Summary of Pressure Gain Combustion Research at NASA
Total Page:16
File Type:pdf, Size:1020Kb
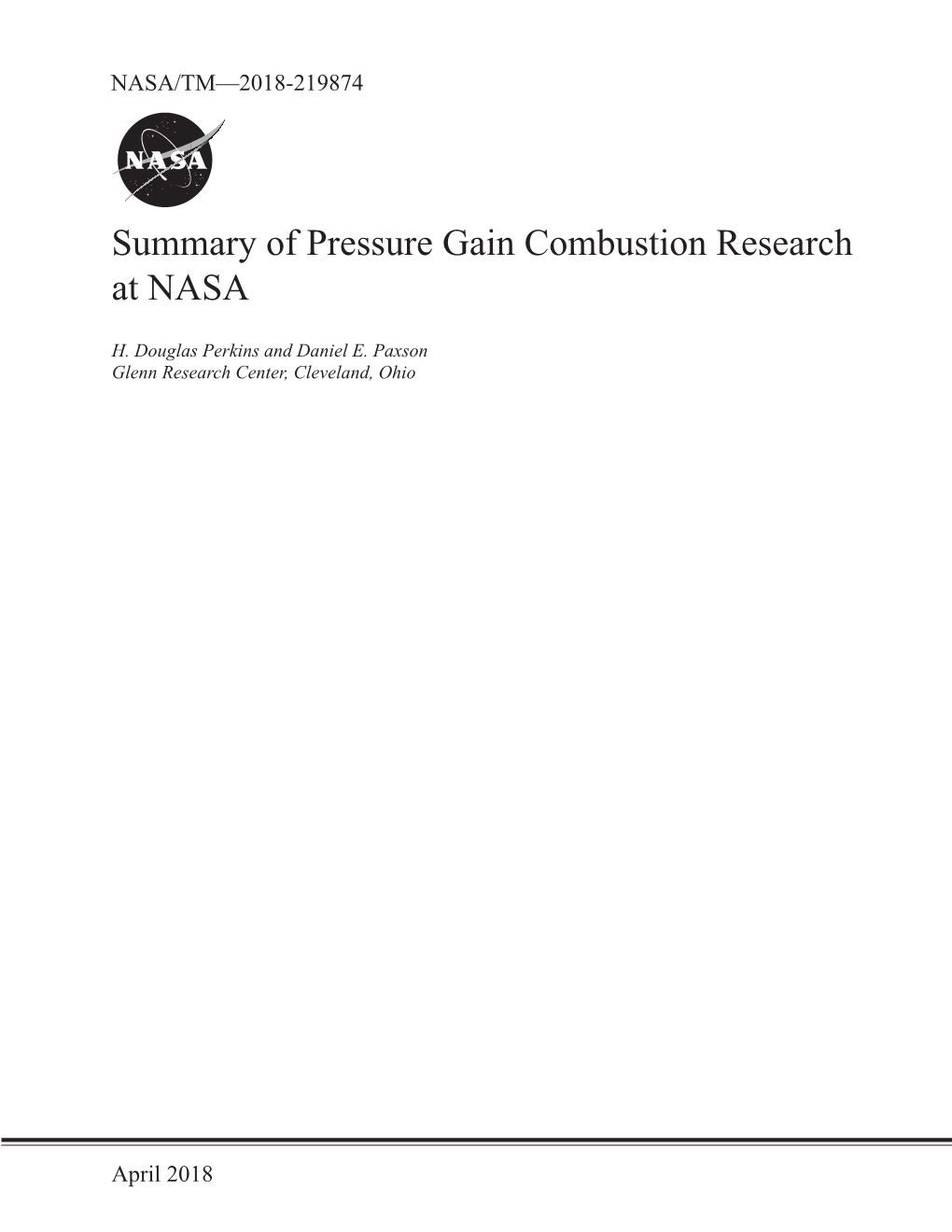
Load more
Recommended publications
-
Considerations and Simulations About Pulse Detonation Engine
MATEC Web of Conferences 290, 04009 (2019) https://doi.org/10.1051/matecconf /2019290 04009 MSE 2019 Considerations and simulations about Pulse Detonation Engine Vasile Prisacariu1,*, Constantin Rotaru1, and Mihai Leonida Niculescu2 1Henri Coandă Air Force Academy, Aviation Department, Brașov, Romania 2INCAS, Aerodynamic Department, București, Romania Abstract. PDE propulsion can work from a subsonic regime to hypersonic regimes; this type of engine can have higher thermodynamic efficiency compared to other turbojet or turbofan engines due to the removal of rotating construction elements (compressors and turbines) that can reduce the mass and total cost of propulsion system. The PDE experimental researches focused on both the geometric configuration and the thermo- gas-dynamic flow aspects to prevent uncontrolled self-ignition. This article presents a series of numerical simulations on the functioning of PDE with hydrogen at supersonic regimens. Acronyms and symbols PDE pulse detonation engine AB PDE after burner pulse detonation engine DDT deflagration-to-detonation transition PDRE pulse detonation rocket engine ZDN Zel'dovich-von Neumann-Doering Mx, My Mach numbers p pressure v volume T temperature ρ density u1, u2 velocity h1, h2 enthalpy s1, s2 (S) entropy Vo,V∞ speed 1 INTRODUCTION Detonation is an effective means of burning a fuel mixture and transforming chemical energy into mechanical energy. However, this concept of running the propulsion systems involves difficulties both in rapidly achieving the fuel mixture at high speeds and in initiating and sustaining detonation in a controlled manner. PDE differs from conventional propulsion systems in two main aspects: it generates an intermittent pulse and produces high pressure increase in the combustion chamber, which also represents a major advantage of a PDE, see Figure 1. -
Study and Numerical Simulation of Unconventional Engine Technology
STUDY AND NUMERICAL SIMULATION OF UNCONVENTIONAL ENGINE TECHNOLOGY by ANJALI SHEKHAR B.E Aeronautical Engineering VTU, Karnataka, 2013 A thesis submitted in partial fulfillment of the requirements for the degree of Master of Science, Aerospace Engineering, College of Engineering and Applied Science, University of Cincinnati, Ohio 2018 Thesis Committee: Chair: Ephraim Gutmark, Ph.D. Member: Shaaban Abdallah, Ph.D. Member: Mark Turner, Sc.D. An Abstract of Study and Numerical Simulation of Unconventional Engine Technology by Anjali Shekhar Submitted to the Graduate Faculty as partial fulfillment of the requirements for the Master of Science Degree in Aerospace Engineering University of Cincinnati December 2018 The aim of this thesis is to understand the working of two unconventional aircraft propul- sion systems and to setup a two-dimensional transient simulation to analyze its operational mechanism. The air traffic has nearly increased by about 40% in past three decades and calls for alternative propulsion techniques to replace or support the current traditional propulsion methodology. In the light of current demand, the thesis draws motivation from renewed inter- est in two non-conventional propulsion techniques designed in the past and had not been given due importance due to various flaws/drawbacks associated. The thesis emphasizes on the work- ing of Von Ohains thermal compression engine and pulsejet combustors. Computational Fluid Dynamics is used in current study as it offers very high flexibility and can be modified easily to incorporate the required changes. Thermal Compression engine is a design suggested by Von Ohain in 1948. The engine works on the principle of pressure rise caused inside the engine which completely depends on the temperature of working fluid and independent of rotations per minute. -
Aeronautical Engineering
NASA/S P--1999-7037/S U P PL407 September 1999 AERONAUTICAL ENGINEERING A CONTINUING BIBLIOGRAPHY WITH INDEXES National Aeronautics and Space Administration Langley Research Center Scientific and Technical Information Program Office The NASA STI Program Office... in Profile Since its founding, NASA has been dedicated CONFERENCE PUBLICATION. Collected to the advancement of aeronautics and space papers from scientific and technical science. The NASA Scientific and Technical conferences, symposia, seminars, or other Information (STI) Program Office plays a key meetings sponsored or cosponsored by NASA. part in helping NASA maintain this important role. SPECIAL PUBLICATION. Scientific, technical, or historical information from The NASA STI Program Office is operated by NASA programs, projects, and missions, Langley Research Center, the lead center for often concerned with subjects having NASA's scientific and technical information. substantial public interest. The NASA STI Program Office provides access to the NASA STI Database, the largest collection TECHNICAL TRANSLATION. of aeronautical and space science STI in the English-language translations of foreign world. The Program Office is also NASA's scientific and technical material pertinent to institutional mechanism for disseminating the NASA's mission. results of its research and development activities. These results are published by NASA in the Specialized services that complement the STI NASA STI Report Series, which includes the Program Office's diverse offerings include following report types: creating custom thesauri, building customized databases, organizing and publishing research TECHNICAL PUBLICATION. Reports of results.., even providing videos. completed research or a major significant phase of research that present the results of For more information about the NASA STI NASA programs and include extensive data or Program Office, see the following: theoretical analysis. -
Sunday Monday
Sunday Sunday, 29 July 2012 1-RECPT-1 Sunday Opening Reception Exhibit Hall 1830 - 2000 hrs Monday Monday, 30 July 2012 2-JPC-1/IECEC-1 JPC/IECEC Opening Monday Keynote Centennial Ballroom I 0800 - 0900 hrs Overview of NASA major program thrusts and Technology Development Opportunities Robert Lightfoot Associate Administrator NASA Monday, 30 July 2012 3-ABPSI-1/GTE-1 Turboelectric Distributed Propulsion I Hanover C Chaired by: H. KIM, NASA Glenn Research Center and A. GIBSON, Empirical Systems Aerospace LLC 1000 hrs 1030 hrs 1100 hrs 1130 hrs AIAA-2012-3700 AIAA-2012-3701 AIAA-2012-3702 Oral Presentation (Invited) Turboelectric Distributed Sensitivity of Mission Fuel Burn Hybrid Axial and Cross-Flow Evaluation of the Propulsion Propulsion System Modelling to Turboelectric Distributed Fan Propulsion for Transonic Integration Aerodynamics on a for Hybrid-Wing-Body Aircraft Propulsion Design Assumptions Blended Wing Body Aircraft Hybrid Wing Body Concept C. Liu, Self, Cranfield, United on the N3-X Hybrid Wing Body J. Kummer, J. Allred, Propulsive J. Chu, NASA Langley Research Kingdom Aircraft Wing, LLC, Elbridge, NY; J. Felder, Center, Hampton, VA J. Felder, G. Brown, NASA Glenn NASA Glenn Research Center, Research Center, Cleveland, OH; J. Cleveland, OH Chu, NASA Langley Research Center, Hampton, VA; M. Tong, NASA Glenn Research Center, Cleveland, OH Monday, 30 July 2012 4-HSABP/HYP-1/PC-1 Constant Volume Combustion Engines Regency VII Chaired by: V. TANGIRALA, General Electric Company and D. DAUSEN, Naval Postgraduate School 1000 hrs 1030 hrs 1100 hrs 1130 hrs AIAA-2012-3703 AIAA-2012-3704 AIAA-2012-3705 AIAA-2012-3706 Development of a Wave Disk Thermodynamics of the Wave Experimental Optimization of Experimental Study of Shock Engine Experimental Facility Disk Engine Static Valveless Self-Aspiration Transfer in a Multiple Pulse N. -
Program Schedule
Program Schedule AIAA Propulsion and Energy Forum and Exposition July 25 - 27, 2016 The Program Report was last updated July 20, 2016 at 01:01 AM EDT. To view the most recent meeting schedule online, visit https://aiaa-mpe16.abstractcentral.com/planner.jsp Monday, July 25, 2016 Time Session or Event Info 8:00 AM-9:00 AM, Ballroom A-D, PLNRY-01. INNOVATE OR DIE! (Note: Dying is easier) , Plenary, Forum Event 8:45 AM-9:30 AM, Exhibit Hall C, NW-01. Networking Coffee Break, Networking 9:30 AM-12:00 PM, 255 F, ABPSI-01. Nozzles and Exhaust, Technical Paper, 52nd AIAA/SAE/ASEE Joint Propulsion Conference, Chair: Chen Chuck, [email protected], Boeing Commercial Airplanes; Co-Chair: Darius Sanders, [email protected], Air Force Reseach Laboratory AIAA-2016-4500. Reducing residue in aluminized fuel-rich propellant 9:30-10:00 AM for Ramjets. N. Rathi; P. Ramakrishna AIAA-2016-4501. Prediction of NO Emissions Using a Stirred x 10:00-10:30 AM Reactor Modelling Approach for an Aero-Engine with RQL Combustor A. Prakash AIAA-2016-4502. Hot Streak Characterization in Serpentine Exhaust 10:30-11:00 AM Nozzles D.S. Crowe; C.L. Martin AIAA-2016-4503. Propulsion AerodynamicWorkshop II, Summary of 11:00-11:30 AM Participant Results for a Dual Separate Flow Reference Nozzle, Including Some Experimental Results R.L. Thornock AIAA-2016-4504. Open and Closed-Loop Responses of a Dual- 11:30-12:00 PM Throat Nozzle during Fluidic Thrust Vectoring M. Ferlauto; R. Marsilio 9:30 AM-12:00 PM, 255 E, ADP-01. -
Imece2007-44068-Pde
Proceedings of IMECE 2007 2007 ASME International Mechanical Engineering Congress and Exposition November 11–17, 2007, Seattle, Washington, USA IMECE2007–44068 PRACTICAL ISSUES IN GROUND TESTING OF PULSED DETONATION ENGINES Philip K. Panicker, Frank K. Lu, Donald R. Wilson Aerodynamics Research Center, Mechanical and Aerospace Engineering Department University of Texas at Arlington Arlington, Texas 76019 U.S.A. [email protected], [email protected], [email protected] ABSTRACT with or replaced by a low-pressure fan. Compact designs may be feasible, thereby achieving high thrust-to-weight ratios. In Pulsed detonation engines can potentially revolutionize aero- addition, various combinations and hybrids have been space propulsion and they are the subject of intense study. proposed, including ejector-augmented and combined cycle However, most of the studies involve single shot and very short engines [6–8], thereby extending the PDEs versatility. There duration test runs. Some of the practical issues in developing are also other potential non-aerospace applications of pulse PDEs are discussed from the viewpoint of developing ground- detonations, including electric power generation [9,10], slag based demonstrators. This represents only the beginning of a removal [11] and others [12]. roadmap toward the successful development of flightweight While a roadmap has been proposed for developing PDEs engines. Viable solutions are offered that may help overcome [13], there are no known operational PDEs presently. Instead, the difficulties posed by the high temperature and pressures on it appears that the lion’s share of experimental studies have the test rig and instrumentation. Commercial solenoid valves been performed using single-shot test beds or with short run and electronic fuel injectors are presented as means to achiev- times at frequencies below 50 Hz in the range of 10 to 20 s. -
2020 NASA Technology Taxonomy the Page Intentionally Left Blank
National Aeronautics and Space Administration 2020 NASA Technology Taxonomy The page intentionally left blank. i CONTENTS Letter from the Chief Technologist . iii Introduction . v TX01: Propulsion Systems . 1 TX02: Flight Computing and Avionics . 15 TX03: Aerospace Power and Energy Storage . 27 TX04: Robotic Systems . 35 TX05: Communications, Navigation, and Orbital Debris Tracking and Characterization Systems . 51 TX06: Human Health, Life Support, and Habitation Systems . 65 TX07: Exploration Destination Systems . 83 TX08: Sensors and Instruments . 95 TX09: Entry, Descent, and Landing . 105 TX10: Autonomous Systems . 115 TX11: Software, Modeling, Simulation, and Information Processing . 127 TX12: Materials, Structures, Mechanical Systems, and Manufacturing . 145 TX13: Ground, Test, and Surface Systems . 157 TX14: Thermal Management Systems . 173 TX15: Flight Vehicle Systems . 185 TX16: Air Traffic Management and Range Tracking Systems . 195 TX17: Guidance, Navigation, and Control . 201 Acronyms . 222 Acknowledgements . 225 ii Letter from the Chief Technologist “And as we renew our commitment to lead in space, let’s go with confidence and let’s go with faith. Faith in the vision and the goal that’s articulated today: that we can achieve it; that Americans can achieve anything that we put our minds to. Faith in the extraordinary ingenuity and capability of the men and women of NASA and America’s space enterprise, and their ability to meet those challenges if given the resources and the support to do it. And especially faith in the courage of the men and women who are now, and those who will join, the storied ranks of American astronauts—that next generation of restless pioneers that will carry American leadership into space. -
FINAL PROGRAM Innovations in Propulsion and Energy Driving System Solutions
2O16 25–27 JULY 2016 SALT LAKE CITY, UT Innovations in Propulsion and Energy Driving System Solutions FINAL PROGRAM www.aiaa-propulsionenergy.org #aiaaPropEnergy 16-1225 Real-Time Q&A and Polling during AIAA Propulsion NEW! and Energy 2016 withwith ConferenceConference IO!IO! During Plenary and Forum 360 Sessions, go to aiaa.cnf.io Getting Your Question Answered is as EASY as 1-2-3! 1. Click the “Ask” button to submit a question. 2. Check out the questions that other attendees are asking. 3. If you see a question that you want answered, click on the arrow on the left. The most popular questions automatically rise to the top. Participate in Session Polls 1. If Polls are available they will appear at the top of the page. Simply click/tap on a Poll to respond. 2. Choose your response(s) and hit “submit”. 3. After responding you will be able to see the results on your own device!* * Some Poll results may be hidden NO DOWNLOADING REQUIRED! Executive Steering Committee 2O16 AIAA Propulsion and Energy 2016 Welcome Welcome to Salt Lake City, Utah, and AIAA Propulsion and Energy 2016. We are excited to share the next few days with you as we explore the most pressing issues facing the future of propulsion and energy systems – the true heart of aerospace. With so many insightful and dynamic speakers and panelists, we are confident you will find the information presented here thought-provoking, impactful, and immediately useful to you in your work. Daniel “Dan” Michael Heil During the forum you will hear from thought leaders, learn about the latest technical Dumbacher Ohio Aerospace breakthroughs, and most importantly collaborate with other attendees from Purdue University Institute (Ret.) government, industry, and academia. -
Web-Based Innovation Indicators – Which Firm Web- Site Characteristics Relate to Firm-Level Innovation Activity?
// NO.19-063 | 12/2019 DISCUSSION PAPER // JANNA AXENBECK AND PATRICK BREITHAUPT Web-Based Innovation Indicators – Which Firm Web- site Characteristics Relate to Firm-Level Innovation Activity? Web-Based Innovation Indicators – Which Firm Website Characteristics Relate to Firm-Level Innovation Activity? Janna Axenbeck†+* & Patrick Breithaupt†* † Department of Digital Economy, ZEW – Leibniz Centre for European Economic Research, L7 1, 68161 Mannheim, Germany +Justus-Liebig-University Giessen, Faculty of Economics, Licher Straße 64, 35394 Gießen, Germany * Correspondence: [email protected]; Phone: +49 621 1235 – 188, [email protected]; Phone: +49 621 1235 – 217 December 31, 2019 Abstract Web-based innovation indicators may provide new insights into firm-level innovation activities. However, little is known yet about the accuracy and relevance of web-based information. In this study, we use 4,485 German firms from the Mannheim Innovation Panel (MIP) 2019 to analyze which website characteristics are related to innovation activities at the firm level. Website characteristics are measured by several text mining methods and are used as features in different Random Forest classification models that are compared against each other. Our results show that the most relevant website characteristics are the website’s language, the number of subpages, and the total text length. Moreover, our website characteristics show a better performance for the prediction of product innovations and innovation expenditures than for the prediction of process innovations. Keywords: Text as data, innovation indicators, machine learning JEL Classification: C53, C81, C83, O30 Acknowledgments: The authors would like to thank the German Federal Ministry of Education and Research for providing funding for the research project (TOBI - Text Data Based Output Indicators as Base of a New Innovation Metric; funding ID: 16IFI001). -
PULSE DETONATION ENGINE TECHNOLOGY: an OVERVIEW by Matthew Lam Daniel Tillie Timothy Leaver Brian Mcfadden APSC
PULSE DETONATION ENGINE TECHNOLOGY: AN OVERVIEW by Matthew Lam Daniel Tillie Timothy Leaver Brian McFadden APSC 201 PULSE DETONATION ENGINE TECHNOLOGY: AN OVERVIEW Submitted to Michael Schoen by Matthew Lam Daniel Tillie Timothy Leaver Brian McFadden Applied Science 201 The University of British Columbia November 26, 2004 ii ABSTRACT Pulse detonation is a propulsion technology that involves detonation of fuel to produce thrust more efficiently than current engine systems. By library research and an interview with Dr. Roger Reed of the Metals and Materials Engineering Department of the University of British Columbia, it is shown that Pulse Detonation Engine (PDE) technology is more efficient than current engine types by virtue of its mechanical simplicity and thermodynamic efficiency. As the PDE produces a higher specific thrust than comparable ramjet engines at speeds of up to approximately Mach 2.3, it is suitable for use as part of a multi-stage propulsion system. The PDE can provide static thrust for a ramjet or scramjet engine, or operate in combination with turbofan systems. As such, it sees potential applications in many sectors of the aerospace, aeronautic, and military industries. However, there remain engineering challenges that must be overcome before the PDE can see practical use. Current methods for initiating the detonation process need refinement. To this end, both Pratt & Whitney and General Electric have developed different processes to accomplish this. Also, current materials used in jet engines, such as Nickel-based super-alloys, are inadequate to withstand the extreme heat and pressure generated by the detonation cycle. Therefore, new materials must be developed for this purpose. -
The Largest Event for Aerospace Research, Development, and Technology
5–9 JANUARY 2015 KISSIMMEE, FL The Largest Event for Aerospace Research, Development, and Technology FINAL PROGRAM www.aiaa-SciTech.org #aiaaSciTech 14-339 WHAT’S IMPOSSIBLE TODAY WON’T BE TOMORROW. AT LOCKHEED MARTIN, WE’RE ENGINEERING A BETTER TOMORROW. We are partnering with our customers to accelerate manufacturing innovation from the laboratory to production. We push the limits in additive manufacturing, advanced materials, digital manufacturing and next generation electronics. Whether it is solving a global crisis like the need for clean drinking water or travelling even deeper into space, advanced manufacturing is opening the doors to the next great human revolution. Learn more at lockheedmartin.com © 2014 LOCKHEED MARTIN CORPORATION VC377_164 Executive Steering Committee AIAA SciTech 2015 Welcome We are excited to welcome you to the AIAA Science and Technology Forum and Exposition 2015 — the largest event for aerospace research, development, and technology in the world. We are confident that you will be informed, inspired, and motivated, as you take part in shaping the future of aerospace! Robert Braun Rich Christiansen Georgia Institute of Sierra Lobo, Inc. Over the coming days you will have the opportunity to hear from thought leaders in Technology our community, learn about the latest technical breakthroughs, collaborate with an unparalleled group of peers, and gain knowledge and insight with each session and event that you attend. Our organizing committee has worked hard to ensure that our plenary sessions will examine the most critical issues in aerospace today: investment trends and strategies for science and technology policy and R&D; how globalization will impact the aerospace economy; the future of aerospace design; climate change and the use of big data to gain a better understanding of Earth’s climate cycles; and how best to John Evans George Lesieutre construct the future workforce. -
Study of Feasibility of Pulse Detonation Engine Powered by Alternative Fuels
International Journal of Engineering and Advanced Technology (IJEAT) ISSN: 2249 – 8958, Volume-8, Issue-2S2, January 2019 Study of Feasibility of Pulse Detonation Engine Powered By Alternative Fuels Mahammadsalman Warimani, Muhammad Hanafi Azami, S. A. Khan, Ahmad Faris Ismail utilization [3]. Due to the rising price, non - renewability and Abstract - World energy demand will continue to increase environmental disadvantages of fossil fuels, researchers have because of the development of the economy of the world and an sought the appropriate alternative renewable fuels [4][2]. increase in population. Non-renewable crude oil- derived liquid Depending on the PDE type, they can range from fuels are used in the world for more than two hundred years. 90 % simple single tube systems to multi-tube systems, of liquid fuels are estimated to be consumed for energy generation and transportation. Liquid fuels cause environmental pollution valve-free or mechanical valves, they can be used as like carbon dioxide (CO2), carbon monoxide (CO), nitrogen combustion chambers for gas turbine and turbofan engines, oxides (NOx) and sulfur-containing residues which results in and they can also be used for rocket propulsion. The PDE can global warming. As we know energy is required but it is short range in size from micro - engines to huge gas turbine or supply, on other side waste is unwanted but it also unavoidable. turbojet engine systems [5]. PDE physical parameters are Agricultural, industrial & domestic waste can be converted into dependent on the fuel being used in them significantly [6]. biodiesel, biogas utilizing various techniques. Biogas, biodiesel, biomass, biofuel, alcohol, vegetable oils and so on can solve This paper aims to investigate various alternative fuel-based environmental problems.