Managing Supplier Integration Into Product Development: a Literature Review and Conceptual Model
Total Page:16
File Type:pdf, Size:1020Kb
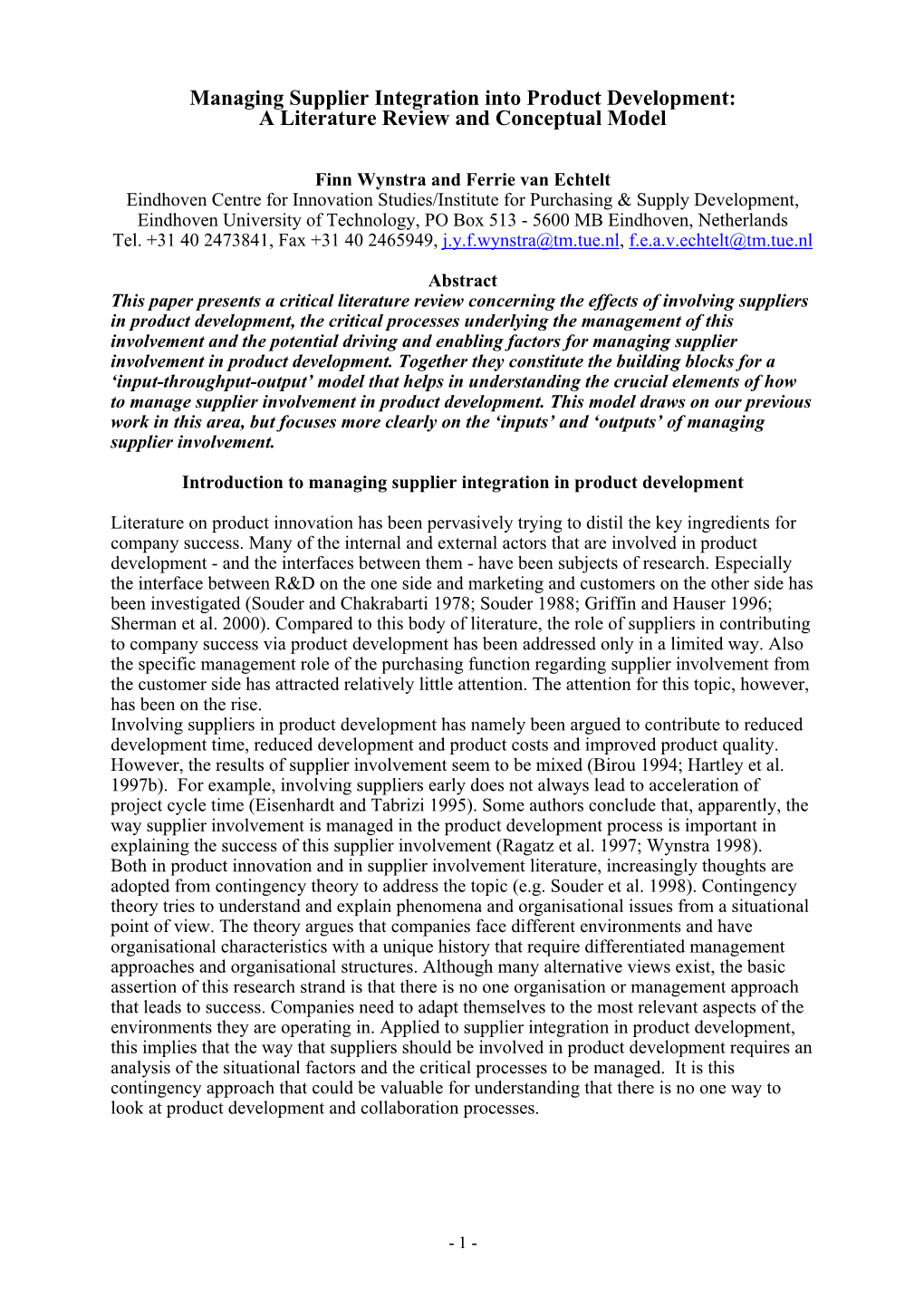
Load more
Recommended publications
-
Product Manager's Desk Reference
ADVANCE PRAISE FOR THE PRODUCT MANAGER’S DESK REFERENCE The Product Manager’s Desk Reference is an encyclopedic refer- ence tool for product managers everywhere. The material is presented in an accessible, logical format with numerous useful templates and outlines. This book should be a prominent addition to every practicing manager’s library. —LINDA G ORCHELS, D IRECTOR, EXECUTIVE M ARKETING, UW–MADISON E XECUTIVE E DUCATION This book very accurately addresses the challenges I have faced dur- ing my time in product management. I only wish such a complete resource as The Product Manager’s Desk Reference had been available to guide me throughout my career. I believe that from now on, this book will stand as an important reference point for all prod- uct management teams. —MARK E LLIOTT, V ICE P RESIDENT P RODUCT M ANAGEMENT, SMITHS D ETECTION This book is the quintessential, comprehensive body of work on prod- uct management. It deserves a spot not only on the desk of every product manager, but within reach of every person involved in the creation, sales, or support of a product. —THERESE PADILLA, P RESIDENT, ASSOCIATION OF I NTERNATIONAL P RODUCT AND M ARKETING M ANAGEMENT Haines strikes the perfect balance between theory and practice, com- bining actionable, practical advice from his extensive professional experience with just the right amount of background for why product managers need to care about the underlying principles. This is an invaluable reference. —TOM S VRCEK, PH .D., M ANAGING D IRECTOR, C ORPORATE E XECUTIVE B OARD Avery readable, well-written book that contains significant insights and provides practical wisdom on the profession of product manage- ment. -
6321 English Iranarze
Challenges in Product Management Product management Summary Complex products and global integrations add additional challenges to a companies product information management process. In order to avoid delays and future issues, even small local projects to automate product information management need to think a bit globally and longer term. This white paper provides the reader with an overview of the typical issues a company has to face when working to integrate and automate its product information, with the idea that understanding the problem is the first step in avoiding or solving it. The problems discussed include: • Data Synchronization and Update • The “Minimum Common Data Structure” Issue • Variation and Configuration • Sales Process Integration • Procurement Process Integration • Globalization • Standardization • Operations • Quality Challenges in Product Management 1 Introduction What Is Product Management? If you work in procurement, sales or IT for a large or mid-sized company, it’s likely that: • You’re struggling to coordinate your product information between catalogs, your web site, your intranet or your customers’ e-procurement portals, or • You’re talking about implementing a product configurator or an improved online product catalog, or • You’re trying to maintain and synchronize product data internally between multiple divisions, systems, and processes, or • Sales is looking to you to provide the infrastructure and support to integrate product information into a customer’s e-procurement portal, or • You’re wondering how you can streamline your procurement process, or how to get vendors to provide better information for your e-procurement system. It’s not hard to see how these questions are related; each is a piece of the larger question of product information management. -
Theproductmanagersinfluencem
C H S U S S U OUTLIERS S E T E M M C C O A IE A G M C N R RKETIN ER S U RESO U SALES CC ACCELERATORS CRITICALC SUPPORTERRS POTENTIALO DISRUPTORS T E O E T N G P S C R FI E GI I N E N H SUPP O NANC NEER RATIO A Practical Guide to Organizational Alignment and Relationship-Building for Product Teams 4 INTRODUCTION 6 METHODOLOGY & DEFINITIONS 9 CRITICAL SUPPORTERS 10 Marketing 15 Engineering 16 ACCELERATORS 18 Technical Support CONTENTS 21 Customer Success 24 POTENTIAL DISRUPTORS 26 Finance 29 Sales 32 OUTLIERS 34 Human Resources 37 Business Operations 40 C-LEVEL EXECUTIVES 42 USING THE MAP 43 THE INFLUENCE MAP PREFACE Most product managers are aware of the mantra that we “lead through influence and not authority.” Yet many entered their roles with very little guidance on what this means and how to apply it within their organizations. Over the past year, Pendo has worked closely with hundreds of product teams and surveyed hundreds more as a part of our “State of Product Leadership” survey with Product Collective. Through that work, a clear theme has emerged: product leaders who can create strong alignment with the various stakeholders within their organizations build the most successful products and companies. New product managers must acquire these skills quickly to be effective in their jobs. We’ve created this map to help define what it means to lead through influence and guide new product leaders through the interactions they’ll have on a daily basis at work. -
Product Management Essentials Tools and Techniques for Becoming an Ef Fective Technical Product Manager — Aswin Pranam Product Management Essentials
Product Management Essentials Tools and Techniques for Becoming an Ef fective Technical Product Manager — Aswin Pranam Product Management Essentials Tools and Techniques for Becoming an Effective Technical Product Manager Aswin Pranam Product Management Essentials Aswin Pranam Santa Clara, California, USA ISBN-13 (pbk): 978-1-4842-3302-3 ISBN-13 (electronic): 978-1-4842-3303-0 https://doi.org/10.1007/978-1-4842-3303-0 Library of Congress Control Number: 2017962635 Copyright © 2018 by Aswin Pranam This work is subject to copyright. All rights are reserved by the Publisher, whether the whole or part of the material is concerned, specifically the rights of translation, reprinting, reuse of illustrations, recitation, broadcasting, reproduction on microfilms or in any other physical way, and transmission or information storage and retrieval, electronic adaptation, computer software, or by similar or dissimilar methodology now known or hereafter developed. Trademarked names, logos, and images may appear in this book. Rather than use a trademark symbol with every occurrence of a trademarked name, logo, or image we use the names, logos, and images only in an editorial fashion and to the benefit of the trademark owner, with no intention of infringement of the trademark. The use in this publication of trade names, trademarks, service marks, and similar terms, even if they are not identified as such, is not to be taken as an expression of opinion as to whether or not they are subject to proprietary rights. While the advice and information in this book are believed to be true and accurate at the date of publication, neither the authors nor the editors nor the publisher can accept any legal responsibility for any errors or omissions that may be made. -
The Strategic Role of PRODUCT MANAGEMENT How a Market-Driven Focus Leads Companies to Build Products People Want to Buy
The Strategic Role of PRODUCT MANAGEMENT How a market-driven focus leads companies to build products people want to buy By Pragmatic Marketing About Pragmatic Marketing Why are we Pragmatic Marketing? Pragmatic Marketing’s training is based on the People sometimes ask why the company is named fundamental belief that a company’s products Pragmatic Marketing. “Isn’t that an oxymoron?” need to be grounded in a strategy that is driven they ask. by the market. We combine this core principle with a team of instructors who have real-world The “pragmatic” moniker makes sense: we offer experience leading high tech product teams, to practical, no-nonsense solutions to the problems deliver training seminars that are informative, facing technology product managers. It’s the term entertaining, and impactful. “marketing” that throws people. Our courses cover everything technology Technology businesses use two definitions companies need to be successfully market- of marketing: driven, from understanding market problems 1) the market experts and business leaders and personas, to creating effective requirements for the product and go-to-market strategies. To find out how — or — you or your company can join the growing 2) the t-shirt and coffee mug department international community of more than 75,000 product management and marketing As quoted in this e-book, Peter Drucker defines professionals trained by Pragmatic Marketing, visit marketing as “to know and understand the www.pragmaticmarketing.com. customer so well that the product or service fits him.” We use this classical definition of marketing. The Strategic Role of Product Management How a market-driven focus leads companies to build products people want to buy 2 The Pragmatic Marketing Framework™ The strategic role of product management is best defined by the Pragmatic Marketing Framework, a model for market-driven companies to build products people want to buy. -
Collaborative New Product Development: Supplier Selection and Purchasing
Faculty of Arts and Science FiF-avhandling 104 Collaborative New Product Development: Supplier Selection and Purchasing Lisa Melander 2011 Department of Management and Engineering Linköping University SE- 581 83 Linköping © Lisa Melander, 2011 Faculty of Arts and Science, FiF-avhandling 104 ISBN: 978-91-7393-028-4 ISSN: 1401-4637 Printed by: LiU-Tryck, Linköping Distributed by: Linköping University Department of Management and Engineering SE--581 83 Linköping Tel: + 46 13-281000, fax: + 46 13-281101 Abstract Suppliers provide new technology to firms and are important in firms‟ NPD. It is not sufficient for firms to select the most appropriate technology; they must also select the most appropriate supplier for their NPD. The purpose of this licentiate thesis is to map and identify criteria used in the process of selecting a suitable supplier, and explore the role of Purchasing in NPD collaborative pro- jects. This thesis is based on case study research where two NPD projects have been studied. The case sampling consisted of searching for projects that were be- lieved to be rich in information about the process of supplier selection. Both studied were conducted at ABB, which is a large high-tech system integration firm. ABB was a good firm to study because as a company, it is used to imple- menting new technology from suppliers. The data collection consisted of inter- views, factory visits, internal and external documents. The data gathered was analysed by conducting content analysis and then using categorization to struc- ture it. In addition, within-case analysis as well as cross-case analysis were per- formed. -
White Paper Product Management As a Leadership Role from Firefighting to Strategic Leadership (How to Increase Product Management’S Value and Influence)
world class product management White Paper Product management as a leadership role From firefighting to strategic leadership (how to increase product management’s value and influence) www.productfocus.com Page 1 world class product management Summary How can you increase the value and influence of product management in your organization? It depends on how product management is done at the moment. This white paper can help if... Your product team is too busy firefighting. Important things are dropped, and there is no time to lead the product and do the more strategic work that will benefit the company and impress senior management. Your product team is too technical or set in their ways. They gravitate to the delivery side of product management, which is their background and where they feel comfortable, but important commercial activities are just not happening. Or they see their job as making sure the developers are kept busy. Your company is dominated by the sales team. A new opportunity comes along, and the roadmap is reconfigured one more time to win the deal. Complexity, technical debt, and operational challenges mount up. If you recognize any of these issues, this white paper will give you the ideas, arguments, and tools to tackle things head-on. It’s about making product management into a leadership role. It’s about moving from firefighting to more strategic product activities. It’s about having more influence and providing more value in your business. That’s good for your company and good for you. Index Introduction Page 3 A story – from firefighting to strategic leadership Page 4 Tools to help Page 11 Conclusion Page 15 References Page 16 www.productfocus.com Page 2 world class product management Introduction It can be difficult to find the time and headspace to think about how you do product management and provide product leadership rather than just focusing on getting stuff done. -
The Eight Key Dimensions of Platform Product Management
The Eight Key Dimensions of Platform Product Management 1 Successful tech companies like Amazon, Google, and Alibaba are unleashing profound global macroeconomic changes through their platform-based business models. But this is not just a tech industry phenomenon. Industry leaders across all market segments are building platforms to seize new opportunities for growth and capital rewards. In fact, 81 percent of executives say platform-based business models will be core to their growth strategy within three years.1 However, managing a platform is different than managing an application and the methods, techniques and skills of product management in these two environments are distinct. 2 The two main objectives of platforms are The core responsibility of the acceleration and extended value. If an platforms is to not just be future organization wants to achieve these objectives thinking but to be velocity oriented. on its platform, it is critical to recognize the differences and employ the appropriate Ashley Still, Vice President/General platform product management capabilities. Manager, Adobe Document Cloud and Adobe Creative Cloud Enterprise, Adobe Successful platforms have product managers who constantly strive to shift the organization’s DNA from product to “platform first.” Accenture interviewed platform product In a complex business with multiple managers from successful platform companies point products and cloud-based such as Adobe, Dropbox, Salesforce and PayPal, solutions at various stages of maturity, along with our own internal platform product the key issue for us, as platform teams, to understand the subtle but critical product managers, is to ensure we nuances between platform and application have “a platform first” or “API first” product management. -
The Pragmatic Institute 2019 Annual Product Management and Product Marketing Survey
The Pragmatic Institute 2019 Annual Product Management and Product Marketing Survey LIKE ITS 18 PREDECESSORS, THE 2019 Pragmatic years (and no, no one said they’re expecting robots Institute Annual Product Management and Product to take their jobs). Marketing Survey is filled with valuable, relevant As you read through this year’s survey, note data about the product management and product that this icon reflects responses to the marketing professions. question, “If you could say one thing to your CEO The following pages offer a profile of today’s without fear of retribution, what would it be?” And professionals as well as insights into their day- when you see this icon, those comments to-day pains and gains. This year’s survey also reflect the open-ended responses to the question, examined the effect respondents expect artificial “How do you see AI and machine learning intelligence to have on their role in the next few impacting your role in the next few years?” Inside the Profession A total of 2,474 respondents GENDER participated in this year’s survey, “ Address the representing product professionals widespread gender of all types and bias that permeates backgrounds from around the world. the company.” Due to rounding, not all numbers in this report add to 100. 58% 42% – Senior Product Manager, PMC-IV AGE EDUCATION 3% DOCTORAL DEGREE 34% 34% 40% MASTER’S DEGREE 19% 43% BACHELOR’S DEGREE 9% 2% ASSOCIATE DEGREE 4% 1% HIGH SCHOOL DIPLOMA 19-29 30-39 40-49 50-59 60+ A combined 11% responded with some college or master’s education 2 | 2019 -
What's the Point of Product Management V3
product What’s the point of product management? Well let me tell you a story. Some of it you may recognize... www.productfocus.com © Product Focus 2019 The early years ou’ve got a product management team that’s been in place a few years. Most of them have come from other parts of the business and haven’t experienced product management Yin other companies. They learned what to do ‘on the job.’ This seems to translate into doing whatever the senior person shouting loudest wants at any point in time. They end up working on detailed requirements, handling sales questions and managing lots of stakeholders. A lot of them have a technical background. They aren’t really clear on what they should be doing, so tend to gravitate to the technical and operational activities with which they are most familiar and where they feel they add most value. They have lile focus on understanding the market, customers or competitors. Other people aren’t really sure what Product Management does. So, they simply assume that any product problems are the product manager’s job to sort out. Everybody wants product management And to add to the confusion there is a Product Marketing to sort out their problems team which seem to do some product stuff but also get A big problem is that it has been taking too long to deliver involved in marketing communications activities as well. new products (and speed to market in your industry is Unfortunately, their messaging is oen quite vague and important). poorly aligned to the product capabilities. -
The Discipline of Product Management
The Discipline of Product Management Phillip J. Windley, Ph.D. Chief Information Officer Office of the Governor State of Utah Product development is the process of designing, building, operating, and maintaining a good or service1. Software and Internet companies use a product development process to ensure that they are not just manufacturing a technology, but creating a product that people will want to buy and continue to use. To be sure, a base technology is at the heart of the product, but product development ensures that the customer’s voice is not lost in the rush to an exciting technology. Product development adds things like pricing, marketing, and customer support to the technology to create a complete product. Without a product management philosophy and discipline, an IT organization becomes focused on the technology instead of the customers and is often organized along technology lines rather than in ways that benefit the customer. Ultimately, an IT organization must serve its customers or it will go out of business, either because the customers go away or because they complain to executive management until the organization is changed. This paper discusses the product management discipline and how it can be applied to creating a customer driven IT organization. Product Development Product development is performed by a multi-disciplinary team whose goal is building, operating, and maintaining the product. Team members may include product managers, software developers, project managers, product operations engineers, customer support managers, software quality assurance engineers, user interface design engineers, marketers, financial personnel, and graphic artists. The product manager serves as the leader of this cross functional team. -
According to Open Product Management Workflow TM Author
Strategic Product Management TM according to Open Product Management Workflow Author: Frank Lemser Last updated April 2021 This book is teaching material of: proProduktmanagement GmbH Deutschherrnstrasse 6 90429 Nuremberg - Germany www.pro-productmanagement.com [email protected] +1 716 800 7312 2 CONTENTS Preface .................................................................................................................................................................... 6 Download Open Product Management Workflow TM ......................................................................................... 6 Download free Product Management Dashboard for JIRA - Software ............................................................... 6 The course teaching methods - Flipped Classroom ............................................................................................ 7 Flipped Classroom, instead of teacher-centred teaching ................................................................................... 7 Benefits for you as a participant ..................................................................................................................... 8 Benefits for your company .............................................................................................................................. 8 Learning objectives to make the very best of yourself ....................................................................................... 9 Product management as an ecological and economic opportunity.....................................................................