Optimal Control of Formula One Car Energy Recovery Systems
Total Page:16
File Type:pdf, Size:1020Kb
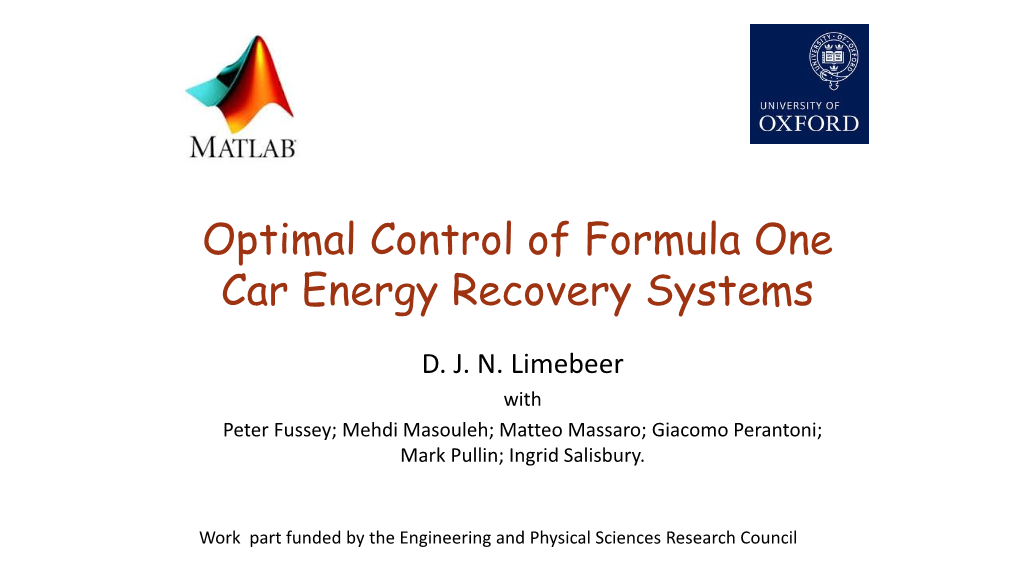
Load more
Recommended publications
-
Formula 1 Race Car Performance Improvement by Optimization of the Aerodynamic Relationship Between the Front and Rear Wings
The Pennsylvania State University The Graduate School College of Engineering FORMULA 1 RACE CAR PERFORMANCE IMPROVEMENT BY OPTIMIZATION OF THE AERODYNAMIC RELATIONSHIP BETWEEN THE FRONT AND REAR WINGS A Thesis in Aerospace Engineering by Unmukt Rajeev Bhatnagar © 2014 Unmukt Rajeev Bhatnagar Submitted in Partial Fulfillment of the Requirements for the Degree of Master of Science December 2014 The thesis of Unmukt R. Bhatnagar was reviewed and approved* by the following: Mark D. Maughmer Professor of Aerospace Engineering Thesis Adviser Sven Schmitz Assistant Professor of Aerospace Engineering George A. Lesieutre Professor of Aerospace Engineering Head of the Department of Aerospace Engineering *Signatures are on file in the Graduate School ii Abstract The sport of Formula 1 (F1) has been a proving ground for race fanatics and engineers for more than half a century. With every driver wanting to go faster and beat the previous best time, research and innovation in engineering of the car is really essential. Although higher speeds are the main criterion for determining the Formula 1 car’s aerodynamic setup, post the San Marino Grand Prix of 1994, the engineering research and development has also targeted for driver’s safety. The governing body of Formula 1, i.e. Fédération Internationale de l'Automobile (FIA) has made significant rule changes since this time, primarily targeting car safety and speed. Aerodynamic performance of a F1 car is currently one of the vital aspects of performance gain, as marginal gains are obtained due to engine and mechanical changes to the car. Thus, it has become the key to success in this sport, resulting in teams spending millions of dollars on research and development in this sector each year. -
Davide Signed with Alpine F1 Team in January 2021 As
ALPINE F1 TEAM PRESS PACK Already recognised for its records It is part of Groupe Renault’s Luca De Meo, CEO Groupe That’s the beauty of racing as In September 2020, Luca De Meo, and successes in endurance strategy to clearly position Renault: “It is a true joy to see a works team in Formula 1. announced the creation of Alpine F1 Team, and rallying, the Alpine name each of its brands. For Alpine, the powerful, vibrant Alpine We will compete against the naturally finds its place in the this is a key step to accelerate name on a Formula One car. biggest names, for spectacular a renaissance of Groupe Renault’s F1 team, high standards, prestige and the development and influence New colours, new managing car races made and followed one of F1’s most historic and successful. performance of Formula 1. The of the brand. Renault remains team, ambitious plans: it’s a new by cheering enthusiasts. I can’t Alpine brand, a symbol of sporting an integral part of the team, beginning, building on a 40-year wait for the season to start.” prowess, elegance and agility, with the hybrid power unit history. We’ll combine Alpine’s will be designated to the chassis retaining its Renault E-Tech values of authenticity, elegance and pay tribute to the expertise moniker and unique expertise and audacity with our in-house that gave birth to the A110. in hybrid powertrains. engineering & chassis expertise. ALPINE F1 TEAM | PRESS PACK | 2021 Alpine Today and Tomorrow As part of Groupe Renault’s strategic plan ‘Renaulution’, Alpine unveiled its long-term plans to position the brand at the forefront of Groupe Renault’s innovation. -
2021 Formula 1 Technical Regulations
2021 FORMULA 1 TECHNICAL REGULATIONS PUBLISHED ON 16 DECEMBER 2020 Issue 7 Convention: Black text: based on 2020 Technical Regulations – Issue 5 (19/06/2020) Pink text: changes for 2021 approved by the WMSC on 19/06/2020, 04/09/2020, 09/10/2020, 30/10/2020 and 16/12/2020 Green text: comments / not regulatory CONTENTS: Pages ARTICLE 1: DEFINITIONS 8 1.1 Formula One Car 1.2 Automobile 1.3 Land Vehicle 1.4 Bodywork 1.5 Wheel 1.6 Complete wheel 1.7 Automobile Make 1.8 Event 1.9 Weight 1.10 Cubic capacity 1.11 Pressure charging 1.12 Cockpit 1.13 Sprung suspension 1.14 Survival cell 1.15 Camera 1.16 Camera housing 1.17 Cockpit padding 1.18 Brake caliper 1.19 Electronically controlled 1.20 Open and closed sections 1.21 Power train 1.22 Power unit 1.23 Engine 1.24 Energy Recovery System (ERS) 1.25 Motor Generator Unit - Kinetic (MGU-K) 2021 Formula 1 Technical Regulations 1 16 December 2020 © 2020 Fédération Internationale de l’Automobile Issue 7 1.26 Motor Generator Unit - Heat (MGU-H) 1.27 Energy Store (ES) 1.28 Compressor inlet 1.29 Compressor outlet 1.30 Combustion chamber 1.31 Fuel injector 1.32 Auxiliary Oil Tank (AOT) 1.33 Engine exhaust system 1.34 Turbocharger (TC) 1.35 In-cylinder pressure sensor 1.36 High pressure Fuel pump 1.37 Fuel Flow meter 1.38 Ignition Coil 1.39 Ancillaries 1.40 Engine Plenum 1.41 ES cells 1.42 DC-DC Converter 1.43 Power Unit Control Electronics (PU-CE) 1.44 Valve Stem ARTICLE 2: GENERAL PRINCIPLES 13 2.1 Role of the FIA 2.2 Applicable regulations and amendments to the regulations 2.3 Dangerous construction 2.4 -
Formula One Race Strategy Mclaren Racing Limited Sports Technology Mclaren Is a Registered Trademark of Mclaren Racing Limited
Formula One Race Strategy McLaren Racing Limited Sports Technology McLaren is a registered trademark of McLaren Racing Limited INTRODUCTION We will solve this problem in three steps as follows: Step 1: How long will it take to reach the first pit stop? From the scenario, we have the following information: Fuel Consumption C = 3 kg/lap How much slower our lap E = 0.03 sec/ time is for every kg of fuel on (lap kg) board (also called the “weight effect”) Time to complete a lap with 1 t1 = 100.045 lap of fuel on board sec Figure 1: A Vodafone McLaren Mercedes driven by Lewis Hamilton Using this, we can calculate how much slower the McLaren Racing, the company behind Vodafone car goes for every lap’s worth of fuel we have on McLaren Mercedes, operates in the highly board. We call this the Fuel Laps Weight Effect competitive and technological environment of (W ) and this is calculated as follows: Formula One. McLaren Racing comprises a W = Fuel Laps Weight Effect multitude of administrative and engineering = Fuel Consumptio n ´ Weight Effect departments, ranging from vehicle design and aerodynamics, to materials science and the paint = 3 ´ 0.03 = 0 .0 9 sec/(lap lap of fuel) shop. As one of the most successful teams in the The extra time taken to complete a lap when we history of Formula One, McLaren has won more have fuel on board can be calculated as follows: Grand Prix than any other Constructor since it Extra time taken to complete lap due to fuel on board entered the sport in 1966. -
Investigation of Turbulence Created by Formula One™ Cars with the Aid of Numerical Fluid Dynamics and Optimization of Overtaking Potential
Investigation of Turbulence Created by Formula One™ Cars with the Aid of Numerical Fluid Dynamics and Optimization of Overtaking Potential Milad Mafi Competence Centre, transtec AG, Tübingen, Germany Summary Formula One™ is the most successful racing series in the world. And with over 25 million television viewers per race it attracts many prominent sponsors who have invested over a billion euros in it, making them indispensable for Formula One™’s survival. In the last ten years the numbers of overtaking maneuvers in Formula One™ races have become rarer and rarer – changes in position now take place in the pit stop or as a result of defective parts. This has caused races to be less eventful, as reflected in falling TV viewing figures. Many sponsors have withdrawn their support and, should this trend continue, it would mean the end of Formula One™. The reason for the decreasing number of overtaking maneuvers, which were quite common in the nineteen-eighties, can be found in the aerodynamics of Formula One™ racing cars: During the age of turbo motors road holding, in racing jargon “grip” which is produced by the tires, the aerodynamics created down force resulting in extra grip. Like the tires, the proper functioning of which is restricted to a certain temperature range, the aerodynamics of a racing car depends on several factors, including the intensity of air turbulence. Laminar air flow is the basis for the efficient functioning of the wings and bodywork. The aerodynamics of modern Formula One™ cars produces a down force of roughly 25000 N, which corresponds to a gravitational force of 2.5 metric tons. -
Design of Formula One Racing Car
International Journal of Engineering Research & Technology (IJERT) ISSN: 2278-0181 Vol. 4 Issue 04, April-2015 Design of Formula One Racing Car Triya Nanalal Vadgama Mr. Arpit Patel, Student Assistant Professor Department of Aeronautical Engineering Department of Aeronautical Engineering Sardar Vallabhbhai Patel Institute of Technology, Vasad Sardar Vallabhbhai Patel Institute of Technology, Vasad Gujarat Technological University, Ahmedabad, India Gujarat Technological University, Ahmedabad, India Dr. Dipali Thakkar, Head & Professor Department of Aeronautical Engineering Sardar Vallabhbhai Patel Institute of Technology, Vasad Gujarat Technological University, Ahmedabad, India Abstract- A modern Formula One (F1) Racing Car has almost as affect the airflow, and placing a badge on a crucial element much in common with an aircraft as it does with an ordinary could produce a two-to-three percent difference in air road car. Aerodynamics has become a key to success in the sport pressure. Disrupted air flow can cause turbulence, which will and teams spend millions of dollars on research and produce drag to slow the car. F1 cars often have small development in the field each year for improving performance. 'winglets' before the rear wing, which 'clean up' complex air The aerodynamic designer has two primary concerns : i. the creation of downforce, to help push the car’s tyres flow in order to maximize down force. The scope of this onto the track and improve cornering forces, project includes : ii. to minimise the drag that occurs due to turbulence and i. Designing of F1 three-dimensional CAD model acts to slow down the car. using CATIA V5 R21 software. In this project, a Formula One race car will be designed using the CAD software CATIA V5R20. -
The Aerodynamics of a Formula One Car Front Cascade Wing During
Journal of Advanced Research in Fluid Mechanics and Thermal Sciences 53, Issue 1 (2019) 53-60 Journal of Advanced Research in Fluid Mechanics and Thermal Sciences Journal homepage: www.akademiabaru.com/arfmts.html ISSN: 2289-7879 Aerodynamics of a Formula One Car Front Cascade Wing Open Access during Cornering Ahmed T. Raheem1, Azwan Sapit1,*, Akmal Nizam Mohammed2 1 Faculty of Mechanical & Manufacturing Engineering, Universiti Tun Hussein Onn Malaysia, 86400 Parit Raja, Batu Pahat, Johor, Malaysia 2 Centre for Energy and Industrial Environment Studies, Universiti Tun Hussein Onn Malaysia, 86400 Parit Raja, Batu Pahat, Johor, Malaysia ARTICLE INFO ABSTRACT Article history: The design for the aerodynamics of front wing based on cornering angle of a Formula- Received 10 October 2018 One car plays an important role on the car's performance. The cascade elements above Received in revised form 21 November 2018 the main front wing is enhanced with new and the deep winglets that manage the Accepted 5 December 2018 airflow for the rest of the car. The front wing cascades are attached with end plates at Available online 8 January 2019 the extremities of the front wing to reduce turbulence. However, when the car turns, the airflow behaviour on these cascades wings changes significantly. This paper presents the aerodynamic characteristics resulting from the cornering forces subjected on Formula One styled cascade wings. The study attempts to predict the down-force and drag-force acting on the front wing under the effect of airflow change in this area. In order to investigate the airflow behaviour, computational fluid dynamics (specifically the ANSYS software) was used to simulate selected cases with specific surface definitions and boundary conditions defined in a 3D domain. -
Materials in the BMW Sauber Formula 1 Race Car, Which Appeared in the November 2008 Issue of Advanced Materials & Processes
Advanced Materials & Processes® Web Exclusive Copyright © 2008 ASM International® November 2008 All rights reserved. DOI: 10.1361/amp1108bmw www.asminternational.org This article was the basis for Materials in the BMW Sauber Formula 1 Race Car, which appeared in the November 2008 issue of Advanced Materials & Processes. This is the original manuscript submitted by the authors. It contains much more information than was possible to include in the magazine. Materials in the BMW Sauber Formula 1 Race Car BMW Team Zurich, Switzerland The F1 regulations inevitably play a central role in the construction of a new car. The two key changes to the rulebook for 2008 were the introduction of a standard electronics unit (SECU) and the new running time stipulation for the gearbox, which is now required to survive four consecutive grands prix. The development of the chassis was particularly hard hit by the incorporation of the SECU, with the traction control and engine braking control systems among the casualties of the new standard unit. This had the effect of making the car considerably more nervous under acceleration and braking. In order to counteract the loss of traction control as far as possible, the engineers focused particular attention on improving mechanical grip. The concept phase got underway in May. “The scheduling looked after itself really, as we wanted to evaluate the data from the first few races of the season before getting down to work on the design of the new car,” says Rampf. Among the areas of the car decided on at this point were the position of the engine, the length of the gearbox, the wheelbase, weight distribution, tank size and suspension concept. -
Formula One Aerodynamics Wind Beneath the Wings Business Auto Giants Set the Pace Overview Circuits, Teams, Drivers Including
The Credit Suisse Magazine March 2007 Formula One Aerodynamics Wind Beneath the Wings Business Auto Giants Set the Pace Overview Circuits, Teams, Drivers Including: New LIFESTYLE® systems from Bose More elegance Greater ease of use Higher performance We named our new LIFESTYLE® range of DVD home entertainment systems with care. They combine purity of style with technical Bose only innovations that make listening to music and enjoying home cinema uncomplicated and more enjoyable. LIFESTYLE® systems are a complete home entertainment solution, combining high performance with elegance, simplicity and expandability. Unique Bose technologies – true listening benefi ts: ADAPTiQ® audio calibration system Customised sound to your room lay out, speaker placement and listening positions. uMusic® intelligent playback system It stores your CD collection. It learns what kind of music you prefer. It plays the music according to your mood. ® BOSE link The new BOSE® LIFESTYLE® 48 DVD home entertainment system. ® Expand your LIFESTYLE® system to other rooms and enjoy Our ultra-compact ACOUSTIMASS module is 30% smaller than before, making it even easier to hide away. Bose performance throughout your home. Hear the difference Bose technology makes. Ask for a demonstration at the authorised Bose dealer. For dealer addresses or more information call 061 975 77 30 or go to our web site www.bose.ch Editorial 03 Man Versus Machine The waiting comes to an end on March 18. Then the checkered flag will fall in Melbourne to start the 58th Formula One season. Motorsport fans around the globe will finally know how the balance of power will change in the wake of Michael Schumacher’s retirement. -
Thursday Press Conference Transcript
FEDERATION INTERNATIONALE DE L' AUTOMOBILE 2017 FIA Formula One World Championship Hungarian Grand Prix Thursday Press Conference Transcript PART ONE: DRIVERS – Sebastian VETTEL (Ferrari), Fernando ALONSO (McLaren), Nico HULKENBERG (Renault) PRESS CONFERENCE Q: Gentlemen, if we could by getting your thoughts on the Halo cockpit protection that is going to be introduced from the start of 2018. Sebastian, if we could begin with you, what are your thoughts about the Halo and how do you feel it compares to the Shield you tested at Silverstone two weeks ago? Sebastian VETTEL: Well, I wasn’t a big fan of the Shield, mostly for the reason that it was impacting visibility. The Halo test I did, I think it was last year in Abu Dhabi, and for sure you need to get used to it but at least it didn’t impact on the vision, so I think that was the biggest difference. Obviously there has been a lot of talk, as I got it, but I think overall you need to understand that it is a decision that helps us in the car in case something goes very wrong. For sure, if you look at Formula One, the way Formula One cars look and so on, I can understand if people say it doesn’t belong on a Formula One car but on the other hand I think times are changing, you are moving forward and I think if you put it very clear, then it also should be very clear for everyone and there shouldn't be a doubt in your mind whether to introduce it or not. -
Driving Transformation at Formula One
Driving Transformation at Formula One Following the 2017 British Grand Prix, Criticaleye talks toMark Gallagher a Formula One team management board member of more than three decades, about the sport’s evolution uring more than three decades at technologies and a lack of succession cutting-edge cars, for which it then sold DFormula One, Mark Gallagher, CEO and leadership development under its corporate advertising and sponsorship. of Performance Insights, has worked on former CEO, Bernie Ecclestone. “The cars were essentially a 200 mile the management board of the highly per hour billboard,” he says. successful Jordan Grand Prix team, run Mark was invited to Criticaleye’s recent the world famous Cosworth engine Member Dinner to discuss the many That model disintegrated in 2005, when business and established the commercial developments at F1, including its sale to the EU banned tobacco sponsorship. arm of Red Bull Racing, which went on to Liberty Media, owner of US TV company With just three years notice to find a become four-times World Champions. Discovery, for $8 billion in January 2017. replacement for 70 per cent of team sponsorship revenue, the organisations During that period Mark’s been witness Rebuilding the Commercial Model involved initially looked for similar to what he describes as Formula One’s sponsors. They had to be established, “existential challenges”. These include When Mark joined Formula One in the profitable and would be enticed by the the collapse of its commercial model, 1980s, its model could not have been glamour of racing. One of which was the development of highly disruptive simpler. -
Just the Formula One Facts
570153 Ch01.qxd 9/18/03 12:04 AM Page 9 Chapter 1 Just the Formula One Facts In This Chapter ᮣ Understanding what Formula One is ᮣ Discovering who the most important people in the sport are ᮣ Getting a glimpse at a Formula One car ᮣ Touring the Formula One tracks ᮣ Recognising the sport’s business side ᮣ A calendar of events ormula One racing is, as its name suggests, the pinnacle of motor racing Faround the world. Small children don’t dream about growing up to race in lesser series – above all else, they want to be a winning Formula One driver. These days, the sport is a truly global circus. At almost every race on the cal- endar, more than 120,000 spectators cram into the grandstands and spectator banking, all vying for a view of the millionaire superstar drivers. At that same time, in 150 countries worldwide, more than 300 million people tune in to watch the fight for glory in the comfort of their front rooms. It is this sort of global following that has attracted huge sponsorship and left television stations around the world falling all over themselves to broadcast the races. The huge marketing drives put on by the sponsors have whipped up even more interest in the sport. Nowadays, only the Olympic Games and the football World Cup can boast the kind of viewership, backing, and inter- est that Formula One has – and those events only take place every four years. Formula One: A Grand and Global Sport Part of Formula One’s mass appeal is that it is truly a global sport.