Enhancing NEMD with Automatic Shear Rate Sampling to Model
Total Page:16
File Type:pdf, Size:1020Kb
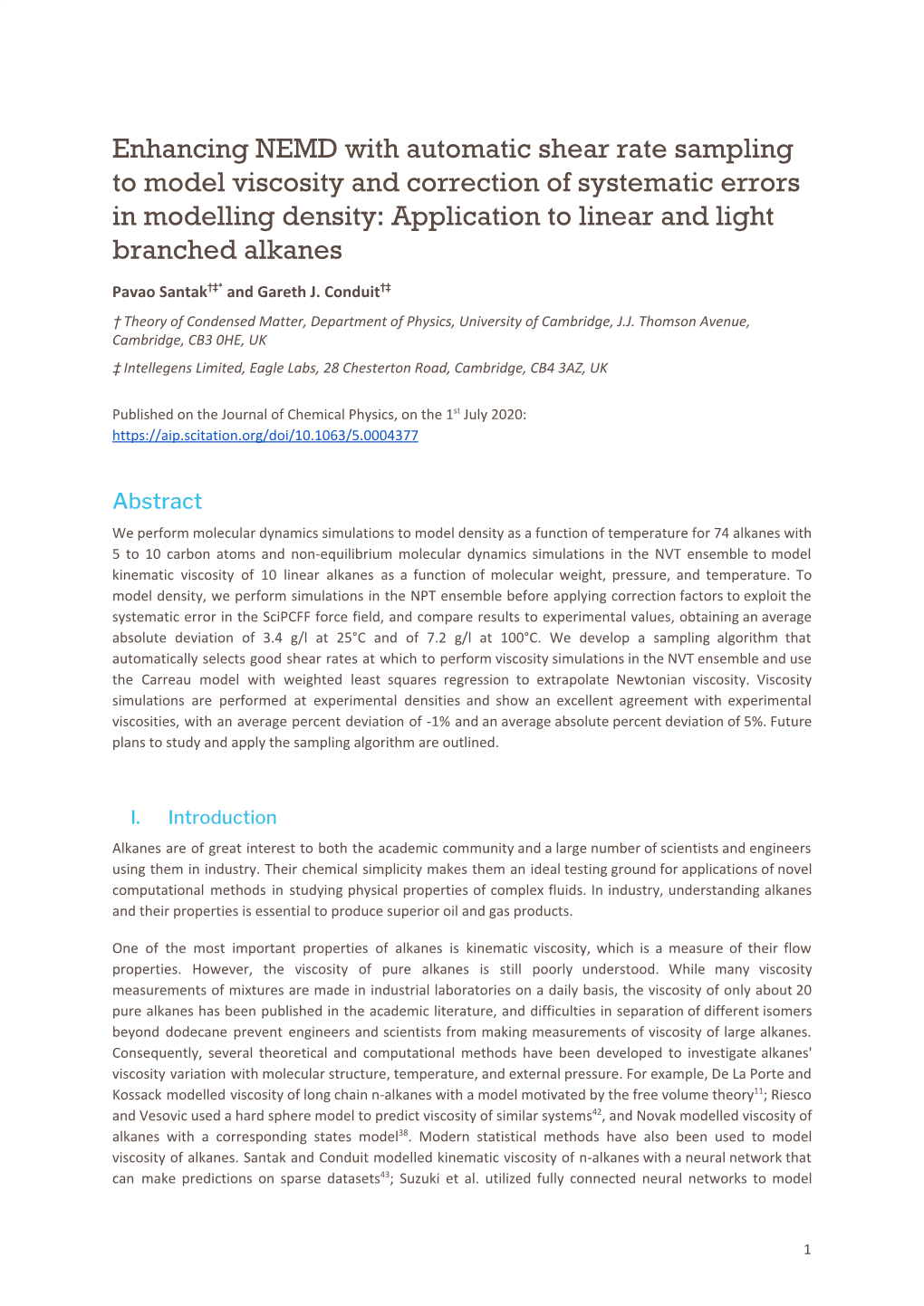
Load more
Recommended publications
-
Quantitation of Hydrocarbons in Vehicle Exhaust and Ambient Air
QUANTITATION OF HYDROCARBONS IN VEHICLE EXHAUST AND AMBIENT AIR by Randall Bramston-Cook Lotus Consulting 5781 Campo Walk, Long Beach, California 90803 Presented at EPA Measurement of Toxic and Related Air Pollutants Conference, Cary, North Caolina, September 1, 1998 Copyright 1998 Lotus Flower, Inc. QUANTITATION OF HYDROCARBONS IN VEHICLE EXHAUST AND AMBIENT AIR Randall Bramston-Cook Lotus Consulting 5781 Campo Walk, Long Beach, California 90803 ABSTRACT Ironically, one of the most complex analyses in gas chromatography involves the simplest computation to generate concentrations. The difficult determination of hydrocarbons in vehicle exhaust and ambient air involves separation of over 200 compounds, requires cryogenic concentration to bring expected concentrations into a detectable range, and mandates usage of multiple columns and intricate valving. Yet, quantitation of these hydrocarbons can be calibrated with only one or two component standards and a simple mathematical operation. Requirements for meeting this goal include: (1) even detector responses for all hydrocarbons from ethane to n-tridecane (including olefins and aromatics), (2) accurate and reproducible measure of the sample injection volumes, (3) maximizing trap, column and detector performances, and (4) minimizing sample carry-over. Importance of these factors and how they can be implemented in routine measurements are presented with examples from vehicle exhaust and ambient air analyses. TEXT Hydrocarbons remain a major pollutant in our atmosphere. Much of the problem generated is from incomplete combustion and unburned fuel in vehicle exhaust. Accurate measure of atmospheric and exhaust levels for hydrocarbons is on-going in many facilities in the world. This analysis is undoubtedly one of the most complex in chromatography due to large number of individual hydrocarbon components found, the low levels required to be measured, and high concentrations of potential inferences to the measuring process. -
Measurements of Higher Alkanes Using NO Chemical Ionization in PTR-Tof-MS
Atmos. Chem. Phys., 20, 14123–14138, 2020 https://doi.org/10.5194/acp-20-14123-2020 © Author(s) 2020. This work is distributed under the Creative Commons Attribution 4.0 License. Measurements of higher alkanes using NOC chemical ionization in PTR-ToF-MS: important contributions of higher alkanes to secondary organic aerosols in China Chaomin Wang1,2, Bin Yuan1,2, Caihong Wu1,2, Sihang Wang1,2, Jipeng Qi1,2, Baolin Wang3, Zelong Wang1,2, Weiwei Hu4, Wei Chen4, Chenshuo Ye5, Wenjie Wang5, Yele Sun6, Chen Wang3, Shan Huang1,2, Wei Song4, Xinming Wang4, Suxia Yang1,2, Shenyang Zhang1,2, Wanyun Xu7, Nan Ma1,2, Zhanyi Zhang1,2, Bin Jiang1,2, Hang Su8, Yafang Cheng8, Xuemei Wang1,2, and Min Shao1,2 1Institute for Environmental and Climate Research, Jinan University, 511443 Guangzhou, China 2Guangdong-Hongkong-Macau Joint Laboratory of Collaborative Innovation for Environmental Quality, 511443 Guangzhou, China 3School of Environmental Science and Engineering, Qilu University of Technology (Shandong Academy of Sciences), 250353 Jinan, China 4State Key Laboratory of Organic Geochemistry and Guangdong Key Laboratory of Environmental Protection and Resources Utilization, Guangzhou Institute of Geochemistry, Chinese Academy of Sciences, 510640 Guangzhou, China 5State Joint Key Laboratory of Environmental Simulation and Pollution Control, College of Environmental Sciences and Engineering, Peking University, 100871 Beijing, China 6State Key Laboratory of Atmospheric Boundary Physics and Atmospheric Chemistry, Institute of Atmospheric Physics, Chinese -
Supporting Information for Modeling the Formation and Composition Of
Supporting Information for Modeling the Formation and Composition of Secondary Organic Aerosol from Diesel Exhaust Using Parameterized and Semi-explicit Chemistry and Thermodynamic Models Sailaja Eluri1, Christopher D. Cappa2, Beth Friedman3, Delphine K. Farmer3, and Shantanu H. Jathar1 1 Department of Mechanical Engineering, Colorado State University, Fort Collins, CO, USA, 80523 2 Department of Civil and Environmental Engineering, University of California Davis, Davis, CA, USA, 95616 3 Department of Chemistry, Colorado State University, Fort Collins, CO, USA, 80523 Correspondence to: Shantanu H. Jathar ([email protected]) Table S1: Mass speciation and kOH for VOC emissions profile #3161 3 -1 - Species Name kOH (cm molecules s Mass Percent (%) 1) (1-methylpropyl) benzene 8.50×10'() 0.023 (2-methylpropyl) benzene 8.71×10'() 0.060 1,2,3-trimethylbenzene 3.27×10'(( 0.056 1,2,4-trimethylbenzene 3.25×10'(( 0.246 1,2-diethylbenzene 8.11×10'() 0.042 1,2-propadiene 9.82×10'() 0.218 1,3,5-trimethylbenzene 5.67×10'(( 0.088 1,3-butadiene 6.66×10'(( 0.088 1-butene 3.14×10'(( 0.311 1-methyl-2-ethylbenzene 7.44×10'() 0.065 1-methyl-3-ethylbenzene 1.39×10'(( 0.116 1-pentene 3.14×10'(( 0.148 2,2,4-trimethylpentane 3.34×10'() 0.139 2,2-dimethylbutane 2.23×10'() 0.028 2,3,4-trimethylpentane 6.60×10'() 0.009 2,3-dimethyl-1-butene 5.38×10'(( 0.014 2,3-dimethylhexane 8.55×10'() 0.005 2,3-dimethylpentane 7.14×10'() 0.032 2,4-dimethylhexane 8.55×10'() 0.019 2,4-dimethylpentane 4.77×10'() 0.009 2-methylheptane 8.28×10'() 0.028 2-methylhexane 6.86×10'() -
Safety Data Sheet
SAFETY DATA SHEET Flammable Liquid Mixture: Docosane / Dodecane / Hexadecane / Hexane / N-Decane / N-Heptane / N-Nonane / N-Octadecane / N-Octane / N-Tridecane / Octacosane / Tetracosane / Tetradecane / Tricontane Section 1. Identification GHS product identifier : Flammable Liquid Mixture: Docosane / Dodecane / Hexadecane / Hexane / N-Decane / N-Heptane / N-Nonane / N-Octadecane / N-Octane / N-Tridecane / Octacosane / Tetracosane / Tetradecane / Tricontane Other means of : Not available. identification Product use : Synthetic/Analytical chemistry. SDS # : 018776 Supplier's details : Airgas USA, LLC and its affiliates 259 North Radnor-Chester Road Suite 100 Radnor, PA 19087-5283 1-610-687-5253 24-hour telephone : 1-866-734-3438 Section 2. Hazards identification OSHA/HCS status : This material is considered hazardous by the OSHA Hazard Communication Standard (29 CFR 1910.1200). Classification of the : FLAMMABLE LIQUIDS - Category 1 substance or mixture SKIN CORROSION/IRRITATION - Category 2 SERIOUS EYE DAMAGE/ EYE IRRITATION - Category 2A TOXIC TO REPRODUCTION (Fertility) - Category 2 TOXIC TO REPRODUCTION (Unborn child) - Category 2 SPECIFIC TARGET ORGAN TOXICITY (SINGLE EXPOSURE) (Respiratory tract irritation) - Category 3 SPECIFIC TARGET ORGAN TOXICITY (SINGLE EXPOSURE) (Narcotic effects) - Category 3 SPECIFIC TARGET ORGAN TOXICITY (REPEATED EXPOSURE) - Category 2 AQUATIC HAZARD (ACUTE) - Category 2 AQUATIC HAZARD (LONG-TERM) - Category 1 GHS label elements Hazard pictograms : Signal word : Danger Hazard statements : Extremely flammable liquid and vapor. May form explosive mixtures in Air. Causes serious eye irritation. Causes skin irritation. May cause respiratory irritation. Suspected of damaging fertility or the unborn child. May cause drowsiness and dizziness. May cause damage to organs through prolonged or repeated exposure. Very toxic to aquatic life with long lasting effects. -
Accuracy and Methodologic Challenges of Volatile Organic Compound–Based Exhaled Breath Tests for Cancer Diagnosis: a Systematic Review and Pooled Analysis
1 Supplementary Online Content Hanna GB, Boshier PR, Markar SR, Romano A. Accuracy and Methodologic Challenges of Volatile Organic Compound–Based Exhaled Breath Tests for Cancer Diagnosis: A Systematic Review and Pooled Analysis. JAMA Oncol. Published online August 16, 2018. doi:10.1001/jamaoncol.2018.2815 Supplement. eTable 1. Search strategy for cancer systematic review eTable 2. Modification of QUADAS-2 assessment tools eTable 3. QUADAS-2 results eTable 6. STARD assessment of each study eTable 7. Summary of factors reported to influence levels of volatile organic compounds within exhaled breath eFigure 1. Risk of bias and applicability concerns using QUADAS-2 eFigure 2. PRISMA flowchart of literature search eTable 4. Details of studies on exhaled volatile organic compounds in cancer eTable 5. Cancer VOCs in exhaled breath and their chemical class. eFigure 3. Chemical classes of VOCs reported in different tumor sites. This supplementary material has been provided by the authors to give readers additional information about their work. © 2018 American Medical Association. All rights reserved. Downloaded From: https://jamanetwork.com/ on 10/01/2021 2 eTable 1. Search strategy for cancer systematic review # Search 1 (cancer or neoplasm* or malignancy).ab. 2 limit 1 to abstracts 3 limit 2 to cochrane library [Limit not valid in Ovid MEDLINE(R),Ovid MEDLINE(R) Daily Update,Ovid MEDLINE(R) In-Process,Ovid MEDLINE(R) Publisher; records were retained] 4 limit 3 to english language 5 limit 4 to human 6 limit 5 to yr="2000 -Current" 7 limit 6 to humans 8 (cancer or neoplasm* or malignancy).ti. 9 limit 8 to abstracts 10 limit 9 to cochrane library [Limit not valid in Ovid MEDLINE(R),Ovid MEDLINE(R) Daily Update,Ovid MEDLINE(R) In-Process,Ovid MEDLINE(R) Publisher; records were retained] 11 limit 10 to english language 12 limit 11 to human 13 limit 12 to yr="2000 -Current" 14 limit 13 to humans 15 7 or 14 16 (volatile organic compound* or VOC* or Breath or Exhaled).ab. -
Airborne Volatile Organic Compounds at an E-Waste Site in Ghana: Source Apportionment, Exposure and Health Risks
Journal of Hazardous Materials 419 (2021) 126353 Contents lists available at ScienceDirect Journal of Hazardous Materials journal homepage: www.elsevier.com/locate/jhazmat Airborne volatile organic compounds at an e-waste site in Ghana: Source apportionment, exposure and health risks Nan Lin a,b, Lawrencia Kwarteng c, Christopher Godwin a, Sydni Warner a, Thomas Robins a, John Arko-Mensah c, Julius N. Fobil c, Stuart Batterman a,* a Department of Environmental Health Sciences, School of Public Health, University of Michigan, Ann Arbor, MI, USA 48109 b Department of Environmental Health, School of Public Health, Shanghai Jiao Tong University, Shanghai, PR China 200025 c Department of Biological, Environmental and Occupational Health Sciences, University of Ghana, School of Public Health, P.O. Box LG13, Accra, Ghana ARTICLE INFO ABSTRACT Editor: Dr. H. Zaher Informal e-waste recycling processes emit various air pollutants. While there are a number of pollutants of concern, little information exists on volatile organic compounds (VOCs) releases at e-waste sites. To assess Keywords: occupational exposures and estimate health risks, we measured VOC levels at the Agbogbloshie e-waste site in E-waste Ghana, the largest e-waste site in Africa, by collecting both fixed-siteand personal samples for analyzing a wide Volatile organic compounds range of VOCs. A total of 54 VOCs were detected, dominated by aliphatic and aromatic compounds. Mean and Source apportionment median concentrations of the total target VOCs were 46 and 37 μg/m3 at the fixedsites, and 485 and 162 μg/m3 Exposure Health risk for the personal samples. Mean and median hazard ratios were 2.1 and 1.4, respectively, and cancer risks were 4.6 × 10-4 and 1.5 × 10-4. -
Section 2. Hazards Identification OSHA/HCS Status : This Material Is Considered Hazardous by the OSHA Hazard Communication Standard (29 CFR 1910.1200)
SAFETY DATA SHEET Flammable Liquefied Gas Mixture: 2-Methylpentane / 2,2-Dimethylbutane / 2, 3-Dimethylbutane / 3-Methylpentane / Benzene / Carbon Dioxide / Decane / Dodecane / Ethane / Ethyl Benzene / Heptane / Hexane / Isobutane / Isooctane / Isopentane / M- Xylene / Methane / N-Butane / N-Pentane / Neopentane / Nitrogen / Nonane / O- Xylene / Octane / P-Xylene / Pentadecane / Propane / Tetradecane / Toluene / Tridecane / Undecane Section 1. Identification GHS product identifier : Flammable Liquefied Gas Mixture: 2-Methylpentane / 2,2-Dimethylbutane / 2, 3-Dimethylbutane / 3-Methylpentane / Benzene / Carbon Dioxide / Decane / Dodecane / Ethane / Ethyl Benzene / Heptane / Hexane / Isobutane / Isooctane / Isopentane / M- Xylene / Methane / N-Butane / N-Pentane / Neopentane / Nitrogen / Nonane / O-Xylene / Octane / P-Xylene / Pentadecane / Propane / Tetradecane / Toluene / Tridecane / Undecane Other means of : Not available. identification Product type : Liquefied gas Product use : Synthetic/Analytical chemistry. SDS # : 018818 Supplier's details : Airgas USA, LLC and its affiliates 259 North Radnor-Chester Road Suite 100 Radnor, PA 19087-5283 1-610-687-5253 24-hour telephone : 1-866-734-3438 Section 2. Hazards identification OSHA/HCS status : This material is considered hazardous by the OSHA Hazard Communication Standard (29 CFR 1910.1200). Classification of the : FLAMMABLE GASES - Category 1 substance or mixture GASES UNDER PRESSURE - Liquefied gas SKIN IRRITATION - Category 2 GERM CELL MUTAGENICITY - Category 1 CARCINOGENICITY - Category 1 TOXIC TO REPRODUCTION (Fertility) - Category 2 TOXIC TO REPRODUCTION (Unborn child) - Category 2 SPECIFIC TARGET ORGAN TOXICITY (SINGLE EXPOSURE) (Narcotic effects) - Category 3 SPECIFIC TARGET ORGAN TOXICITY (REPEATED EXPOSURE) - Category 2 AQUATIC HAZARD (ACUTE) - Category 2 AQUATIC HAZARD (LONG-TERM) - Category 1 GHS label elements Hazard pictograms : Signal word : Danger Hazard statements : Extremely flammable gas. May form explosive mixtures with air. -
N-Alkane Category: Decane, Undecane, Dodecane (CAS Nos
June 17, 2004 n-Alkane Category: decane, undecane, dodecane (CAS Nos. 124-18-5, 1120-21-4, 112-40-3) Voluntary Children’s Chemical Evaluation Program (VCCEP) Tier 1 Pilot Submission Docket Number OPPTS – 00274D American Chemistry Council n-Alkane VCCEP Consortium Sponsors: Chevron Phillips Chemical Company LP Sasol North America Inc. Shell Chemical LP June 17, 2004 TABLE OF CONTENTS Glossary of Terms 4 1. Executive Summary 5 2. Basis for Inclusion in the VCCEP Program 2.1 Total Exposure Assessment Methodology Data 10 2.2 Air Monitoring Data 11 2.3 How Sponsors Were Identified for the n-Alkane VCCEP Effort 12 3. Previous and On-Going Health Assessments 3.1 OECD SIDS/ICCA HPV Imitative 14 3.2 Total Petroleum Hydrocarbon Criteria Working Group 15 3.3 Hydrocarbon Solvent Guidance Group Values (GGVs) for Setting Occupational Exposure Limits (OELs) for Hydrocarbon Solvents 15 4. Regulatory Overview 4.1 CPSC Child-Resistant Packaging for Hydrocarbons 16 4.2 Occupational Exposure Limits 16 4.3 VOC Regulations 17 5. Product Overview 5.1 Physical, Chemical, and Environmental Fate Properties 18 5.2 Production of n-Alkanes 20 5.3 Uses for n-Alkane Products 20 5.4 Petroleum Products Which Contain n-Alkanes 21 6. Exposure Assessment 6.1 Summary 25 6.2 Non-Occupational Exposure 28 6.2.1 Indoor Sources of Exposure 6.2.2 Outdoor Source of Exposure 6.2.3 Unique Children’s Exposure 6.3 Integrated 24 hour Exposure 36 6.4 Occupational Exposure 36 6.5 Potential for Dermal and Oral Exposure 40 6.6 Selection of Exposure Scenarios and Exposure Concentrations 43 7. -
Assessment of Indoor Volatile Organic Compounds in Head Start Child Care T Facilities Danh C
Atmospheric Environment 215 (2019) 116900 Contents lists available at ScienceDirect Atmospheric Environment journal homepage: www.elsevier.com/locate/atmosenv Assessment of indoor volatile organic compounds in Head Start child care T facilities Danh C. Vua, Thi L. Hob, Phuc H. Voa, Mohamed Bayatic, Alexandra N. Davisd, Zehra Gulsevene, ⁎ Gustavo Carloe, Francisco Palermoe, Jane A. McElroyf, Susan C. Nagelg, Chung-Ho Lina, a Center for Agroforestry, School of Natural Resources, University of Missouri, Columbia, MO, USA b Center of Core Facilities, Cuu Long Delta Rice Research Institute, Viet Nam c Department of Civil and Environmental Engineering, University of Missouri, Columbia, MO, USA d Department of Individual, Family, and Community Education, University of New Mexico, NM, USA e Center for Children and Families Across Cultures, Department of Human Development and Family Science, University of Missouri, Columbia, MO, USA f Department of Family and Community Medicine, University of Missouri, Columbia, MO, USA g Department of Obstetrics, Gynecology and Women's Health, School of Medicine, University of Missouri, USA ARTICLE INFO ABSTRACT Keywords: Exposure to volatile organic compounds (VOCs) in child care environments has raised a public concern. This Head start study aimed to characterize indoor VOCs in four facilities of Head Start programs in Kansas city, Missouri, Child care investigate seasonal and spatial variations in VOC levels, and assess health risks associated with children's VOC Children exposure. In total, 49 VOCs including aromatic and aliphatic hydrocarbons, aldehydes, glycol ethers, esters and Volatile organic compounds chlorinated hydrocarbons were identified and quantified in the facilities. Significant differences were notedfor Indoor air the VOC concentrations among the facilities. -
Catalytic Dehydroaromatization of Alkanes By
CATALYTIC DEHYDROAROMATIZATION OF ALKANES BY PINCER-LIGATED IRIDIUM COMPLEXES By ANDREW MURRAY STEFFENS A dissertation submitted to the Graduate School-New Brunswick Rutgers, The State University of New Jersey In partial fulfillment of the requirements For the degree of Doctor of Philosophy Graduate Program in Chemistry and Chemical Biology Written under the direction of Alan S. Goldman And approved by _______________________________________ _______________________________________ _______________________________________ _______________________________________ New Brunswick, New Jersey January 2016 ABSTRACT OF THE DISSERTATION CATALYTIC DEHYDROAROMATIZATION OF ALKANES BY PINCER-LIGATED IRIDIUM COMPLEXES By ANDREW MURRAY STEFFENS Dissertation Director: Alan S. Goldman Further understanding of the activation of small molecules by metal complexes is an ongoing goal in organometallic chemistry, and expansion on previously reported reactions is of particular interest. This thesis will discuss expansion of transfer dehydrogenation reactions, specifically multiple transfer dehydrogenation reactions of alkanes leading to aromatic products in one pot. The synthesis of the pincer catalyst used for dehydroaromatization reactions is presented along with full characterization of each step. Optimization of dehydroaromatization reactions was performed on a variety of n-alkane starting materials to maximize yield of alkylbenzene products. Kinetics and concentrations for each starting material are presented to highlight the complexity of these reactions. Despite a mechanism that would suggest otherwise, dehydroaromatization reactions surprisingly yield benzene regardless of the starting n-alkane. This interesting appearance of benzene is discussed along with yields of benzene for various n-alkanes. ii Mechanistic studies and DFT calculations were performed to elucidate the mechanism through which benzene is formed, and these studies show that benzene forms though a retro-ene mechanism. -
Supplement of Sensitive Detection of N-Alkanes Using a Mixed Ionization Mode Proton- Transfer-Reaction Mass Spectrometer
Supplement of Atmos. Meas. Tech., 9, 5315–5329, 2016 http://www.atmos-meas-tech.net/9/5315/2016/ doi:10.5194/amt-9-5315-2016-supplement © Author(s) 2016. CC Attribution 3.0 License. Supplement of Sensitive detection of n-alkanes using a mixed ionization mode proton- transfer-reaction mass spectrometer Omar Amador-Muñoz et al. Correspondence to: Omar Amador-Muñoz ([email protected]) The copyright of individual parts of the supplement might differ from the CC-BY 3.0 licence. Example application of the calibrated fragment algorithm for quantifying n-alkanes mixtures The algorithm explained in section 2.3 was applied to calculate n-decane (m/z 142) concentration, taken as an example, in a mixture created in the laboratory containing nine n-alkanes: + 1. wcps(O2 ) for n-decane = 77256 at 541.5 ppbv. + 2. wS(O2 ) = 142.7 wcps/ppbv 3. FCD of m/z 142 on: m/z 156 (n-undecane) = 0.005, m/z 170 (n-dodecane) = 0.053 and m/z 184 (n- tridecane) = 0.059 (Table 3). 4. Over signal of m/z 142 ion: [11621 wcps * 0.005 (n-undecane)] + [17717 wcps * 0.053 (n-dodecane)] + [18887 wcps * 0.059 (n-tridecane)] = 2111 wcps. 5. Pure signal of m/z 142 ion: 10099 wcps - 2111 wcps = 7988 wcps. 7992 푤푐푝푠 6. 푛 − decane concentration = 푤푐푝푠 = 57.0 푝푝푏푣 142.7 ppbv 7. The bias with respect to the known concentration of n-decane (60.0 ppbv, Table S2) was -5.0 % as illustrated in table 4. Figures + The panels in figure S1 show the variability at low water flow (2 sccm) of the key source ions comprising H3O + + + (m/z 19), O2 (m/z 32), NO (m/z 30) and H2O.(H3O) (m/z 37) as a function of E/N. -
Control Technology Center EPA-600 12-91-061 November 1991
United States Envimnmentai Protection Agency Control Technology Center EPA-600 12-91-061 November 1991 EVALUATION OF VOC EMISSIONS FROM HEATED ROOFING ASPHALT RESEARCH REPORTING SERIES Research reports of the Office of Research and Development. U.S. Environmental Protection Agency, have been grouped into nine series. These nine broad cate- gories were established to facilitate further development and application of en- vironmental technology. Elimination of traditional grouping was consciously planned to foster technology transfer and a maximum interface in related fields. The nine series are: 1. Environmental Health Effects Research 2. Environmental Protection Technology 3. Ecological Research 4. Environmental Monitoring 5. Socioeconomic Environmental Studies 6. Scientific and Technical Assessment Reports (STAR) 7. Interagency Energy-Environment Research and Development 8. "Special" Reports 9. Miscellaneous Reports This report has been assigned to the ENVIRONMENTAL PROTECT1ON TECH- NOLOGY series. This series describes research performed to develop and dem- onstrate instrumentation, equipment, and methodology to repair or prevent en- vironmental degradation from point and non-point sources of pollution. This work provides the new or improved technology required for the control and treatment of pollution sources to meet environmental quality standards. EPA REVIEW NOTICE This report has been reviewed by the U.S. Environmental Protection Agency, and approved for publication. Approval does not signify that the contents necessarily reflect the views and policy of the Agency, nor does mention of trade names or 'commercial products constitute endorsement or recommendation for use. This document is available to the public through the National Technical Informa- tion Service. Springfield. Virginia 22161. EPA-600/2-91-061 November 1991 EVALUATION OF VOC EMISSIONS FROM HEATED ROOFING ASPHALT Prepared by: Peter Kariher, Michael Tufts, and Larry Hamel Acurex Corporation Environmental Systems Division 49 15 Prospectus Drive P.O.