Extraction and Recovery of Gold from Both Primary and Secondary
Total Page:16
File Type:pdf, Size:1020Kb
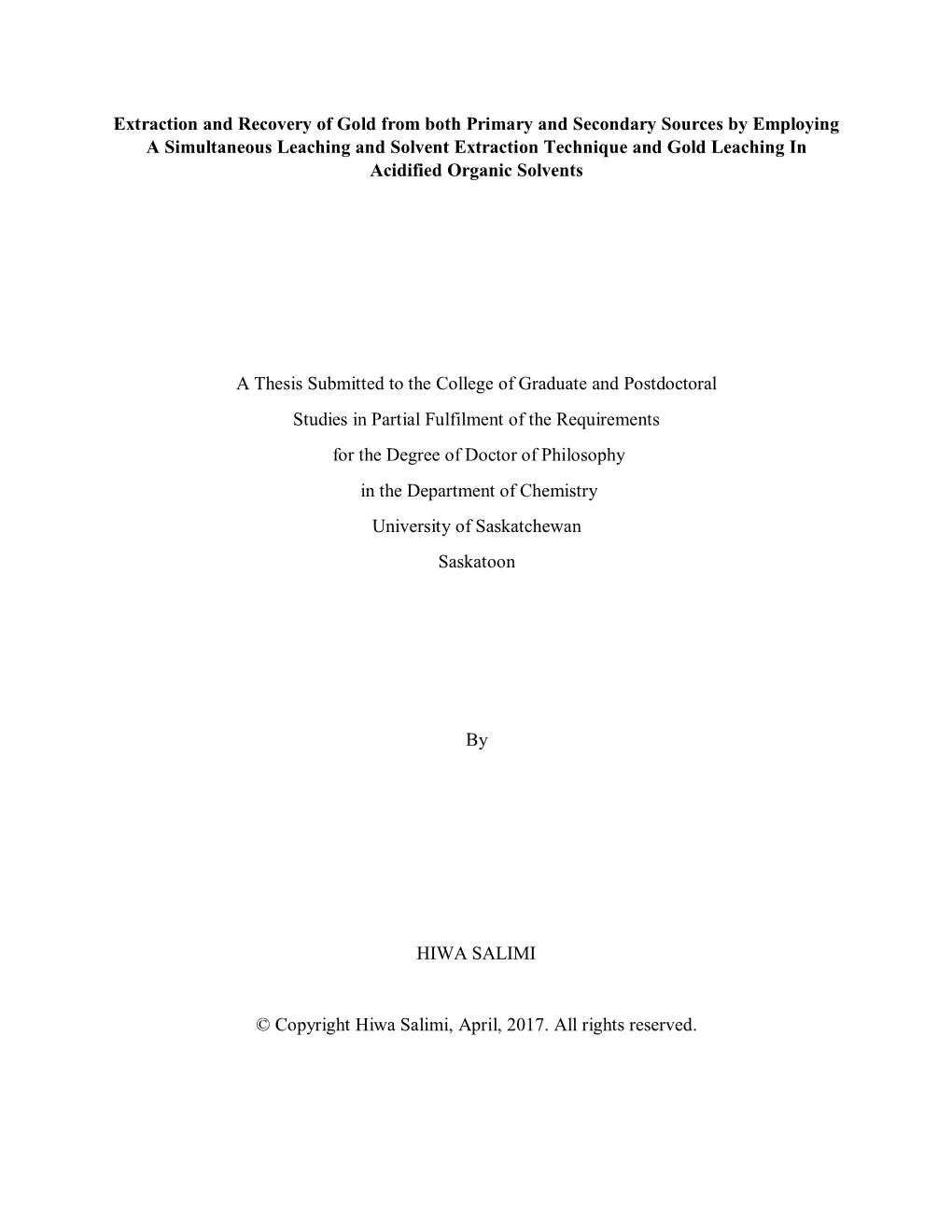
Load more
Recommended publications
-
Metal Extraction Processes for Electronic Waste and Existing Industrial Routes: a Review and Australian Perspective
Resources 2014, 3, 152-179; doi:10.3390/resources3010152 OPEN ACCESS resources ISSN 2079-9276 www.mdpi.com/journal/resources Review Metal Extraction Processes for Electronic Waste and Existing Industrial Routes: A Review and Australian Perspective Abdul Khaliq, Muhammad Akbar Rhamdhani *, Geoffrey Brooks and Syed Masood Faculty of Science, Engineering and Technology, Swinburne University of Technology, Hawthorn, VIC 3122, Australia; E-Mails: [email protected] (A.K.); [email protected] (G.B.); [email protected] (S.M.) * Author to whom correspondence should be addressed; E-Mail: [email protected]; Tel.: +61-3-9214-8528; Fax: +61-3-9214-8264. Received: 11 December 2013; in revised form: 24 January 2014 / Accepted: 5 February 2014 / Published: 19 February 2014 Abstract: The useful life of electrical and electronic equipment (EEE) has been shortened as a consequence of the advancement in technology and change in consumer patterns. This has resulted in the generation of large quantities of electronic waste (e-waste) that needs to be managed. The handling of e-waste including combustion in incinerators, disposing in landfill or exporting overseas is no longer permitted due to environmental pollution and global legislations. Additionally, the presence of precious metals (PMs) makes e-waste recycling attractive economically. In this paper, current metallurgical processes for the extraction of metals from e-waste, including existing industrial routes, are reviewed. In the first part of this paper, the definition, composition and classifications of e-wastes are described. In the second part, separation of metals from e-waste using mechanical processing, hydrometallurgical and pyrometallurgical routes are critically analyzed. -
Cip and Cil Circuit Modelling
SGS MINERALS SERVICES – T3 SGS 1338 02-2014 CIP AND CIL CIRCUIT MODELLING The SGS carbon-in-pulp (CIP) / carbon- in-leach (CIL) modelling package is used to estimate the performance of a full-scale CIP or CIL plant and to derive the optimum design criteria based on the results of small scale experiments. It is a powerful design tool that uses the results from standard leach and adsorption tests (bottle roll tests) to generate kinetic data that are fitted to leaching and carbon adsorbtion rate equations (Figure 2). The rate data and mass balance equations are then applied to the SGS model to calculate the concentrations of gold in solution, on the carbon and in the ore for each stage of a multi-stage leach- adsorbtion circuit. The model allows for the generation of multiple operating scenarios, where • the number of leach and adsorption stages can be varied, • the carbon concentration per tank can be adjusted, • the carbon loading and final barren solutions can be manipulated, • and carbon advance and elution rates adjusted. PHILOSOPHY The SGS CIP/CIL model is based on a model developed by Fleming and Nicol • Robust predictions of steady state as (1984). The philosophy then was to strive APPLICATIONS well as transient carbon adsorption for simplicity and user-friendliness, rather behaviour from simple laboratory The SGS CIP/CIL model can be used for than precision through complexity. This batch tests, feasibility or production stage projects. is still true today in SGS‘ CIP and CIL • Economic sensitivity analyses of It is a cost effective way to determine modelling package. -
Colloidal Goldgold
ColloidalColloidal GoldGold Markus Niederberger Email: [email protected] 22.11.2006 OutlineOutline 1) Definition 2) History 3) Synthesis 4) Chemical and Physical Properties 5) Applications 6) References DefinitionDefinition Colloidal gold: Stable suspension of sub-micrometer- sized particles of gold in a liquid ShortShort HistoryHistory ofof GoldGold 4000 B.C.: A culture in Eastern Europe begins to use gold to fashion decorative objects 2500 B.C.: Gold jewelry was found in the Tomb of Djer, king of the First Egyptian Dynasty 1200 B.C.: The Egyptians master the art of beating gold into leaf as well as alloying it with other metals for hardness and color variations 1091 B.C.: Little squares of gold are used in China as a form of money 300 B.C.: Greeks and Jews of ancient Alexandria start to practice Alchemy, the quest of turning base metals into gold 200 B.C.: The Romans gain access to the gold mining region of Spain 50 B.C.: The Romans begin issuing a gold coin called the Aureus 1284 A.D.: Venice introduces the gold Ducat, which soon becomes the most popular coin in the world Source: National Mining Association, Washington HistoryHistory ofof GoldGold ColloidsColloids andand theirtheir ApplicationApplication History: Gold in Medicine Humankind has linked the lustre of gold with the warm, life-giving light of the sun. In cultures, which deified the sun, gold represented its earthly form. The earliest records of the use of gold for medicinal and healing purposes come from Alexandria, Egypt. Over 5000 years ago the Egyptians ingested gold for mental and bodily purification. -
A History of Iridium OVERCOMING the DIFFICULTIES of MELTING and FABRICATION by L
A History of Iridium OVERCOMING THE DIFFICULTIES OF MELTING AND FABRICATION By L. B. Hunt The Johnson Matthey Group The use in unmanned space craft of iridium to encapsulate the radio- isotope thermoelectric generators, where temperatures of up to 20OO0C have to be withstood over several years of operation, with possible impact velocities of 90 metres per second, has focused greater attention on the remarkable properties of this member of the platinum group of metals. But these same properties of very high melting point and great mechanical strength have been the cause of difficulties in its melting and fabrication over a long period of years. How these problems were tackled and eventually overcome is described in this article. One of the less well-known members of the For some fifty years after the discovery of platinum group, iridium possesses quite platinum in South America and the early remarkable chemical and physical properties. It investigations of its properties by a number of is not only the most resistant of all metals to English, French, German and Swedish scien- corrosion, insoluble in all mineral acids in- tists, it was not realised that the native platinum cluding aqua regia and unattacked by other they were examining also contained other molten metals or by silicates at high tem- elements. The first to recognise that a small in- peratures, but has a very high melting point soluble residue survived the dissolution of and is the only metal to maintain good native platinum in aqua regia was the French mechanical properties in air at temperatures chemist Joseph Louis Proust, working for a above 1600OC.Its great stability can be gauged time in Madrid under the patronage of King from its physical properties, outlined in the Carlos IV, but he failed to grasp that other Table. -
Material Safety Data Sheet AQUA REGIA, 2-1-5 (NITRIC 20%/HCL 5%)
2290 Avenue A, Bethlehem, PA 18017 Effective Date: 4/16/2010 NON-EMERGENCY TELEPHONE 24-HOUR CHEMTREC EMERGENCY TELEPHONE 610-866-4225 800-424-9300 Material Safety Data Sheet AQUA REGIA, 2-1-5 (NITRIC 20%/HCL 5%) 1. Product Identification: MIXED ACID CONTAINING NITRIC ACID AND HYDROCHLORIC ACID Synonyms: None CAS No: N/A Molecular Weight: N/A Chemical Formula: N/A 2. Composition/Information on Ingredients Ingredient CAS No Percent Hazardous Nitric Acid 7697-37-2 1 - 25% Yes Hydrochloric Acid 7647-01-0 1 – 10% Yes Water 7732-18-5 65 - 98% No 3. Hazards Identification Emergency Overview POISON! DANGER! CORROSIVE! CORROSIVE. LIQUID AND MIST CAUSE SEVERE BURNS TO ALL BODY TISSUE. MAY BE FATAL IF SWALLOWED OR INHALED. INHALATION MAY CAUSE LUNG AND TOOTH DAMAGE. Potential Health Effects Nitric acid is extremely hazardous; it is a corrosive and a poison. In concentrated solutions it is an oxidizer. Hydrochloric acid is a corrosive. Mixtures of nitric acid and hydrochloric acid may form aqua regia releasing toxic nitrosyl chloride (yellow to reddish-brown) gas. Inhalation: Corrosive! Inhalation of vapors can cause breathing difficulties and lead to pneumonia and pulmonary edema, which may be fatal. Other symptoms may include coughing, choking, and irritation of the nose, throat, and respiratory tract. Ingestion: 1 Corrosive! Swallowing nitric acid and hydrochloric acid can cause immediate pain and burns of the mouth, throat, esophagus and gastrointestinal tract. Skin Contact: Corrosive! Can cause redness, pain, and severe skin burns. Concentrated solutions cause deep ulcers and stain skin a yellow or yellow-brown color. Eye Contact: Corrosive! Vapors are irritating and may cause damage to the eyes. -
Production of Gold
Production of Gold Background A feasibility study on the production of gold at a fictitious mine (Moapa mine) in Elko County, Nevada is to be performed. The mine is capable of producing 325,800 tons of high-grade ore per year for 8 years. The deposit contains 0.12 ounces of gold per ton of high-grade ore and can be acquired at a cost of $10 per ton of ore (cost of mining ore at site). A sodium cyanide process is used to extract the gold from the ore, and various other processing techniques are used to produce 99.9% pure gold bullion from the ore. The results of the feasibility study show that the ore can be processed by agitation leaching, which is preferred over heap leaching due to the low recovery associated with the heap leaching technology. The problem is to find the break-even price of gold for this mining operation. The process is currently unprofitable with a gold price around $300 per ounce. Process Description Unit 100 – Size Reduction of Ore The BFD of the overall process is shown in Figure 1. The PFD for Unit 100, shown in Figure 2, is designed to reduce 41.5 tons/hr of gold ore from a feed range of 2- 5” to 160 microns. The mined ore is fed using a Grizzly Feeder, F-101, into a Jaw Crusher, J-101, where 80% of the ore is crushed to 1.75” or smaller. The remaining 20% are recycled back into F-101 (not shown on PFD). The ore is then sent to Screen S-101 where the ore that does not pass through the first deck is sent to the Standard Cone Crusher SC-101. -
Myths and Realities in Artisanal Gold Mining Mercury Contamination
MYTHS AND REALITIES IN ARTISANAL GOLD MINING MERCURY CONTAMINATION by GUSTAVO ANGELOCI SANTOS A THESIS SUBMITTED IN PARTIAL FULFILLMENT OF THE REQUIREMENTS FOR THE DEGREE OF MASTER OF APPLIED SCIENCE in THE FACULTY OF GRADUATE STUDIES (Mining Engineering) THE UNIVERSITY OF BRITISH COLUMBIA (Vancouver) April 2013 © Gustavo Angeloci Santos 2013 ABSTRACT The world faces a major gold rush currently. Worldwide 15 million people work directly in artisanal gold mining in more than 55 countries. The usual method of extraction is amalgamation and cyanidation, or very commonly a combination of both. Significant amounts of contaminants are released to rivers and soil, generating environmental and health concerns. The majority of artisanal miners are involved in micro-mining, but it is believed that the majority of contamination comes from small to large artisanal operations. Larger operations involve less people, but process much more material, re- leasing much more contaminants as well. The present work explains how contamination is generated, through a com- prehensive analysis of the labor division in small-scale mining sites around the world, and also analyses aspects of different intervention approaches. Different approaches are taken by different groups working on the problem around the world. This work evaluates the most common kinds of interven- tion, with special attention to technical and legal aspects in trying to elimi- nate mercury use in gold extraction. The study is conducted by comparing different interventions strategies to evaluate the myths and realities from an engineering perspective. Special attention is paid to the evaluation of alterna- tives to amalgamation process for gold such as intensive cyanidation, borax direct smelting and chlorination. -
Studying of Preliminary Roast and Smelting Gold-Containing Electronic Scrap with Copper Collector
SCIENTIFIC PROCEEDINGS IX INTERNATIONAL CONGRESS "MACHINES, TECHNOLОGIES, MATERIALS" 2012 ISSN 1310-3946 STUDYING OF PRELIMINARY ROAST AND SMELTING GOLD-CONTAINING ELECTRONIC SCRAP WITH COPPER COLLECTOR. Prof. Strizhko L.S., engineer Shigin E.S., engineer Fokin O.A. Abstract: Electronic scrap is valuable type of complex recyclable metallurgical raw. Efficient technology requires complex recovering electronic scrap with extraction ferrous, non-ferrous and precious metals. Requirement of preliminary roast to remove and recycle gases from organic combusting are shown. Optimal parameters of roast has been determined. Keywords: Gold, precious metals, copper, electronic scrap, collector smelting, recycle, roast 1. Introduction. Organic materials (polystyrene, hardened paper, One of mass valuable type of complex recyclable metallurgical polyvinylchloride etc.) make 5-27 % of electronic scrap, according raw is electronic scrap. Total value of obtained electronic scrap in to scrap’s type. Organic materials have to be removed from Russia is millions tons per year now. During conversion to market electronic scrap preliminarily (before melt) due to high speed of economy thousands of unprofitable plants has been stopped and organic materials’ combusting significant amount of obtained gases liquidated in recent years, huge amounts equipment and hardware as well as problem with recovery and cleaning. has been formed, that should be recycled. On the one hand this In connection with the above electronic scrap with precious scrap is damage to environment, and on the other hand it’s very metals is preliminarily treated by roast. valuable recourse, that exceed raw mineral in precious components’ Degree of organic removal from electronic scrap in dependence content. Usage of complex-composition hard-processing electronic of temperature, duration has been studied when research was scrap in metal recycling is increased now. -
Gold Extraction by Chlorination Using a Pyrometallurgical Process
Minerals Engineering 22 (2009) 409–411 Contents lists available at ScienceDirect Minerals Engineering journal homepage: www.elsevier.com/locate/mineng Technical Note Gold extraction by chlorination using a pyrometallurgical process M.W. Ojeda a,*, E. Perino b, M. del C. Ruiz a a Instituto de Investigaciones en Tecnología Química (INTEQUI), Universidad Nacional de San Luis-CONICET, C.C. 290, 5700 San Luis, Argentina b Área de Química Analítica, Universidad Nacional de San Luis, San Luis, Argentina article info abstract Article history: The feasibility to recover the gold present in alluvial material, by means of a chlorination process, using Received 18 October 2007 chlorine as a reactive agent, has been studied. The influence of temperature and reaction time was stud- Accepted 4 September 2008 ied through changes in the reactant solid. The techniques used to characterize the mineral samples and Available online 15 October 2008 the reaction residues were stereomicroscopy, X-ray diffraction, X-ray fluorescence and scanning elec- tronic microscopy. Results indicate that gold extraction is favored by increasing, both, the temperature Keywords: and the reaction time. The best recovery values were of 98.23% at 873 K and 3600 s and of 98.73% at Gold ores 873 K and 5400 s, with very low attack of the matrix containing the metal. The powder of pure gold Pyrometallurgy was not chlorinated at this temperature level. Extractive metallurgy Ó 2008 Elsevier Ltd. All rights reserved. 1. Introduction X-ray fluorescence (XRF), X-ray diffraction (XRD) and scanning electronic microscopy (SEM) techniques. Over the last years, gold recovery has been the central issue in a wide range of studies as a consequence of its high demand and va- 2. -
Analysis of Dental Gold Alloys
S532 ANALYSIS OF DENTAL GOLD ALLOYS By William H. Swanger AESTRACT Complete chemical analyses of about 40 dental gold alloys were made as part of the investigation of their physical properties. These analyses required the determination of silver, gold, platinum, palladium, iridium, rhodium, copper, zinc, nickel, tin, manganese, iron, and magnesium. Methods as found in the literature for the determination of the above-named metals were modified so as to give accurate results when applied to alloys of this type. New methods were developed for the determination of tin and iridium. Many analyses of mixtures of known composition are given to show the degree of accuracy of the methods used. These methods are assembled in a detailed procedure for the complete analysis of dental gold alloys. The composition of 13 typical alloys is given in a table. CONTENTS Page I. Introduction 210 II. Sampling 210 III. Reagents 211 IV. Qualitative examination 212 1. Detection of silver and iridium 212 2. Detection of tin and iron 213 3. Detection of gold 214 4. Detection of copper 214 5. Detection of platinum, palladium, and rhodium 215 6. Detection of nickel, manganese, zinc, and magnesium 216 V. Determination of silver 217 VI. Determination of iridium 218 VII. Determination of tin 221 VIII. Determination of gold ' 225 IX. Determination of palladium 228 X. Determination of copper 229 XI. Determination of platinum 231 XII. Determination of rhodium 233 XIII. Determination of zinc 234 XIV. Determination of nickel 235 XV. Determination of manganese 236 XVI. Determination of iron 237 XVII. Determination of magnesium 237 XVIII. Results of analyses of a number of alloys 238 XIX. -
Principles of Extractive Metallurgy
Principles of Extractive Metallurgy by Professor Nosa O. Egiebor Environmental Engineering Program Department of Chemical Engineering Tuskegee University Tuskegee, AL 36088 USA Course Reference Texts Materials for the course were taken from multiple textbook. The main texts include: Principles of Extractive Metallurgy by Terkel Rosenquist; Tapir Academic Press, Trondheim, Norway, 2004. The Chemistry of Gold Extraction (2nd Ed) by John O. Marsden and C. Lain House, SME Littleton, Colorado, USA (2006) Process Selection in Extractive Metallurgy by Peter Hayes, Hayes Publishing Co., Brisbane, Australia (1985) Instructor’s Lecture Notes, Prof. Nosa O. Egiebor (2011) Introduction - Definitions Metallurgy is the science of extracting and refining metals from ores and the compounding of metals to form alloys. Extractive metallurgy is the branch of metallurgical science & engineering which deals with the extraction and refining of metals from ores. An ore is a rock that contains commercially viable amounts of metallic/non-metallic solid minerals. Ores are complex associations of mineral grains A mineral is a chemical compound that constitute a component of an ore, and with its own characteristic chemical composition. Introduction – Types of Ores & Minerals Most metals are combined with other elements to form minerals. Few exist as pure metals. The table below provides examples of the common types of ores with minerals, their chemical formula and Common Names: Native Metals (Can occur as Pure Metals) Silver-(Ag), Gold-(Au), Bismuth-(Bi), -
Comparison of Different Gold Recovery Methods with Regard To
52 Clean 2007, 35 (1), 52 – 61 Lars D. Hylander1 Research Article David Plath2 Conrado R. Miranda3 Sofie Lcke1 Comparison of Different Gold Recovery Methods Jenny hlander1 Ana T. F. Rivera4 with Regard to Pollution Control and Efficiency 1 Uppsala University, Department of Earth This case study performed at the largest gold mining village in the Philippines compa- Sciences, Air, Water and Landscape res four methods for gold recovery: amalgamation, cyanide leaching, a shaking sluice, Science, Sweden. and Cleangoldm sluices. The results show that a combination of manual panning or 2 Cleangold, Lincoln City, OR, USA. Cleangoldm sluices followed by cyanidation is the best solution under present condi- 3 Mines and Geosciences Bureau, The tions, followed by cyanidation alone. Based on the knowledge obtained, remarks on Philippines. suitable policy actions, which may be applied also in other gold fields, are made. 4 Environmental and Occupational Health Keywords: Amalgamation; Cyanide; Gravity Separation; Mercury; Small-scale Gold Mining; Office, National Center for Disease Prevention and Control, Department of Received: November 14, 2006; revised: December 11, 2006; accepted: December 16, 2006 Health, The Philippines. DOI: 10.1002/clen.200600024 1 Introduction mining, where the technique of amalgamation with Hg, generally, is not feasible [6]. The UNIDO Global Mercury Project estimates that Amalgamation with mercury is the dominating method for gold alluvial gold deposits could be as low as 10% of the ores worked by extraction used by 10 million small-scale gold miners (SSGM) in SSGM [12]. more than 50 countries, resulting in that several hundred to possi- Here results from comparative studies are presented of ore pro- bly 1000 tons of Hg are annually released into soil, air, and water [1].