MCU-710M SMKC-710 Operation Manual
Total Page:16
File Type:pdf, Size:1020Kb
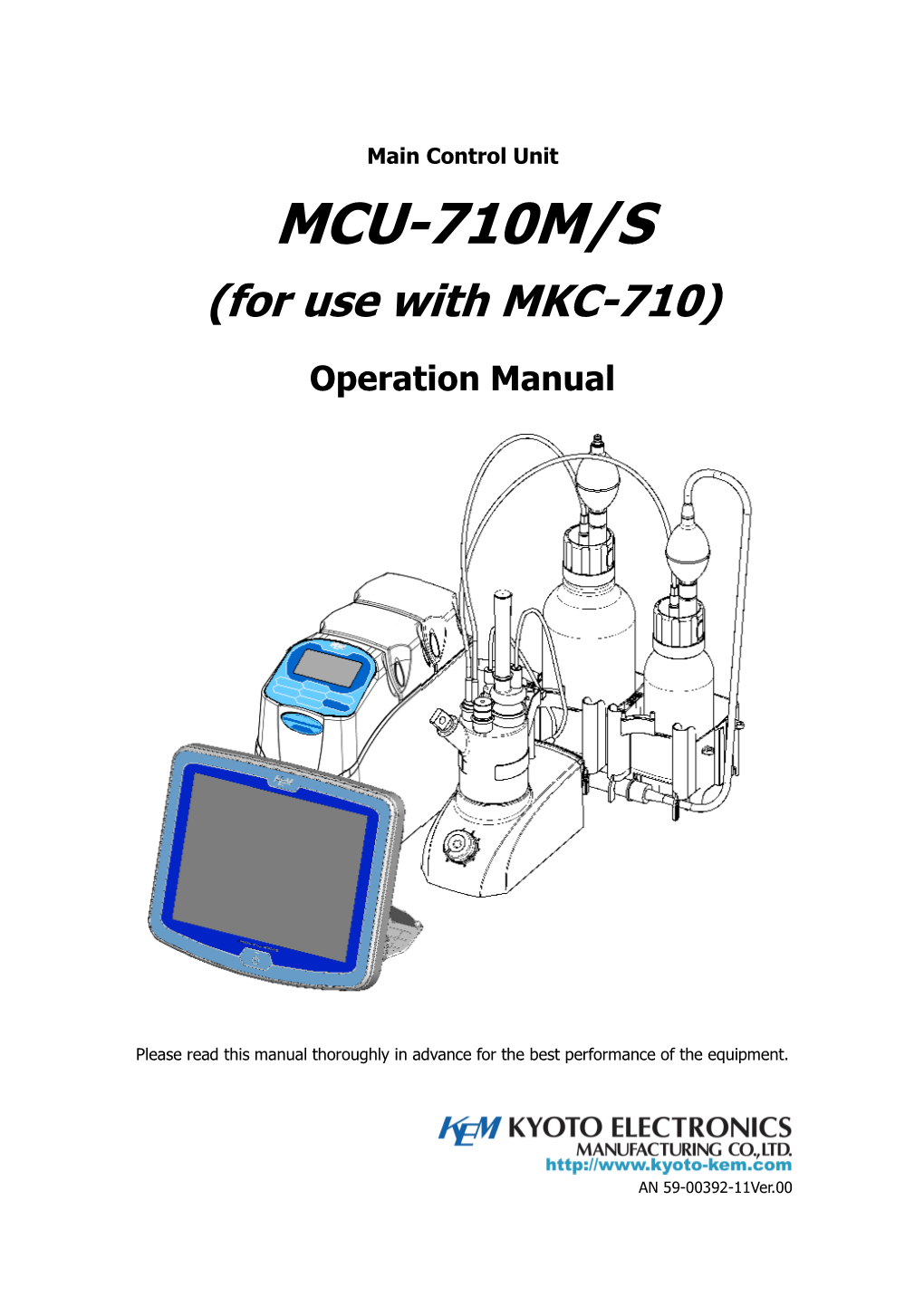
Load more
Recommended publications
-
Pinzgauer 716 Mk
PINZGAUER 716 MK Manufacturer: BAE Mobility & Protection Systems Product type: Auxiliary Vehicles Name: Patrol Vehicle Pinzgauer is a high mobility all-terrain 4x4 and 6x6 military utility vehicle manufactured in Guildford, Surrey, United Kingdom, by BAE Systems Land Systems. The Pinzgauer has been manufactured in the United Kingdom since the year 2000, originally by Automotive Technik Ltd (ATL). Before then the Pinzgauer was produced by Steyr- Daimler-Puch in Graz, Austria (hence the name, based on an Austrian breed of horse). ATL has since then been acquired by Stewart & Stevenson Services, Inc. in 2005, which in turn became a subsidiary of the aerospace and defence group Armor Holdings, Inc in May 2006. One year later Armor Holdings was itself acquired by BAE Systems. The original prototype was produced in 1965 and production began in 1971, as successor of the Haflinger. This first generation model was produced until 1985 by Steyr-Daimler-Puch. The Pinzgauer is one of the most capable all-terrain vehicles ever made. While it is not as fast as the HMMWV, it can carry more troops. Even the smaller 710M can carry 10 people, or two NATO pallets. Both the 4x4 and 6x6 models can tow 5,000 kg on road, and 1,500 or 1,800 kg, respectively off-road. It has a range of over 400 km on one tank of fuel or nearly 700 km with the optional 125-litre tank. The first generation Pinzgauer is available in both four-wheel drive (model 710) and six-wheel drive (model 712) versions. The Pinzgauer was also designed to be reliable and easy to fix, so it is shipped with an air-cooled dual-carbureted engine. -
Non-Muslim Integration Into the Early Islamic Caliphate Through the Use of Surrender Agreements
University of Arkansas, Fayetteville ScholarWorks@UARK History Undergraduate Honors Theses History 5-2020 Non-Muslim Integration Into the Early Islamic Caliphate Through the Use of Surrender Agreements Rachel Hutchings Follow this and additional works at: https://scholarworks.uark.edu/histuht Part of the History of Religion Commons, Islamic World and Near East History Commons, and the Medieval History Commons Citation Hutchings, R. (2020). Non-Muslim Integration Into the Early Islamic Caliphate Through the Use of Surrender Agreements. History Undergraduate Honors Theses Retrieved from https://scholarworks.uark.edu/histuht/6 This Thesis is brought to you for free and open access by the History at ScholarWorks@UARK. It has been accepted for inclusion in History Undergraduate Honors Theses by an authorized administrator of ScholarWorks@UARK. For more information, please contact [email protected]. Non-Muslim Integration Into the Early Islamic Caliphate Through the Use of Surrender Agreements An Honors Thesis submitted in partial fulfillment of the requirements of Honors Studies in History By Rachel Hutchings Spring 2020 History J. William Fulbright College of Arts and Sciences The University of Arkansas 1 Acknowledgments: For my family and the University of Arkansas Honors College 2 Table of Content Introduction…………………………………….………………………………...3 Historiography……………………………………….…………………………...6 Surrender Agreements…………………………………….…………….………10 The Evolution of Surrender Agreements………………………………….…….29 Conclusion……………………………………………………….….….…...…..35 Bibliography…………………………………………………………...………..40 3 Introduction Beginning with Muhammad’s forceful consolidation of Arabia in 631 CE, the Rashidun and Umayyad Caliphates completed a series of conquests that would later become a hallmark of the early Islamic empire. Following the Prophet’s death, the Rashidun Caliphate (632-661) engulfed the Levant in the north, North Africa from Egypt to Tunisia in the west, and the Iranian plateau in the east. -
PDC Catalog 2021
Professional Development Courses® ONLINE GRADUATE COURSES FOR EDUCATORS 2021 COURSE CATALOG ACCREDITED • GRADUATE LEVEL • SELF-PACED pdc.laverne.edu Enroll Now! 800.793.6533 TABLE OF CONTENTS About the University of La Verne. .1 About Our Courses .......................................3 Connect With Us .........................................3 Certificate Program .......................................3 COURSE OFFERINGS Education and Psychology .................................4 Motivation and Classroom Management ...................4 Educational Tools for Teachers ............................5 Exceptionalities and Disabilities. .9 Psychology ........................................... 11 Multi-Cultural ........................................ 15 Health and Fitness .................................... 16 School Violence and Legal Issues ........................ 17 English and Literature ................................... 18 History ................................................ 20 History - Art ........................................... 25 History - Music ......................................... 26 he University of La Verne, established in 1891, Sciences ............................................... 26 is a non-profit institution located in La Verne, T Site Visit ............................................... 29 California and is accredited by the Western Association of Schools and Colleges (http://www.wscuc.org). Technology ............................................ 30 Sports and Coaching ................................... -
ARTIK 710/710S Module Datasheet Samsung Semiconductor, Inc
ARTIK 710/710s Module Datasheet Samsung Semiconductor, Inc. ARTIK 710/710s Module Datasheet MODULE OVERVIEW The Samsung ARTIK™ 710/710s Module is a highly-integrated ARTIK 710 System-in-Module that combines an eight-core ARM® Cortex®-A53 processor packaged with DRAM and Flash memory, a Security Subsystem, and a wide range of wireless communication options—such as 802.11a/b/g/n/ac for Wi-Fi®, Bluetooth® 4.2 (BLE+Classic), and 802.15.4 for Zigbee—all into an extremely compact footprint. The many standard digital control interfaces support external sensors and higher performance peripherals to expand the module’s capabilities. With the combination of 802.11 , Bluetooth® and 802.15.4, the ARTIK 710/710s Module is the perfect choice for home automation and home hub devices, while also supporting a rich UI/UX capability for camera and display requirements. The inclusion of a hardware-based Secure Element works with the ARM® TrustZone® and Trustware’s Trusted Execution Environment (TEE) to provide end-to-end security. ARTIK 710s Processor CPU Octa-core ARM® Cortex®[email protected] GPU 3D graphics accelerator Media Camera I/F 4-lane MIPI CSI up to 5M (1920x1080@30fps) Display 4-lane MIPI DSI and HDMI1.4a (1920x1080p@60fps) or LVDS (1280×720p@60fps) Audio Two I2S audio interface Memory DRAM 1GB DDR3 @ 800MHz FLASH 4GB eMMC v4.5 Security Secure Element Secure point to point authentication and data transfer Figure 1. ARTIK™ 710/710s Modules Top View Trusted Execution Trustware Environment Radio WLAN IEEE 802.11a/b/g/n/ac, dual-band SISO Bluetooth® 4.0 (Classic+BLE) LR_WPAN IEEE 802.15.4 Power Management PMIC Provides all power of the ARTIK 710/710s Module using onboard bucks and LDOs Interfaces Ethernet 10/100/1000Base-T MAC (External PHY required) Analog and Digital I/O GPIO, UART, I2C, SPI, SDIO, USB Host, USB OTG, HSIC, ADC, PWM, I2S, JTAG 2 Samsung Semiconductor, Inc. -
Figure 21 MW-704S Cvoc Concentrations Vs. Time 120
Figure 21 MW-704S cVOC Concentrations vs. Time 120 100 80 Tetrachloroethene 60 Trichloroethene Trichloroethene/Tetrachloroethene GW-1 Concentration(ug/L) Concentration(ug/L) Vinyl Chloride 40 Vinyl Chloride GW-1 20 0 Figure 22 MW-709S cVOC Concentrations vs. Time 120 100 80 Tetrachloroethene 60 Trichloroethene Trichloroethene/Tetrachloroethene GW-1 Concentration(ug/L) Concentration(ug/L) Vinyl Chloride 40 Vinyl Chloride GW-1 20 0 Figure 23 MW-709D cVOC Concentrations vs. Time 120 100 80 Tetrachloroethene 60 Trichloroethene Trichloroethene/Tetrachloroethene GW-1 Concentration(ug/L) Concentration(ug/L) Vinyl Chloride 40 Vinyl Chloride GW-1 20 0 Figure 24 MW-710S cVOC Concentrations vs. Time 120 100 80 Tetrachloroethene 60 Trichloroethene Trichloroethene/Tetrachloroethene GW-1 Concentration (ug/L) Concentration Concentration (ug/L) Concentration Vinyl Chloride 40 Vinyl Chloride GW-1 20 0 Figure 25 MW-710M cVOC Concentrations vs. Time 120 100 80 Tetrachloroethene 60 Trichloroethene Trichloroethene/Tetrachloroethene GW-1 Concentration(ug/L) Concentration(ug/L) Vinyl Chloride 40 Vinyl Chloride GW-1 20 0 Figure 26 MW-711D cVOC Concentrations vs. Time 120 100 80 Tetrachloroethene 60 Trichloroethene Trichloroethene/Tetrachloroethene GW-1 Concentration(ug/L) Concentration(ug/L) Vinyl Chloride 40 Vinyl Chloride GW-1 20 0 Figure 27 MW-713D cVOC Concentrations vs. Time 120 100 80 Tetrachloroethene 60 Trichloroethene Trichloroethene/Tetrachloroethene GW-1 Concentration(ug/L) Concentration(ug/L) Vinyl Chloride 40 Vinyl Chloride GW-1 20 0 Figure 28 MW-714S cVOC Concentrations vs. Time 120 100 80 Tetrachloroethene 60 Trichloroethene Trichloroethene/Tetrachloroethene GW-1 Concentration(ug/L) Concentration(ug/L) Vinyl Chloride 40 Vinyl Chloride GW-1 20 0 Figure 29 PCE - MW-711 to MW-704 Concentration vs. -
Approaches to Community and Otherness in the Late Merovingian and Early Carolingian Periods
View metadata, citation and similar papers at core.ac.uk brought to you by CORE provided by White Rose E-theses Online Approaches to Community and Otherness in the Late Merovingian and Early Carolingian Periods Richard Christopher Broome Submitted in accordance with the requirements for the degree of Doctor of Philosophy The University of Leeds School of History September 2014 ii The candidate confirms that the work submitted is his own and that appropriate credit has been given where reference has been made to the work of others. This copy has been supplied on the understanding that it is copyright material and that no quotation from the thesis may be published without proper acknowledgement. The right of Richard Christopher Broome to be identified as Author of this work has been asserted by him in accordance with the Copyright, Designs and Patents Act 1988. © 2014 The University of Leeds and Richard Christopher Broome iii Acknowledgements There are many people without whom this thesis would not have been possible. First of all, I would like to thank my supervisor, Ian Wood, who has been a constant source of invaluable knowledge, advice and guidance, and who invited me to take on the project which evolved into this thesis. The project he offered me came with a substantial bursary, for which I am grateful to HERA and the Cultural Memory and the Resources of the Past project with which I have been involved. Second, I would like to thank all those who were also involved in CMRP for their various thoughts on my research, especially Clemens Gantner for guiding me through the world of eighth-century Italy, to Helmut Reimitz for sending me a pre-print copy of his forthcoming book, and to Graeme Ward for his thoughts on Aquitanian matters. -
Directory of Commercial Testing and College Research Laboratories
DEPARTMENT OF COMMERCE BUREAU OF STANDARDS GEORGE K. BURGESS, Director DIRECTORY OF COMMERCIAL TESTING AND COLLEGE RESEARCH LABORATORIES MISCELLANEOUS PUBLICATION No. 90 BUREAU OF STANDARDS PAMPHLETS ON TESTING There are listed below a few of the official publications of the Bureau of Standards relating to certain phases of testing, including Scientific Papers (S), Technologic Papers (T), Circulars (C), and Miscellaneous Publications (M). Copies of the pamphlets can be obtained, at the prices stated, from the Superintendent of Documents, Government Printing Office, Washington, D. C. In ordering pamphlets from the Superintendent of Documents the bureau publication symbol and number must be stated, and the order must be accompanied by cash. Automobile-tire fabric testing, standardization of, Hose, garden, selection and care of C327. (In T68. Price, 10 cents. press.) Hydrogen sulphide in gas, lead acetate test for, T41. Bags, paper, for cement and lime, a study of test Price, 25 cents. methods for, T187. Price, 5 cents. Hydrometers, testing of, CI 6. Price, 5 cents. Barometers, the testing of, C46. Price, 10 cents. Inks, their composition, Beams, reinforced concrete, shear tests of, T314. manufacture, and methods of testing, C95. Price, 10 Price, 50 cents. cents. Inks, printing, the composition, properties, and test- Bricks, transverse test of, T251. Price, 10 cents. ing of, C53. Price, 10 cents. Bridge columns, large, tests of, T101. Price, 30 cents. Lamp life-testing equipment and methods, recent Cast steel, centrifugally, tests of, T192. Price, 10 developments in, T325. Price, 15 cents. cents. Lamps, incandescent, life testing of, S265. Price, Clay refractories, the testing of, with special refer- 10 cents. -
Sansoni Planters A. Silvestri
Pots, Planters & Urns www.asilvestri.com 71 A. Silvestri Co. Three Ring Pots Stone 7087 22”H 26”W - Base: 17” 7088 18.5”H 22”W Base: 14.5” 7086 24”H 30”W Base: 19” 7089 7090 15”H 18”W 12”H 14”W Base: 12” Base: 9” Stone 7086XL Three Ring Pot 7086L Three Ring Pot 30.5”H 39”W - 22.5” Base 26”H 35”W - 20” Base 72 Double Rolled Rim Pots A. B. C D. New Bronze E. A. 7190 - 26.5”H 39”W - 21” Base D. 7193 - 14”H 23”W - 12” Base B. 7191 - 22”H 32”W - 18” Base E. 7194 - 10.5”H 18”W - 10” Base C. 7192 - 18”H 28”W - 16” Base A. Italian Pots B. C. D. Stone A. 7175 B. 7176 C. 7177 D. 7178 25”H 31”W 21”H 25”W 14”H 16”W 10”H 12”W 18” Base 16” Base 10” Base 7” Base www.asilvestri.com 73 A. Silvestri Co. Urban Planters Espresso Urban 7320 7321 7322 7323 14”H 31.5”L 14”D 11”H 27.5”L 11”D 9”H 24”L 9”D 7”H 22”L 6.5”D Planters - Rectangular Espresso 7328 7329 7330 20”H 40”L 13”D 16”H 32”L 10”D 12”H 23.5”L 8”D Espresso Urban Planters - Square Espresso 7318 11.5”H 12”W 7319 9”H 9.5”W 7317 14”H 14.5”W 7317L 16”H 16”W 74 Espresso Urban Planters - Tall 7314 7315 7316 33”H 15.5”W 28”H 14”W 23”H 13”W Base: 10”sq Base: 8”sq Base: 8”sq Urban Planter - Tall Square Espresso 7324 7325 7326 7327 32”H 15”W 27.5”H 12.5”W 22”H 10.5”W 15.5”H 8.5”W www.asilvestri.com 75 A. -
Brownfield Cleanup Program Application
Brownfield Cleanup Program Application Buffalo Development Corp. Hotel Site Buffalo,New York June 2006 Preoared For: Buffalo Development Corp. Prellared Bv: ENVIRONMENTAL ENGINEERING 8 SCIENCE, PLLC (7vjj8856-05991 fax: (716) 856-058;" um NEW YORK STATE DEPARTMENT OF ENVIRONMENTAL CONSERVATION BROWNFIELD CLEANUP PROGRAM (BCP) APPLICATION ECL ARTICLE 27 / TITLE 14 -- -- -- - DEPARTMENT USE ONLY # BCP SITE - NAME Buffalo Development Corporation ADDRESS 297 Franklin Street CITY/TOWN Buffalo ZIP CODE 14202 PHONE 842-6800 FAX 847-6296 E-MAIL [email protected] NAME OF REQUESTOR'S REPRESENTATIVE Robert E. Qoer ADDRESS 68 Niagara Street C~TYmOWN Buffalo ZIP CODE 14202 PHONE (716) 855-1673 FAX (716) 855-1675 E-MAIL [email protected] NAME OF REQUESTOR'S CONSULTANT Paul Werthman ( Benchmark Environmental Engineering & Science, PLLC) ADDRESS 726 Exchange Street, Suite 624 CITYITOWN Buffalo ZIP CODE 14210 PHONE (716) 856-0599 FAX (716) 856-0583 E-MAIL NAME OF REQUESTOR'S ATTORNEY Robert E. Qoer ADDRESS 68 Niagara Street CITYmoWN Buffalo ZIP CODE 14202 PHONE 7 16-855-1673 FAX 716-855-1675 E-MAIL [email protected] THE REQUESTOR MUST CERTIFY THAT IT IS EITHER A PARTICIPANT OR VOLUNTEER IN ACCORDANCE WITH ECL 8 27-1405 (1) BY CHECKING ONE OF THE BOXES BELOW: PARTICIPANT VOLUNTEER A requestor who either 1) was the owner of the site at the time of the disposal A requestor other than a participant, including a requestor whose liability arises solely of hazardous waste or discharge of petroleum or 2) is otherwise a person as a result of ownership, operation of or involvement with the site subsequent to the responsible for the contamination, unless the liability arises solely as a result disposal of hazardous waste or discharge of petroleum. -
2016 Manufactors Cup
2016 MANUFACTORS CUP 730B (1) Ric Alvarado 216B (2) Sean Rogers 9.881, 106.007( 0.158) 9.971, 103.448( 0.668) 730B Ric Alvarado 086B Don Blayney 10.248, 102.506( 0.051) 10.065, 96.670( 0.310) BYE 086B (7) Don Blayney 10.092, 95.137( 0.000) 730B Ric Alvarado 169B Ricky Sneed 9.941, 103.211( 0.027) 10.170, 101.124( -0.086) 043B (4) Randall Docke 169B (3) Ricky Sneed 9.277, 115.237( 1.123) 10.447, 98.901( 0.151) 321B Mike Edmondson 169B Ricky Sneed 9.978, 101.580( 0.315) 10.287, 100.111( 0.038) 321B (5) Mike 1008B (6) David Mcardl 10.049, 100.559( 0.176) 9.716, 101.580( 0.784) 730B Ric Alvarado Precision Timing by www.DragTimeRacing.com Live Timing Data at www.DragBoatRacing.com Class: 10.00-10.99 - Racers in Class:7 Printed: SUNDAY 05/22/16 20:16:40 2016 MANUFACTORS CUP 1953B (1) Arek Strohme 110B (2) Joe Lakamp 5.951, 126.029( 0.314) 0.000, 0.000(0.000) 1953B Arek 302B Mike Schiller 6.077, 119.408( 0.202) 5.929, 139.717( 0.206) BYE 302B (11) Mike Schille 5.907, 140.581( -0.032) 1953B Arek 0090B Mike Davis 6.018, 121.971( 0.103) 657B (6) Brian Coin 0090B (5) Mike Davis 6.015, 126.968( 0.356) 5.886, 144.760( 0.251) 657B Brian Coin 0090B Mike Davis 6.039, 128.403( 0.318) 6.023, 132.908( 0.088) 38B (7) Tim Goodwin 724B (8) Duncan Patter 5.983, 125.797( 0.197) 6.105, 121.971( -0.122) 1953B Arek 0090B Mike Davis 6.087, 123.967( 0.091) 6.032, 140.581( 0.150) 6040B (3) Kelly Rhead 5.879, 131.372( 0.078) 6040B Kelly Rhead 6.084, 126.263( 0.237) 149B (10) Willis Johns 5.816, 133.952( 0.295) 927B Steve Penberthy BYE 6.011, 134.481( 0.252) 927B (4) -
Developments in Egypt's Early Islamic Postal System
Bulletin of SOAS, 81, 1 (2018), 25–40. © The Author(s) 2017. This is an Open Access article, distributed under the terms of the Creative Commons Attribution licence (http://creativecommons.org/licenses/by/4.0/), which permits unrestricted re-use, distribution, and reproduction in any medium, provided the original work is properly cited. doi:10.1017/S0041977X17001380 First published online 21 December 2017 Developments in Egypt’s early Islamic postal system (with an edition of P.Khalili II 5)* Jelle Bruning Leiden University [email protected] Abstract The importance of documentary sources for the history of the official pos- tal system (barīd) in the first century of Islam has long been acknowl- edged. In addition to a small number of documents from the eastern part of the Muslim Empire, Egyptian papyri from the 90s/710s and 130s/ 750s form the main documentary sources for modern studies on the postal system. These papyri belong to a distinct phase in Islamic history. Papyri from other, especially earlier, phases have largely been neglected. The pre- sent article addresses the history of Egypt’s official postal system from the Muslim conquest up to c. 132/750. It argues that the postal system grad- ually developed out of Byzantine practices and was shaped by innovations by Muslim rulers through which their involvement in the postal system’s administration gradually increased. The article ends with an edition of P.Khalili II 5, a papyrus document from 135/753 on the provisioning of postal stations. Keywords: Postal system (barīd), Early Islamic history, Egypt, Administration, Papyri It is well known that historical studies of the first two centuries of Islam depend on sources other than the literary works written in the second century AH/eighth cen- tury AD or later. -
Higher Education Facility Study, Revised 2020
HIGHER EDUCATION FACILITY STUDY Prepared for the Washington State Office of Financial Management August 2019 Revised: April 2020 Table of Contents EXECUTIVE SUMMARY 1 SECTION 1: OVERVIEW AND CONSIDERATIONS 11 SECTION 2: CLASSROOMS + INSTRUCTIONAL LABORATORIES 23 SECTION 3: RESEARCH SPACE 47 SECTION 4: OFFICE SPACE 55 SECTION 5: LIBRARY + STUDY/COLLABORATION SPACE 63 SECTION 6: OTHER NON‐RESIDENTIAL SPACE 71 SECTION 7: SUPPORT / PHYSICAL PLANT SPACE 81 SECTION 8: SCOPE + COST RANGE ANALYSIS 87 SECTION 9: RECOMMENDATIONS TO THE OFM HIGHER EDUCATION CRITERIA + SCORING STANDARDS 125 APPENDICES: APPENDIX A – ANALYTICAL OUTCOMES BY COLLEGE/CAMPUS A.1 APPENDIX B – SPACE ALLOCATION QUICKBOARD B.1 APPENDIX C – DATA REQUEST FORM C.1 APPENDIX D – REVISED HE2019‐21 SPACE ALLOCATION + AVAILABILITY D.1 APPENDIX E – COLLEGES/CAMPUSES INCLUDED + EXCLUDED FROM STUDY E.1 APPENDIX F – NORMALIZATION OF SPACE INVENTORY F.1 0 Office of Financial Management 2019 Higher Education Facility Study EXECUTIVE SUMMARY The goal of this study is to provide the Office of Financial Management, the Legislature, the State Board for Community and Technical Colleges, and the public four‐year institutions of higher education with updated methods and outcomes to prioritize the development, construction, and planning of future higher education facilities. INTRODUCTION In December 2008, Berk & Associates completed a Higher Education Capital Facilities Financing Study (Berk Report). The primary goal of the Berk Report was to provide the government with a comprehensive review of revenue source and cost management strategies used in the State of Washington and the Washington Learns Global Challenge States. The Berk Report also served to identify potential new revenue sources and cost saving strategies for higher education capital facilities.