Utilizing Finite Element Analysis (FEA) for Flexible Heater Designs
Total Page:16
File Type:pdf, Size:1020Kb
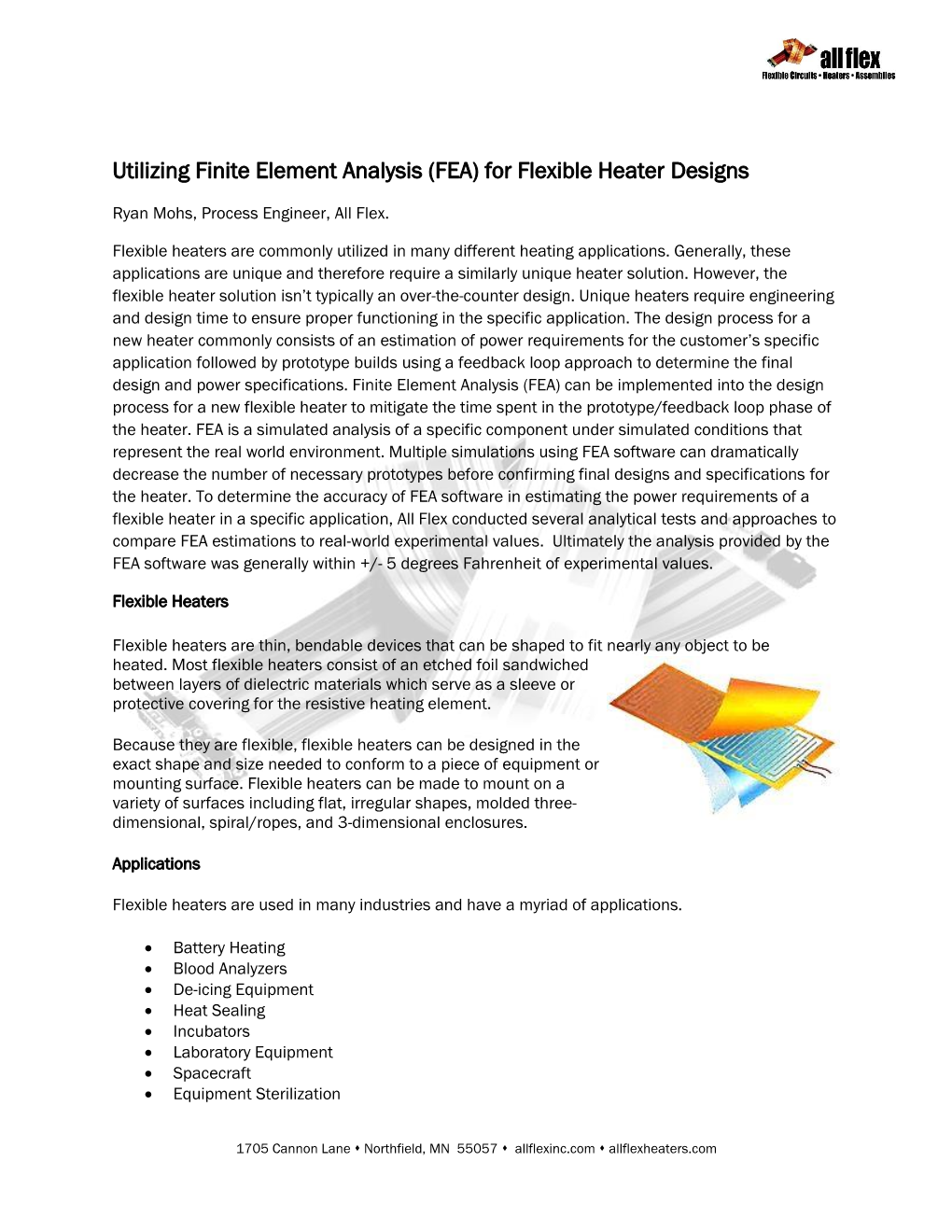
Load more
Recommended publications
-
Tubular Heaters Heat up the Foodservice Industry
FOODSERVICE TUBULAR HEATERS Tubular Heaters Heat Up the Foodservice Industry When there’s a need for heat in your foodservice equipment Applications application—from fryers to griddles to ovens—turn to Watlow, the leader with more than 25 years experience providing • Griddles heating solutions to the foodservice equipment market. Using • Rotisserie ovens • Convection ovens Watlow’s WATROD round tubular and FIREBAR® flat tubular heating elements in the cooking process promotes faster • Combi ovens cooking, consistent food preparation, ease of operation and • Conveyor ovens low maintenance. • Fryers • Steamers These reliable, versatile heating elements can be configured • Smokers with a variety of wattage and voltage ratings, terminations, • Warewashers sheath materials and mounting options to satisfy the most • Warming cabinets demanding foodservice applications. • Toasters • Other clamp-on applications Advantages • Watlow’s heaters for the foodservice industry are constructed with epoxy or silicone seals to combat moisture contamination from environmental kitchen conditions. • Compacted MgO insulation transfers heat away from resistance wire to sheath material and media more efficiently resulting in faster heat up. • Over 36 standard and a virtually limitless array of custom bend formation options enable the heating element to be HAN-FTH-0807 designed around available space to maximize heating efficiency. To be automatically connected to the nearest North American Technical and Sales Office: 1-800-WATLOW2 • www.watlow.com • [email protected] -
Commercial Electric Water Heaters
Service Handbook COMMERCIAL ELECTRIC WATER HEATERS MODELS CSB52**I, CSB82**I, CSB120**I & CSB52**S, CSB82**S, CSB120**S INSTALLATION CONSIDERATIONS - PRE SERVICE CHECKS - WATER HEATER CONSTRUCTION - 500 Tennessee Waltz Parkway OPERATION & SERVICE - TROUBLESHOOTING Ashland City, TN 37015 SERVICING SHOULD ONLY BE PERFORMED BY A QUALIFIED SERVICE AGENT. PRINTED IN THE U.S.A 1008 315015-000 1 COMMERCIAL ELECTRIC WATER HEATER SERVICE MANUAL TABLE OF CONTENTS INTRODUCTION .......................................................................2 ELECTRONIC CONTROLS..................................................... 41 Qualifications ......................................................................2 CCB - Central Control Board............................................ 42 Service Warning .................................................................2 CCB Socket & Wiring Terminal Identification ............ 43 Tools Required....................................................................3 CCB Enable Disable Circuit(s) Test........................... 45 INSTALLATION CONSIDERATIONS ........................................4 Checking Power And Ground To The CCB ............... 46 Closed Water Systems .......................................................4 UIM - User Interface Module ............................................ 47 Thermal Expansion.............................................................4 ELECTRONIC CONTROL SYSTEM ....................................... 48 Electrical Requirements......................................................5 -
Misc Thesisdb Bythesissuperv
Honors Theses 2006 to August 2020 These records are for reference only and should not be used for an official record or count by major or thesis advisor. Contact the Honors office for official records. Honors Year of Student Student's Honors Major Thesis Title (with link to Digital Commons where available) Thesis Supervisor Thesis Supervisor's Department Graduation Accounting for Intangible Assets: Analysis of Policy Changes and Current Matthew Cesca 2010 Accounting Biggs,Stanley Accounting Reporting Breaking the Barrier- An Examination into the Current State of Professional Rebecca Curtis 2014 Accounting Biggs,Stanley Accounting Skepticism Implementation of IFRS Worldwide: Lessons Learned and Strategies for Helen Gunn 2011 Accounting Biggs,Stanley Accounting Success Jonathan Lukianuk 2012 Accounting The Impact of Disallowing the LIFO Inventory Method Biggs,Stanley Accounting Charles Price 2019 Accounting The Impact of Blockchain Technology on the Audit Process Brown,Stephen Accounting Rebecca Harms 2013 Accounting An Examination of Rollforward Differences in Tax Reserves Dunbar,Amy Accounting An Examination of Microsoft and Hewlett Packard Tax Avoidance Strategies Anne Jensen 2013 Accounting Dunbar,Amy Accounting and Related Financial Statement Disclosures Measuring Tax Aggressiveness after FIN 48: The Effect of Multinational Status, Audrey Manning 2012 Accounting Dunbar,Amy Accounting Multinational Size, and Disclosures Chelsey Nalaboff 2015 Accounting Tax Inversions: Comparing Corporate Characteristics of Inverted Firms Dunbar,Amy Accounting Jeffrey Peterson 2018 Accounting The Tax Implications of Owning a Professional Sports Franchise Dunbar,Amy Accounting Brittany Rogan 2015 Accounting A Creative Fix: The Persistent Inversion Problem Dunbar,Amy Accounting Foreign Account Tax Compliance Act: The Most Revolutionary Piece of Tax Szwakob Alexander 2015D Accounting Dunbar,Amy Accounting Legislation Since the Introduction of the Income Tax Prasant Venimadhavan 2011 Accounting A Proposal Against Book-Tax Conformity in the U.S. -
Putting It All Together: Infrared Heat and Ceramicx ENGINEERING COMPETENCIES PRODUCT GUIDE TYPES of HEATERS NEW BUILDING CERAMICX INFRARED for INDUSTRY
HeatWorksHeatWorks 20 │ www.ceramicx.com Putting it all together: Infrared Heat and Ceramicx ENGINEERING COMPETENCIES PRODUCT GUIDE TYPES OF HEATERS NEW BUILDING CERAMICX INFRARED FOR INDUSTRY Welcome A fresh look at a new science A new factory certainly gives inspiration to take a fresh look at all manner of things. Such is the case here at Ceramicx and especially with regard to this the 20th issue of our in-house magazine – HeatWorks. We have chosen to celebrate our newly constructed facilities with a companion issue of the magazine – one that reminds, re-iterates and underscores the fundamentals of the science of Infrared heating. It is my hope that the reader retains this magazine issue as a regular primer and refresher on these IR heating matters. Four sections cover the ground; Principal types of IR heaters Primary Industrial Applications for IR heating Energy and radiation fundamentals Control and measurement of IR energy and heating. Make no mistake, Ceramicx is at the forefront of the scientific advancement of Infrared heating: Our commercial successes on five continents simply attest to the superior technical and scientific nature of our manufacturing and our resulting products and heaters. Empirical scientific research backs everything we do. And - as this magazine issue clearly shows - such IR science is not approximate. No ‘black art’ skills are required here. Instead, the clean, green and cost-effective energy solution for the C21 is becoming better understood and applied with every passing year. The new Ceramicx factory and enterprise remains at the cutting edge of that advancement. Frank Wilson Managing Director, Ceramicx Ltd. -
Technical Information Radiant Infrared Heating - Theory & Principles
Technical Technical Information Radiant Infrared Heating - Theory & Principles Infrared Theory Emissivity and an Ideal Infrared Source — Reflectivity — Materials with poor emissivity The ability of a surface to emit radiation is frequently make good reflectors. Polished gold Infrared energy is radiant energy which passes defined by the term emissivity. The same term with an emissivity of 0.018 is an excellent through space in the form of electromagnetic is used to define the ability of a surface to infrared reflector that does not oxidize easily. waves (Figure 1). Like light, it can be reflected absorb radiation. An ideal infrared source Polished aluminum with an emissivity of 0.04 and focused. Infrared energy does not depend would radiate or absorb 100% of all radiant is an excellent second choice. However, once on air for transmission and is converted to energy. This ideal is referred to as a “perfect” the surface of any metal starts to oxidize or heat upon absorption by the work piece. In black body with an emissivity of unity or 1.0. collect dirt, its emissivity increases and its fact, air and gases absorb very little infrared. The spectral distribution of an ideal infrared effectiveness as an infrared reflector decreases. As a result, infrared energy provides for emitter is below. efficient heat transfer without contact between Table 1 — Approximate Emissivities the heat source and the work piece. Spectral Distribution of a Blackbody Metals Polished Rough Oxidized Figure 1 at Various Temperatures Aluminum 0.04 0.055 0.11-0.19 !Peak Wavelength Brass 0.03 0.06-0.2 0.60 Copper 0.018-0.02 — 0.57 1400°F Gold 0.018-0.035 — — Wien Displacement Curve Steel 0.12-0.40 0.75 0.80-0.95 Stainless 0.11 0.57 0.80-0.95 ! Lead 0.057-0.075 0.28 0.63 1200°F Nickel 0.45-0.087 — 0.37-0.48 Silver 0.02-0.035 — — Tin 0.04-0.065 — — Infrared heating is frequently missapplied and Zinc 0.045-0.053 — 0.11 capacity requirements underestimated due to Radiant Energy 1000°F Galv. -
Historical Introduction Summarized History of Air Heating and Sheathed Heating Elements
Jacques Jumeau English version History of technologies linked to heating. Chapter 5 Historical introduction Summarized history of air heating and sheathed heating elements Copyright: Jacques Jumeau 1st edition 2015/11/26 Copy is allowed, provided you cite the origin: Ultimheat Museum 1 Update 2019/02/20 Historical introduction Summarized history of air heating and sheathed heating elements The invention of sheathed heating elements comprising a metal tube swaged around a coiled heating wire, and which is insulated by compressed magnesia, was an essential step of the electrothermics development. Thanks to their mechanical strength, impermeability and resistance to corrosion, these are the most professional heating technical solutions. The appearance of these heating elements, now universally used, was the result of a combination of different advanced techniques of the early 20th Century. Over the last two decades of the 19th Century, the emergence of electric heating had revealed the need to find reliable solutions for converting electricity into heat. The first electrical heaters were platinum wires (inherited laboratory equipment), nickel silver or even iron. Research carried on resistive elements with greater resistivity and good temperature resistance. On October 12, 1878, St. George Lane Fox-Pitt filed patent in England 4043, in which he developed the use of electricity for lighting and heating. This patent, based on the use of platinum filaments, was not followed for heating but it was the basis for the development of electric bulbs. In 1884, French Henri Marbeau, a pioneer in the manufacture of Nickel in New Caledonia and France, founded the company "Le Ferro-Nickel'' in Lizy sur Ourcq". -
On the Electrical Behaviour of Metal Mesh Heating Elements for Resistance Welding of Thermoplastic Composites
This is an Accepted Manuscript of an article published by SAGE in The Journal of Thermoplastic Composite Materials on 2015, available online: DOI: 10.1177/0892705712475012 CHARACTERISATION OF A METAL MESH HEATING ELEMENT FOR CLOSED-LOOP RESISTANCE WELDING OF THERMOPLASTIC COMPOSITES Irene Fernandez Villegasa, Harald E.N. Berseea aStructural Integrity and Composites, Faculty of Aerospace Engineering Delft University of Technology, Kluyverweg 1, 2629 HS Delft, The Netherlands Corresponding author: Irene Fernandez-Villegas, T:+31152789745, F: +31152781151, [email protected] ABSTRACT Resistance welding is one of the most suitable and mature welding techniques for thermoplastic composites. It uses the heat generated at the welding interface when electric current flows through in a resistive element, frequently a metal mesh. Closed- loop resistance welding relies on indirect temperature feedback from the weld line for process control. Its implementation is more complex than the most common open-loop welding, but on the contrary it does not in principle require the definition of processing windows for each welding configuration and it allows for constant-temperature welding. The temperature at the welding interface can be indirectly monitored through the resistance of the heating element. The relationship between resistance and temperature, expected to be approximately linear for a metal mesh heating element, can then be used to translate the welding temperature into a target resistance value for the process control routine. Despite the apparent straightforwardness of this procedure, the research results presented in this paper prove that different types of characterization tests yield different 1 This is an Accepted Manuscript of an article published by SAGE in The Journal of Thermoplastic Composite Materials on 2015, available online: DOI: 10.1177/0892705712475012 resistance versus temperature relations for a metal mesh heating element, which can lead to significant temperature deviations when used in closed-loop processes. -
How to Determine If an Electric Heater Is Good Or Bad Using an Ohmmeter By: Admin - November 06, 2020
How to Determine if an Electric Heater is Good or Bad Using an Ohmmeter By: Admin - November 06, 2020 (abcimg://ohm%20meter) Your Watlow® electric heater (/en/products/heaters) is designed to hold up to years of use in some harsh industrial conditions. Over time, the electric insulation may deteriorate and you may experience performance issues. Both heaters and power and temperature controllers are subject to performance issues, so it is important to inspect both for signs of wear and breakdown. Here we will cover all you need to know about ohms, ohmmeters and signs that your electric heater needs to be repaired or replaced with a new Watlow unit. Understanding ohms Before you check your heating products to see whether they are working effectively, it is important to understand ohms, watts, volts and amps. These electrical units allow you to compare the output of various heaters and identify signs of an inefficient or failing heater. According to Ohm’s Law the current is equal to the voltage divided by the resistance. This can also be expressed in the following equation: I = V/R (where I = current, V = voltage and R = resistance) The current of a thermocouple (/en/products/sensors/thermocouples)or other electrical device is measured in amps, the voltage is measured in volts and the resistance is measured in ohms. A high level of resistance is necessary to transform electrical energy into heat energy. The thickness, material and other factors of the conductor affect its efficiency and available temperature range. Resistors are made of materials that have a high level of electrical resistance. -
Ceramic Fiber Heaters
SPECIFICATION SHEET Ceramic Fiber Heaters Heated Insulation Package Ceramic fiber heaters offer some of the highest temperature heating element capabilities in the Watlow® family of heaters. Heating units constructed with ceramic fiber insulation isolate the heating chamber from the outside. Ceramic fiber heaters High are extremely low mass, high insulation value units with Temperature ICA Heating self-supported heating elements. Many applications benefit Element from the convenience of the heating element and insulation Lightweight combined into one package. Lightweight, low-density Alumina- properties make Watlow’s ceramic fiber heaters ideal for Silica Fiber high-temperature applications requiring low thermal mass. Composition Features and Benefits Ductile Alloy Strip High temperature ICA resistance elements Additional Leads • Bounds integrally into required position Coating for Added Strength • Allows five element configurations and Surface Thin, Tough, High Temperature Ceramic Hardness Coating over Embedded Elements, plus Lightweight, low-density alumina-silica composition Optional High Emissivity Coating molded into shape • Acts as an insulation to isolate the heating chamber from Performance Capabilities the outside • Operates at temperatures up to 2200°F (1204°C) • Provides low shrinkage fiber and inorganic binder • Allows watt densities from 5 to 30 W/in2 (0.8 to 4.6 W/cm2) • Ensures a firm, thermal shock resistant, self-supporting unit at all operating temperatures • Uses “radiant” heat transfer exclusively Operating temperatures -
The Resistance Heating Element Is the Mainstay of Electric Heaters, Furnaces, and Electric Clothes Dryers
MARK GOODSON, PE TONY PERRYMAN, EIT KELLY COLWELL The resistance heating element is the mainstay of electric heaters, furnaces, and electric clothes dryers. Resistance elements are found on electric furnaces and on heat pump systems that use resistance heat for backup or emergency purposes. The typical resistance heating ele- ment for a heater or furnace consists of a length of coiled resistance wire configured in a 5000 watt configuration. Photo 1 shows such a resistance coil for a furnace. On a dryer, typical wattages for resistance elements are between 5000 and 6000 watts. The resistance heating element is akin to a light bulb filament, in that electric current is applied and heat is generated. Just as light bulb filaments fail over time, so will the resistance element. Eventually, the heating element will fail with a parting arc; the splattered molten metal, often nichrome, is capable of igniting combustibles that it may land on. We have seen numerous fires caused by the ignition of plastic Photo 1 ductwork, dust accumulations, and air filters. Obviously, filter loca- tion and ductwork construction vary with each installation, such that not every failed resistance element will cause a fire. We examined eight 5000 watt heater elements, installed in 3 sepa- rate furnaces in the same building. The wattages for the eight elements, A second mode of fire causation occurs when the element fails, which were installed new in 1989, are as follows: and then ‘welds’ itself onto surrounding metal. While probably of little concern from a fire standpoint on a 120 VAC appliance, on a 240 VAC 5042, 5114, 5162, 5270, 5148, 5075, 5070, 5221. -
PTC Thermistor (POSISTOR®)
!Note • This PDF catalog is downloaded from the website of Murata Manufacturing co., ltd. Therefore, it’s specifications are subject to change or our products in it may be discontinued without advance notice. Please check with our sales representatives or product engineers before ordering. R16E.pdf • This PDF catalog has only typical specifications because there is no space for detailed specifications. Therefore, please approve our product specifications or transact the approval sheet for product specifications before ordering. 08.9.25 PTC Thermistor (POSISTOR®) Application Manual Murata Manufacturing Co., Ltd. Cat.No.R16E-4 !Note • This PDF catalog is downloaded from the website of Murata Manufacturing co., ltd. Therefore, it’s specifications are subject to change or our products in it may be discontinued without advance notice. Please check with our sales representatives or product engineers before ordering. R16E.pdf • This PDF catalog has only typical specifications because there is no space for detailed specifications. Therefore, please approve our product specifications or transact the approval sheet for product specifications before ordering. 08.9.25 for EU RoHS Compliant • All the products on this catalog are complied with EU RoHS. • EU RoHS is "the European Directive 2002/95/EC on the Restriction of the Use of Certain Hazardous Substances in Electrical and Electronic Equipment". • For more details, please refer to our website 'Murata's Approach for EU RoHS' (http://www.murata.com/info/rohs.html). !Note • This PDF catalog is downloaded from the website of Murata Manufacturing co., ltd. Therefore, it’s specifications are subject to change or our products in it may be discontinued without advance notice. -
High-Temperature Heaters
High-Temperature Heaters Max. Operating Typical Max. Temperatures Watt Densities High-Temperature Heaters Sheath Materials °F °C W/in2 W/cm2 Page MULTICELL™ Alloy 800 2050 1120 30 4.6 411 High-Temperature FIREROD® Platen 1800 982 100 15.5 417 High-Temperature Tubular Alloy 800 1800 983 30 4.6 418 Ceramic Fiber Ceramic fiber 2200 1204 30 4.6 419 High-Temperature Heaters 409 410 High-Temperature Heaters EXTENDED Extended Capabilities for CAPABILITY MULTICELL™ Heaters The advanced design of the MULTICELL™ insertion heater from Watlow® offers three major advantages: extreme process temperature capability, independent zone control for precise temperature uniformity and loose fit design for easy insertion and removal. Performance Capabilities • Engineered to achieve sheath temperatures up to 2050°F (1120°C) • Up to six independently controllable zones Multiple 3 6 Zoned Platens 2 5 1 4 No-heat Toe End No-heat Section Designed for Longer Element Life Potting Cup to Seal Electrical Termination High-Temperature Flexible Leads Wide Range of Terminations Available Independently Controllable Heated Zones Features and Benefits Resistance High Grade MgO Zone 1 Multiple, independently controllable zones Wire Insulation • Allows process temperature uniformity not possible with any other single-sheathed heater Radiant design of heater • Allows for loose insertion in boiling holes and piping holes Cross Section Zone 3 High Temperature Zone 2 • Permits easy removal and replacement with minimal Alloy for Outer Sheath down time since it will not bind or seize