Predicting the Flowability of Powder Mixtures from Their
Total Page:16
File Type:pdf, Size:1020Kb
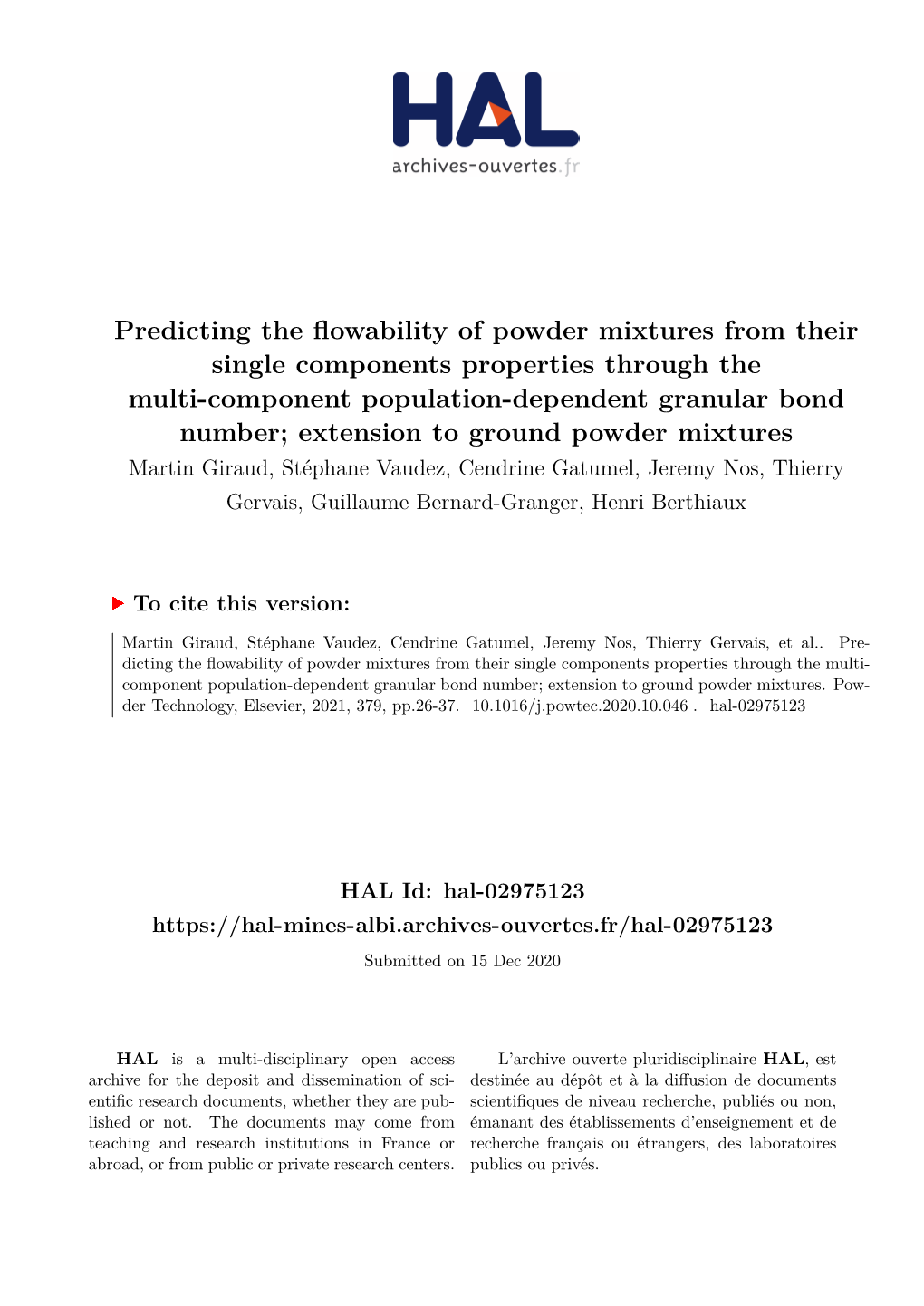
Load more
Recommended publications
-
Effective Interaction Between Membrane and Scaffold
Effective Interaction Between Membrane And Scaffold Masterarbeit aus der Physik Vorgelegt von Matthias Sp¨ath 04.02.2016 PULS Group Friedrich-Alexander-Universit¨atErlangen-N¨urnberg Betreuung: Prof. Dr. Ana-Sunˇcana Smith Summary Life threatening and life forming events, like the spreading of cancer and embryogen- esis, are governed by how cells interact with each other and therefore by cell adhesion. Further, all cells are surrounded by membranes. Therefore, the understanding of membrane interactions is the foundation for evaluating the role of biological mem- branes in the process of cell adhesion. While the role of various adhesive proteins in this process is mostly dealt with by biology, physics can be used to analyze and describe the mechanistic details of the membrane. This makes membranes and their interactions a highly relevant and exciting field in biophysics. From a physical point of view the interaction between two opposing membranes or membrane and substrate is governed by the interaction potentials and the bend- ing energy of the membrane. Even though the individual contributions, such as the Helfrich and steric repulsion, the van der Waals attraction, and the hydration forces are reasonably well understood, there is a discrepancy between the experimentally determined effective potential and its theoretical prediction. We address this dis- crepancy from several angles. We perform an in-depth analysis of the van der Waals interaction for membranes to make sure that there are no unexpected contributions for that potential. Additionally we construct real space Monte Carlo simulations for fluctuating membranes and their interactions. These are the two main chapters of this thesis. -
Mechanisms in Surface Enhanced Raman Scattering
Mechanisms in Surface Enhanced Raman Scattering by Matthias Meyer A thesis submitted to the Victoria University of Wellington in fullfilment of the requirements for the degree of Doctor of Philosophy in Physics Victoria University of Wellington The MacDiarmid Institute for Advanced Materials and Nanotechnology 2009 Abstract This thesis focusses on a number of topics in surface enhanced Raman scattering (SERS). The aim of the undertaken research was to deepen the general understanding of the SERS effect and, thereby, to clarify some of the disputed issues, among them: What is the origin of the enhancement? What is the physical or chemical effect of ‘salt activation’ in SERS systems? Can we observe single-molecules using SERS? Can we determine the ab- sorbate’s orientation on the surface? In part one (chapters 1-3), as a general introduction, I start with a short overview of the Raman effect and its relation to other molecular spectro- scopic effects (such as fluorescence, Rayleigh scattering, etc... ). Follow- ing these basic remarks, the surface enhancement mechanisms underlying SERS are explained (as a largely electromagnetic field enhancement) and are investigated theoretically on the canonical model of a nanoscopic dimer of silver spheres. The second part (chapter 4) reports on the experimental investigation (elec- tron microscopy, in-situ Raman measurements) of a typical real SERS sys- tem: Lee & Meisel silver colloids. An emphasis is put on the self-limiting aggregation kinetics which is observed in such systems after salt addi- tion. This is also investigated and rationalised by means of Monte-Carlo simulations which are footed on empiric theoretical considerations for the interaction potential. -
Electrical Double Layer Interactions with Surface Charge Heterogeneities
Electrical double layer interactions with surface charge heterogeneities by Christian Pick A dissertation submitted to Johns Hopkins University in conformity with the requirements for the degree of Doctor of Philosophy Baltimore, Maryland October 2015 © 2015 Christian Pick All rights reserved Abstract Particle deposition at solid-liquid interfaces is a critical process in a diverse number of technological systems. The surface forces governing particle deposition are typically treated within the framework of the well-known DLVO (Derjaguin-Landau- Verwey-Overbeek) theory. DLVO theory assumes of a uniform surface charge density but real surfaces often contain chemical heterogeneities that can introduce variations in surface charge density. While numerous studies have revealed a great deal on the role of charge heterogeneities in particle deposition, direct force measurement of heterogeneously charged surfaces has remained a largely unexplored area of research. Force measurements would allow for systematic investigation into the effects of charge heterogeneities on surface forces. A significant challenge with employing force measurements of heterogeneously charged surfaces is the size of the interaction area, referred to in literature as the electrostatic zone of influence. For microparticles, the size of the zone of influence is, at most, a few hundred nanometers across. Creating a surface with well-defined patterned heterogeneities within this area is out of reach of most conventional photolithographic techniques. Here, we present a means of simultaneously scaling up the electrostatic zone of influence and performing direct force measurements with micropatterned heterogeneously charged surfaces by employing the surface forces apparatus (SFA). A technique is developed here based on the vapor deposition of an aminosilane (3- aminopropyltriethoxysilane, APTES) through elastomeric membranes to create surfaces for force measurement experiments. -
Chapter 5 Co-Culture of Young Porcine Islets with Liver Microvascular Endothelial Cells in Fibrin Improves Insulin Secretion and Reduces Apoptosis
UNIVERSITE DE SHERBROOKE Faculte de genie Departement de genie chimique et de genie biotechnologique DEVELOPPEMENT ET VALIDATION DE SURFACES ET D’ECHAFAUDAGES PROPICES AU DEVELOPPEMENT ET AU MAINTIEN DES FONCTIONS DE CELLULES PANCREATIQUES BETA TOWARDS THE DEVELOPMENT AND VALIDATION OF BIOMATERIAL SURFACES AND SCAFFOLDS SUITABLE FOR PANCREATIC BETA CELL DEVELOPMENT AND FUNCTION These de doctorat Specialite: genie chimique Evan Aiozie DUBIEL Jury : Patrick VERMETTE (directeur) Jonathan LAKEY Steven PARASKEVAS Marie-Josee BOUCHER Marcel LACROIX (rapporteur) Sherbrooke (Quebec) Canada Novembre 2012 Library and Archives Bibliotheque et Canada Archives Canada Published Heritage Direction du 1+1 Branch Patrimoine de I'edition 395 Wellington Street 395, rue Wellington Ottawa ON K1A0N4 Ottawa ON K1A 0N4 Canada Canada Your file Votre reference ISBN: 978-0-494-93268-1 Our file Notre reference ISBN: 978-0-494-93268-1 NOTICE: AVIS: The author has granted a non L'auteur a accorde une licence non exclusive exclusive license allowing Library and permettant a la Bibliotheque et Archives Archives Canada to reproduce, Canada de reproduire, publier, archiver, publish, archive, preserve, conserve, sauvegarder, conserver, transmettre au public communicate to the public by par telecommunication ou par I'lnternet, preter, telecommunication or on the Internet, distribuer et vendre des theses partout dans le loan, distrbute and sell theses monde, a des fins commerciales ou autres, sur worldwide, for commercial or non support microforme, papier, electronique et/ou commercial purposes, in microform, autres formats. paper, electronic and/or any other formats. The author retains copyright L'auteur conserve la propriete du droit d'auteur ownership and moral rights in this et des droits moraux qui protege cette these. -
Determining Charge Distribution of Metal Oxide Surfaces with Afm Using Colloid Probe Technique
DETERMINING CHARGE DISTRIBUTION OF METAL OXIDE SURFACES WITH AFM USING COLLOID PROBE TECHNIQUE A Thesis Submitted to the Graduate School of Engineering and Sciences of İzmir Institute of Technology in Partial Fulfillment of the Requirements for the Degree of MASTER OF SCIENCE in Chemical Engineering by Ayşe GÜREL December 2012 İZMİR We approve the thesis of Ayşe GÜREL Examining Committee Members: _________________________ Prof. Dr. Mehmet POLAT Department of Chemical Engineering İzmir Institute of Technology _________________________ Prof. Dr. Metin TANOĞLU Department of Mechanical Engineering İzmir Institute of Technology _________________________ Assoc. Prof. Dr. Ekrem ÖZDEMİR Department of Chemical Engineering İzmir Institute of Technology 4 December 2012 ______________________ Prof. Dr. Mehmet POLAT Supervisor Department of Chemical Engineering İzmir Institute of Technology _______________________ ________________________ Prof. Dr. Mehmet POLAT Prof. Dr. R. Tuğrul SENGER Head of the Department of Dean of the Graduate School of Chemical Engineering Engineering and Sciences ACKNOWLEDGMENTS First and foremost, I would like to express my gratitude to my supervisor Prof. Dr. Mehmet POLAT for his supervision, academic guidance, encouragement and insight throughout my thesis study. Secondly, I acknowledge the Scientific and Technological Research Council of Turkey (TÜBİTAK), one of the distinguished institutions of my country, for granting me a graduate scholarship. I also owe many thanks to Gülnihal Yelken Özek for her valuable helping in the laboratory, experience, motivations, understanding during the study. I would like to thank to Prof. Dr. Hürriyet Polat for her helping in Particle Size distribution analysis. I am grateful to Assoc. Prof. Ekrem Özdemir at İzmir Institute of Technology in the Department of Chemical Engineering for his valuable help in Zeta Potential Measurement analysis. -
Understanding Fundamentals of Plasmonic Nanoparticle Self-Assembly at Liquid-Air
A Dissertation entitled Understanding Fundamentals of Plasmonic Nanoparticle Self-assembly at Liquid-air Interface by Chakra P. Joshi Submitted to the Graduate Faculty as partial fulfillment of the requirements for the Doctor of Philosophy Degree in Chemistry _________________________________________ Dr. Terry P. Bigioni, Committee Chair _________________________________________ Dr. Dragan Isailovic, Committee Member _________________________________________ Dr. Mark Mason, Committee Member _________________________________________ Dr. Jacques G. Amar, Committee Member _________________________________________ Dr. Patricia R. Komuniecki, Dean College of Graduate Studies The University of Toledo December 2013 Copyright 2013, Chakra P. Joshi This document is copyrighted material. Under copyright law, no parts of this document may be reproduced without the expressed permission of the author. An Abstract of Understanding Fundamentals of Plasmonic Nanoparticle Self-assembly at Liquid-air Interface by Chakra P. Joshi Submitted to the Graduate Faculty as partial fulfillment of the requirements for the Doctor of Philosophy Degree in Chemistry The University of Toledo December 2013 Two-dimensional self-assemblies of plasmonic nanoparticles (NPs) could one day become a useful technology for mankind as it has a potential to produce desirable structures with various patterning and ordering that is difficult to achieve by the top- down approach. Furthermore, these patterned and ordered structures of NPs have been known to display interesting optoelectronic -
Thesis Oct 3 2014 Unlinked Editted
Drainage and Stability of Foam Films during Bubble Coalescence in Aqueous Salt Solutions Mahshid Firouzi B.Eng., M.Eng. Chemical Engineering A thesis submitted for the degree of Doctor of Philosophy at The University of Queensland in 2014 School of Chemical Engineering Abstract Bubble coalescence and thin liquid films (TLFs) between bubbles known as foam films, are central to many daily activities, both natural and industrial. They govern a number of important processes such as foam fractionation, oil recovery from tar sands and mineral recovery by flotation using air bubbles. TLFs are known to be stabilized by some salts and bubble coalescence in saline water can be inhibited at salt concentrations above a critical (transition) concentration. However, the mechanisms of the inhibiting effect of these salts are as yet contentious. The aim of this work is to characterise the behaviour of saline liquid films both experimentally and theoretically to better understand the mechanisms. The effect of sodium halide and alkali metal salts including NaF, NaBr, NaI, NaCl, KCl and LiCl on the stability of a foam film was investigated by applying the TLF interferometry method. To mimic realistic conditions of bubble coalescence in separation processes, the drainage and stability of TLFs were studied under non-zero bubble (air-liquid interface) approach speeds (10-300 µm/s) utilizing a nano-pump. For each of the salts studied, a critical concentration ( Ccr ) above which liquid films lasted for up to 50 s depending on the salt type, concentration and the interface approach speed, was determined. For concentrations below Ccr , the saline liquid films either ruptured instantly or lasted for less than 0.2 s. -
A Digital-Based Approach for Characterising Spread Powder Layer in Additive Manufacturing
Materials and Design 196 (2020) 109102 Contents lists available at ScienceDirect Materials and Design journal homepage: www.elsevier.com/locate/matdes A digital-based approach for characterising spread powder layer in additive manufacturing Yi He ⁎, Jabbar Gardy, Ali Hassanpour, Andrew E. Bayly School of Chemical and Process Engineering, University of Leeds, Leeds, United Kingdom HIGHLIGHTS GRAPHICAL ABSTRACT • A general approach to characterise spread powder layer based on space discretization. • Qualitative and quantitative evaluations enabled for packing density, surface profile and pores. • Density pore for less populated area and chamber pore for size of empty patch. • Sensitivity tests conducted on sampling parameters. • Applicability demonstrated for simula- tion-generated and experimentally spread powder layers. article info abstract Article history: Assessing the quality of a spread powder layer is critical to understanding powder spreadability in additive Received 19 July 2020 manufacturing. However, the small layer thickness presents a great challenge for a systematic and consistent Received in revised form 21 August 2020 characterisation of the spread powder layer. In this study, a novel digital-based characterisation approach is pro- Accepted 24 August 2020 posed based on space discretization, with an emphasis on the characteristics that is important to powder-bed- Available online 27 August 2020 based additive manufacturing. With the developed approach, the spread powder layer can be qualitatively illus- trated by contour maps and quantified by statistics of packing density, surface profile and pore characteristics. For Keywords: fi Powder spreading the rst time, two types of pores are proposed for the spread powder layer. The density pore can identify those Additive manufacturing less populated areas while the chamber pore is able to quantify the size of empty patches observed in the spread Discrete element method powder bed. -
Control of Physical and Chemical Processes with Nonlocal Metal− Dielectric Environments Vanessa N
Perspective Cite This: ACS Photonics 2019, 6, 3039−3056 pubs.acs.org/journal/apchd5 Control of Physical and Chemical Processes with Nonlocal Metal− Dielectric Environments Vanessa N. Peters,‡,# Srujana Prayakarao,# Samantha R. Koutsares, Carl E. Bonner, and Mikhail A. Noginov* Center for Materials Research, Norfolk State University, Norfolk, Virginia 23504, United States ABSTRACT: In this Perspective, we make the case that (meta) material platforms that were originally designed to control the propagation of light can affect scores of physical and chemical phenomena, which are often thought to lie outside of the traditional electrodynamics domain. We show that nonlocal metal-dielectric environments, which can be as simple as metal−dielectric interfaces, can control spontaneous and stimulated emission, Förster energy transfer, wetting contact angle, and rates of chemical reactions. The affected phenomena can occur in both strong and weak coupling regimes and the large coupling strength seems to enhance the effects of nonlocal environments. This intriguing field of study has experienced a rapid growth over the past decade and many exciting discoveries and applications are expected in the years to come. KEYWORDS: metamaterials, plasmonics, nonlocal metal−dielectric environment, weak and strong coupling regimes anipulation of light with dielectric media and metallic Hyperbolic Metamaterials, (ii) Control of Energy Transfer M surfaces is not limited to traditional large-scale optics, with Nonlocal Metal−Dielectric Environments, (iii) Long- like eyeglass lenses and looking glasses. Thus, metal−dielectric Range Wetting Transparency on Top of Layered Metal- interfaces and metallic nanostructures support a variety of Dielectric Substrates, and (iv) Control of Chemical Reactions propagating and localized surface plasmons (SPs): resonant in Weak and Strong Coupling Regimes. -
A Materials Perspective on Casimir and Van Der Waals Interactions
A Materials Perspective on Casimir and van der Waals Interactions 1L. M. Woods, 2D. A. R. Dalvit, 3A. Tkatchenko, 4P. Rodriguez-Lopez, 5A. W. Rodriguez, and 6;7R. Podgornik 1Department of Physics, University of South Florida, Tampa FL, 33620, USA 2Theoretical Division, MS B123, Los Alamos National Laboratory, Los Alamos NM, 87545, USA 3Fritz-Haber-Institut der Max-Planck-Gesellschaft, D-14195 Berlin, Germany 4Laboratoire de Physique Th´eorique et Mod`elesStatistiques, CNRS UMR 8626, B^at.100, Universit´eParis-Sud, 91405 Orsay cedex, France 5Princeton Univ, Dept Elect Engn, Princeton, NJ 08540 USA 6Jozef Stefan Inst, Dept Theoret Phys, SI-1000 Ljubljana, Slovenia 7Univ Massachusetts, Dept Phys, Amherst, MA 01003 USA Interactions induced by electromagnetic fluctuations, such as van der Waals and Casimir forces, are of universal nature present at any length scale between any types of systems with finite dimensions. Such interactions are important not only for the fundamental science of materials behavior, but also for the design and improvement of micro- and nano-structured devices. In the past decade, many new materials have become available, which has stimulated the need of understanding their dispersive interactions. The field of van der Waals and Casimir forces has experienced an impetus in terms of developing novel theoretical and computational methods to provide new insights in related phe- nomena. The understanding of such forces has far reaching consequences as it bridges concepts in materials, atomic and molecular physics, condensed matter physics, high en- ergy physics, chemistry and biology. In this review, we summarize major breakthroughs and emphasize the common origin of van der Waals and Casimir interactions. -
To Love and Regenerate the Earth: Further Perspectives On
To Love And Regenerate The Earth: Further Perspectives On Written and Compiled by Don Weaver, Co-Author of FERTILE GROUND by Rob Schouten ã 1995 To Love And Regenerate The Earth: Further Perspectives on The Survival of Civilization. Written and compiled by Don Weaver. Copyright 2002 by Don Weaver, to protect the wholeness and integrity of this work. Communications may be addressed to: Don Weaver Earth Health Regeneration POB 620478 Woodside, CA 94062-0478 e-mail: [email protected] The purpose of this book is to offer the world's responsible people a non-commercial gift of potentially world-transforming information, ideas, and insights on the social, ecological and climatic problems now threatening the future of humanity and the whole Biosphere. Also, to offer potential solutions which respond to the causes of these problems, and which might empower us to wisely regenerate the Biosphere and restore health and balance to the sociosphere. The author/editor is an independent (and interdependent) volunteer researcher hoping to encourage humanity's continued awakening, as well as "the progress of Science and useful Arts," one of the Constitutionally stated purposes of copyright law. In quoting from a broad spectrum of journals, websites, and books, I did not intend to substitute for them nor discourage careful, open-minded study of the entirety of them, nor do I in any way discourage their purchase if for sale. I found very helpful, as you may, the information and guidelines on the Fair Use privilege in books and websites on the topic. Especially comprehensive is the Fifth Edition (Feb. -
Subject 429..438
429 Subject Index a absorption 278 b absorption-pressure number 153f. bead-and-necklace 358 acrylamide (AAm) 40 bending energy 281 adhesion 206f., 210, 214, 216 bifluid 277f., 301 adsorbed amount 366ff., 372ff. bilayer 285 adsorption 159, 412 bimorph force sensor 175 – energy 263 bioaffinity 52 – isotherm 366ff., 378 bioavailability 409 – length 157 biodegradability 411 – parameters 255 biopolymers 131 – specific 268, 272 bioprobe 52 aggregation 84f., 93f. biotinylation 419 – diffusion-limited (DLA) 96ff., 105ff. Bjerrum length 327 – number 346ff., 356ff. black spots 405 – reaction-limited (RLA) 96, 106ff. blob 328 alkali metal n-dodecyl sulfates 247 block copoly(oxyalylene) 66ff. alkanethiol 16 – critical micelle temperature 66ff. alloy 1, 10, 38f., 48 – gelation of micellar solutions 74f. alumina 106f., 115 – micellar properties 66ff. amphoteric surfaces 272 – mixed micellar systems 75 angle hysteresis 288 – molecular characterization 65f. anionic micelles 245 – relative hydrophobicity 67 anionic monolayers 245 – sequential oxyanionic polymerisation anionic polymerization 413 64 annealing 34, 46 – solubilization of griseofulvin 68ff. antibodies 420 – solubilization of poorly soluble drugs apolipoproteins 416 61ff. aqueous phase 279 blood-brain barrier (BBB) 417 arrays, two-dimensional 283f. – in vitro model 418 asphaltene aggregates 138, 144 – permeability 418 asphaltenes 136 Boltzmann equation 251 atomic force microscopy (AFM) 107, 112, Boltzmann weights 256 125, 134, 173, 179ff., 313, 315ff., 329ff. bottle test 124, 136, 141 – contact mode 181 Bragg-Williams approximation 241, – non-contact mode 181 253, 258, 264, 343 – tapping mode 181 Brewster angle microscopy 129 – tip 180 bridging 277, 281, 287, 360, 388ff. avidin-biotin 420 – forces 215f. azidothymidine (AZT) 423 Colloids and Interface Science Series, Vol.