Table of Contents
Total Page:16
File Type:pdf, Size:1020Kb
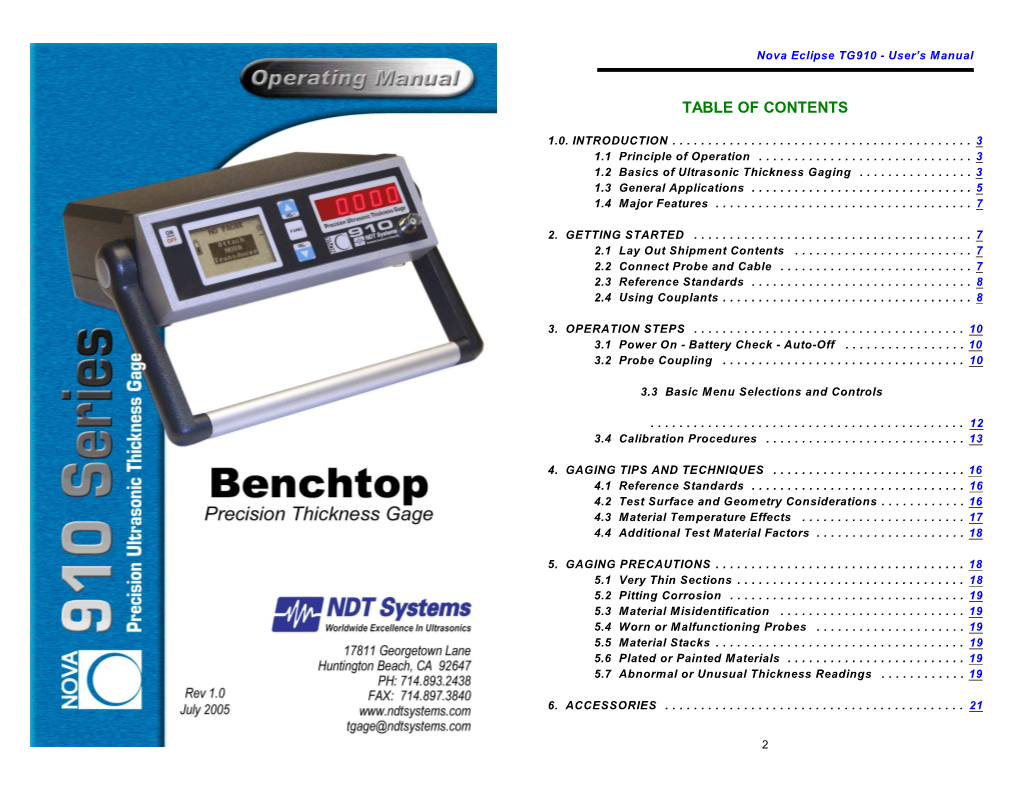
Load more
Recommended publications
-
Time and Frequency Users' Manual
,>'.)*• r>rJfl HKra mitt* >\ « i If I * I IT I . Ip I * .aference nbs Publi- cations / % ^m \ NBS TECHNICAL NOTE 695 U.S. DEPARTMENT OF COMMERCE/National Bureau of Standards Time and Frequency Users' Manual 100 .U5753 No. 695 1977 NATIONAL BUREAU OF STANDARDS 1 The National Bureau of Standards was established by an act of Congress March 3, 1901. The Bureau's overall goal is to strengthen and advance the Nation's science and technology and facilitate their effective application for public benefit To this end, the Bureau conducts research and provides: (1) a basis for the Nation's physical measurement system, (2) scientific and technological services for industry and government, a technical (3) basis for equity in trade, and (4) technical services to pro- mote public safety. The Bureau consists of the Institute for Basic Standards, the Institute for Materials Research the Institute for Applied Technology, the Institute for Computer Sciences and Technology, the Office for Information Programs, and the Office of Experimental Technology Incentives Program. THE INSTITUTE FOR BASIC STANDARDS provides the central basis within the United States of a complete and consist- ent system of physical measurement; coordinates that system with measurement systems of other nations; and furnishes essen- tial services leading to accurate and uniform physical measurements throughout the Nation's scientific community, industry, and commerce. The Institute consists of the Office of Measurement Services, and the following center and divisions: Applied Mathematics -
The Impact of the Speed of Light on Financial Markets and Their Regulation
When Finance Meets Physics: The Impact of the Speed of Light on Financial Markets and their Regulation by James J. Angel, Ph.D., CFA Associate Professor of Finance McDonough School of Business Georgetown University 509 Hariri Building Washington DC 20057 USA 1.202.687.3765 [email protected] The Financial Review, Forthcoming, May 2014 · Volume 49 · No. 2 Abstract: Modern physics has demonstrated that matter behaves very differently as it approaches the speed of light. This paper explores the implications of modern physics to the operation and regulation of financial markets. Information cannot move faster than the speed of light. The geographic separation of market centers means that relativistic considerations need to be taken into account in the regulation of markets. Observers in different locations may simultaneously observe different “best” prices. Regulators may not be able to determine which transactions occurred first, leading to problems with best execution and trade- through rules. Catastrophic software glitches can quantum tunnel through seemingly impregnable quality control procedures. Keywords: Relativity, Financial Markets, Regulation, High frequency trading, Latency, Best execution JEL Classification: G180 The author is also on the board of directors of the Direct Edge stock exchanges (EDGX and EDGA). I wish to thank the editor and referee for extremely helpful comments and suggestions. I also wish to thank the U.K. Foresight Project, for providing financial support for an earlier version of this paper. All opinions are strictly my own and do not necessarily represent those of Georgetown University, Direct Edge, the U.K. Foresight Project, The Financial Review, or anyone else for that matter. -
Using Microsecond Single-Molecule FRET to Determine the Assembly
Using microsecond single-molecule FRET to determine PNAS PLUS the assembly pathways of T4 ssDNA binding protein onto model DNA replication forks Carey Phelpsa,b,1, Brett Israelsa,b, Davis Josea, Morgan C. Marsha,b, Peter H. von Hippela,2, and Andrew H. Marcusa,b,2 aDepartment of Chemistry and Biochemistry, Institute of Molecular Biology, University of Oregon, Eugene, OR 97403; and bDepartment of Chemistry and Biochemistry, Oregon Center for Optical, Molecular and Quantum Science, University of Oregon, Eugene, OR 97403 Edited by Stephen C. Kowalczykowski, University of California, Davis, CA, and approved March 20, 2017 (received for review December 2, 2016) DNA replication is a core biological process that occurs in pro- complete coverage of the exposed ssDNA templates at the precisely karyotic cells at high speeds (∼1 nucleotide residue added per regulated concentration of protein that needs to be maintained in millisecond) and with high fidelity (fewer than one misincorpora- the infected Escherichia coli cell (8, 9). The gp32 protein has an tion event per 107 nucleotide additions). The ssDNA binding pro- N-terminal domain, a C-terminal domain, and a core domain. tein [gene product 32 (gp32)] of the T4 bacteriophage is a central The N-terminal domain is necessary for the cooperative binding integrating component of the replication complex that must con- of the gp32 protein through its interactions with the core domain of tinuously bind to and unbind from transiently exposed template an adjacent gp32 protein. To bind to ssDNA, the C-terminal domain strands during DNA synthesis. We here report microsecond single- of the gp32 protein must undergo a conformational change that molecule FRET (smFRET) measurements on Cy3/Cy5-labeled primer- exposes the positively charged region of its core domain, which in template (p/t) DNA constructs in the presence of gp32. -
Aquatic Primary Productivity Field Protocols for Satellite Validation and Model Synthesis (DRAFT)
Ocean Optics & Biogeochemistry Protocols for Satellite Ocean Colour Sensor Validation IOCCG Protocol Series Volume 7.0, 2021 Aquatic Primary Productivity Field Protocols for Satellite Validation and Model Synthesis (DRAFT) Report of a NASA-sponsored workshop with contributions (alphabetical) from: William M. Balch Bigelow Laboratory for Ocean Sciences, Maine, USA Magdalena M. Carranza Monterey Bay Aquarium Research Institute, California, USA Ivona Cetinic University Space Research Association, NASA Goddard Space Flight Center, Maryland, USA Joaquín E. Chaves Science Systems and Applications, Inc., NASA Goddard Space Flight Center, Maryland, USA Solange Duhamel University of Arizona, Arizona, USA Zachary K. Erickson University Space Research Association, NASA Goddard Space Flight Center, Maryland, USA Andrea J. Fassbender NOAA Pacific Marine Environmental Laboratory, Washington, USA Ana Fernández-Carrera Leibniz Institute for Baltic Sea Research Warnemünde, Rostock, Germany Sara Ferrón University of Hawaii at Manoa, Hawaii, USA E. Elena García-Martín National Oceanography Centre, Southampton, UK Joaquim Goes Lamont Doherty Earth Observatory at Columbia University, New York, USA Helga do Rosario Gomes Lamont Doherty Earth Observatory at Columbia University, New York, USA Maxim Y. Gorbunov Department of Marine and Coastal Sciences, Rutgers University, New Jersey, USA Kjell Gundersen Plankton Research Group, Institute of Marine Research, Bergen, Norway Kimberly Halsey Department of Microbiology, Oregon State University, Oregon, USA Toru Hirawake -
Nanosecond X-Ray Photon Correlation Spectroscopy Using Pulse Time
research papers Nanosecond X-ray photon correlation spectroscopy IUCrJ using pulse time structure of a storage-ring source ISSN 2052-2525 NEUTRONjSYNCHROTRON Wonhyuk Jo,a Fabian Westermeier,a Rustam Rysov,a Olaf Leupold,a Florian Schulz,b,c Steffen Tober,b‡ Verena Markmann,a Michael Sprung,a Allesandro Ricci,a Torsten Laurus,a Allahgholi Aschkan,a Alexander Klyuev,a Ulrich Trunk,a Heinz Graafsma,a Gerhard Gru¨bela,c and Wojciech Rosekera* Received 25 September 2020 Accepted 2 December 2020 aDeutsches Elektronen-Synchrotron (DESY), Notkestr. 85, 22607 Hamburg, Germany, bInstitute of Physical Chemistry, University of Hamburg, Grindelallee 117, 20146 Hamburg, Germany, and cThe Hamburg Centre for Ultrafast Imaging, Luruper Chaussee 149, 22761 Hamburg, Germany. *Correspondence e-mail: [email protected] Edited by Dr T. Ishikawa, Coherent X-ray Optics Laboratory, Harima Institute, RIKEN, Japan X-ray photon correlation spectroscopy (XPCS) is a routine technique to study slow dynamics in complex systems at storage-ring sources. Achieving ‡ Current address: Deutsches Elektronen- Synchrotron (DESY), Notkestr. 85, 22607 nanosecond time resolution with the conventional XPCS technique is, however, Hamburg, Germany. still an experimentally challenging task requiring fast detectors and sufficient photon flux. Here, the result of a nanosecond XPCS study of fast colloidal Keywords: materials science; nanoscience; dynamics is shown by employing an adaptive gain integrating pixel detector SAXS; dynamical studies; time-resolved studies; (AGIPD) operated at frame rates of the intrinsic pulse structure of the storage X-ray photon correlation spectroscopy; adaptive ring. Correlation functions from single-pulse speckle patterns with the shortest gain integrating pixel detectors; storage rings; pulse structures. -
Low Latency – How Low Can You Go?
WHITE PAPER Low Latency – How Low Can You Go? Low latency has always been an important consideration in telecom networks for voice, video, and data, but recent changes in applications within many industry sectors have brought low latency right to the forefront of the industry. The finance industry and algorithmic trading in particular, or algo-trading as it is known, is a commonly quoted example. Here latency is critical, and to quote Information Week magazine, “A 1-millisecond advantage in trading applications can be worth $100 million a year to a major brokerage firm.” This drives a huge focus on all aspects of latency, including the communications systems between the brokerage firm and the exchange. However, while the finance industry is spending a lot of money on low- latency services between key locations such as New York and Chicago or London and Frankfurt, this is actually only a small part of the wider telecom industry. Many other industries are also now driving lower and lower latency in their networks, such as for cloud computing and video services. Also, as mobile operators start to roll out 5G services, latency in the xHaul mobile transport network, especially the demanding fronthaul domain, becomes more and more important in order to reach the stringent 5G requirements required for the new class of ultra-reliable low-latency services. This white paper will address the drivers behind the recent rush to low- latency solutions and networks and will consider how network operators can remove as much latency as possible from their networks as they also race to zero latency. -
Simulating Nucleic Acids from Nanoseconds to Microseconds
UC Irvine UC Irvine Electronic Theses and Dissertations Title Simulating Nucleic Acids from Nanoseconds to Microseconds Permalink https://escholarship.org/uc/item/6cj4n691 Author Bascom, Gavin Dennis Publication Date 2014 Peer reviewed|Thesis/dissertation eScholarship.org Powered by the California Digital Library University of California UNIVERSITY OF CALIFORNIA, IRVINE Simulating Nucleic Acids from Nanoseconds to Microseconds DISSERTATION submitted in partial satisfaction of the requirements for the degree of DOCTOR OF PHILOSOPHY in Chemistry, with a specialization in Theoretical Chemistry by Gavin Dennis Bascom Dissertation Committee: Professor Ioan Andricioaei, Chair Professor Douglas Tobias Professor Craig Martens 2014 Appendix A c 2012 American Chemical Society All other materials c 2014 Gavin Dennis Bascom DEDICATION To my parents, my siblings, and to my love, Lauren. ii TABLE OF CONTENTS Page LIST OF FIGURES vi LIST OF TABLES x ACKNOWLEDGMENTS xi CURRICULUM VITAE xii ABSTRACT OF THE DISSERTATION xiv 1 Introduction 1 1.1 Nucleic Acids in a Larger Context . 1 1.2 Nucleic Acid Structure . 5 1.2.1 DNA Structure/Motion Basics . 5 1.2.2 RNA Structure/Motion Basics . 8 1.2.3 Experimental Techniques for Nucleic Acid Structure Elucidation . 9 1.3 Simulating Trajectories by Molecular Dynamics . 11 1.3.1 Integrating Newtonian Equations of Motion and Force Fields . 12 1.3.2 Treating Non-bonded Interactions . 15 1.4 Defining Our Scope . 16 2 The Nanosecond 28 2.1 Introduction . 28 2.1.1 Biological Processes of Nucleic Acids at the Nanosecond Timescale . 29 2.1.2 DNA Motions on the Nanosecond Timescale . 32 2.1.3 RNA Motions on the Nanosecond Timescale . -
Microsecond and Millisecond Dynamics in the Photosynthetic
Microsecond and millisecond dynamics in the photosynthetic protein LHCSR1 observed by single-molecule correlation spectroscopy Toru Kondoa,1,2, Jesse B. Gordona, Alberta Pinnolab,c, Luca Dall’Ostob, Roberto Bassib, and Gabriela S. Schlau-Cohena,1 aDepartment of Chemistry, Massachusetts Institute of Technology, Cambridge, MA 02139; bDepartment of Biotechnology, University of Verona, 37134 Verona, Italy; and cDepartment of Biology and Biotechnology, University of Pavia, 27100 Pavia, Italy Edited by Catherine J. Murphy, University of Illinois at Urbana–Champaign, Urbana, IL, and approved April 11, 2019 (received for review December 13, 2018) Biological systems are subjected to continuous environmental (5–9) or intensity correlation function analysis (10). CPF analysis fluctuations, and therefore, flexibility in the structure and func- bins the photon data, obscuring fast dynamics. In contrast, inten- tion of their protein building blocks is essential for survival. sity correlation function analysis characterizes fluctuations in the Protein dynamics are often local conformational changes, which photon arrival rate, accessing dynamics down to microseconds. allows multiple dynamical processes to occur simultaneously and However, the fluorescence lifetime is a powerful indicator of rapidly in individual proteins. Experiments often average over conformation for chromoproteins and for lifetime-based FRET these dynamics and their multiplicity, preventing identification measurements, yet it is ignored in intensity-based analyses. of the molecular origin and impact on biological function. Green 2D fluorescence lifetime correlation (2D-FLC) analysis was plants survive under high light by quenching excess energy, recently introduced as a method to both resolve fast dynam- and Light-Harvesting Complex Stress Related 1 (LHCSR1) is the ics and use fluorescence lifetime information (11, 12). -
Picosecond Multi-Hole Transfer and Microsecond Charge- Separated States at the Perovskite Nanocrystal/Tetracene Interface
Electronic Supplementary Material (ESI) for Chemical Science. This journal is © The Royal Society of Chemistry 2019 Electronic Supplementary Information for: Picosecond Multi-Hole Transfer and Microsecond Charge- Separated States at the Perovskite Nanocrystal/Tetracene Interface Xiao Luo, a,† Guijie Liang, ab,† Junhui Wang,a Xue Liu,a and Kaifeng Wua* a State Key Laboratory of Molecular Reaction Dynamics, Dynamics Research Center for Energy and Environmental Materials, and Collaborative Innovation Center of Chemistry for Energy Materials (iChEM), Dalian Institute of Chemical Physics, Chinese Academy of Sciences, Dalian, Liaoning 116023, China b Hubei Key Laboratory of Low Dimensional Optoelectronic Materials and Devices, Hubei University of Arts and Science, Xiangyang, Hubei 441053, China * Corresponding Author: [email protected] † Xiao Luo and Guijie Liang contributed equally to this work. Content list: Figures S1-S9 Sample preparations TA experiment set-ups Estimation of the number of attached TCA molecules per NC Estimation of FRET rate Estimation of average exciton number at each excitation density Estimation of exciton dissociation number S1 a 100 b long edge c short edge 70 7.90.1 nm 9.60.1 nm 60 80 50 s s 60 t t n 40 n u u o o C 30 C 40 20 20 10 0 0 4 6 8 10 12 14 16 18 2 4 6 8 10 12 Size (nm) Size (nm) Figure S1. (a) A representative transmission electron microscopy (TEM) image of CsPbBrxCl3-x perovskite NCs used in this study. Inset: high-resolution TEM. (b,c) Length distribution histograms of the NCs along the long (b) and short (c) edges. -
EXAMPLE EXERCISE 3.1 Metric Basic Units and Prefixes
EXAMPLE EXERCISE 3.1 Metric Basic Units and Prefixes Give the symbol for each of the following metric units and state the quantity measured by each unit: (a) gigameter (b) kilogram (c) centiliter (d) microsecond Solution We compose the symbol for each unit by combining the prefix symbol and the basic unit symbol. If we refer to Tables 3.1 and 3.2, we have the following: (a) Gm, length (b) kg, mass (c) cL, volume (d) µs, time Introductory Chemistry: Concepts and Critical Thinking, 6th Edition © 2011 Pearson Education, Inc. Charles H. Corwin EXAMPLE EXERCISE 3.1 Metric Basic Units and Prefixes Continued Practice Exercise Give the symbol for each of the following metric units and state the quantity measured by each unit: (a) nanosecond (b) milliliter (c) decigram (d) megameter Answers: (a) ns, time; (b) mL, volume; (c) dg, mass; (d) Mm, length Concept Exercise What is the basic unit of length, mass, and volume in the metric system? Answer: See Appendix G. Introductory Chemistry: Concepts and Critical Thinking, 6th Edition © 2011 Pearson Education, Inc. Charles H. Corwin EXAMPLE EXERCISE 3.2 Metric Unit Equations Complete the unit equation for each of the following exact metric equivalents: (a) 1 Mm = ? m (b) 1 kg = ? g (c) 1 L = ? dL (d) 1 s = ? ns Solution We can refer to Table 3.2 as necessary. (a) The prefix mega- means 1,000,000 basic units; thus, 1 Mm = 1,000,000 m. (b) The prefix kilo- means 1000 basic units; thus, 1 kg = 1000 g. (c) The prefix deci- means 0.1 of a basic unit, thus, 1 L = 10 dL. -
Siunitx – a Comprehensive (Si) Units Package∗
siunitx – A comprehensive (si) units package∗ Joseph Wright† Released 2021-09-22 Contents 1 Introduction 3 2 siunitx for the impatient 3 3 Using the siunitx package 4 3.1 Numbers . 4 3.2 Angles . 5 3.3 Units . 6 3.4 Complex numbers and quantities . 7 3.5 The unit macros . 8 3.6 Unit abbreviations . 10 3.7 Creating new macros . 14 3.8 Tabular material . 15 4 Package control options 17 4.1 The key–value control system . 17 4.2 Printing . 18 4.3 Parsing numbers . 20 4.4 Post-processing numbers . 22 4.5 Printing numbers . 25 4.6 Lists, products and ranges . 28 4.7 Complex numbers . 31 4.8 Angles . 32 4.9 Creating units . 34 4.10 Using units . 35 4.11 Quantities . 38 4.12 Tabular material . 39 4.13 Locale options . 49 4.14 Preamble-only options . 49 5 Upgrading from version 2 49 6 Unit changes made by BIPM 51 ∗This file describes v3.0.31, last revised 2021-09-22. †E-mail: [email protected] 1 7 Localisation 52 8 Compatibility with other packages 52 9 Hints for using siunitx 52 9.1 Adjusting \litre and \liter ........................ 52 9.2 Ensuring text or math output . 53 9.3 Expanding content in tables . 53 9.4 Using siunitx with datatool .......................... 54 9.5 Using units in section headings and bookmarks . 55 9.6 A left-aligned column visually centred under a heading . 56 9.7 Regression tables . 57 9.8 Maximising performance . 58 9.9 Special considerations for the \kWh unit . -
Microsecond-Timescale Simulations Suggest 5-HT–Mediated
Microsecond-timescale simulations suggest 5-HT– mediated preactivation of the 5-HT3A serotonin receptor Nicholas B. Gurosa,b, Arvind Balijepallib, and Jeffery B. Klaudaa,1 aDepartment of Chemical and Biomolecular Engineering, University of Maryland, College Park, MD 20742; and bBiophysics Group, Microsystems and Nanotechnology Division, National Institute of Standards and Technology, Gaithersburg, MD 20899 Edited by Michael L. Klein, Temple University, Philadelphia, PA, and approved November 27, 2019 (received for review May 22, 2019) Aided by efforts to improve their speed and efficiency, molecular Molecular dynamics (MD) simulations are a useful technique dynamics (MD) simulations provide an increasingly powerful tool for examining the basis of pLGIC function, including the to study the structure–function relationship of pentameric ligand- mechanisms that govern rapid and dynamic transitions between gated ion channels (pLGICs). However, accurate reporting of the states that cannot be observed through experimental techniques channel state and observation of allosteric regulation by agonist (10–12). Numerous pLGICs have been investigated using all- binding with MD remains difficult due to the timescales necessary atom MD simulations, including the nicotinic acetylcholine to equilibrate pLGICs from their artificial and crystalized conforma- (nAChR) (13), glutamate-gated chloride channel (GluCl) (14), tion to a more native, membrane-bound conformation in silico. and glycine (GlyR) (15) receptors, which have provided valuable Here, we perform