Leaking Rear Axles: a Design for Six Sigma Project at General Motors
Total Page:16
File Type:pdf, Size:1020Kb
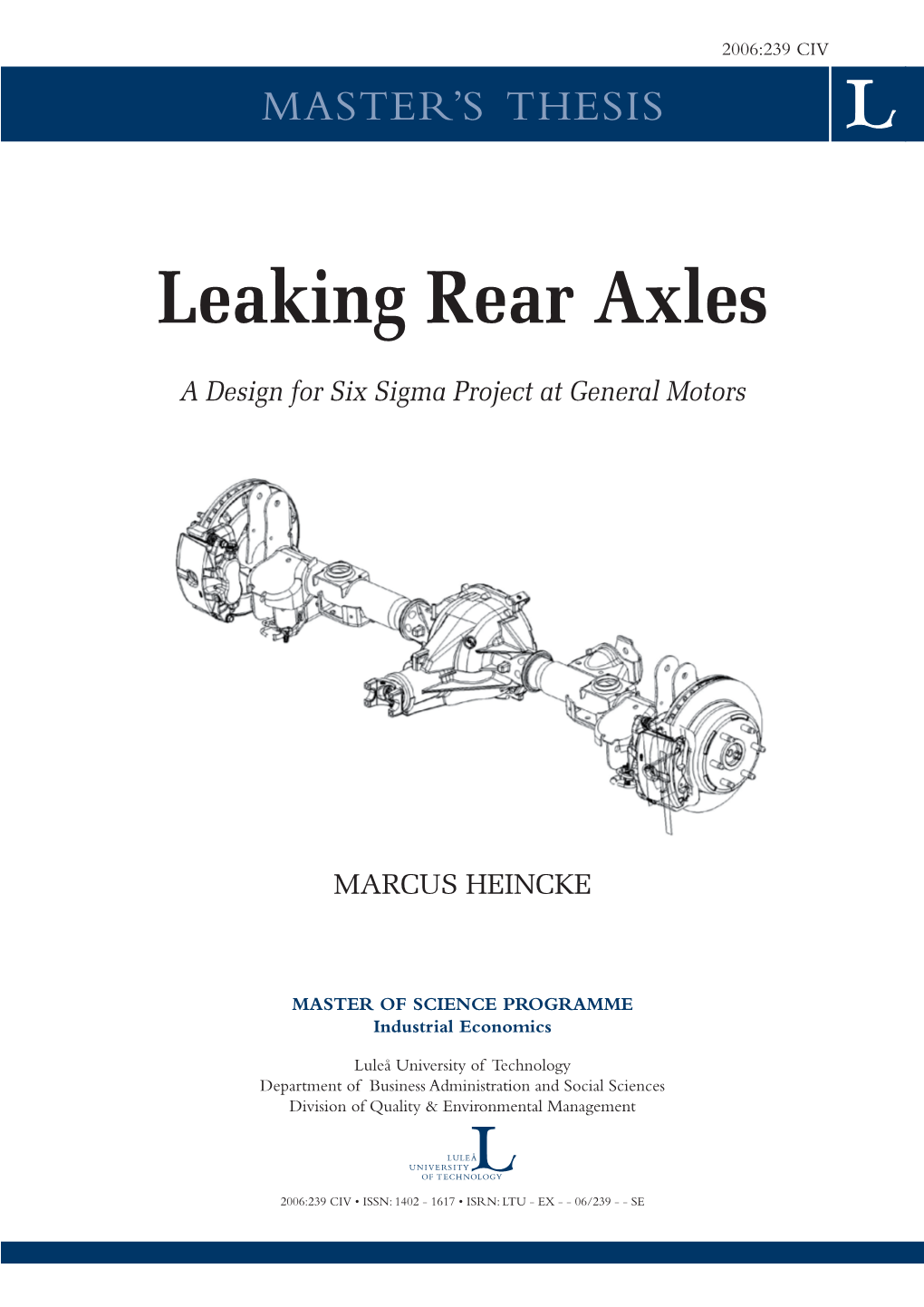
Load more
Recommended publications
-
The 1999 ASA Quality and Productivity Research Conference Presentation Abstracts Wednesday Keynote Address
The 1999 ASA Quality and Productivity Research Conference Presentation Abstracts Wednesday Keynote Address Six Sigma: From Strategic Deployment to Bottom-line Results A. Blanton Godfrey, Joseph A. DeFeo and Richard Chua Juran Institute, Inc. There are many challenges in creating a strong, competitive position today. They start with creating the right strategic direction for the organization and developing an aggressive, yet realistic strategic plan. But the plan is only a starting point. Without deployment, the strategic planning process is just another non- valued-added activity. In the last few years a small number of companies have used the emerging ideas, concepts and tools of Six Sigma to develop deployment plans leading to stunning results. We shall review some of the successful approaches - and some of the failed ones - and share lessons learned from a number of case studies. 1999 ASA QPRC Presentation Abstracts 1 Six Sigma Implementation I Applying Six Sigma in an Innovative R&D Organization Jane C. Li, James Rockwell and Anne Raich UOP LLC UOP has a proud history of innovation as a world leader in development and commercialization of new technologies for petroleum refining and petrochemical process industries. Two years after successful introduction of Six Sigma to manufacturing in 1995, over 250 UOP engineers, scientists and managers began participation in an accelerated in-house customized Six Sigma program. Long-term success through new product and process design is emphasized with a broad training approach. A culture change has begun toward aligning complex technical and business issues, providing a fresh view of catalysis, material, and process research and development, and improving testing efficiency. -
Making It LOUD
Making it LOUD 2011 Annual Report WWW.USFIRST.ORG1 For over 20 years, FIRST® Founder Dean Kamen and everyone associated with FIRST have been on a mission to spread President Barack Obama, along with White House Technology Officer Aneesh Chopra, continued to feature FIRST teams as perfect examples of the president’s national White the word about the many educational, societal, economical, and House Science Fair initiative promoting STEM (science, technology, engineering, and Dean Kamen will.i.am planetary benefits of getting youth and adults alike involved in theFIRST math) education and celebrating science and math achievement in American schools. Morgan Freeman experience. Despite not having access to the millions of marketing Soledad O’Brien dollars required to make FIRST a household “brand,” the program has continued to grow each year at a blistering pace. …aND loudER Books, magazines, newspapers, cable TV, and the Web helped us create noise, too, with ongoing national coverage by Bloomberg, CNN, Popular Mechanics, In 2011, however, thanks to the fervent interest of major figures Popular Science, Wired, ESPN Magazine, WallStreetJournal.com, and more. Author Neal Bascomb brought the FIRST experience to life in his inspiring in government, the media, and mainstream entertainment, the book, The New Cool.Time Warner Cable incorporated “volume” of voices promoting FIRST... FIRST into its national “Connect A Million Minds™” initiative, featuring our FRC program in its TV show “It Ain’t Rocket Science.” The clamor of FIRST recognition continues to grow ...GOT TuRNED UP loud...VERY loud! louder every day. The continuing mainstream exposure is helping propel us toward our goal of making FIRST known and recognized around the globe. -
A Brief History of QUALITY’S Seminal Moments
A Brief History of QUALITY’s Seminal Moments 1 A SAMPLING OF THE SEMINAL MOMENTS IN THE HISTORY OF QUALITY, AND THE ASSOCIATED PEOPLE, THAT HAVE MADE A DIFFERENCE Stephen N. Luko Statistician, engineering Fellow United Technologies Aerospace Systems November 11, 2018 Forward 2 This presentation is about some of the important moments and people contributing key concepts and knowledge to the theory and application of Quality. It is therefore a sample of these and not the whole story. The people, concepts and techniques reviewed are a testimony to a field that has blossomed in our lifetime to become the “Quality Sciences”. Today, Quality is a multidisciplinary field and applied in many disciplines, comprising such diverse fields as management, psychology, mathematics, statistics, planning, and leadership among others. One thought before we begin 3 It cannot be helped that most of the people in this story were scientists, engineers, mathematicians or statisticians by training, so much of the following presentation has a technical bedrock. Beginning’s 4 Quality goes back a long time 13th century to the early 19th century - The “Guilds” of medieval Europe and elsewhere throughout the world was the banner of quality goods for centuries. Guilds fostered craftsmanship, apprenticeship, and individual piece to piece inspection and quality. This system continued until the modern period and the dawn of the industrial revolution. Artifacts and antiquities have left us materials thousands of years old. Beginning’s, Shewhart’s long view 5 From: Shewhart, “Statistical Method from the Viewpoint of Quality Control”, 1939 Beginning’s - Shewhart’s long view 6 From: Shewhart, “Statistical Method from the Viewpoint of Quality Control”, 1939. -
Specialty Tools Brake Tools
Specialty Tools SPECIALTY TOOLS • Includes sizes T-40, T-45, T-50. • All Torxbits are made of heat-treated alloy steel. 27740 - 3 pc. set includes T-40, T-45, T-50 sizes BRAKE TOOLS for servicing disc brakes fitting GM and Ford brake caliper Torx bolts. • 3-Stone Hone Fits Cylinders to 2" (21.4-50.8mm). • Available Individually: 26620 T-40 3/8" drive, 26630 T-45 3/8" drive, 26640 T-50 3/8" drive • Controlled pressure makes it possible to polish or hone with just one stone grit. Square ends of stones hone to the end in Lisle Brake Caliper Torx Bit Set LST 27740 step-cut and blind-end cylinders. 240 grit stones are 1 1/8" long. Flexible driver. • # 10050 Replacement Stones • Hardened alloy steel bits. Lisle Brake Cylinder Hone LST 10000 • Professional sand finish. • Sizes: T40, T45 & T50. Performance Tool 3 Pc Brake Caliper Star Bit Set • 2-Stone Hone Fits Cylinders 11/16" to 2 1/2" (17.4 - 63.5mm). WIL W1337 • Controlled pressure makes it possible to polish or hone with just one stone grit. Square ends of stones hone to the end in step-cut and blind-end cylinders. 240 grit stones are • Hangs the Disc Brake Caliper Out of the Way During Service While 1-1/8" long. Flexible driver. Keeping Tension Off the Brake Line. • # 10550 Replacement Stones • Helps prevent damage to calipers and lines when servicing brakes, Lisle Brake Cylinder Hone LST 10500 suspension, hubs and more. • Overall length of 9" for hanging the disc brake caliper out of the way while keeping tension off the brake line. -
Michigan Auto Project Progress Report - December 2000 I Inaugural Progress Report Michigan Automotive Pollution Prevention Project
A VOLUNTARY POLLUTION PREVENTION AND RESOURCE CONSERVATION PARTNERSHIP ADMINISTERED BY: Michigan Department of Environmental Quality Environmental Assistance Division DECEMBER, 2000: 1st ISSUE John Engler, Governor • Russell J. Harding, Director www.deq.state.mi.us ACKNOWLEDGMENTS DaimlerChrysler Corporation, Ford Motor Company, General Motors Corporation and the Michigan Department of Environmental Quality (MDEQ) thank the Auto Project Stakeholder Group members for providing advice to the Auto Project partners and facilitating public information exchange. The Auto Companies and MDEQ also acknowledge the guidance and counsel provided by the US EPA Region V. CONTACTS FOR ADDITIONAL INFORMATION For information regarding the Michigan Automotive Pollution Prevention Project Progress Report, contact DaimlerChrysler, Ford, or General Motors at the addresses listed below or the Environmental Assistance Division of the Michigan Department of Environmental Quality at 1-800-662-9278. DaimlerChrysler Ford Doug Orf, CIMS 482-00-51 Sue Rokosz DaimlerChrysler Corporation Ford Motor Company 800 Chrysler Drive One Parklane Blvd., Suite 1400 Auburn Hills, MI 48326-2757 Dearborn, MI 48126 [email protected] [email protected] General Motors MDEQ Sandra Brewer, 482-303-300 Anita Singh Welch General Motors Corporation Environmental Assistance Division 465 W. Milwaukee Ave. Michigan Department of Environmental Quality Detroit, MI 48202 P.O. Box 30457 [email protected] Lansing, MI 48909 [email protected] Michigan Auto Project Progress Report - December 2000 i Inaugural Progress Report Michigan Automotive Pollution Prevention Project TABLE OF CONTENTS Page Foreward iv I. Executive Summary Project Overview 1 Activities and Accomplishments 4 Focus on Michigan 11 Auto Company Profiles II. DaimlerChrysler Corporation Project Status 12 Activities and Accomplishments 14 Focus on Michigan 16 III. -
Flint Fights Back, Environmental Justice And
Thank you for your purchase of Flint Fights Back. We bet you can’t wait to get reading! By purchasing this book through The MIT Press, you are given special privileges that you don’t typically get through in-device purchases. For instance, we don’t lock you down to any one device, so if you want to read it on another device you own, please feel free to do so! This book belongs to: [email protected] With that being said, this book is yours to read and it’s registered to you alone — see how we’ve embedded your email address to it? This message serves as a reminder that transferring digital files such as this book to third parties is prohibited by international copyright law. We hope you enjoy your new book! Flint Fights Back Urban and Industrial Environments Series editor: Robert Gottlieb, Henry R. Luce Professor of Urban and Environmental Policy, Occidental College For a complete list of books published in this series, please see the back of the book. Flint Fights Back Environmental Justice and Democracy in the Flint Water Crisis Benjamin J. Pauli The MIT Press Cambridge, Massachusetts London, England © 2019 Massachusetts Institute of Technology All rights reserved. No part of this book may be reproduced in any form by any electronic or mechanical means (including photocopying, recording, or information storage and retrieval) without permission in writing from the publisher. This book was set in Stone Serif by Westchester Publishing Services. Printed and bound in the United States of America. Library of Congress Cataloging-in-Publication Data Names: Pauli, Benjamin J., author. -
Simplificaton of Six Sigma Implementation Using Shainin Tools for Process Improvement Justin T
International Journal of Scientific & Engineering Research, Volume 8, Issue 4, April-2017 ISSN 2229-5518 390 Simplificaton of Six Sigma Implementation Using Shainin Tools for Process Improvement Justin T. Aichail, Arju D. Jadhav, Aniket P. Baviskar, Chandan S. Gajare, R. S. Patil Abstract— The purpose of this paper is to provide a brief overview of Six Sigma and Shainin methodology and to propose the modification of Six Sigma methodology in order to achieve improved efficiency of DMAIC in the process improvement journey by using some of the Shainin tools. The success of the Six Sigma program in an organization depends to a large extent on the success of the Six Sigma project, which in turn depends on how combination of tools is being applied to address the root cause. Shainin Design of Experiments (DOE) offers powerful and effective experimental design approach for solving the chronic quality problems that plague manufacturers worldwide. The objective of this paper is to examine as to how to simplify the implementation of Six Sigma methodology by the applicability of a simpler but not very frequently used methodology known as Shainin methodology. The comparative study of various approaches of Six Sigma implementation has been done. Index Terms— DOE, DMAIC, Process Improvement, Quality Tools, Shainin, Simplification, Six Sigma Implementation. —————————— —————————— 1 INTRODUCTION HE demands placed on an organization in today‘s global long been used to identify the key input variables responsible T business environment are driven by customer satisfaction for variations in the output. as well as the fulfilment of the expectation of stakeholders A technical feature that distinguishes Six Sigma from other regarding cost reduction, improving business performance quality approaches is its ability to use statistical methods with- and maintaining a competitive advantage. -
SN. Market Make Model Year Range Feature Model Code OBD
MX-Sensor_V3.09 Function List(Note:For reference only) NOTES: ● This function is supported. ○ This function is not supported. ▲ This function is a new feature in this version. Mark explaining(Red:New,Yellow:Modify) Special Declaration: 1).If the "Relearn Type" of MX-Sensor is only OBD type, and the "OBD-II Function" has not been released for the moment, you can just do the clone for relearning the MX-Sensor. 2).All the Automatic Relearn Procedure for MX-Sensor,the drive speed should be controlled between 16 mph (25 km/h) and 64 mph (100 km/h). Relearn Type Model OBD-II Programming Sensor Manufacturer Number on SN. Market Make Model Year Range Feature Tires (A=Automatic, Frequency OE Part NO. code Function Status Manufactuer Sensor # Sensor# S=Stationary, O=OBD) 103 EU BMW M5 2014/03-2016/06 F10 ○ 4 ● A 433Mhz Huf/Beru 36106798872 0532207017 RDE017 104 EU BMW M6 2014/03-2016/06 F12 ○ 4 ● A 433Mhz Huf/Beru 36106798872 0532207017 RDE017 105 EU BMW M7 2014/03-2016/06 F01 ○ 4 ● A 433Mhz Huf/Beru 36106798872 0532207017 RDE017 2906 EU BYD G5 2014/01-2015/12 ○ 4 ● S 433Mhz BYD 6B3609200 2907 EU BYD G6 2013/01-2015/12 ○ 4 ● S 433Mhz BYD 6B3609200 2903 EU BYD S7 2015/01-2015/12 ○ 4 ● S 433Mhz BYD 6B3609200 2909 EU BYD Sirui 2015/01-2015/12 ○ 4 ● S 433Mhz BYD 6B3609200 2904 EU BYD Song 2016/1-2016/12 ○ 4 ● S 433Mhz BYD 6B3609200 2908 EU BYD Surui 2015/01-2015/12 ○ 4 ● S 433Mhz BYD 6B3609200 2905 EU BYD Tang 2015/01-2015/12 ○ 4 ● S 433Mhz BYD 6B3609200 2939 EU Cadillac ATS-V 2016/01-2016/12 ○ 4 ● 433Mhz Schrader 20925925 60518416 20925925 2940 EU -
2008 Advanced Vehicle Technology Analysis and Evaluation Activities
annual progress report 2008V EHICLE T ECHNOLOGIES P ROGRAM ADVANCED VEHICLE TECHNOLOGY ANALYSIS AND EVALUATION ACTIVITIES AND HEAVY VEHICLE SYSTEMS OPTIMIZATION PROGRAM A Strong Energy Portfolio for a Strong America Energy efficiency and clean, renewable energy will mean a stronger economy, a cleaner environment, and greater energy independence for America. Working with a wide array of state, community, industry, and university partners, the U.S. Department of Energy’s Office of Energy Efficiency and Renewable Energy invests in a diverse portfolio of energy technologies. For more information contact: EERE Information Center 1-877-EERE-INF (1-877-337-3463) www.eere.energy.gov U.S. Department of Energy Vehicle Technologies Program 1000 Independence Avenue, S.W. Washington, DC 20585-0121 FY 2008 Annual Progress Report for Advanced Vehicle Technology Analysis and Evaluation Activities and Heavy Vehicle Systems Optimization Program Submitted to: U.S. Department of Energy Energy Efficiency and Renewable Energy Vehicle Technologies Program Advanced Vehicle Technology Analysis and Evaluation Lee Slezak, Technology Manager FY 2008 Annual Report AVTAE Activities & HVSO Program ii AVTAE Activities & HVSO Program FY 2008 Annual Report CONTENTS I. INTRODUCTION.................................................................................................................................1 II. MODELING AND SIMULATION....................................................................................................9 A. PSAT Model Validation ...............................................................................................................9 -
File-20160121154604.Pdf
ÍNDICE DE CONTENIDO Catálogo de componentes para Eje Diferencial GM EJE DIFERENCIAL DELANTERO AAM 7.25” IFS CLAMSHELL 4-7 EJE DIFERENCIAL DELANTERO AAM 7.25” IOP CLAMSHELL 8-11 EJE DIFERENCIAL DELANTERO AAM 7.6” IFS SALISBURY 12-15 EJE DIFERENCIAL TRASERO AAM 7.6” (10 TORNILLOS) SALISBURY 16-19 EJE DIFERENCIAL TRASERO AAM 8.0” (10 TORNILLOS) SALISBURY 20-23 EJE DIFERENCIAL DELANTERO AAM 8.25” IFS 800 CLAMSHELL 24-27 EJE DIFERENCIAL DELANTERO AAM 8.25” IFS 900 CLAMSHELL 28-31 EJE DIFERENCIAL TRASERO AAM 8.6” (10 TORNILLOS) SALISBURY 32-37 MÓDULO DE TRACCIÓN TRASERA (RDM) AAM 195 MM 38-41 MÓDULO DE TRACCIÓN TRASERA (RDM) AAM 218 MM 42-45 MÓDULO DE TRACCIÓN TRASERA (RDM) AAM 250 MM 46-49 EJE DIFERENCIAL DELANTERO AAM 9.25” IFS CLAMSHELL 50-53 EJE DIFERENCIAL DELANTERO AAM 9.25” IFS SALISBURY 54-57 EJE DIFERENCIAL TRASERO AAM 9.5” (14 TORNILLOS) SALISBURY 58-61 EJE DIFERENCIAL TRASERO AAM 9.5” (12 TORNILLOS) SALISBURY 62-65 EJE DIFERENCIAL TRASERO AAM 9.76” (12 TORNILLOS) SALISBURY 66-69 EJE DIFERENCIAL TRASERO AAM 10.5” (14 TORNILLOS) SALISBURY 70-75 EJE DIFERENCIAL TRASERO AAM 11.5” (14 TORNILLOS) SALISBURY 76-81 GUÍA DE REFERENCIAS 83 REFERENCIA RÁPIDA - FABRICANTES 84 CONSEJOS TÉCNICOS 86 INFORMACIÓN DE SEGURIDAD 88 GARANTÍA 89 Demand the original. Catálogo de componentes para Eje Diferencial GM EJE DIFERENCIAL DELANTERO AAM 7.25” IFS 4WD AWD GUÍA DE REFERENCIA DE VEHÍCULOS T TRUCK - Camionetas 4x4 de tamaño mediano, Pick-Ups y Blazers L VAN - Van 4x4 (Astro, Safari) G VAN - Van de peso completo (también GMT600), Express/Savana 4 Demand the original. -
Durham E-Theses
Durham E-Theses Concise Process Improvement Methods COX, STEVEN How to cite: COX, STEVEN (2011) Concise Process Improvement Methods, Durham theses, Durham University. Available at Durham E-Theses Online: http://etheses.dur.ac.uk/3275/ Use policy The full-text may be used and/or reproduced, and given to third parties in any format or medium, without prior permission or charge, for personal research or study, educational, or not-for-prot purposes provided that: • a full bibliographic reference is made to the original source • a link is made to the metadata record in Durham E-Theses • the full-text is not changed in any way The full-text must not be sold in any format or medium without the formal permission of the copyright holders. Please consult the full Durham E-Theses policy for further details. Academic Support Oce, Durham University, University Oce, Old Elvet, Durham DH1 3HP e-mail: [email protected] Tel: +44 0191 334 6107 http://etheses.dur.ac.uk Concise Process Improvement Methods Steven Cox BEng MSc by Research School of Engineering and Computing Sciences University of Durham 2011 Steven Cox Concise Process Improvement Methods Abstract This thesis reviews two methodologies for process improvement; Six Sigma and the Shainin System. A strengthened methodology is developed following the 12-step Six Sigma DMAIC cycle with an added Shainin loop in the Analyse phase to narrow down sources of variation. This Hybrid Six Sigma framework is used to develop a sampling strategy known as the Process Variation Diagnostic Tool (PVDT). The PVDT allows a Gage R&R and a Provisional Process Capability study to be carried out with just 20 samples. -
General Motors WE CARE Case Study Air Filter Refurbishment Program
General Motors WE CARE Case Study Air Filter Refurbishment Program Moves Forward GM Vehicle Operations, Flint Truck Assembly, Flint, Michigan: Recipient of a 2002 WE CARE Award for Materials Conservation/Pollution Prevention Description of the Facility: The General Motors (GM) Flint Truck Assembly plant is located in Flint, Michigan. The 3.2 million square foot facility is situated on 159 acres and employs over 3,100 people. Flint Truck produces the Chevrolet Silverado and GMC Sierra Crew Cab and the new 560 Medium duty truck. Description of the Opportunity: Air filtration systems that utilize cylindrical air filters are used extensively throughout GM Assembly, Metal Fabricating, and Powertrain Operations. These air filtration systems filter particulate matter from the air that is generated from plant production activities, such as welding. Therefore, these systems help keep plant indoor air clean. The system uses filters, which are changed on a regular basis when dirty as indicated by pressure differential. The filters are typically two feet in height, 15 to 20-inches in diameter, and weigh 12 to 15 pounds new. They consist of a mesh metal cylinder, metal end caps, neoprene seals, and a polyester-blend pleated media. In the past, used filters were placed in a 20 or 32-yard waste gondola. When the gondola was full, it was removed and the filters were placed in a landfill. Description of the Improvement: Flint Truck Assembly was the first GM plant to utilize a new development in air filter reuse and recycling. The process involves a GM supplier who built a mobile recycling unit, based on GM recommendations.