Manned Spacecraft Center INTRODUCTION It I
Total Page:16
File Type:pdf, Size:1020Kb
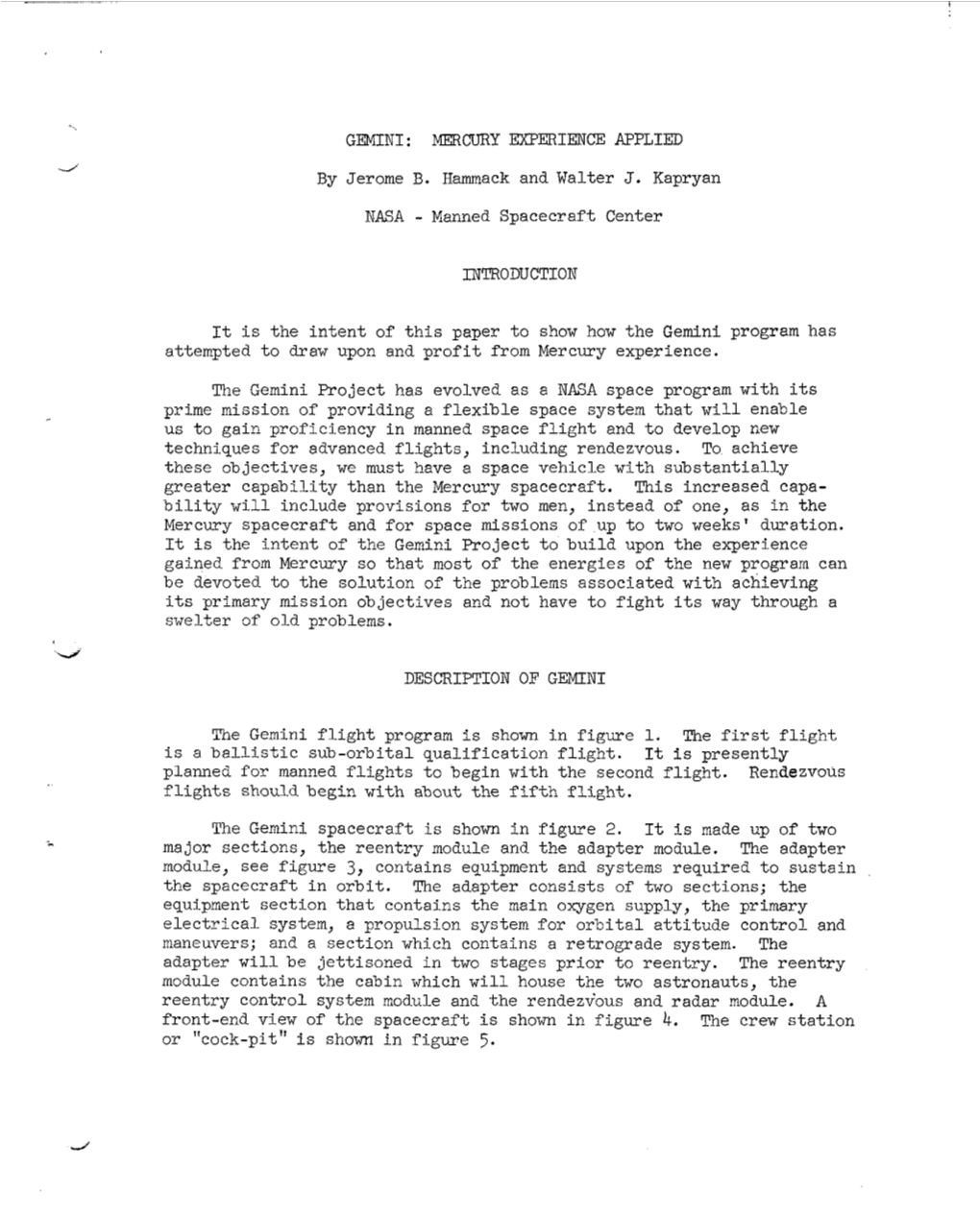
Load more
Recommended publications
-
The SKYLON Spaceplane
The SKYLON Spaceplane Borg K.⇤ and Matula E.⇤ University of Colorado, Boulder, CO, 80309, USA This report outlines the major technical aspects of the SKYLON spaceplane as a final project for the ASEN 5053 class. The SKYLON spaceplane is designed as a single stage to orbit vehicle capable of lifting 15 mT to LEO from a 5.5 km runway and returning to land at the same location. It is powered by a unique engine design that combines an air- breathing and rocket mode into a single engine. This is achieved through the use of a novel lightweight heat exchanger that has been demonstrated on a reduced scale. The program has received funding from the UK government and ESA to build a full scale prototype of the engine as it’s next step. The project is technically feasible but will need to overcome some manufacturing issues and high start-up costs. This report is not intended for publication or commercial use. Nomenclature SSTO Single Stage To Orbit REL Reaction Engines Ltd UK United Kingdom LEO Low Earth Orbit SABRE Synergetic Air-Breathing Rocket Engine SOMA SKYLON Orbital Maneuvering Assembly HOTOL Horizontal Take-O↵and Landing NASP National Aerospace Program GT OW Gross Take-O↵Weight MECO Main Engine Cut-O↵ LACE Liquid Air Cooled Engine RCS Reaction Control System MLI Multi-Layer Insulation mT Tonne I. Introduction The SKYLON spaceplane is a single stage to orbit concept vehicle being developed by Reaction Engines Ltd in the United Kingdom. It is designed to take o↵and land on a runway delivering 15 mT of payload into LEO, in the current D-1 configuration. -
Initial Investigation of Reaction Control System Design on Spacecraft Handling Qualities for Earth Orbit Docking
Initial Investigation of Reaction Control System Design on Spacecraft Handling Qualities for Earth Orbit Docking Randall E. Bailey1 E. Bruce Jackson,2 and Kenneth H. Goodrich 3 NASA Langley Research Center, Hampton, Virginia, 23681 W. Al Ragsdale4, and Jason Neuhaus 5 Unisys Corporation, Hampton, VA, 23681 and Jim Barnes6 ARINC, Hampton, VA, 23666 A program of research, development, test, and evaluation is planned for the development of Spacecraft Handling Qualities guidelines. In this first experiment, the effects of Reaction Control System design characteristics and rotational control laws were evaluated during simulated proximity operations and docking. Also, the influence of piloting demands resulting from varying closure rates was assessed. The pilot-in-the-loop simulation results showed that significantly different spacecraft handling qualities result from the design of the Reaction Control System. In particular, cross-coupling between translational and rotational motions significantly affected handling qualities as reflected by Cooper-Harper pilot ratings and pilot workload, as reflected by Task-Load Index ratings. This influence is masked – but only slightly – by the rotational control system mode. While rotational control augmentation using Rate Command Attitude Hold can reduce the workload (principally, physical workload) created by cross-coupling, the handling qualities are not significantly improved. The attitude and rate deadbands of the RCAH introduced significant mental workload and control compensation to evaluate when deadband firings would occur, assess their impact on docking performance, and apply control inputs to mitigate that impact. I. Introduction Handling qualities embody “those qualities or characteristics of an aircraft that govern the ease and precision with which a pilot is able to perform the tasks required in support of an aircraft role."1 These same qualities are as critical, if not more so, in the operation of spacecraft. -
NASA Ares I Launch Vehicle Roll and Reaction Control Systems Design Status
https://ntrs.nasa.gov/search.jsp?R=20090037058 2019-08-30T08:10:16+00:00Z NASA Ares I Launch Vehicle Roll and Reaction Control Systems Design Status 1 Adam Butt and Chris G. Popp2 NASA George C. Marshall Space Flight Center, Huntsville, AL, 35812 Hank M. Pitts3 Qualis Corporation, ESTS Group, Huntsville, AL, 35812 and David J. Sharp4 Jacobs Engineering, ESTS Group, Huntsville, AL, 35812 This paper provides an update of design status following the Preliminary Design Review of NASA’s Ares I First Stage Roll and Upper Stage Reaction Control Systems. The Ares I launch vehicle is the selected design, chosen to return humans to the moon, mars, and beyond. It consists of a first stage five segment solid rocket booster and an upper stage liquid bi-propellant J-2X engine. Similar to many launch vehicles, the Ares I has reaction control systems used to provide the vehicle with three degrees of freedom stabilization during the mission. During launch, the First Stage Roll Control System will provide the Ares I with the ability to counteract induced roll torque. After first stage booster separation, the Upper Stage Reaction Control System will provide the upper stage element with three degrees of freedom control as needed. Trade studies and design assessments conducted on the roll and reaction control systems include: propellant selection, thruster arrangement, pressurization system configuration, system component trades, and more. Since successful completion of the Preliminary Design Review, work has progressed towards the Critical Design Review with accomplishments made in the following areas: pressurant/propellant tanks, thruster assemblies, component configurations, as well as thruster module designs, and waterhammer mitigation approaches. -
Design and Performance Evaluations of a LO2/Methane Reaction Control Engine" (2016)
University of Texas at El Paso DigitalCommons@UTEP Open Access Theses & Dissertations 2016-01-01 Design and Performance Evaluations of a LO2/ Methane Reaction Control Engine Aaron Johnson University of Texas at El Paso, [email protected] Follow this and additional works at: https://digitalcommons.utep.edu/open_etd Part of the Aerospace Engineering Commons, and the Mechanical Engineering Commons Recommended Citation Johnson, Aaron, "Design and Performance Evaluations of a LO2/Methane Reaction Control Engine" (2016). Open Access Theses & Dissertations. 671. https://digitalcommons.utep.edu/open_etd/671 This is brought to you for free and open access by DigitalCommons@UTEP. It has been accepted for inclusion in Open Access Theses & Dissertations by an authorized administrator of DigitalCommons@UTEP. For more information, please contact [email protected]. DESIGN AND PERFORMANCE EVALUATIONS OF A LO2/METHANE REACTION CONTROL ENGINE AARON JOHNSON Master’s Program in Mechanical Engineering APPROVED: Ahsan Choudhuri, Ph.D., Chair Norman Love Jr., Ph.D. Tzu-Liang (Bill) Tseng, Ph.D., CMfgE Charles Ambler, Ph.D. Dean of the Graduate School Copyright © by Aaron Johnson 2016 Dedication I would like to dedicate this thesis to my family and friends all of whom have supported me unconditionally in this crazy journey through life. CS. DESIGN AND PERFORMANCE EVALUATIONS OF A LO2/METHANE REACTION CONTROL ENGINE by AARON JOHNSON, B.S. Mechanical Engineering THESIS Presented to the Faculty of the Graduate School of The University of Texas at El Paso in Partial Fulfillment of the Requirements for the Degree of MASTER OF SCIENCE Department of Mechanical Engineering THE UNIVERSITY OF TEXAS AT EL PASO December 2016 Acknowledgements I would like to thank Dr. -
Space Shuttle Main Engine Orientation
BC98-04 Space Transportation System Training Data Space Shuttle Main Engine Orientation June 1998 Use this data for training purposes only Rocketdyne Propulsion & Power BOEING PROPRIETARY FORWARD This manual is the supporting handout material to a lecture presentation on the Space Shuttle Main Engine called the Abbreviated SSME Orientation Course. This course is a technically oriented discussion of the SSME, designed for personnel at any level who support SSME activities directly or indirectly. This manual is updated and improved as necessary by Betty McLaughlin. To request copies, or obtain information on classes, call Lori Circle at Rocketdyne (818) 586-2213 BOEING PROPRIETARY 1684-1a.ppt i BOEING PROPRIETARY TABLE OF CONTENT Acronyms and Abbreviations............................. v Low-Pressure Fuel Turbopump............................ 56 Shuttle Propulsion System................................. 2 HPOTP Pump Section............................................ 60 SSME Introduction............................................... 4 HPOTP Turbine Section......................................... 62 SSME Highlights................................................... 6 HPOTP Shaft Seals................................................. 64 Gimbal Bearing.................................................... 10 HPFTP Pump Section............................................ 68 Flexible Joints...................................................... 14 HPFTP Turbine Section......................................... 70 Powerhead........................................................... -
Development of the Thermal Control System of the European Service Module of the Multi-Purpose Crew Vehicle
47th International Conference on Environmental Systems ICES-2017-355 16-20 July 2017, Charleston, South Carolina Development of the thermal control system of the European Service Module of the Multi-Purpose Crew Vehicle Patrick Oger.1 Airbus Safran Launchers, Les Mureaux, 78133, France Giovanni Loddoni2, Paolo Vaccaneo3 Thales Alenia Space, Turin, , 10146, Italy and David Schwaller4 ESA/ESTEC, Noordwijk, 2201AZ, The Netherlands The Orion Multi-Purpose Crew Vehicle (Orion MPCV) is a spacecraft intended to carry a crew of up to four astronauts to destinations at or beyond low Earth orbit (LEO). Under an agreement between NASA and ESA, ratified in December 2012, the new American Orion MPCV will be powered by a European Service Module (ESM), this latest based on the design and experience of the ATV (Automated Transfer Vehicle), the supply spacecraft for the International Space Station (ISS). The MPCV ESM will provide the Orion vehicle with propulsion, electrical power and storage of consumables (water, oxygen and nitrogen) for the mission, it will also ensure the thermal control of the whole vehicle by collecting and rejecting heat generated by the Crew Module (CM) toward space. The Thermal Control System (TCS) of the MPCV ESM is composed of two parts: the Active TCS (ATCS) based on fluid loops that collect heat from the CM (Crew Module) and from the ESM dissipative items and reject it toward space via body mounted radiators and the Passive TCS (PTCS) composed of a set of heater lines, Multi-Layer Insulations (MLI) and Hot Thermal Protection to perform the thermal control of the ESM and protect it against external environment. -
Apollo-Soyuz Test Project
--.I m ...ir,,.= The document_-contains materials on the Soyuz-Apollo test and consists of two parts, prepared by the USSR and USA sides res- pectively. Both parts outline the purposes and program of the mission, the spacecraft design, the flight plan and information on Joint and unilateral scientific experiments. Brief biographies of the cosmonauts and astronauts, the Joint mission crew members_ are also presented. The document covers technical support activities providing mission control and gives information about the ASTP Soviet and American leaders. As the USSR and USA parts of the document have been prepared independently, there might be duplication in the sections dealing with the Joint activities. The document is intended for press representatives and various mass information means. CONTENTS Page I.0 INTRODUCTION ....................................... 10 1.1 Background ......................................... I0 1,2 Apollo-Soyuz joint test project objectives .......... 13 2.0 COMPATIBILITY PROBLEMS ................... ......... • 15 2.1 Spacecraft compatibility conditions and principal solutions accepted for Apollo-Ssyuz Test Mission .... 15 2.2 Compatibility of ground flight control personnel ... 18 2_3 Methodological compatibility ....................... 20 3.0 SOYUZ SPACECRAFT ................................... 22 3.1 PurPose. Brief data on Soyuz spacecraft flights .... 22 3.2 Soyuz spacecraft description ....................... 25 3.2.1 General description of the Soyuz spacecraft.. 25 Main characteristics ........................ -
X-34 High Pressure Nitrogen Reaction Control System Design and Analysis
Proceedings of the Eighth Annua Therma uids Analysis Workshop Spacecraft Ana ysis and Design X-34 HIGH PRESSURE NITROGEN REACTION CONTROL SYSTEM DESIGN AND ANALYSIS BRIAN A. WINTERS, P.E.* TREY WALTERS, P.E.† Orbital Sciences Corporation Applied Flow Technology Dulles, Virginia Woodland Park, Colorado by Orbital’s L-1011 carrier aircraft, can perform Abstract missions that reach Mach 8 and 250,000 feet, land The X-34 program is developing a reusable launch horizontally on a conventional runway, and can quickly vehicle that will be capable of reaching Mach 8 and be prepared for subsequent flights using aircraft-style 250,000 feet. The X-34 vehicle will carry a 5,000 psia turnaround operations. A high operational rate of up to cold gas nitrogen reaction control system that will be 25 flights per year, with rapid integration and low used for augmentation of vehicle control at high altitudes operating cost per flight is achieved through a simple, and velocities. The nitrogen is regulated to 1,100 psia maintainable design. and directed to 10 thrusters oriented to provide control capability about all three axes. Orbital Sciences Orbital Sciences Corporation (Orbital) is the prime Corporation of Dulles, Virginia has the responsibility for contractor responsible for the design, development, design and performance verification of the system as fabrication, integration, and flight testing of the X-34 test prime contractor for the X-34 program. Applied Flow bed demonstration vehicle. This baseline flight test Technology’s Arrow compressible network analysis program (BFTP) includes two flights to verify the software was evaluated, selected, and purchased for integration with the carrier aircraft, performance of the analyzing the reaction control system performance. -
Greenization of RCS (Reaction Control System) for Spacecrafts
Mitsubishi Heavy Industries Technical Review Vol. 48 No. 4 (December 2011) 44 The “Greening” of Spacecraft Reaction Control Systems NOBUHIKO TANAKA*1 TETSUYA MATSUO*1 KATSUMI FURUKAWA*2 MITSURU NISHIDA*3 SHIGENORI SUEMORI*3 AKINORI YASUTAKE*4 Recently, higher performance (i.e., reduction of propellant consumption), operability improvement/safer handling (i.e., lower toxicity) and cost reduction are required for thrusters used for the orbital maneuvering and attitude control of spacecraft such as rockets, artificial satellites and space probes. For this reason, reaction control systems (RCSs) which use lower toxicity propellants called “Green Propellants” instead of the conventional toxic propellant hydrazine are attracting attention as next generation fuels. Mitsubishi Heavy Industries, Ltd. (MHI) has continued the development of monopropellant thrusters that use SHP, a green hydroxylammonium nitrate (HAN)-based propellant that has the potential to achieve higher performance than hydrazine. This report describes the results of the evaluation of system advantages and safety (detonability), as well as the firing test for evaluating lifetime. |1. Introduction Spacecraft such as rockets, artificial satellites, and space probes have small rocket engines (thrusters) for orbital maneuvering and attitude control. These thrusters produce thrust using the reaction force by exhausting gas. As shown in Figure 1, for supplying propellants to thrusters, tanks, valves and heat control materials are necessary, which are assembled to form the Reaction Control System (RCS). Figure 1 Reaction control system *1 Maritime & Space Systems Department, Aerospace Systems *2 Administrator, Maritime & Space Systems Department, Aerospace Systems *3 Nagasaki Research & Development Center, Technology & Innovation Headquarters *4 Research Manager, Nagasaki Research & Development Center, Technology & Innovation Headquarters Mitsubishi Heavy Industries Technical Review Vol. -
International Space Station Attitude Motion Associated with Flywheel Energy Storage
International Space Station Attitude Motion Associated With Flywheel Energy Storage Carlos M. Roithmayr NASA Langley Research Center, Hampton, Virginia, 23681 757-864-6778; [email protected] Abstract. Flywheels can exert torque that alters the Station's attitude motion, either intentionally or unintentionally. A design is presented for a once planned experiment to contribute torque for Station attitude control, while storing or discharging energy. Two contingencies are studied: the abrupt stop of one rotor while another rotor continues to spin at high speed, and energy storage performed with one rotor instead of a counter rotating pair. Finally, the possible advantages to attitude control offered by a system of ninety-six flywheels are discussed. INTRODUCTION The International Space Station (ISS) Payloads Office, through Johnson Space Center's Engineering and Research Technology Program, has for the past two years funded a program at Glenn Research Center to develop flywheel energy storage technology. What began as an experiment planned to demonstrate integrated energy storage and attitude control has evolved into a project that may add significantly to the capacity for energy storage onboard the Station, and reduce or eliminate the cost and time required to replace chemical batteries. The resulting technology could be applied by the industrial participants of this program in future spacecraft, or in a wide variety of other areas. Energy storage and attitude control are accomplished with two separate devices on present spacecraft. Batteries are typ- ically used to store and supply electrical energy produced by photovoltaic cells; however, batteries are quite massive, and battery life often limits the life of a spacecraft. -
LYNDON B. JOHNSON SPACE CENTER Houlton, Texaj December 1975 JSC-10638
( JSC-10638 APOLLO SOYUZ MISSION ANOMALY REPORT NO. 1 TOXIC GAS ENTERED CABIN DURING EARTH LANDING SEQUENCE I National Aeronautics and Space Adminutration LYNDON B. JOHNSON SPACE CENTER Houlton, TexaJ December 1975 JSC-10638 APOLLO SOYUZ MISSION Anomaly Report No. 1 TOXIC GAS ENTERED CABIN DURING EARTH LANDING SEQUENCE PREPARED BY Mi&sion Evaluation Team APPROVED BY NATIONAL AERONAUTICS AND SPACE ADMINISTRATION LYNDON B. JOHNSON SPACE CENTER HOUSTON, TEXAS December 1975 TOXIC GAS ENTERED CABIN DURING EARTH LANDING SEQUENCE STATEMENT Toxic gas entered the cabin during repressurization for 30 seconds from manual deployment of the drogue parachutes at 18 550 feet (5650 m) t~ disabling of the reaction control system at 9600 feet (2925 m). EARTH LANDING SEQUENCE Nominal Sequence Nominal operation of the Apollo earth landing sequence for the Apollo Soyuz Test Project was for the crew to arm the sequencer ?Yrotechnic buses at 50 000 feet (15 240m) altitude. At 30 000 feet (9145 m), the crew was to arm the automatic earth landing system (ELS) sequencer by positioning the two ELS switches to LOGIC and AUTO. As shown in figure 1, arming the earth landing system applies sense power to the 24 000-foot (7315-m) bare switches. When the 24 000-foot baroswitches close, the sense power latches the ELS activate relay. This applies power to the reaction control system (RCS) disable relay and the 0.4-, 2.0-, and 14.0-second timers for the apex cover (forward heat shield), drogue parachutes, and main parachutes, respectively. Timeout of the 14-second timer applies power to the 10 000- foot (3050-m) baroswitchea. -
Direct Flight Apollo
](68 90648 _'_ ___EPORTNO.9182._ 31OCTOBER1962 I T FLI HT LL (,_AS A-CI- 155617) STUD ¥. VCLUME 2: APPL]C_TICNS (McDcnnell / MCDONNELL L.d DIRECT FLIGHT APOLLO STUDY vo_.oM_,, ERRATA St___"T W Page 1-15 2nd line from bottom, "VHF transmitter/" should be "UEF transmitter/" p Page 1-16 _th line, "VEF-DSIF" should be "L_-DSIF" Page 2-2 Figure 2-1, replace with new figure transmitted herein p Page 2-5 Figure 2-4, lower right hand corner of page, "52-79702 - Battery (3 req'd.)" should be "52-79702-5 Battery (3 req'd.)" Page 2-7 Figure 2-5, "MA_" and "SQUIB" battery callouts should be the same as Page 2-8, Figure 2-6 Page R-15 Section 2.1.4, delete item C • Page 3-33 Figure 3-26, lower right hand sketch, ".84 min." should be ".80 mln." w m m MCDONNELL W iv U. _ J + J L J . - " i 1 I • i _REPORTNO.9182_ 310C10BER1962 DIRECT FLIGHT APOLLO STU _G emini SpacecraftVolume 11:Applications CONTROL NO. C-72079 COPY NO. 'Y_ THIS DOCU_S INF'ORMATION AFF_ THE NATIONAL DEFENSE OF THE UIq_I_TATES _Tj_P_E MEANING OF THE ESPIONAGE LAW_ TI_ECTIONS 793 AND 794. THE TRANSMISSION OR_F WHICH IN ANY MANNER DO_ LS: TO AN UNA_I'D PERS_ LAW. MCDONNELL AIRCRAFT CORPORATION LAMBERT -- ST. LOUIS MUNICIPAL AIRPORT. BOX 516. ST. LOUIS 66. MO. A m.T. m2 DIRECT FLIGHT APOLLO STUDY vo,oM_, 310CmE,,.2 TABLE OF CONTENTS PAGE ITEM NUMBER INTRODUCTION . ................ 1-1 lo SUMMARY i 2 i.i Study Ground Rules ..........