Aerodynamic and Structural Design of a 2022 Formula One Front Wing Assembly
Total Page:16
File Type:pdf, Size:1020Kb
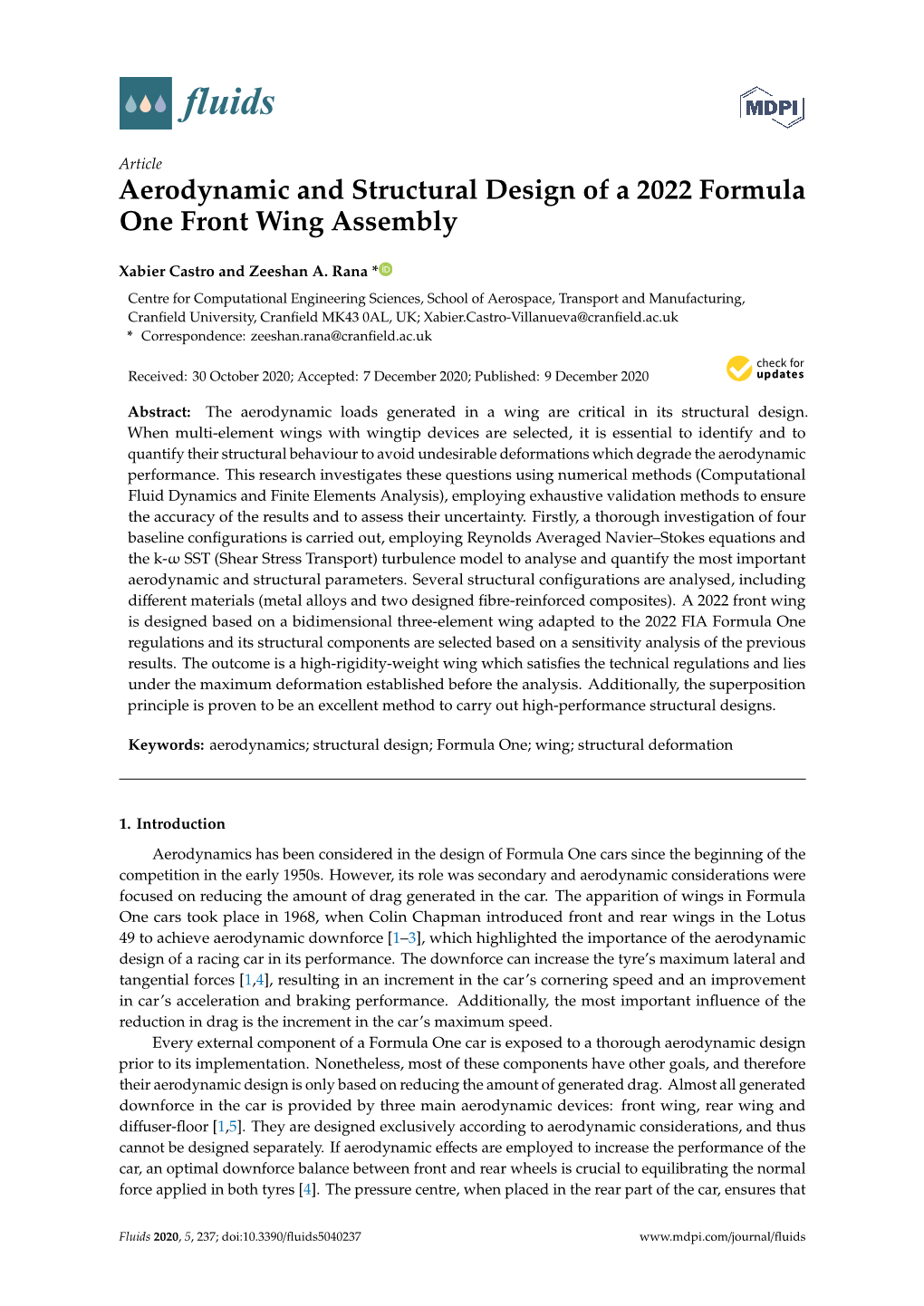
Load more
Recommended publications
-
On the Road in New Vantage, 2018'S Hottest Sports
REPRINTED FROM CAR MAGAZINE FEBRUARY 2018 ASTON RISING! On the road in new Vantage, 2018’s hottest sports car PLUS: Reborn DB4 GT driven! Valkyrie’s F1 tech secrets! February 2018 | CARMAGAZINE.CO.UK DB4 GT VALKYRIE THEY’VE YOUR GUIDED A SENSATIONAL NEW VANTAGE FAITHFULLY T O U R O F REPRODUCED A S T O N ’ S THEIR ICONIC HYPERCAR BY RACER – WE THE MEN WHO EPIC ENGINES AND ELECTRONICS FROM AMG DRIVE IT MADE IT VANTAGE A N E X C L U S I V E RIDE IN A COSY RELATIONSHIP WITH RED BULL 2018’S MOST EXCITING A NEW EX-MCLAREN TEST PILOT SPORTS CAR DB11 SALES SUCCESS, A NEW FACTORY AND FULL-YEAR PROFITS IN 2017 A V12 HYPERCAR TO REDEFINE THE CLASS HERITAGE TO DIE FOR… …WHY 2018 IS ALREADY ASTON’S YEAR CARMAGAZINE.CO.UK | February 2018 February 2018 | CARMAGAZINE.CO.UK Aston special New Vantage SPECIAL FTER 12 YEARS' sterling service, the old Vantage has finally been put out to pasture. Its replacement is this vision in eye-melting lime green, and it’s by no means just a styling refresh – the new Vantage is powered by a 4.0-litre twin-turbo V8 from AMG (as deployed in the V8 DB11), uses a new aluminium architecture with Aa shorter wheelbase than a 911’s and boasts a gorgeous interior with infotainment pinched from the latest Mercedes-Benz S-Class. Admittedly the new car shares parts with the DB11 – suspension, for example – but 70 per cent are bespoke. The days of Aston photocopying old blueprints and changing the scale are gone. -
Formula 1 Race Car Performance Improvement by Optimization of the Aerodynamic Relationship Between the Front and Rear Wings
The Pennsylvania State University The Graduate School College of Engineering FORMULA 1 RACE CAR PERFORMANCE IMPROVEMENT BY OPTIMIZATION OF THE AERODYNAMIC RELATIONSHIP BETWEEN THE FRONT AND REAR WINGS A Thesis in Aerospace Engineering by Unmukt Rajeev Bhatnagar © 2014 Unmukt Rajeev Bhatnagar Submitted in Partial Fulfillment of the Requirements for the Degree of Master of Science December 2014 The thesis of Unmukt R. Bhatnagar was reviewed and approved* by the following: Mark D. Maughmer Professor of Aerospace Engineering Thesis Adviser Sven Schmitz Assistant Professor of Aerospace Engineering George A. Lesieutre Professor of Aerospace Engineering Head of the Department of Aerospace Engineering *Signatures are on file in the Graduate School ii Abstract The sport of Formula 1 (F1) has been a proving ground for race fanatics and engineers for more than half a century. With every driver wanting to go faster and beat the previous best time, research and innovation in engineering of the car is really essential. Although higher speeds are the main criterion for determining the Formula 1 car’s aerodynamic setup, post the San Marino Grand Prix of 1994, the engineering research and development has also targeted for driver’s safety. The governing body of Formula 1, i.e. Fédération Internationale de l'Automobile (FIA) has made significant rule changes since this time, primarily targeting car safety and speed. Aerodynamic performance of a F1 car is currently one of the vital aspects of performance gain, as marginal gains are obtained due to engine and mechanical changes to the car. Thus, it has become the key to success in this sport, resulting in teams spending millions of dollars on research and development in this sector each year. -
Davide Signed with Alpine F1 Team in January 2021 As
ALPINE F1 TEAM PRESS PACK Already recognised for its records It is part of Groupe Renault’s Luca De Meo, CEO Groupe That’s the beauty of racing as In September 2020, Luca De Meo, and successes in endurance strategy to clearly position Renault: “It is a true joy to see a works team in Formula 1. announced the creation of Alpine F1 Team, and rallying, the Alpine name each of its brands. For Alpine, the powerful, vibrant Alpine We will compete against the naturally finds its place in the this is a key step to accelerate name on a Formula One car. biggest names, for spectacular a renaissance of Groupe Renault’s F1 team, high standards, prestige and the development and influence New colours, new managing car races made and followed one of F1’s most historic and successful. performance of Formula 1. The of the brand. Renault remains team, ambitious plans: it’s a new by cheering enthusiasts. I can’t Alpine brand, a symbol of sporting an integral part of the team, beginning, building on a 40-year wait for the season to start.” prowess, elegance and agility, with the hybrid power unit history. We’ll combine Alpine’s will be designated to the chassis retaining its Renault E-Tech values of authenticity, elegance and pay tribute to the expertise moniker and unique expertise and audacity with our in-house that gave birth to the A110. in hybrid powertrains. engineering & chassis expertise. ALPINE F1 TEAM | PRESS PACK | 2021 Alpine Today and Tomorrow As part of Groupe Renault’s strategic plan ‘Renaulution’, Alpine unveiled its long-term plans to position the brand at the forefront of Groupe Renault’s innovation. -
2021 Formula 1 Technical Regulations
2021 FORMULA 1 TECHNICAL REGULATIONS PUBLISHED ON 16 DECEMBER 2020 Issue 7 Convention: Black text: based on 2020 Technical Regulations – Issue 5 (19/06/2020) Pink text: changes for 2021 approved by the WMSC on 19/06/2020, 04/09/2020, 09/10/2020, 30/10/2020 and 16/12/2020 Green text: comments / not regulatory CONTENTS: Pages ARTICLE 1: DEFINITIONS 8 1.1 Formula One Car 1.2 Automobile 1.3 Land Vehicle 1.4 Bodywork 1.5 Wheel 1.6 Complete wheel 1.7 Automobile Make 1.8 Event 1.9 Weight 1.10 Cubic capacity 1.11 Pressure charging 1.12 Cockpit 1.13 Sprung suspension 1.14 Survival cell 1.15 Camera 1.16 Camera housing 1.17 Cockpit padding 1.18 Brake caliper 1.19 Electronically controlled 1.20 Open and closed sections 1.21 Power train 1.22 Power unit 1.23 Engine 1.24 Energy Recovery System (ERS) 1.25 Motor Generator Unit - Kinetic (MGU-K) 2021 Formula 1 Technical Regulations 1 16 December 2020 © 2020 Fédération Internationale de l’Automobile Issue 7 1.26 Motor Generator Unit - Heat (MGU-H) 1.27 Energy Store (ES) 1.28 Compressor inlet 1.29 Compressor outlet 1.30 Combustion chamber 1.31 Fuel injector 1.32 Auxiliary Oil Tank (AOT) 1.33 Engine exhaust system 1.34 Turbocharger (TC) 1.35 In-cylinder pressure sensor 1.36 High pressure Fuel pump 1.37 Fuel Flow meter 1.38 Ignition Coil 1.39 Ancillaries 1.40 Engine Plenum 1.41 ES cells 1.42 DC-DC Converter 1.43 Power Unit Control Electronics (PU-CE) 1.44 Valve Stem ARTICLE 2: GENERAL PRINCIPLES 13 2.1 Role of the FIA 2.2 Applicable regulations and amendments to the regulations 2.3 Dangerous construction 2.4 -
How Advancements in Aerodynamics Improves the Performance of Formula 1 Racecars Joshua Fields Union College - Schenectady, NY
Union College Union | Digital Works Honors Theses Student Work 6-2015 How Advancements in Aerodynamics Improves the Performance of Formula 1 Racecars Joshua Fields Union College - Schenectady, NY Follow this and additional works at: https://digitalworks.union.edu/theses Part of the Aerodynamics and Fluid Mechanics Commons Recommended Citation Fields, Joshua, "How Advancements in Aerodynamics Improves the Performance of Formula 1 Racecars" (2015). Honors Theses. 300. https://digitalworks.union.edu/theses/300 This Open Access is brought to you for free and open access by the Student Work at Union | Digital Works. It has been accepted for inclusion in Honors Theses by an authorized administrator of Union | Digital Works. For more information, please contact [email protected]. How Advancements in Aerodynamics Improves the Performance of Formula 1 Racecars By Joshua Fields ************************* Submitted in partial fulfillment of the requirements for Honors in the Department of Mechanical Engineering UNION COLLEGE June, 2015 1 ABSTRACT FIELDS, JOSHUA How Advancements in Aerodynamics Improves the Performance of Formula 1 Racecars. Department of Mechanical Engineering, June 2015. ADVISOR: Prof. Andrew Rapoff The purpose of this paper is to review how knowledge of aerodynamics improved the performance of Formula 1 racing cars since the beginnings of Formula 1 racing after World War II. Formula 1 racing places each competitive team on a similar level in regulating the cars to be safe while driving above 350 kph. This paper begins with how Formula 1 racing began and how race cars were designed and looked. Then each decade of racing will be discussed and remarks on major advancements and changes in aerodynamics. -
Formula One Race Strategy Mclaren Racing Limited Sports Technology Mclaren Is a Registered Trademark of Mclaren Racing Limited
Formula One Race Strategy McLaren Racing Limited Sports Technology McLaren is a registered trademark of McLaren Racing Limited INTRODUCTION We will solve this problem in three steps as follows: Step 1: How long will it take to reach the first pit stop? From the scenario, we have the following information: Fuel Consumption C = 3 kg/lap How much slower our lap E = 0.03 sec/ time is for every kg of fuel on (lap kg) board (also called the “weight effect”) Time to complete a lap with 1 t1 = 100.045 lap of fuel on board sec Figure 1: A Vodafone McLaren Mercedes driven by Lewis Hamilton Using this, we can calculate how much slower the McLaren Racing, the company behind Vodafone car goes for every lap’s worth of fuel we have on McLaren Mercedes, operates in the highly board. We call this the Fuel Laps Weight Effect competitive and technological environment of (W ) and this is calculated as follows: Formula One. McLaren Racing comprises a W = Fuel Laps Weight Effect multitude of administrative and engineering = Fuel Consumptio n ´ Weight Effect departments, ranging from vehicle design and aerodynamics, to materials science and the paint = 3 ´ 0.03 = 0 .0 9 sec/(lap lap of fuel) shop. As one of the most successful teams in the The extra time taken to complete a lap when we history of Formula One, McLaren has won more have fuel on board can be calculated as follows: Grand Prix than any other Constructor since it Extra time taken to complete lap due to fuel on board entered the sport in 1966. -
Aerodynamic Analysis of the Undertray of Formula 1
Treball de Fi de Grau Grau en Enginyeria en Tecnologies Industrials Aerodynamic analysis of the undertray of Formula 1 MEMORY Autor: Alberto Gómez Blázquez Director: Enric Trillas Gay Convocatòria: Juny 2016 Escola Tècnica Superior d’Enginyeria Industrial de Barcelona Aerodynamic analysis of the undertray of Formula 1 INDEX SUMMARY ................................................................................................................................... 2 GLOSSARY .................................................................................................................................... 3 1. INTRODUCTION .................................................................................................................... 4 1.1 PROJECT ORIGIN ................................................................................................................................ 4 1.2 PROJECT OBJECTIVES .......................................................................................................................... 4 1.3 SCOPE OF THE PROJECT ....................................................................................................................... 5 2. PREVIOUS HISTORY .............................................................................................................. 6 2.1 SINGLE-SEATER COMPONENTS OF FORMULA 1 ........................................................................................ 6 2.1.1 Front wing [3] ....................................................................................................................... -
RL-Tyrrell 010/02 Dec.Pages
! 1980 Tyrrell 010 Chassis No: 010/2 • A competitive and useable ground effect entry to the flourishing FIA Historic Formula One Championship, with a sister 010 taking six wins so far this season. • Raced for 11 Grand Prix in 1980 by Derek Daly with a 4th at the British Grand Prix. • Driven in 1981 by Ricardo Zunino and Eddie Cheever, with another 4th at the British Grand Prix for Cheever. • HSCC Historic Formula 1 Champion with Richard Peacock in 1989. • In the current ownership for the last 10 years, with minimal use. The Tyrrell Racing Organisation is a name that rings out with some of the all time Formula 1 greats, with three Formula 1 World Championships and one Constructors Championship to its name. It’s founder, Ken Tyrrell first came into racing in 1958 when he ran three Formula 3 cars for himself and a couple of local stars. Ken soon realised that he was not destined to be a racing driver and stood down from driving duties in 1959, instead to focus on running a Formula Junior team from a woodshed owned by his family business, Tyrrell Brothers. Tyrrell ran a variety of cars in the lower formulas through the 1960s, giving drivers like John Surtees, Jacky Ickx and most notably Jackie Stewart their single seater debuts. In 1968, Tyrrell’s involvement with Matra in Formula 2 was stepped up to the main stage of Formula 1, where Ken ran Matra International, a joint venture between Tyrrell and Matra. They had many wins with Stewart in the MS10 during ’68. -
Investigation of Turbulence Created by Formula One™ Cars with the Aid of Numerical Fluid Dynamics and Optimization of Overtaking Potential
Investigation of Turbulence Created by Formula One™ Cars with the Aid of Numerical Fluid Dynamics and Optimization of Overtaking Potential Milad Mafi Competence Centre, transtec AG, Tübingen, Germany Summary Formula One™ is the most successful racing series in the world. And with over 25 million television viewers per race it attracts many prominent sponsors who have invested over a billion euros in it, making them indispensable for Formula One™’s survival. In the last ten years the numbers of overtaking maneuvers in Formula One™ races have become rarer and rarer – changes in position now take place in the pit stop or as a result of defective parts. This has caused races to be less eventful, as reflected in falling TV viewing figures. Many sponsors have withdrawn their support and, should this trend continue, it would mean the end of Formula One™. The reason for the decreasing number of overtaking maneuvers, which were quite common in the nineteen-eighties, can be found in the aerodynamics of Formula One™ racing cars: During the age of turbo motors road holding, in racing jargon “grip” which is produced by the tires, the aerodynamics created down force resulting in extra grip. Like the tires, the proper functioning of which is restricted to a certain temperature range, the aerodynamics of a racing car depends on several factors, including the intensity of air turbulence. Laminar air flow is the basis for the efficient functioning of the wings and bodywork. The aerodynamics of modern Formula One™ cars produces a down force of roughly 25000 N, which corresponds to a gravitational force of 2.5 metric tons. -
Design of Formula One Racing Car
International Journal of Engineering Research & Technology (IJERT) ISSN: 2278-0181 Vol. 4 Issue 04, April-2015 Design of Formula One Racing Car Triya Nanalal Vadgama Mr. Arpit Patel, Student Assistant Professor Department of Aeronautical Engineering Department of Aeronautical Engineering Sardar Vallabhbhai Patel Institute of Technology, Vasad Sardar Vallabhbhai Patel Institute of Technology, Vasad Gujarat Technological University, Ahmedabad, India Gujarat Technological University, Ahmedabad, India Dr. Dipali Thakkar, Head & Professor Department of Aeronautical Engineering Sardar Vallabhbhai Patel Institute of Technology, Vasad Gujarat Technological University, Ahmedabad, India Abstract- A modern Formula One (F1) Racing Car has almost as affect the airflow, and placing a badge on a crucial element much in common with an aircraft as it does with an ordinary could produce a two-to-three percent difference in air road car. Aerodynamics has become a key to success in the sport pressure. Disrupted air flow can cause turbulence, which will and teams spend millions of dollars on research and produce drag to slow the car. F1 cars often have small development in the field each year for improving performance. 'winglets' before the rear wing, which 'clean up' complex air The aerodynamic designer has two primary concerns : i. the creation of downforce, to help push the car’s tyres flow in order to maximize down force. The scope of this onto the track and improve cornering forces, project includes : ii. to minimise the drag that occurs due to turbulence and i. Designing of F1 three-dimensional CAD model acts to slow down the car. using CATIA V5 R21 software. In this project, a Formula One race car will be designed using the CAD software CATIA V5R20. -
The Aerodynamics of a Formula One Car Front Cascade Wing During
Journal of Advanced Research in Fluid Mechanics and Thermal Sciences 53, Issue 1 (2019) 53-60 Journal of Advanced Research in Fluid Mechanics and Thermal Sciences Journal homepage: www.akademiabaru.com/arfmts.html ISSN: 2289-7879 Aerodynamics of a Formula One Car Front Cascade Wing Open Access during Cornering Ahmed T. Raheem1, Azwan Sapit1,*, Akmal Nizam Mohammed2 1 Faculty of Mechanical & Manufacturing Engineering, Universiti Tun Hussein Onn Malaysia, 86400 Parit Raja, Batu Pahat, Johor, Malaysia 2 Centre for Energy and Industrial Environment Studies, Universiti Tun Hussein Onn Malaysia, 86400 Parit Raja, Batu Pahat, Johor, Malaysia ARTICLE INFO ABSTRACT Article history: The design for the aerodynamics of front wing based on cornering angle of a Formula- Received 10 October 2018 One car plays an important role on the car's performance. The cascade elements above Received in revised form 21 November 2018 the main front wing is enhanced with new and the deep winglets that manage the Accepted 5 December 2018 airflow for the rest of the car. The front wing cascades are attached with end plates at Available online 8 January 2019 the extremities of the front wing to reduce turbulence. However, when the car turns, the airflow behaviour on these cascades wings changes significantly. This paper presents the aerodynamic characteristics resulting from the cornering forces subjected on Formula One styled cascade wings. The study attempts to predict the down-force and drag-force acting on the front wing under the effect of airflow change in this area. In order to investigate the airflow behaviour, computational fluid dynamics (specifically the ANSYS software) was used to simulate selected cases with specific surface definitions and boundary conditions defined in a 3D domain. -
Aerodynamics of Race Cars
AR266-FL38-02 ARI 22 November 2005 19:22 Aerodynamics of Race Cars Joseph Katz Department of Aerospace Engineering, San Diego State University, San Diego, California 92182; email: [email protected] Annu. Rev. Fluid Mech. Key Words 2006. 38:27–63 downforce, inverted wings, ground effect, drag The Annual Review of Fluid Mechanics is online at fluid.annualreviews.org Abstract doi: 10.1146/annurev.fluid. Race car performance depends on elements such as the engine, tires, suspension, 38.050304.092016 road, aerodynamics, and of course the driver. In recent years, however, vehicle aero- Copyright c 2006 by dynamics gained increased attention, mainly due to the utilization of the negative Annual Reviews. All rights lift (downforce) principle, yielding several important performance improvements. reserved This review briefly explains the significance of the aerodynamic downforce and how 0066-4189/06/0115- it improves race car performance. After this short introduction various methods to 0027$20.00 generate downforce such as inverted wings, diffusers, and vortex generators are dis- Annu. Rev. Fluid Mech. 2006.38:27-63. Downloaded from www.annualreviews.org by Universidade Estadual de Campinas (Unicamp) on 04/17/11. For personal use only. cussed. Due to the complex geometry of these vehicles, the aerodynamic interaction between the various body components is significant, resulting in vortex flows and lifting surface shapes unlike traditional airplane wings. Typical design tools such as wind tunnel testing, computational fluid dynamics, and track testing, and their rel- evance to race car development, are discussed as well. In spite of the tremendous progress of these design tools (due to better instrumentation, communication, and computational power), the fluid dynamic phenomenon is still highly nonlinear, and predicting the effect of a particular modification is not always trouble free.