Environment, Health and Safety Management Guide Santos Version 3.0 November 2007 EHSMS V3.1 28/6/07 2:59 PM Page 2
Total Page:16
File Type:pdf, Size:1020Kb
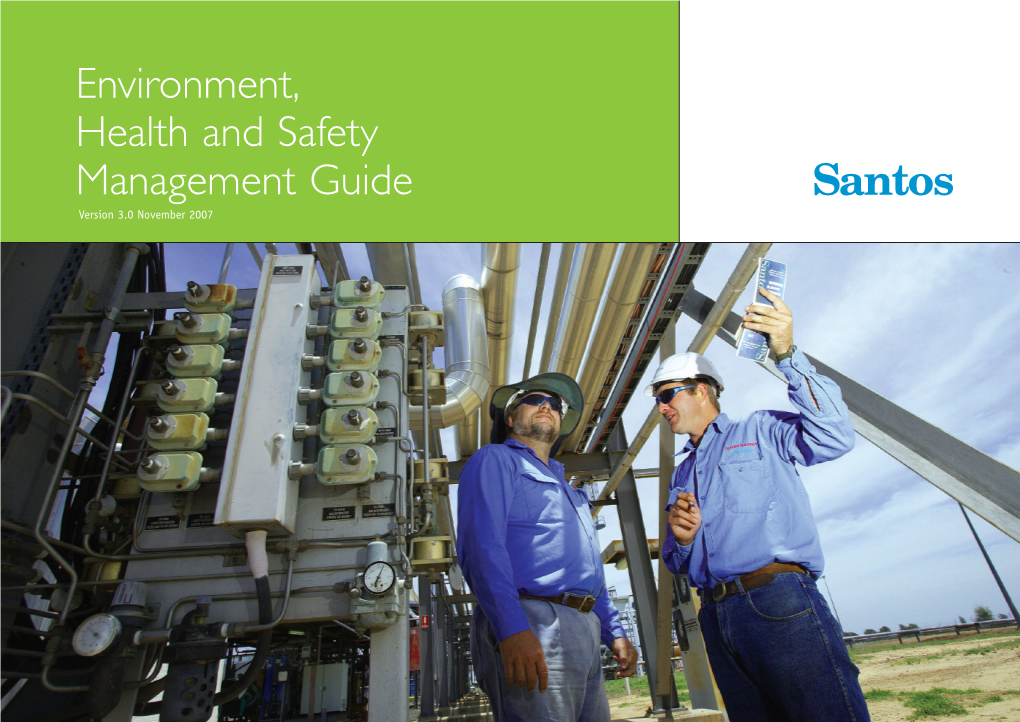
Load more
Recommended publications
-
Permits-To-Work in the Process Industries
SYMPOSIUM SERIES NO. 151 # 2006 IChemE PERMITS-TO-WORK IN THE PROCESS INDUSTRIES John Gould Environmental Resources Management, Suite 8.01, 8 Exchange Quay, Manchester M5 3EJ; [email protected] The paper presents the collective results from a number of Safety Management System audits. The audit protocol is based on the Health and Safety Executive pub- lication ‘Successful health and safety management’ and takes into account formal (written) and informal procedures as well as their implementation. Focused on permit-to-work systems, these have shown a number of common failings. The most common failure in implementing a permit-to-work system is the issue of too many permits. However, the audit protocol considers the whole risk control system. The failure to ‘close’ the management loop with an effective regular review process is the largest obstacle to an effective permit system. INTRODUCTION ‘Permits save lives – give them proper attention’. This is a startling statement made by the Health and Safety Executive (HSE) in its free leaflet IND(G) 98 (Rev 3) PTW systems. The leaflet goes on to state that two thirds of all accidents in the chemical industry are main- tenance related, with the permit-to-work (PTW) failures being the largest single cause. Given these facts, it comes as no surprise that PTW systems are a key part in the provision of a safe working environment. Over the past four years Environmental Resources Management (ERM) has been auditing PTW systems as part of its key risk control systems audits. Numerous systems have been evaluated from a wide rage of industries, covering personal care products man- ufacturing to refinery operations. -
Operational Formality for Department of Energy Nuclear Facilities and Activities
DNFSDrrECII-l~ OPERATIONAL FORMALITY FOR DEPARTMENT OF ENERGY NUCLEAR FACILITIES AND ACTIVITIES Defense Nuclear Facilities Safety Board Technical Report March 1997 OPERATIONAL FORMALITY FOR DEPARTMENT OF ENERGY NUCLEAR FACILITIES AND ACTIVITIES This technical report was prepared for the Defense Nuclear Facilities Safety Board by the following staff members: Steve Krahn Matthew Moury with assistance from: Wayne Andrews Dan Burnfield Don Owen and outside expert John Drain FOREWORD The Board has emphasized that when performing work involving hazardous materials, it is important to plan the work carefully, and to develop the controls and implementing procedures necessary to provide reasonable assurance that the work will be conducted safely. While the exact nature ofthese practices will valY depending on the work being performed, certain operational practices have evolved that have been effective. These operational practices are treated in this report as a composite forming what is termed "formality ofoperations." John T. Conway Chairman III EXECUTIVE SUMMARY Commercial manufacturing organizations ofall sizes have developed policies and practices, termed "formality ofoperations," to be followed by employees to ensure safety in the workplace, establish norms ofperformance, and promote work practices fostering efficiency and uniform product quality. For small companies, these "good engineering (or shop) practices" are often passed on by example and by word ofmouth from journeyman to apprentice. Larger organizations usually codify these concepts in policies, requirements, and procedural documents to achieve desired practices on the shop floor, and such practices become an integral part ofnew employee training. When these policies and procedures are reinforced by all managers, fi'om upper-level management to first-line supervisors, formality ofoperations becomes second nature. -
Office of State Human Resources
OFFICE OF STATE HUMAN RESOURCES NUMBER: LOTO-1 TOTAL PAGES: 19 SUBJECT: Lockout/Tagout Program Effective Date: Revision Date: Revision #: RELATED LEGISLATION: North Carolina Occupational Safety and Health Standards for General Industry, 29 CFR 1910.147. I. Purpose Each employee shall be informed that the purpose of the lockout/tagout procedure is to provide a system for the lockout and/or tagout of energy isolating devices and thereby protect employees from potentially hazardous energy. Wherever possible, energy-isolating devices should be locked out. Before employee’s service, repair or perform maintenance, the machine or equipment must be isolated from all potentially hazardous energy, and the isolating energy device(s) for the machine or equipment must be locked out or tagged out. II. Types and Magnitude of Energy and Hazards Each employee must be instructed in the types and magnitude of energy used by the company. The following types of energy are used: (a) (b) (c) (d) The magnitude of energy (a) ( energy) used is: ; the magnitude of hazards presented by the _____________ energy is: . The magnitude of energy (b) ( energy) used is: ; the magnitude of hazards presented by the _____________ energy is: . The magnitude of energy (c) ( energy) used is: ; the magnitude of hazards presented by the _____________ energy is: . The magnitude of energy (d) ( energy) used is: ; the magnitude of hazards presented by the _____________ energy is: . 1 III. Training and Retraining of Affected and Authorized Employees Each employee must be thoroughly trained with respect to lockout/tagout procedure used by the company. Each employee must know that lockout/ tagout is used to protect employees against hazardous energy from inadvertent operation of equipment or machinery. -
Abrasive Blasting Operations, Engineering Control and Work
ABRASIVE BLASTING OPERATIONS Engineering Control and Work Practices Manual Enviro-Management & Research, Inc. Washington, D.C. 20001 FINAL REPORT Contract No. 210-75-0029 U.S " DEPARTMENT OF HEALTH, EDUCATION, AND WELFARE Public Health Service Center for Discese Control National Institute for Occupational Safety and Health Division of Physical Sciences and Engineering Cincinnati, Ohio 45226 March 1976 For allle by the Superintendent of Documents , U .S. Government PtlntJni Otfice , Wa8hington. D.C. 2 0402 ACKNOWLEDGDAENTS This contract was conducted by Enviro Management &Research, Inc. under contract COC-210-75-0029 for the Division of Physical Sciences and Engineering. National Institute for Occupational Safety and Health, Center for Disease Control. Department of Health, We acknowledge with grateful appreciation the assistance provided by the Education and Welfare. Technical monitoring was proVided by Robert T. Hughes, Control Technology Research Branch. American Foundrymen's Society and The American Iron and Steel Institute, This report is reproduced as received from the contractor. The conc7usions and recommendations contained herein represent the va r l'OUS manufacturers of abrasl've blastl'ng equl'pment, and Mr. Robert T. Hughes, opinion of the contractor and do not necessarily constitute NIOSH endorsement Engineering Branch, Division of Physical Sciences and Engineering, National Institute for Occupational Safety and Health. HEW Publication No. (NIOSH) 76 -179 iii ii CONTENTS ABSTRACT vii L UTRODUCTION 1 II. CURRENT METHODS AND OPERATIONS 2 1. ~~ thods of Applicat ion 3 1.1 Dry blasting 1.2 Wet blastLTlg 12 2. Abrasives in common use 3. Abrasive Blasting Equipment 13 3.1 Portable blast cleaning machines 15 3.2 Hand-operated lli~its in blast cleaning rooms J.5 3.3 Hand-operated cabinet type blast cleaning 18 machines 3.4 Automatic blast cleaning machLTles 20 3.5 Wei blast cleanL~g machines 22 III. -
WORKERS' COMPENSATION PROGRAM Title Description File Type
file:///W|/Inetpub/wwwroot/RMTSA_Guidelines/Volume_Three/TOC3.php SECTION ONE: WORKERS' COMPENSATION PROGRAM Title Description File Type Chapter 1 Overview of Workers' Compensation (revised) HTML The Texas Workers' Compensation Act, Texas Chapter 2 HTML Labor Code, Title 5, Subtitle A (revised) Texas Workers' Compensation Act, "Old Chapter 3 HTML Law" (under revision) Workers' Compensation Claims Administration Chapter 4 HTML for State Agencies (revised) Chapter 5 Return-to-Work Programs (revised) HTML Reporting Requirements for Building or Chapter 6 Construction Projects for Governmental Entities HTML (revised) SECTION TWO: EMPLOYEE SAFETY AND HEALTH PROGRAM Title Description File Type Overview of an Employee Safety and Health Chapter 1 Program Subchapter: 1.0 Introduction (revised) HTML Causes of Occupational Accidents, Injuries, Subchapter: 1.1 HTML Illnesses and Diseases (revised) Costs Associated with an Employee Safety and Subchapter: 1.2 HTML Health Program (revised) Benefits of an Employee Safety and Health Subchapter: 1.3 HTML Program (revised) Technical Safety and Health Operations Subchapter: 1.4 HTML (revised) Safety and Health Management Programs Subchapter: 1.5 HTML (revised) file:///W|/Inetpub/wwwroot/RMTSA_Guidelines/Volume_Three/TOC3.php (1 of 6)6/21/2005 4:48:08 AM file:///W|/Inetpub/wwwroot/RMTSA_Guidelines/Volume_Three/TOC3.php Elements of an Employee Safety and Health Subchapter: 1.6 HTML Program (revised) Available Resources for Texas State Agencies Subchapter: 1.7 HTML (revised) Subchapter: 1.8 Executive Order (revised) -
Asbestos Operating Plan
Asbestos Operating Plan Keesler AFB February 1995 Table of Contents Purpose Statement PS - 1 1.0 Introduction 1 - 1 1.1 Background 1 - 1 1.2 Medical Concerns 1 - 1 2.0 Designation of Duties 2 - 1 2.1 Environmental Protection Committee (EPC) 2 - 2 2.2 Wing Commander 2 - 3 2.3 The Civil Engineer (BCE) 2 - 3 2.4 Asbestos Operations Officer (AOO) 2 - 3 2.4.1 Training 2 - 3 2.4.2 Duties 2 - 4 2.5 Asbestos Program Officer (APO) 2 - 4 2.5.1 Training 2 - 4 2.5.2 Duties 2 - 4 2.6 Public Health (PH) 2 - 5 2.7 Civil Engineering 2 - 6 2.8 Contracting Officer 2 - 6 2.9 Military Family Housing (MFH) .....2 - 6 2.10 Facility Managers 2 - 7 2.11 Public Affairs (PA) 2 - 7 2.12 Bioenvironmental Engineering (BEE) 2 - 7 2.13 Environmental Legal Adviser 2 - 8 2.14 Base Safety Officer 2 - 9 3.0 Work Control Procedures 3 - 1 3.1 Project Planning 3 - 1 3.1.1 Work Order Requests 3 - 1 3.1.2 Renovation or Demolition Projects 3 - 1 3.1.3 Routine Abatement or Repair Activities 3 - 1 3.1.3.1 Existing Hazards Requiring Immediate Abatement 3 - 4 3.1.3.2 New Hazards 3 - 4 3.2 Work Control Procedures 3 - 4 3.2.1 Small Scale, Short-Duration Abatement Activities .....3 - 4 3.2.1.1 Notification 3 - 5 3.2.1.2 Work Area Preparation 3 - 5 3.2.1.3 Air Monitoring 3 - 5 3.2.1.4 Final Visual Inspection 3 - 5 3.2.2 Large-Scale Abatement Activities 3 - 6 3.2.2.1 Project Design 3 - 6 3.2.2.2 Notification 3 - 6 3.2.2.3 Work Area Preparation 3 - 6 3.2.2.4 Air Monitoring 3 - 6 Table of Contents (cont'd) 3.2.2.5 Final Visual Inspection 3 - 7 4.0 Operations and Maintenance Work Orders -
OSHA: Safeguarding Equipment and Protecting Employees From
www.osha.gov Safeguarding Equipment and Protecting Employees from Amputations Small Business Safety and Health Management Series OSHA 3170-02R 2007 Employers are responsible for providing a safe and healthful workplace for their employees. OSHA’s role is to assure the safety and health of America’s employees by setting and enforcing standards; pro- viding training, outreach, and education; establish- ing partnerships; and encouraging continual im- provement in workplace safety and health. This publication is in the public domain and may be reproduced, fully or partially, without permission. Source credit is requested, but not required. This information is available to sensory impaired individuals upon request. Voice phone: (202) 693- 1999; teletypewriter (TTY) number: (877) 889-5627. Edwin G. Foulke, Jr. Assistant Secretary of Labor for Occupational Safety and Health Safeguarding Equipment and Protecting Employees from Amputations Occupational Safety and Health Administration U.S. Department of Labor OSHA 3170-02R 2007 This OSHA publication is not a standard or regulation, and it creates no new legal obligations. The publication is advisory in nature, informational in content, and is intended to assist employers in providing a safe and healthful workplace. The Occupational Safety and Health Act requires employers to comply with hazard-specific safety and health standards. In addition, pursuant to Section 5(a)(1), the General Duty Clause of the Act, employers must provide their employees with a workplace free from recognized hazards likely to cause death or serious physical harm. Employers can be cited for violating the General Duty Clause if there is a recognized hazard and they do not take reasonable steps to prevent or abate the hazard. -
Professional Biography
Comprehensive Industrial Hygiene Review Course March 2018 Instructor Biographies Terrance G. Alexander, MS, CIH, PE, BCEE Topic(s): IH Program Management Terrance G. Alexander, MS, CIH, PE, BCEE is the retiring Executive Director of Occupational Safety & Environmental Health for the University of Michigan. He was responsible for health, safety and environmental issues facing both the academic and business operations of the University. He directed programs involving hazardous materials, environmental management, biological & laboratory safety, industrial hygiene, radiation safety, ergonomics, food service sanitation, fire safety, and sustainability. Mr. Alexander has over 40 years’ experience in these programs, ranging from environmental consulting, to managing a site remediation program at a Department of Energy facility with over 350 historic waste sites. He began his career as an industrial hygienist and environmental engineer with the U.S. Air Force for nine years. He is a licensed professional engineer in Michigan and Illinois, a certified industrial hygienist, and a Board Certified Environmental Engineer with the American Academy of Environmental Engineers. He received his BS in civil engineering from South Dakota State University and MS in environmental science from the University of Idaho. Stuart Batterman, PhD Topic(s): Indoor Air Quality, Air Pollution Stuart Batterman is Professor of Environmental Health Sciences in the School of Public Health at the University of Michigan, and Center Director of the University of Michigan Center for Occupational Health and Safety Engineering. He is also appointed as Professor of Civil and Environmental Engineering at UM, and as honorary Professor in the Department of Occupational and Environmental Health, Medical School, at the University of KwaZulu-Natal, Durban, South Africa. -
Preventing Illness and Injury in the Workplace (Part 24 Of
References References 1. AFL-CIO v. Brerzrum, s30 F.2d 109 (3d Cir., 14. American Public Health Association, “Compen- Dec. 31, 1975), sation for and Prevention of Occupational Dis- 2. Amchan, A. J., “Callous Disregard” for Em- ease (Position Paper), ” APHA Policy Statement ployee Safety: The Exclusivity of the Workers’ 8329, adopted Nov. 16, 1983, published in Compensation Remedy Against Employers,” La- American Journal of Public Health, 74(3):292- bor Law ]oumal, pp. 683-696, November 1983. 295, March 1984. 3. American Bar Association, Commission on Law 15. American Standards Association, American and the Economy, Federal Regulation: Roads to Standard Safety Code for the Protection of Heads, lle~orrn (Washington, DC: American Bar Asso- Eyes, and Respiratory Organs, Z2-1938, Decem- ciation, 1979). ber 1938. 4. American Board of Engineering and Technol- 16. American Standards Association, American ogy, Cn”ten”a for Accrediting Programs in Engi- Standard Safety Code for Fiead, Eye, and Res- neering in the United States (New York: Amer- piratory Protection, Z2.1-1959, November 1959. ican Board of Engineering and Technology, Oct. 17. American Textile Manufacturers Institute, Znc. 18, 1980). v. Donovan, 452 U.S. 490; (June 17, 1981). 5. American Conference of Governmental Indus- 18. Ames, B. N., “Dietary Carcinogens and Anticar- trial Hygienists, Threshold Limit Values of Air- cinogens,” Science 221:1256- 1264, 1983. bome Contaminants and Jntended Changes, 19. Ames, B, N,, letter, Science 224:668 et seq., adopted by ACGIH for 1970 (Cincinnati, OH: 1984. ACGIH, 1970), 20. Anderson, L,, “Management of a Local Exhaust 6. American Conference of Governmental Indus- Ventilation Program, ” (slide presentation), Cer- trial Hygienists, Industrial Ventilation; A Man- tified Industrial Hygienist, IBM, Inc., Lexington, ual o) Recommended Practice, 18th ed, (Cin- KY, personal communication, June 14, 1983. -
Guide Health Monitoring for Exposure to Hazardous Chemicals
Guide Health monitoring for exposure to hazardous chemicals www.worksafe.nt.gov.au Disclaimer This publication contains information regarding work health and safety. It includes some of your obligations under the Work Health and Safety (National Uniform Legislation) Act – the WHS Act – that NT WorkSafe administers. The information provided is a guide only and must be read in conjunction with the appropriate legislation to ensure you understand and comply with your legal obligations. Acknowledgement This guide is based on material produced by Safe Work Australia at www.swa.gov.au Creative Commons All material presented in this publication is provided under a Creative Commons Attribution 3.0 Australia licence. For the avoidance of doubt, this means this licence only applies to material as set out in this document. The details of the relevant licence conditions are available on the Creative Commons website as is the full legal code for the CC BY 3.0 AU licence. Version: 1.2 Publish date: September 2018 Contents Introduction ..............................................................................................................................5 What is health monitoring?...................................................................................................5 Key terms used in this guide ................................................................................................6 When is health monitoring required? .......................................................................................7 Duty to provide -
Forest Operations Engineering and Management – the Ways Behind and Ahead of a Scientific Discipline
Subject review – Pregledni ~lanak Forest operations engineering and management – the ways behind and ahead of a scientific discipline Hans Rudolf Heinimann Abstract – Nacrtak The forest operations engineering and management community has been facing the problem of improving its scientific visibility, realigning its research efforts to the future challenges, and of strengthening its self-confidence. The paper aims at exploring the paradigms that shaped the development of forest operations as a scientific discipline, sketching a vision how forest operations could look like in 2020, establishing a common understanding for future of the discipline, and discussing the major challenges ahead. The investigation identified five periods of steady state development (paradigms) and developed a vision of network-based forest operations systems, built of »self-organizing« cells. It then discusses the challenges that we will probably been faced with in the fields of »harvesting and transportation engineering«, »forest operations management«, »forest ergonomics«, and »forest operations ecology«. The study intended to trigger a broad discussion on the future directions of forest operations engineering and management, and to build a basis for a redesign of cor- responding curricula in higher education. Keywords: forest operations, forest engineering, paradigms, future challenges, scienti- fic discipline, historical development 1. Introduction – Uvod even fallen silent, resulting in decreasing funding and recognition. The International Union of Forest Forest operations has been the prevailing term to Research Organization IUFRO has undertaken a ma- characterize a scientific discipline, which addresses jor effort (1) to strengthen research, (2) to expand design, implementation, control, and continuous im- strategic partnership and cooperation, (3) to enhan- provement of forest operations systems. -
Chapter 3: Controlling Lead Exposures in the Construction
Section V (previously Section IV of Oregon OSHA’s Technical Manual) CONSTRUCTION OPERATIONS DEMOLITION CHAPTER 1: CHAPTER 2: EXCAVATIONS: HAZARD RECOGNITION IN TRENCHING AND SHORING CHAPTER 3: CONTROLLING LEAD EXPOSURE IN THE CONSTRUCTION INDUSTRY: ENGINEERING AND WORK PRACTICE CONTROLS Section V / Chapter 3 - Page 1 SECTION V: CHAPTER 3 CONTROLLING LEAD EXPOSURES IN THE CONSTRUCTION INDUSTRY: ENGINEERING AND WORK PRACTICE CONTROLS Chapter Revision Information: This chapter was previously identified as Section IV, Chapter 3 in Oregon OSHA’s circa 1996 Technical Manual. The section number was modified from Section IV to Section V in March 2014 to provide uniformity with federal OSHA’s Technical Manual (OTM). In March 2014, the chapter’s multilevel listing format was modified from an alphanumeric system to a roman numeral system. In March 2014, all references to “Material Safety Data Sheets (MSDS)” were replaced with references to “Safety Data Sheets (SDS).” Section V / Chapter 3 - Page 2 SECTION V: CHAPTER 3 CONTROLLING LEAD EXPOSURES IN THE CONSTRUCTION INDUSTRY: ENGINEERING AND WORK PRACTICE CONTROLS TABLE OF CONTENTS I. INTRODUCTION . 5 II. ENGINEERING AND WORK PRACTICE CONTROLS. 6 A. Engineering Controls . 6 B. Work Practice Controls . 7 III. OPERATIONS . 11 A. Open Abrasive Blast Cleaning . 11 B. Vacuum Blast Cleaning . 14 C. Wet Abrasive Blast Cleaning. 14 D. High-Pressure Water Jetting . 15 E. High-Pressure with Abrasive Injection. 16 F. Ultrahigh-Pressure Water Jetting . 16 G. Sponge Jetting . 16 H. Carbon-Dioxide (Dry-Ice) Blasting . 16 I. Welding, Burning, and Torch Cutting . 17 J. Spray Painting with Lead-Based Paint. 19 K. Manual Scraping and Sanding of Lead-Based Paints.