INNOVATION Eric Divito Master Class 102 Derek Trucks
Total Page:16
File Type:pdf, Size:1020Kb
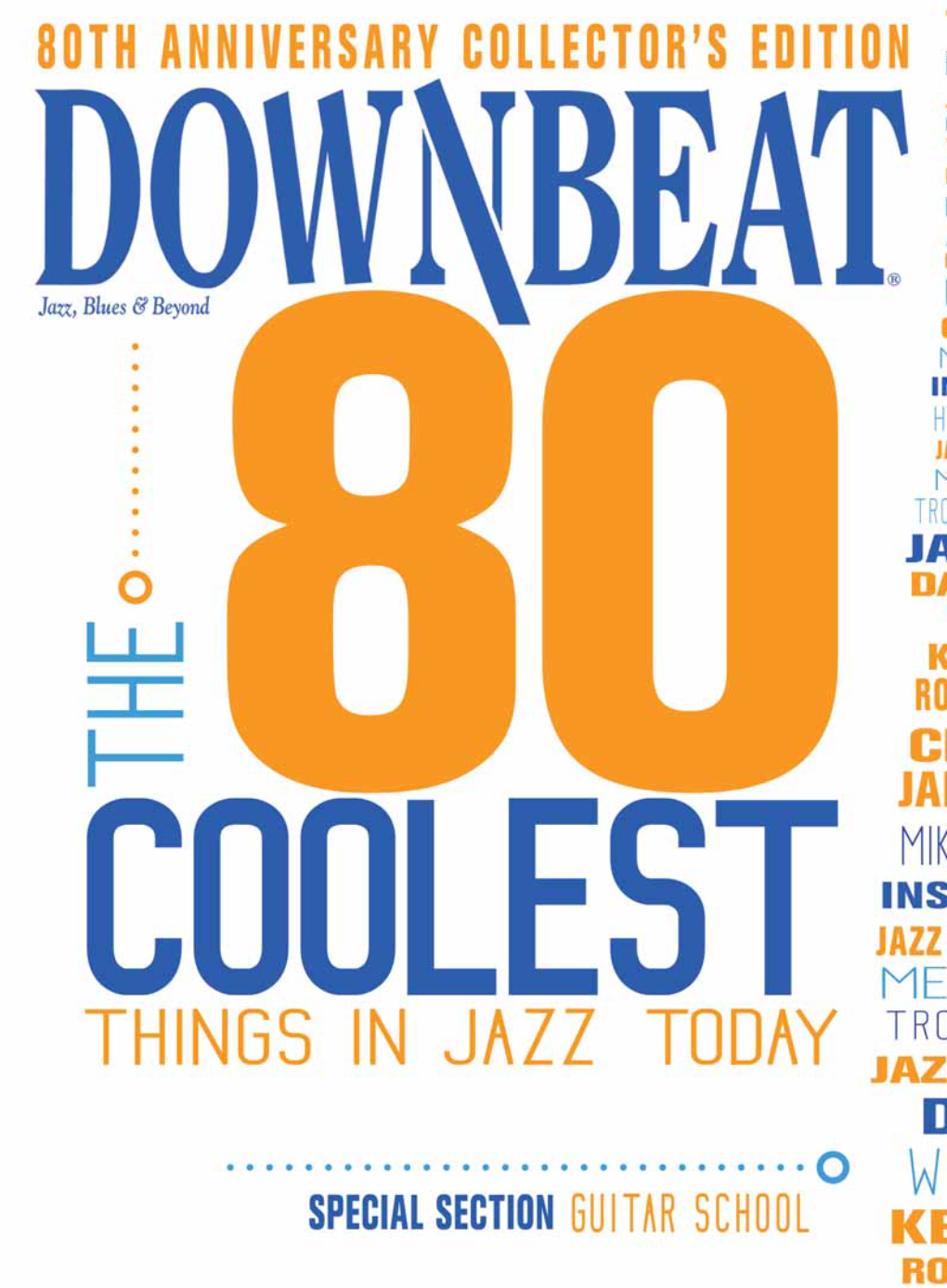
Load more
Recommended publications
-
Parker 2003 Nitefly M for Sale
Technical Description • Body o Wood: Mahogany o Finish: Polyurethane • Neck o Wood: Mahogany o Scale: 25.5 in. o Radius: 10-13 in. Conical form o Fingerboard: Composite o Nut width: 1.68 in. o Finish: Polyurethane o Frets: 22 Stainless steel o Fret size: .052 in. High .0103 in. Wide • Nut: GraphTech • Bridge: Parker cast aluminum vibrato bridge, with stainless steel saddles • String Spacing: 2.14 in. wide at bridge, 1.38 in. wide at nut • Tuners: Sperzel Locking • Electronics o Pickups: 2 Custom DiMarzio humbuckers, 6-element Fishman piezo system Mag Volume: 500k Mag Tone: 500k Piezo Volume: 2k Push/pull coil tap selection on the magnetic tone knob (M only) o 3-Way Mag selector switch: (position 1 closest to neck) Neck humbucker Inside coil of both humbuckers (in series) Bridge humbucker o 3-Way Mag/Piezo Switch: Mag pickups only Piezo and mag pickups Piezo pickups • Preamp/Mixer: Custom designed Fishman active circuit • Battery Life: Estimated 200 hours • Output: Split stereo or summed mono operation (Includes Stereo Cable) • Factory Setup o String Gauge: D'Addario EXL120 .09-.42 (Elixir SuperLite’s installed) o String Height: .050 in. treble .070 in. bass, at 12th fret (while fretted at 1st) Technical Description NiteFly M Specific Detail The M model sports a satin-finished mahogany body and bolt-on neck. Loaded with tonal possibilities, it's equipped with a Fishman six-element piezo pickup system that's coupled to a Powerchip active pre-amp with 'smart switching" jack for stereo or summed mono output. The two DiMarzio custom-wound humbuckers are controlled with a three- position magnetic pickup selector and push-pull coil-split switch. -
Marquetry on Drawer-Model Marionette Duo-Art
Marquetry on Drawer-Model Marionette Duo-Art This piano began life as a brown Recordo. The sound board was re-engineered, as the original ribs tapered so soon that the bass bridges pushed through. The strings were the wrong weight, and were re-scaled using computer technology. Six more wound-strings were added, and the weights of the steel strings were changed. A 14-inch Duo-Art pump, a fan-expression system, and an expression-valve-size Duo-Art stack with a soft-pedal compensation lift were all built for it. The Marquetry on the side of the piano was inspired by the pictures on the Arto-Roll boxes. The fallboard was inspired by a picture on the Rhythmodic roll box. A new bench was built, modeled after the bench originally available, but veneered to go with the rest of the piano. The AMICA BULLETIN AUTOMATIC MUSICAL INSTRUMENT COLLECTORS’ ASSOCIATION SEPTEMBER/OCTOBER 2005 VOLUME 42, NUMBER 5 Teresa Carreno (1853-1917) ISSN #1533-9726 THE AMICA BULLETIN AUTOMATIC MUSICAL INSTRUMENT COLLECTORS' ASSOCIATION Published by the Automatic Musical Instrument Collectors’ Association, a non-profit, tax exempt group devoted to the restoration, distribution and enjoyment of musical instruments using perforated paper music rolls and perforated music books. AMICA was founded in San Francisco, California in 1963. PROFESSOR MICHAEL A. KUKRAL, PUBLISHER, 216 MADISON BLVD., TERRE HAUTE, IN 47803-1912 -- Phone 812-238-9656, E-mail: [email protected] Visit the AMICA Web page at: http://www.amica.org Associate Editor: Mr. Larry Givens VOLUME 42, Number -
Designing and Building an Electric Baritone Guitar
Hendrik Gideonse Audio Research December 14, 2008 Designing an Electric Baritone Guitar 0 Anatomy of a Guitar ................................................................................................... 2 1 Introduction ................................................................................................................. 3 2 Baritone History .......................................................................................................... 3 3 Problems with Existing Designs ................................................................................. 5 3.1 String Tension ..................................................................................................... 5 3.2 Balance, Ease of Playing 1st Position Chords and Bridge Position .................... 7 3.3 Rigidity for Tone and Sustain ........................................................................... 11 4 Designing the Baritone Guitar .................................................................................. 12 4.1 Woods, Tone and Rigidity ................................................................................ 13 4.2 Angled Headstock and ‘V’ Neck Contour ........................................................ 16 4.3 Headstock Shapes ............................................................................................. 19 4.4 Joining the Neck to the Body ............................................................................ 24 4.5 Body Shape ...................................................................................................... -
Design, Manufacture and Analysis of a Carbon Fiber Epoxy Composite Acoustic Guitar
Design, Manufacture and Analysis of a Carbon Fiber Epoxy Composite Acoustic Guitar Stephen M. Probert A thesis submitted in partial fulfillment of the requirements for the degree of Master of Science in Mechanical Engineering University of Washington 2007 Program Authorized to Offer Degree: Mechanical Engineering University of Washington Graduate School This is to certify that I have examined this copy of a master’s thesis by Stephen M. Probert and have found that it is complete and satisfactory in all respects, and that any and all revisions required by the final examining committee have been made. Committee Members: ________________________________________________ Per Reinhall ________________________________________________ Vipin Kumar ________________________________________________ Vladimir Chaloupka Date:______________________________________ In presenting this thesis in partial fulfillment of the requirements for a master’s degree at the University of Washington, I agree that the Library shall make its copies freely available for inspection. I further agree that extensive copying of this thesis is allowable only for scholarly purposes, consistent with “fair use” as prescribed in the U.S. Copyright Law. Any other reproduction for any purposes or by any means shall not be allowed without my written permission. Signature _____________________________ Date _________________________________ TABLE OF CONTENTS Page List of Figures...................................................................................................................v -
The Fender 5G8 Twin-Amp
Mountainview Publishing, LLC INSIDE the Are you making it as a guitarist? It ain’t up to “them” – it’s up to you… Why great chops, all the The Player’s Guide to Ultimate Tone TM gear, a solid resumé, cool $10.00 US, September 2005/VOL.6 NO.11 Report songs & a great recording still may not get you noticed in the music biz today… Johnny A The Johnny A Interview “When you strum a guitar you have everything – rhythm, bass, lead and melody.” 9 – David Gilmore Is this love or confusion? The Marshall 30th Of all the guitars you have ever owned, has one seemed to suit you more than all the others? Did Anniversary Amp – you keep it, or has your memory of perfection only deepened with every guitar that failed to blue, brass-plated, 3 measure up to the one that got away? channels, and why it’s the only amp in Johnny A’s rig… Marshall’s Nick Bowcott on the 30th Anniversary 11 Review… Gibson’s Johnny A Signature Guitar This one does it all 13 The Gibson ‘57 Classic humbucking pickup with original designer J.T. Ribiloff 14 Review… The new Eric Johnson Signature Stratocaster… Long time coming, affordable, and the pickups rock… 16 Most of us have been guilty of letting great guitars go due to a temporary cash crunch or the The mythical low-power fever that clouds rational judgment when we impulsively sell an instrument to acquire the next brown Twin Part III… one. How many players traded a vintage goldtop, ‘59 burst or ‘50s Strat or Telecaster for an acrylic Why it never existed and Dan Armstrong, Kustom tuck n’ roll PA gear for the band, a Sunn head, or simply for the sake of how to build your own! change? www.tonequest.com cover story Consider the fickle, shifting fads that have alternately placed nothing, on-again-off-again stops and starts typical of the various Fender, Gretsch, Gibson and Martin guitars among rock music scene in the ‘70s, ‘80s and ‘90s. -
Nycemf 2021 Program Book
NEW YORK CITY ELECTROACOUSTIC MUSIC FESTIVAL __ VIRTUAL ONLINE FESTIVAL __ www.nycemf.org CONTENTS DIRECTOR’S WELCOME 3 STEERING COMMITTEE 3 REVIEWING 6 PAPERS 7 WORKSHOPS 9 CONCERTS 10 INSTALLATIONS 51 BIOGRAPHIES 53 DIRECTOR’S NYCEMF 2021 WELCOME STEERING COMMITTEE Welcome to NYCEMF 2021. After a year of having Ioannis Andriotis, composer and audio engineer. virtually all live music in New York City and elsewhere https://www.andriotismusic.com/ completely shut down due to the coronavirus pandemic, we decided that we still wanted to provide an outlet to all Angelo Bello, composer. https://angelobello.net the composers who have continued to write music during this time. That is why we decided to plan another virtual Nathan Bowen, composer, Professor at Moorpark electroacoustic music festival for this year. Last year, College (http://nb23.com/blog/) after having planned a live festival, we had to cancel it and put on everything virtually; this year, we planned to George Brunner, composer, Director of Music go virtual from the start. We hope to be able to resume Technology, Brooklyn College C.U.N.Y. our live concerts in 2022. Daniel Fine, composer, New York City The limitations of a virtual festival meant that we could plan only to do events that could be done through the Travis Garrison, composer, Music Technology faculty at internet. Only stereo music could be played, and only the University of Central Missouri online installations could work. Paper sessions and (http://www.travisgarrison.com) workshops could be done through applications like zoom. We hope to be able to do all of these things in Doug Geers, composer, Professor of Music at Brooklyn person next year, and to resume concerts in full surround College sound. -
Adventuring with Books: a Booklist for Pre-K--Grade 6. 1997 Edition
DOCUMENT RESUME ED 406 672 CS 215 782 AUTHOR Sutton, Wendy K., Ed. TITLE Adventuring with Books: A Booklist for Pre-K--Grade 6. 1997 Edition. NCTE Bibliography Series. INSTITUTION National Council of Teachers of English, Urbana, Ill. REPORT NO ISBN-0-8141-0080-5; ISSN-1051-4740 PUB DATE 97 NOTE 447p.; Foreword by Patricia MacLachlan. For the 1993 (Tenth) Edition, see ED 362 878. Also prepared by the Committee To Revise the Elementary School Booklist. AVAILABLE FROM National Council of Teachers of English, 1111 West Kenyon Road, Urbana, IL 61801-1096; phone: 1-800-369-6283 (Stock No. 00805: $16.95 members, $22.95 nonmembers). PUB TYPE Reference Materials Bibliographies (131) EDRS PRICE MFO1 /PC18 Plus Postage. DESCRIPTORS *Adolescent Literature; Annotated Bibliographies; *Childrens Literature; Elementary Education; Fiction; Nonfiction; Picture Books; Poetry; Preschool Education; Reading Interests; *Reading Material Selection; *Recreational Reading IDENTIFIERS Historical Fiction ABSTRACT This book contains descriptions of over 1,200 books published between 1993 and 1995, all chosen for their high quality and their interest to children, parents, teachers, and librarians. Materials described in the book include fiction, nonfiction, poetry, picture books, young adult novels, and interactive CD-ROMs. Individual book reviews in the book include a description of the book's form and content, information on the type and medium of the illustrations, suggestions on how the book might best be incorporated into the elementary school curriculum, and full bibliographic information. A center insert in the book displays photographs of many of the titles, allowing readers to see the quality of the illustrations for themselves. -
Design of a Composite Guitar Master Thesis Report Max Roest
Technische Universiteit Delft Design of a composite guitar Master Thesis Report Max Roest Design of a composite guitar Master Thesis Report by Max Roest Student number: 4084217 Hand-in date: August 17, 2016 Supervisor: dr. ir. O.K. Bergsma, TU Delft Summary Today’s acoustic guitars are getting increasingly expensive due to the worsening availability of the highest quality woods. Composites show great promise in replacing wood in acoustic guitars as they are lightweight, are not as sensitive to environmental effects and are much stronger. Current composite guitars however do not sound as good as their wooden counterparts. Therefore this thesis research has been set-up to create a composite material that can match wood acoustically and therefore have all the benefits in terms of environ- mental sensitivity and strength while not compromising the sound quality of the instrument. A new com- posite is developed and extensively tested. This composite consists of a carbon fibre reinforced polyurethane foam and has a comparable acoustic response to high quality spruce used for guitar soundboards. With this new composite a complete composite guitar is designed, manufactured and tested. The psychoacoustic anal- ysis performed showed that the new composite guitar is considerably more wood like in its sound compared to current carbon fibre acoustic guitars. ii Preface Max Roest Delft, July 2016 It is over 20 years ago that I received my first guitar. A few months later, at the age of 4, I had my first guitar lessons. Now at the age of 24, it is hard to remember any period in my life where guitars and music have not played a major role in my life. -
Report Hamer
Mountainview Publishing, LLC INSIDE the The Jol Dantzig Interview... Hamer’s co- The Player’s Guide to Ultimate Tone TM founder talks $10.00 US, December 2004/VOL.6 NO.2 Report about launching the original ‘con- temporary vin- tage guitars,’ the Hamer lure of the sight- gag design, & “Among God's creatures two, the dog and the guitar, why building gui- have taken all the sizes and all the shapes, in order tars the hard way not to be separated from man.” —Andrés Segovia still matters. During the past 30 years, the history of guitar design has been meticulously documented down to the variances found in pickguard screws and peghead pitch by a gaggle of giddy guitar enthusiast-authors around the world. It seems as if 13 nothing has escaped their scrutiny, while the Internet has provided a forum to Hamer USA further discuss, explore, debate and speculate on the stylistic nuances of the Guitar Reviews! most popular musical instrument of our time. The Monaco But many inspiring stories remain untold in the guitar industry – stories of com- Elite, Monaco III panies that have remained true to their founding principles of quality, innovative & Phantom design and old world craftsmanship, even when economic conditions have Custom... placed such values in peril and compelled others to abandon quality for the bot- tom line. Jol Dantzig and Paul Hamer launched Hamer Guitars in 1975 as a survival 17 strategy to supplement their income as musicians, collectors and used gui- Jason Lollar... tar dealers. In the process, they produced instruments clearly the truth about superior to those made by the very companies that had inspired them. -
GUITAR SHOW Miami Beach Convention Center April 11Th 13Th Sponsored By: Allied Lutherie Healdsburg, CA Dream Guitars Weaverville, NC Glades Guitars Pembroke Pines, FL
100s of hand-built Guitars 100s of Acoustic Concerts Master Classes and Seminars Win a $5,000 Solomon Guitar ! South Florida’s Leading GUITAR SHOW Miami Beach Convention Center April 11th 13th Sponsored by: Allied Lutherie Healdsburg, CA Dream Guitars Weaverville, NC Glades Guitars Pembroke Pines, FL newportguitarfestmb.com Welcome to Newport Guitar Festival Miami Beach Welcome Ticket Prices Parking in Miami Beach of Content Table Tickets will be Welcome to the Newport Guitar Festival in Miami Beach. Musicians and Guitar lovers will recognize available at the door and through many of the world’s top guitar-makers (luthiers) and players in this unprecedented gathering in South Florida—and perhaps the world. We have collectable guitars for sale and display, hundreds of mini- concerts, seminars, and master classes—something for everyone who loves guitar, an most everything free with admission. One day pass $20.00 Music lovers will be introduced to the renaissance in guitar-making and acoustic music which has Two day pass been quietly building to a crescendo for the past 15 years, creating a new golden age of guitar in $36.00 our time. Art Collectors and other investors will learn about instruments which have value for their Three day pass mastery, rare materials, and ground-breaking inlay, which consistently far out-perform everything from $48.00 Gold to the S&P 500. Sponsors While providing “art that sings” for the world’s top musicians as well as enthusiastic amateurs, these guitars are recognized by museums around the world. Imagine if you could have bought a Stradi- varius Violin from Stradivarius! Well, at this show you can come very close (and hear Paganini dem- onstrate it!). -
Adrian Belew Signature Fly Manual
ADRIAN BELEW SIGNATURE FLY Owner’S MANUAL IMPORTANT! Before using your Parker Adrian Belew Signature Fly guitar please read these Safety Instructions. Although the design of this instrument has been extensively field tested by Adrian Belew, while on the road with King Crimson and other acts, it is important to remember that it has far more on-board electronics than any other guitar ever built, and should be treated with proper care & respect. 1. Please be VERY CAREFUL when installing new strings to pull them up and over the piezo bridge saddles when pushing them through the tremolo tailpiece. If you accidentally jam a string under a piezo saddle, there is a very good chance of breaking the connection to that transducer. Replacing a saddle is not something you would want to do while on the road! 2. Don’t force or jam the connectors or controls. If something doesn’t feel right or if you have any other concerns, show it to your technician sooner rather than later! 3. Avoid extremes of temperature, humidity, and vibration. 4. Check your shoulder straps, guitar stands, and other accessories routinely to be sure they are up to the job. 5. If you let others play or handle the instrument, be sure they understand the unique status and importance of this design before they take the wheel. 6. Don’t forget to turn the standby switch on the back cover OFF when you put the instrument away. Remove the 9 Volt battery if you’re not going to play it for a while. -
THE UNIVERSITY of QUEENSLAND Bachelor of Engineering Thesis
THE UNIVERSITY OF QUEENSLAND Bachelor of Engineering Thesis The Manufacture and Acoustic Analysis of Hemp/Agave Fibre Reinforced Vinyl Ester Bio-Composite Guitar Student Name: Mohammad Noor Farhan ABD RAHIM Course Code: MECH4500 Supervisor: Dr. Luigi Vandi Prof. Martin Veidt Submission date: 28th October 2016 A thesis submitted in partial fulfilment of the requirements of the Bachelor of Engineering degree in Mechanical Engineering UQ Engineering Faculty of Engineering, Architecture and Information Technology Acknowledgement In completing this thesis report, I would like to express my sincerest appreciation to the people that helped me in making this thesis a success. Without their help and guidance, this thesis project would not achieve the level that it has. Special gratitude goes to Dr Luigi Vandi, my supervisor whose guidance and expertise enabled the project to be carried with ease and controlled manner. Without his insight and supervision, this project would not have been possible. Many thanks to Professor Martin Veidt, who provide essential guidance and feedback on various aspects of the project throughout the year. I would also like to thank John Milne, UQ Composite laboratory manager, for always being ready to help and share his wide technical knowledge on manufacturing processes and composite materials as well as providing an overall positive atmosphere in the laboratory. This project would also not have been possible without the feedback and opinions from UQ Composite Group members Juan, Nico, Clement and Charles, especially during the manufacturing phase. The 2015 project group for their effort in designing the guitar mould as well as provides the results from their findings.