Reducing Foreign Object Damage Through Improved Human Performance: Best Practices
Total Page:16
File Type:pdf, Size:1020Kb
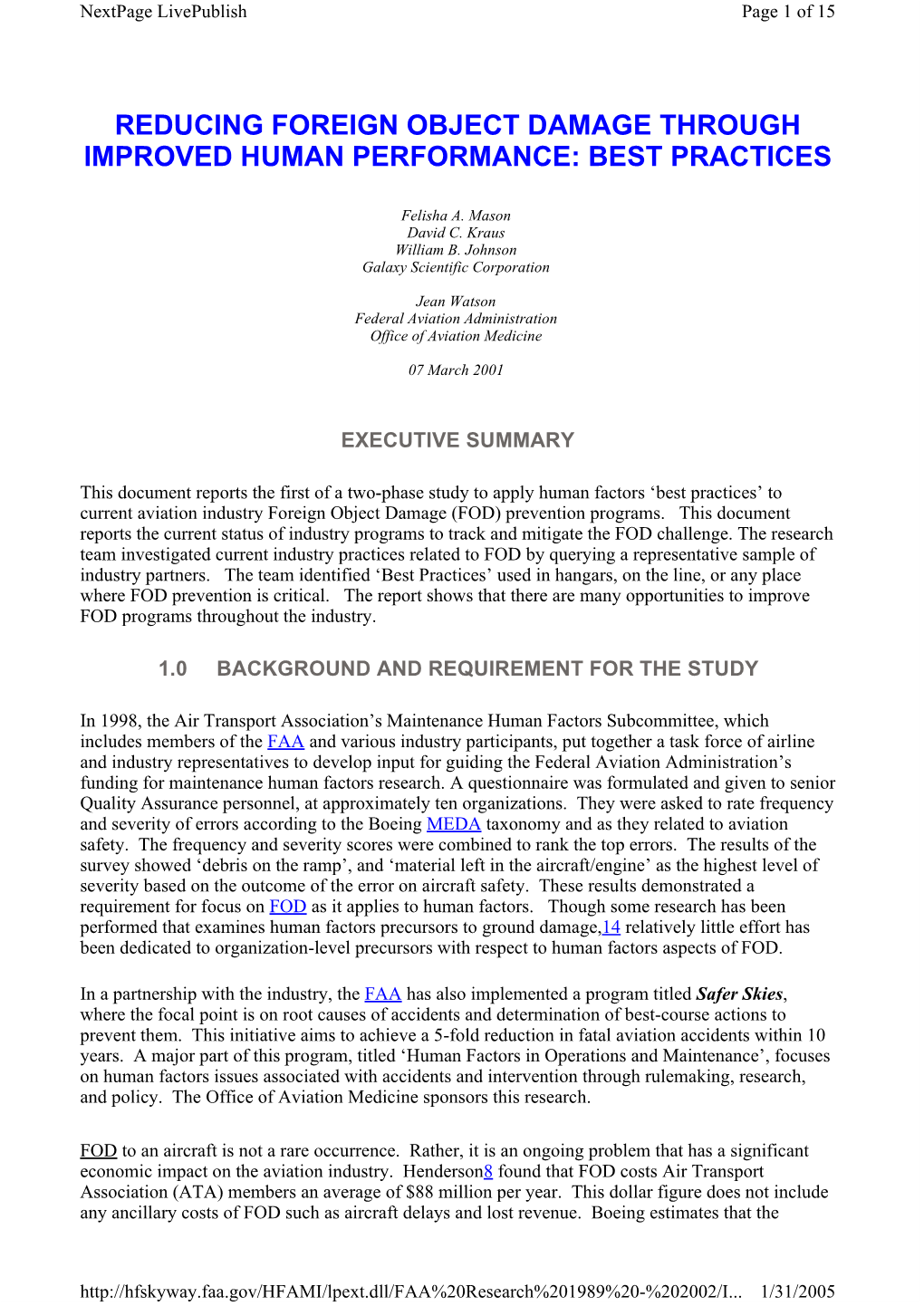
Load more
Recommended publications
-
Turbofan Engine Malfunction Recognition and Response Final Report
07/17/09 Turbofan Engine Malfunction Recognition and Response Final Report Foreword This document summarizes the work done to develop generic text and video training material on the recognition and appropriate response to turbofan engine malfunctions, and to develop a simulator upgrade package improving the realism of engine malfunction simulation. This work was undertaken as a follow-on to the AIA/AECMA report on Propulsion System Malfunction Plus Inappropriate Crew Response (PSM+ICR), published in 1998, and implements some of the recommendations made in the PSM+ICR report. The material developed is closely based upon the PSM+ICR recommendations. The work was sponsored and co-chaired by the ATA and FAA. The organizations involved in preparation and review of the material included regulatory authorities, accident investigation authorities, pilot associations, airline associations, airline operators, training companies and airplane and engine manufacturers. The FAA is publishing the text and video material, and will make the simulator upgrade package available to interested parties. Reproduction and adaptation of the text and video material to meet the needs of individual operators is anticipated and encouraged. Copies may be obtained by contacting: FAA Engine & Propeller Directorate ANE-110 12 New England Executive Park Burlington, MA 01803 1 07/17/09 Contributing Organizations and Individuals Note: in order to expedite progress and maximize the participation of US airlines, it was decided to hold all meetings in North America. European regulators, manufacturers and operators were both invited to attend and informed of the progress of the work. Air Canada Capt. E Jokinen ATA Jim Mckie AirTran Capt. Robert Stienke Boeing Commercial Aircraft Van Winters CAE/ Flight Safety Boeing Capt. -
What Is Quality? FOD &
What is Quality? FOD & ESD Presented by Janey Diogo 1 Agenda • Quality – Aerospace and Aviation • Foreign Object Debris (FOD) • Electrostatic Discharge (ESD) 2 What is Quality? • Quality is conformance to requirements. – For the product and the customer's requirements. – The system of quality is prevention. – The performance standard is zero defects (relative to requirements). – The measurement of quality is the price of nonconconformance. • Philip Crosby, a well known guru of Quality Management said “It is less expensive to do it right the first time than to pay for rework & repairs. • 3 Quality Assurance • A systematic process of checking to see whether a product or service being developed is meeting specified requirements. – Quality Assurance is a monitoring process. 4 Quality Control • A measure of excellence or a state of being free from defects, deficiencies and significant variations. – Quality Control is an evaluation process. 5 Quality History 1901 - Sir John Wolfe-Barry (the man who designed London's Tower Bridge) instigated the Council of the Institution of Civil Engineers to form a committee to consider standardizing iron and steel sections 1937 - Joseph Juran Introduced the Pareto principle (80/20 rule) 1937 - Hindenburg explosion 36 lives lost (ESD) 1946 - International Organization for Standardization founded in Geneva, Switzerland and the American Society for Quality Control (ASQC) was formed 1960 - First Quality Control Circles formed in Japan 1967 - Apollo 1 fire (ESD) 3 lives lost 1967 1970 - Apollo 13 Oxygen tank explosion (ESD) – No lives lost 6 Quality History 1977 - International Quality Control Circles formed 1979 - British Standard BS 5750 issued (replaced by ISO 9001 in 1987) 1980 - Aviation System Standards (AVN) focused on safety operations Managed by the FAA Safety and Quality Assurance Office 1986 - Six Sigma formulated by Bill Smith (Motorola) 1986 - Kaizen Institute established 1987 - Malcom Baldrige National Quality Award established 1988 - European Foundation for Quality management established by 14 European countries. -
Composites Fact Sheet
COMPOSITES FACT SHEET Composites Fact sheet Introduction to Composites Composites are lighter, stronger and have more design shape freedom than aluminium.1 These advantages are reasons why aircraft manufacturers use more composite materials in their aircraft nowadays. Composites increase the design shape freedom. For example, the Boeing 787 Dreamliner weight consists of 50% composite materials2 and is more aerodynamic than previous models due to more design flexibility of composites in comparison with metals. Low weight and better aerodynamics contribute to 20 – 30% less fuel consumption than today’s similarly sized aircraft.2 However composite material has a few disadvantages as well. Composites are susceptible to different kinds of damage than metal structures such as micro-cracking and delamination.3 Conventional damage detection methods are not optimized to detect these kind of damages. That is why additional structural weight is necessary to provide safety at all times.4 Furthermore, damage Figure 1: A Boeing 787 Dreamliner from Arkefly assessments of composites (Figure 1) take more time nowadays than traditional metal structures (Example 1) due to the lack of routine with the repair of these large structures. Example 1: WILLEMSTAD, September 25th, 2014 A Boeing 787 Dreamliner from Arkefly was involved in an incident with a ground vehicle. The aircraft was hit by a high-loader, which was supplying the aircraft at the time. Due to a thorough assessment by Arkefly in cooperation with Boeing the passengers were delayed for almost a day. After inspection it turned out the aircraft was not damaged by the ground vehicle and Arkefly received approval to fly to Amsterdam. -
Raspberry Pi Based Vision System for Foreign Object Debris (FOD) Detection
Bachelor Thesis Electrical Engineering June 2020 Raspberry Pi Based Vision System for Foreign Object Debris (FOD) Detection Sarfaraz Ahmad Mahammad Sushma Vendrapu Department of Mathematics and Nature Sciences Blekinge Institute of Technology SE–371 79 Karlskrona, Sweden This thesis is submitted to the Department of Mathematics and Nature Science at Blekinge Institute of Technology in partial fulfillment of the requirements for the degree of Bach- elor in Electrical Engineering with Emphasis on Telecommunication. Contact Information: Authors: Sarfaraz Ahmad Mahammad E-mail: [email protected] Sushma Vendrapu E-mail: [email protected] Supervisor: Prof. Wlodek J. Kulesza Industrial Supervisors: Dawid Gradolewski Damian M. Dziak Address: Bioseco Sp. z o. o. Budowlanych 68 Street 80-298 Gdansk´ Poland University Examiner: Irina Gertsovich Department of Mathematics and Nature Sci- Internet : www.bth.se ence Blekinge Institute of Technology Phone : +46 455 38 50 00 SE–371 79 Karlskrona, Sweden Fax : +46 455 38 50 57 Abstract Background: The main purpose of this research is to design and develop a cost-effective system for detection of Foreign Object Debris (FOD), dedicated to airports. FOD detection has been a significant problem at airports as it can cause damage to aircraft. Developing such a device to detect FOD may require complicated hardware and software structures. The proposed solution is based on a computer vision system, which comprises of flexible off the shelf components such as a Raspberry Pi and Camera Module, allowing the simplistic and efficient way to detect FOD. Methods: The solution to this research is achieved through User-centered design, which implies to design a system solution suitably and efficiently. -
Mcdonnell Douglas DC 10-30, PP-VMD
McDonnell Douglas DC 10-30, PP-VMD AAIB Bulletin No: 7/97 Ref: EW/C97/2/1Category: 1.1 Aircraft Type and Registration: McDonnell Douglas DC 10-30, PP-VMD No & Type of Engines: 3 CF6 turbofan engines Year of Manufacture: 1975 Date & Time (UTC): 8 February 1997 at 2227 hrs Location: London Heathrow Airport Type of Flight: Scheduled Passenger Persons on Board: Crew - 18 - Passengers - 127 Injuries: Crew - None - Passengers - None Nature of Damage: No 7 and 8 wheels and tyres badly damaged Commander's Licence: Airline Transport Pilot's Licence Commander's Age: 50 years (approximately) Commander's Flying Experience: 14,000 hours (of which 4,500 were on type) Last 90 days - 60 hours Last 28 days - 20 hours Information Source: AAIB Field Investigation History of Flight The aircraft involved in this accident arrived at London HeathrowAirport from Rio de Janeiro earlier the same day at 1233 hrs. On arrival it was parked at Gate H30 and later towed to its departureGate H5 at 1945 hrs. At 2207 hrs the flight was cleared for enginestart and push-back and it commenced taxiing to Runway 27R nineminutes later. The taxi route to the runway took the aircraftdirectly onto the outer taxiway and then onto Runway 23 whichit backtracked. The total time spent taxiing was approximatelynine minutes. The flight destination was São Paulo, Brazil and, due tothe length of the flight, two flight deck crews were on board. The crew had arrived two days previously and, for the departure,consisted of a Captain in the left hand seat, who was undertakinga conversion from a different aircraft type, and a training Captainin the right hand seat who was the designated aircraft commander. -
FOD Awareness
FOD Awareness What is FOD? Foreign Object Debris (FOD) can be as simple as a nut, a piece of concrete, a piece of paper, a stone, a suitcase handle, a screwdriver or a passenger. Throwaway items are inherently dangerous. In the working environment of an apron, they contribute to the damage or potential damage to aircraft, ground equipment and perhaps even endanger life. Foreign Object Debris can lead to Foreign Object Damage. Examples of FOD • Aircraft parts, rocks, broken pavement, ramp equipment, and vehicle parts: Damage usually occurs when the aircraft is taking off or landing. The intake suction from a jet engine is powerful enough to suck up loose material lying on the runway, and the winds created by a helicopter or prop-driven aircraft's rotors or by a jet blast can send such objects airborne, creating hazards to nearby personnel. • Parts from ground vehicles • Garbage, maintenance tools, etc. mistakenly or purposely deposited on tarmac and/or runway surfaces. • Hail can break windshields and damage or stop engines. • Ice on the wings, propellers, or engine intakes • Dust or ash clogging the air intakes (as in sandstorms in desert operating conditions or ash clouds in volcanic eruptions). • Tools, bolts, metal shavings, lock wire, etc. mistakenly left behind inside aircraft during the manufacturing process or maintenance. Generally speaking, bird strikes (when an aero plane flies into a bird, the impact can cause severe damage from a bird striking the fuselage, engine, etc) are not considered to be FOD strikes, unless the bird or wildlife was already dead and lying on the operating surface when the strike occurred. -
Differences in Characteristics of Aviation Accidents During 1993-2012 Based on Aircraft Type
NASA/CR–2015-218999 Differences in Characteristics of Aviation Accidents during 1993-2012 Based on Aircraft Type Joni K. Evans Analytical Mechanics Associates, Inc., Hampton, Virginia December 2015 NASA STI Program . in Profile Since its founding, NASA has been dedicated to the x CONFERENCE PUBLICATION. advancement of aeronautics and space science. The Collected papers from scientific and technical NASA scientific and technical information (STI) conferences, symposia, seminars, or other program plays a key part in helping NASA maintain meetings sponsored or this important role. co-sponsored by NASA. The NASA STI program operates under the auspices x SPECIAL PUBLICATION. Scientific, of the Agency Chief Information Officer. It collects, technical, or historical information from NASA organizes, provides for archiving, and disseminates programs, projects, and missions, often NASA’s STI. The NASA STI program provides access concerned with subjects having substantial to the NTRS Registered and its public interface, the public interest. NASA Technical Reports Server, thus providing one of the largest collections of aeronautical and space x TECHNICAL TRANSLATION. science STI in the world. Results are published in both English-language translations of foreign non-NASA channels and by NASA in the NASA STI scientific and technical material pertinent to Report Series, which includes the following report NASA’s mission. types: Specialized services also include organizing x TECHNICAL PUBLICATION. Reports of and publishing research results, distributing completed research or a major significant phase of specialized research announcements and feeds, research that present the results of NASA providing information desk and personal search Programs and include extensive data or theoretical support, and enabling data exchange services. -
A Study of Foreign Object Damage (Fod) and Prevention Method at the Airport and Aircraft Maintenance Area
Special Issue - 2019 International Journal of Engineering Research & Technology (IJERT) ISSN: 2278-0181 CONFCALL - 2019 Conference Proceedings A Study of Foreign Object Damage (Fod) and Prevention Method at the Airport and Aircraft Maintenance Area N. Rajamurugu Assistant professor of Aero dept Apollo Engineering College. P. Karthikeyan A. Imran Hussain Assistant professor of Aero dept Dept.of Aero Apollo Engineering College. Apollo Engineering College. K. Ajithkumar V. Vimalpraksh Dept.of Aero Dept.of Aero Apollo Engineering College. Apollo Engineering College. Abstract:- Foreign object damage (FOD) is a common risk for FOD cases happened. Apart from that, this paper is aimed aviation industry that causes potential damage for an aircraft to classify FOD based on their specification, understand the ,external FOD hazards include bird strikes , sand stormes ,ash consequences of FOD to the aircraft and identify the cost clouds on the runway .Internal FOD Hazards creates an contributed by FOD. Throughout the completion of this interference with flight safety by means of sort out electrical research, several methods had been used to gather reliable connections, improper control cables etc,since long time ago and it has contributed to many terrible incidents .The cost of information and data. Most information was obtained FOD obstrucles every year is very high, which is around RM through research from reliable sources such as internet, 1.2 billion. Therefore, FOD has to be eliminated without technical report, books, articles and journals. Moreover, creating an impact on performance and it should proper Federal Aviation Administration (FAA) and ATSB technique and strategy has to be taken by the designated websites were really useful in searching for information, organizations including airlines to further eliminate the FOD especially for FOD occurrences and the FOD Prevention occurrences. -
Integrative Use of Computer Vision and Unmanned Aircraft Technologies in Public Inspection: Foreign Object Debris Image Collection
Integrative Use of Computer Vision and Unmanned Aircraft Technologies in Public Inspection: Foreign Object Debris Image Collection Travis J. E. Munyer Daniel Brinkman Department of Computer Science, University of Nebraska Department of Computer Science, University of Nebraska Omaha Omaha [email protected] [email protected] Chenyu Huang Xin Zhong Aviation Institute, University of Nebraska Omaha Department of Computer Science, University of Nebraska [email protected] Omaha [email protected] ABSTRACT ACM Reference Format: Unmanned Aircraft Systems (UAS) have become an important re- Travis J. E. Munyer, Daniel Brinkman, Chenyu Huang, and Xin Zhong. 2021. Integrative Use of Computer Vision and Unmanned Aircraft Technologies source for public service providers and smart cities. The purpose of in Public Inspection:: Foreign Object Debris Image Collection. In DG.O2021: this study is to expand this research area by integrating computer The 22nd Annual International Conference on Digital Government Research vision and UAS technology to automate public inspection. As an (DG.O’21), June 09–11, 2021, Omaha, NE, USA. ACM, New York, NY, USA, initial case study for this work, a dataset of common foreign object 7 pages. https://doi.org/10.1145/3463677.3463743 debris (FOD) is developed to assess the potential of light-weight automated detection. This paper presents the rationale and cre- ation of this dataset. Future iterations of our work will include 1 INTRODUCTION further technical details analyzing experimental implementation. Integrating state-of-the-art advances in technology has provided At a local airport, UAS and portable cameras are used to collect the consistent benefit towards major city operations. Artificial intel- data contained in the initial version of this dataset. -
A MID Region Wildlife& FOD Risk Reduction Program
24- 26 March 2014 Cairo, Egypt A MID Region Wildlife& FOD Risk Reduction Program Session #7 Presentation #2 Contents 1. Common FOD damage expenses 2. Egyptian Law #28 3. ECAR Part 139 4. EAC 139-25 Chapter 3 5. EAC 139-25 Chapter 10 6. ECAR PART 121.703 7. ECAR PART 39 SUBPART B 8. Most important thing (FOD is preventable) 9. Summary 10. Conclusion Common FOD damage expenses: Engine damage fuselage damage Flight Tire damage delay/cancellation cost FOD presented by ECAA *Egyptian Law #28 issued 1981 amended by law 136 2010 Article 20 bis Responsibility for the Operation of the Aerodromes and Air Navigation Services: • A person authorized to operate any of the aerodromes, landing areas, airstrips or the facilities of air navigation services shall be responsible for their operation and the implementation of the requirements of the flight’s security and safety under the supervision of the Civil Aviation Authority. FOD presented by ECAA ECAR Part 139 Certification and Operations: Land Airports Intended To Serve Commercial Or Non-Commercial Aircraft Operations States that” 139.315 Paved areas. (a) Each certificate holder shall maintain, and promptly repair the pavement of, each runway, taxiway, loading ramp, and parking area on the airport which is available for air carrier use as follows: • (4) Mud, dirt, sand, loose aggregate, debris, foreign objects, rubber deposits, and other contaminants shall be removed promptly and as completely as practicable. • (b) EAC 139-26 contains standards and procedures for the maintenance and configuration of paved areas which are acceptable to the ECAA. • FOD presented by ECAA • 139.349 (last amended October 2013) • c) Removal of contaminants • (1) (2)(3)Slush, standing water, mud, dust, sand, oil, rubber deposits and other contaminants shall be removed from the surface of runways ,Taxiways and Aprons in use as rapidly and completely as possible to minimize accumulation. -
VLCA Aircraft Discussion
Analysis of Air Transportation Systems The Aircraft and the System Dr. Antonio A. Trani Associate Professor of Civil and Environmental Engineering Virginia Polytechnic Institute and State University Falls Church, Virginia June 9-12, 2003 NEXTOR - National Center of Excellence for Aviation Research 1 Material Presented in this Section • The aircraft and the airport • Aircraft classifications • Aircraft characteristics and their relation to airport planning • New large capacity aircraft (NLA) impacts NEXTOR - National Center of Excellence for Aviation Research 2 Purpose of the Discussion • Introduces the reader to various types of aircraft and their classifications • Importance of aircraft classifications in airport engineering design • Discussion on possible impacts of Very Large Capacity Aircraft (VLCA, NLA, etc.) • Preliminary issues on geometric design (apron standards) and terminal design NEXTOR - National Center of Excellence for Aviation Research 3 Relevance of Aircraft Characteristics • Aircraft classifications are useful in airport engineering work (including terminal gate sizing, apron and taxiway planning, etc.) • Most of the airport design standards are intimately related to aircraft size (i.e., wingspan, aircraft length, aircraft wheelbase, aircraft seating capacity, etc.) • Airport fleet compositions vary over time and thus is imperative that we learn how to forecast expected vehicle sizes over long periods of time NEXTOR - National Center of Excellence for Aviation Research 4 Aircraft Classifications Aircraft are generally classified -
European Aviation Safety Agency NOTICE of PROPOSED
European Aviation Safety Agency 18 Jan 2013 NOTICE OF PROPOSED AMENDMENT (NPA) 2013-02 DRAFT DECISION OF THE EXECUTIVE DIRECTOR OF THE EUROPEAN AVIATION SAFETY AGENCY amending Decision 2003/2/RM of the Executive Director of the European Aviation Safety Agency of 17 October 2003 on certification specifications for large aeroplanes (‘CS-25’) ‘Protection from debris impacts’ TE.RPRO.00034-002© European Aviation Safety Agency. All rights reserved. Proprietary document. Copies are not controlled. Confirm revision status through the EASA Internet/Intranet. NPA 2013-02 18 Jan 2013 EXECUTIVE SUMMARY This NPA proposes new certification standards for protection of large aeroplanes against some categories of threats: tyre and wheel failure (debris, burst pressure effect), small engine debris and runway debris. The proposed amendment of CS-25 would rationalise the current regulatory material by developing a model for each type of threat which will be applicable to the whole aeroplane. It was prepared based on the reports made by a Working Group including representatives of the industry (Airbus, Boeing, Rolls Royce) and aviation authorities (EASA, ENAC Italy, FAA, TCCA). The Working Group reviewed all available information from existing certification practices, studies and known in-service occurrences. Recognizing that some differences exist among manufacturers practices, the Working Group had to make compromises to reach a proposal for amending CS-25 that is acceptable by everyone and that will contribute to improve the level of safety on future designs. The proposal meets the objective of this rulemaking task without creating unacceptable costs for applicants. An economic benefit is even anticipated from the simplification of the certification process.