(Khevi–Ubisa Section) Improvement Project Financed by the Asian Development Bank
Total Page:16
File Type:pdf, Size:1020Kb
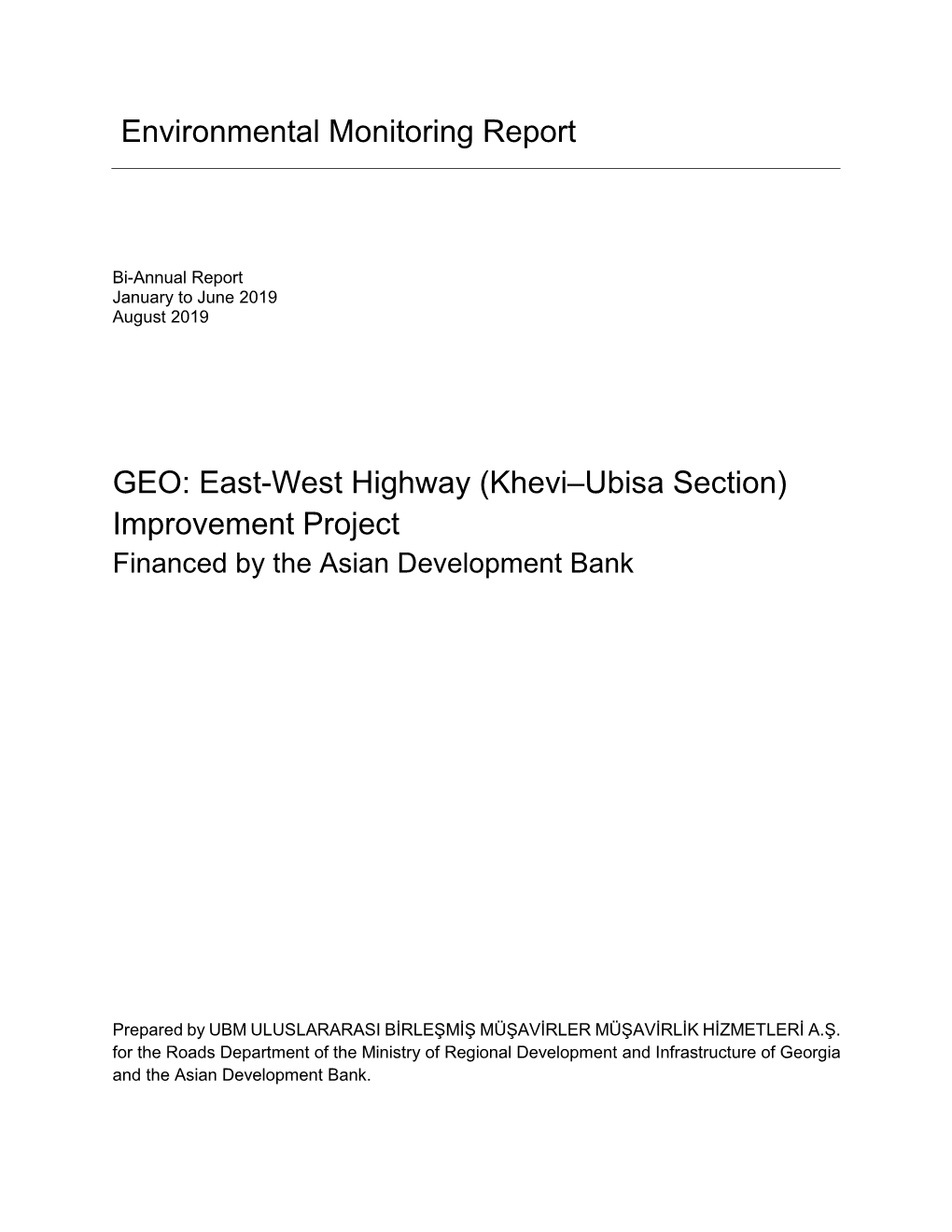
Load more
Recommended publications
-
A Short History of Georgian Architecture
A SHORT HISTORY OF GEORGIAN ARCHITECTURE Georgia is situated on the isthmus between the Black Sea and the Caspian Sea. In the north it is bounded by the Main Caucasian Range, forming the frontier with Russia, Azerbaijan to the east and in the south by Armenia and Turkey. Geographically Georgia is the meeting place of the European and Asian continents and is located at the crossroads of western and eastern cultures. In classical sources eastern Georgia is called Iberia or Caucasian Iberia, while western Georgia was known to Greeks and Romans as Colchis. Georgia has an elongated form from east to west. Approximately in the centre in the Great Caucasian range extends downwards to the south Surami range, bisecting the country into western and eastern parts. Although this range is not high, it produces different climates on its western and eastern sides. In the western part the climate is milder and on the sea coast sub-tropical with frequent rains, while the eastern part is typically dry. Figure 1 Map of Georgia Georgian vernacular architecture The different climates in western and eastern Georgia, together with distinct local building materials and various cultural differences creates a diverse range of vernacular architectural styles. In western Georgia, because the climate is mild and the region has abundance of timber, vernacular architecture is characterised by timber buildings. Surrounding the timber houses are lawns and decorative trees, which rarely found in the rest of the country. The population and hamlets scattered in the landscape. In eastern Georgia, vernacular architecture is typified by Darbazi, a type of masonry building partially cut into ground and roofed by timber or stone (rarely) constructions known as Darbazi, from which the type derives its name. -
Semi-Annual Environmental Monitoring Report
Semi-annual Environmental Monitoring Report Project Number GEO 49257 Loan No GEO 3715 Bi- Annual Report July - December 2019 January 2020 Georgia: East - West Highway (Khevi-Ubisa Section) Improvement Project Financed by the Asian Development Bank Prepared by: Kashif Bashir Senior Environmental Specialist of UBM Endorsed by: Levan Kupatashvili, Deputy Chairman of Roads Department of the Ministry of Regional Development and Infrastructure of Georgia Abbreviations ADB Asian Development Bank AP Affected Person BOD Bio-Chemical Oxygen Demand BP Batching Plant CAREC Central Asia Regional Economic Corridor CC Construction Contractor COD Chemical Oxygen Demand CSCS Consultancy Services for Construction Supervision CSC Construction Supervision Consultant CSEMP Contractor’s Contract Specific Environmental Management Plan dB (A) Decibel DO Dissolved Oxygen EIA Environmental Impact Assessment EIB European Investment Bank EMP Environmental Management Plan EMR Environmental Monitoring Report ESR Environmental Sensitive Receiver GRM Grievance Redress Mechanism HS Health & Safety HSE Health Safety and Environment IEE Initial Environmental Examination IFC International Finance Corporation MAC Maximum Admissible Concentration MoEPA Ministry of Environmental Protection and Agriculture MoESD Ministry of Economy and Sustainable Development 3 NCN Non-Conformance Notice NCR Non-Conformance Report NFA National Forest Agency NOC No Objection Certificate OSHA Occupational Safety and Health Administration PPE Personnel Protective Equipment’ PAPs Project Affected Persons PIU Project Implementation Unit QC Quality Control RD Road Department RoW Right of Way SC Supervision Consultant SEMP Site Specific Environmental Management Plan SFF State Forest Fund SPS Safeguard Policy Statement STD Sexually Transmitted Diseases TSS Total Suspended Solids VG Village Governor This Bi- Annual Environmental Monitoring is a document of the borrower. The views expressed herein do not necessarily represent those of ADB's Board of Directors, Management, or staff, and may be preliminary in nature. -
PRO GEORGIA JOURNAL of KARTVELOLOGICAL STUDIES N O 27 — 2017 2
1 PRO GEORGIA JOURNAL OF KARTVELOLOGICAL STUDIES N o 27 — 2017 2 E DITOR- IN-CHIEF David KOLBAIA S ECRETARY Sophia J V A N I A EDITORIAL C OMMITTEE Jan M A L I C K I, Wojciech M A T E R S K I, Henryk P A P R O C K I I NTERNATIONAL A DVISORY B OARD Zaza A L E K S I D Z E, Professor, National Center of Manuscripts, Tbilisi Alejandro B A R R A L – I G L E S I A S, Professor Emeritus, Cathedral Museum Santiago de Compostela Jan B R A U N (†), Professor Emeritus, University of Warsaw Andrzej F U R I E R, Professor, Universitet of Szczecin Metropolitan A N D R E W (G V A Z A V A) of Gori and Ateni Eparchy Gocha J A P A R I D Z E, Professor, Tbilisi State University Stanis³aw L I S Z E W S K I, Professor, University of Lodz Mariam L O R T K I P A N I D Z E, Professor Emerita, Tbilisi State University Guram L O R T K I P A N I D Z E, Professor Emeritus, Tbilisi State University Marek M ¥ D Z I K (†), Professor, Maria Curie-Sk³odowska University, Lublin Tamila M G A L O B L I S H V I L I, Professor, National Centre of Manuscripts, Tbilisi Lech M R Ó Z, Professor, University of Warsaw Bernard OUTTIER, Professor, University of Geneve Andrzej P I S O W I C Z, Professor, Jagiellonian University, Cracow Annegret P L O N T K E - L U E N I N G, Professor, Friedrich Schiller University, Jena Tadeusz Ś W I Ę T O C H O W S K I (†), Professor, Columbia University, New York Sophia V A S H A L O M I D Z E, Professor, Martin-Luther-Univerity, Halle-Wittenberg Andrzej W O Ź N I A K, Professor, Polish Academy of Sciences, Warsaw 3 PRO GEORGIA JOURNAL OF KARTVELOLOGICAL STUDIES No 27 — 2017 (Published since 1991) CENTRE FOR EAST EUROPEAN STUDIES FACULTY OF ORIENTAL STUDIES UNIVERSITY OF WARSAW WARSAW 2017 4 Cover: St. -
Ordinance of the Government of Georgia No 209 of 1 April 2020 – Website, 1.4.2020
Government of Georgia Ordinance No 181 23 March 2020 Tbilisi On the Approval of Measures to be Implemented in connection with the Prevention of the Spread of the Novel Coronavirus (COVID-19) in Georgia Article 1 On the basis of Decree No 1 of 21 March 2020 of the President of Georgia on ‘Measures to be Implemented in connection with the Declaration of a State of Emergency throughout the Whole Territory of Georgia’, the attached ‘Measures to be Implemented in connection with the Prevention of the Spread of the Novel Coronavirus (COVID-19) in Georgia’ shall be approved. Article 11 The list of business entities carrying out economic activities, whose operation shall not be restricted during the period of the state of emergency, shall be approved as provided for in Annex No 1. Ordinance of the Government of Georgia No 209 of 1 April 2020 – website, 1.4.2020 Article 12 The annexed list of economic activities which, on respective conditions, shall not be restricted during the period of the state of emergency, shall be approved in accordance with Annex No 2. Ordinance of the Government of Georgia No 211 of 1 April 2020 – website, 2.4.2020 Article 13 The economic activities and facilities/business entities carrying out economic activities, which shall not be restricted during the period of the state of emergency and which are not listed in Annexes No 1 and No 2 approved by this Ordinance, shall be approved in accordance with Annex No 3. Ordinance of the Government of Georgia No 211 of 1 April 2020 – website, 2.4.2020 Article 14 In accordance with Annex No 4, the list of entities carrying out economic activities, whose operation shall not be restricted during the period of the state of emergency only for the purpose of implementing the projects defined by the same annex, shall be approved. -
6. Imereti – Historical-Cultural Overview
SFG2110 SECOND REGIONAL DEVELOPMETN PROJECT IMERETI REGIONAL DEVELOPMENT PROGRAM IMERETI TOURISM DEVELOPMENT STRATEGY Public Disclosure Authorized STRATEGIC ENVIRONMENTAL, CULTURAL HERITAGE AND SOCIAL ASSESSMENT Public Disclosure Authorized Public Disclosure Authorized Public Disclosure Authorized Tbilisi, December, 2014 ABBREVIATIONS GNTA Georgia National Tourism Administration EIA Environnemental Impact Assessment EMP Environmental Management Plan EMS Environmental Management System IFI International Financial Institution IRDS Imereti Regional Development Strategy ITDS Imereti Tourism Development Strategy MDF Municipal Development Fund of Georgia MoA Ministry of Agriculture MoENRP Ministry of Environment and Natural Resources Protection of Georgia MoIA Ministry of Internal Affairs MoCMP Ministry of Culture and Monument Protection MoJ Ministry of Justice MoESD Ministry of Economic and Sustaineble Developmnet NACHP National Agency for Cultural Heritage Protection PIU Project Implementation Unit PPE Personal protective equipment RDP Regional Development Project SECHSA Strategic Environmental, Cultural Heritage and Social Assessment WB World Bank Contents EXECUTIVE SUMMARY ........................................................................................................................................... 0 1. INTRODUCTION ........................................................................................................................................... 14 1.1 PROJECT CONTEXT ............................................................................................................................... -
Some Notes on the Topography of Eastern Pontos Euxeinos in Late Antiquity and Early
Andrei Vinogradov SOME NOTES ON THE TOPOGRAPHY OF EASTERN PONTOS EUXEINOS IN LATE ANTIQUITY AND EARLY BYZANTIUM BASIC RESEARCH PROGRAM WORKING PAPERS SERIES: HUMANITIES WP BRP 82/HUM/2014 This Working Paper is an output of a research project implemented within NRU HSE’s Annual Thematic Plan for Basic and Applied Research. Any opinions or claims contained in this Working Paper do not necessarily reflect the views of HSE. Andrei Vinogradov1 SOME NOTES ON THE TOPOGRAPHY OF EASTERN PONTOS EUXEINOS IN LATE ANTIQUITY AND EARLY BYZANTIUM2 This paper clarifies some issues of late antique and early Byzantine topography of Eastern Pontos Euxeinos. These questions can be divided into two large groups: the ecclesiastical topography and the locations of Byzantine fortresses. The earliest testimony of Apostolic preaching on the Eastern black sea coast—the list of the apostles by Pseudo- Epiphanius—following the ‘Chronicon’ of Hyppolitus of Rome, unsuccessfully connects South- Eastern Pontos Euxeinos to Sebastopolis the Great (modern Sukhumi), which subsequently gives rise to an itinerary of the apostle Andrew. The Early Byzantine Church in the region had a complicated arrangement: the Zekchians, Abasgians and possibly Apsilians had their own bishoprics (later archbishoprics); the Lazicans had a metropolitan in Phasis (and not in their capital Archaeopolis) with five bishop-suffragans. Byzantine fortresses, mentioned in 7th c sources, are located mostly in Apsilia and Missimiania, in the Kodori valley, which had strategic importance as a route from -
Chiatura Reference Plan, 2016
Community managed urban strategies in historical cities Chiatura reference plan, 2016 CHIATURA REFERENCE PLAN COMMUNITY LED URBAN STRATEGIES IN HISTORIC TOWNS (COMUS) Chiatura, 2016 0 Community managed urban strategies in historical cities Chiatura reference plan, 2016 1 Community managed urban strategies in historical cities Chiatura reference plan, 2016 Abstract For the purposes of social and economic development of Chiatura Municipality, in terms of limited resources, it is the most important to identify priorities correctly and ensure efficient use of funds. The reference plan aims to support the Administration of Chiatura Municipality to identify strategic goals, tasks and actions for medium and long-term development on the basis of local engagement, which will be the basis of the further levels for monitoring their implementation and performance. According to the guidelines developed by the Council of Europe, the reference plan reflects the objective possibilities for Chiatura development, identified through participation of the stakeholders and serves to improvement of the living environment and social and economic conditions for local residents through rehabilitation of cultural heritage. 2 Community managed urban strategies in historical cities Chiatura reference plan, 2016 Analysis 3 Community managed urban strategies in historical cities Chiatura reference plan, 2016 1. Basic information Administrative Centre of Chiatura Municipality, - the city of Chiatura, - is situated in the west Georgia, in the narrow valley of the Qvirila River and Chiatura plateau at 350-500 metres above the sea level. Chiatura has been mentioned in historical sources since 1879, andacquired the status of a town in 1917. As of the year of 2016, population of the town equals to 12 800 persons. -
From India to the Black Sea: an Overlooked Trade Route?
From India to the Black Sea : an overlooked trade route? Pierre Schneider To cite this version: Pierre Schneider. From India to the Black Sea : an overlooked trade route?. 2017. hal-01376630v2 HAL Id: hal-01376630 https://hal.archives-ouvertes.fr/hal-01376630v2 Preprint submitted on 16 Mar 2017 HAL is a multi-disciplinary open access L’archive ouverte pluridisciplinaire HAL, est archive for the deposit and dissemination of sci- destinée au dépôt et à la diffusion de documents entific research documents, whether they are pub- scientifiques de niveau recherche, publiés ou non, lished or not. The documents may come from émanant des établissements d’enseignement et de teaching and research institutions in France or recherche français ou étrangers, des laboratoires abroad, or from public or private research centers. publics ou privés. From India to the Black Sea : an overlooked trade route? (Slightly revised version with addenda) Abstract. Some Hellenistic sources and Pliny the Elder briefly describe a trade route linking the Pontic area and India. Eastern commodities were carried by various middlemen using both land and river routes. The Caspian Sea was even crossed. This existence of this itinerary, which is documented by too few texts and very little archaeological remains, has been called into question by some scholars. On the basis of several literary sources so far overlooked if not missed, I argue that the "northern road" played a continuous role in the so-called Indo-Mediterranean trade, along with the better known Indian Ocean routes. Was the Black Sea the ending point of a trade route from Central Asia? P. -
East–West Highway (Shorapani–Argveta Section) Improvement Project
Report and Recommendation of the President to the Board of Directors Project Number: 53178-001 October 2019 Proposed Loan Georgia: East–West Highway (Shorapani–Argveta Section) Improvement Project Distribution of this document is restricted until it has been approved by the Board of Directors. Following such approval, ADB will disclose the document to the public in accordance with ADB’s Access to Information Policy. CURRENCY EQUIVALENTS (as of 3 October 2019) Currency unit – lari (GEL) GEL1.00 = $0.3366 $1.00 = GEL2.9710 $1.00 = €0.9175 ABBREVIATIONS ADB – Asian Development Bank CAREC – Central Asia Regional Economic Cooperation EIB – European Investment Bank EIRR – economic internal rate of return ETCIC – Eurasian Transport Corridor Investment Center EWH – East–West Highway FMA – financial management assessment JICA – Japan International Cooperation Agency km – kilometer km/h – kilometers per hour LARP – land acquisition and resettlement plan m – meter MRDI – Ministry of Regional Development and Infrastructure PAM – project administration manual PBM – performance-based maintenance NOTE In this report, “$” refers to United States dollars. Vice-President Shixin Chen, Operations 1 Director General Werner Liepach, Central and West Asia Department (CWRD) Director Dong-Soo Pyo, Transport and Communications Division, CWRD Team leader Valerie Lisack, Senior Transport Specialist, CWRD Team members Michael Beauchamp, Senior Social Development Specialist (Safeguards), CWRD Gladys Puzon Franco, Social Development Officer (Gender), CWRD Didier Guynet, -
Ordinance of the Government of Georgia No 209 of 1 April 2020 – Website, 1.4.2020
Government of Georgia Ordinance No 181 23 March 2020 Tbilisi On the Approval of Measures to be Implemented in connection with the Prevention of the Spread of the Novel Coronavirus (COVID-19) in Georgia Article 1 On the basis of Decree No 1 of 21 March 2020 of the President of Georgia on ‘Measures to be Implemented in connection with the Declaration of a State of Emergency throughout the Whole Territory of Georgia’, the attached ‘Measures to be Implemented in connection with the Prevention of the Spread of the Novel Coronavirus (COVID-19) in Georgia’ shall be approved. Article 11 The list of business entities carrying out economic activities, whose operation shall not be restricted during the period of the state of emergency, shall be approved as provided for in Annex No 1. Ordinance of the Government of Georgia No 209 of 1 April 2020 – website, 1.4.2020 Article 12 The annexed list of economic activities which, on respective conditions, shall not be restricted during the period of the state of emergency, shall be approved in accordance with Annex No 2. Ordinance of the Government of Georgia No 211 of 1 April 2020 – website, 2.4.2020 Article 13 The economic activities and facilities/business entities carrying out economic activities, which shall not be restricted during the period of the state of emergency and which are not listed in Annexes No 1 and No 2 approved by this Ordinance, shall be approved in accordance with Annex No 3. Ordinance of the Government of Georgia No 211 of 1 April 2020 – website, 2.4.2020 Article 14 In accordance with Annex No 4, the list of entities carrying out economic activities, whose operation shall not be restricted during the period of the state of emergency only for the purpose of implementing the projects defined by the same annex, shall be approved. -
53178-001: East–West Highway (Shorapani–Argveta Section
Environmental Impact Assessment Project Number: 53178-001 May 2019 GEO: East–West Highway (Shorapani–Argveta Section) Improvement Project Part 2 (Sections A–B) Prepared by the Roads Department of the Ministry of Regional Development and Infrastructure of Georgia for the Asian Development Bank. This environmental impact assessment is a document of the borrower. The views expressed herein do not necessarily represent those of ADB's Board of Directors, Management, or staff, and may be preliminary in nature. Your attention is directed to the “terms of use” section on ADB’s website. In preparing any country program or strategy, financing any project, or by making any designation of or reference to a particular territory or geographic area in this document, the Asian Development Bank does not intend to make any judgments as to the legal or other status of any territory or area. Section F4 of the Khevi-Ubisa-Shorapani-Argveta Road (E60 Highway) Environmental Impact Assessment Section F: Description of the Environment – This section of the report discusses the regional and local environmental baseline conditions. This section is divided into subsections relating to: (i) Physical: geology; topography; soils; climate; air quality; noise; surface water; groundwater; seismicity and natural hazards. (ii) Biological: flora and fauna; rare and/or endangered species (Red List species); critical habitats and ecosystems; protected areas. Particular attention shall be given to the presence of land plots registered as the State Forest Fund. (iii) Human: population; communities; demographics; employment and socio- economics; land use; infrastructure (including local access roads); transport; public health; cultural heritage; archaeology; waste management; tourism. -
Guidebook on Legal Immigration Guidebook on Legal Immigration 2015 Author: Secretariat of the State Commission on Migration Issues Address: 67A, A
GUIDEBOOK ON LEGAL IMMIGRATION GUIDEBOOK ON LEGAL IMMIGRATION 2015 Author: Secretariat of the State Commission on Migration Issues Address: 67a, A. Tsereteli ave., Tbilisi 0154 Georgia Tel: +995 322 401 010 Email: [email protected] Website: www.migration.commission.ge STATE COMMISSION ON MIGRATION ISSUES Ministry of Internally Displaced Ministry of Justice Ministryinistry of InternalInternal AffairsAffairs Ministry of Foreign Affairs Persons from the Occupied Territories, Accommodation and Refugees Office of the State Minister for Ministry of Labour, Health and Office of the State Minister for Ministry of Economy and Diaspora Issues Social Affairs European and Euro-Atlantic Sustainable Development Integration Ministry of Finance Ministry of Education and Science National Statistics Office Ministry of Regional Development and Infrastructure The Guidebook has been developed by the Secretariat of the State Commission on Migration Issues. Translated and published within the framework of the EU-funded project “enhancing Georgia’s migration management” (eniGmma) 2 TABLE OF CONTENTS About the Guidebook .......................................................................................................................4 Getting settled in Georgia ................................................................................................................5 Categories and types of Georgian visa ......................................................................................... 11 Who can travel visa-free to Georgia ...........................................................................................