DIY Belt Sharpening System
Total Page:16
File Type:pdf, Size:1020Kb
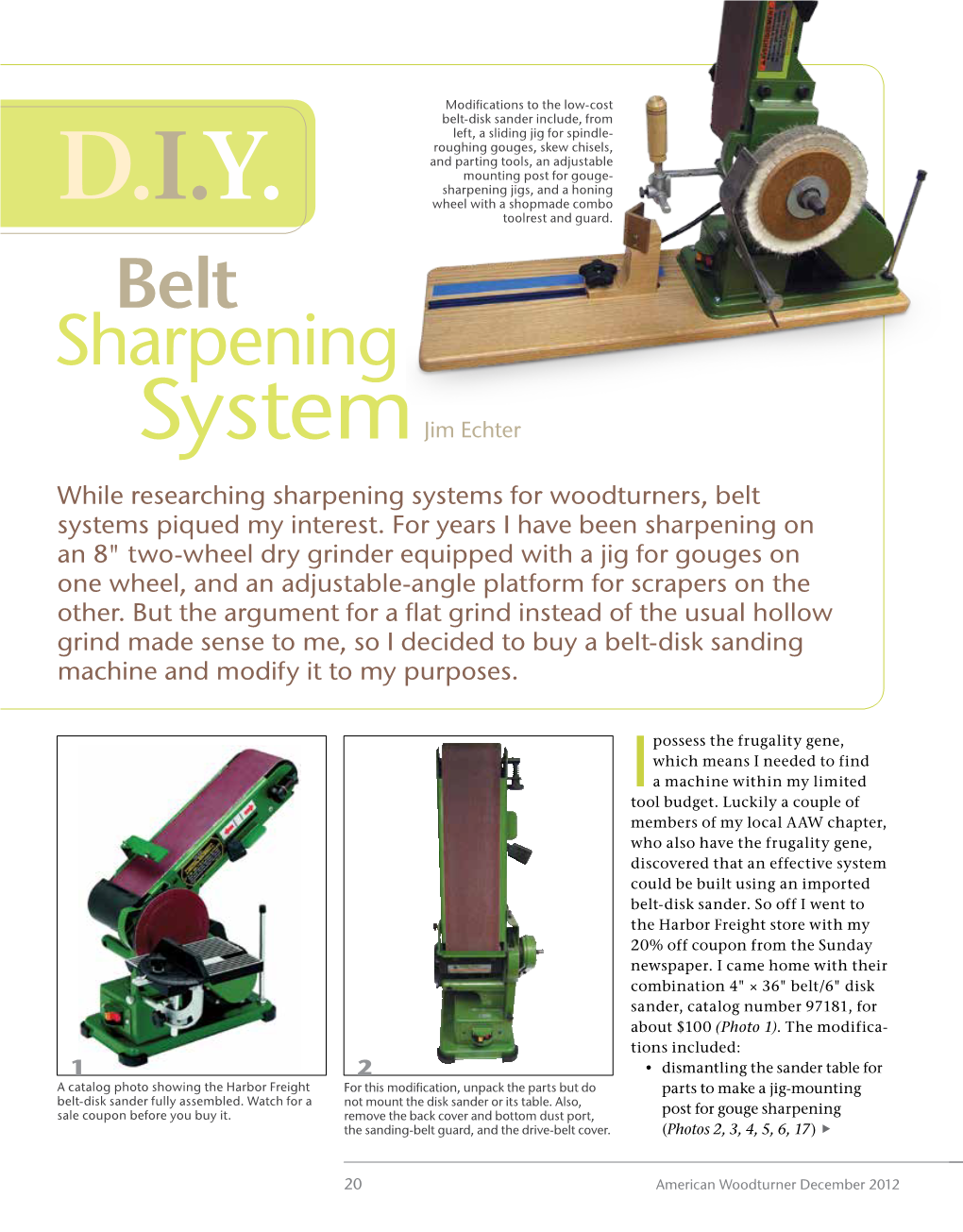
Load more
Recommended publications
-
THREE WHEEL BANDSAW/DISC SANDER Model: SM1214
INSTRUCTIONS FOR: THREE WHEEL BANDSAW/DISC SANDER Model: SM1214 Thank you for purchasing a Sealey product. Manufactured to a high standard this product will, if used according to these instructions and properly maintained, give you years of trouble free performance. IMPORTANT: PLEASE READ THESE INSTRUCTIONS CAREFULLY. NOTE THE SAFE OPERATIONAL REQUIREMENTS, WARNINGS AND CAUTIONS. USE THIS PRODUCT CORRECTLY AND WITH CARE FOR THE PURPOSE FOR WHICH IT IS INTENDED. FAILURE TO DO SO MAY CAUSE DAMAGE AND/OR PERSONAL INJURY AND WILL INVALIDATE THE WARRANTY. PLEASE KEEP INSTRUCTIONS SAFE FOR FUTURE USE. 1. SAFETY INSTRUCTIONS 1.1. ELECTRICAL SAFETY. p WARNING! It is the users responsibility to read, understand and comply with the following: You must check all electrical equipment and appliances to ensure they are safe before using. You must inspect power supply leads, plugs and all electrical connections for wear and damage. You must ensure the risk of electric shock is minimised by the installation of appropriate safety devices. An RCCB (Residual Current Circuit Breaker) should be incorporated in the main distribution board. We also recommend that an RCD (Residual Current Device) is used with all electrical products. It is particularly important to use an RCD with portable products that are plugged into an electrical supply not protected by an RCCB. If in doubt consult a qualified electrician. You may obtain a Residual Current Device by contacting your Sealey dealer. You must also read and understand the following instructions concerning electrical safety. 1.1.1. The Electricity At Work Act 1989 requires all portable electrical appliances, if used on business premises, to be tested by a qualified electrician, using a Portable Appliance Tester (PAT), at least once a year. -
Finishing Sander
Finishing Sander I. Competencies Given a properly adjusted finishing sander, accessories, instruction and demonstration of use, each student will be able to: A. Identify the major parts of the finishing sander. B. Pass a written test on safety and operating procedures of the finishing sander with 100 percent accuracy. C. Demonstrate ability to use the finishing sander, following suggested safety rules and correct operation procedures. II. Instructional Materials and Procedures A. Identification of basic finishing sander parts. 1. Brush Holder 6. Paper Clamp 2. Switch Lock 7. Pad 3. Trigger Switch 8. Paper Clamp 4. Handle 9. Aluminum Housing 5. Cord Strain Reliever 10. Front Hand Knob B. Finishing Sander Safety 1. Wear safety glasses at all times when using the finishing sander. 2. Wear a dust mask or respirator to prevent breathing the fine saw dust particles that are generated by the finishing sander. 3. Keep the electrical and extension cords away from the work area. 4. Wear hearing protectors when using finishing sanders that are noisy. 5. Secure or clamp the stock before starting the sanding operation. 6. Watch out for slick walking suffices when using the finishing sander. Fine dust particles will settle on the floor making it slick. 7. Visually inspect the sander to make sure the electrical cord is not frayed or pulled out of the sander housing. If either condition exists repair the sander before using. 8. If the sander sparks excessively when being used check the brushes. Reseat or replace the brushes as necessary to reduce sparking. 9. Do not over-extend and get off balance when using the finishing sander. -
The Original. Versatile and Powerful
iNTEriOr CONSTruCTiON The Original. Versatile and powerful. FEiN MultiMastEr – the universal system for interior construction and renovation NEW! Now available in a cordless version From the inventor of the power tool: FEIN MultiMaster. More than 40 year’s experience is built into this system. Original FEiN accessories – developed for the MultiMastEr. FEIN brought the first oscillating power tool to the market Original FEIN accessories guarantee outstanding results and an over 40 years ago. These decades of experience are built into unrivalled long service life. It handles all common renovation and the FEIN MultiMaster, making this universal system for interior interior construction work for professionals and also provides construction and renovation unique in its diversity of applications unique application solutions. Maximum performance, safety and and performance. In addition, the MultiMaster impresses with high reliability are guaranteed with the FEIN MultiMaster. quality components and is an indispensible companion for trade and industrial professionals. Technology / Quality The Original Page 4 The MultiMaster Page 6 The MultiMaster Cordless Page 7 Accessories know-how Page 10 2 FEiN MultiMastEr Cordless – mobile and powerful. Your benefits with FEiN oscillating power tools: The new battery version makes the FEIN MultiMaster more flexible and convenient than ever. Cordless, but with identical performance, ɰ More than 40 year’s experience with oscillation technology. so work can be done anywhere, even without a power supply. And ɰ The high “Made in Germany” quality you expect. all this in the durable quality that you expect from a real Original. ɰ Unrivalled performance and versatility. ɰ Original FEIN accessories for perfect results and maximum tool life. -
Router Table
Router Table Read This Important Safety Notice To prevent accidents, keep safety in mind while you work. Use the safety guards installed on power equipment; they are for your protection. When working on power equipment, keep fingers away from saw blades, wear safety goggles to prevent injuries from flying wood chips and sawdust, wear hearing protection and consider installing a dust vacuum to reduce the amount of air- borne sawdust in your woodshop. Don’t wear loose clothing, such as neckties or shirts with loose sleeves, or jewelry, such as rings, necklaces or bracelets, when working on power equipment. Tie back long hair to prevent it from getting caught in your equipment. People who are sensitive to certain chemicals should check the chemical con- tent of any product before using it. Due to the variability of local conditions, construction materials, skill levels, etc., neither the author nor Popular Woodworking Books assumes any responsibility for any accidents, injuries, damages or other losses incurred resulting from the mate- rial presented in this book. The authors and editors who compiled this book have tried to make the con- tents as accurate and correct as possible. Plans, illustrations, photographs and text have been carefully checked. All instructions, plans and projects should be carefully read, studied and understood before beginning construction. Prices listed for supplies and equipment were current at the time of publica- tion and are subject to change. Metric Conversion Chart to convert to multiply by Inches. Centimeters. 2.54 Centimeters. Inches . 0.4 Feet. Centimeters. 30.5 Centimeters. Feet. 0.03 Yards. -
09-2Nd AWS Section 05
Architectural Woodwork Standards finishing 5s e c t i o n section 5 Finishing table of contents Introductory InformatIon complIance requIrements Introduction ......................................................................................... 110 General Purpose ............................................................................................... 110 Basic Considerations .................................................................... 117 Factory / Field Finishing ...................................................................... 110 Grade ..................................................................................... 117 Important Considerations .................................................................... 110 Classifications ................................................................. 117 Specifications ............................................................................... 110 Compliance Requirements .................................................... 117 Varying Costs ............................................................................... 110 Contract Documents .............................................................. 117 Intermixing Systems ..................................................................... 110 Aesthetic Compliance ............................................................ 117 Application .................................................................................... 110 Listing ................................................................................... -
10-2Nd AWS Section 06
Architectural Woodwork Standards millwork 6s e c t i o n section 6 Millwork table of contents Introductory InformatIon Ornamental Woodwork .......................................................................142 Typical Sources ..............................................................................142 Guide Specifications ...........................................................................131 Fire Retardant Solid Lumber ..........................................................143 Introduction .........................................................................................132 Sources for Wood Ornamentation ..................................................143 Methods of Production ........................................................................132 Working with an Artisan ..................................................................143 Flat Surfaces ................................................................................132 Design Ideas .......................................................................................144 Molded Surfaces ..........................................................................132 Specify Requirements For ..................................................................144 Smoothness of Flat and Molded Surfaces ..........................................132 Recommendations ..............................................................................144 Design and Use of Resources ............................................................132 Examples -
STYLE GUIDE – SANDER and SAW
STYLE GUIDE – SANDER and SAW This document is intended as a guidance to create effective, accurate product listings to improve your business potential. Amazon product detail page shows information about the product - including title, bullet points, product description and images. This information is crucial to ensure customers find and purchase your products. Providing a consistent format for your listings will better inform customers and enhance product discovery. In addition to using this document, we encourage you take advantage of the information available in our ‘Help pages’. 1. Title Guidelines: Product title is the first thing customers see when searching for a product. It is vital to have crisp and informative title for customers to find your products when they visit Amazon.in or search online. Recommended title format to use while listing Tent and related products: For the Parent and Standalone or Child of Variation Products for SANDER and SAW [Brand Name] + [Power Source Type] + [Name of the Product] + With + [Included Components] Examples for SANDER: 1. Bosch Corded Random Orbit Sander with Dust Collector and Carry Bag 2. Makita Corded Belt Sander with Abrasive Belt, 80G Belt and Dust Bag 3. RYOBI Cordless Sheet Sander with Batteries, Charger, Dust Collector and Bag Examples for SAW: 1. RYOBI Cordless Circular Saw with Lithium Ion Battery 2. DEWALT Cord Reciprocating Saw (Tool-Only) 3. DEWALT Cordless Band Saw Kit with (2) Batteries 5Ah, Charger and Case Sample values for [Name of the Product] under SANDERS and SAW: Belt Sanders; Combination disc & Belt Sanders; Detail Sanders; Disc Sanders; Sheet SANDER Sanders; Random Orbit Sanders; Drum Sanders etc, Saws; Band Saws; Circular Saws; Jig Saws; Metal cutting saws; Miter saws; Plunge Saws; SAW Reciprocating saws; Table Saws; Tile & Masonry saws etc, What to Do What Not to Do Capitalize the first letter of each word. -
MA F Schoo FACE Ol Sho E Op Inj Jury R Repor Rt
MA FACE School Shop Injury Report High School Student Sustains a Partial Fingertip Amputation While Using a Jointer in Wood Shop - Massachusetts Release Date: December 21, 2015 Massachusetts Department of Public Health Investigation: # 14-MA-1NF-01 Occupational Health Surveillance Program SUMMARY In 2014, a 9th grade student enrolled in a regional compreehensive high school that also offered some shop classes partially amputated a fingertip. The student wwas operating a wood jointer in shop class when the student’s left hand middle finger came in contact with the jointer’s cutting head. Immediately after the incident occurred, the student informed the substtitute teacher in charge about the injury. The student was brought to the school nurse who placed a call for emergency medical services (EMS). The local police and EMS arrived at the incident location within minutes. The victim was transported to a local hospital where the partially amputated fingertip was reattached and the victim was then released from the hospital. Contributing factors identified in this investigation included lack of comprehensive standard operating procedures, not having access to the jointer operator’s manual, and inexperience. Another contributing factor was the limitations of the jointer’s guard. The Massachusetts Department of Public Health concluded that to prevent similaar occurrences in the future, schools with shop classes should: • Develop, implement, and enforce standard operating procedures for operating machinery; • Develop guidelines to ensure students have a clear understandinng of the task they will be performing; and • Provide shop environments that, at a minimum, meet all relevant Occupational Safety and Health Administration (OSHA) regulations to protect students and school employees from injury. -
Power Tools Dependable Tools • Reliable Brand • Affordable Price
Power Tool Catalog The Right Tool for the Right Project Power Tools Dependable Tools • Reliable Brand • Affordable Price Introducing Alltrade Trades Pro® power tools, a complete assortment of the most popular power tools with competitive features at affordable price points. Perfect for the basic maintenance projects value-conscious homeowners need to tackle from time-to-time. With an extensive range of cordless portable power tools, electric portable power tools and bench top tools, Alltrade Trades Pro® caters to every customer’s category requirements. The tools offer outstanding features, dependable quality and are backed by a solid warranty to ensure end-user satisfaction. Our high-impact packaging is attractive, informative and communicates brand reliability and value to the consumer. We are committed to delivering the very best value for the price. Alltrade Trades Pro® has what you need for sales success! 2 Cordless Power Tools 836777 836774 4.8 Volt 3-Position Cordless Screwdriver 14.4 Volt Cordless Drill/Driver • Handle locks in 3 positions • 3/8” keyless chuck, 16 position clutch • Built-in worklight, auto spindle lock • Variable speed trigger, electric brake • Includes 4 pc. 2” power bits • Includes battery and 5-8 hour charger UPC: 028907-340135 Case Qty: 10 Shelf Qty: 10 UPC: 028907-340104 Case Qty: 8 Shelf Qty: 8 836710 836840 18 Volt Cordless Drill/Driver 18 Volt Cordless Drill/Driver & Worklight • 3/8” keyless chuck, 16 position clutch • 3/8” keyless chuck, 16 position clutch • Variable speed trigger, electric brake • Variable speed trigger, electric brake • Includes battery and 5-8 hour charger • Includes worklight, battery and 5-8 hour charger UPC: 028907-338439 Case Qty: 8 Shelf Qty: 8 UPC: 28907-344065 Case Qty: 6 Shelf Qty: 6 836785 24 Volt Cordless Drill/Driver Kit • 3/8” keyless chuck, 25 position clutch • Variable speed trigger, electric brake • Includes battery, 5-8 hour charger, 13 pc. -
Construction Technologies
Construction Technologies Technology Education Safety Procedures and Recommendations For all Woodworking Classes Safety Pledge: Read and discuss rules, have students and their parents sign the safety pledge. Students will return the pledge signed by parent we will then keep the pledge on file while the student is enrolled in Technology Education classes. General Safety: Discuss general safety rules applicable to any shop or lab. Hand Tool Safety: Discuss and demonstrate proper use of common hand tools used in the lab or shop. Machine Tool Safety: Students will learn the key features, adjustments, purpose and the safety concerns of the machines utilized in the course they are enrolled in. The machines and power tools are included but not limited to these: Tablesaw Radial Arm Saw Widebelt Sander Jointer Miter Saw Overhead Router Bandsaw Belt/Disc/Spindle Sander Drill Press Router Table Panel Saw Panel Router Hand Router Corded/Cordless drills Orbit Sander Portable Belt Sander Circular Saw Saber Saw Plate Joiner Wood Lathe Planer Pocket Hole Cutter Students will be evaluated by tests and quizzes, performance evaluations, and observation by the instructor. Construction Technologies 2 6/2003 Unsafe behavior is the number one cause of accidents and injuries on the job and in woodworking workshops. Get into the habit of working safely. You'll benefit yourself and your co-workers. Develop a Safe Attitude Work quietly and give your full attention to the task at hand. Never indulge in horseplay or other foolish behavior. Keep Yourself and the Work Area Neat and Clean Fewer accidents occur in shops that are well maintained. -
Cautron: Model No. 572.24700 Sears/Craftsman
CAUTRON: Read SAFETY RULES and INSTRUCTIONS carefully SEARS/CRAFTSMAN MODEL NO. 15 iNCH MOTORIZED SCROLL SAW/SANDER 572.24700 assembly o operating o repair parts Searsl Roebuck and Co., Chicago, Ill. 60607 U.S.A. ,,,ado,nU_SoA. ,1/1/72 and Simpsons-Sears Limited, Toronto Par! No. 405015 L FOR SAFE OPERATIO 1. Know your Power Tool. Read the owner's manual 9o Use right tool. Don't force tool or attachment carefully_ Learn its application and limitations as to do a job it was not designed for,, well as the specific potential hazards peculiar to this tool. 10. Wear proper apparel. No loose clothing or jewelry to get caught in moving parts. 2. If tool is equipped with three-prong plug, it 1t. Use safety glasses. Also use face or dust mask should be plugged into a PROPERLY GROUNDED if cutting operation is dusty° receptacle° 12. Secure work. Use clamps or a vise to hold work 3. Keep guards in place and in working order_ when practical, it's safer than using your hand, frees both hands to operate tool. 4. Remove adjusting keys and wrenches. Form habit of checking to see that keys and adjusting 13. Don't overreach. Keep your proper footing and wrenches are removed from tool before turning on balance at all times, tool. 14. Maintain tools in top condition. Keep tools 5. Keep work area clean. Cluttered areas and sharp and clean for best and safest performance° benches invite accidents. Follow instructions for lubricating and changing accessories. 6. Avoid dangerous environment. Don't use power 15. -
The 1960S Cummins Portable Power Tool Catalog This Is a Brief Intro To
The 1960s Cummins Portable Power Tool Catalog This is a brief intro to the pdf version of a 1960s Cummins Catalog, the most heavily used file on my website. Images and descriptions of sleek, art-deco-styled chrome-clad portable electric saw, drills, saber saws, orbital sanders, and accessories, all made to last. I only wish that I had more manufacturer's catalogs of this vintage, because I would quickly upload them to my servers so that people worldwide would have access to material that, otherwise, is unavailable. Please Send Me Your Vintage Portable Power Tool Catalogs/Manuals If you have vintage portable power tool catalogs and/or manuals, you can help in this service by getting in touch – [email protected] – and arrange with me for the creation of a pdf. Below is an image of my 1950s 1/2-inch portable drill, sold by the – now-defunct – national mail order firm, Montgomery-Ward, but – as you can see on pages 8 and 9 of the Cummins catalog – identical to the the Cummins portable drill. At the time, both Sears Roebuck and Montgomery Ward sold products bearing their respective labels, but products made for them by a large array of manufacturers. Cummins was the M-W manufacturer of this drill. With pleasure I use this drill in my shop frequently. A powerful hand-operated power tool – operating at about 550 rpms – with a two-step metal drill bit, you can drill accurate holes in almost any metal, which means that – with cheap recycled aluminum – you can make all sorts of jigs for your shop or even fabricate outdoor furniture and other accessories.