Bridge Engineering Handbook
Total Page:16
File Type:pdf, Size:1020Kb
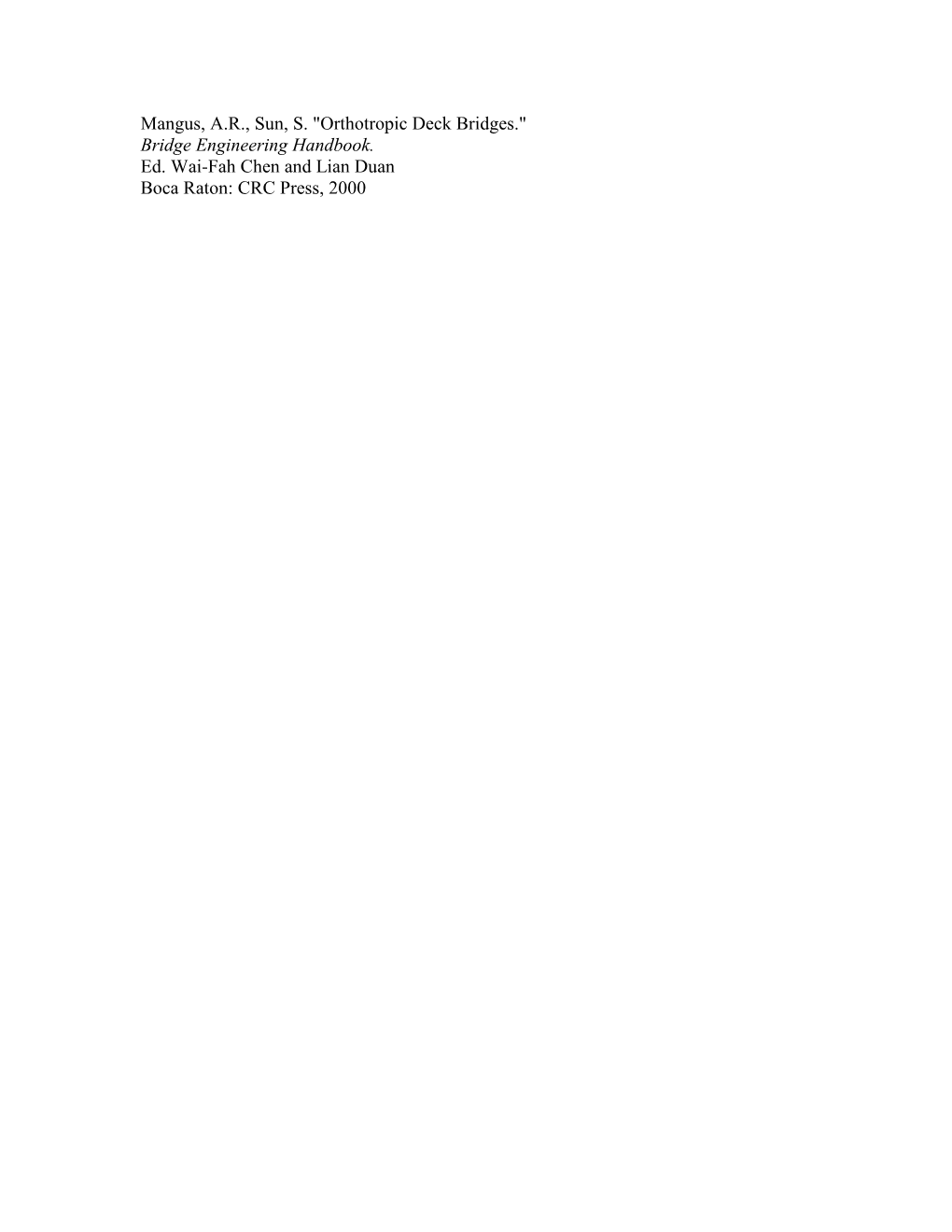
Load more
Recommended publications
-
Evaluation of Wearing Surface Systems for the Orthotropic Steel Deck of the San Mateo Hayward Bridge
EVALUATION OF WEARING SURFACE SYSTEMS FOR THE ORTHOTROPIC STEEL DECK OF THE SAN MATEO HAYWARD BRIDGE _______________________________________ A Thesis presented to the Faculty of the Graduate School at the University of Missouri-Columbia _______________________________________________________ In Partial Fulfillment of the Requirements for the Degree Master of Science _____________________________________________________ by Ravi Sankar Chamarthi, Vellore S. Gopalaratnam, Thesis Supervisor December, 2012 The undersigned, appointed by the dean of the Graduate School, have examined the thesis entitled EVALUATION OF WEARING SURFACE SYSTEMS FOR THE ORTHOTROPIC STEEL DECK OF THE SAN MATEO HAYWARD BRIDGE Presented by Ravi Sankar Chamarthi, a candidate for the degree of Master of Science and hereby certify that, in their opinion, it is worthy of acceptance. Vellore S. Gopalaratnam Sarah Orton P. Frank Pai i EVALUATION OF WEARING SURFACE SYSTEMS FOR THE ORTHOTROPIC STEEL DECK OF THE SAN MATEO HAYWARD BRIDGE Ravi Sankar Chamarthi Dr. Vellore S. Gopalaratnam Thesis supervisor ABSTRACT Performance under static and fatigue loads are evaluated for two different wearing surfaces for possible use on the steel orthotropic deck of San Mateo Hayward Bridge in the bay area of California. The two wearing surface materials studied include a 2" thick (nominal) premixed polyester concrete (PC) and a 2" thick (nominal) epoxy asphalt concrete (EAC). Flexural specimens that comprise a “steel-plate - wearing surface” composite simulating the surfacing system and geometry specific to the orthotropic steel deck of the San Mateo Hayward Bridge are used for the static and fatigue tests. Flexural tests were conducted at different dynamic loading frequencies (0.0167, 1.0, 2.5, 5.0, 7.5, 10.0 and 15.0 Hz) and at several different temperatures (20˚F- 120˚F) to study the temperature dependency and loading rate effects. -
Experience the Moselle Landscape of Wine And
EN MOSELLANDTOURISTIK WINE EVENTS & HOSTS 2019 EXPERIENCE THE MOSELLE LANDSCAPE OF WINE AND CULTURE WINE EVENTS, ARRANGEMENTS & HOSTS 2019 Dear guests and friends of the Moselle region, UNIQUE ORIGINS, we are delighted by your interest in spending your For information on your SEDUCTIVE ENJOYMENT. holiday in our attractive landscape of wine and culture. Moselle vacation contact: This brochure starts off by providing you with a Mosellandtouristik GmbH comprehensive overview of the appealing package Kordelweg 1 · 54470 Bernkastel-Kues offers available for a care-free stay by the Moselle, Saar Telephone +49(0)6531/9733-0 and Ruwer rivers. Thereafter we will introduce our local Fax +49(0)6531/9733-33 hosts, who will gladly spoil you individually with the hospitality that is typical for the Moselle region. [email protected] www. mosellandtouristik.de/en Discover the Moselle region with us – be it on a www.facebook.com/mosellandtouristik short trip or an entire holiday, as a guest in a hotel, a boarding house, in a winery, or in a holiday apartment. Please don’t hesitate to contact us directly if you are Bookinghotline: +49 (0)6531 97330 seeking advice or would like to place a booking. eMail: [email protected] Web: www.mosellandtouristik.de/en, www.facebook.com/Mosellandtouristik Have fun planning your holidays! Your Moselland Tourism EXPERIENCE THE MOSELLE LANDSCAPE OF WINE AND CULTURE Map of the region 4 in the footsteps of the Romans 21 The Mosel – One of the most beautiful Exclusive short trip to the Saarburger Land 22 river landscapes in Europe 6 UNESCO World Heritage treasures in Trier 22 The most beautiful side of country life 8 Discover the city of Trier on the Roman Wine Road 22 Moselle, with body and soul 10 Girls on Tour – Discover. -
Study on Mechanical Behaviors of Orthotropic Deck of Highway Bridge
6th International Conference on Machinery, Materials, Environment, Biotechnology and Computer (MMEBC 2016) Study on Mechanical Behaviors of Orthotropic Deck of Highway Bridge Bing Han1,a,Qianhui Pu1,b, Leiping Xu1-2,c ,Shili Yang1,d, Liangjun Chen1,e 1School of Civil Engineering, Southwest Jiaotong University, Chengdu 610031,China; 2China Railway Major Bridge Reconnaissance & Design Institute Co., Ltd.,China [email protected], b [email protected], [email protected], [email protected] [email protected] Keywords: Orthotropic Deck; Mechanic Behavior; Finite Element Method; Welding Details Abstract. In order to investigate mechanic behaviors of the orthotropic deck welding conformation details of highway steel bridge, take Zhongdu Yangtze River Bridge located in Jiangjin of Chongqing district as an engineering background, the 3-dimension spatial section model of steel box girder was firstly established based on the numerical finite element method, and then the stress level of welding conformation including the top plate of orthotropic deck, stiffening rib and transverse diaphragm was studied. The numerical analyzed results show that the stress level of welding conformation is mainly influenced by the second system and the third system. The mechanical performance of box girder is specifically represented as global bending action, global shearing action and local supporting action, which reflects significant local stress state. Also, the degree of the above mentioned actions for different conformation details is different. Introduction Orthotropic deck has advantages of light weight, high strength, large bearing capacity, fast installation speed, beautiful appearance and wide application range, which is frequently used in long-span bridge structures. However, due to the complicated space welding structures, it is easy to cause the fatigue crack of the orthotropic bridge deck [1][6]. -
Dodam Bridge
A GLOBAL BRIDGE World’s Longest Sea Bridge NETWORK SYSTRA has been a world leader in the World’s Longest Floating Bridge fi eld of transportation infrastructure for 60 years. Bridges are a major product SHEIKH JABER AL-AHMAD AL-SABAH CAUSEWAY line and a cornerstone of our technical Kuwait MONTREAL excellence in providing safe, effi cient, PARIS SEOUL and economical solutions. SAN DIEGO EVERGREEN POINT FLOATING BRIDGE World’s Longest Span International Bridge Technologies joined Seattle, Washington Railway Cable-Stayed Bridge NEW DELHI SYSTRA in 2017. The two companies DUBAI have combined their complementary World’s Longest technical expertise to offer specialized Concrete Span engineering services in all facets of bridge TIANXINGZHOU BRIDGE design, construction, and maintenance. China World’s Fastest Design & SYSTRA’s Global Bridge Network consists Construction Supervision on any Metro Project of over 350 bridge specialists deployed 3rd PANAMA CANAL CROSSING worldwide, with Bridge Design Centers Colón, Panama World’s Longest located in San Diego, Montreal, São Paolo, Double Suspension Bridge SÃO PAOLO Paris, Dubai, New Delhi, and Seoul. MECCA (MMMP) METRO Saudi Arabia CHACAO BRIDGE BRIDGE DESIGN CENTERS Chacao, Chile • SERVICES • Tender Preparation • BIM / BrIM • Conceptual Design • Complex Drafting & Specialized Detailing • Pre-Bid Engineering • Realistic Graphics • Proposal Preparation - 3D Renderings - Visual Animation • Specifications Preparation - Construction Sequence Animation • Bids Analysis • Technical Assistance During Construction -
Deck Design for Steel Bridges
Deck Design for Steel Bridges Four (4) Continuing Education Hours Course #CV1218 Approved Continuing Education for Licensed Professional Engineers EZ-pdh.com Ezekiel Enterprises, LLC 301 Mission Dr. Unit 571 New Smyrna Beach, FL 32170 800-433-1487 [email protected] Deck Design for Steel Bridges Ezekiel Enterprises, LLC Course Description: The Deck Design for Steel Bridges course satisfies four (4) hours of professional development. The course is designed as a distance learning course that offers insight for engineers in decking options and design considerations for steel bridges. Objectives: The primary objective of this course is to enable the student to understand design options & methods for various steel bridge deck types such as concrete deck slabs, metal grid decks, orthotropic steel decks, wood decks, and several others. Grading: Students must achieve a minimum score of 70% on the online quiz to pass this course. The quiz may be taken as many times as necessary to successful pass and complete the course. A copy of the quiz questions are attached to last pages of this document. ii Deck Design for Steel Bridges Ezekiel Enterprises, LLC Table of Contents Deck Design for Steel Bridges 1. Introduction ...................................................... 1 2. Concrete Deck Slabs ........................................... 2 3. Metal Grid Decks ............................................. 19 4. Orthotropic Steel Decks ................................... 26 5. Wood Decks ..................................................... 31 6. Other Deck Systems ......................................... 34 Quiz Questions ...................................... 38 iii Deck Design for Steel Bridges Ezekiel Enterprises, LLC 1.0 INTRODUCTION This course provides practical information regarding the decking options and design considerations for steel bridges, presenting deck types such as concrete deck slabs, metal grid decks, orthotropic steel decks, wood decks, and several others. -
Initial and Replacement Riding Surface for the Orthotropic San Mateo/Hayward Bridge
Bridge Structures 13 (2017) 81–92 81 DOI:10.3233/BRS-170116 IOS Press Initial and replacement riding surface for the orthotropic San Mateo/Hayward Bridge R. Maggentia and S. Shatnawib,∗ aPECG, California Department of Transportation, Sacramento, CA, USA bShatec Engineering Consultants, LLC, El Dorado Hills, CA, USA Abstract. When opened in 1967, the San Mateo/Hayward Bridge crossing the San Francisco Bay south of San Francisco incorporated the United States’ first major orthotropic steel bridge deck. The mile long orthotropic steel deck of the bridge was the largest in the world at the time. The orthotropic deck is included within a 2 mile long steel high rise portion of the 7 mile long bridge. Over 40 materials were evaluated for the riding surface of the original orthotropic deck. Epoxy asphalt was chosen and remained in place well past its life expectancy until it was finally replaced in 2015 by a polyester concrete material. The paper chronicles the factors leading to the selection of the material and construction of the initial and replacement riding surface. The replacement needed to be done on a critical bridge in service connecting the East-Bay Area communities to San Francisco. This made accelerated construction a factor in choosing a replacement and motivated evaluation of polyester concrete as a possibility. Keywords: Orthotropic bridge deck, epoxy asphalt, polyester concrete, accelerated bridge construction, overlay, riding surface, wearing surface 1. Introduction orthotropic decks a separate riding surface on the steel plates is inherently required. The subject of this paper is the riding surface for Orthotropic is derived from the terms ‘orthogo- the orthotropic portion of the San Mateo/Hayward nal’ meaning having properties at 90 degree angles Bridge deck. -
Golden Gate Bridge History Golden Gate Bridge History
Golden Gate Bridge History Golden Gate Bridge History • August 27, 1930: Joseph B. Strauss submits final plans • January 5, 1933: Construction officially starts • January-June 1933: Marin pier construction • November 1933-June 1934: Marin tower construction • March 1933-November 1934: San Francisco pier fender construction • November 1934-January 1935: San Francisco pier construction • January-June 1935: San Francisco tower construction • August 1935-April 1937: Superstructure construction • May 27, 1937: Grand Opening Golden Gate Bridge Statistics • 8,891 ft. total length with 4,200 ft. main span • 220 ft. vertical waterway clearance • 7,260 ft. of 36 in. diameter cable with 80,000 miles of wire • Towers – 746 ft. above water and 500 ft. above roadway – 44,000 tons and more than 600,000 rivets in each Golden Gate Bridge Statistics • Maximum design downward deflection = 10.8 ft. • Maximum design transverse deflection = 27.7 ft. • 38 million crossings per year (3.3 million in 1937) San Francisco (South) Tower Pier • Constructed within dewatered fender • Fender details – Encloses football field-sized area – Over 120 ft. maximum height in 75 ft. average water depth – 40 ft. maximum wall thickness – Over 105,000 cu. yds. of concrete – Pier protection from fog-bound ships San Francisco (South) Tower Pier • 140 ft. long by 66 ft. wide • Supports two 34 ft. by 33 ft. tower legs • Foundation keyed into bedrock at 110 ft. below sea level • 23,500 cu. yds. of concrete • Within 40 ft. thick fender walls Marin (North) Tower Pier • Constructed within dewatered cofferdam • Same general size as South Tower Pier • Supports two 54 ft. -
Field Testing of an Orthotropic Steel Deck Bridge RAYMOND EUGENE DAVIS, California Division of Highways
Field Testing of an Orthotropic Steel Deck Bridge RAYMOND EUGENE DAVIS, California Division of Highways Field studies were made of an orthotropic steel deck bridge to investigate (a) correlations between observed structural behavior and that predicted by theoretical analyses, either existing or derived in the course of the project; (b) construction and fabri cation problems; and (c) durability of two types of wearing sur faces and various methods of application. The nature of the structure, the large number of transducer circuits (over 1,200), and the requirement for expeditious acquisition of data required some unique loading methods as well as sophisticated machinery for transducer reading and data reduction, tabulation, and plot ting. Equipment was constructed to apply large, single or mul tiple, concentrated loads to the steel deck. Data reduction and plotting methods were developed. Cost of the structure was very high, as might be expected in the short-span range em ployed. Moreover, it has demonstrated a particular vulnerabil ity to icing. •THIS PAPER describes a research project pertinent to an orthotropic steel deck plate bridge. The program is being conducted by the California Division of Highways, Bridge and Materials and Research Departments, in cooperation with the University of Cali fornia, Berkeley, and the U.S. Bureau of Public Roads. Work has been in progress since 1963. The specific objectives of the project are to (a) establish correlations between em pirically observed structural behavior of an orthotropic steel deck plate bridge and theoretical behavior based on analyses either existing or to be derived as part of the -----------• /1-\ .! -----L.!--L- ----L----L!-- --..:I .l:-L--.!--L.!-- ---'-1 ----- l! -- LL!- L---- -l! -L---- }J.1 u~.1:a.111, \U / J.11 Vt;:~l,J.~ct.Lt:: \,;UU.:>L.1 U\;L.1UU i::UlU .Li::LUJ.:.11.,;c:1.LJ.VU ,lJ.1 uu.u:aUib .LVJ. -
Dynamic Testing of Alfred Zampa Memorial Bridge
UC San Diego UC San Diego Previously Published Works Title Dynamic Testing of Alfred Zampa Memorial Bridge Permalink https://escholarship.org/uc/item/3t27x1w3 Journal Journal of Structural Engineering, ASCE, 134(6) ISSN 0733-9445 Authors Conte, Joel P He, Xianfei Moaveni, Babak et al. Publication Date 2008-06-01 DOI 10.1061/(ASCE)0733-9445(2008)134:6(1006) Peer reviewed eScholarship.org Powered by the California Digital Library University of California Journal of Structural Engineering, ASCE, ST/2006/025227, Revised Version: 06/07/2007 Dynamic Testing of Alfred Zampa Memorial Bridge Joel P. Conte1, Member, ASCE, Xianfei He2, Babak Moaveni3, Sami F. Masri4, John P. Caffrey5, Mazen Wahbeh6, Farzad Tasbihgoo7, Daniel H. Whang8, and Ahmed Elgamal9, Member, ASCE Abstract This paper describes a set of dynamic field tests performed on the Alfred Zampa Memorial Bridge (AZMB), also known as the New Carquinez Bridge, which is located 32km northeast of San Francisco on interstate Highway I-80. The AZMB, opened to traffic in November 2003, is the first suspension bridge in the United States with an orthotropic steel deck, reinforced concrete towers and large-diameter drilled shaft foundations. The dynamic field tests described herein were conducted just before the bridge opening to traffic. They included ambient vibration tests, mainly wind-induced, and forced vibration tests based on controlled traffic loads and vehicle-induced impact loads. Four different controlled traffic load patterns and seven different vehicle-induced impact load configurations were used in the forced vibration tests. The dynamic response of the bridge was measured through an array of 34 uni-axial and 10 tri-axial force- balanced accelerometers deployed along the whole length of the bridge. -
Analysis of an Orthotropic Deck Stiffened with a Cement-Based Overlay
Downloaded from orbit.dtu.dk on: Oct 04, 2021 Analysis of an Orthotropic Deck Stiffened with a Cement-Based Overlay Walter, Rasmus; Olesen, John Forbes; Stang, Henrik; Vejrum, Tina Published in: Journal of Bridge Engineering Link to article, DOI: 10.1061/(ASCE)1084-0702(2007)12:3(350) Publication date: 2007 Document Version Early version, also known as pre-print Link back to DTU Orbit Citation (APA): Walter, R., Olesen, J. F., Stang, H., & Vejrum, T. (2007). Analysis of an Orthotropic Deck Stiffened with a Cement-Based Overlay. Journal of Bridge Engineering, 12(3), 350-363. https://doi.org/10.1061/(ASCE)1084- 0702(2007)12:3(350) General rights Copyright and moral rights for the publications made accessible in the public portal are retained by the authors and/or other copyright owners and it is a condition of accessing publications that users recognise and abide by the legal requirements associated with these rights. Users may download and print one copy of any publication from the public portal for the purpose of private study or research. You may not further distribute the material or use it for any profit-making activity or commercial gain You may freely distribute the URL identifying the publication in the public portal If you believe that this document breaches copyright please contact us providing details, and we will remove access to the work immediately and investigate your claim. Analysis of an Orthotropic Deck Sti®ened with a Cement-Based Overlay Rasmus Walter*, John F. Olesen*, Henrik Stang*, & Tina Vejrum** *Department of Civil Engineering, Technical University of Denmark, DK-2800 Kgs. -
Orthotropic Design Meets Cold Weather Challenges an Overview of Orthotropic Steel Deck Bridges in Cold Regions
Orthotropic Design Meets Cold Weather Challenges An Overview of Orthotropic Steel Deck Bridges in Cold Regions By Alfred R. Mangus, P.E. Transportation Engineer, Civil California Dept. of Transportation (CALTRANS) Sacramento, California Introduction Initially developed by German engineers following World War II, orthotropic bridge design was a creative response to material shortages during the post- war period. Lightweight orthotropic steel bridge decks not only offered excellent structural characteristics, but were also In Norway economical to build (Troitsky 1987). Nordhordland Floating Bridge Moreover, they could be built in cold The Nordhordland Bridge across the climates at any time of the year. Salhus fjord is Norway’s second float- Engineers from around the world utilize ing bridge and the world’s largest float- this practical and economic system for ing bridge (Meaas, Lande, and Vindoy, all types of bridges. While concrete 1994). The bridge was opened for traf- must be at or above 5 degrees Celsius fic in 1994. The total bridge length is to properly cure, it is physically possible Figure 1. Rib designs. 1615 m and consists of a high level to encapsulate and heat the concrete 369 m long cable stayed bridge and a construction process; admittedly, this cover a matrix of rib types, superstruc- 1246 m long floating bridge (Figure 2). adds to construction costs (Mangus ture types and various bridge types. The floating bridge consists of a steel 1988), (Mangus 1991). Russia has developed a mass manu- box girder, which is supported on ten factured panelized orthotropic deck concrete pontoons and connected to Orthotropic steel deck bridges have system and has devised special abutments with transition elements in proven to be durable in cold regions. -
Golden Gate Bridge Mass Transit Feasibility Study / [Prepared For
GOLDEN GATE bridg|V1 TRANSWI FEASIBILITY STUDY N GOLDEN GATE BRIDGE, - HIGHWAY AND TRANSPORTATION DISTRICT D REF 388.4097 SAN FRANCISCO. CALIFORNIA S e4 3 g OOCUMKNT9 OETT. SAN FRANCISCO PUBLIC LIBRARY INFERENCE BOOK Not to be taken from the Library GOLDEN GATE BRIDGE MASS TRANSIT Feasibility Study Golden Gate Bridge, Highway and Transportation District San Francisco, California Charles Seim, P.£. Mark Ketchum, Ph.D., P.E. T.Y. Lin International San Francisco, California in professional collaboration with: Roman Wolchuk Bechtel Civil Imbsen & Associates P.G.H. Wong Engineering Faye Bernstein Associates Safety and Systems Assurance Prof. Robert H. Scanlan Wilson Ihrig Associates West Wind Laboratory Campbell Associates Don Todd Associates PSG Corrosion Engineering COWI Consult Prof. A.C. Scordelis Prof. Ben Gerwick October 1990 D REF 388.4097 Se43g Seim, Charles, 1944- Golden Gate Bridge mass transit feasibility 1990 . S.F. PUBLIC LIBRARY 3 1223 04180 0690 EXECUTIVE SUMMARY The Golden Gate Bridge is considered one of the great construction achievements of the 20th century, and is at the same time a vital transportation link and a symbol of San Francisco recognized around the world. It was built with some reserve load capacity, and recent structural improvements have lightened the structure and thus increased this reserve load capacity. This study, commissioned by the Golden Gate Bridge, Highway and Transportation District, evaluates the structural feasibility of utilizing this reserve load capacity for implementation of a mass transit system on a special purpose deck to be built beneath the existing highway deck, within the existing structural envelope of the suspended structure.