Classroom Activities in Aerodynamics
Total Page:16
File Type:pdf, Size:1020Kb
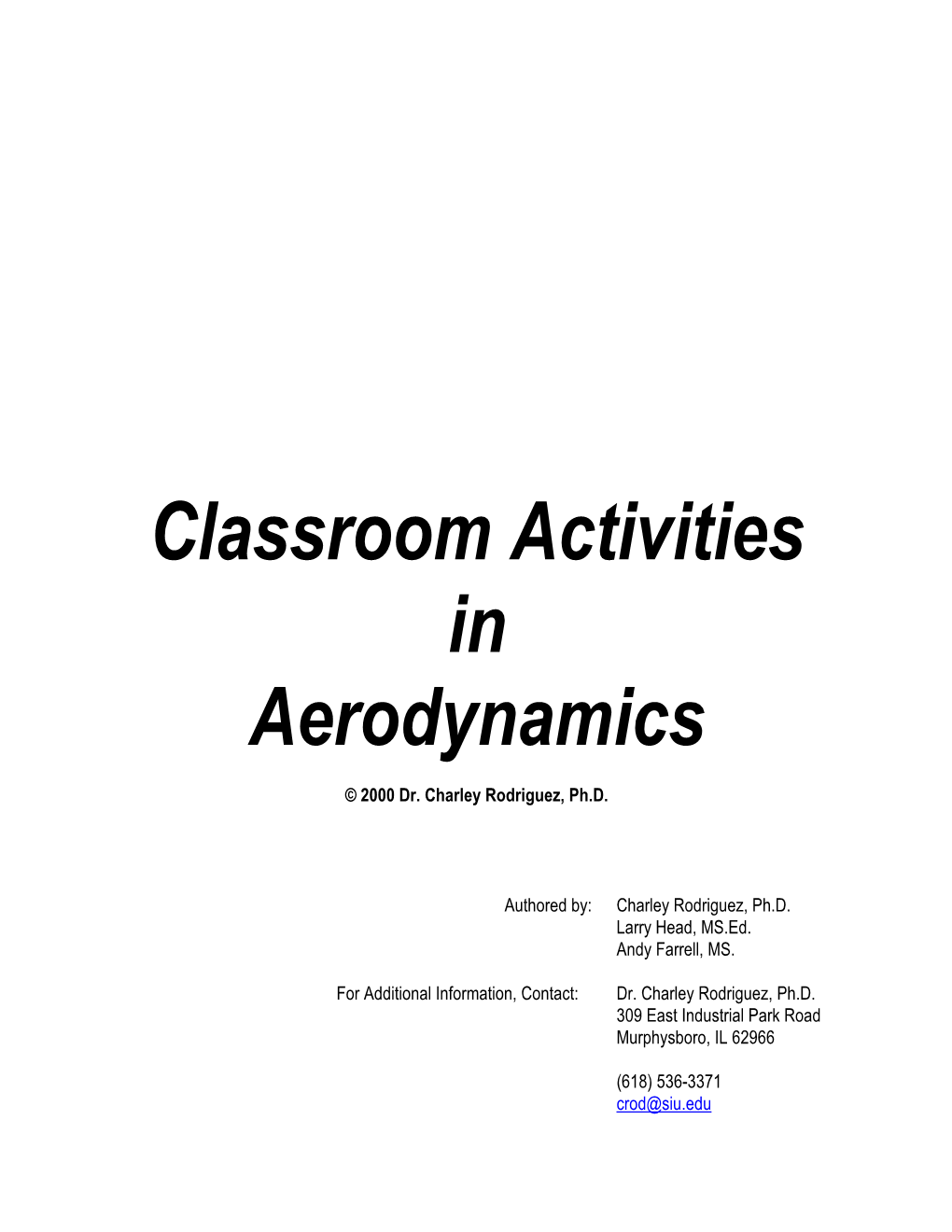
Load more
Recommended publications
-
Experimental Analysis of a Low Cost Lift and Drag Force Measurement System for Educational Sessions
International Research Journal of Engineering and Technology (IRJET) e-ISSN: 2395-0056 Volume: 04 Issue: 09 | Sep -2017 www.irjet.net p-ISSN: 2395-0072 Experimental Analysis of a Low Cost Lift and Drag Force Measurement System for Educational Sessions Asutosh Boro B.Tech National Institute of Technology Srinagar Indian Institute of Science, Bangalore 560012 ---------------------------------------------------------------------***--------------------------------------------------------------------- Abstract - A low cost Lift and Drag force measurement wind- tunnel and used for educational learning with good system was designed, fabricated and tested in wind tunnel accuracy. In addition, an indirect wind tunnel velocity to be used for basic practical lab sessions. It consists of a measurement capability of the designed system was mechanical linkage system, piezo-resistive sensors and tested. NACA airfoil 4209 was chosen as the test subject to NACA Airfoil to test its performance. The system was tested measure its performance and tests were done at various at various velocities and angle of attacks and experimental angles of attack and velocities 11m/s, 12m/s and 14m/s. coefficient of lift and drag were then compared with The force and coefficient results obtained were compared literature values to find the errors. A decent accuracy was with literature data from airfoil tools[1] to find the deduced from the lift data and the considerable error in system’s accuracy. drag was due to concentration of drag forces across a narrow force range and sensor’s fluctuations across that 1.1 Methodology range. It was inferred that drag system will be as accurate as the lift system when the drag forces are large. -
Sailing for Performance
SD2706 Sailing for Performance Objective: Learn to calculate the performance of sailing boats Today: Sailplan aerodynamics Recap User input: Rig dimensions ‣ P,E,J,I,LPG,BAD Hull offset file Lines Processing Program, LPP: ‣ Example.bri LPP_for_VPP.m rigdata Hydrostatic calculations Loading condition ‣ GZdata,V,LOA,BMAX,KG,LCB, hulldata ‣ WK,LCG LCF,AWP,BWL,TC,CM,D,CP,LW, T,LCBfpp,LCFfpp Keel geometry ‣ TK,C Solve equilibrium State variables: Environmental variables: solve_Netwon.m iterative ‣ VS,HEEL ‣ TWS,TWA ‣ 2-dim Netwon-Raphson iterative method Hydrodynamics Aerodynamics calc_hydro.m calc_aero.m VS,HEEL dF,dM Canoe body viscous drag Lift ‣ RFC ‣ CL Residuals Viscous drag Residuary drag calc_residuals_Newton.m ‣ RR + dRRH ‣ CD ‣ dF = FAX + FHX (FORCE) Keel fin drag ‣ dM = MH + MR (MOMENT) Induced drag ‣ RF ‣ CDi Centre of effort Centre of effort ‣ CEH ‣ CEA FH,CEH FA,CEA The rig As we see it Sail plan ≈ Mainsail + Jib (or genoa) + Spinnaker The sail plan is defined by: IMSYC-66 P Mainsail hoist [m] P E Boom leech length [m] BAD Boom above deck [m] I I Height of fore triangle [m] J Base of fore triangle [m] LPG Perpendicular of jib [m] CEA CEA Centre of effort [m] R Reef factor [-] J E LPG BAD D Sailplan modelling What is the purpose of the sails on our yacht? To maximize boat speed on a given course in a given wind strength ‣ Max driving force, within our available righting moment Since: We seek: Fx (Thrust vs Resistance) ‣ Driving force, FAx Fy (Side forces, Sails vs. Keel) ‣ Heeling force, FAy (Mx (Heeling-righting moment)) ‣ Heeling arm, CAE Aerodynamics of sails A sail is: ‣ a foil with very small thickness and large camber, ‣ with flexible geometry, ‣ usually operating together with another sail ‣ and operating at a large variety of angles of attack ‣ Environment L D V Each vertical section is a differently cambered thin foil Aerodynamics of sails TWIST due to e.g. -
How Do Wings Generate Lift? 2
GENERAL ARTICLE How Do Wings Generate Lift? 2. Myths, Approximate Theories and Why They All Work M D Deshpande and M Sivapragasam A cambered surface that is moving forward in a fluid gen- erates lift. To explain this interesting fact in terms of sim- pler models, some preparatory concepts were discussed in the first part of this article. We also agreed on what is an accept- able explanation. Then some popular models were discussed. Some quantitative theories will be discussed in this conclud- ing part. Finally we will tie up all these ideas together and connect them to the rigorous momentum theorem. M D Deshpande is a Professor in the Faculty of Engineering The triumphant vindication of bold theories – are these not the and Technology at M S Ramaiah University of pride and justification of our life’s work? Applied Sciences. Sherlock Holmes, The Valley of Fear Sir Arthur Conan Doyle 1. Introduction M Sivapragasam is an We start here with two quantitative theories before going to the Assistant Professor in the momentum conservation principle in the next section. Faculty of Engineering and Technology at M S Ramaiah University of Applied 1.1 The Thin Airfoil Theory Sciences. This elegant approximate theory takes us further than what was discussed in the last two sections of Part 111, and quantifies the Resonance, Vol.22, No.1, ideas to get expressions for lift and moment that are remarkably pp.61–77, 2017. accurate. The pressure distribution on the airfoil, apart from cre- ating a lift force, leads to a nose-up or nose-down moment also. -
A Concept of the Vortex Lift of Sharp-Edge Delta Wings Based on a Leading-Edge-Suction Analogy Tech Library Kafb, Nm
I A CONCEPT OF THE VORTEX LIFT OF SHARP-EDGE DELTA WINGS BASED ON A LEADING-EDGE-SUCTION ANALOGY TECH LIBRARY KAFB, NM OL3042b NASA TN D-3767 A CONCEPT OF THE VORTEX LIFT OF SHARP-EDGE DELTA WINGS BASED ON A LEADING-EDGE-SUCTION ANALOGY By Edward C. Polhamus Langley Research Center Langley Station, Hampton, Va. NATIONAL AERONAUTICS AND SPACE ADMINISTRATION For sale by the Clearinghouse for Federal Scientific and Technical Information Springfield, Virginia 22151 - Price $1.00 A CONCEPT OF THE VORTEX LIFT OF SHARP-EDGE DELTA WINGS BASED ON A LEADING-EDGE-SUCTION ANALOGY By Edward C. Polhamus Langley Research Center SUMMARY A concept for the calculation of the vortex lift of sharp-edge delta wings is pre sented and compared with experimental data. The concept is based on an analogy between the vortex lift and the leading-edge suction associated with the potential flow about the leading edge. This concept, when combined with potential-flow theory modified to include the nonlinearities associated with the exact boundary condition and the loss of the lift component of the leading-edge suction, provides excellent prediction of the total lift for a wide range of delta wings up to angles of attack of 20° or greater. INTRODUCTION The aerodynamic characteristics of thin sharp-edge delta wings are of interest for supersonic aircraft and have been the subject of theoretical and experimental studies for many years in both the subsonic and supersonic speed ranges. Of particular interest at subsonic speeds has been the formation and influence of the leading-edge separation vor tex that occurs on wings having sharp, highly swept leading edges. -
Computational Fluid Dynamic Analysis of Scaled Hypersonic Re-Entry Vehicles
Computational Fluid Dynamic Analysis of Scaled Hypersonic Re-Entry Vehicles A project presented to The Faculty of the Department of Aerospace Engineering San Jose State University In partial fulfillment of the requirements for the degree Master of Science in Aerospace Engineering by Simon H.B. Sorensen March 2019 approved by Dr. Periklis Papadopoulous Faculty Advisor 1 i ABSTRACT With the advancement of technology in space, reusable re-entry space planes have become a focus point with their ability to save materials and utilize existing flight data. Their ability to not only supply materials to space stations or deploy satellites, but also in atmosphere flight makes them versatile in their deployment and recovery. The existing design of vehicles such as the Space Shuttle Orbiter and X-37 Orbital Test Vehicle can be used to observe the effects of scaling existing vehicle geometry and how it would operate in identical conditions to the full-size vehicle. These scaled vehicles, if viable, would provide additional options depending on mission parameters without losing the advantages of reusable re-entry space planes. 2 Table of Contents Abstract . i Nomenclature . .1 1. Introduction. .1 2. Literature Review. 2 2.1 Space Shuttle Orbiter. 2 2.2 X-37 Orbital Test Vehicle. 3 3. Assumptions & Equations. 3 3.1 Assumptions. 3 3.2 Equations to Solve. 4 4. Methodology. 5 5. Base Sized Vehicles. 5 5.1 Space Shuttle Orbiter. 5 5.2 X-37. 9 6. Scaled Vehicles. 11 7. Simulations. 12 7.1 Initial Conditions. 12 7.2 Initial Test Utilizing X-37. .13 7.3 X-37 OTV. -
Lift for a Finite Wing
Lift for a Finite Wing • all real wings are finite in span (airfoils are considered as infinite in the span) The lift coefficient differs from that of an airfoil because there are strong vortices produced at the wing tips of the finite wing, which trail downstream. These vortices are analogous to mini-tornadoes, and like a tornado, they reach out in the flow field and induce changes in the velocity and pressure fields around the wing Imagine that you are standing on top of the wing you will feel a downward component of velocity over the span of the wing, induced by the vortices trailing downstream from both tips. This downward component of velocity is called downwash. The local downwash at your location combines with the free-stream relative wind to produce a local relative wind. This local relative wind is inclined below the free- stream direction through the induced angle of attack α i . Hence, you are effectively feeling an angle of attack different from the actual geometric angle of attack of the wing relative to the free stream; you are sensing a smaller angle of attack. For Example if the wing is at a geometric angle of attack of 5°, you are feeling an effective angle of attack which is smaller. Hence, the lift coefficient for the wing is going to be smaller than the lift coefficient for the airfoil. This explains the answer given to the question posed earlier. High-Aspect-Ratio Straight Wing The classic theory for such wings was worked out by Prandtl during World War I and is called Prandtl's lifting line theory. -
Human Powered Hydrofoil Design & Analytic Wing Optimization
Human Powered Hydrofoil Design & Analytic Wing Optimization Andy Gunkler and Dr. C. Mark Archibald Grove City College Grove City, PA 16127 Email: [email protected] Abstract – Human powered hydrofoil watercraft can have marked performance advantages over displacement-hull craft, but pose significant engineering challenges. The focus of this hydrofoil independent research project was two-fold. First of all, a general vehicle configuration was developed. Secondly, a thorough optimization process was developed for designing lifting foils that are highly efficient over a wide range of speeds. Given a well-defined set of design specifications, such as vehicle weight and desired top speed, an optimal horizontal, non-surface- piercing wing can be engineered. Design variables include foil span, area, planform shape, and airfoil cross section. The optimization begins with analytical expressions of hydrodynamic characteristics such as lift, profile drag, induced drag, surface wave drag, and interference drag. Research of optimization processes developed in the past illuminated instances in which coefficients of lift and drag were assumed to be constant. These shortcuts, made presumably for the sake of simplicity, lead to grossly erroneous regions of calculated drag. The optimization process developed for this study more accurately computes profile drag forces by making use of a variable coefficient of drag which, was found to be a function of the characteristic Reynolds number, required coefficient of lift, and airfoil section. At the desired cruising speed, total drag is minimized while lift is maximized. Next, a strength and rigidity analysis of the foil eliminates designs for which the hydrodynamic parameters produce structurally unsound wings. Incorporating constraints on minimum takeoff speed and power required to stay foil-borne isolates a set of optimized design parameters. -
Aerodyn Theory Manual
January 2005 • NREL/TP-500-36881 AeroDyn Theory Manual P.J. Moriarty National Renewable Energy Laboratory Golden, Colorado A.C. Hansen Windward Engineering Salt Lake City, Utah National Renewable Energy Laboratory 1617 Cole Boulevard, Golden, Colorado 80401-3393 303-275-3000 • www.nrel.gov Operated for the U.S. Department of Energy Office of Energy Efficiency and Renewable Energy by Midwest Research Institute • Battelle Contract No. DE-AC36-99-GO10337 January 2005 • NREL/TP-500-36881 AeroDyn Theory Manual P.J. Moriarty National Renewable Energy Laboratory Golden, Colorado A.C. Hansen Windward Engineering Salt Lake City, Utah Prepared under Task No. WER4.3101 and WER5.3101 National Renewable Energy Laboratory 1617 Cole Boulevard, Golden, Colorado 80401-3393 303-275-3000 • www.nrel.gov Operated for the U.S. Department of Energy Office of Energy Efficiency and Renewable Energy by Midwest Research Institute • Battelle Contract No. DE-AC36-99-GO10337 NOTICE This report was prepared as an account of work sponsored by an agency of the United States government. Neither the United States government nor any agency thereof, nor any of their employees, makes any warranty, express or implied, or assumes any legal liability or responsibility for the accuracy, completeness, or usefulness of any information, apparatus, product, or process disclosed, or represents that its use would not infringe privately owned rights. Reference herein to any specific commercial product, process, or service by trade name, trademark, manufacturer, or otherwise does not necessarily constitute or imply its endorsement, recommendation, or favoring by the United States government or any agency thereof. The views and opinions of authors expressed herein do not necessarily state or reflect those of the United States government or any agency thereof. -
Upwind Sail Aerodynamics : a RANS Numerical Investigation Validated with Wind Tunnel Pressure Measurements I.M Viola, Patrick Bot, M
Upwind sail aerodynamics : A RANS numerical investigation validated with wind tunnel pressure measurements I.M Viola, Patrick Bot, M. Riotte To cite this version: I.M Viola, Patrick Bot, M. Riotte. Upwind sail aerodynamics : A RANS numerical investigation validated with wind tunnel pressure measurements. International Journal of Heat and Fluid Flow, Elsevier, 2012, 39, pp.90-101. 10.1016/j.ijheatfluidflow.2012.10.004. hal-01071323 HAL Id: hal-01071323 https://hal.archives-ouvertes.fr/hal-01071323 Submitted on 8 Oct 2014 HAL is a multi-disciplinary open access L’archive ouverte pluridisciplinaire HAL, est archive for the deposit and dissemination of sci- destinée au dépôt et à la diffusion de documents entific research documents, whether they are pub- scientifiques de niveau recherche, publiés ou non, lished or not. The documents may come from émanant des établissements d’enseignement et de teaching and research institutions in France or recherche français ou étrangers, des laboratoires abroad, or from public or private research centers. publics ou privés. I.M. Viola, P. Bot, M. Riotte Upwind Sail Aerodynamics: a RANS numerical investigation validated with wind tunnel pressure measurements International Journal of Heat and Fluid Flow 39 (2013) 90–101 http://dx.doi.org/10.1016/j.ijheatfluidflow.2012.10.004 Keywords: sail aerodynamics, CFD, RANS, yacht, laminar separation bubble, viscous drag. Abstract The aerodynamics of a sailing yacht with different sail trims are presented, derived from simulations performed using Computational Fluid Dynamics. A Reynolds-averaged Navier- Stokes approach was used to model sixteen sail trims first tested in a wind tunnel, where the pressure distributions on the sails were measured. -
6.2 Understanding Flight
6.2 - Understanding Flight Grade 6 Activity Plan Reviews and Updates 6.2 Understanding Flight Objectives: 1. To understand Bernoulli’s Principle 2. To explain drag and how different shapes influence it 3. To describe how the results of similar and repeated investigations testing drag may vary and suggest possible explanations for variations. 4. To demonstrate methods for altering drag in flying devices. Keywords/concepts: Bernoulli’s Principle, pressure, lift, drag, angle of attack, average, resistance, aerodynamics Curriculum outcomes: 107-9, 204-7, 205-5, 206-6, 301-17, 301-18, 303-32, 303-33. Take-home product: Paper airplane, hoop glider Segment Details African Proverb and Cultural “The bird flies, but always returns to Earth.” Gambia Relevance (5min.) Have any of you ever been on an airplane? Have you ever wondered how such a heavy aircraft can fly? Introduce Bernoulli’s Principle and drag. Pre-test Show this video on Bernoulli’s Principle: (10 min.) https://www.youtube.com/watch?v=bv3m57u6ViE Note: To gain the speed so lift can be created the plane has to overcome the force of drag; they also have to overcome this force constantly in flight. Therefore, planes have been designed to reduce drag Demo 1 Use the students to demonstrate the basic properties of (10 min.) Bernoulli’s Principle. Activity 2 Students use paper airplanes to alter drag and hypothesize why (30 min.) different planes performed differently Activity 3 Students make a hoop glider to understand the effects of drag (20 min.) on different shaped objects. Post-test Word scramble. (5 min.) https://www.amazon.com/PowerUp-Smartphone-Controlled- Additional idea Paper-Airplane/dp/B00N8GWZ4M Suggested Interpretation of Proverb What comes up must come down Background Information Bernoulli’s Principle Daniel Bernoulli, an eighteenth-century Swiss scientist, discovered that as the velocity of a fluid increases, its pressure decreases. -
CFD Simulations of Flow Over Airfoils: an Analysis of Wind Turbine Blade Aerodynamics
CFD Simulations of Flow over Airfoils: An Analysis of Wind Turbine Blade Aerodynamics By: John Hamilla, Mechanical Engineering Advisor: Maria-Isabel Carnasciali, Ph.D. Abstract Wind turbines are rapidly becoming a hot topic when faced with today’s sustainable energy challenges. As such, attention needs to be turned to analyzing the flow over such structures. Computational Fluid Dynamics (CFD) software was used to study the flow fields surrounding fixed airfoils. The simulations provided data on how air flows past various blade shapes. With more realistic simulations, progress can be made on evaluating unique designs. Introduction turbines are lift devices, as opposed to drag devices. Drag devices rely on the wind to push parts. This is Wind turbines are becoming an increasingly popular relatively inefficient. Lift devices instead use airfoils. solution to generate clean, sustainable, power. This The rotors of this type of wind turbine are shaped to emerging technology was the underlying focus of this create lift as wind flows past. A component of the study. generated lift creates a torque on the blade which causes them to rotate around an axis. With this setup, More specifically, this study aimed at gaining an the rotational speed of the blade can surpass that of understanding of the flow fields around a wind the wind (Wind Energy). turbine structure. Computational Fluid Dynamics (CFD) software was used to simulate air flow past two distinct shapes. Given the flow fields, one could visualize the effects particular shapes have on the air stream. The air flow gives rise to lift and drag forces on the airfoils. -
04 Delta Wings
ExperimentalExperimental AerodynamicsAerodynamics Lecture 4: Delta wing experiments G. Dimitriadis Experimental Aerodynamics Introduction •! In this course we will demonstrate the use of several different experimental aerodynamic methodologies •! The particular application will be the aerodynamics of Delta wings at low airspeeds. •! Delta wings are of particular interest because of their lift generation mechanism. Experimental Aerodynamics Delta wing history •! Until the 1930s the vast majority of aircraft featured rectangular, trapezoidal or elliptical wings. •! Delta wings started being studied in the 1930s by Alexander Lippisch in Germany. •! Lippisch wanted to create tail-less aircraft, and Delta wings were one of the solutions he proposed. Experimental Aerodynamics Delta Lippisch DM-1 Designed as an interceptor jet but never produced. The photos show a glider prototype version. Experimental Aerodynamics High speed flight •! After the war, the potential of Delta wings for supersonic flight was recognized both in the US and the USSR. MiG-21 Convair XF-92 Experimental Aerodynamics Low speed performance •! Although Delta wings are designed for high speeds, they still have to take off and land at small airspeeds. •! It is important to determine the aerodynamic forces acting on Delta wings at low speed. •! The lift generated by such wings are low speeds can be split into two contributions: –! Potential flow lift –! Vortex lift Experimental Aerodynamics Delta wing geometry cb Wing surface: S = 2 2b Aspect ratio: AR = "! c c! b AR Sweep angle: tan ! = = 2c 4 b/2! Experimental Aerodynamics Potential flow lift •! Slender wing theory •! The wind is discretized into transverse segments. •! The flow around each segment is modeled as a 2D flow past a flat plate perpendicular to the free stream Experimental Aerodynamics Slender wing theory •! The problem of calculating the flow around the wing becomes equivalent to calculating the flow around each 2D segment.