Electromagnetic Damping of a Mechanical Harmonic Oscillator with the Effect of Magnetic Hysteresis
Total Page:16
File Type:pdf, Size:1020Kb
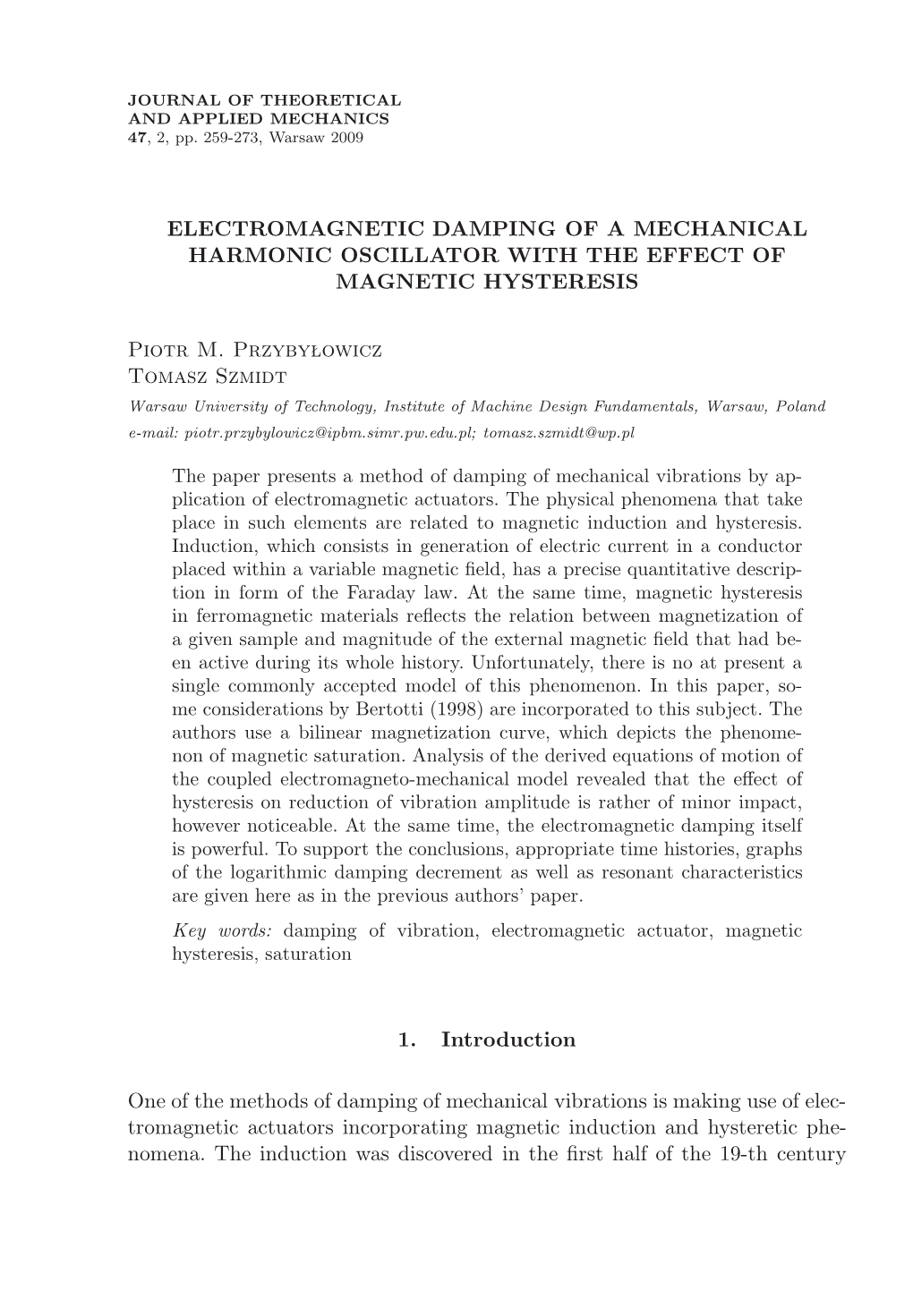
Load more
Recommended publications
-
Module 2: Hydrostatics
Module 2: Hydrostatics . Hydrostatic pressure and devices: 2 lectures . Forces on surfaces: 2.5 lectures . Buoyancy, Archimedes, stability: 1.5 lectures Mech 280: Frigaard Lectures 1-2: Hydrostatic pressure . Should be able to: . Use common pressure terminology . Derive the general form for the pressure distribution in static fluid . Calculate the pressure within a constant density fluids . Calculate forces in a hydraulic press . Analyze manometers and barometers . Calculate pressure distribution in varying density fluid . Calculate pressure in fluids in rigid body motion in non-inertial frames of reference Mech 280: Frigaard Pressure . Pressure is defined as a normal force exerted by a fluid per unit area . SI Unit of pressure is N/m2, called a pascal (Pa). Since the unit Pa is too small for many pressures encountered in engineering practice, kilopascal (1 kPa = 103 Pa) and mega-pascal (1 MPa = 106 Pa) are commonly used . Other units include bar, atm, kgf/cm2, lbf/in2=psi . 1 psi = 6.695 x 103 Pa . 1 atm = 101.325 kPa = 14.696 psi . 1 bar = 100 kPa (close to atmospheric pressure) Mech 280: Frigaard Absolute, gage, and vacuum pressures . Actual pressure at a give point is called the absolute pressure . Most pressure-measuring devices are calibrated to read zero in the atmosphere. Pressure above atmospheric is called gage pressure: Pgage=Pabs - Patm . Pressure below atmospheric pressure is called vacuum pressure: Pvac=Patm - Pabs. Mech 280: Frigaard Pressure at a Point . Pressure at any point in a fluid is the same in all directions . Pressure has a magnitude, but not a specific direction, and thus it is a scalar quantity . -
Slightly Disturbed a Mathematical Approach to Oscillations and Waves
Slightly Disturbed A Mathematical Approach to Oscillations and Waves Brooks Thomas Lafayette College Second Edition 2017 Contents 1 Simple Harmonic Motion 4 1.1 Equilibrium, Restoring Forces, and Periodic Motion . ........... 4 1.2 Simple Harmonic Oscillator . ...... 5 1.3 Initial Conditions . ....... 8 1.4 Relation to Cirular Motion . ...... 9 1.5 Simple Harmonic Oscillators in Disguise . ....... 9 1.6 StateSpace ....................................... ....... 11 1.7 Energy in the Harmonic Oscillator . ........ 12 2 Simple Harmonic Motion 16 2.1 Motivational Example: The Motion of a Simple Pendulum . .......... 16 2.2 Approximating Functions: Taylor Series . ........... 19 2.3 Taylor Series: Applications . ........ 20 2.4 TestsofConvergence............................... .......... 21 2.5 Remainders ........................................ ...... 22 2.6 TheHarmonicApproximation. ........ 23 2.7 Applications of the Harmonic Approximation . .......... 26 3 Complex Variables 29 3.1 ComplexNumbers .................................... ...... 29 3.2 TheComplexPlane .................................... ..... 31 3.3 Complex Variables and the Simple Harmonic Oscillator . ......... 32 3.4 Where Making Things Complex Makes Them Simple: AC Circuits . ......... 33 3.5 ComplexImpedances................................. ........ 35 4 Introduction to Differential Equations 37 4.1 DifferentialEquations ................................ ........ 37 4.2 SeparationofVariables............................... ......... 39 4.3 First-Order Linear Differential Equations -
Students' Conception and Application of Mechanical Equilibrium Through Their Sketches
Paper ID #17998 Students’ Conception and Application of Mechanical Equilibrium Through Their Sketches Ms. Nicole Johnson, University of Illinois, Urbana-Champaign Nicole received her B.S. in Engineering Physics at the Colorado School of Mines (CSM) in May 2013. She is currently working towards a PhD in Materials Science and Engineering at the University of Illinois at Urbana-Champaign (UIUC) under Professor Angus Rockett and Geoffrey Herman. Her research is a mixture between understanding defect behavior in solar cells and student learning in Materials Science. Outside of research she helps plan the Girls Learning About Materials (GLAM) summer camp for high school girls at UIUC. Dr. Geoffrey L. Herman, University of Illinois, Urbana-Champaign Dr. Geoffrey L. Herman is a teaching assistant professor with the Deprartment of Computer Science at the University of Illinois at Urbana-Champaign. He also has a courtesy appointment as a research assis- tant professor with the Department of Curriculum & Instruction. He earned his Ph.D. in Electrical and Computer Engineering from the University of Illinois at Urbana-Champaign as a Mavis Future Faculty Fellow and conducted postdoctoral research with Ruth Streveler in the School of Engineering Educa- tion at Purdue University. His research interests include creating systems for sustainable improvement in engineering education, conceptual change and development in engineering students, and change in fac- ulty beliefs about teaching and learning. He serves as the Publications Chair for the ASEE Educational Research and Methods Division. c American Society for Engineering Education, 2017 Students’ Conception and Application of Mechanical Equilibrium Through Their Sketches 1. Introduction and Relevant Literature Sketching is central to engineering practice, especially design[1]–[4]. -
PHYS2100: Hamiltonian Dynamics and Chaos
PHYS2100: Hamiltonian dynamics and chaos M. J. Davis September 2006 Chapter 1 Introduction Lecturer: Dr Matthew Davis. Room: 6-403 (Physics Annexe, ARC Centre of Excellence for Quantum-Atom Optics) Phone: (334) 69824 email: [email protected] Office hours: Friday 8-10am, or by appointment. Useful texts Rasband: Chaotic dynamics of nonlinear systems. Q172.5.C45 R37 1990. • Percival and Richards: Introduction to dynamics. QA614.8 P47 1982. • Baker and Gollub: Chaotic dynamics: an introduction. QA862 .P4 B35 1996. • Gleick: Chaos: making a new science. Q172.5.C45 G54 1998. • Abramowitz and Stegun, editors: Handbook of mathematical functions: with formulas, graphs, and• mathematical tables. QA47.L8 1975 The lecture notes will be complete: However you can only improve your understanding by reading more. We will begin this section of the course with a brief reminder of a few essential conncepts from the first part of the course taught by Dr Karen Dancer. 1.1 Basics A mechanical system is known as conservative if F dr = 0. (1.1) I · Frictional or dissipative systems do not satisfy Eq. (1.1). Using vector analysis it can be shown that Eq. (1.1) implies that there exists a potential function 1 such that F = V (r). (1.2) −∇ for some V (r). We will assume that conservative systems have time-independent potentials. A holonomic constraint is a constraint written in terms of an equality e.g. r = a, a> 0. (1.3) | | A non-holonomic constraint is written as an inequality e.g. r a. | | ≥ 1.2 Lagrangian mechanics For a mechanical system of N particles with k holonomic constraints, there are a total of 3N k degrees of freedom. -
On the Development of Optimization Theory
The American Mathematical Monthly pp ON THE DEVELOPMENT OF OPTIMIZATION THEORY Andras Prekopa Intro duction Farkass famous pap er of b ecame a principal reference for linear inequalities after the publication of the pap er of Kuhn and Tucker Nonlinear Programming in In that pap er Farkass fundamental theorem on linear inequalities was used to derive necessary conditions for optimality for the nonlinear programming problem The results obtained led to a rapid development of nonlinear optimization theory The work of John containing similar but weaker results for optimality published in has b een generally known but it was not until a few years ago that Karushs work of b ecame widely known although essentially the same result was obtained by Kuhn and Tucker in In this pap er we call attention to some imp ortantwork done in the last century and b efore We show that fundamental ideas ab out the necessary optimality conditions for nonlinear optimization sub ject to inequality constraints can b e found in pap ers byFourier Cournot and Farkas as well as by Gauss Ostrogradsky and Hamel To start to describ e the early development of optimization theory it is very helpful to lo ok at the rst two sentences in Farkass pap er The natural and systematic treatment of analytical mechanics has to have as its background the inequalit y principle of virtual displacements rst formulated byFourier Andras Prekopa received his PhD in at the University of Budap est under the leadership of A Renyi He was Assistant Professor and later Asso ciate Professor -
Arxiv:2104.05789V1 [Physics.Class-Ph]
Thermal Radiation Equilibrium: (Nonrelativistic) Classical Mechanics versus (Relativistic) Classical Electrodynamics Timothy H. Boyer Department of Physics, City College of the City University of New York, New York, New York 10031 Abstract Physics students continue to be taught the erroneous idea that classical physics leads inevitably to energy equipartition, and hence to the Rayleigh-Jeans law for thermal radiation equilibrium. Actually, energy equipartition is appropriate only for nonrelativistic classical mechanics, but has only limited relevance for a relativistic theory such as classical electrodynamics. In this article, we discuss harmonic-oscillator thermal equilibrium from three different perspectives. First, we contrast the thermal equilibrium of nonrelativistic mechanical oscillators (where point collisions are allowed and frequency is irrelevant) with the equilibrium of relativistic radiation modes (where frequency is crucial). The Rayleigh-Jeans law appears from applying a dipole-radiation approx- imation to impose the nonrelativistic mechanical equilibrium on the radiation spectrum. In this discussion, we note the possibility of zero-point energy for relativistic radiation, which possibility does not arise for nonrelativistic classical-mechanical systems. Second, we turn to a simple electro- magnetic model of a harmonic oscillator and show that the oscillator is fully in radiation equilibrium (which involves all radiation multipoles, dipole, quadrupole, etc.) with classical electromagnetic zero-point radiation, but is not in equilibrium with the Rayleigh-Jeans spectrum. Finally, we discuss the contrast between the flexibility of nonrelativistic mechanics with its arbitrary poten- tial functions allowing separate scalings for length, time, and energy, with the sharply-controlled behavior of relativistic classical electrodynamics with its single scaling connecting together the arXiv:2104.05789v1 [physics.class-ph] 12 Apr 2021 scales for length, time, and energy. -
Hydrodynamic Description of the Adiabatic Piston
Hydrodynamic description of the adiabatic piston M. Malek Mansoura, Alejandro L. Garciab and F. Barasc (a) Universite Libre de Bruxelles - 1050 Brussels, Belgium (b) San Jose State University, Dept. Physics, San Jose CA, USA (c) Universit´e de Bourgogne, LRRS, F - 21078 Dijon Cedex, France (Dated: November 19, 2005) A closed macroscopic equation for the motion of the two-dimensional adiabatic piston is derived from standard hydrodynamics. It predicts a damped oscillatory motion of the piston towards a final rest position, which depends on the initial state. In the limit of large piston mass, the solution of this equation is in quantitative agreement with the results obtained from both hard disk molecular dynamics and hydrodynamics. The explicit form of the basic characteristics of the piston’s dynamics, such as the period of oscillations and the relaxation time, are derived. The limitations of the theory’s validity, in terms of the main system parameters, are established. PACS numbers: 05.70.Ln, 05.40.-a I. INTRODUCTION Consider an isolated cylinder with two compartments, separated by a piston. The piston is free to move without friction along the axis of the cylinder and it has a zero heat conductivity, hence its designation as the adiabatic piston. This construction, first introduced by Callen [1], became widely known after Feynman discussed it in his famous lecture series [2]. Since then it has attracted considerable attention [3–5]. For a sufficiently large piston mass, the following scenario describes the evolution of the system [6, 7]. Starting from a nonequilibrium configuration (i.e., different pressures in each compartment) the piston performs a damped oscillatory motion. -
Laboratory Manual Physics 166, 167, 168, 169
Laboratory Manual Physics 166, 167, 168, 169 Lab manual, part 1 For PHY 166 and 168 students Department of Physics and Astronomy HERBERT LEHMAN COLLEGE Spring 2018 TABLE OF CONTENTS Writing a laboratory report ............................................................................................................................... 1 Introduction: Measurement and uncertainty ................................................................................................. 3 Introduction: Units and conversions ............................................................................................................ 11 Experiment 1: Density .................................................................................................................................... 12 Experiment 2: Acceleration of a Freely Falling Object .............................................................................. 17 Experiment 3: Static Equilibrium .................................................................................................................. 22 Experiment 4: Newton’s Second Law .......................................................................................................... 27 Experiment 5: Conservation Laws in Collisions ......................................................................................... 33 Experiment 6: The Ballistic Pendulum ......................................................................................................... 41 Experiment 7: Rotational Equilibrium ........................................................................................................ -
Classical Mechanics January 2012
1 2 3 4 5 6 7 8 9 10 11 12 13 14 15 16 17 18 19 20 21 22 23 THE CITY UNIVERSITY OF NEW YORK First Examination for PhD Candidates in Physics Analytical Dynamics Summer 2010 Do two of the following three problems. Start each problem on a new page. Indicate clearly which two problems you choose to solve. If you do not indicate which problems you wish to be graded, only the first two problems will be graded. Put your identification number on each page. 1. A particle moves without friction on the axially symmetric surface given by 1 z = br2, x = r cos φ, y = r sin φ 2 where b > 0 is constant and z is the vertical direction. The particle is subject to a homogeneous gravitational force in z-direction given by −mg where g is the gravitational acceleration. (a) (2 points) Write down the Lagrangian for the system in terms of the generalized coordinates r and φ. (b) (3 points) Write down the equations of motion. (c) (5 points) Find the Hamiltonian of the system. (d) (5 points) Assume that the particle is moving in a circular orbit at height z = a. Obtain its energy and angular momentum in terms of a, b, g. (e) (10 points) The particle in the horizontal orbit is poked downwards slightly. Obtain the frequency of oscillation about the unperturbed orbit for a very small oscillation amplitude. 2. Use relativistic dynamics to solve the following problem: A particle of rest mass m and initial velocity v0 along the x-axis is subject after t = 0 to a constant force F acting in the y-direction. -
Classical Mechanics 220
Classical Mechanics 220 Eric D'Hoker Department of Physics and Astronomy, UCLA Los Angeles, CA 90095, USA 9 November 2015 1 Contents 1 Review of Newtonian Mechanics 5 1.1 Some History . .5 1.2 Newton's laws . .6 1.3 Comments on Newton's laws . .7 1.4 Work . .8 1.5 Dissipative forces . .9 1.6 Conservative forces . 10 1.7 Velocity dependent conservative forces . 12 1.8 Charged particle in the presence of electro-magnetic fields . 14 1.9 Physical relevance of conservative forces . 15 1.10 Appendix 1: Solving the zero-curl equation . 15 2 Lagrangian Formulation of Mechanics 17 2.1 The Euler-Lagrange equations in general coordinates . 17 2.2 The action principle . 20 2.3 Variational calculus . 21 2.4 Euler-Lagrange equations from the action principle . 23 2.5 Equivalent Lagrangians . 24 2.6 Symmetry transformations and conservation laws . 24 2.7 General symmetry transformations . 26 2.8 Noether's Theorem . 28 2.9 Examples of symmetries and conserved charges . 29 2.10 Systems with constraints . 31 2.11 Holonomic versus non-holonomic constrains . 33 2.12 Lagrangian formulation for holonomic constraints . 36 2.13 Lagrangian formulation for some non-holonomic constraints . 38 2.14 Examples . 38 3 Quadratic Systems: Small Oscillations 41 3.1 Equilibrium points . 41 3.2 Mechanical stability of equilibrium points . 42 3.3 Small oscillations near a general solution . 44 3.4 Magnetic stabilization . 45 3.5 Lagrange Points . 46 3.6 Stability near the non-colinear Lagrange points . 49 2 4 Hamiltonian Formulation of Mechanics 51 4.1 Canonical position and momentum variables . -
Thermodynamic Explanation of Landau Damping by Reduction to Hydrodynamics
entropy Article Thermodynamic Explanation of Landau Damping by Reduction to Hydrodynamics Michal Pavelka 1,* ID , Václav Klika 2 ID and Miroslav Grmela 3 1 Mathematical Institute, Faculty of Mathematics and Physics, Charles University, Sokolovská 83, 186 75 Prague, Czech Republic 2 Department of Mathematics, FNSPE, Czech Technical University in Prague, Trojanova 13, 120 00 Prague, Czech Republic; vaclav.klika@fjfi.cvut.cz 3 École Polytechnique de Montréal, C.P.6079 suc. Centre-ville, Montréal, QC H3C 3A7, Canada; [email protected] * Correspondence: [email protected]; Tel.: +420-22191-3248 Received: 11 April 2018; Accepted: 8 June 2018; Published: 12 June 2018 Abstract: Landau damping is the tendency of solutions to the Vlasov equation towards spatially homogeneous distribution functions. The distribution functions, however, approach the spatially homogeneous manifold only weakly, and Boltzmann entropy is not changed by the Vlasov equation. On the other hand, density and kinetic energy density, which are integrals of the distribution function, approach spatially homogeneous states strongly, which is accompanied by growth of the hydrodynamic entropy. Such a behavior can be seen when the Vlasov equation is reduced to the evolution equations for density and kinetic energy density by means of the Ehrenfest reduction. Keywords: Landau damping; entropy; non-equilibrium thermodynamics; Ehrenfest reduction 1. Introduction Dynamics of self-interacting gas is well described by the Vlasov equation, ¶ f (t, r, p) p ¶ f (t, r, p) ¶ f = − · − F( f (t, r, p)) · , (1) ¶t m ¶r ¶p where m is the mass of one particle and f (t, r, p) is the one-particle distribution function on phase space and F is the force exerted on the gas from outside or by the gas itself. -
Deterministic Motion of the Controversial Piston in The
Deterministic motion of the controversial piston in the thermodynamic limit Christian Gruber and S´everine Pache Institut de Physique Th´eorique, Ecole Polytechnique F´ed´erale de Lausanne, CH-1015 Lausanne, Switzerland Annick Lesne Laboratoire de Physique Th´eorique des Liquides, Universit´ePierre et Marie Curie, Case courrier 121, 4 Place Jussieu, 75252 Paris Cedex 05, France (November 1, 2018) We consider the evolution of a system composed of N non-interacting point particles of mass m in a cylindrical container divided into two regions by a movable adiabatic wall (the adiabatic piston). We study the thermodynamic limit for the piston where the area A of the cross-section, the mass M of the piston, and the number N of particles go to infinity keeping A/M and N/M fixed. The length of the container is a fixed parameter which can be either finite or infinite. In this thermodynamic limit we show that the motion of the piston is deterministic and the evolution is adiabatic. Moreover if the length of the container is infinite, we show that the piston evolves toward a stationary state with velocity approximately proportional to the pressure difference. If the length of the container is finite, introducing a simplifying assumption we show that the system evolves with either weak or strong damping toward a well-defined state of mechanical equilibrium where the pressures are the same, but the temperatures different. Numerical simulations are presented to illustrate possible evolutions and to check the validity of the assumption. Key Words: Liouville equation, adiabatic, piston, equilibrium, damping. 1.