Project Guidelines
Total Page:16
File Type:pdf, Size:1020Kb
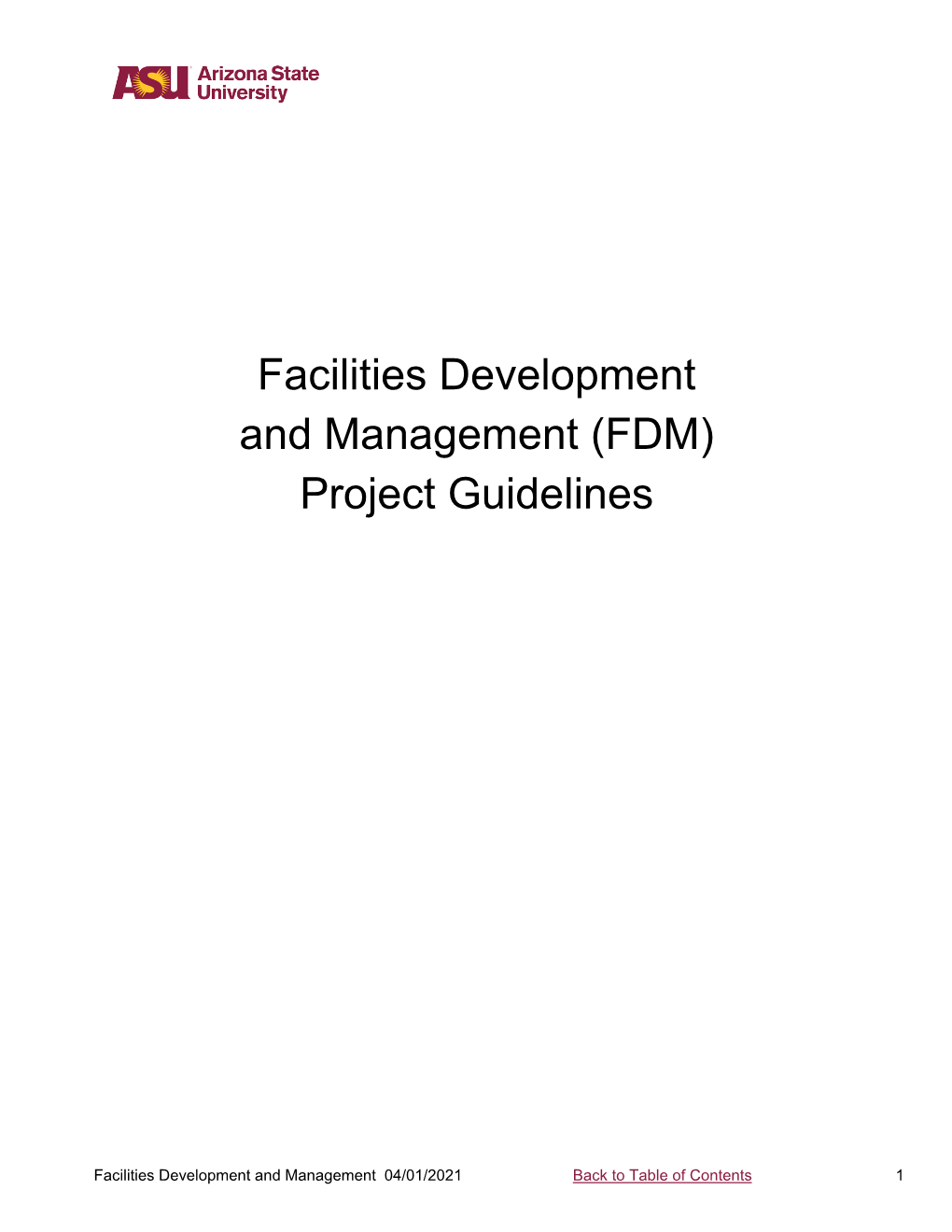
Load more
Recommended publications
-
INTERNET and AUTISM: the Reflection of Communication Experiences in Narrative Practices
CORE Metadata, citation and similar papers at core.ac.uk Provided by Göteborgs universitets publikationer - e-publicering och e-arkiv DEPARTMENT OF EDUCATION AND SPECIAL EDUCATION INTERNET AND AUTISM: The reflection of communication experiences in narrative practices Ekaterina Boytsova Master in Education: 30 hp Program: International Master in Educational Research Level: Advanced level Term: Spring term 2015 Superviser: Eva Hjörne Examiner: Ernst Thoutenhoofd Report number: VT15 IPS PDA184:6 Acknowledgements I would like to express my gratitude to all the respondents who devoted their time to take part in this study. I would also like to thank my supervisor Eva Hjörne at the Department of Education and Special Education at the University of Gothenburg for her inspiring approach and valuable comments. Gothenburg, May 19, 2015. Abstract. Background: Perspectives of Internet use among students with ASD are not a clearly investigated field although positive results in mainstream schools are already received. Multiple pieces of research have shown that computer technology facilitates a broader range of educational activities to meet a variety of needs for students with mild learning disorders, and adaptive technology can enable students with severe disabilities to become active learners in the classroom alongside their peers who do not have disabilities. The aim of this study is to understand and describe representation and perception of online communication by persons with ASD via their postings in blogs and online survey. The role of Internet, the importance of ICT in education and the relation between online and offline communication are in the focus of the study. Although the use of technologies in education and everyday routines is not wide-spread due to high costs and teachers’ lack of training in applying modern technologies in the classroom, the results of this study reveal the importance of applying ICT in everyday life for people with autism. -
Fil-B /Advisory Committee Co
Reading Comprehension Strategies In Children With High- Functioning Autism: A Social Constructivist Perspective Item Type Thesis Authors Cotter, June Ann Download date 26/09/2021 17:04:41 Link to Item http://hdl.handle.net/11122/9075 READING COMPREHENSION STRATEGIES IN CHILDREN WITH HIGH FUNCTIONING AUTISM: A SOCIAL CONSTRUCTIVIST PERSPECTIVE By June Ann Cotter RECOMMENDED: £> P \ - I V v^jQ JL-V% lh -i> Advisory Committee Chair a . fil-b /Advisory Committee Co Chair, Department of Communication APPROVED: Dean, College of Liberal Arts / r Dean of the Graduate School Date READING COMPREHENSION STRATEGIES IN CHILDREN WITH HIGH- FUNCTIONING AUTISM: A SOCIAL CONSTRUCTIVIST PERSPECTIVE A DISSERTATION Presented to the Faculty of the University of Alaska Fairbanks in Partial Fulfillment of the Requirements for the Degree of DOCTOR OF PHILOSOPHY By June Ann Cotter, MSEd. Fairbanks, Alaska May 2011 © 2011 June Ann Cotter UMI Number: 3463936 All rights reserved INFORMATION TO ALL USERS The quality of this reproduction is dependent upon the quality of the copy submitted. In the unlikely event that the author did not send a complete manuscript and there are missing pages, these will be noted. Also, if material had to be removed, a note will indicate the deletion. UMT Dissertation Publishing UMI 3463936 Copyright 2011 by ProQuest LLC. All rights reserved. This edition of the work is protected against unauthorized copying under Title 17, United States Code. uestA ® ProQuest LLC 789 East Eisenhower Parkway P.O. Box 1346 Ann Arbor, Ml 48106-1346 Abstract Individuals with autism see the world, by definition of the diagnosis, in a very different way than the typical student. -
Communication Shutdown’ Launched to Engage Social Media Users to Shut Their Networks for a Day on Nov 1 2010, in Support of a Good Cause
4.5 Billion Social Media Users worldwide & over 33 million social media users in India to support the cause of Autism ‘Communication Shutdown’ launched to engage social media users to shut their networks for a day on Nov 1 2010, in support of a good cause New Delhi, October 4, 2010‐ One day without Social Networking‐ Can you brave it? On Nov 1, 2010, citizens around the world will become part of, ‘Communication Shutdown’, a global initiative extended across 40 countries to create awareness and raise funds for charity for Autism. Through this initiative, people around the world have been challenged to go without Facebook or Twitter, for one day. Social communication is one of the biggest challenges for people with autism. By choosing to shutdown their social networks for one day, users will have some idea of what it’s like for people with autism who face this challenge every day. The Communication Shutdown campaign encourages Facebook and Twitter users to make a donation and receive a charity app or (CHAPP) that will signal their support and intention to boycott their social networking accounts on 1 November. ComScore, Inc. (NASDAQ: SCOR), has released a August 2010 report on traffic to Social Networking sites in India, revealing that India has over 33 million social network users and globally more than two thirds of the world’s population stay connected through networks like Facebook and Twitter. As people become more reliant on these channels to communicate worldwide, the Communication Shutdown fundraising campaign will also serve as a social experiment on social media habits. -
In Childhood
In childhood About Autism 1 Developed by Parent to Parent NZ Inc for its Care Matters services. www.parent2parent.org.nz • www.carematters.org.nz © Parent to Parent NZ July 2021 This publication is reviewed annually. Kia ora If you are reading this, it is likely a child in your care has just received a diagnosis of autism spectrum disorder (ASD), commonly known as autism. We’ve compiled this booklet with input from autistic people, parents and professionals to provide you with information about autism and how it can affect children’s experience of the world around them. It has been designed as a practical tool to educate and empower you and your family. This document is a general overview current at the time of writing. This information has been provided for education/information purposes only. It is not intended or implied to be a substitute for advice, diagnosis or treatment from registered health professionals. Every care has been taken to ensure its accuracy. If you have any questions or would like further information please contact Parent to Parent on 0508 236 236 or email [email protected] In this booklet we use identity first language. Identity first language is preferred by the autistic community as it celebrates the unique strengths and identity that being autistic offers an individual. Not all autistic people choose to be referred to in the same way. If you are unsure, ask the individual what they would prefer. Contents 6 What is autism? 8 What does autism look like? 10 The senses and autism 12 Strengths and abilities in autism 16 Common difficulties 17 Causes and prevalence 18 Diagnosis 19 Disclosing the diagnosis 22 So we have a diagnosis, where to from here? 24 Therapies and supports 26 Positive behaviour support and techniques 29 Communication supports 30 Alternative and augmentative communication tools 31 Visual supports 34 Autistic behaviour 36 Strategies at home What is autism? Autism affects communication and social interaction as well as thinking and behaviour. -
Morgen Kann Warten
Monika Scheele Knight | Morgen kann warten MORGEN KANN WARTEN MONIKA SCHEELE KNIGHT Originalausgabe Morgen kann warten Copyright © März 2017 | Monika Scheele Knight Schmollerstr. 3, 12435 Berlin Printed in Germany by Amazon Distribution GmbH, Leipzig ISBN: 1544176872 ISBN-13: 978-1544176871 INHALT Vorwort – In der Welt sein 1 1 Thassos – Sprache 14 2 Hiddensee – Elternsein 30 3 Rhodos – Epilepsie 44 4 Côte d’Azur – Fernand Deligny 62 5 Mallorca – Diagnoseanstieg 84 6 Connemara – Therapien 105 7 Südtirol – Neurodiversität 135 8 Südschweden – Inklusion 153 9 Normandie & Elsass – Geschichte 169 10 Valencia – Kultur 183 11 Prag & Theresienstadt – Ethik 204 12 Texel – Freundschaft 222 13 Berlin – Autismus als Metapher 236 Nachwort – Für immer 15 253 Respekt und Dank 257 Anmerkungen 259 Literaturverzeichnis 295 Dieses Buch ist für John, den Jungen mit der Bonbon-Agenda, der in den Mülleimer beißt, und die Gitarre wie einen Kontrabass spielt. Ein Partisan und ein Meister puren Seins. Vorwort – In der Welt sein »In jeder Krankheit treffen sich zwei Ereignisse: Die Geschichte einer Person und die Geschichte der Gesellschaft, in der diese Person lebt.« (Maurice Dorès) John wurde im September 2000 in Arlington Heights in den USA geboren. Als er achtzehn Monate alt war, entwickelte er plötzlich epileptische Anfälle und wurde in ein Krankenhaus eingewiesen. Sein Gitterbett hatte gepolsterte Stäbe, war nach oben hin ver schlossen, ein Käfig. Über eine Klammer an seinem großen Zeh führte ein Kabel zu einem Monitor, 126/96 war darauf in roten Digitalziffern zu lesen. Unser vorher fröhliches, starkes und neu gieriges Kind lag schwach in diesem Käfigbett, tief erschöpft von Medikamenten, Untersuchungen und Krampfanfällen. -
Autistics Speak
Spectrum | Autism Research News https://www.spectrumnews.org OPINION Autistics speak BY VIRGINIA HUGHES 1 NOVEMBER 2011 A year ago, an Australian group launched an autism awareness and fundraising event called Communication Shutdown. The idea was simple: Neurotypical people would ignore social networking sites such as Facebook and Twitter for the entire day, to simulate and show support for people with autism who have trouble communicating. Celebrities such as astronaut Buzz Aldrin, actress Fran Drescher, and animal scientist and autism advocate Temple Grandin were all on board. But Corina Lynn Becker, an adult with autism who has a blog, wasn't at all happy about it. "A non-Autistic person still [has] the capability to text on their phones, and speak verbally, and so would not be totally comprehending the true reality of Autistic disability," she wrote. "Twitter and Facebook are two of the sites that actually allow Autistics to communicate and connect with others in the community, so I will not be disappearing from the Internet, as it is my lifeline." Becker teamed up with Kathryn Bjornstad, another blogger and adult with autism, to create an alternative event: Autistics Speaking Day, which encourages people to exploit the power of social networks to raise awareness and reject negative stereotypes about the disorder. Last year, the day was far larger than Becker ever envisioned, with more than 500 participants from across the world speaking out about autism — including many people with the disorder who were inspired to launch blogs simply because of the event. Today marks the second annual Autistics Speaking Day, which I think should be broadcast not only to the general public, but to autism researchers. -
Shining the Light on Autism AEIOU Foundation Annual Report 2010/2011 Ii AEIOU Foundation Annual Report 2010-2011
Shining the light on Autism AEIOU Foundation Annual Report 2010/2011 ii AEIOU Foundation Annual Report 2010-2011 Welcome to AEIOU... Shining the Light on Autism It’s been a challenging year for many That same year, AEIOU Foundation Registered office: Our reporting process Queenslanders, but here at AEIOU was established. It was the first N70 Recreation Road This is the second annual report submitted Foundation we never cease to be organisation of its kind, and Nathan, Qld, 4111 by AEIOU Foundation. This report amazed by the generosity we have continues to lead the way in Australia documents the Foundation’s financial, Telephone: 07 3320 7500 witnessed in our community. It’s also in providing best practice early operational and community performance Facsimile: 07 3277 5500 for the financial year ending 30 June 2011. incredible to celebrate the triumphant intervention to children with autism, We welcome your feedback on this report. milestones the children and families along with practical and caring Postal: PO Box 226 Nathan, Qld, 4111 To contact us, please phone 07 3320 7500 in our centres achieve every day. support for families. Today, with nine or visit www.aeiou.org.au. Email: [email protected] Because at the end of the day, our centres located across Queensland, Website: www.aeiou.org.au goal is a simple one: it is to make a we remain committed to raising difference to the lives of every child awareness and understanding about ABN: 19 135 897 255 autism, providing exemplary education with autism. AEIOU Foundation is a registered charity services and helping families to break (CH1818) under ‘The Collections Act’ of You might know that in 2005, a report the bubble of autism. -
Facilitating Affective Engagement
ENGAGING THE FEELING AND WILL OF CHILDREN WITH AUTISM THROUGH THE MEDIUM OF COLOUR by DIANA MARY PAULI A thesis submitted to The University of Birmingham for the degree of DOCTOR OF PHILOSOPHY School of Education The University of Birmingham March 2004 University of Birmingham Research Archive e-theses repository This unpublished thesis/dissertation is copyright of the author and/or third parties. The intellectual property rights of the author or third parties in respect of this work are as defined by The Copyright Designs and Patents Act 1988 or as modified by any successor legislation. Any use made of information contained in this thesis/dissertation must be in accordance with that legislation and must be properly acknowledged. Further distribution or reproduction in any format is prohibited without the permission of the copyright holder. ABSTRACT This is a case study of the role of feeling and will in interaction with children with autism. It investigates the use of changing colours of light for enhancement of engagement at this level. The research was carried out in a specially designed room where the whole interior colour could be changed using dimmer-controlled lights. 19 children aged between 8 and 17 years with a diagnosis of severe autism were involved in the study. Data were collected using video recordings, a research diary and small-scale informal interviews and were analysed by quantitative and qualitative methods. Three main stages were developed. These involved observations of behaviour of children in different colours of light, of children interacting directly with changing coloured light, and of intensive interaction augmented by changing colour moods. -
Universal Periodic Review (Upr): Mid-Term Report 2020
UNIVERSAL PERIODIC REVIEW (UPR): MID-TERM REPORT 2020 Assessing India’s Implementation Of UPR-III Recommendations Aditi Patil 1 UNIVERSAL PERIODIC REVIEW (UPR): MID- TERM REPORT 2020 Assessing India’s Implementation Of UPR-III Recommendations Submitted by The Working Group on Human Rights in India and the UN EDITORIAL BOARD Mr. Sanjoy Hazarika Ms. Enakshi Ganguly Mr. Miloon Kothari Ms. Shivani Chaudhry COMPILATION AND EDITING Ms. Aditi Patil For further information, contact: Working Group on Human Rights in India and the UN Address: 3rd Floor, 55A, Siddharth Chambers, Kalu Sarai, New Delhi – 110016, India Tel: +91 11 4318 0200 Fax: +91 11 4318 0217 Website: http://wghr.org/ Email: [email protected] FOREWORD India’s Universal Periodic Review (UPR) took place for the third time (UPR-III) on 4 May 2017, when it received a total of 249 recommendations on diverse subjects and issues. India will be reviewed in its fourth UPR cycle (UPR-IV) in 2022. This mid-term review is an attempt by the Working Group on Human Rights in India and the United Nations (WGHR) to assess how far the Government of India has been able to implement the recommendations received. The report has been prepared with contributions from WGHR charter members as well as other partners. We are grateful to The YP Foundation, the Civil Society Forum on Human Rights (CSFHR), and Mr. Ankur Bisen for their contributions and inputs to this report. WGHR has allowed each contributor to write their respective chapter without being limited by a word count. We have sought to keep to a uniform format that is not judgmental, either in tone or content, and have based our report on factual research from a range of sources including government, international organizations, academic research, civil society reports, and media accounts. -
Terms Definition 3:1 Learning
Terms Definition (3:1 model) A service delivery model where 3 weeks out of each month are designated for direct intervention with students and one week is set aside for indirect services, such as meeting with 3:1 learning teachers, parents, and other specialists, developing treatment materials and completing paperwork. Reverse 3:1 model is 3 weeks of indirect services and 1 week of direct services. A legal document falling under the provisions of the Rehabilitation Act of 1973. It is designed to plan a program of instructional services to assist students with special needs who are 504 plan in a regular education setting. A 504 plan is not an Individualized Education Program (IEP) as a required for special education students. Supports or services provided to help a student access the Accommodation general education curriculum and validly demonstration learning. The term ADL is the basic tasks necessary to perform daily Activities of Daily activities. Examples are: eating, toileting, bathing, grooming, Living (ADL's) dressing, transferring, and mobility. The ability to react age appropriately and purposefully to Adaptive behavior changing circumstances. An action or thought in response to social and environmental situations. Attention-Deficit/Hyperactivity Disorder (AD/HD) is a ADHD (Attention neurobiological disorder. It is a persistent pattern of inattention Deficit Hyperactivity and/ or hyperactivity - impulsivity that is more frequent and Disorder) severe that is typically observed in individuals at a comparable level of development. A portable assistive technology device that allows one to edit and Alpha Smart enter text, then send it to a computer for formatting or send directly to a printer. -
COVID-19 Back-To-Classroom THINK Toolbox
COVID-19 Back-to-Classroom THINK Toolbox Teaching with Healthcare Informed Neurological Strategies for Kids Publication 821-148 August 2021 To request this document in another format, call 1-800-525-0127. Deaf or hard of hearing customers, please call 711 (Washington Relay) or email [email protected]. COVID-19 Back-to-Classroom THINK Toolbox: Teaching with Healthcare Informed Neurological Strategies for Kids Teachers, school staff, parents, caregivers, and students may experience emotional responses as they return to in-person school during the COVID-19 pandemic. This toolbox provides behavioral health tips and resources for navigating some of those responses. The toolbox includes general information about common emotional responses of children, teens, and adults during disasters and how these may present in the classroom and other areas of school life. Teachers and other school staff can use this resource to help with their own adjustment to returning to in- person school. Additionally, resources are provided for parents and caregivers to help their school-age children and teens deal with emotional responses to disasters and assist their return to in-person school. While we all are living though this global pandemic, many communities – particularly marginalized and communities of color – have been disproportionately impacted by COVID-19. The Department of Health believes that health equity is a human right and that promoting and working towards health equity benefits everyone. Using this Toolbox As outlined in the Contents section on the next page, this toolbox opens with an overview of the common emotional impacts of disasters on children and teens, followed by information on resilience, the impact of COVID-19 on school staff, and practicing self-care. -
Neurodiversity
Embracing Neurodiversity: Advocacy and Allyship Jessica Leza, MA, MT-BC Learning Objectives • Explore the concepts and culture of the neurodiversity movement that can impact a client’s therapeutic needs (CBMT Board Certification Domain I.D.9). • Identify cultural factors of the neurodiversity movement that can impact components of therapy such as rapport, motivation to participate in treatment, and appropriate goals and objectives (CBMT Board Certification Domain I.B.4.d). Overview 1. What is neurodiversity? Terminology 2. Values & culture of the neurodiversity movement 3. Autistic Experiences of Therapy 4. Implications for clinical practice in MT 5. Additional resources PowerPoint available at: http://www.JessicaLeza.com What is Neurodiversity? Terminology Neurodiversity (ND) - the phenomena of naturally-occurring, neurological diversity; the differences between all people Diversity does not only apply to race, sexuality, religion, et. al. Diversity also refers to disability & neurology. Term originally developed within autism community, independently coined by Judy Singer & Kassiane Asasumasu Read more: #Neurodiversity “Neurodiversity, some basic terms and definitions” by Nick Walker https://neurocosmopolitanism.com/neurodiversity-some-basic-terms-definitions/ “The essence of beauty is unity in variety.” – Felix Mendelssohn What is Neurodiversity? The Neurodiversity Movement Operates according to the Neurodiversity Paradigm – “the understanding of neurodiversity as a natural form of human diversity, subject to the same societal dynamics as other forms of diversity.” (Nick Walker, in “Throw Away the Master’s Tools”, in Loud Hands) •A disability rights movement, influenced by social model of disability •Fights for support & accommodations for diverse neurologies •Powered by self-advocacy (doesn’t speak for everybody, but stands up for the right for everyone to speak up for themselves) •Encourages a strengths-based perspective •Values the idea that human society needs/benefits from all types of brains.