Significance and Challenges of Biomass As a Suitable Feedstock
Total Page:16
File Type:pdf, Size:1020Kb
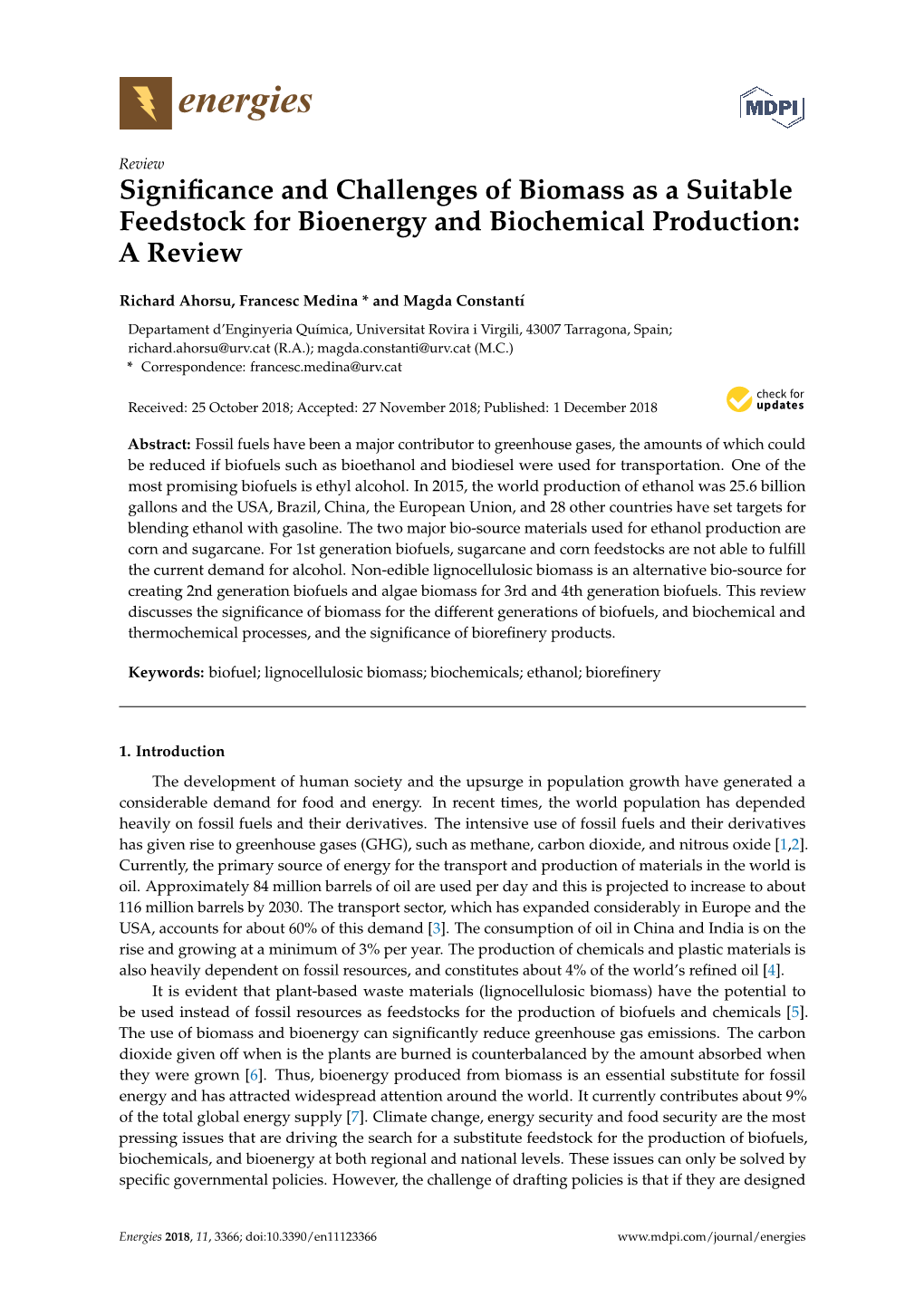
Load more
Recommended publications
-
What Is Still Limiting the Deployment of Cellulosic Ethanol? Analysis of the Current Status of the Sector
applied sciences Review What is still Limiting the Deployment of Cellulosic Ethanol? Analysis of the Current Status of the Sector Monica Padella *, Adrian O’Connell and Matteo Prussi European Commission, Joint Research Centre, Directorate C-Energy, Transport and Climate, Energy Efficiency and Renewables Unit C.2-Via E. Fermi 2749, 21027 Ispra, Italy; [email protected] (A.O.); [email protected] (M.P.) * Correspondence: [email protected] Received: 16 September 2019; Accepted: 15 October 2019; Published: 24 October 2019 Abstract: Ethanol production from cellulosic material is considered one of the most promising options for future biofuel production contributing to both the energy diversification and decarbonization of the transport sector, especially where electricity is not a viable option (e.g., aviation). Compared to conventional (or first generation) ethanol production from food and feed crops (mainly sugar and starch based crops), cellulosic (or second generation) ethanol provides better performance in terms of greenhouse gas (GHG) emissions savings and low risk of direct and indirect land-use change. However, despite the policy support (in terms of targets) and significant R&D funding in the last decade (both in EU and outside the EU), cellulosic ethanol production appears to be still limited. The paper provides a comprehensive overview of the status of cellulosic ethanol production in EU and outside EU, reviewing available literature and highlighting technical and non-technical barriers that still limit its production at commercial scale. The review shows that the cellulosic ethanol sector appears to be still stagnating, characterized by technical difficulties as well as high production costs. -
Is Biodiesel As Attractive an Economic Alternative As Ethanol?
PURDUE EXTENSION Bio ID-341 Fueling America ThroughE Renewablenergy Resources Is Biodiesel as Attractive an Economic Alternative as Ethanol? Allan Gray Department of Agricultural Economics Purdue University What Is Biodiesel? and as a lubricant additive to low sulfur diesel Biodiesel is a renewable fuel alternative to fuel. A change in environmental laws associ- standard on-road diesel. Biodiesel is made ated with sulfur emissions from diesel has from plant oils, such as soybean oil; animal caused the industry to move from a standard fat from slaughter facilities; or used greases. number 2 diesel to a cleaner burning number Seventy-three percent of biodiesel produced 1 diesel with much lower sulfur emission. in the United States comes from soybean oil. The remaining 27% is produced from the However, number 1 diesel fuel has a much other feedstocks. lower lubricity than number 2 diesel, causing additional wear on diesel engines. By blending The ability to use a variety of feedstocks to number 1 diesel with at least 2% biodiesel, the make biodiesel differentiates this biofuel mar- lubricity properties of the fuel can be the same ket from the current ethanol market, which as number 2 diesel fuel. And, because biodie- is dominated by corn in the U.S. and sugar sel contains only small traces of sulfur when in South America. The ability to use various burned, the sulfur emission standards can still feedstocks is one of the reasons that biodiesel be met. production facilities are not as concentrated in the Midwest as ethanol plants. In 2005, approximately 75 million gallons of biodiesel were produced in 65 plants scattered How Is Biodiesel Used? across the United States (Figure 1). -
Paper 20Th World Energy Congress Rome 2007
BTL: a solution to increase energy efficiency in the Brazilian alcohol business 1 Dr. Eduardo Falabella Souza-Aguiar Coordinator - GTL Cell CENPES - PETROBRAS Avenida Jequitibá, 950, Quadra 7, Ilha do Fundão, Rio de Janeiro, Brasil 2 Sirlei Sebastião Alves de Sousa Senior Consultant - GTL Cell FUJB - Universidade Federal do Rio de Janeiro, UFRJ Avenida Jequitibá, 950, Quadra 7, Ilha do Fundão, Rio de Janeiro, Brasil 3 Fernando Barbosa de Oliveira Process Engineer - GTL Cell CENPES - PETROBRAS Avenida Jequitibá, 950, Quadra 7, Ilha do Fundão, Rio de Janeiro, Brasil 1. Introduction Due to 1973 oil crisis, the Brazilian government, then run by a military junta, initiated in 1975 the ProÁlcool program. The ProÁlcool or Programa Nacional do Álcool (National Alcohol Program) was nationwide program financed by the government to phase out all automobile fuels derived from fossil fuels (such as gasoline) in favor of ethanol. It began with the anhydrous alcohol to blend with the gasoline. This mixture has been used since then and is now done with 24% of alcohol and 76% gasoline [1]. The decision to produce ethanol from fermented sugarcane was based on the low cost of sugar at the time. Other sources of fermentable carbohydrates were tested such as the manioc [1]. Sugarcane is in itself an enormously efficient production unit: every ton has an energy potential that is equivalent to 1.2 barrels of petroleum. Brazil is the largest sugarcane world producer, having the lowest production costs, followed by India and Australia. On average, 55% of Brazilian sugarcane is turned into alcohol [2]. Sugarcane is grown in Brazil’s Central-South and North-Northeast regions, with two harvest periods. -
Global Production of Second Generation Biofuels: Trends and Influences
GLOBAL PRODUCTION OF SECOND GENERATION BIOFUELS: TRENDS AND INFLUENCES January 2017 Que Nguyen and Jim Bowyer, Ph. D Jeff Howe, Ph. D Steve Bratkovich, Ph. D Harry Groot Ed Pepke, Ph. D. Kathryn Fernholz DOVETAIL PARTNERS, INC. Global Production of Second Generation Biofuels: Trends and Influences Executive Summary For more than a century, fossil fuels have been the primary source of a wide array of products including fuels, lubricants, chemicals, waxes, pharmaceuticals and asphalt. In recent decades, questions about the impacts of fossil fuel reliance have led to research into alternative feedstocks for the sustainable production of those products, and liquid fuels in particular. A key objective has been to use feedstocks from renewable sources to produce biofuels that can be blended with petroleum-based fuels, combusted in existing internal combustion or flexible fuel engines, and distributed through existing infrastructure. Given that electricity can power short-distance vehicle travel, particular attention has been directed toward bio-derived jet fuel and fuels used in long distance transport. This report summarizes the growth of second-generation biofuel facilities since Dovetail’s 2009 report1 and some of the policies that drive that growth. It also briefly discusses biofuel mandates and second-generation biorefinery development in various world regions. Second generation biorefineries are operating in all regions of the world (Figure 1), bringing far more favorable energy balances to biofuels production than have been previously realized. Substantial displacement of a significant portion of fossil-based liquid fuels has been demonstrated to be a realistic possibility. However, in the face of low petroleum prices, continuing policy support and investment in research and development will be needed to allow biofuels to reach their full potential. -
Biomass with CO2 Capture and Storage (Bio-CCS)
Biomass with CO2 Capture and Storage (Bio-CCS) The way forward for Europe This document has been prepared on behalf of the Advisory Council of the European Technology Platform for Zero Emission Fossil Fuel Power Plants (ZEP) and the Steering Committee of the European Biofuels Technology Platform (EBTP). The information and views contained in this document are the collective view of the ZEP Advisory Council and EBTP Steering Committee and not of individual members, or of the European Commission. Neither the ZEP Advisory Council, the EBTP Steering Committee, the European Commission, nor any person acting on their behalf, is responsible for the use that might be made of the information contained in this publication. European Technology Platform for Zero Emission Fossil Fuel Power Plants Contents KEY CONCLUSIONS........................................................... ....................................................................... 4 1 WHY EUROPE NEEDS TO GO CARBON-NEGATIVE ....................................................................... 5 1.1 More powerful technologies are now needed to keep global warming below 2°C........................5! 1.2 Bio-CCS: the only large-scale technology that can remove CO2 from the atmosphere.... ........... 5! 1.3 The EBTP/ZEP Joint Taskforce Bio-CCS: uniting high-level European stakeholders ................. 6! 2! CO2 CAPTURE AND STORAGE.......................................................................................................... 7! 2.1! CCS could provide almost 20% of global -
Alternate Algae Fuel Spencer Meredith Columbus State
RUNNING HEAD: ALTERNATE ALGAE FUEL 1 Alternate Algae Fuel Spencer Meredith Columbus State Community College ALTERNATE ALGAE FUEL 2 Abstract Hold your nose as we dive into the aquatic world of microalgae. Conducting research seeking a renewable energy source, I found algae has the potential to change the world for the better. The oil from algae species can be turned into a biofuel, fuel produced from agricultural processes that can be used in transportation engines. This fuel and overall process of algae production has been found to be a safer and more environmental friendly process than fossil fuels. Also, algae grows in water, making it farmable in many different ways, each system holding their own unique advantages. What stands in the way of commercial viability is the amount of money needed to build enough mechanisms that make algae a cheaper and more available fuel than the current fossil fuel, but scientist remain determined and believe it can work. Keywords: Biofuel, Algae Oil, Alternate Energy ALTERNATE ALGAE FUEL 3 Alternate Algae Fuel "We are going to exit the fossil fuel era. It is inevitable.” says Elon Musk, CEO and lead designer of multiple prodigious projects (Felix, 2015). Musk is the head developer of Space-X, a multi-billion dollar private spacecraft company with goals of colonizing Mars. He also invented the hyperloop, a machine that will carry passengers from Los Angeles to San Francisco in thirty- five minutes, normally a seven hour drive. The superstar inventor also works closely to refine Tesla, Inc., an automotive electric car company. Needless to say, Musk is in touch with the current environmental needs of the world and his thoughts on drastically reducing the use of fossil fuels is a commonly shared opinion among a greater part of the science community. -
Biodiesel Production from Microalgae
J. Biol. Today's World. 2013 Feb; 2 (2): 38-42 ∙∙∙∙∙∙∙∙∙∙∙∙∙∙∙∙∙∙∙∙∙∙∙∙∙∙∙∙∙∙∙∙∙∙∙∙∙∙∙∙∙∙∙∙∙∙∙∙∙∙∙∙∙∙∙∙∙∙∙∙∙∙∙∙∙∙∙∙∙∙∙∙∙∙∙∙∙∙∙∙∙∙∙∙∙∙∙∙∙∙∙∙∙∙∙∙∙∙∙∙∙∙∙∙∙∙∙∙∙∙∙∙∙∙∙∙∙∙∙∙∙∙∙∙∙∙∙∙∙∙∙∙∙∙∙∙∙∙∙∙∙∙∙∙∙∙∙∙∙∙∙∙∙∙∙∙∙∙∙∙∙∙∙∙∙ Journal of Biology and Today's World ISSN 2322-3308 Journal home page: http://journals.lexispublisher.com/jbtw/ Received: 26 January 2013 • Accepted: 10 February 2013 Review doi:10.15412/J.JBTW. 01020204 Biodiesel Production from Microalgae Mahya Mohammadi, Morteza Azizollahi-Aliabadi* Department of Microbiology, Faculty of Basic Science, Lahijan Branch, Islamic Azad University, Lahijan, Iran *correspondence should be addressed to Morteza Azizollahi-Aliabadi, Department of Microbiology, Faculty of Basic Science, Lahijan Branch, Islamic Azad University, Lahijan, Iran; Tell: +98; Fax: +98; Email: [email protected]. ABSTRACT Technology for creating also applying biodiesel has been recognized for more than 50 years. Microalgae are a various type of prokaryotic as well as eukaryotic photosynthetic microorganisms that grow rapidly due to their simple structure. Biodiesel is considered as a renewable fuel because it can be obtained from the transformation of vegetable oils, cooking greases or animal fats. Microalgae are sunlight-driven cell factories that convert carbon dioxide to potential biofuels, foods, nourish also high-value bioactives. In addition, these photosynthetic microorganisms are beneficial in bioremediation applications nitrogen fixing biofertilizers. This article focuses on microalgae as a potential source -
Coal Biomass to Liquid Fuels
Small-Scale Coal-Biomass to Liquids Production Using Highly Selective Fischer-Tropsch Synthesis n Background Co-conversion of coal with some biomass to liquid fuels can help to reduce CO2 emissions because of the neutrality of biomass with respect to CO2 emissions. An NETL study [Affordable, low cost diesel fuel from domestic coal and biomass, DOE/NETL2009/1349, January 2009], in fact, has indicated that addition of even moderate amounts of biomass to coal for the production of liquids can potentially reduce Life Cycle Analysis (LCA) CO2 emissions relative to petroleum diesel baseline; for example, 20% less CO2 is produced with 8% biomass addition, with Carbon Capture, Storage, and Utilization (CCUS). Fischer-Tropsch synthesis (FTS) is a leading technology for converting syngas from gasification to hydrocarbons in coal to liquids (CTL) and coal-biomass to liquids (CBTL) processes. However, conventional FT catalysts produce undesirable waxes (C21+) that need to be upgraded to liquids (C5-C20) by hydrotreating. This adds significantly to the cost of FTS. Development and commercialization of a cost-effective gasification/FTS-based CBTL process to produce renewable gasoline and diesel can reduce the nation’s dependency on oil imported from foreign countries, help to stabilize the prices at the pump, and lower the emission of greenhouse gases. PLEASE CONTACT PARTICIPANTS PROJECT COST Santosh Gangwal Doe Technical Project Officer Chevron Energy DURATION Total Project Principal Investigator Arun Bose Technology Start Date Value Southern Research -
Industrial Biorefineries for Production of Biofuels, Materials and Chemicals
Industrial Biorefineries for Production of Biofuels, Materials and Chemicals IEA End-Use Working Party Webinar on Deep Decarbonization in Industry 9 December 2020 Tech. Lic. Mats Larsson, Research Programme Manager, Biofuels and Industry, Swedish Energy Agency Usage of fossile energy in Sweden (2018) (TWh) 120 Housing, 11 TWh/year 100 80 60 Transport sector, 64 TWh. 40 20 Industry sector, 27 TWh. 0 Energy usage in domestic transport sector 110 100 Biofuels 90 80 70 Aviation (light blue) Diesel 60 TWh • Fossils fuels, mostly 50 petrol and diesel, are the 40 origin for around 75% • Bio fuels has increased 30 Petrol rapidly during the last 20 years 10 The fossil part is around 0 6-7 million m3 per year. Source: Swedish Energy Agency Biofuels Biogas 20 18 16 Biodiesel, 14 Hydrogenated vegetable oil (HVO) and Fatty Acid Methyl 12 Ester (FAME). 10 TWh 8 Increase mainly due to 6 import of HVO. 4 2 Bioethanol 0 Source: Swedish Energy Agency Domsjö Fabriker The biorefinery Domsjö Fabriker AB refines wood into products with strong environmental profile. In addition to the main products cellulose, bioethanol and lignin the biorefinery produces more and more complementary products such as carbon dioxide, biogas, bio resin and soil improvers. Source: http://www.domsjo.adityabirla.com/sidor/Domsjo-Fabriker.aspx The biorefinery originates from the sulphite pulp mill that was started in 1903 and has since yearly 2000’s been transformed into the modern biorefinery it is today. The production capacity is 230 000 tonnes cellulose, 120 000 tonnes lignin and 20 000 tonnes bioethanol. The production of biogas from the biological treatment plant is one of the largest in Sweden. -
Natural Fibers and Fiber-Based Materials in Biorefineries
Natural Fibers and Fiber-based Materials in Biorefineries Status Report 2018 This report was issued on behalf of IEA Bioenergy Task 42. It provides an overview of various fiber sources, their properties and their relevance in biorefineries. Their status in the scientific literature and market aspects are discussed. The report provides information for a broader audience about opportunities to sustainably add value to biorefineries by considerin g fiber applications as possible alternatives to other usage paths. IEA Bioenergy Task 42: December 2018 Natural Fibers and Fiber-based Materials in Biorefineries Status Report 2018 Report prepared by Julia Wenger, Tobias Stern, Josef-Peter Schöggl (University of Graz), René van Ree (Wageningen Food and Bio-based Research), Ugo De Corato, Isabella De Bari (ENEA), Geoff Bell (Microbiogen Australia Pty Ltd.), Heinz Stichnothe (Thünen Institute) With input from Jan van Dam, Martien van den Oever (Wageningen Food and Bio-based Research), Julia Graf (University of Graz), Henning Jørgensen (University of Copenhagen), Karin Fackler (Lenzing AG), Nicoletta Ravasio (CNR-ISTM), Michael Mandl (tbw research GesmbH), Borislava Kostova (formerly: U.S. Department of Energy) and many NTLs of IEA Bioenergy Task 42 in various discussions Disclaimer Whilst the information in this publication is derived from reliable sources, and reasonable care has been taken in its compilation, IEA Bioenergy, its Task42 Biorefinery and the authors of the publication cannot make any representation of warranty, expressed or implied, regarding the verity, accuracy, adequacy, or completeness of the information contained herein. IEA Bioenergy, its Task42 Biorefinery and the authors do not accept any liability towards the readers and users of the publication for any inaccuracy, error, or omission, regardless of the cause, or any damages resulting therefrom. -
Heat and Mass Transfer During Lignocellulosic Biomass Torrefaction: Contributions from the Major Components—Cellulose, Hemicellulose, and Lignin
processes Article Heat and Mass Transfer during Lignocellulosic Biomass Torrefaction: Contributions from the Major Components—Cellulose, Hemicellulose, and Lignin Ken-ichiro Tanoue 1,*, Kentaro Hikasa 1, Yuuki Hamaoka 1, Akihiro Yoshinaga 1, Tatsuo Nishimura 1, Yoshimitsu Uemura 2,3 and Akihiro Hideno 4 1 Department of Mechanical Engineering, School of Sciences and Engineering for Innovation, Yamaguchi University, Tokiwadai 2-16-1, Ube, Yamaguchi 755-8611, Japan; [email protected] (K.H.); [email protected] (Y.H.); [email protected] (A.Y.); [email protected] (T.N.) 2 NPO Kuramae Bioenergy, Minato-ku, Tokyo 108-0023, Japan; [email protected] 3 Center for Biofuel and Biochemical Research, Universiti Teknologi PETRONAS, Seri Iskandar 32610, Malaysia 4 Paper industry innovation center of Ehime University, 127 Mendori-cho, Shkokuchuo 799-0113, Japan; [email protected] * Correspondence: [email protected]; Tel.: +81-836-85-9122 Received: 27 June 2020; Accepted: 6 August 2020; Published: 9 August 2020 Abstract: The torrefaction of three representative types of biomass—bamboo, and Douglas fir and its bark—was carried out in a cylindrical-shaped packed bed reactor under nitrogen flow at 573 K of the reactor wall temperature. As the thermal energy for the torrefaction was supplied from the top and the side of the bed, the propagation of the temperature profile of the bed is a crucial factor for discussing and improving the torrefaction reactor performance. Therefore, the temperature and gas flow rate (vector) profiles throughout the bed were calculated by model simulation so as to scrutinize this point. -
Download PDF (Inglês)
Brazilian Journal of Chemical ISSN 0104-6632 Printed in Brazil Engineering www.abeq.org.br/bjche Vol. 32, No. 01, pp. 23 - 33, January - March, 2015 dx.doi.org/10.1590/0104-6632.20150321s00003146 EVALUATION OF COMPOSITION, CHARACTERIZATION AND ENZYMATIC HYDROLYSIS OF PRETREATED SUGAR CANE BAGASSE A. A. Guilherme1*, P. V. F. Dantas1, E. S. Santos1, F. A. N. Fernandes2 and G. R. Macedo1 1Department of Chemical Engineering, Federal University of Rio Grande do Norte, UFRN, Av. Senador Salgado Filho 3.000, Campus Universitário, Lagoa Nova, Bloco 16, Unidade II, 59.078-970, Natal - RN, Brazil. Phone: + (55) 84 3215 3769, Fax: + (55) 84 3215 3770 E-mail: [email protected] 2Department of Chemical Engineering, Federal University of Ceará, UFC, Campus do Pici, Bloco 709, 60455-760, Fortaleza - CE, Brazil. (Submitted: December 2, 2013 ; Revised: March 28, 2014 ; Accepted: March 31, 2014) Abstract - Glucose production from sugarcane bagasse was investigated. Sugarcane bagasse was pretreated by four different methods: combined acid and alkaline, combined hydrothermal and alkaline, alkaline, and peroxide pretreatment. The raw material and the solid fraction of the pretreated bagasse were characterized according to the composition, SEM, X-ray and FTIR analysis. Glucose production after enzymatic hydrolysis of the pretreated bagasse was also evaluated. All these results were used to develop relationships between these parameters to understand better and improve this process. The results showed that the alkaline pretreatment, using sodium hydroxide, was able to reduce the amount of lignin in the sugarcane bagasse, leading to a better performance in glucose production after the pretreatment process and enzymatic hydrolysis.