Steam Explosion Resistance of an Internal Core Catcher of a Nuclear Reactor Pressure Vessel
Total Page:16
File Type:pdf, Size:1020Kb
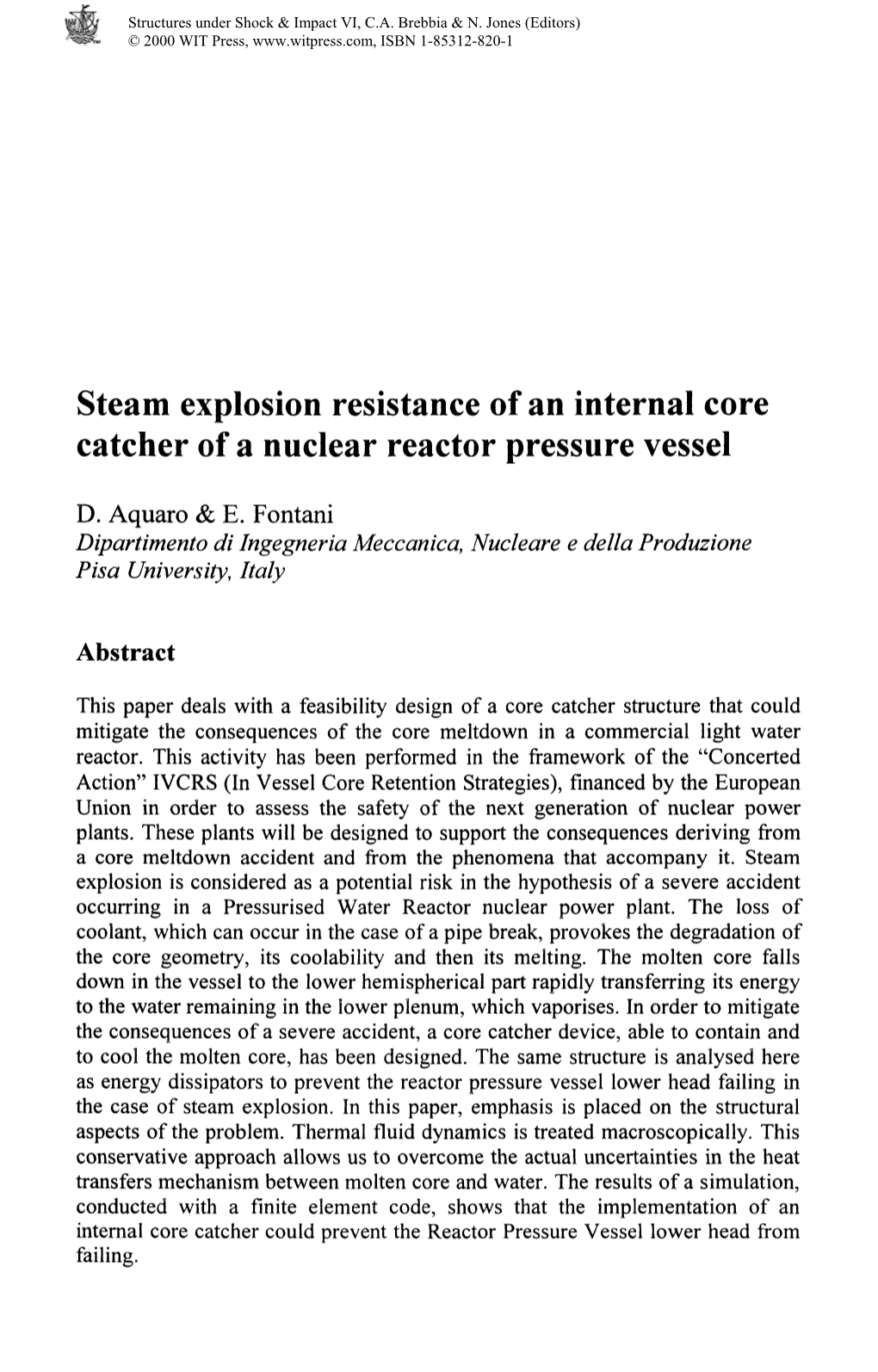
Load more
Recommended publications
-
Nuclear Reactor Realities
Page 1 of 26 Nuclear Reactor Realities NUCLEAR REACTOR REALITIES (An Australian viewpoint) PREFACE Now that steam ships are no longer common, people tend to forget that nuclear power is just a replacement of coal, oil or gas for heating water to form steam to drive turbines, or of water (hydro) to do so directly. As will be shown in this tract, it is by far the safest way of doing so to generate electricity economically in large quantities – as a marine engineer of my acquaintance is fond of saying. Recently Quantum Market Research released its latest Australian Scan (The Advertiser, Saturday April 17, 2012, p 17). It has been tracking social change by interviewing 2000 Australians annually since 1992. In the concerns in the environment category, “[a]t the top of the list is nuclear accidents and waste disposal” (44.4 per cent), while “global warming” was well down the list of priorities at No 15, with only 27.7 per cent of people surveyed rating the issue as “extremely serious.” Part of the cause of such information must be that people are slowly realising that they have been deluded by publicity about unverified computer models which indicate that man’s emissions of CO2 play a major part in global warming. They have not yet realised that the history of the dangers of civilian nuclear power generation shows the reverse of their images. The topic of nuclear waste disposal is also shrouded in reactor physics mysteries, leading to a mis-placed general fear of the unknown. In this article only nuclear reactors are considered. -
Implications of the Accident at Chernobyl for Safety Regulation of Commercial Nuclear Power Plants in the United States Final Report
NUREG-1251 Vol. I Implications of the Accident at Chernobyl for Safety Regulation of Commercial Nuclear Power Plants in the United States Final Report Main Report U.S. Nuclear Regulatory Commission p. o AVAILABILITY NOTICE Availability of Reference Materials Cited in NRC Publications Most documents cited in NRC publications will be available from one of the following sources: 1. The NRC Public Document Room, 2120 L Street, NW, Lower Level, Washington, DC 20555 2. The Superintendent of Documents, U.S. Government Printing Office, P.O. Box 37082, Washington, DC 20013-7082 3. The National Technical Information Service, Springfield, VA 22161 Although the listing that follows represents the majority of documents cited in NRC publica- tions, it is not intended to be exhaustive. Referenced documents available for inspection and copying for a fee from the NRC Public Document Room include NRC correspondence and internal NRC memoranda; NRC Office of Inspection and Enforcement bulletins, circulars, information notices, inspection and investi- gation notices; Licensee Event Reports; vendor reports and correspondence; Commission papers; and applicant and licensee documents and correspondence. The following documents in the NUREG series are available for purchase from the GPO Sales Program: formal NRC staff and contractor reports, NRC-sponsored conference proceed- ings, and NRC booklets and brochures. Also available are Regulatory Guides, NRC regula- tions in the Code of Federal Regulations, and Nuclear Regulatory Commission Issuances. Documents available from the National Technical Information Service include NUREG series reports and technical reports prepared by other federal agencies and reports prepared by the Atomic Energy Commission, forerunner agency to the Nuclear Regulatory Commission. -
Calculating Nuclear Accident Probabilities from Empirical Frequencies Minh Ha-Duong, V
Calculating nuclear accident probabilities from empirical frequencies Minh Ha-Duong, V. Journé To cite this version: Minh Ha-Duong, V. Journé. Calculating nuclear accident probabilities from empirical frequencies. Environment Systems and Decisions, Springer, 2014, 34 (2), pp.249-258. 10.1007/s10669-014-9499-0. hal-01018478v2 HAL Id: hal-01018478 https://hal.archives-ouvertes.fr/hal-01018478v2 Submitted on 21 Jul 2014 HAL is a multi-disciplinary open access L’archive ouverte pluridisciplinaire HAL, est archive for the deposit and dissemination of sci- destinée au dépôt et à la diffusion de documents entific research documents, whether they are pub- scientifiques de niveau recherche, publiés ou non, lished or not. The documents may come from émanant des établissements d’enseignement et de teaching and research institutions in France or recherche français ou étrangers, des laboratoires abroad, or from public or private research centers. publics ou privés. Distributed under a Creative Commons Attribution - NonCommercial - ShareAlike| 4.0 International License Manuscript to appear in Environment, Systems and Decisions CALCULATING NUCLEAR ACCIDENT PROBABILITIES FROM EMPIRICAL FREQUENCIES Minh Ha-Duong et Venance Journé1 2014-04-10 Summary Since there is no authoritative, comprehensive and public historical record of nuclear power plant accidents, we reconstructed a nuclear accident dataset from peer-reviewed and other literature. We found that, in a sample of five random years, the worldwide historical frequency of a nuclear major accident, defined as an INES level 7 event, is 14%. This value is 67 % to have at least one nuclear accident rated at level ≥ 4 on the INES scale. These numbers are subject to uncertainties because the fuzziness of the definition of a nuclear accident. -
The SL-1 Accident Consequences
The SL-1 Accident Consequences Key Things to Remember On the night of January 3, 1961, the SL-1 nuclear reactor, a About prototype for a military installation to be used in remote Arctic SL-1 Accident Consequences: locations, exploded, killing the three-member military crew. The crew had been performing the routine process of re-assembling 1. The SL-1’s highly enriched fuel the reactor control rod drive mechanisms during a reactor outage. had high burnup and had The SL-1 was a small 3 Mega-Watt-thermal (MWt) boiling water operated for 932 MW-days, reactor, complete with a turbine-generator and condenser building up fission products in designed to generate both electric power and building heat. 1 the fuel before the accident. 2. The SL-1 condensers were on The SL-1 was designed, constructed and initially operated by the top of the building and the Argonne National Laboratory. It was located at the Idaho reactor was in a ventilated National Laboratory, then called the National Reactor Testing building with no containment. Station. Combustion Engineering became the operating 3. About 30 percent of SL-1’s fuel contractor for the Atomic Energy Commission (now the was absent from the reactor Department of Energy) for SL-1 on February 5, 1959. vessel after the accident. 4. The AEC claimed that basically The SL-1 had first gone critical on August 1, 1958 and by only iodine-131 was in the July 1, 1959 had accumulated 160 Mega-Watt operating days radioactive plume from the (MWD). By August 21, 1960, the reactor had accumulated 680 accident. -
Ex-Vessel Steam Explosion Analysis for Pressurized Water Reactor and Boiling Water Reactor
Nuclear Engineering and Technology 48 (2016) 72e86 Available online at ScienceDirect Nuclear Engineering and Technology journal homepage: www.elsevier.com/locate/net Original Article Ex-vessel Steam Explosion Analysis for Pressurized Water Reactor and Boiling Water Reactor * Matjaz Leskovar and Mitja Ursic Jozef Stefan Institute, Jamova cesta 39, SI-1000 Ljubljana, Slovenia article info abstract Article history: A steam explosion may occur during a severe accident, when the molten core comes into Received 8 June 2015 contact with water. The pressurized water reactor and boiling water reactor ex-vessel Received in revised form steam explosion study, which was carried out with the multicomponent three- 20 August 2015 dimensional Eulerian fuelecoolant interaction code under the conditions of the Organi- Accepted 23 August 2015 sation for Economic Co-operation and Development (OECD) Steam Explosion Resolution for Available online 28 October 2015 Nuclear Applications project reactor exercise, is presented and discussed. In reactor cal- culations, the largest uncertainties in the prediction of the steam explosion strength are Keywords: expected to be caused by the large uncertainties related to the jet breakup. To obtain some Boiling Water Reactor insight into these uncertainties, premixing simulations were performed with both avail- Fuel-Coolant Interaction able jet breakup models, i.e., the global and the local models. The simulations revealed that Pressure Load weaker explosions are predicted by the local model, compared to the global model, due to Pressurized Water Reactor the predicted smaller melt droplet size, resulting in increased melt solidification and Reactor Cavity increased void buildup, both reducing the explosion strength. Despite the lower active melt Severe Accident mass predicted for the pressurized water reactor case, pressure loads at the cavity walls Steam Explosion are typically higher than that for the boiling water reactor case. -
On Vapor/Steam Explosion Analysis
THE NUCLEAR NEWS INTERVIEW Fauske and Henry: On vapor/steam explosion analysis Vapor explosions are an integral part of reactor safety evaluations when accident conditions could lead to molten fuel coming in contact with liquid coolant. he book Experimental Technical Bases for Evalu- involving these types of explosions must be evaluated ating Vapor/Steam Explosions in Nuclear Reactor in a manner consistent with the available experimen- TSafety was recently published by the American tal technical bases. Their new book, they say, provides a Nuclear Society. The authors, Hans Fauske and Robert common reference that includes the total experimental Henry, say that the possibility of vapor/steam explo- database for vapor/steam explosions, as well as informa- sions occurring at nuclear power plants is an important tion directly related to molten materials and the coolant consideration for safety assessments of events wherein a of interest. high-temperature molten mass could come into contact Early in his career, Fauske joined Argonne National with a liquid coolant. Laboratory, where he focused on reactor safety evalua- The authors stress that potential accident conditions tions for both fast and light-water reactors. Vapor explo- sions were a key element of the safety evaluations for the Fast Flux Test Fa- cility and the Clinch River Breeder Reactor designs, and steam explo- sions were an important part of the safety assessments for water-cooled reactors. Fauske left ANL in 1980 to establish, with Robert Henry and Michael Grolmes, Fauske & Associ- ates. In 2011, Fauske stepped away from management responsibilities at the company to spend more time on engineering evaluations and writing. -
SKI Report 02:16 a Review of Steam Explosions with Special Emphasis
The APRI 4 (Accident Phenomena of Risk Importance) research project is accomplished by: • Swedish Nuclear Power Inspectorate • Ringhals AB • OKG Aktiebolag • Forsmarks Kraftgrupp AB • Barsebäck Kraft AB • Teollisuuden Voima Oy (TVO) and supervised by the Project Board, consisting of: OKG Aktiebolag Mauritz Gärdinge, chairman Swedish Nuclear Power Inspectorate Oddbjörn Sandervåg Ringhals AB Anders Henoch Forsmarks Kraftgrupp AB Ingvar Berglund Barsebäcks Kraft AB Erik Larsen TVO Heikki Sjövall Contents Abstract v 1 Introduction 1 1.1 Study objectives and workscope . .................. 2 1.2 References . ............................. 3 2 Task 1: A general review of the phenomenology of a steam explosion during a postulated severe accident in nuclear power plants 4 2.1 General picture on MFCI . ......................... 4 2.1.1 Fuel Coolant Interaction (FCI) . .................. 5 2.2 Molten fuel-coolant premixing . .................. 7 2.2.1 Status of current research and recent results . ........... 7 2.2.2 Inter-relations and uncertainties of molten fuel-coolant premixing . 9 2.2.3 Self-limiting mechanisms in melt-water premixing . .... 11 2.3 Molten fuel-coolant triggering . .................. 12 2.3.1 Status of current research and recent results . ........... 12 2.3.2 Triggering experiments . .................. 14 2.3.3 Analytical work on triggering . .................. 17 2.3.4 Conclusions . ............................. 18 i 2.4 Results from steam explosion experiments with different melt materials . 19 2.5 Computational investigation of steam explosion . ........... 20 2.5.1 PM-ALPHA and ESPROSE.m codes . ........... 20 2.5.2 MC3D code . ............................. 22 2.5.3 Computations of the KROTOS tests with the codes COMETA, TEXAS and SEURBNUK/EURDYN . .................. 23 2.6 Summary . ............................. 24 2.6.1 Premixing/Quenching . -
Historical Loss Experiences in the Global Power Industry August 2014 Contents
MARSH RISK MANAGEMENT RESEARCH HISTORICAL LOSS EXPERIENCES IN THE GLOBAL POWER INDUSTRY AUGUST 2014 CONTENTS 1 INTRODUCTION 2 PART ONE: PRINCIPLES OF GENERATING ELECTRICITY 8 PART TWO: HISTORICAL LOSSES 48 CONCLUSION HISTORICAL LOSS EXPERIENCES IN THE GLOBAL POWER INDUSTRY ii marsh.com MARSH RISK MANAGEMENT RESEARCH INTRODUCTION At Marsh, our claims management and power industry experience enables us to present an accurate description of the types of events that commonly lead to insurance claims. To compile this study, we used data and an analysis of global trends that many power clients will already be acquainted with. The purpose of this document is to provide commentary on the world of power generation, the risks affecting that industry, and the importance of effective risk management in preventing or mitigating these risks. The report is divided into two parts: ȫ Part one provides a brief overview of some of the key technologies being used in power generation, including details of some areas that are either emergent or in the research-and-development stage at the time of writing. ȫ Part two features a narrative description of some of the historical loss experiences that have affected the power generation industry in recent years. It may be helpful to review this document along with the following recent Marsh Risk Management Research briefings on power generation: ȫ The Impact of Large Losses in the Global Power Industry. ȫ Common Causes of Large Losses in the Global Power Industry. We trust that you will find this document both illuminating and helpful as you consider the risks your own organization faces. -
Steam Handbook
Products Solutions Services Steam Handbook An introduction to steam generation and distribution 1 Steam Handbook An introduction to steam generation and distribution Dr. Ian Roberts Phillip Stoor Michael Carr Dr. Rainer Höcker Oliver Seifert 2 Endress+Hauser – Steam Handbook Impressum Publisher Endress+Hauser Flowtec AG, CH-4153 Reinach/BL Editor in chief Thomas Stauss Editorial team Michael Carr, Dr. Rainer Höcker, Dr. Ian Roberts, Romeo Rocchetti, Oliver Seifert, Thomas Stauss, Phillip Stoor Illustrations Kodotec (Lörrach, Germany) Layout, set Beatrice Meyer Steam Handbook, 1st Edition 2017 © Copyright 2017 by: Endress+Hauser Flowtec AG, CH-4153 Reinach/BL All rights reserved. This work is copyright protected in its entirety. All use in breach of copyright laws without the express permission of the publisher is forbidden. Duplication, translation, microfilming, storage and processing in any form of electronic media is prohibited. 3 Contents 5 Foreword 37 How steam moves 5 What this document is about? (simple explanation) 5 Who this document is for? 5 How to use the document? 41 On the motion of steam (detailed explanation) 7 A short history of 55 Some hazards of steam boiler designs 55 Boiling liquid expanding vapor explosion (BLEVE) 11 Why use steam? 56 Column collapse water hammer 11 What is steam used for? 59 Sub-cooled condensate induced 12 Where is steam used? water hammer 61 Flash steam explosion 13 A generic steam system 61 Overpressure in the distribution system 17 Types of industrial 61 Overpressure (inside a pressure vessel) -
Experimental Technical Bases for Evaluating Vapor/Steam Explosions
Contents Foreword . xi Acronyms . xiii Preface . xv Chapter 1 Industrial Accidents Involving Large Vapor/Steam Explosions . 1. 1.1 Non-Nuclear Explosion Boiling Studies . .1 1.1.1 Smelt–Water Explosions . .2 1.1.2 Metal–Water Interactions . .2 1.1.3 Intentional LNG Spills. .3 1.2 Nuclear Incidents . .4 1.2.1 Nuclear Test Reactors . .4 1.2.2 Water-Cooled versus Water-Moderated Thermal Reactors . .7 1.3 Objective of This Book . .8 Chapter 2 Basic Considerations of Large-Scale Vapor Explosions and Their Application to Nuclear Fast and Thermal Reactor Safety . .11 . 2.1 Technical Basis for Coarse Intermixing, Triggering, and Propagation . 11 2.1.1 Coarse Intermixing . 20 2.1.2 Triggering an Explosion . 22 2.1.3 Propagation of an Explosion and Fine-Scale Fragmentation . 24 2.2 Large-Scale Vapor Explosion Requirements. .28 2.3 Application to Nuclear Reactor Systems . .34 2.4 Assessment of Fuel–Coolant Interactions in the Fast Breeder Reactor Core Disruptive Accident. .38 2.4.1 Introduction . 38 2.4.2 General Behavior Principles and Contact Modes . 39 2.4.3 CORECT-II Experiments . 49 2.4.4 Concluding Remarks and Summary. .54 v Chapter 3 Experimental Basis for Water-Cooled Reactor Evaluations . 57 3.1 Methodology for Assessing the Coarse Mixing Conversion Ratios for Explosive Interactions . 59 3.2 Early Investigations with Reactive Metals . .65 3.2.1 Long’s Aluminum–Water Studies . 67 3.2.2 Aluminum–Water Studies by Hess . 69 3.2.3 Reactive Metal–Water Studies by Higgins . 70 3.2.4 Shock Tube Tests by Wright . -
The Chernobyl-4 Reactor and the Possible Causes of the Accident
INIS-mf—10945 The Chernobyl-4 Reactor and the Possible Causes of the Accident F. MOTTE Reactor Division SCK/CEN presented at the Seminar THE CHERNOBYL ACCIDENT AND ITS IMPACT organized by SCK/CEN at Mol on October 7th 1986 - I - The Chernobyl-4 Reactor and the Possible Causes of the Accident F. MOTTE Reactor Division SCK/CEN presented at the Seminar THE CHERNOBYL ACCIDENT AND ITS IMPACT organized by SCK/CEN at Mol on October 7th 1986 INTRODUCTION I will limit the description of the Chernobyl plant to the extent required to introduce the accident sequence of events. I will afterwards attempt to delineate some analogies and differences between the Chernobyl power station and better known nuclear plants operated in the Western coun- tries. And a last part will be devoted to the description of the events which were, at least for a large part, the cause of the accident. In 1954 the Soviet Union put into operation its first nuclear electrical power plant (6 MWe) in Obninsk. This was 3 years before Shippingport (90 MWe) became the first American PWR operating power plant, but 3 years later than the very first nuclear power plant in the world, which was a fast power plant of 0.2 MWe, the EBR (Experimental Breeder Reactor) built in Arco (Idaho): the first known generation of electricity from nuclear power was realized from the EBR in late December 1951. The Obninsk power plant is still working; to those amongst you who are familiar with our own reactors, I would say that it is the Soviet BR3. -
Steam Explosion Experiments Using Partially Oxidized Corium† J
Journal of Mechanical Science and Technology Journal of Mechanical Science and Technology 22 (2008) 2245~2253 www.springerlink.com/content/1738-494x DOI 10.1007/s12206-008-0748-3 Steam explosion experiments using partially oxidized corium† J. H. Kim*, B. T. Min, I. K. Park, H. D. Kim and S. W. Hong Thermal Hydraulics Safety Research Division, Korea Atomic Energy Research Institute, 150 Dukjin-Dong, Yusong, Taejon, Republic of Korea 305-353 (Manuscript Received October 17, 2007; Revised April 10, 2008; Accepted July 28, 2008) ------------------------------------------------------------------------------------------------------------------------------------------------------------------------------------------------------------------------------------------------------------------------------------ Abstract Two steam explosion experiments were performed in the TROI (Test for Real cOrium Interaction with water) facil- ity by using partially oxidized molten corium (core material), which is produced during a postulated core melt accident in a nuclear reactor. A triggered steam explosion occurred in one case, but none occurred in the other case. The dy- namic pressure and the dynamic load measured in the former experiment show a stronger explosion than those per- formed previously with oxidic corium. Meanwhile, a steam explosion is prohibited when the melt temperature is low, because the melt is easily solidified to prevent a liquid-liquid interaction. The partially oxidized corium could enhance the strength of a steam explosion due to the