Review of Rapid Prototyping-Technology for the Future by Prof
Total Page:16
File Type:pdf, Size:1020Kb
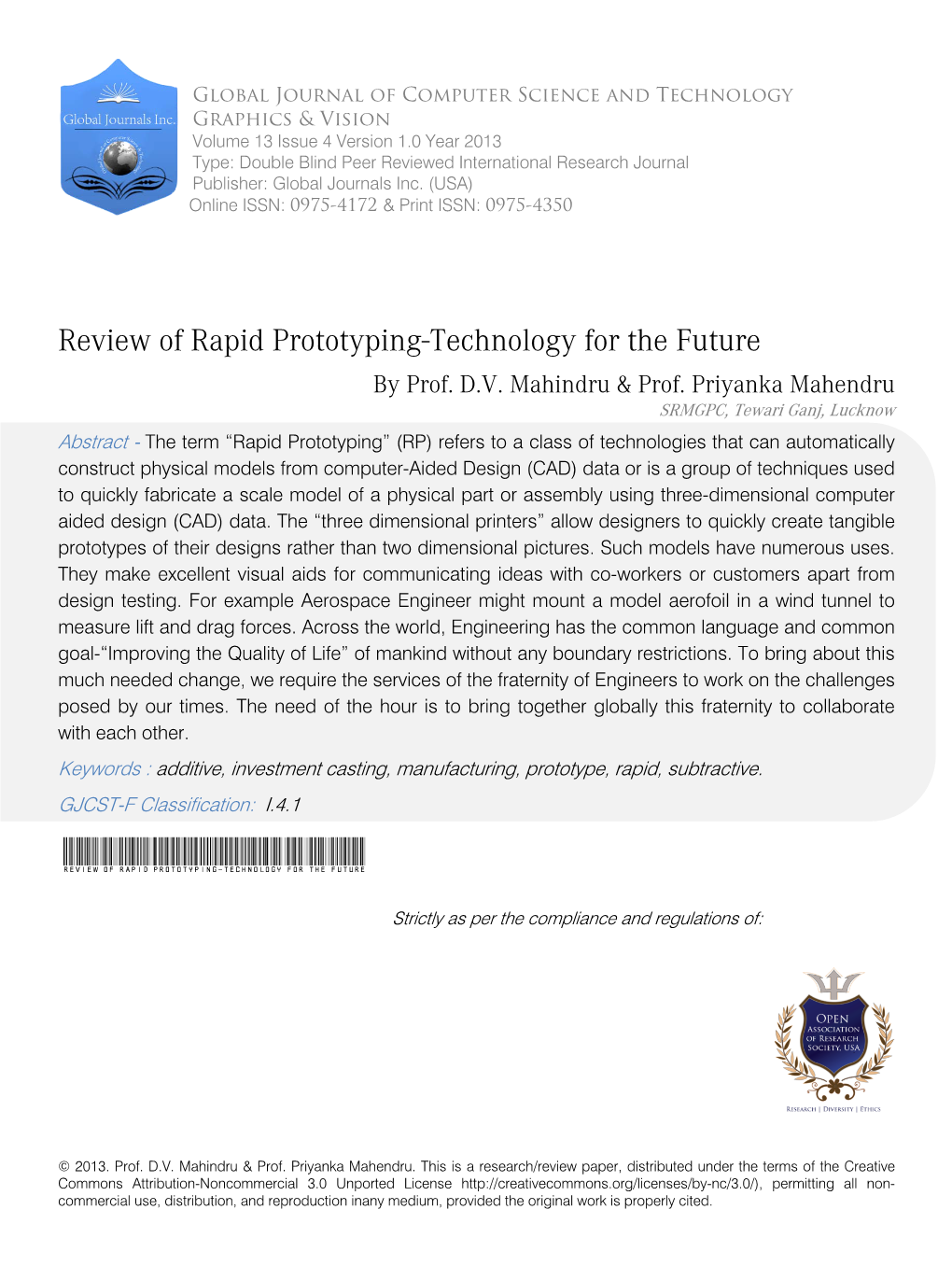
Load more
Recommended publications
-
Rapid Prototyping Technology- Classification and Comparison
International Research Journal of Engineering and Technology (IRJET) e-ISSN: 2395 -0056 Volume: 04 Issue: 06 | June -2017 www.irjet.net p-ISSN: 2395-0072 Rapid Prototyping Technology- Classification and Comparison Dharipalli Hyndhavi1, S.Bhanu Murthy2 1M.Tech Student, Mechanical Engineering Department, VNRVJIET, Hyderabad, India. 2Assistant Professor, Mechanical Engineering Department, VNRVJIET, India. ---------------------------------------------------------------------***--------------------------------------------------------------------- Abstract - Rapid Prototyping is a group of techniques used ISO/ASTM52900-15 defines seven categories of AM to quickly fabricate a prototype, develop a product of high processes: binder jetting, directed energy deposition, quality, low cost in shortest period available, using three- material extrusion, material jetting, powder bed fusion, sheet dimensional CAD data, present in stereo lithography (.STL) file lamination and vat photo polymerization. format. Construction of the part or an assembly is usually done using 3D printing which is also known as additive 2. OVERVIEW OF RAPID PROTOTYPING manufacturing technology or Layer manufacturing. 3D TECHNOLOGY printing technology has guided the technology in advancing the design and development more quickly and at a much lower Prototypes were constructed by high skilled model makers cost than with that of the conventional methods. 3D printing from standardized 2 dimensional engineering drawing. The has wide applications in research and development of process was highly expensive and time consuming. With components ranging from simple structures to complicated advancement in technology of new CAD/CAM technologies products. This paper presents an overview of rapid and layer manufacturing, prototypes are being produced prototyping technology, its importance, classification and rapidly from 3D CAD models. Rapid Prototyping method has comparison of properties of products obtained by adopting two systems for two distinct markets. -
Additive Manufacturing with Reprap Methodology: Current Situation and Future Prospects
Additive manufacturing with RepRap methodology: current situation and future prospects L. Romero1, A. Guerrero1, M. M. Espinosa1, M. Jiménez 2, I.A. Domínguez1, M. Domínguez1 1 Design Engineering Area - Universidad Nacional de Educación a Distancia (UNED), Madrid, Spain 2 Department of Mechanical Engineering, Technical School of Engineering - ICAI, Comillas University, Madrid, Spain Abstract In February 2004, Adrian Bowyer, from the University of Bath, began an open initiative called RepRap, with the purpose of creating an open source rapid prototyping machine which, moreover, could replicate itself. This article analizes the current status of the RepRap initiative, commenting the basic components of RepRap machines, the differences between the different 3D printers developed by the RepRap community so far, and the technical possibilities that opens this technology from the engineering point of view. In addition we propose some improvements that could be perfectly feasible in the short term. For this purpose, the assembly of a RepRap Mendel Prusa was performed, but with some modifications. 120 1. Introduction to RepRap community. A 3D printing machine (and any computing device in general) is composed of hardware (electric, electronic, electromechanic and mechanic physical components) and control software (the logical equipment as the operating system or software applications), usually both developed by companies that control them. However, there are several companies in the world that are dedicated to the development of hardware in a peculiar way: they publish the sources of their inventions and sharing them with the whole world, with the aim that users from all the planet can use them and propose improvements. This is the model of open source hardware: hardware whose design, components, tools and documentation are open and they are publicly available to anyone. -
Advanced Manufacturing Choices
Advanced Manufacturing Choices Additive Manufacturing Techniques J.Ramkumar Dept of Mechanical Engineering IIT Kanpur [email protected] 2 Table of Contents 1. Introduction: What is Additive Manufacturing 2. Historical development 3. From Rapid Prototyping to Additive Manufacturing (AM) – Where are we today? 4. Overview of current AM technologies 1. Laminated Object Manufacturing (LOM) 2. Fused Deposition Modeling (FDM) 3. 3D Printing (3DP) 4. Selected Laser Sintering (SLS) 5. Electron Beam Melting (EBM) 6. Multijet Modeling (MJM) 7. Stereolithography (SLA) 5. Modeling challenges in AM 6. Additive manufacturing of architected materials 7. Conclusions 3 From Rapid Prototyping to Additive Manufacturing What is Rapid Prototyping - From 3D model to physical object, with a “click” - The part is produced by “printing” multiple slices (cross sections) of the object and fusing them together in situ - A variety of technologies exists, employing different physical principles and working on different materials - The object is manufactured in its final shape, with no need for subtractive processing How is Rapid Prototyping different from Additive Manufacturing? The difference is in the use and scalability, not in the technology itself: Rapid Prototyping: used to generate non-structural and non-functional demo pieces or batch-of-one components for proof of concept. Additive Manufacturing: used as a real, scalable manufacturing process, to generate fully functional final components in high-tech materials for low-batch, high-value manufacturing. 4 Why is Additive Manufacturing the Next Frontier? EBF3 = Electron Beam Freeform Fabrication (Developed by NASA LaRC) 5 Rapid Prototyping vs Additive Manufacturing today AM breakdown by industry today Wohlers Report 2011 ~ ISBN 0-9754429-6-1 6 From Rapid Prototyping to Additive Manufacturing A limitation or an opportunity? Rapid Prototyping in a nutshell 1. -
Rapid Prototyping Rev II
Rapid Prototyping Rev II DR. TAREK A. TUTUNJI REVERSE ENGINEERING PHILADELPHIA UNIVERSITY, JORDAN 2 0 1 5 Prototype A prototype can be defined as a model that represents a product or system. This model is usually used for functionality testing and product visualization. Prototyping is essential in the development of products and all industrial nations have prototyping centers. In fact, prototyping plays a major role in the advancement of technology. Prototype In the prototyping development cycle, initial prototypes are built, tested, and then reworked as necessary until an acceptable prototype is finally achieved from which the complete system or product can be developed. Three types of prototyping PCB Prototyping Virtual Prototyping Rapid Prototyping PCB Prototyping The production of a functional Printed Circuit Board (PCB). The product can then be tested for its functionality and reliability Virtual Prototyping Computer-based without the option of a physical part or object. It uses virtual reality to create product prototypes and test their properties. It provides a virtual 3-D prototype that can be manipulated from all views and angles. The computer program can then test many aspects of the product such as vibration, forces, materials and weight. Rapid Prototyping Produces physical prototypes in short time (within hours or days rather than weeks). These prototypes are frequently used to quickly test the product's look, dimension, and feel. Rapid prototyping usually result in plastic objects. Prototyping Advantages Provides -
Future of Manufacturing Technology Rapid Prototyping Technique
International Journal of Mechanical Engineering and Technology (IJMET) Volume 7, Issue 5, September–October 2016, pp.117–126, Article ID: IJMET_07_05_014 Available online at http://iaeme.com/Home/issue/IJMET?Volume=7&Issue=5 Journal Impact Factor (2016): 9.2286 (Calculated by GISI) www.jifactor.com ISSN Print: 0976-6340 and ISSN Online: 0976-6359 © IAEME Publication FUTURE OF MANUFACTURING TECHNOLOGY RAPID PROTOTYPING TECHNIQUE Yembadi Koushik Varma B. Tech, Mechatronics (Mechanical) Engineering Department, Mahatma Gandhi Institute of Technology, Hyderabad, India Samatham Madhukar B. Tech, Mechanical Engineering Department, VidyaJyothi Institute of Technology, Hyderabad, India Bootla Akhil B. Tech, Mechanical Engineering Department, VidyaJyothi Institute of Technology, Hyderabad, India Pokala Saiprasanna Kumar B.Tech, Mechanical Engineering Department, Joginpally B.R Engineering College, Hyderabad, India ABSTRACT The term “Rapid Prototyping” (RP) refers to a class of technologies that can automatically construct physical models from computer-Aided Design (CAD) data or is a group of techniques used to quickly fabricate a scale model of a physical part or assembly using three-dimensional computer aided design (CAD) data. The edges and surfaces of a complex solid model and their information are used for defining a product which is further manufactured as a finished product by CNC machining. They make excellent visual aids for communicating ideas with co-workers or customers apart from design testing. Across the world, Engineering has the common language and common goal-“Improving the Quality of Life” of mankind without any boundary restrictions. The common goal can be attained by the engineers in less time by RAPID PROTOTYPING TECHNIQUE and this paper provides a better platform for researchers, new learners and product manufacturers for various applications of RP models. -
Stereolithography the First 3D Printing Technology Designated May 18, 2016
ASME Historic Mechanical Engineering Landmark Stereolithography The First 3D Printing Technology Designated May 18, 2016 The American Society of Mechanical Engineers Mr. Hull made two significant contributions that advanced the viability of 3D technology: • He designed/established the STL file format that is widely accepted for defining 3D images in 3D printing software. • He established the digital slicing and in-fill Historical Significance of the strategies common in most 3D printing processes. Landmark Mr. Hull obtained patent no. 4,575,330 (filed Stereolithography is recognized as the first August 8, 1984) for an “Apparatus for production commercial rapid prototyping device for what of three-dimensional objects by is commonly known today as 3D printing. 3D stereolithography.” In 1986, he co-founded 3D printing is revolutionizing the way the world Systems, Inc. (3D Systems) to commercialize the thinks and creates, and has been identified as technology. 3D Systems introduced their first 3D a ‘disruptive technology’ – an innovation that printer, the SLA-1, in 1987. has displaced established technologies and created new industries. ASME Landmark Plaque Text 3D Systems SLA-1 3D Printer | 1987 This is the first 3D printer manufactured for commercial sale and use. This system pioneered the rapid development of additive manufacturing, a method in which material is added layer-by-layer to form a solid object, as opposed to traditional manufacturing in which material is cut or machined away. The SLA-1 is based on stereolithography, using a precisely controlled beam of UV light to solidify liquid polymers one layer at a time. Stereolithography process Chuck Hull developed stereolithography in 1983 and formed 3D Systems to manufacture and While the origins of 3D printing date back to market a commercial printer. -
The Reprap Project
CASE STUDY: THE REPRAP PROJECT 3D PRINTING 3D Printing Today • 3D Printing in the news: 3D printed… • Organs, toys, cars, buildings, astronaut food • 3D printers (I’m so meta even this acronym…) • 3D Printing Materials commercially available today • Plastics • Ceramics (including food grade) • Metal • Rapid prototyping accessible for artists, engineers, etc. 3D PRINTING 3D Printing Technology for RepRap • Fused Deposition Modeling (FDM): Method of 3D printing in which thin filament of material is pushed through a heated nozzle and deposited layer-by-layer on a surface • Based on US Patent 5,121,329 (first full description of FDM technology; now expired) • Objective of the RepRap project: create an open source 3D printer capable of printing all of the parts necessary to build a new RepRap (assisted self replication) 3D PRINTING Anatomy of an FDM 3D Printer • 3 Axis CNC Platform: Provides motion for the tool head and print bed in the X, Y, and Z axes • Extruder: Geared mechanism which accepts filament and feeds it into the hot end • “Hot End”: Heated nozzle which receives filament from the extruder and deposits it on the print surface • Control Electronics: Used to control movement of tool head and print bed, heating controls for print bed and hot end, homing and other features • Sensors: Provide feedback to control electronics about the position of tool head and print bed, as well as other features 3D PRINTING Anatomy of an FDM 3D Printer • Filament: A “wire” of material on a reel which is used by the 3D printer to create the 3D shape • -
$200 Vs. $20,000
$200 vs. $20,000 The Real Difference Between Hobbyist and Professional 3D Printers From futuristic concept to creative hobby to new industrial revolution, 3D printing has had a tumultuous journey of self-actualization since it first emerged in the 1980s. Originally conceived as rapid prototyping technology during the expansion phase of 3D CAD, early 3D printers rarely saw use outside of form modeling in well-funded R&D centers. The specialized labor requirements (3D CAD was still considered a rare skill in the 90s!) and high costs made it prohibitively expensive for the average prototype. As the technology matured through the 1990s and 2000s and early patents neared expiration, 3D printers proliferated through open source initiatives like RepRap and became commercially available. Around the same time, Maker culture made a comeback in the form of makerspaces and fablabs across the world, as whitecollar workers sought a tangible escape from spreadsheets and paperwork. A second wave of 3D printing entrepreneurs rose from the Maker movement, invoking imagery of the Star Trek replicator, and championing the democratization of manufacturing. 3D printing was hyped up in the media with promises of liberation from large corporations $200 vs $20,000: The Real Difference Between Hobbyist and Professional 3D Printers 1 and futuristic innovations that would change solution scalability. While some 3D printer the world; yet, by the time the bubble finally companies focused internally on cutting costs burst in 2015, most of the industry had not to improve the value of their product offerings, progressed beyond form models, home DIY others focused externally on new materials projects, and tabletop figurines. -
Preliminary Component Integration Utilizing Rapid Prototyping Techniques Ken Cooper, NASA Marshall Space Flight Center Pat Salvail, IITRI
Preliminary Component Integration Utilizing Rapid Prototyping Techniques Ken Cooper, NASA Marshall Space Flight Center Pat Salvail, IITRI Abstract employs an ultraviolet laser to selectively cure the epoxy into One of the most costly errors the shape desired. committed during the development of an 2. Selective Laser Sintering, a element to be used in the space industry powder-based process which is the lack of communication between uses a laser to melt cross design and manufacturing engineers. A sections of polymer or semi- very important tool that should be metallic powders into the utilized in the development stages by shape desired. both design and manufacturing 3. Laminated Object disciplines is rapid prototyping. Manufacturing, a solid-based Communication levels are intensified process which adheres layers with the injection of functional models of paper, plastic or composite that are generated from a drawing. and cuts each cross section with a laser. At the Marshall Space Flight 4. Fused Deposition Modeling, Center, this discipline is utilized on a another solid-based process more frequent basis as a manner by which extrudes a semi-molten which hardware may be tested for design thermoplastic through a and material compatibility. moving XY orifice to form the necessary shape. Background 5. Multi Jet Modeling builds solid wax patterns by printing layers Rapid prototyping in this text of hot wax directly through refers to a collective set of solid standard print jets. freeform fabrication technologies, which 6. Three Dimensional Printing build physical models directly from prints layers of binder into a computer aided design (CAD) data. The polymer powder matrix. -
Application of Rapid Prototyping to the Investment Casting of Test Hardware (MSFC Center Director's Discretionary Fund Final Report, Project No
NASA/TM--2000-210384 Application of Rapid Prototyping to the Investment Casting of Test Hardware (MSFC Center Director's Discretionary Fund Final Report, Project No. 98-08) K.G. Cooper and D. Wells Marshall Space Flight Center, Marshall Space Flight Center, Alabama National Aeronautics and Space Administration Marshall Space Flight Center • MSFC, Alabama 35812 June 2000 Available from: NASA Center for AeroSpace Inlormation National Technical In|ormation Service 7121 Standard Drive 5285 Port Royal Road Hanover, MD 21076-1320 Springfield, VA 22161 (301) 621-0390 (703) 487-4650 ii TABLE OF CONTENTS I. PURPOSE ......................................................................................................................................... 2. BACKGROUND/APPROACH ........................................................................................................ 2 3. TEST RESULTS ............................................................................................................................... 3 3.1 Selective Laser Sintering--Polycarbonate Material .................................................................. 4 3.2 Selective Laser Sintering--Trueform Polyamide ...................................................................... 4 3.3 Fused Deposition Modeling--Investment Casting Wax ............................................................ 5 3.4 Laminated Object Manufacturing--High-Performance Paper .................................................. 6 3.5 Three-Dimensional Printing--Starch (Cellulose) ..................................................................... -
Tutorial: Rapid Prototyping Technologies
OPTI 521 Wei-Ren Ng Tutorial: Rapid Prototyping Technologies 1. Introduction Rapid prototyping (RP) is a new manufacturing technique that allows for fast fabrication of computer models designed with three-dimension (3D) computer aided design (CAD) software. RP is used in a wide variety of industries, from shoe to car manufacturers. This technique allows for fast realizations of ideas into functioning prototypes, shortening the design time, leading towards successful final products. RP technique comprise of two general types: additive and subtractive, each of which has its own pros and cons. Subtractive type RP or traditional tooling manufacturing process is a technique in which material is removed from a solid piece of material until the desired design remains. Examples of this type of RP includes traditional milling, turning/lathing or drilling to more advanced versions - computer numerical control (CNC), electric discharge machining (EDM). Additive type RP is the opposite of subtractive type RP. Instead of removing material, material is added layer upon layer to build up the desired design such as stereolithography, fused deposition modeling (FDM), and 3D printing. This tutorial will introduce additive type RP techniques: Selective Laser Sintering (SLS), StereoLithography Apparatus (SLA), FDM, Inkjet based printing. It will also cover how to properly prepare 3D CAD models for fabrication with RP techniques. 2. Advantages and disadvantages of rapid prototyping Subtractive type RP is typically limited to simple geometries due to the tooling process where material is removed. This type of RP also usually takes a longer time but the main advantage is that the end product is fabricated in the desired material. -
Binding Mechanisms in Selective Laser Sintering and Selective Laser Melting Prof
Binding Mechanisms in Selective Laser Sintering and Selective Laser Melting Prof. Dr. Ir. J.P. Kruth1, Ir. P. Mercelis1, Prof. Dr. Ir. L. Froyen2, Ir. Marleen Rombouts 2 1 University of Leuven (K.U.Leuven), Dept. of Mechanical Engineering, Division PMA 2 University of Leuven (K.U.Leuven), Dept. of Metallurgy and Materials Engineering Reviewed, accepted August 4, 2004 Abstract Layer Manufacturing (LM) technologies like Selective Laser Sintering (SLS) were developed in the late 80’s as techniques for Rapid Prototyping (RP). Today, SLS - as well as its derived technology Selective Laser Melting (SLM) - is used as well for prototyping, tooling and manufacturing purposes. This widening of applications is caused mainly by the possibility to process a large variety of materials, resulting in a broad range of physical and mechanical properties. This paper presents a survey of the various binding mechanisms in SLS and SLM, which are responsible for the broad range of materials and applications. Basic binding mechanisms involve solid state sintering, chemically induced binding, liquid phase sintering, partial melting and full melting. Many subcategories can be distinguished based on the type of structural or binder powder composition: single component powder grains (single material or alloy), composite powder grains, mixtures of different powder grains, distinct binder material (sacrificial or permanent), etc. The paper will explain how these binding mechanisms apply for sintering various types of materials: plastics, metal, ceramics and composites (e.g. glass reinforced polymers, cermets, hardmetals, etc.). It gives a survey of research done at the University of Leuven, Belgium, as well as at other European and non-European organizations.