Synthesis of Dimethyl Carbonate from Urea and Methanol Catalyzed by the Metallic Compounds at Atmospheric Pressure
Total Page:16
File Type:pdf, Size:1020Kb
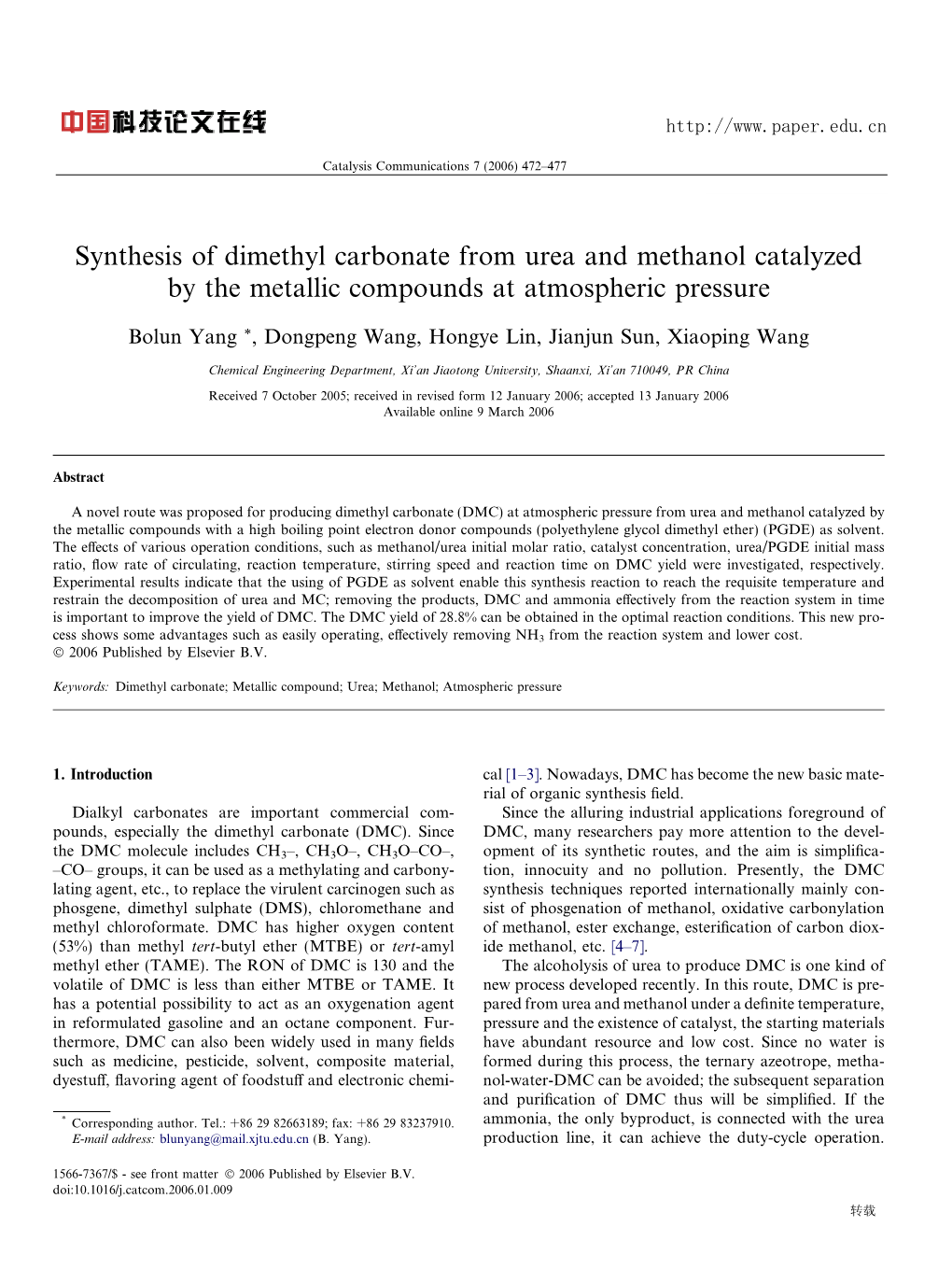
Load more
Recommended publications
-
Synthesis of 2-Substituted Benzimidazole-5-Carbamates As 1109 Potential Antifilarial Agents Siya Ram, Dean S
Jul-Aug 1986 Synthesis of 2-Substituted Benzimidazole-5-carbamates as 1109 Potential Antifilarial Agents Siya Ram, Dean S. Wise and Leroy B. Townsend* Department of Medicinal Chemistry, College of Pharmacy, and Department of Chemistry, The University of Michigan, Ann Arbor, Michigan 48109-1065 Received August 26, 1985 A number of 2,5-disubstituted benzimidazoles have been prepared from 2-benzyl-5-nitrobenzimidazole (5) and 2-p-fluorobenzyl-5-nitrobenzimidazole(6), and evaluated as potential antifilarial agents. None of the compounds prepared in this study have demonstrated any significant antifilarial activity. J. Heterocyclic Chem.. 23, 1109 (1986). A large group of benzimidazole derivatives are highly effective as an anthelmintics [ 11. Among these, meben- dazole (la, methyl 5-benzoylbenzimidazole-2-carbamate) and flubendazole (lb, methyl 5-p-fluorobenzoylbenzimida- 5. x-H zole-Z-carbamate) have demonstrated a broad-spectrum of 6, X-F activity against helminth diseases including filarial infec- 4.. XZH tions [2-51. In our continuing studies to develop new an- b. X=F tifilarial agents [6-81, we have found that two of the metabolites of mebendazole, methyl 5-(c~-hydroxylbenzyl)- 0 I benzimidazole-2-carbamate (lc), and, methyl 5-benzyl- benzimidazole-2-carbamate (la)possess antifilarial activi- ty very similar to that of the parent drug la [9]. Recently, a 9.X:H. R:CH, 10, X= F . R -CH, series of benzothiazoles, typified by structure 2, were 11, X=H. R-C,H, I 7, XzH I c:o taco, I CH,OH OR / reported to possess both micro- and macrofilarial activity against B. pahangi [lo]. -
A Novel Nonphosgene Process for the Synthesis of Methyl Nphenyl
Chinese Journal of Chemistry, 2004.22.782-786 Article A Novel Non-phosgene Process for the Synthesis of Methyl N-Phenyl Carbamate from Methanol and Phenylurea: Effect of Solvent and Catalyst WANG, Xin-Kuia(3/l&S) YAN, Shi-Run'vb(/q@%d) CAO, Yong*(g!F!) FAN, Kang-Nian'pb(3i5@+) HE,He-Yongb(W@B!) KANG, Mao-Qing"(fiit$W) PENG, Shao-Yia(G9B) a Institute of Coal Chemistty Chinese Academy of Sciences, Taiyuan, Shami 030001, China b Shanghai Key Laboratory of Molecular Catalysis and Innovative Materials, Deparfment of Chemistv, Fudan University, Shanghai 200433. China A novel environmentally benign process for the synthesis of methyl N-phenyl carbamate (Mpc) from methanol and phenylurea was studied. Effect of solvent and catalyst on the reaction behavior was investigated. The IR spectra of methanol and phenylurea dissolved in different solvents were also recorded. Compared with use of methanol as both a reactant and a solvent, phenylurea conversion and selectivity to Mpc increased by using toluene, benzene or anisole as a solvent, while phenylurea conversion decreased slightly by using n-octane as a solvent. The phenylurea conversion declined nearly 50% when dimethyl sulfoxide (DMSO) was used as a reaction media, and MPC selec- tivity decreased as well. The catalytic reaction tests showed that a basic catalyst enhanced the selectivity to Mpc while an acidic catalyst promoted the formation of methyl carbamate and aniline. Moderate degree of basicity showed the best catalyhc performance in the cases studied. Keywords methyl N-phenyl carbamate synthesis, phenylurea, phosgene-free, solvent effect, acid-base catalyst Introduction tion of methanol from DMC azeotrope, and DMC is relatively expensive. -
List of Lists
United States Office of Solid Waste EPA 550-B-10-001 Environmental Protection and Emergency Response May 2010 Agency www.epa.gov/emergencies LIST OF LISTS Consolidated List of Chemicals Subject to the Emergency Planning and Community Right- To-Know Act (EPCRA), Comprehensive Environmental Response, Compensation and Liability Act (CERCLA) and Section 112(r) of the Clean Air Act • EPCRA Section 302 Extremely Hazardous Substances • CERCLA Hazardous Substances • EPCRA Section 313 Toxic Chemicals • CAA 112(r) Regulated Chemicals For Accidental Release Prevention Office of Emergency Management This page intentionally left blank. TABLE OF CONTENTS Page Introduction................................................................................................................................................ i List of Lists – Conslidated List of Chemicals (by CAS #) Subject to the Emergency Planning and Community Right-to-Know Act (EPCRA), Comprehensive Environmental Response, Compensation and Liability Act (CERCLA) and Section 112(r) of the Clean Air Act ................................................. 1 Appendix A: Alphabetical Listing of Consolidated List ..................................................................... A-1 Appendix B: Radionuclides Listed Under CERCLA .......................................................................... B-1 Appendix C: RCRA Waste Streams and Unlisted Hazardous Wastes................................................ C-1 This page intentionally left blank. LIST OF LISTS Consolidated List of Chemicals -
NJ Environmental Hazardous Substance List by CAS Number
NJ Community Right to Know Environmental Hazardous Substance (EHS) List in CAS Number Order Reporting Quantity (RQ) Sub. DOT if below CAS Number Substance Name No. No. 500 pounds Haz Waste, N.O.S. (only if EHS reported) liquid 2461 3082 Haz Waste, N.O.S. (only if EHS reported) solid 2461 3077 Organorhodium Complex (PMN-82-147) * + 2611 2811 10 Petroleum Oil4 2651 1270 Substance Samples (only if EHS reported) 3628 Waste Oil4 2851 1270 50-00-0 Formaldehyde * 0946 1198 50-07-7 Mitomycin C * 1307 1851 50-14-6 Ergocalciferol * 2391 1851 50-29-3 DDT 0596 2761 51-03-6 Piperonyl butoxide 3732 51-21-8 Fluorouracil * 1966 1851 51-28-5 2,4-Dinitrophenol 2950 0076 51-75-2 Mechlorethamine * + (S) 1377 2810 10 51-75-2 Nitrogen mustard * + (S) 1377 2810 10 51-79-6 Urethane 1986 51-83-2 Carbachol chloride * 2209 52-68-6 Trichlorfon 1882 2783 52-85-7 Famphur 2915 2588 53-96-3 2-Acetylaminofluorene 0010 54-11-5 Nicotine * + 1349 1654 100 54-62-6 Aminopterin * 2112 2588 55-18-5 N-Nitrosodiethylamine 1404 55-21-0 Benzamide 2895 55-38-9 Fenthion 0916 2902 (O,O-Dimethyl O-[3-methyl-4-(methylthio) phenyl] ester, phosphorothioic acid) 55-63-0 Nitroglycerin 1383 0143 55-91-4 Isofluorphate * + 2500 3018 100 56-23-5 Carbon tetrachloride 0347 1846 56-25-7 Cantharidin * + 2207 100 56-35-9 Bis(tributyltin) oxide 3479 2902 56-38-2 Parathion * + 1459 2783 100 56-72-4 Coumaphos * + 0536 2783 100 57-12-5 Cyanide 0553 1588 57-14-7 1,1-Dimethyl hydrazine * 0761 2382 57-24-9 Strychnine * + 1747 1692 100 57-33-0 Pentobarbital sodium 3726 57-41-0 Phenytoin 1507 57-47-6 Physostigmine * + 2681 2757 100 57-57-8 beta-Propiolactone * 0228 57-64-7 Physostigmine, salicylate (1:1) * + 2682 2757 100 57-74-9 Chlordane * 0361 2762 58-36-6 Phenoxarsine, 10,10'-oxydi- * 2653 1557 58-89-9 Lindane * 1117 2761 59-88-1 Phenylhydrazine hydrochloride * 2659 2572 59-89-2 N-Nitrosomorpholine 1409 60-09-3 4-Aminoazobenzene 0508 1602 60-11-7 4-Dimethylaminoazobenzene (S) 0739 1602 60-11-7 C.I. -
Environmental-Friendly Synthesis of Alkyl Carbamates from Urea and Alcohols with Silica Gel Supported Catalysts
catalysts Article Environmental-Friendly Synthesis of Alkyl Carbamates from Urea and Alcohols with Silica Gel Supported Catalysts Yubo Ma 1,2 , Lei Wang 1,3,*, Xiaodong Yang 4,* and Ronghui Zhang 5 1 School of Chemical Engineering, Chongqing Chemical Industry Vocational College, Chongqing 401220, China; [email protected] 2 Lanzhou Institute of Chemical Physics, Chinese Academy of Sciences, Lanzhou 730000, China 3 Department of Chemistry and Chemical Engineering, Xinjiang University, Urumqi 830011, China 4 Institute of Resources and Environment Science, Xinjiang University, Urumqi 830011, China 5 Guangdong Key Laboratory of Intelligent Transportation System, School of Engineering, Sun Yat-sen University, Guangzhou 510275, China; [email protected] * Correspondence: [email protected] (L.W.); [email protected] (X.Y.) Received: 7 October 2018; Accepted: 19 November 2018; Published: 23 November 2018 Abstract: TiO2/SiO2, Cr2O3-NiO/SiO2, and TiO2-Cr2O3/SiO2 were prepared by the impregnation method for alkyl carbamate synthesis using urea as the carbonyl source. Up to 97.5% methyl carbamate yield, 97% ethyl carbamate yield, and 96% butyl carbamate yield could be achieved, respectively. The catalysts were characterized by ICP-AES, BET, XRD, XPS, NH3-TPD, and EPMA. Catalytic activity investigation revealed that TiO2/SiO2, Cr2O3-NiO/SiO2, and TiO2-Cr2O3/SiO2 were effective catalysts for methyl carbamate (MC), ethyl carbamate (EC), and butyl carbamate (BC), respectively. The recycling tests suggested that these silica gel supported catalyst system is active, stable, and reusable. A total of 96–97% alkyl carbamate (methyl, ethyl, and butyl) could be obtained in a 2 L autoclave, and these data suggested that our catalyst system is relatively easy to scale up. -
Acutely Toxic Chemicals Chemical Class Standard Operating Procedure
Acutely Toxic Chemicals Chemical Class Standard Operating Procedure Acutely Toxic Chemicals (ATCs) H300 H301 H304 H310 H311 H330 H331 H370 H372 Areas with blue text indicate that information must be provided or modified by researcher prior to the SOP approval. This SOP is not a substitute for hands-on training. Print a copy and insert into your laboratory SOP binder. Department: Chemistry Date SOP was written: Monday, October 24, 2016 Date SOP was approved by PI/lab supervisor: Name: R. Sarpong Principal Investigator: Signature: ______________________________ Name: Melissa Hardy/Justin Jurczyk Internal Lab Safety Coordinator or Lab Manager: Lab Phone: 406-696-1225/412-728-1952 Office Phone: 510-642-6312 Name: Melissa Hardy/Justin Jurczyk Emergency Contact: Lab Phone: 406-696-1225/412-728-1952 Latimer Hall Location(s) covered by this SOP: 831,832,834,836,837,838,839,842,844,847,849 1. Purpose This SOP covers the precautions and safe handling procedures for the use of Acutely Toxic Chemicals (ATCs). For a list of ATCs covered by this SOP and their use(s), see “List of Chemicals”. Procedures described in Section 12 apply to all materials covered in this SOP. If you have questions concerning the applicability of any recommendation or requirement listed in this procedure, contact the Principal Investigator/Laboratory Supervisor or the campus Chemical Hygiene Officer at [email protected]. Rev. Date: 09Sept2016 1 Acutely Toxic Chemicals Chemical Class Standard Operating Procedure 2. Acutely Toxic Chemicals Information Acute toxicity refers to those adverse effects occurring following oral or dermal administration of a single dose of a substance, or multiple doses within 24 hours, or an inhalation exposure of 4 hours as defined by the Globally Harmonized System (GHS). -
Ethyl Carbamate 1. Exposure Data
ETHYL CARBAMATE There appears to be no general consensus on a common trivial name for this sub- stance: ethyl carbamate and urethane (or urethan) are both commonly used; however, a preference for ethyl carbamate was noted in the more recent literature. The name urethane is also sometimes applied to high-molecular-weight polyurethanes used as foams, elastomers and coatings. Such products are not made from and do not generate the chemical ethyl carbamate on decomposition. Due to this possible confusion, the term ethyl carbamate has been used in this monograph. 1. exposure Data 1.1 Chemical and physical data 1.1.1. synonyms CAS Registry No.:.51–79–6 synonyms: Carbamic acid ethyl ester; ethylurethan; ethyl urethan; ethyl urethane; urethan; urethane 1.1.2. Chemical.formula.and.relative.molecular.mass NH2COOC2H5 Relative molecular mass: 89.1 1.1.3. Chemical.and.physical.properties.of.the.pure.substance From Budavari (2000) (a) Description: Colourless, almost odourless, columnar crystals or white granular powder; the pH of an aqueous solution is neutral (b) Boiling-point: 182–184.°C (c) Melting-point: 48–50.°C (d) solubility: Dissolves in water (1 g/0.5 mL), ethanol (1 g/0.8 mL), chloroform (1 g/0.9 mL), ether (1 g/1.5 mL), glycerol (1 g/2.5 mL) and olive oil (1 g/32 mL) (e).Volatility: Sublimes readily at 103°C at 54 mm Hg; volatile at room temperature –1281– 1282 IARC MONOGRAPHS VOLUME 96 1.1.4. Technical.products.and.impurities Trade names for ethyl carbamate include Leucothane, Leucethane and Pracarbamine. -
Highly Selective Phosgene-Free Carbamoylation of Aniline By
Article pubs.acs.org/OPRD Highly Selective Phosgene-Free Carbamoylation of Aniline by Dimethyl Carbonate under Continuous-Flow Conditions Sandra Grego, Fabio Arico,̀ and Pietro Tundo* Department of Environmental Sciences, Informatics and Statistics, Ca’ Foscari University of Venice, Dorsoduro 2137, 30123 Venezia, Italia ABSTRACT: Over the last 20 years organic carbamates have found numerous applications in pesticides, fungicides, herbicides, dyes, pharmaceuticals, cosmetics, and as protecting groups and intermediates for polyurethane synthesis. Recently, in order to avoid phosgene-based synthesis of carbamates, many environmentally benign and alternative pathways have been investigated. However, few examples of carbamoylation of aniline in continuous-flow apparatus have been reported. In this work, we report a high-yielding, dimethyl carbonate (DMC)-mediated carbamoylation of aniline in a fixed-bed continuously fed reactor employing basic zinc carbonate as catalyst. Several variables of the system have been investigated (i.e. molar ratio of reagents , flow rate, and reaction temperature) to optimize the operating conditions of the system. 1. INTRODUCTION Recently, several examples of carbamoylation of aniline,9 4,4′-methylenedibenzenamine10 (for the synthesis of methylene Organic carbamates are industrially relevant compounds which, 11 over the last 20 years, have found numerous applications in diphenyl diisocyanate, MDI) and 2,4-diaminotoluene (for the pesticides, fungicides, herbicides, dyes, pharmaceuticals, cos- synthesis of toluene diisocyanate TDI) have been reported by 1 DMC chemistry in the presence of either homogeneous or metics, and as protecting groups. Carbamates can also be ffi readily converted into isocyanates for polyurethane synthesis supported catalysts. An example is the e cient carbamoylation via thermodecomposition.2 of 2,4-diaminotoluene (DAT) by gold-catalyzed phosgene-free Industrially, these compounds are synthesised predominantly synthesis. -
An Improved Method for Determination of Ethyl Carbamate in Korean Traditional Rice Wine I-S Woo1,I-Hkim1, U-J Yun1, S-K Chung1, I-K Rhee2, S-W Choi3 and H-D Park1
Journal of Industrial Microbiology & Biotechnology (2001) 26, 363 – 368 D 2001 Nature Publishing Group 1367-5435/01 $17.00 www.nature.com/jim An improved method for determination of ethyl carbamate in Korean traditional rice wine I-S Woo1,I-HKim1, U-J Yun1, S-K Chung1, I-K Rhee2, S-W Choi3 and H-D Park1 1Department of Food Science and Technology, Kyungpook National University, 1370 Sankyuk, Taegu 702-701, Korea; 2Department of Agricultural Chemistry, Kyungpook National University, 1370 Sankyuk, Taegu 702-701, Korea; 3Department of Food Science and Nutrition, Catholic University of Daegu, Hayang, Kyungpook 712-702, Korea An improved extraction method for ethyl carbamate, a genotoxic and carcinogenic compound found in various fermented foods and beverages, was investigated for its determination in the two most typical Korean traditional rice wines, takju and yakju. When the rice wines were extracted twice with chloroform at 308C for 60 min, the recovery of ethyl carbamate was less than 16%. When they were saturated with NaCl before extraction, the recovery of ethyl carbamate increased to 24.4% in takju and 67.2% in yakju. Adjustment of pH to 9.0 after NaCl saturation in takju resulted in a dramatic increase of recovery to 81.2%, but not in yakju. When the contents of ethyl carbamate and its precursor, urea, in various Korean traditional rice wines were determined, there was no correlation between the two contents. This is due to the fact that storage time is more important than urea content in the formation of ethyl carbamate in rice wine. In addition, its storage at high temperature resulted in a dramatic increase in ethyl carbamate content according to the prolonged storage time, suggesting that storage time and temperature play a key role in the formation of ethyl carbamate in Korean traditional rice wine. -
Synthesis of Dimethyl Carbonate from Urea and Methanol M
Reducing the Carbon Footprint of Fuels and Petrochemicals DGMK Conference October 8 – 10, 2012, Berlin, Germany Synthesis of Dimethyl Carbonate from Urea and Methanol M. Polyakov*, V.N. Kalevaru*, K. Müller**, W. Arlt**, J. Strautmann***, D. Kruse***, A. Martin* *Leibniz Institute for Catalysis at University of Rostock, Germany, **Friedrich-Alexander- University Erlangen-Nuremberg, Germany, ***Creavis Technologies and Innovation, Evonik Industries AG, Marl, Germany This project is funded by the German state of North Rhine-Westphalia (Ministry for innovation, science and research) and co-financed by the EU (European Regional Development Fund) as well as by Evonik Industries AG. Abstract Alcoholation of urea with methanol to produce dimethyl carbonate (DMC) is an interesting approach from both the ecological and economical points of view because the urea synthesis usually occurs by the direct use of carbon dioxide. Literature survey reveals that metal oxide catalysts for instance MgO, ZnO, etc. or polyphosphoric acids are mostly used as catalysts for this reaction. In this contribution, we describe the application of ZnO, MgO, CaO, TiO2, ZrO2 or Al2O3 catalysts for the above mentioned reaction. The catalytic activity of different metal oxides towards DMC synthesis was checked and additionally a comparison of achieved conversions with that of predictions made by thermodynamic calculations was also carried out. The achieved conversions are in good agreement with those of calculated ones. The test results reveal that the reaction pressure and temperature have a strong influence on the formation of DMC. Higher reaction pressure improved the yield of DMC. Among different catalysts investigated, ZnO displayed the best performance. The conversion of urea in most cases is close to 100 % and methyl carbamate MC is the major product of the reaction. -
Hybrid Computational Toxicology Models for Regulatory Risk Assessment Prachi Pradeep Marquette University
Marquette University e-Publications@Marquette Dissertations (2009 -) Dissertations, Theses, and Professional Projects Hybrid Computational Toxicology Models for Regulatory Risk Assessment Prachi Pradeep Marquette University Recommended Citation Pradeep, Prachi, "Hybrid Computational Toxicology Models for Regulatory Risk Assessment" (2015). Dissertations (2009 -). Paper 503. http://epublications.marquette.edu/dissertations_mu/503 HYBRID COMPUTATIONAL TOXICOLOGY MODELS FOR REGULATORY RISK ASSESSMENT by PRACHI PRADEEP A Dissertation submitted to the Faculty of the Graduate School, Marquette University, in Partial Fulfillment of the Requirements for the Degree of Doctor of Philosophy Milwaukee, Wisconsin May 2015 ABSTRACT HYBRID COMPUTATIONAL TOXICOLOGY MODELS FOR REGULATORY RISK ASSESSMENT Prachi Pradeep Marquette University, 2015 Computational toxicology is the development of quantitative structure activity relationship (QSAR) models that relate a quantitative measure of chemical structure to a biological effect. In silico QSAR tools are widely accepted as a faster alternative to time-consuming clinical and animal testing methods for regulatory risk assessment of xenobiotics used in consumer products. However, different QSAR tools often make contrasting predictions for a new xenobiotic and may also vary in their predictive ability for different class of xenobiotics. This makes their use challenging, especially in regulatory applications, where transparency and interpretation of predictions play a crucial role in the development of safety -
Industrial Chemicals, Ashfords Dictionary, Chemical Name Index
2 Chemical name index A A ACA 4-AA ACA AA ACAC AA acamprosate calcium AAA acarbose AABA ACB AADMC 7-ACCA AAEM ACE AAMX acebutolol AAOA aceclidine AAOC aceclofenac AAOT acemetacin AAPP acenaphthene AAPT acenocoumarol 4-ABA acephate ABA acepromazine abacavir acequinocyl ABAH acesulfame-K abamectin acetaldehyde ABFA acetaldehyde ethyl phenethyl diacetal ABL acetaldehyde oxime ABPA acetaldehyde n-propyl phenethyl diacetal ABS acetaldoxime ABS acetal resins O-ABTF acetal resins P-ABTF acetamide ACN acetamidine hydrochloride 7-ACA 5-acetamido-2-aminobenzenesulfonic acid 7-ANCA 6-acetamido-2-aminophenol-4-sulfonic acid Name Index: Ashford’s Dictionary of Industrial Chemicals 3-acetamidoaniline 3-acetamidoaniline acetic acid, s-butyl ester 4-acetamidoaniline acetic acid, calcium salt p-acetamidoanisole acetic acid, chromium salt 4-acetamidobenzenesulfonyl chloride acetic acid, cinnamyl ester 2-acetamidocinnamic acid acetic acid, citronellyl ester 3-acetamido-2-hydroxyaniline-5-sulfonic acid acetic acid, cobalt salt 1-acetamido-7-hydroxynaphthalene acetic acid, decahydro-β-naphthyl ester 8-acetamido-1-hydroxynaphthalene-3,6-disulfonic acid acetic acid, dicyclopentenyl ester 1-acetamido-7-naphthol acetic acid, diethylene glycol monobutyl ether ester 4-acetamidonitrobenzene acetic acid, 2-ethoxyethyl ester p-acetamidophenol acetic acid, ethoxypropyl ester 3-acetamidopropylsulfonic acid, calcium salt acetic acid, ethyl diglycol ester 5-acetamido-2,4,6-triiodo-N-methylisophthalamic acid acetic acid, ethylene glycol diester 4-acetamido-2-ethoxybenzoic