High-Performance Alloys for Resistance to Aqueous Corrosion
Total Page:16
File Type:pdf, Size:1020Kb
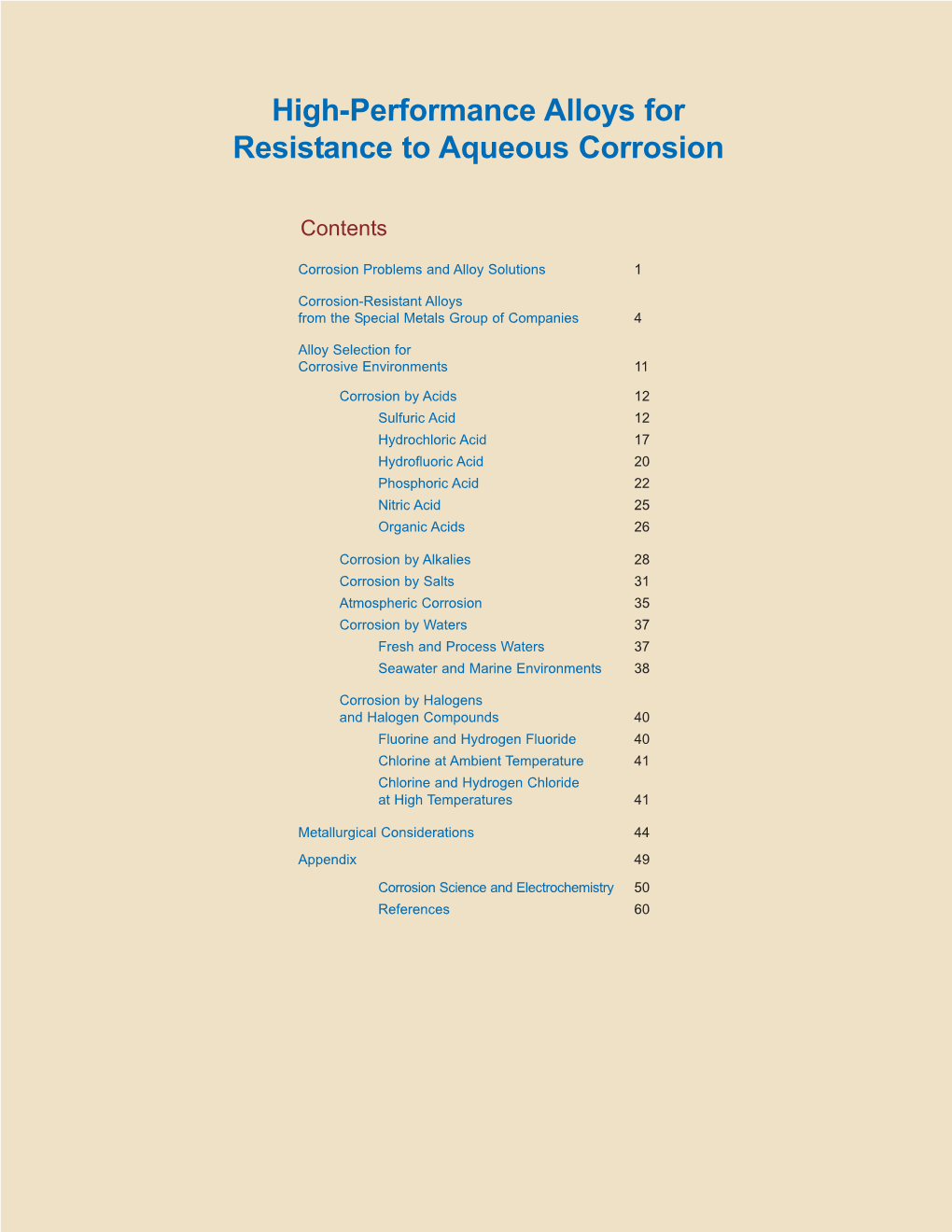
Load more
Recommended publications
-
Outside Diameter Initiated Stress Corrosion Cracking Revised Final White Paper", Developed by AREVA and Westinghouse Under PWROG Program PA-MSC-0474
Program Management Office PWROG 102 Addison Road Connecticut 06095 q .Windsor, ko'ners-- PA-MSC-0474 Project Number 694 October 14, 2010 OG-10-354 U.S. Nuclear Regulatory Commission Document Control Desk Washington, DC 20555-0001 Subject: PWR Owners Group For Information Only - Outside Diameter Initiated Stress Corrosion Crackin2 Revised Final White Paper, PA-MSC-0474 This letter transmits two (2) non-proprietary copies of PWROG document "Outside Diameter Initiated Stress Corrosion Cracking Revised Final White Paper", developed by AREVA and Westinghouse under PWROG program PA-MSC-0474. This document is being submitted for information only. No safety evaluation (SE) is expected and therefore, no review fees should be incurred. This white paper summarizes the recent occurrences of ODSCC of stainless steel piping identified at Callaway, Wolf Creek and SONGS. Available operating experience (OE) at units that have observed similar phenomena is summarized as well to give a better understanding of the issue. Each of the key factors that contribute to ODSCC was considered along with the reported operating experience to perform a preliminary assessment of areas that may be susceptible to ODSCC. Also a qualitative evaluation was performed to determine whether ODSCC of stainless steel piping represents an immediate safety concern. This white paper is meant to address the issue of ODSCC of stainless steel systems for the near term. I&E guidelines are currently being developed through the PWROG to provide long term guidance. Correspondence related to this transmittal should be addressed to: Mr. W. Anthony Nowinowski, Manager Owners Group, Program Management Office Westinghouse Electric Company 1000 Westinghouse Drive, Suite 380 Cranberry Township, PA 16066 U.S. -
Forms of Corrosion Uniform Corrosion
Chapter 4 Forms of corrosion Uniform corrosion In such type of corrosion there is a uniform decrease in the volume of the metal due to direct contact with the surrounding environment. Examples Dissolvation of Zn, Al metal in acids and Pb metal in base. Atmospheric corrosion Atmospheric corrosion take place due to direct contact between metal and atmosphere Types of atmosphere: Gas type: contain mainly oxygen gas( 23% W / W) and water vapor. Liquid type: contain mainly water and dissolved oxygen. iron rust Atmospheric corrosion involve formation of metal oxide layer when metal in direct contact with its surrounding environment. Example: Formation of iron rust due to contact with air Fe + air, H2O Fe(OH)2 Fe2O3 Fe2O3 .3H2O is Iron rust (reddish brown ppt.) Oxide layers Protective Non Protective Non active active Non porous porous Ex: Zn, Al, Ni Ex: iron rust Rate of atmospheric corrosion depends on Nature of metal or alloy. Nature of oxide layer. Factors affecting atmospheric corrosion: Type of metal or alloy. Type of atmosphere (dust, humidity, pollutant. Water vapor, gases,…) Temperature( as T increase as rate increase) Time: The extent of corrosion increases with increased time Surface Condition: more roughness, more corrosion The presence of foreign matter influence the speed of corrosion PLAY ACTIVE FIGURE Galvanic corrosion Take place due to the contact between bimetallic couple exposed to the same environment due to the potential difference. Mechanism of galvanic corrosion: For two different metals M1 and M2 when exposed to the same corrosive environment, if M1 is more active than M2 M1 M2 Anodic reaction: M M n+ + ne- (n=1, 2, 3, …) Anodic metal will be corroded. -
Introduction to Corrosion Your Friendly TSC Corrosion Staff
Introduction to Corrosion Your Friendly TSC Corrosion Staff: Daryl Little Ph.D. Materials Science & Engineering [email protected] 303-445-2384 Lee Sears Ph.D. Materials Science & Engineering [email protected] 303-445-2392 Jessica Torrey Ph.D. Materials Science & Engineering [email protected] 303-445-2376 Roger Turcotte, PE, CPS Materials Engineer [email protected] 303-445-2383 What is Corrosion? CORROSION IS DEFINED AS THE DETERIORATION OF A MATERIAL AND/OR ITS PROPERTIES CAUSED BY A REACTION WITH ITS ENVIRONMENT. Why is Corrosion a Major Concern? First and Most Important- Public Safety! • June 28, 1983: Mianus River Bridge, Greenwich, CT (TIME photo archive) • Northbound 3-lane section of I-95 bridge collapsed, killing 3 people • “Pin and Hanger” design was compromised when pin was displaced due to extensive corrosion of load-bearing components, amplified by salt from road maintenance. • Inadequate maintenance procedures were also cited as a contributing factor. • Subsequent to this failure, extensive inspections were conducted on this type of bridge across the country, and design modification were made to prevent catastrophic failures of this kind. First and Most Important- Public Safety! • April 28,1988, Aloha Airlines 737 Accident • 18 feet of cabin skin ripped off, resulting in the death of a flight attendant and many injuries • Attributed to corrosion fatigue Reclamation Case Study- Folsom Dam • Spillway gate No. 3 was damaged beyond repair, but no flooding occurred. • Replacement of No. 3 and repair of other gates cost ~$20 million and required 40% drainage of reservoir • Cause of failure: Increasing corrosion at the trunnion pin-hub interface raised the coefficient of friction and, therefore, the bending stress in the strut and the axial force in the brace exceeded limits. -
Stainless Steel Selection Guide
TAContentsBLE OF Discovery of Stainless Steel . .page 2 What is Stainless Steel . .page 3 Stainless Steel Classifications . .page 4 • Austenitic . .page 4 • Ferritic . .page 5 • Duplex . .page 5 • Martensitic . .page 6 • Precipitation Hardening . .page 6 Nickel Based Alloys . .page 7 Strength & Heat Treatment . .page 7 The Basics of Corrosion . .page 8 • General or Uniform Corrosion . .page 9 • Galvanic Corrosion . .page 11 • Pitting Corrosion . .page 11 • Crevice Corrosion . .page 13 • Intergranular Corrosion . .page 14 • Stress Corrosion Cracking . .page 15 • Microbiologically Influence Corrosion . .page 17 Welding Stainless Steel . .page 18 Alloy Selection . .page 22 Wrought Stainless Steel Composition . .page 24 Wrought Nickel Alloy Composition . .page 25 Stainless Steel and Nickel Alloy Filler Metal . .page 26 PR“It’sEF stainlessAC steel,E it shouldn’t rust” This is often the kind of statements heard from individuals when discussing a failure of process piping or equipment. This is also an indication of how little is actually understood about stainless steel and the applications where it is used. For years the food, beverage and pharmaceutical industries have used stainless steels in their process piping systems. Most of the time stainless steel components provide satisfactory results. Occasionally a catastrophic failure will occur. The purpose of the information contained within this document is to bring an understanding to stainless steel, it’s uses, and why it will fail under certain conditions. In the following pages we will discuss the different classes of stainless steel, heat treatment, corrosion, welding, and finally material selection. As with any failure, it is imperative the cause of the failure be identified before a proper fix can be recognized. -
United States Patent Office Patented Sept
/ w 3,466,192 United States Patent Office Patented Sept. 9, 1969 1. 2 Typical examples of aqueous oxidizing acid system 3,466,192 CORROSION PREVENTION PROCESS which contain an agent from the class consisting of nitrate George S. Gardner, Elkins Park, Pa., assignor to Amchem ion, ferric ion and hydrogen peroxide, and which are - Products, Inc., Ambler, Pa., a corporation of Delaware suitable for use in accordance with the process of this No Drawing. Filed Jan. 23, 1967, Ser. No. 610,788 invention include: Int, Cl, B08b. 17/00 Nitric acid. - ". U.S. C. 134-3 4 Claims Nitric acid-hydrochloric acid. itric acid--sulfuric acid. Nitric acid, sulfuric acid--ferric sulfate. ABSTRACT OF THE DISCLOSURE 10 Nitric acid--hydrofluoric acid. Oxidizing acid attack on basis metal surfaces is re Hydrochloric acid--ferric chloride. duced by use of an oxidizing acid solution containing Hydrochloric acid, ferric chloride--citric acid. nitrate, ferric ion or hydrogen peroxide along with solu Sulfuric acid--ferric sulfate. ble methylol thiourea compounds in the acid solution. Acetic acid--ferric nitrate. Copper ion is added to enhance corrosion prevention by 15 Glycolic and formic acids--ferric nitrate. the acid solutions. Hydrogen peroxide and hydrofluoric acid. Hydrogen peroxide, hydrochloric acid and acetic or nitric acids. The present invention relates to a method of inhibiting the corrosion of metal surfaces and more particularly is 20 The concentration of the respective components in each concerned with the utilization of inhibited oxidizing acid of these examples of oxidizing acid systems will vary systems for treating metal surfaces. depending upon the type of metal being treated and the It is known in the art that oxidizing acid systems, temperature of treatment as is well known to those skilled while capable of producing the desired treatment of metal in the art of pickling and cleaning of metal surfaces. -
Pitting Growth Rate in Carbon Steel Exposed to Simulated Radioactive Waste (U)
WSRC-TR-96-0024 Pitting Growth Rate in Carbon Steel Exposed to Simulated Radioactive Waste (U) by P. E. Zapp Westinghouse Savannah River Company Savannah River Site • Aiken, South Carolina 29808 DOE Contract No. DE-AC09-89SR18035 This paper was prepared in connection with work done under the above contract number with the U. S. Department of Energy. By acceptance of this paper, the publisher and/or recipient acknowledges the U. S. Government's right to retain a nonexclusive, royalty-free license in and to any copyright covering this paper, along with the right to reproduce and to authorize others to reproduce all or part of the copyrighted paper. DISTRIBUTION OF THIS DOCUMENT IS UNLIMITED DISCLAIMER Portions of this document may be illegible in electronic image products. Images are produced from the best available original document. DISCLAIMER This report was prepared as an account of work sponsored by an jagency of. the United States Government Neither the United States Government nor any agency thereof, nor any of their employees, makes any warranty, express or implied, or assumes any legal liability or •responsibility for the accuracy, completeness, or usefulness of any information, apparatus, product, or process disclosed, .or represents that its use would not infringe privately owned rights. Reference herein to any specific commercial product, process, or service by trade name, trademark, manufacturer, or otherwise does not necessarily constitute or imply its endorsement,, recommendation, or favoring by the United States Government or any agency thereof. The views and opinions of authors expressed herein do not necessarily state or reflect those of the United States Government or any agency thereof. -
In-Situ Monitoring and Analysis of the Pitting Corrosion of Carbon Steel by Acoustic Emission
applied sciences Article In-Situ Monitoring and Analysis of the Pitting Corrosion of Carbon Steel by Acoustic Emission Junlei Tang 1 , Junyang Li 2, Hu Wang 2,*, Yingying Wang 1 and Geng Chen 3 1 School of Chemistry and Chemical Engineering, Southwest Petroleum University, Chengdu 610500, China; [email protected] (J.T.); [email protected] (Y.W.) 2 School of Material Science and Engineering, Southwest Petroleum University, Chengdu 610500, China; [email protected] 3 CNOOC Energy Technology & Services-Shanghai Environmental Engineering & Technology Branch, Shanghai 200335, China; [email protected] * Correspondence: [email protected]; Tel.: +86-028-83037361 Received: 5 November 2018; Accepted: 8 February 2019; Published: 18 February 2019 Abstract: The acoustic emission (AE) technique was applied to monitor the pitting corrosion of carbon steel in NaHCO3 + NaCl solutions. The open circuit potential (OCP) measurement and corrosion morphology in-situ capturing using an optical microscope were conducted during AE monitoring. The corrosion micromorphology was characterized with a scanning electron microscope (SEM). The propagation behavior and AE features of natural pitting on carbon steel were investigated. After completion of the signal processing, including pre-treatment, shape preserving interpolation, and denoising, for raw AE waveforms, three types of AE signals were classified in the correlation diagrams of the new waveform parameters. Finally, a 2D pattern recognition method was established to calculate the similarity of different continuous AE graphics, which is quite effective to distinguish the localized corrosion from uniform corrosion. Keywords: carbon steel; pitting corrosion; acoustic emission; wavelets; pattern recognition 1. Introduction In the modern construction industry, carbon steel is widely used because of its low price and good mechanical properties. -
Pitting Corrosion of Metals a Review of the Critical Factors
Journal of the Electrochemical Society, Vol. 145, No. 6, 1998, pp. 2186-2198. ISSN: (Print 0013-4651) (Online 1945-7111) DOI: 10.1149/1.1838615 http://www.electrochem.org/ http://scitation.aip.org/JES http://scitation.aip.org/getpdf/servlet/GetPDFServlet?filetype=pdf&id=JESOAN000145000006002186000001&idty pe=cvips&prog=normal © The Electrochemical Society, Inc. 1998. All rights reserved. Except as provided under U.S. copyright law, this work may not be reproduced, resold, distributed, or modified without the express permission of The Electrochemical Society (ECS). The archival version of this work was published in Journal of the Electrochemical Society, Vol. 145, No. 6, 1998, pp. 2186-2198. Pitting Corrosion of Metals A Review of the Critical Factors G. S. Frankel Fontana Corrosion Center, The Ohio State University, Columbus, Ohio ABSTRACT Pitting corrosion is localized accelerated dissolution of metal that occurs as a result of a breakdown of the otherwise protective passive film on the metal surface. This paper provides an overview of the critical factors influencing the pitting corrosion of metals. The phenomenology of pitting corrosion is discussed, including the effects of alloy composition, environment, potential, and temperature. A summary is then given of studies that have focused on various stages of the pitting process, including breakdown of the passive film, metastable pitting, and pit growth. Introduction Many engineering alloys, such as stainless steels and Al alloys, are useful only because of passive films, which are thin (nanometer scale), oxide layers that form naturally on the metal surface and greatly reduce the rate of corrosion of the alloys. Such passive films, however, are often susceptible to localized breakdown resulting in accelerated dissolution of the underlying metal. -
Four Types of Heat Exchanger Failures
Four Types of Heat Exchanger Failures . mechanical, chemically induced corrosion, combination of mechanical and chemically induced corrosion, and scale, mud, and algae fouling By MARVIN P. SCHWARTZ, Chief Product Engineer, ITT Bell & Gossett a unit of Fluid Handling Div., International Telephone & Telegraph Corp , Skokie IL Hcat exchangers usually provide a long service life with Maximum recommended velocity in the tubes and little or no maintenance because they do not contain any entrance nozzle is a function of many variables, including moving parts. However, there are four types of heat tube material, fluid handled, and temperature. Materials exchanger failures that can occur, and can usually be such as steel, stainless steel, and copper-nickel withstand prevented: mechanical, chemically induced corrosion, higher tube velocities than copper. Copper is normally combination of mechanical and chemically induced limited to 7.5 fps; the other materials can handle 10 or 11 corrosion, and scale, mud. and algae fouling. fps. If water is flowing through copper tubing, the velocity This article provides the plant engineer with a detailed should be less than 7.5 fps when it contains suspended look at the problems that can develop and describes the solids or is softened. corrective actions that should be taken to prevent them. Erosion problems on the outside of tubes usually result Mechanical-These failures can take seven different from impingement of wet, high-velocity gases, such as forms: metal erosion, steam or water hammer, vibration, steam. Wet gas impingement is controlled by oversizing thermal fatigue, freeze-up, thermal expansion. and loss of inlet nozzles, or by placing impingement baffles in the cooling water. -
Pitting Corrosion Resistance and Repassivation Behavior of C-Bearing Duplex Stainless Steel
metals Article Pitting Corrosion Resistance and Repassivation Behavior of C-Bearing Duplex Stainless Steel Hanme Yoon 1,2, Heon-Young Ha 2,* , Tae-Ho Lee 2, Sung-Dae Kim 2, Jae Hoon Jang 2 , Joonoh Moon 2 and Namhyun Kang 1,* 1 Department of Materials Science and Engineering, Pusan National University, Busan 46241, Korea 2 Ferrous Alloy Department, Korea Institute of Materials Science, Changwon 51508, Korea * Correspondence: [email protected] (H.-Y.H.); [email protected] (N.K.); Tel.: +82-55-280-3422 (H.-Y.H.); +82-51-510-3274 (N.K.) Received: 24 July 2019; Accepted: 22 August 2019; Published: 26 August 2019 Abstract: The effects of C-substitution for part of the N content, on the pitting corrosion resistance and repassivation tendencies of duplex stainless steels (DSSs) were investigated. For this investigation, normal UNS S32205 containing N only (DSS-N) and the C-substituted DSS (DSS-NC) were fabricated. Microstructural analyses confirmed that the two DSSs had dual-phase microstructures without precipitates, and they possessed similar initial microstructure, including their grain sizes and phase fractions. Polarization and immersion tests performed in concentrated chloride solutions revealed that the DSS-NC was more resistant against stable pitting corrosion and possessed a higher repassivation tendency than the DSS-N. Furthermore, the corrosion pits initiated and propagated to a less corrosion resistant α phase. Polarization tests and corrosion depth measurements conducted in an HCl solution indicated that the DSS-NC exhibited lower galvanic corrosion rate between the α and γ phases than the DSS-N. Therefore, the growth rate of pit embryo was lowered in the DSS-NC, which shifted the potentials for the stable pit initiation and the pit extinction to the higher values. -
Guidelines for Using Perchloric Acid
Guidelines for Using Perchloric Acid Perchloric acid (HClO4) is a strong mineral acid. Under some circumstances it may act as an oxidizer and/or present an explosion hazards. These guidelines present information on how to handle and store perchloric acid safely. Please notify EH&S at 8-8182 if you are using perchloric acid in your laboratory. Using Perchloric Acid (< 72%) at Room Temperature At room temperature, perchloric acid up to concentrations of 72% has properties similar to other strong mineral acids. It is a highly corrosive substance and causes severe burns on contact with the eyes, skin, and mucous membranes. When used under these conditions, perchloric acid reacts as a strong non-oxidizing acid. The following precautions should be taken when using perchloric acid under these conditions: · Substitute with less hazardous chemicals when appropriate. Use dilute solutions (< 60%) whenever possible. · Conduct operations involving cold perchloric acid in a properly functioning chemical fume hood with current EH&S certification. If operations are conducted frequently or in large quantities contact EH&S to determine if a specially designed fume hood dedicated to perchloric acid use is required. · Always use impact-resistant chemical goggles, a face shield, neoprene gloves, and a rubber apron when handling perchloric acid. · When using or storing even dilute perchloric acid solutions avoid contact with strong dehydrating agents (concentrated sulfuric acid, anhydrous phosphorous pentoxide, etc.). These chemicals may concentrate the perchloric acid and make it unstable. · Always transfer perchloric acid over a sink or other suitable containment in order to catch any spills and afford a ready means of cleanup and disposal. -
Fouling Corrosion in Aluminum Heat Exchangers
Chinese Journal of Aeronautics (2015) xxx, xxx–xxx Chinese Society of Aeronautics and Astronautics & Beihang University Chinese Journal of Aeronautics [email protected] www.sciencedirect.com REVIEW ARTICLE Fouling corrosion in aluminum heat exchangers Su Jingxin a,*, Ma Minyu a, Wang Tianjing b, Guo Xiaomei b, Hou Liguo b, Wang Zhiping a a Tianjin Key Laboratory for Civil Aircraft Airworthiness and Maintenance, Civil Aviation University of China, Tianjin 300300, China b Aircraft Maintenance and Engineering Corporation, Beijing Capital International Airport, Beijing 100621, China Received 15 September 2014; revised 30 October 2014; accepted 15 December 2014 KEYWORDS Abstract Fouling deposits on aluminum heat exchanger reduce the heat transfer efficiency and Aluminum; cause corrosion to the apparatus. This study focuses on the corrosive behavior of aluminum cou- EIS; pons covered with a layer of artificial fouling in a humid atmosphere by their weight loss, Tafel Heat exchanger; plots, electrochemical impedance spectroscopy (EIS), and scanning electron microscope (SEM) Pitting corrosion; observations. The results reveal that chloride is one of the major elements found in the fouling Tafel plots which damages the passive film and initiates corrosion. The galvanic corrosion between the metal and the adjacent carbon particles accelerates the corrosive process. Furthermore, the black carbon favors the moisture uptake, and gives the dissolved oxygen greater chance to migrate through the fouling layer and form a continuous diffusive path. The corrosion rate decreasing over time is con- formed to electrochemistry measurements and can be verified by Faraday’s law. The EIS results indicate that the mechanism of corrosion can be interpreted by the pitting corrosion evolution mechanism, and that pitting was observed on the coupons by SEM after corrosive exposure.