS. On October 21, 1959, the Interstate Commerce maximum extent. William Gill, later involved in the Commission gave notice in its Finance Docket No. streetcar museum at Lake Roland, worked on the 20678 that the Green Spring track west of Rockland scrapping of the upper branch and said his boss kept would be abandoned on December 18, 1959. This did saying; "Where's all the steel?" Another Baltimore not really affect any operations on the Green Spring railfan, Mark Topper, worked for Phillips on the Branch. Infrequently, a locomotive and a boxcar would removal of the bridge over Park Heights Avenue as a continue to make the trip from Hollins to the Rockland teenager for a summer job. By the autumn of 1960, Team Track and return. the track through the valley was just a sad but fond No train was dispatched to pull the rail from the memory. Green Spring Valley. The steel was sold in place to the The operation between Hollins and Rockland con- scrapper, the Phillips Construction Company of tinued for another 11/2 years and then just faded away. Timonium, and their crews worked from trucks on ad- So far as is known, no formal abandonment procedure jacent roads. Apparently, Phillips based their bid for was carried out, and no permission to abandon was the job on old charts that showed the trackage at its ' obtained. -
G 13.1 Guidelines for Steel Girder Bridge Analysis.Pdf
G13.1 Guidelines for Steel Girder Bridge Analysis 2nd Edition American Association of State Highway Transportation Officials National Steel Bridge Alliance AASHTO/NSBA Steel Bridge Collaboration Copyright © 2014 by the AASHTO/NSBA Steel Bridge Collaboration All rights reserved. ii G13.1 Guidelines for Steel Girder Bridge Analysis PREFACE This document is a standard developed by the AASHTO/NSBA Steel Bridge Collaboration. The primary goal of the Collaboration is to achieve steel bridge design and construction of the highest quality and value through standardization of the design, fabrication, and erection processes. Each standard represents the consensus of a diverse group of professionals. It is intended that Owners adopt and implement Collaboration standards in their entirety to facilitate the achievement of standardization. It is understood, however, that local statutes or preferences may prevent full adoption of the document. In such cases Owners should adopt these documents with the exceptions they feel are necessary. Cover graphics courtesy of HDR Engineering. DISCLAIMER The information presented in this publication has been prepared in accordance with recognized engineering principles and is for general information only. While it is believed to be accurate, this information should not be used or relied upon for any specific application without competent professional examination and verification of its accuracy, suitability, and applicability by a licensed professional engineer, designer, or architect. The publication of the material contained herein is not intended as a representation or warranty of the part of the American Association of State Highway and Transportation Officials (AASHTO) or the National Steel Bridge Alliance (NSBA) or of any other person named herein, that this information is suitable for any general or particular use or of freedom from infringement of any patent or patents. -
Difference Between Deck Type and Through Type Bridge and Their Components
Difference between Deck Type and Through Type Bridge and their Components Naveen Choudhary 1 DEFERENCE BETWEEN DECK TYPE AND THROUGH TYPE RAILWAY BRIDGES • Deck-type bridges refer to those in which the road deck is carried on the top flange or on top of the supporting girders. • Through type bridge - The carriageway rests at the bottom level of the main load carrying members. In the through type plate girder bridge, the roadway or railway is placed at the level of bottom flanges. Mr. Naveen Choudhary, GEC Ajmer 2 DEFERENCE BETWEEN DECK TYPE AND THROUGH TYPE RAILWAY BRIDGES Mr. Naveen Choudhary,GEC Ajmer 3 DEFERENCE BETWEEN DECK TYPE AND THROUGH TYPE RAILWAY BRIDGES Through type deck bridge Mr. Naveen Choudhary,GEC Ajmer 4 DEFERENCE BETWEEN DECK TYPE AND THROUGH TYPE RAILWAY BRIDGES Mr. Naveen Choudhary,GEC Ajmer 5 DEFERENCE BETWEEN DECK TYPE AND THROUGH TYPE RAILWAY BRIDGES Mr. Naveen Choudhary,GEC Ajmer 6 Through Type Bridge Mr. Naveen Choudhary,GEC Ajmer 7 Through Type Bridge Mr. Naveen Choudhary,GEC Ajmer 8 Through Type Bridge Mr. Naveen Choudhary,GEC Ajmer 9 Deck Type Bridge Mr. Naveen Choudhary,GEC Ajmer 10 Deck Type Bridge Mr. Naveen Choudhary,GEC Ajmer 11 Deck Type Bridge Mr. Naveen Choudhary,GEC Ajmer 12 Cross-Section deck type bridge Mr. Naveen Choudhary,GEC Ajmer 13 Normal span ranges of bridge system Mr. Naveen Choudhary,GEC Ajmer 14 Normal span ranges of bridge system TYPE Maximum Span 500 m Steel arch bridge 240 m Steel bow-string girder bridge 1200 m Steel cable suspension bridge 30 m Steel plate girder 10 m Steel rolled beam bridge 180 m Steel truss bridge Mr. -
Wisdot Bridge Manual Chapter 24 – Steel Girder Structures
WisDOT Bridge Manual Chapter 24 – Steel Girder Structures Table of Contents 24.1 Introduction ...................................................................................................................... 5 24.1.1 Types of Steel Girder Structures ............................................................................... 5 24.1.2 Structural Action of Steel Girder Structures .............................................................. 5 24.1.3 Fundamental Concepts of Steel I-Girders ................................................................. 5 24.2 Materials ........................................................................................................................ 11 24.2.1 Bars and Plates ...................................................................................................... 12 24.2.2 Rolled Sections ....................................................................................................... 12 24.2.3 Threaded Fasteners ............................................................................................... 12 24.2.3.1 Bolted Connections ......................................................................................... 13 24.2.4 Quantity Determination ........................................................................................... 14 24.3 Design Specification and Data ....................................................................................... 15 24.3.1 Specifications ........................................................................................................ -
Plate Girder
3/13/2018 CE 6321 Bridge Structure PLATE GIRDER Dr. AZ Department of Civil Engineering Brawijaya University Introduction These girders are usually fabricated from welded plates and thus are called "Plate Girders". Plate girders may be defined as structural members that resist loads primarily in bending and shear. Although shaped similarly to the commonly used hot-rolled steel I-beams, plate girders differ from them in that they are fabricated from plates, and sometimes angles, that are joined together to form I- shapes. 1 3/13/2018 Introduction (cont’d) Several cross sections may be used for plate girders as shown in Fig. 1. Early plate girders were fabricated by riveting, Fig. 1(a). Their flanges consisted of two angles riveted to the web ends and cover plates riveted to the outstanding legs of the angles. Structural welding, which began to be widely used in the 1950s, has significantly simplified the fabrication of plate girders. Modern plate girders are normally fabricated by welding together two flange plates and a web plate as shown in Fig. 1(b), other variations are possible as shown in Fig. 1(c). Introduction (cont’d) Fig. 1 Cross sections of plate girders 2 3/13/2018 Introduction (cont’d) In common, section used for plate girders are shown in Fig. 2. It shows the simplest form of plate girder, Fig. 2(a). In case, the simple section cannot take the load. Sufficient flange material, additional plates are riveted to outstanding legs of angles as shown in Fig. 2(b) and 2(c). When number of cover plates become excess then the section of plate girder is modified. -
An Investigation of a Prefabricated Steel Truss Girder Bridge with A
AN INVESTIGATION OF A PREFABRICATED STEEL TRUSS GIRDER BRIDGE WITH A COMPOSITE CONCRETE DECK by Tyler William Kuehl A thesis submitted in partial fulfillment of the requirements for the degree of Master of Science in Civil Engineering MONTANA STATE UNIVERSITY Bozeman, Montana April 2018 ©COPYRIGHT by Tyler William Kuehl 2018 All Rights Reserved ii ACKNOWLEDGEMENTS I would like to express the upmost gratitude to my advisor, Dr. Damon Fick, who aided me in my coursework and research during my time at Montana State University. I would also like to recognize the other members of my committee, Dr. Jerry Stephens, Dr. Mike Berry, and Mr. Anders Larsson for their contributions to my research and education. An additional note of gratitude is extended to the various other professors and graduate students who helped with my research and education along the way. Thank you to the Montana Department of Transportation who provided the funding for the research. Lastly, I would like to extend a thank you to my wife, Alyson Kuehl, who has stood by my side through the many years of schooling and came on this adventure of moving across the country to Montana. iii TABLE OF CONTENTS 1. INTRODUCTION .........................................................................................................1 Description of Proposed Prefabricated Bridge System ..................................................1 Summary of Work..........................................................................................................3 2. LITERATURE REVIEW ..............................................................................................5 -
Chapter 9 Steel Plate Girders
BRIDGE DESIGN PRACTICE ● FEBRUARY 2015 CHAPTER 9 STEEL PLATE GIRDERS TABLE OF CONTENTS 9.1 INTRODUCTION ............................................................................................................... 1 9.2 STRUCTURAL MATERIALS ........................................................................................... 1 9.2.1 Structural Steel ...................................................................................................... 1 9.2.2 Concrete ................................................................................................................ 2 9.3 SPAN AND FRAMING ARRANGEMENT ...................................................................... 2 9.3.1 Span Configuration ............................................................................................... 2 9.3.2 Girder Spacing ....................................................................................................... 2 9.3.3 Diaphragms and Cross Frames .............................................................................. 3 9.3.4 Lateral Bracing ...................................................................................................... 5 9.3.5 Field Splice Locations ........................................................................................... 5 9.3.6 Expansion Joints and Hinges ................................................................................. 5 9.4 SECTION PROPORTION .................................................................................................. 6 9.4.1 -
Modeling a Plate Girder Bridge
Modeling a Deck Plate Girder Bridge By Charlie Crawford, MMR Bridges are everywhere. This is the St. Anthony Falls Bridge in Minneapolis. It is a post-tensioned precast concrete box girder bridge. It’s on the same location as the I-35W Bridge before it’s 2007 collapse. I-35W bridge after the 2007 collapse. I-35 Bridge showing bowed gussets in 2003. The investigation found that the failure of only one gusset would cause the bridge to collapse. Not much redundancy. In Minneapolis, there’s really quite a variety. The suspension bridge carries Hennepin Avenue. The stone arch bridge was built in 1883 for the Great Northern Railroad. And behind the open-spandrel concrete arch Third Avenue Bridge is another old timer. There it is, a deck plate girder bridge, the 1884 Minneapolis BNSF Rail Bridge. However due to their strength and redundancy, relatively few deck plate girder bridges have failed. This is the former Herkimer, Newport and Poland narrow gauge bridge over West Canada Creek. Note no footing and a standard splice plate. Since they are difficult to dismantle, a section was cut out on each end and it was just left in place. My favorite deck plate girder bridge: On the Adirondack Division over Twitchell Creek This is a three section bridge(2 60 footers and a 75 footer.) That’s my son enjoying the hike. The bridge is reached after a two mile hike. It crosses Twitchell Creek with 40’ of clearance. It has a concrete bed for ballast and ties and four platforms. NMRA Data Sheets: a great member benefit They are available to members the website, some quite dated and some with valuable prototype information. -
A Context for Common Historic Bridge Types
A Context For Common Historic Bridge Types NCHRP Project 25-25, Task 15 Prepared for The National Cooperative Highway Research Program Transportation Research Council National Research Council Prepared By Parsons Brinckerhoff and Engineering and Industrial Heritage October 2005 NCHRP Project 25-25, Task 15 A Context For Common Historic Bridge Types TRANSPORATION RESEARCH BOARD NAS-NRC PRIVILEGED DOCUMENT This report, not released for publication, is furnished for review to members or participants in the work of the National Cooperative Highway Research Program (NCHRP). It is to be regarded as fully privileged, and dissemination of the information included herein must be approved by the NCHRP. Prepared for The National Cooperative Highway Research Program Transportation Research Council National Research Council Prepared By Parsons Brinckerhoff and Engineering and Industrial Heritage October 2005 ACKNOWLEDGEMENT OF SPONSORSHIP This work was sponsored by the American Association of State Highway and Transportation Officials in cooperation with the Federal Highway Administration, and was conducted in the National Cooperative Highway Research Program, which is administered by the Transportation Research Board of the National Research Council. DISCLAIMER The opinions and conclusions expressed or implied in the report are those of the research team. They are not necessarily those of the Transportation Research Board, the National Research Council, the Federal Highway Administration, the American Association of State Highway and Transportation Officials, or the individual states participating in the National Cooperative Highway Research Program. i ACKNOWLEDGEMENTS The research reported herein was performed under NCHRP Project 25-25, Task 15, by Parsons Brinckerhoff and Engineering and Industrial Heritage. Margaret Slater, AICP, of Parsons Brinckerhoff (PB) was principal investigator for this project and led the preparation of the report.