Surface Diffusion Measurements of in on Ingaas Enabled by Droplet Epitaxy
Total Page:16
File Type:pdf, Size:1020Kb
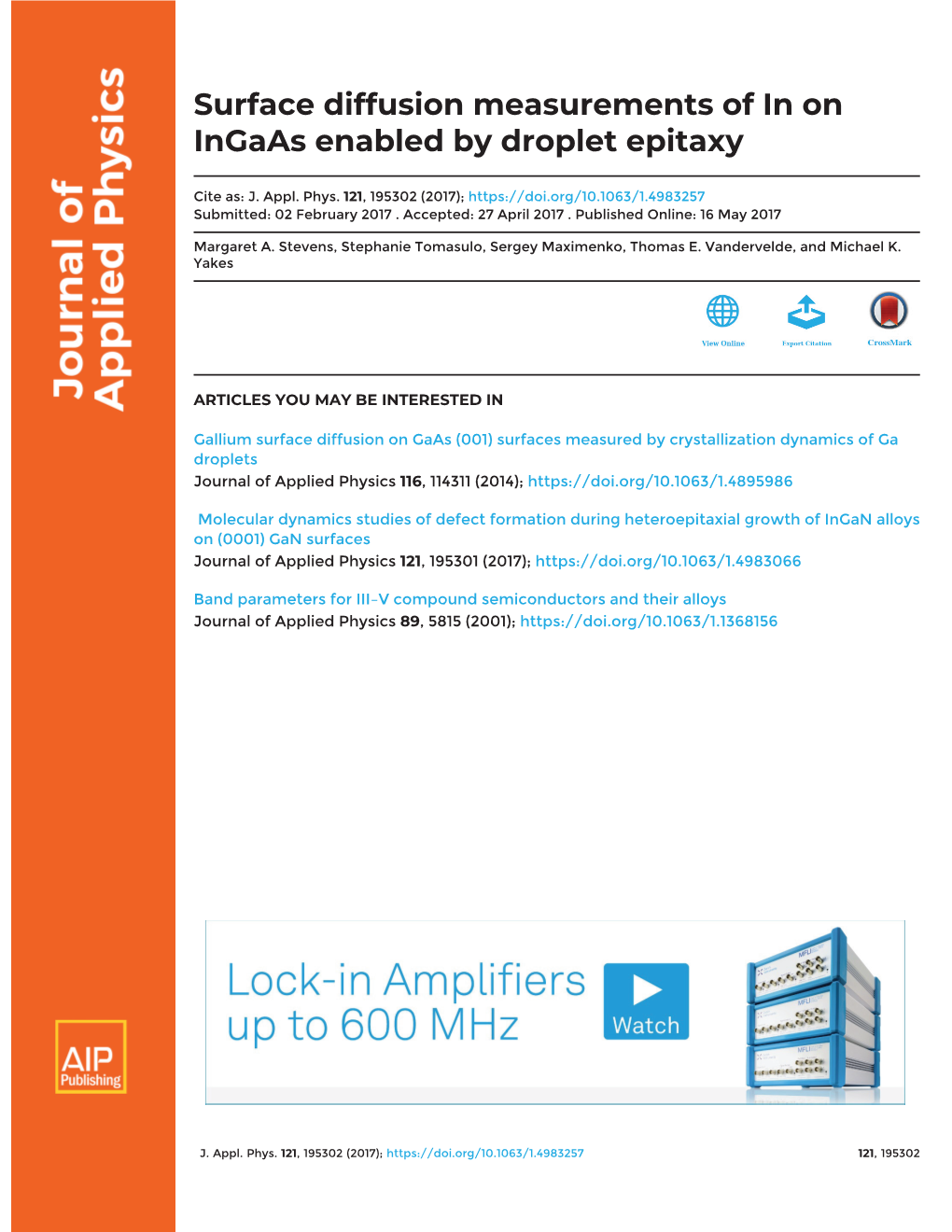
Load more
Recommended publications
-
Surface Diffusion Driven by Surface Energy
Spring 2004 Evolving Small Structures Z. Suo Lecture 6 Surface Diffusion Driven by Surface Energy Examples Flattening a surface. Spherodizing. Rayleigh instability. Grain boundary grooving. Sintering Self-assembled quantum dots Atomic Flux and Surface Velocity Atoms can arrive to the surface in many ways. Atoms in the vapor can condense to the surface. Or conversely, atoms on the solid surface can evaporate. Atoms can diffuse in the volume of the solid. The body can also change shape by creep. In this lecture, we assume atoms can only move on the surface by diffusion, and all other modes of transport are negligibly slow. This situation happens for crystals at relatively low temperature, in a low vapor pressure environment. Define the atomic flux on a solid surface by numberof atoms J = ()length (time) Note that this flux is a vector tangent to the surface, and has a different dimension from that in the bulk. The flux is a vector field on the solid surface Consider a small element of the surface of the body. Let vn be the velocity of the solid surface, taken to be positive when the surface element gains atoms. The velocity is normal to the solid surface. The velocity is a scalar field on the solid surface. February 21, 2009 1 Spring 2004 Evolving Small Structures Z. Suo The surface element extends when it gains atoms, and recedes when it loses atoms. Let Ω be the volume per atom in the solid. Thus, vn / Ω is the number of atoms gained per unit area and per unit time. -
Single Adatom Adsorption and Diffusion on Fe Surfaces
Journal of Modern Physics, 2011, 2, 1067-1072 1067 doi:10.4236/jmp.2011.29130 Published Online September 2011 (http://www.SciRP.org/journal/jmp) Single Adatom Adsorption and Diffusion on Fe Surfaces Changqing Wang1*, Dahu Chang2, Chunjuan Tang2, Jianfeng Su2, Yongsheng Zhang2, Yu Jia3 1Department of Civil Engineering, Luoyang Institute of Science and Technology, Luoyang, China 2Department of Mathematics and Physics, Luoyang Institute of Science and Technology, Luoyang, China 3School of Physics and Engineering, Key Laboratory of Material Physics of Ministry of Education, Zhengzhou University, Zhengzhou, China E-mail: *[email protected] Received December 25, 2010; revised March 22, 2011; accepted April 8, 2011 Abstract Using Embedded-atom-method (EAM) potential, we have performed in detail molecular dynamics studies on a Fe adatom adsorption and diffusion dynamics on three low miller index surfaces, Fe (110), Fe (001), and Fe (111). Our results present that adatom adsorption energies and diffusion barriers on these surfaces have similar monotonic trend: adsorption energies, Ea(110) < Ea(001) < Ea(111), diffusion barriers, Ed(110) < Ed(001) < Ed(111). On the Fe (110) surface, adatom simple jump is the main diffusion mechanism with relatively low energy barrier; nevertheless, adatoms exchange with surface atoms play a dominant role in surface diffusion on the Fe (001). Keywords: EAM Potential, Molecular Dynamics, Diffusion, Nudged Elastic Band (NEB) Method, Iron, Adsorption 1. Introduction and Monte Carlo (MC) [16,17], it has been investigated intensively [18]. Understanding the processes of nucleation and growth on Iron is a very common metal for application. Abun- a substrate surface is of importance for growing high- dant work has been done on atom diffusion on the Fe quality thin film materials. -
Heterogeneous Electrocatalysis in Porous Cathodes of Solid Oxide Fuel Cells
Electrochimica Acta 159 (2015) 71–80 Contents lists available at ScienceDirect Electrochimica Acta journa l homepage: www.elsevier.com/locate/electacta Heterogeneous electrocatalysis in porous cathodes of solid oxide fuel cells a b a,c b b b a,d, Y. Fu , S. Poizeau , A. Bertei , C. Qi , A. Mohanram , J.D. Pietras , M.Z. Bazant * a Department of Chemical Engineering, Massachusetts Institute of Technology, Cambridge, MA, USA b Saint-Gobain Ceramics and Plastics, Northboro Research and Development Center, Northboro, MA, USA c Department of Civil and Industrial Engineering, University of Pisa, Italy d Department of Mathematics, Massachusetts Institute of Technology, Cambridge, MA, USA A R T I C L E I N F O A B S T R A C T Article history: A general physics-based model is developed for heterogeneous electrocatalysis in porous electrodes and Received 3 December 2014 used to predict and interpret the impedance of solid oxide fuel cells. This model describes the coupled Received in revised form 19 January 2015 processes of oxygen gas dissociative adsorption and surface diffusion of the oxygen intermediate to the Accepted 22 January 2015 triple phase boundary, where charge transfer occurs. The model accurately captures the Gerischer-like Available online 24 January 2015 frequency dependence and the oxygen partial pressure dependence of the impedance of symmetric cathode cells. Digital image analysis of the microstructure of the cathode functional layer in four different Keywords: cells directly confirms the predicted connection between geometrical properties and the impedance electrochemical impedance spectroscopy response. As in classical catalysis, the electrocatalytic activity is controlled by an effective Thiele (EIS) modulus, which is the ratio of the surface diffusion length (mean distance from an adsorption site to the Gerischer element porous electrode triple phase boundary) to the surface boundary layer length (square root of surface diffusivity divided by oxygen reduction reaction (ORR) the adsorption rate constant). -
A Study of Surface Diffusion with the Scanning Tunneling Microscope from Fluctuations of the Tunneling Current Manuel Leonardo Pasetes Lozano Iowa State University
Iowa State University Capstones, Theses and Retrospective Theses and Dissertations Dissertations 1995 A study of surface diffusion with the scanning tunneling microscope from fluctuations of the tunneling current Manuel Leonardo Pasetes Lozano Iowa State University Follow this and additional works at: https://lib.dr.iastate.edu/rtd Part of the Condensed Matter Physics Commons Recommended Citation Pasetes Lozano, Manuel Leonardo, "A study of surface diffusion with the scanning tunneling microscope from fluctuations of the tunneling current " (1995). Retrospective Theses and Dissertations. 10959. https://lib.dr.iastate.edu/rtd/10959 This Dissertation is brought to you for free and open access by the Iowa State University Capstones, Theses and Dissertations at Iowa State University Digital Repository. It has been accepted for inclusion in Retrospective Theses and Dissertations by an authorized administrator of Iowa State University Digital Repository. For more information, please contact [email protected]. INFORMATION TO USERS This manuscr^t has been reproduced from the nuarofilm master. UMI films tiie text directfy from the original or copy submitted. Hius, some thesis and dissertation copies are in typewriter face, while others may be £rom aiQr type of conq)uter printer. The qnality of this Feprodnction is dependent upon the qoali^ of the copy submitted. Broken or indistinct print, colored or poor quality illustrations and photographs, print bleedthrough, substandard margirnt^ and is^oper alignment can adverse^ affect reproduction. In the unlikely event that the author did not send UMI a complete manuscript and there are missing pages, these will be noted. Also, if unauthorized copyright material had to be removed, a note wiQ indicate the deletion. -
A Study of the Surface Reactions of Hydrocarbons on Tungsten by Field Electron Emission Microscopy Nelson Craig Gardner Iowa State University
Iowa State University Capstones, Theses and Retrospective Theses and Dissertations Dissertations 1966 A study of the surface reactions of hydrocarbons on tungsten by field electron emission microscopy Nelson Craig Gardner Iowa State University Follow this and additional works at: https://lib.dr.iastate.edu/rtd Part of the Physical Chemistry Commons Recommended Citation Gardner, Nelson Craig, "A study of the surface reactions of hydrocarbons on tungsten by field electron emission microscopy " (1966). Retrospective Theses and Dissertations. 5365. https://lib.dr.iastate.edu/rtd/5365 This Dissertation is brought to you for free and open access by the Iowa State University Capstones, Theses and Dissertations at Iowa State University Digital Repository. It has been accepted for inclusion in Retrospective Theses and Dissertations by an authorized administrator of Iowa State University Digital Repository. For more information, please contact [email protected]. This dissertation has been microfihned exactly as received ® 7-5587 GARDNER, Nelson Craig, 1937- A STUDY OF THE SURFACE REACTIONS OF HYDRO CARBONS ON TUNGSTEN BY FIELD ELECTRON EMIS SION MICROSCOPY. Iowa State University of Science and Technology, Ph.D„ 1966 Chemistry, physical University Microfilms, Inc., Ann Arbor, Michigan A STUDY OF THE SURFACE REACTIONS OF HYDROCARBONS ON TUNGSTEN BY FIELD ELECTRON EMISSION MICROSCOPY by Nelson Craig Gardner A Dissertation Submitted to the Graduate Faculty in partial Fulfillment of The Requirements for the Degree of DOCTOR OF PHILOSOPHY Major Subject: -
Chapter 7 Solid Surface
Chapter 7 Solid Surface Definition of solid : A matter that is rigid and resists stress. Difference between solid and liquid surface : Liquid : always in equilibrium and equipotential. (Fig 7.1a,b) Solid : the two assumptions are not valid. (Fig 7.1c,d) 7.1 Surface Mobility in Solids Consider a surface being in a dynamic state with interchange of molecules between the surface , the bulk , and the vapor phase . The impinging rate of vapor on a surface : Z 1 2 ⎛ 3 ⎞ −2 −1 Z = 0.23P⎜ ⎟ [cm ⋅ sec ]…….. (7.1) ⎝ MRT ⎠ P: vapor pressure of the material M: molecular weight ex. for tungsten(W) , P ≈ 10-37mmHg Z≈ 10~20 (atoms / cm2 ⋅ sec) Lifetime≈ 1037sec Tamman Temperature : (for bulk diffusion) z The temperature at which the atoms or molecules of the solid acquired sufficient energy for their bulk mobility and reactivity to become appreciable. (ex : sintering) z Tamman temperature ≈ one-half of melting point (K) z For example : for Cu at 725℃ P≈ 10-8mmHg , Z ≈ 1015 atoms/cm2.sec Surface resident time ≈ 1 sec Bulk diffusion rate ≈ 10nm in 0.1 sec But at room temperature ⇒ 10nm needs 1027 sec Surface diffusion : perform below the Tamman temperature bulk diffusion : no change in total activation energy (Fig 7.2a) surface diffusion : has a much lower barrier to diffusion (Fig 7.2b) , and much greater mobility. The history (especially thermal) of the material is important to the property (nature) of a solid surface. Surface changes ⇒ alterations in characteristics such as adsorption , wetting , adhesion , friction , or lubrication 7.1.1 Sintering Definition : For solid powders , fusion of adjacent particles occur when the system is heated to some temperature below the melting point. -
Diffusion in Copper and Copper Alloys. Part I. Volume and Surface Self-Diffusion in Copper
Diffusion in Copper and Copper Alloys. Part I. Volume and Surface Self-Diffusion in Copper Cite as: Journal of Physical and Chemical Reference Data 2, 643 (1973); https://doi.org/10.1063/1.3253129 Published Online: 29 October 2009 Daniel B. Butrymowicz, John R. Manning, and Michael E. Read ARTICLES YOU MAY BE INTERESTED IN Diffusion in Copper and Copper Alloys, Part II. Copper-Silver and Copper-Gold Systems Journal of Physical and Chemical Reference Data 3, 527 (1974); https:// doi.org/10.1063/1.3253145 Diffusion in copper and copper alloys. Part III. Diffusion in systems involving elements of the groups IA, IIA, IIIB, IVB, VB, VIB, and VIIB Journal of Physical and Chemical Reference Data 4, 177 (1975); https://doi.org/10.1063/1.555516 Diffusion in copper and copper alloys part IV. Diffusion in systems involving elements of group VIII Journal of Physical and Chemical Reference Data 5, 103 (1976); https://doi.org/10.1063/1.555528 Journal of Physical and Chemical Reference Data 2, 643 (1973); https://doi.org/10.1063/1.3253129 2, 643 © 1973 The U. S. Secretary of Commerce on behalf of the United States. Diffusion in Copper and Copper Alloys Part I. Volume and Surface Self-Diffusion in Copper DanielB. Butrymowicz:, John R. Manning, and Michael E. Read Institute for Materials Research, National Bureau of Standards, Washington, D. C. 20234 A survey, comparison, and critical analysis is presented of data compiled fr.om t~e sci~nt~c literature concerning copper self-di1fusion. Topics include volume diffusion, dislocat1o~ PI~ diffus~on, surface diffusion, sintering, electromigration, thermomigration, pressure effect on diffuSlO~, st~am~nhanced diffusion nuclear magnetic resonance measurements of solid state diffusion and diffUSion m molten copper. -
CHAPTER 3: Epitaxy
Chapter 3 1 CHAPTER 3: Epitaxy Epitaxy (epi means "upon" and taxis means "ordered") is a term applied to processes used to grow a thin crystalline layer on a crystalline substrate. The seed crystal in epitaxial processes is the substrate. Unlike the Czochralski process, crystalline thin films can be grown below the melting point using techniques such as chemical vapor deposition (CVD), molecular beam epitaxy (MBE), etc. When a material is grown epitaxially on a substrate of the same material, the process is called homoepitaxy, an example of which is depicted in Figure 3.1. On the contrary, if the layer and substrate are of different materials, such as AlxGa1-xAs on GaAs, the process is termed heteroepitaxy. Naturally, in heteroepitaxy, the crystal structures of the layer and the substrate must be similar in order to achieve good crystalline integrity. Performance of many devices, such as CMOS (Complementary MOS) and DRAM (Dynamic Random Access Memory), can be improved by employing epitaxial wafers. Succinctly speaking, epitaxial wafers have two fundamental advantages over bulk wafers. First, they offer device engineers a means to control the doping profiles not attainable through other conventional means such as diffusion or ion implantation. Secondly, the physical and chemical properties of the epitaxial layers can be made different from the bulk materials. A DRAM (dynamic random access memory) circuit employing MOS devices (Figure 3.2- 1) is vulnerable to soft errors created by alpha particles originating from packaging materials and the environment. These alpha particles can cause electron-hole pairs in the bulk of the wafer. If these charges migrate to the storage cell of a DRAM structure, the data stored can be wiped out. -
Surface Diffusion
Surface Di®usion Oleg M. Braun Institute of Physics National Academy of Sciences of Ukraine Contents 1 Introduction 3 2 Di®usion of a Single Atom 5 2.1 Di®usion: what is it? . 5 2.2 Langevin and Fokker-Planck-Kramers equations . 7 2.3 Solution: one-dimensional system . 10 2.3.1 Conventional di®usion equation . 10 2.3.2 The FPK equation in the absence of the substrate potential . 11 2.3.3 General case . 12 2.3.4 Smoluchowski equation . 13 2.3.5 Low-friction limit . 17 2.3.6 Intermediate friction . 19 2.4 Kramers theory . 20 2.5 Computer simulation: Molecular Dynamics . 23 2.6 Lattice models . 24 3 Collective Di®usion 27 3.1 Mechanisms of interaction between adsorbed atoms . 27 3.2 Di®erent di®usion coe±cients . 28 3.2.1 Susceptibility . 28 3.2.2 Self-di®usion coe±cient . 29 3.2.3 Mobility . 30 3.2.4 Chemical di®usivity . 30 3.3 Ideology of quasiparticles . 32 3.4 One-dimensional chain (the Frenkel-Kontorova model) . 32 3.5 Gas model . 32 3.6 Lattice models . 32 3.7 2D Frenkel-Kontorova model . 33 3.8 Phase transitions . 33 3.8.1 First-order phase transition . 33 3.8.2 Second-order phase transition . 33 3.9 Computer simulation . 34 3.9.1 Monte Carlo simulation . 34 3.9.2 Molecular Dynamics simulation . 34 4 Defects 35 4.1 ... 35 1 2 CONTENTS 5 Experimental Methods 37 6 Results 39 6.1 Quasi-one-dimensional systems . 39 6.2 .. -
Cluster Diffusion and Coalescence on Metal Surfaces: Applications of a Self-Learning Kinetic Monte-Carlo Method
Cluster Diffusion and Coalescence on Metal Surfaces: applications of a Self-learning Kinetic Monte-Carlo method Talat S. Rahman1*, Abdelkader Kara1, Altaf Karim1, Oleg Trushin2 1Department of Physics, Cardwell Hall, Kansas State University, Manhattan, KS 66506 2Institute of Microelectronics and Informatics, Russian Academy of Sciences, Yaroslavl 150007, Russia. *email:[email protected] ABSTRACT The Kinetic Monte Carlo (KMC) method has become an important tool for examination of phenomena like surface diffusion and thin film growth because of its ability to carry out simulations for time scales that are relevant to experiments. But the method generally has limited predictive power because of its reliance on predetermined atomic events and their energetics as input. We present a novel method, within the lattice gas model in which we combine standard KMC with automatic generation of a table of microscopic events, facilitated by a pattern recognition scheme. Each time the system encounters a new configuration, the algorithm initiates a procedure for saddle point search around a given energy minimum. Nontrivial paths are thus selected and the fully characterized transition path is permanently recorded in a database for future usage. The system thus automatically builds up all possible single and multiple atom processes that it needs for a sustained simulation. Application of the method to the examination of the diffusion of 2-dimensional adatom clusters on Cu(111) displays the key role played by specific diffusion processes and also reveals the presence of a number of multiple atom processes, whose importance is found to decrease with increasing cluster size and decreasing surface temperature. Similarly, the rate limiting steps in the coalescence of adatom islands are determined. -
8. Surface Diffusion
Surface Physics 2008 8. Surface Diffusion Assistant: Dr. Enrico Gnecco NCCR Nanoscale Science Random-Walk Motion • Thermal motion of an adatom on an ideal crystal surface : - Thermal excitation the adatom can hop from one adsorption site to the next • Mean square displacement at time t: 2 2 ∆r = νa t a = jump distance; ν = hopping frequency (Note that νt = number of hops!) • Diffusion coefficient : 2 ∆r νa2 2 in 1D diffusion D = = z = number of first neighbors = 4 on a square lattice zt z 6 on a hexagonal lattice Random-Walk Motion - Hopping surmounting a potential barrier • Arrhenius law : E ν0 = oscillation frequency of the atom in the well; ν = ν exp − diff 0 k T B Ediff = barrier height Tipically Ediff ~ 5-20% of Q (heat of desorption) • For chemisorbed species: Ediff >> kBT • If Ediff < kBT: 2D gas (only a few physisorbed species) Fick’s Laws • Fick’s First Law (for 1D diffusion): ∂c J = −D ∂x diffusion flux concentration gradient (flux region of lower concentration) • Fick’s Second Law (for 1D diffusion): ∂c ∂2c = D from equation of continuity ∂t ∂x2 • Analytical solutions can be found for specific initial and boundary conditions! Analytical Solutions of Fick’s Laws • We introduce the error function 2 x erf (x) = ∫ exp( −t 2 ) dt π 0 • Source of constant concentration: x c(x,t) = c0 1− erf 2 Dt 2 Dt : diffusion length - Example: Submonolayer film with 3D islands supplying mobile adatoms Analytical Solutions of Fick’s Laws • Source of infinite extent: c x c(x,t) = 0 1− erf 2 2 Dt - Example: Submonolayer -
Molecular Dynamics Study on the Melting and Coalescence of Au Nanoparticles
Surface-Induced Phase Transition During Coalescence of Au Nanoparticles: A Molecular Dynamics Simulation Study1 Reza Darvishi Kamachali Contact Address: Max-Planck-Institut für Eisenforschung, Max-Planck-Str. 1, 40237 Düsseldorf, Germany. Email: [email protected] Abstract In this study, the melting and coalescence of Au nanoparticles were investigated using molecular dynamics simulation. The melting points of nanoparticles were calculated by studying the potential energy and Lindemann indices as a function of temperature. The simulations show that coalescence of two Au nanoparticles of the same size occurs at far lower temperatures than their corresponding melting temperature. For smaller nanoparticles, the difference between melting and coalescence temperature increases. Detailed analyses of the Lindemann indices and potential energy distribution across the nanoparticles show that the surface melting in nanoparticles begins at several hundred degrees below the melting point. This suggests that the coalescence is governed by the surface diffusion and surface melting. Furthermore, the surface reduction during the coalescence accelerates its kinetics. It is found that for small enough particles and/or at elevated temperatures, the heat released due to the surface reduction results in a melting transition of the two attached nanoparticles. Keywords: Molecular Dynamics Simulation; Nanosystems; Coalescence; Surface Melting; Gold Nanoparticles; Phase Transition. 1. Introduction Due to the unique electronic, optical and catalytic properties of metallic nanoparticles [1-3], an increasingly growing interest is developing to explore 1 Completed in April 2008. See Acknowledgments for details. 1 nanoparticles technological applications [4-6]. In this context, the interactions between nanoparticles and their surrounding objects such as solvents, ion/electron beams, and other nanoparticles are fundamentally and technologically important for their storage and performance [7, 8].