Wireless Passive Surface Acoustic Wave (SAW) Sensing System
Total Page:16
File Type:pdf, Size:1020Kb
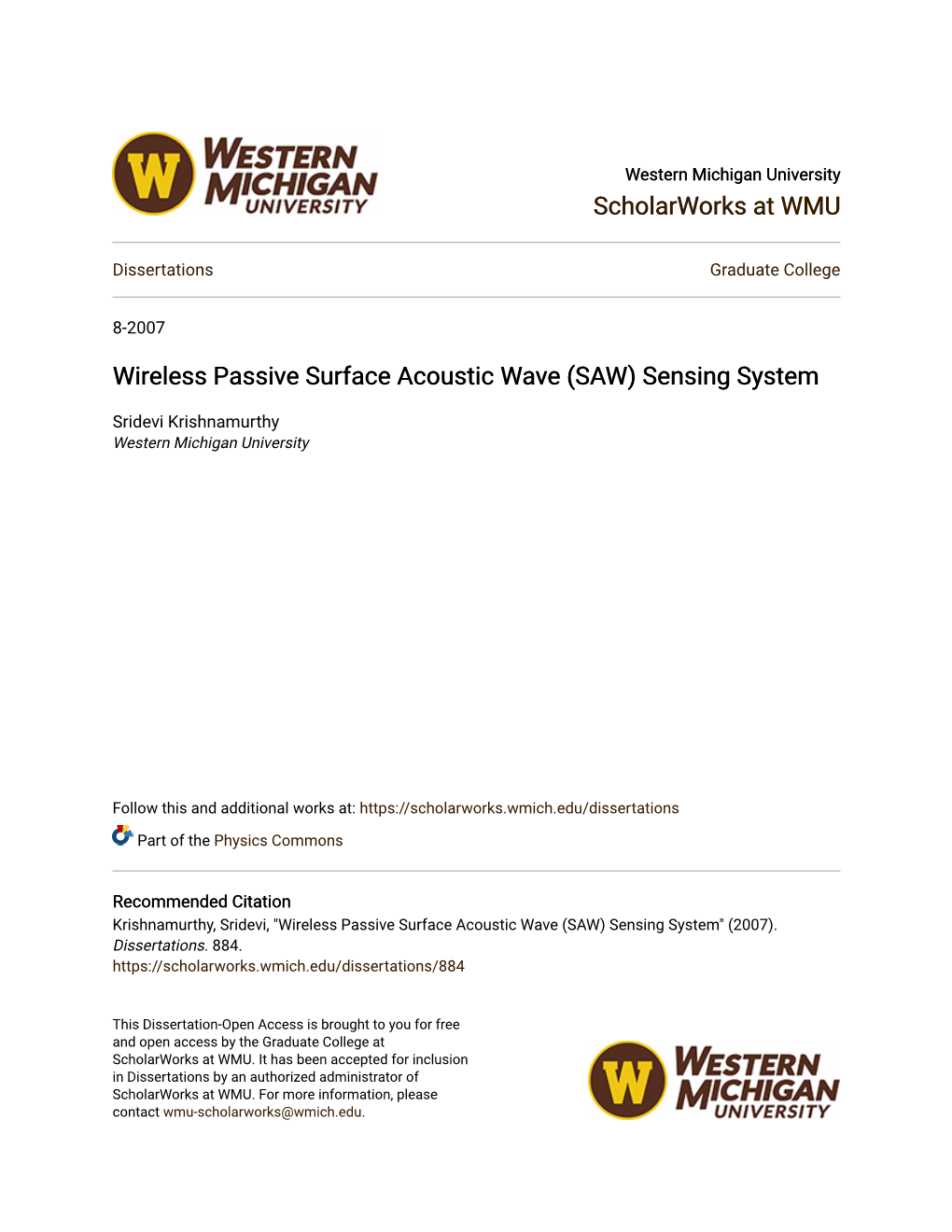
Load more
Recommended publications
-
Surface Acoustic Wave Driven Microfluidics – a Review
Surface Acoustic Wave Driven Microfluidics – A Review Author Luong, TD, Nguyen, NT Published 2010 Journal Title Micro and Nanosystems DOI https://doi.org/10.2174/1876402911002030217 Copyright Statement © 2010 Bentham Science Publishers. This is the author-manuscript version of this paper. Reproduced in accordance with the copyright policy of the publisher. Please refer to the journal website for access to the definitive, published version. Downloaded from http://hdl.handle.net/10072/62189 Griffith Research Online https://research-repository.griffith.edu.au Surface Acoustic Wave Driven Microfluidics Trung-Dung Luong and Nam-Trung Nguyen* School of Mechanical and Aerospace Engineering, Nanyang Technological University, 50 Nanyang Avenue, Singapore, 639798 *Address correspondence to this author at the School of Mechanical and Aerospace Engineering, Nanyang Technological University, 50 Nanyang Avenue, Singapore, 639798 E-mail: [email protected] Tel: (+65) 67904457 Fax: (+65) 67911859 Abstract: This paper presents a systematic overview on the recent works on surface acoustic wave (SAW) driven microfluidics. SAW microfluidics is based on acoustic streaming induced by leaky SAW radiation into a liquid. The development of this field attracts attention from microfluidic research community due to its rapid actuation, programmable capability, simple and yet efficient operation. In our paper, SAW microfluidic applications are categorized into droplet-based applications and continuous-flow applications. Droplet is actuated into unique behaviours depending on the applied SAW power. A wide range of droplet based applications have been employed utilizing these behaviours. In continuous-flow system, applications are further categorized based on the interaction of travelling SAW and standing SAW with the bulk liquid. Finally, future perspectives of SAW driven microfluidics are discussed. -
Eel 4915 Senior Design Ii Department of Electrical & Computer
EEL 4915 SENIOR DESIGN II DEPARTMENT OF ELECTRICAL & COMPUTER ENGINEERING UNIVERSITY OF CENTRAL FLORIDA Senior Design II Term Paper ACDC – A Helping Hand – Group A Akash Jinandra – EE & CpE Carlos Cuesta – EE & CpE Devin Defond – EE Chang Ching Wu – EE Table of Contents 1. Executive Summary.................................................................................................................. 1 2. Project Description.................................................................................................................... 2 2.1. Motivation ........................................................................................................................... 2 2.2. Project Specifications........................................................................................................ 2 2.2.1. Overall Block Diagram ............................................................................................... 2 2.2.1.1. Hardware .............................................................................................................. 3 2.2.1.1.1. Hardware of Arm .......................................................................................... 3 2.2.1.1.2. Hardware of Sleeve ..................................................................................... 4 2.2.1.2. Software ............................................................................................................... 5 2.2.1.2.1. Software of Arm .......................................................................................... -
Surface Acoustic Wave Optical Modulation by Stanley Seokjong Hong
Surface Acoustic Wave Optical Modulation by Stanley Seokjong Hong Submitted to the Department of Electrical Engineering and Computer Science in partial fulfillment of the requirements for the degree of Master of Engineering in Electrical Engineering and Computer Science at the MASSACHUSETTS INSTITUTE OF TECHNOLOGY February 2001 @ Stanley Seokjong Hong, MMI. All rights reserved. BARKER The author hereby grants to MIT permission to reproduce and distribute publicly paper and electronic copies of this thesis document in whole or in part. 4~ ~ WUTE OF T 3CHNOL2GY rJUL 11 2 LIBRARIES A uthor ............................ .. .... Department of Electrical E ixiering and Computer Science February, 2 2001 C ertified by ..... ................. .. ....................... Dennis M. Freeman Associate Professor Thpsps Supervisor Accepted by........... .. Arthur C. Smith Chairman, Department Committee on Graduate Students Surface Acoustic Wave Optical Modulation by Stanley Seokjong Hong Submitted to the Department of Electrical Engineering and Computer Science on February, 2 2001, in partial fulfillment of the requirements for the degree of Master of Engineering in Electrical Engineering and Computer Science Abstract The lack of refractive optical elements at ultraviolet (UV) and X ray wavelengths has made the construction of high-performance optical systems such as microscopes and photolithography projectors difficult at wavelengths below 200 nm. Synthetic aper- ture optical systems potentially eliminate the need for refractive elements by using sets of electronically modulated laser beams to synthesize the front apertures of high- performance optical systems. However, the optical modulators typically used with synthetic aperture optics are themselves refractive elements. As a solution, this the- sis developed surface acoustic wave optical modulation, an all-reflective technique for optical modulation that in principle scales from visible to UV and X ray wavelengths and is suitable for use in synthetic aperture optical systems. -
The 2019 Surface Acoustic Waves Roadmap
Journal of Physics D: Applied Physics TOPICAL REVIEW • OPEN ACCESS The 2019 surface acoustic waves roadmap To cite this article: Per Delsing et al 2019 J. Phys. D: Appl. Phys. 52 353001 View the article online for updates and enhancements. This content was downloaded from IP address 130.183.90.175 on 21/08/2019 at 14:25 IOP Journal of Physics D: Applied Physics Journal of Physics D: Applied Physics J. Phys. D: Appl. Phys. J. Phys. D: Appl. Phys. 52 (2019) 353001 (40pp) https://doi.org/10.1088/1361-6463/ab1b04 52 Topical Review 2019 The 2019 surface acoustic waves roadmap © 2019 IOP Publishing Ltd Per Delsing1, Andrew N Cleland2, Martin J A Schuetz3, JPAPBE Johannes Knörzer4 , Géza Giedke5,6 , J Ignacio Cirac4 , Kartik Srinivasan7, Marcelo Wu7,8, Krishna Coimbatore Balram7,9, 10 10 11 353001 Christopher Bäuerle , Tristan Meunier , Christopher J B Ford , Paulo V Santos12 , Edgar Cerda-Méndez13 , Hailin Wang14 , Hubert J Krenner15,16,30 , Emeline D S Nysten15, P Delsing et al Matthias Weiß15, Geoff R Nash17 , Laura Thevenard18 , Catherine Gourdon18 , Pauline Rovillain18, Max Marangolo18 , Jean-Yves Duquesne18 , Gerhard Fischerauer19 , Werner Ruile20, Alexander Reiner15, Ben Paschke15, Dmytro Denysenko15,28, 15 15,16 21 Printed in the UK Dirk Volkmer , Achim Wixforth , Henrik Bruus , Martin Wiklund22, Julien Reboud23 , Jonathan M Cooper23 , YongQing Fu24 , Manuel S Brugger15, Florian Rehfeldt25 and JPD Christoph Westerhausen15,16,26,27,28 1 Microtechnology and Nanoscience, Chalmers University of Technology, 412 96 Göteborg, Sweden 10.1088/1361-6463/ab1b04 -
Experiences in Using Open Source Software for Teaching Electronic Engineering CAD
Experiences in Using Open Source Software for Teaching Electronic Engineering CAD Dr Simon Busbridge1 & Dr Deshinder Singh Gill School of Computing, Engineering and Mathematics, University of Brighton, Brighton BN2 4GJ [email protected] Abstract Embedded systems and simulation distinguish modern professional electronic engineering from that learnt at school. First year undergraduates typically have little appreciation of engineering software capabilities and file handling beyond elementary word processing. This year we expedited blended teaching through the experiential based learning process via open source engineering software. Students engaged with the entire electronic engineering product creation process from inception, performance simulation, printed circuit board design, manufacture and assembly, to cabinet design and complete finished product. Currently students learn software skills using a mixture of electronic and mechanical engineering software packages. Although these have professional capability they are not available off-campus and are sometimes surprisingly poor in simulating real world devices. In this paper we report use of LTspice, FreePCB and OpenSCAD for the learning and teaching of analogue electronics simulation and manufacture. Comparison of the software options, the type of tasks undertaken, examples of student assignments and outputs, and learning achieved are presented. Examples of assignment based learning, integration between the open source packages and difficulties encountered are discussed. Evaluation of student attitudes and responses to this method of learning and teaching are also discussed, and the educational advantages of using this approach compared to the use of commercial packages is highlighted. Introduction Most educational establishments use software for simulating or designing engineering. Most commercial packages come with an academic licence which restricts access to on-site computers. -
Analysis and Design of Miniaturized Rf Saw Duplexer Package
University of Central Florida STARS Electronic Theses and Dissertations, 2004-2019 2005 Analysis And Design Of Miniaturized Rf Saw Duplexer Package Hao Dong University of Central Florida Part of the Electrical and Electronics Commons Find similar works at: https://stars.library.ucf.edu/etd University of Central Florida Libraries http://library.ucf.edu This Doctoral Dissertation (Open Access) is brought to you for free and open access by STARS. It has been accepted for inclusion in Electronic Theses and Dissertations, 2004-2019 by an authorized administrator of STARS. For more information, please contact [email protected]. STARS Citation Dong, Hao, "Analysis And Design Of Miniaturized Rf Saw Duplexer Package" (2005). Electronic Theses and Dissertations, 2004-2019. 441. https://stars.library.ucf.edu/etd/441 ANALYSIS AND DESIGN OF MINIATURIZED RF SAW DUPLEXER PACKAGE by HAO DONG Eng.D. Zhejiang University, 1997 M.S. Northwestern Polytechnical University, 1994 B.S. Northwestern Polytechnical University, 1991 A dissertation submitted in partial fulfillment of the requirements for the degree of Doctor of Philosophy in the Department of Electrical and Computer Engineering in the College of Engineering and Computer Science at the University of Central Florida Orlando, Florida Summer Term 2005 Major Professor: Thomas X. Wu © 2005 Hao Dong ii ABSTRACT This dissertation provides a comprehensive methodology for accurate analysis and design of miniaturized radio frequency (RF) surface acoustic wave (SAW) duplexer package. Full-wave analysis based on the three dimensional (3-D) finite element method (FEM) is successfully applied to model the package. The die model is obtained by combining the acoustics and die busbars parasitics models. -
Tinycad Free Download
Tinycad free download TinyCAD is a program for drawing electrical circuit diagrams commonly known as schematic drawings. It supports PCB layout programs with several netlist formats and can also produce SPICE simulation netlists. It is also often used to draw one-line diagrams, block diagrams, and. TinyCAD, free and safe download. TinyCAD latest version: Get help drawing professional-looking circuit diagrams. TinyCAD is a good, free software only. Download TinyCAD for Windows now from Softonic: % safe and virus free. More than downloads this month. Download TinyCAD latest version TinyCAD - TinyCAD is a program for drawing circuit diagrams commonly known as schematic drawings. It supports standard and custom symbol libraries. TinyCAD allows you to design basic or complex electrical or electronic circuit diagrams. It has symbols distributed in 42 libraries which. TinyCAD is fully open-source so you can use it for free and you can to put the original drawing on your web-site, with a link to TinyCAD for download, this isn't. 9/10 - Download TinyCAD Free. Download TinyCAD free and you will be able to design and develop printed circuit boards. TinyCAD can also be used to check. TinyCad is a software application that provides you tools and other features that helps you make circuit diagrams in just a matter of minutes. You could either add. Download TinyCAD for free. TinyCAD is an open source schematic capture program for MS Windows. Free Download TinyCAD Build - Create schematic drawings with the help of the extensive built-in library and check for design. Download TinyCAD Simple drafting device for multiple professional purposes. -
Freepcb User Guide Version 1.4
FreePCB User Guide Version 1.4 Allan Wright April 14, 2007 FreePCB User Guide - Ver 1.4 1 21 Apr 07 Table of Contents 1. Introduction...........................................................................3 5.15.1 Copper Area Cutouts.......................................... ........57 2. User Guide History................................................................4 5.16 Text...................................................................... ...............58 2.1 What's new in version 1.4................................... ....................4 5.17 Solder Mask Cutouts................................................. ..........59 2.2 What's new in version 1.2................................... ....................4 5.18 Groups.......................................................... ......................60 3. Installing FreePCB................................................................6 5.19 Design Rule Checking........................................................ .62 4. Overview of the PCB Design Process...................................7 5.20 Exporting Drill and Gerber Files................................ .........69 5.20.1 Creating Files...................................................... .......69 4.1 Schematic Diagram....................................................... ..........7 5.20.2 Viewing and Printing Files................................ .........72 4.2 Specifying Parts, Packages and Pin Names.............................7 5.20.3 Drill Sizes................................................. .................73 -
Multiplexed Photometry and Fluorimetry Using Multiple Frequency Channels Khaled M
Wayne State University Wayne State University Dissertations 1-2-2013 Multiplexed Photometry And Fluorimetry Using Multiple Frequency Channels Khaled M. Dadesh Wayne State University, Follow this and additional works at: http://digitalcommons.wayne.edu/oa_dissertations Part of the Electrical and Computer Engineering Commons Recommended Citation Dadesh, Khaled M., "Multiplexed Photometry And Fluorimetry Using Multiple Frequency Channels" (2013). Wayne State University Dissertations. Paper 757. This Open Access Dissertation is brought to you for free and open access by DigitalCommons@WayneState. It has been accepted for inclusion in Wayne State University Dissertations by an authorized administrator of DigitalCommons@WayneState. MULTIPLEXED PHOTOMETRY AND FLUORIMETRY USING MULTIPLE FREQUENCY CHANNELS by KHALED M. DADESH DISSERTATION Submitted to the Graduate School of Wayne State University, Detroit, Michigan in partial fulfillment of the requirements for the degree of DOCTOR OF PHILOSOPHY 2013 MAJOR: ELECTRICAL ENGINEERING Approved by: ________________________________ Advisor Date ——————————————————— ——————————————————— ——————————————————— © COPYRIGHT BY KHALED M. DADESH 2013 All Rights Reserved DEDICATION I dedicate my humble work to the soul of my father who encouraged and supported me to be in the right path, my mother who raised me and still prays for me to be a successful person to people and community, my wife and kids, and all my family members and friends who gave me support and help to finish my dissertation. ii ACKNOWLEDGEMENTS I would like to express my sincere appreciation to Dr. Amar Basu, who contributed tremendous time and valuable support to my research. I also appreciate Dr. Yang Zhao, Dr. Mark Ming-Cheng, and Dr. Jessica Back for their constructive comments and precious suggestions and support. -
Wireless and Batteryless Surface Acoustic Wave Sensors for High Temperature Environments
WIRELESS AND BATTERYLESS SURFACE ACOUSTIC WAVE SENSORS FOR HIGH TEMPERATURE ENVIRONMENTS T. Aubert1, O. Elmazria1,2, M.B. Assouar1 1Institut Jean Lamour (IJL), UMR 7198 CNRS-Nancy University 54506 Vandoeuvre lès Nancy, France 2Ecole Supérieur des Sciences et Techniques d’Ingénieurs de Nancy, 54506 Vandœuvre-lès-Nancy, France e-mail : [email protected] Abstract I. INTRODUCTION Surface acoustic wave (SAW) devices are Surface acoustic wave (SAW) devices are used for widely used as filter, resonator or delay line in several years as components for signal processing in electronic systems in a wide range of applications: communication systems. SAW devices are for mobile communication, TVs, radar, stable resonator example widely used as bandpass filter and resonator for clock generation, etc. The resonance frequency and in mobile phones [1,2]. Far from being confined to the delay line of SAW devices are depending on the properties of materials forming the device and could be this single use, SAW are or may find applications in very sensitive to the physical parameters of the many other areas. The SAW can be used to generate environment. Since SAW devices are more and more movement in microfluidics leading to mixe move, and used as sensor for a large variety of area: gas, pressure, heat very low quantities of liquid in the range of force, temperature, strain, radiation, etc. The sensors nanoliter [3]. They can also be used in chemistry, based SAW present the advantage to be passive where some properties of the SAW in terms of (batteryless) and/or wireless. These interesting heterogeneous catalysis could be identified. -
Materials, Design, and Characteristics of Bulk Acoustic Wave Resonator: a Review
micromachines Review Materials, Design, and Characteristics of Bulk Acoustic Wave Resonator: A Review Yan Liu, Yao Cai, Yi Zhang, Alexander Tovstopyat , Sheng Liu and Chengliang Sun * Institute of Technological Sciences, Wuhan University, Wuhan 430072, China; [email protected] (Y.L.); [email protected] (Y.C.); [email protected] (Y.Z.); [email protected] (A.T.); [email protected] (S.L.) * Correspondence: [email protected]; Tel.: +86-027-68776588 Received: 17 May 2020; Accepted: 18 June 2020; Published: 28 June 2020 Abstract: With the rapid commercialization of fifth generation (5G) technology in the world, the market demand for radio frequency (RF) filters continues to grow. Acoustic wave technology has been attracting great attention as one of the effective solutions for achieving high-performance RF filter operations while offering low cost and small device size. Compared with surface acoustic wave (SAW) resonators, bulk acoustic wave (BAW) resonators have more potential in fabricating high- quality RF filters because of their lower insertion loss and better selectivity in the middle and high frequency bands above 2.5 GHz. Here, we provide a comprehensive review about BAW resonator researches, including materials, structure designs, and characteristics. The basic principles and details of recently proposed BAW resonators are carefully investigated. The materials of poly-crystalline aluminum nitride (AlN), single crystal AlN, doped AlN, and electrode are also analyzed and compared. Common approaches to enhance the performance of BAW resonators, suppression of spurious mode, low temperature sensitivity, and tuning ability are introduced with discussions and suggestions for further improvement. Finally, by looking into the challenges of high frequency, wide bandwidth, miniaturization, and high power level, we provide clues to specific materials, structure designs, and RF integration technologies for BAW resonators. -
Flexible Strain Detection Using Surface Acoustic Waves: Fabrication and Tests
PhD Dissertations and Master's Theses 12-2020 Flexible Strain Detection Using Surface Acoustic Waves: Fabrication and Tests Rishikesh Srinivasaraghavan Govindarajan Follow this and additional works at: https://commons.erau.edu/edt Part of the Aerospace Engineering Commons Scholarly Commons Citation Govindarajan, Rishikesh Srinivasaraghavan, "Flexible Strain Detection Using Surface Acoustic Waves: Fabrication and Tests" (2020). PhD Dissertations and Master's Theses. 557. https://commons.erau.edu/edt/557 This Thesis - Open Access is brought to you for free and open access by Scholarly Commons. It has been accepted for inclusion in PhD Dissertations and Master's Theses by an authorized administrator of Scholarly Commons. For more information, please contact [email protected]. FLEXIBLE STRAIN DETECTION USING SURFACE ACOUSTIC WAVES: FABRICATION AND TESTS By Rishikesh Srinivasaraghavan Govindarajan A Thesis Submitted to the Faculty of Embry-Riddle Aeronautical University In Partial Fulfillment of the Requirements for the Degree of Master of Science in Aerospace Engineering December 2020 Embry-Riddle Aeronautical University Daytona Beach, Florida ii FLEXIBLE STRAIN DETECTION USING SURFACE ACOUSTIC WAVES: FABRICATION AND TESTS By Rishikesh Srinivasaraghavan Govindarajan This Thesis was prepared under the direction of the candidate’s Thesis Committee Chair, Dr. Daewon Kim, Department of Aerospace Engineering, and has been approved by the members of Thesis Committee. It was submitted to the Office of the Senior Vice President for Academic Affairs and Provost, and was accepted in the partial fulfillment of the requirements for the Degree of Master of Science in Aerospace Engineering. THESIS COMMITTEE Digitally signed by Daewon Kim Daewon Kim Date: 2020.12.03 11:46:45 -05'00' Chairman, Dr.