Coupled Distributed Recycling and Manufacturing with Recyclebot and Reprap 3-D Printing Shan Zhong, Joshua Pearce
Total Page:16
File Type:pdf, Size:1020Kb
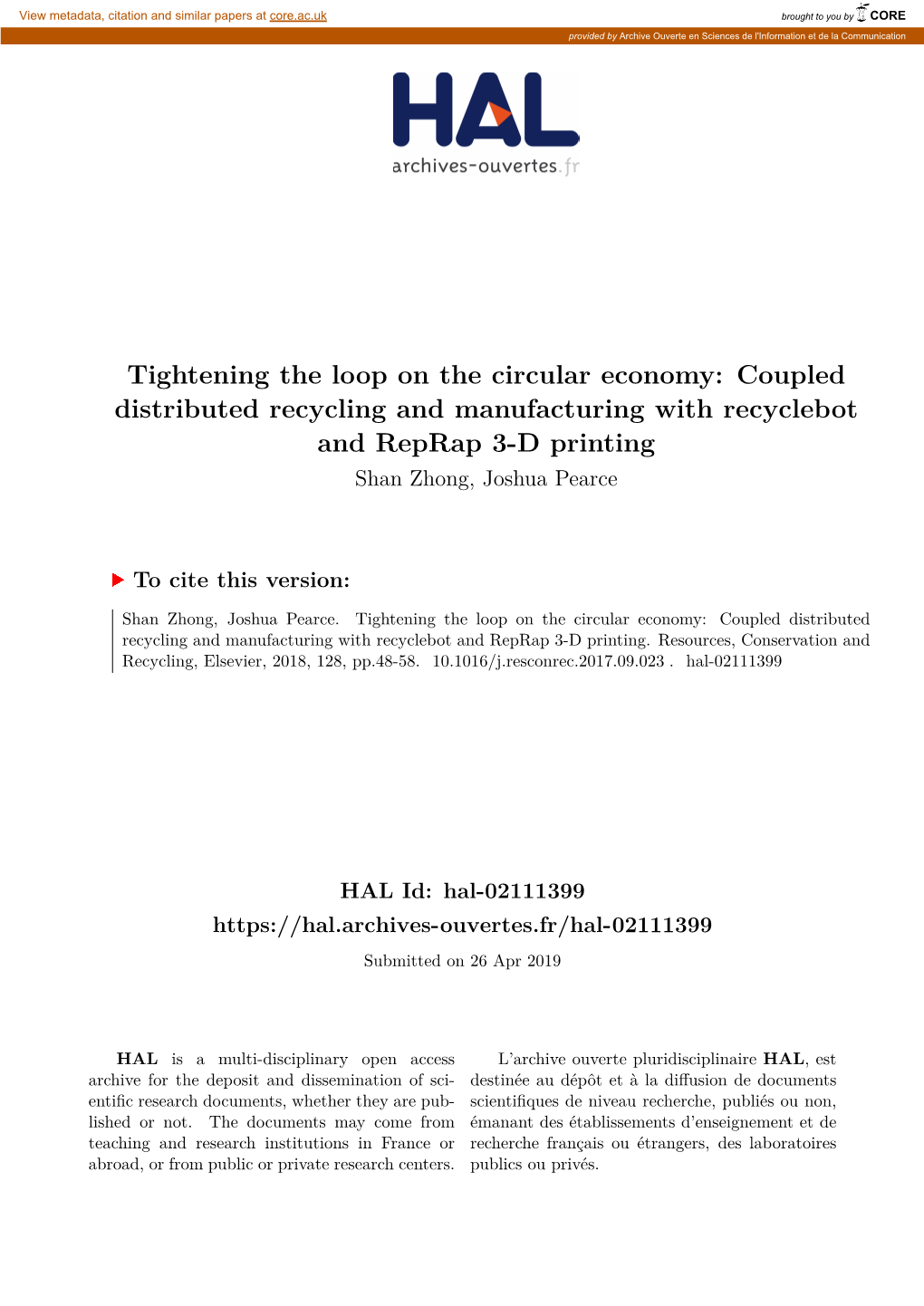
Load more
Recommended publications
-
Free Download on How to Build a 3D Printer 3D Printers DIY Plans and Build Instructions
free download on how to build a 3d printer 3D printers DIY plans and build instructions. There are many DIY projects today that can be used to make 3D printers at home, and some of them can be found here. These are mostly printers based on the RepRap 3D printer, and you can choose to either make one on your own or buy a kit and assemble the parts. What matters is that you can become the owner of a 3D printer by spending just a small amount of money; we have even come across an extruder plan to help you make the filament out of recycled plastic! - Darwin 3D printer. RepRap 1.0 "Darwin" is a rapid prototyping machine that is capable of making the majority of its own component parts. Instructions and all necessary data are available completely free under the GNU General Public Licence from this website to everyone. As RepRap 1.0 "Darwin" copy itself, once you have one you can make others for your friends; or if they have one you can ask them to make one for you. Of course, you can also make as many as you want for yourself; the more you have, the faster you will be able to make other items. RepRap etiquette asks that you use your machine to make the parts for at least two more Darwins for other people at cost, as well as using it to make whatever you or anyone else on the internet can think up. Darwin consists of a frame made from rods and printed parts. -
Open-Source, Self-Replicating 3-D Printer Factory for Small-Business Manufacturing Andre Laplume, Gerald Anzalone, Joshua Pearce
Open-source, self-replicating 3-D printer factory for small-business manufacturing Andre Laplume, Gerald Anzalone, Joshua Pearce To cite this version: Andre Laplume, Gerald Anzalone, Joshua Pearce. Open-source, self-replicating 3-D printer factory for small-business manufacturing. International Journal of Advanced Manufacturing Technology, Springer Verlag, 2016, 85 (1-4), pp.633-642. 10.1007/s00170-015-7970-9. hal-02113502 HAL Id: hal-02113502 https://hal.archives-ouvertes.fr/hal-02113502 Submitted on 28 Apr 2019 HAL is a multi-disciplinary open access L’archive ouverte pluridisciplinaire HAL, est archive for the deposit and dissemination of sci- destinée au dépôt et à la diffusion de documents entific research documents, whether they are pub- scientifiques de niveau recherche, publiés ou non, lished or not. The documents may come from émanant des établissements d’enseignement et de teaching and research institutions in France or recherche français ou étrangers, des laboratoires abroad, or from public or private research centers. publics ou privés. Preprint of: Andre Laplume, Gerald C. Anzalone, Joshua M. Pearce. Open-source, self-replicating 3-D printer factory for small-business manufacturing. The International Journal of Advanced Manufacturing Technology. 85(1), pp 633-642 (2016). doi:10.1007/s00170-015-7970-9 Open-Source Self-Replicating 3-D Printer Factory for Small-Business Manufacturing Andre Laplume1, Gerald C. Anzalone2, and Joshua M. Pearce2,3,* 1. Department: School of Business & Economics, Michigan Technological University, Houghton, MI, USA 2. Department of Materials Science & Engineering, Michigan Technological University, Houghton, MI, USA 3. Department of Electrical & Computer Engineering, Michigan Technological University, Houghton, MI, USA * contact author: 601 M&M Building 1400 Townsend Drive Houghton, MI 49931-1295 906-487-1466 [email protected] Abstract: Additive manufacturing with 3-D printers may be a key technology enabler for entrepreneurs seeking to use disruptive innovations, such as business models utilizing distributed manufacturing. -
1 Open Source 3-D Filament Diameter Sensor for Recycling, Winding and Additive Manufacturing Machines Aliaksei L. Petsiuk1 and J
Open Source 3-D Filament Diameter Sensor for Recycling, Winding and Additive Manufacturing Machines Aliaksei L. Petsiuk1 and Joshua M. Pearce1,2,3 1Department of Electrical & Computer Engineering, Michigan Technological University, Houghton, MI 49931, USA 2Department of Material Science & Engineering, Michigan Technological University, Houghton, MI 49931, USA 3Department of Electronics and Nanoengineering, School of Electrical Engineering, Aalto University, Espoo, FI-00076, Finland [email protected], [email protected] Graphical Abstract Filament images Extracted pseudo- surface Highlights • Developed a portable optical computer vision-based diameter measurement system. • The module can be integrated into a control system of a plastic waste recycling machine. • Multi-axis measurements with ovality detection and texture analysis assure quality. • Measurement logging allows tracking the quality of the filament along its length. 1 Abstract To overcome the challenge of upcycling plastic waste into 3-D printing filament in the distributed recycling and additive manufacturing systems, this study designs, builds, tests and validates an open source 3-D filament diameter sensor for recycling and winding machines. The modular system for multi-axis optical control of the diameter of the recycled 3-D-printer filament makes it possible to analyze the surface structure of the processed filament, save the history of measurements along the entire length of the spool, as well as mark defective areas. The sensor is developed as an independent module and integrated into a recyclebot. The diameter sensor was tested on different kinds of polymers (ABS, PLA) different sources of plastic (recycled 3-D prints and virgin plastic waste) and different colors including clear plastic. The results of the diameter measurements using the camera were compared with the manual measurements, and the measurements obtained with a one-dimensional digital light caliper. -
Fused Particle Fabrication 3-D Printing: Recycled Materials' Optimization and Mechanical Properties
This is an electronic reprint of the original article. This reprint may differ from the original in pagination and typographic detail. Woern, Aubrey L.; Byard, Dennis J.; Oakley, Robert B.; Fiedler, Matthew J.; Snabes, Samantha L.; Pearce, Joshua M. Fused particle fabrication 3-D printing Published in: Materials DOI: 10.3390/ma11081413 Published: 12/08/2018 Document Version Publisher's PDF, also known as Version of record Published under the following license: CC BY Please cite the original version: Woern, A. L., Byard, D. J., Oakley, R. B., Fiedler, M. J., Snabes, S. L., & Pearce, J. M. (2018). Fused particle fabrication 3-D printing: Recycled materials' optimization and mechanical properties. Materials, 11(8), [1413]. https://doi.org/10.3390/ma11081413 This material is protected by copyright and other intellectual property rights, and duplication or sale of all or part of any of the repository collections is not permitted, except that material may be duplicated by you for your research use or educational purposes in electronic or print form. You must obtain permission for any other use. Electronic or print copies may not be offered, whether for sale or otherwise to anyone who is not an authorised user. Powered by TCPDF (www.tcpdf.org) materials Article Fused Particle Fabrication 3-D Printing: Recycled Materials’ Optimization and Mechanical Properties Aubrey L. Woern 1, Dennis J. Byard 1, Robert B. Oakley 2, Matthew J. Fiedler 2,3, Samantha L. Snabes 2,3 and Joshua M. Pearce 3,4,5,* ID 1 Department of Mechanical Engineering–Engineering -
Distributed Plastic Recycling with an Open Source Recyclebot
Michigan Technological University Digital Commons @ Michigan Tech Dissertations, Master's Theses and Master's Reports 2017 TIGHTENING THE LOOP ON THE CIRCULAR ECONOMY: DISTRIBUTED PLASTIC RECYCLING WITH AN OPEN SOURCE RECYCLEBOT Shan Zhong Michigan Technological University, [email protected] Copyright 2017 Shan Zhong Recommended Citation Zhong, Shan, "TIGHTENING THE LOOP ON THE CIRCULAR ECONOMY: DISTRIBUTED PLASTIC RECYCLING WITH AN OPEN SOURCE RECYCLEBOT", Open Access Master's Thesis, Michigan Technological University, 2017. https://doi.org/10.37099/mtu.dc.etdr/397 Follow this and additional works at: https://digitalcommons.mtu.edu/etdr Part of the Other Materials Science and Engineering Commons, and the Polymer and Organic Materials Commons TIGHTENING THE LOOP ON THE CIRCULAR ECONOMY: DISTRIBUTED PLASTIC RECYCLING WITH AN OPEN SOURCE RECYCLEBOT By Shan Zhong A THESIS Submitted in partial fulfillment of the requirements for the degree of MASTER OF SCIENCE In Materials Science and Engineering MICHIGAN TECHNOLOGICAL UNIVERSITY 2017 © 2017 Shan Zhong This thesis has been approved in partial fulfillment of the requirements for the Degree of MASTER OF SCIENCE in Materials Science and Engineering. Department of Materials Science and Engineering Thesis Advisor: Dr. Joshua A. Pearce Committee Member: Dr. Stephen L. Kampe Committee Member: Dr. Yun Hang Hu Department Chair: Dr. Stephen L. Kampe Table of Contents List of Figures ..................................................................................................................... v -
Open Source Completely 3-D Printable Centrifuge
Preprints (www.preprints.org) | NOT PEER-REVIEWED | Posted: 18 April 2019 doi:10.20944/preprints201904.0207.v1 Peer-reviewed version available at Instruments 2019, 3, 30; doi:10.3390/instruments3020030 1 Type of the Paper (Article) 2 Open Source Completely 3-D Printable Centrifuge 3 Salil S. Sule1, Aliaksei L. Petsiuk2 and Joshua M. Pearce 2,3,4* 4 1 Department of Mechanical Engineering–Engineering Mechanics, Michigan Technological University, 5 Houghton, MI, 49931; [email protected] 6 2 Department of Electrical & Computer Engineering, Michigan Technological University, Houghton, MI, 7 49931; [email protected] 8 3 Department of Material Science & Engineering, Michigan Technological University, Houghton, MI, 49931; 9 [email protected] 10 3 Department of Electronics and Nanoengineering, School of Electrical Engineering, Aalto University, Espoo, 11 Finland, FI-00076; [email protected] 12 * Correspondence: [email protected]; Tel.: +01-906-487-1466 13 14 Abstract: Centrifuges are commonly required devices in medical diagnostics facilities as well as 15 scientific laboratories. Although there are commercial and open source centrifuges, costs of the 16 former and required electricity to operate the latter, limit accessibility in resource-constrained 17 settings. There is a need for low-cost, human-powered, verified and reliable lab-scale centrifuge. This 18 study provides the designs for a low-cost 100% 3-D printed centrifuge, which can be fabricated on 19 any low-cost RepRap-class fused filament fabrication (FFF) or fused particle fabrication (FPF)-based 20 3-D printer. In addition, validation procedures are provided using a web camera and free and open 21 source software. This paper provides the complete open source plans including instructions for 22 fabrication and operation for a hand-powered centrifuge. -
Energy Payback Time of a Solar Photovoltaic Powered Waste Plastic Recyclebot System Shan Zhong, Pratiksha Rakhe, Joshua Pearce
Energy Payback Time of a Solar Photovoltaic Powered Waste Plastic Recyclebot System Shan Zhong, Pratiksha Rakhe, Joshua Pearce To cite this version: Shan Zhong, Pratiksha Rakhe, Joshua Pearce. Energy Payback Time of a Solar Photovoltaic Powered Waste Plastic Recyclebot System. Recycling, MDPI, 2017, 2 (2), pp.10. 10.3390/recycling2020010. hal-02113450 HAL Id: hal-02113450 https://hal.archives-ouvertes.fr/hal-02113450 Submitted on 28 Apr 2019 HAL is a multi-disciplinary open access L’archive ouverte pluridisciplinaire HAL, est archive for the deposit and dissemination of sci- destinée au dépôt et à la diffusion de documents entific research documents, whether they are pub- scientifiques de niveau recherche, publiés ou non, lished or not. The documents may come from émanant des établissements d’enseignement et de teaching and research institutions in France or recherche français ou étrangers, des laboratoires abroad, or from public or private research centers. publics ou privés. Distributed under a Creative Commons Attribution| 4.0 International License recycling Article Energy Payback Time of a Solar Photovoltaic Powered Waste Plastic Recyclebot System Shan Zhong 1, Pratiksha Rakhe 1 and Joshua M. Pearce 1,2,* 1 Department of Materials Science & Engineering, Michigan Technological University, Houghton, MI 49931, USA; [email protected] (S.Z.); [email protected] (P.R.) 2 Department of Electrical & Computer Engineering, Michigan Technological University, Houghton, MI 49931, USA * Correspondence: [email protected]; Tel.: +1-906-487-1466 Academic Editor: Michele Rosano Received: 25 April 2017; Accepted: 8 June 2017; Published: 15 June 2017 Abstract: The growth of both plastic consumption and prosumer 3-D printing are driving an interest in producing 3-D printer filaments from waste plastic. -
Distributed Manufacturing of Flexible Products: Technical Feasibility and Economic Viability
technologies Article Distributed Manufacturing of Flexible Products: Technical Feasibility and Economic Viability Aubrey L. Woern 1 and Joshua M. Pearce 2,3,4,* ID 1 Department of Mechanical Engineering-Engineering Mechanics, Michigan Technological University, Houghton, MI 49931, USA; [email protected] 2 Department of Electronics and Nanoengineering, School of Electrical Engineering, Aalto University, FI-02150 Espoo, Finland 3 Department of Material Science and Engineering, Michigan Technological University, Houghton, MI 49931, USA 4 Department of Electrical and Computer Engineering, Michigan Technological University, Houghton, MI 49931, USA * Correspondence: [email protected]; Tel.: +1-906-487-1466 Received: 11 October 2017; Accepted: 26 October 2017; Published: 30 October 2017 Abstract: Distributed manufacturing even at the household level is now well established with the combined use of open source designs and self-replicating rapid prototyper (RepRap) 3-D printers. Previous work has shown substantial economic consumer benefits for producing their own polymer products. Now flexible filaments are available at roughly 3-times the cost of more conventional 3-D printing materials. To provide some insight into the potential for flexible filament to be both technically feasible and economically viable for distributed digital manufacturing at the consumer level this study investigates 20 common flexible household products. The 3-D printed products were quantified by print time, electrical energy use and filament consumption by mass to determine the cost to fabricate with a commercial RepRap 3-D printer. Printed parts were inspected and when necessary tested for their targeted application to ensure technical feasibility. Then, the experimentally measured cost to DIY manufacturers was compared to low and high market prices for comparable commercially available products. -
Open-Source Lab This Page Intentionally Left Blank
Open-Source Lab This page intentionally left blank Open-Source Lab How to Build Your Own Hardware and Reduce Research Costs Joshua M. Pearce Department of Materials Science & Engineering, Department of Electrical & Computer Engineering, Michigan Technological University, Houghton, MI, USA AMSTERDAM • BOSTON • HEIDELBERG • LONDON • NEW YORK • OXFORD PARIS • SAN DIEGO • SAN FRANCISCO • SYDNEY • TOKYO Elsevier 225 Wyman Street, Waltham, MA 02451, USA The Boulevard, Langford Lane, Kidlington, Oxford OX5 1GB, UK Radarweg 29, PO Box 211, 1000 AE Amsterdam, The Netherlands Copyright © 2014 Elsevier Inc. All rights reserved. No part of this publication may be reproduced, stored in a retrieval system or transmitted in any form or by any means electronic, mechanical, photocopying, recording or otherwise without the prior written permission of the publisher Permissions may be sought directly from Elsevier’s Science & Technology Rights Department in Oxford, UK: phone (+44) (0) 1865 843830; fax (+44) (0) 1865 853333; email: [email protected]. Alternatively you can submit your request online by visiting the Elsevier web site at http://elsevier.com/locate/permissions, and selecting Obtaining permission to use Elsevier material Notices No responsibility is assumed by the publisher for any injury and/or damage to persons or property as a matter of products liability, negligence or otherwise, or from any use or operation of any methods, products, instructions or ideas contained in the material herein. Because of rapid advances in the medical sciences, in particular, independent verification of diagnoses and drug dosages should be made Library of Congress Cataloging-in-Publication Data Pearce, Joshua, author. Open-source lab : how to build your own hardware and reduce research costs / Joshua Pearce. -
Quantifying the Value of Foam-Based Flexible Floating Solar Photovoltaic Systems
Michigan Technological University Digital Commons @ Michigan Tech Dissertations, Master's Theses and Master's Reports 2021 QUANTIFYING THE VALUE OF FOAM-BASED FLEXIBLE FLOATING SOLAR PHOTOVOLTAIC SYSTEMS Koami Soulemane Hayibo Michigan Technological University, [email protected] Copyright 2021 Koami Soulemane Hayibo Recommended Citation Hayibo, Koami Soulemane, "QUANTIFYING THE VALUE OF FOAM-BASED FLEXIBLE FLOATING SOLAR PHOTOVOLTAIC SYSTEMS", Open Access Master's Thesis, Michigan Technological University, 2021. https://doi.org/10.37099/mtu.dc.etdr/1176 Follow this and additional works at: https://digitalcommons.mtu.edu/etdr Part of the Other Engineering Commons, Power and Energy Commons, and the Water Resource Management Commons QUANTIFYING THE VALUE OF FOAM-BASED FLEXIBLE FLOATING SOLAR PHOTOVOLTAIC SYSTEMS By Koami Soulemane Hayibo A THESIS Submitted in partial fulfillment of the requirements for the degree of MASTER OF SCIENCE In Electrical and Computer Engineering MICHIGAN TECHNOLOGICAL UNIVERSITY 2021 © 2021 Koami Soulemane Hayibo This thesis has been approved in partial fulfillment of the requirements for the Degree of MASTER OF SCIENCE in Electrical and Computer Engineering. Department of Electrical and Computer Engineering Thesis Advisor: Joshua M. Pearce Committee Member: Paul L. Bergstrom Committee Member: David Watkins Department Chair: Glen E. Archer Table of Contents List of figures .......................................................................................................................v List of tables ..................................................................................................................... -
Fused Particle Fabrication 3-D Printing: Recycled Materials' Optimization and Mechanical Properties
materials Article Fused Particle Fabrication 3-D Printing: Recycled Materials’ Optimization and Mechanical Properties Aubrey L. Woern 1, Dennis J. Byard 1, Robert B. Oakley 2, Matthew J. Fiedler 2,3, Samantha L. Snabes 2,3 and Joshua M. Pearce 3,4,5,* ID 1 Department of Mechanical Engineering–Engineering Mechanics, Michigan Technological University, Houghton, MI 49931, USA; [email protected] (A.L.W.); [email protected] (D.J.B.) 2 re:3D Inc., 1100 Hercules STE 220, Houston, TX 77058, USA; [email protected] (R.B.O.); [email protected] (M.J.F.); [email protected] (S.L.S.) 3 Department of Material Science and Engineering, Michigan Technological University, Houghton, MI 49931, USA 4 Department of Electrical and Computer Engineering, Michigan Technological University, Houghton, MI 49931, USA 5 Department of Electronics and Nanoengineering, School of Electrical Engineering, Aalto University, 00076 Espoo, Finland * Correspondence: [email protected] or joshua.pearce@aalto.fi; Tel.: +01-906-487-1466 Received: 21 July 2018; Accepted: 9 August 2018; Published: 12 August 2018 Abstract: Fused particle fabrication (FPF) (or fused granular fabrication (FGF)) has potential for increasing recycled polymers in 3-D printing. Here, the open source Gigabot X is used to develop a new method to optimize FPF/FGF for recycled materials. Virgin polylactic acid (PLA) pellets and prints were analyzed and were then compared to four recycled polymers including the two most popular printing materials (PLA and acrylonitrile butadiene styrene (ABS)) as well as the two most common waste plastics (polyethylene terephthalate (PET) and polypropylene (PP)). The size characteristics of the various materials were quantified using digital image processing. -
3-D Printable Polymer Pelletizer Chopper for Fused Granular Fabrication-Based Additive Manufacturing
inventions Article 3-D Printable Polymer Pelletizer Chopper for Fused Granular Fabrication-Based Additive Manufacturing Aubrey L. Woern 1 and Joshua M. Pearce 2,3,* 1 Department of Mechanical Engineering–Engineering Mechanics, Michigan Technological University, Houghton, MI 49931, USA; [email protected] 2 Department of Material Science & Engineering and Department of Electrical & Computer Engineering, Michigan Technological University, Houghton, MI 49931, USA 3 Department of Electronics and Nanoengineering, School of Electrical Engineering, Aalto University, FI-00076 Espoo, Finland * Correspondence: [email protected] or joshua.pearce@aalto.fi; Tel.: +1-906-487-1466 Received: 2 November 2018; Accepted: 21 November 2018; Published: 27 November 2018 Abstract: Although distributed additive manufacturing can provide high returns on investment, the current markup on commercial filament over base polymers limits deployment. These cost barriers can be surmounted by eliminating the entire process of fusing filament by three-dimensional (3-D) printing products directly from polymer granules. Fused granular fabrication (FGF) (or fused particle fabrication (FPF)) is being held back in part by the accessibility of low-cost pelletizers and choppers. An open-source 3-D printable invention disclosed here allows for precisely controlled pelletizing of both single thermopolymers as well as composites for 3-D printing. The system is designed, built, and tested for its ability to provide high-tolerance thermopolymer pellets with a number of sizes capable of being used in an FGF printer. In addition, the chopping pelletizer is tested for its ability to chop multi-materials simultaneously for color mixing and composite fabrication as well as precise fractional measuring back to filament. The US$185 open-source 3-D printable pelletizer chopper system was successfully fabricated and has a 0.5 kg/h throughput with one motor, and 1.0 kg/h throughput with two motors using only 0.24 kWh/kg during the chopping process.