Operational Telecom Network for the Connected Pipeline System Design
Total Page:16
File Type:pdf, Size:1020Kb
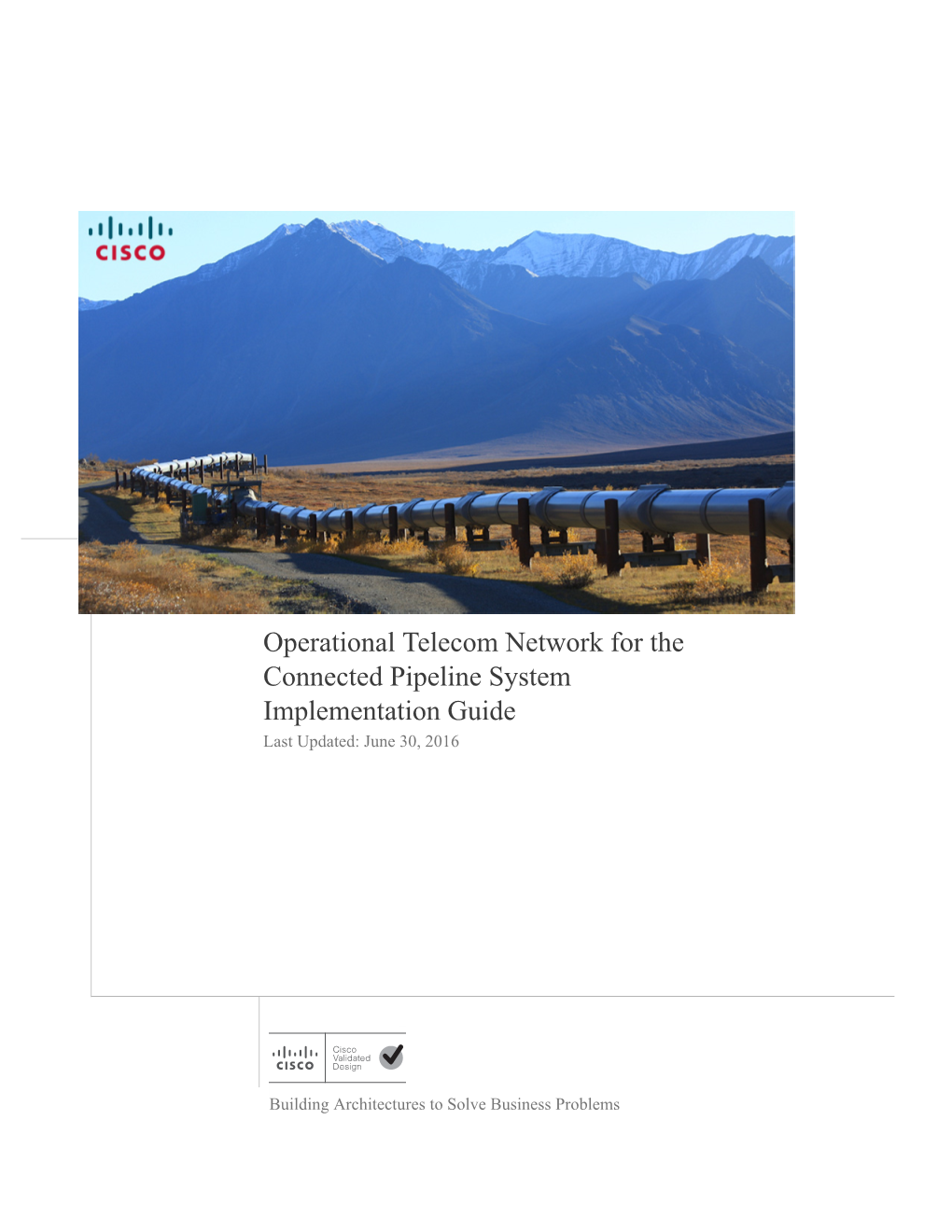
Load more
Recommended publications
-
Router Configuration Guide R15.0.R1
ROUTER CONFIGURATION GUIDE RELEASE 15.0.R1 7450 ETHERNET SERVICE SWITCH 7750 SERVICE ROUTER 7950 EXTENSIBLE ROUTING SYSTEM ROUTER CONFIGURATION GUIDE RELEASE 15.0.R1 3HE 11976 AAAA TQZZA 01 Issue: 01 March 2017 Nokia — Proprietary and confidential. Use pursuant to applicable agreements. ROUTER CONFIGURATION GUIDE RELEASE 15.0.R1 Nokia is a registered trademark of Nokia Corporation. Other products and company names mentioned herein may be trademarks or tradenames of their respective owners. The information presented is subject to change without notice. No responsibility is assumed for inaccuracies contained herein. © 2017 Nokia. Contains proprietary/trade secret information which is the property of Nokia and must not be made available to, or copied or used by anyone outside Nokia without its written authorization. Not to be used or disclosed except in accordance with applicable agreements. 2 3HE 11976 AAAA TQZZA 01 Issue: 01 ROUTER CONFIGURATION GUIDE RELEASE 15.0.R1 Table of Contents 1 Getting Started..............................................................................11 1.1 About This Guide.......................................................................................11 1.2 In This Chapter..........................................................................................12 1.3 Router Configuration Process ...................................................................12 2 IP Router Configuration ..............................................................13 2.1 In This Chapter..........................................................................................13 -
New York University— 3D Resilience
Customer Profile New York University— 3D Resilience New York University (NYU) deploys a network core based upon a radical “tetrahedron” design with seven levels of resilience. The core is built with Cisco Catalyst® 6500 Series switches, which meet all design requirements. Background currently a member of Internet 2. It has a Founded in 1831, NYU is the largest network built end-to-end with Cisco private nonprofit university in the United products and technologies, developed over States and occupies six major centers in time beginning with Cisco AGS routers in Manhattan. The university’s founding the early 1990s. The 120 networked fathers planned NYU as a center of higher buildings of NYU house approximately learning that would be open to all, 1100 network devices, an assortment of regardless of national origin, religious Cisco Catalyst switches and Cisco routers. beliefs, or social background. Current Upgrades are scheduled to accommodate enrollment exceeds 51,000 students growth, support new features, or increase attending 14 schools and colleges in 135 performance. The NYU network supports buildings at 6 locations in Manhattan and about 27,000 active network nodes running in more than 20 countries. The curriculum IP, IPX, and AppleTalk on a variety of encompasses every major discipline, and server and desktop platforms. NYU provides leadership education and The core network installed in 1995 research in medicine, dentistry, business, consisted of Cisco routers with 100-Mbps science, fine arts, law, social work, and Fiber Distributed Data Interface (FDDI) education, among others. The faculty, links. Since its installation, this network has which in 1831 consisted of 14 professors never failed, which can be attributed to the (among them artist and inventor Samuel F. -
End to End IPTV Design and Implementation, How to Avoid Pitfalls Rajiv Chaudhuri Ericsson Consulting Agenda for the IP TV Design Tutorial
End to End IPTV Design and Implementation, How to avoid Pitfalls Rajiv Chaudhuri Ericsson Consulting Agenda for the IP TV Design Tutorial 1. IP TV Business Models and Challenges 2. Key IP TV Design Considerations 3. Delivering IP TV Services and Quality of Experience 4. Testing Considerations 5. Future Directions 6. Finally – Key Messages NETWORKS20008 2 1. IP TV Business Models and Business Case Challenges What is IP TV ? It is “TV anytime” with no strict dependency on the fixed program guide Can replace cable and satellite based video and TV broadcast services It is broadband TV, video on demand and interactive TV It offers triple play service bundling – voice, video and data on FTTP and ADSL 2+ and VDSL access Viewers would expect a predictable or better service quality, when comparing IP TV with Broadcast FTA, cable and Satellite TV services NETWORKS20008 4 Slide 4 What is TV? (Broadcast, Internet TV, IPTV) air DVB-S DVB-T DVB STB Broadcast TV HFC DVB-C DVB-H / HSPA Internet TV xDSL/FTTx Internet DVB-IP IPTV STB IPTV TV xDSL/FTTx IP Server NETWORKS20008 5 IPTV Scenarios Managed vs Unmanaged Live content Ingestion 1 Telcos (QoS) Telcos (QoS) 2 ManagedManaged NetworkNetwork 3 4 Internet Content InternetInternet UnmanagedUnmanaged NetworkNetwork 1. Professional content over managed network to PC client (Broadband TV) 2. Professional content over managed network to STB (IPTV) 3. Internet originating content to STB (Internet TV = Web TV) 4. Internet orientating content to PC (Internet TV = Web TV) NETWORKS20008 6 IP TV Scenario Analysis -
Cisco Next Generation Routing
A B NGR Brochure Cisco Next Generation Routing Section 1 Issues for networking in the Broadband Era Section 2 Next Generation WAN Services using MPLS Section 3 Cisco's Next Generation IP Network Solution Section 4 Cisco’s Next Generation Optical Ring Solution Section 5 Service differentiation and Quality of Service Section 6 Service with Security Section 7 Cisco Next Generation Routers – Core and Edge Section 8 Cisco Next Generation Routers – Access W NGR Brochure 12400 series 3700 series 12416 7600 series 12410 7300 series 2600XM/2691 series 10000 series 7609 7613 12406 7304 12404 1700/1760 series 7301 7606 7400 series 7603 10700 series SOHO and 800 series Larg SoH SM e Bra o B / Enterprise nch CPE Cisco Next Generation Routing (NGR) Solution Next Generation Internet in the Broadband Era Broadband networking is rapidly expanding in usage; consequently, routers Innovative Next Generation metro IP solution must support an ever growing range of features and service capabilities to RPR (Resilient Packet Ring), represents a key technology for the meet the unique needs of this high growth area. As the world's leading router deployment of advanced IP ring technology. RPR is used by a large manufacturer, Cisco’s routers are in widespread use, helping to support and number of customers in the metro access arena, for providing an expand the development and usage of the Internet and its rich service base. It advanced, industry-first, IP-based metro Ethernet access solution. This is Cisco's charter to continue this focused development, building upon the ensures an optimum linkage between the router and the Ethernet base, a success of Cisco deployments to date. -
Nokia Digital Automation Cloud Broadband Everywhere July 2020
Nokia Digital Automation Cloud Broadband Everywhere July 2020 Frank Shelton 1 © 201 9 Nokia Nokia internal use The technology to keep everyone, everywhere connected has never been more important 2 © 2020 Nokia Public Nokia internal use Disciplined execution for successful integration and transformation Acquired Sold Acquired Acquired Motorola Solutions Devices Acquired Deepfield Unium & Services wireless networks Alcatel-Lucent Acquired Acquired Launched Networks Created Sold Acquired Comptel SpaceTime transformation plan Nokia HERE Gainspeed Created Insight Technologies Nokia Shanghai Acquired Bell Elenion Pulp, Paper, Rubber, Early Bell System products, Mobile phones 2012 2014 2016 2018 2020 3 © 2020 Nokia Public Nokia internal use Creating the technology to connect the world in a sustainable way Improving lives with our technology Integrity Climate Culture Excellent housekeeping practices Operational environmental management & circularity, responsible sourcing, health & safety, preventing the misuse of technology and labor practices in our operations 4 © 2020 Nokia Public Nokia internal use Integrity is the foundation of our business Nokia is a trusted and valued partner to many of the largest companies worldwide. We work tirelessly to earn and keep trust by adhering to the highest standards of ethics, integrity and compliance. *Recognized as one of 2020’s “World’s Most Ethical Companies” by Ethisphere, a global leader in defining and advancing the standards of ethical and responsible business practices. * ”World’s Most Ethical Companies” -
Azqtel: Transitioning from Wimax to TD-LTE
DEC 2015 VOL. 17 ● NO. 6 ● ISSUE 161 VIP Voices AzQTel: Transitioning from WiMAX to TD-LTE Tech Forum Development Trends for Router Technologies Special Smart Operations Topic Jayhun Mollazade, CEO of AzQTel Big Data Mining for Smart Operations 05 CONTENTS ZTE TECHNOLOGIES DEC 2015 VIP Voices AzQTel: Transitioning from WiMAX to TD-LTE 05 Reporter: Zhang Ying Linkem to Expand 4G LTE Coverage 10 Reporter: Zhang Ying Telenor Pakistan and ZTE: One Goal One Team Jayhun Mollazade, CEO of AzQTel 14 Reporter: Pan Xiaolin AzQTel is an Azerbaijan-based telecom company founded in 2005. The company launched its 4G broadband services in October 2010 under the “Sazz” Tech Forum brand name. ZTE TECHNOLOGIES interviewed Jayhun Mollazade, CEO of AzQTel. He discussed AzQTel’s latest developments, the Sazz 4G brand, and the progress of Development Trends for Router Technologies AzQTel’s LTE transition, and also shared his views on 17 By Fan Chengfa the partnership with ZTE. Special Topic: Smart Operations Big Data Mining for Smart Operations 20 By Huang Yuzhu NetNumen™ AOS: A Powerful Platform to Integrate a Unified Portal and Application 24 Virtualization By Feng Huaxing NetNumen™ FMS: Improving Operational 27 Efficiency By Yin Qiaozhi NetNumen™ eFlow Enables Operational 10 Visibility and Intelligence 29 By Yang Yang and Liu Junjie 01 ZTE TECHNOLOGIES DEC 2015 20 ZTE TECHNOLOGIES 14 Advisory Committee Director: Zhao Xianming Deputy Directors: Chen Jane, Xu Huijun, Zhu Jinyun Advisers: Bao Zhongjun, Chen Jian, Chen Xinyu, Cui Li, Fang Jianliang, Sun 33 -
The Telecommunication Industry: Cisco and Lucent's Supply Chains
The Telecommunication Industry: Cisco and Lucent’s Supply Chains by Yishai Boasson M.Eng. Massachusetts Institute of Technology © 2005 Yishai Boasson All rights reserved The author hereby grants to MIT permission to reproduce and to distribute publicly paper and electronic copies of this thesis document in whole or in part. The Telecommunications Industry: Cisco and Lucent’s Supply Chains by Yishai Boasson Abstract This work aims at describing the current trends in supply chain management prevalent in the telecommunications industry. This is done through looking at the telecommunications industry (telephony and data communications), its history and the factors shaping what it currently is. In addition, two companies – Cisco Systems Inc. and Lucent Technologies Inc. are used as two case studies. Looking at these two companies enables us to dive deeper into actual supply chain practices, trying to understand current best practices. As we analyzed these two companies’ supply chains, we used a framework delineated by the belief that excellent supply chain management is a collection of business processes supporting operational goals, which in turn should enable an overall business strategy. Our initial perception of current supply chain practices was shaped by available literature as well as by the image projected by telecommunications companies in forums and publications concerning their supply chain management practices. However, the opportunity to look closely and intimately at one of Cisco’s supply chains has revealed a slightly different picture, where supply chains are not necessarily used as a means to gain sustained competitive advantage. In addition, marked differences in the two companies’ 2 practices might be attributed not only to differing strategies, but also do differing histories. -
ZTE ZXR10 MPLS + SDN + NFV World Congress 2018
MPLS + SDN + NFV World Congress 2018 Multi-Vendor Interoperability Test SDN Controller Orchestrator Controller Path Comp Cisco Huawei Cisco Nokia NSO NCE(IP Domain) IOS XRv9000 NSP Huawei Juniper Arista CX6608 QFX5110 7050SX2-72Q Cisco Nexus 7702 ZTE ZXR10 ZTE ZXR10 T8000-18 M6000-8S PLUS Juniper BISDN Nokia QFX10002 Spirent Basebox 7750 SR-7 Ixia TestCenter IxNetwork Nokia ZTE Cisco ZTE Arista 7750 SR-7 ZXR10 ASR 9000 ZXR10 IP Infusion 7050SX2- M6000-18S Ixia 72Q M6000-5S OcNOS Metaswitch Arista IxNetwork CNRouter 7280SR- ZTE ZXR10 Cisco Nokia Nexus 93180 Huawei 48C6 M6000-18S Arista Juniper 7750 MX240 NE9000-8 SR-7 7280SR-48C6 Huawei NE40E-M2K 12:50:00 Meinberg LANTIME M1000S ZTE Ixia Ericsson IxNetwork Router 6672 ZXR10 Arista Adva M6000-3S 7280SR- FSP150 NEC 48C6 Spirent ProVMe TestCenter Ericsson iPASOLINK VR Huawei Baseband 6620 CX6608 12:50:00 Meinberg LANTIME M4000 Ericsson Ericsson Router 6672 Baseband 6630 Calnex Huawei Calnex Paragon-X CX600-X2-M8A Paragon-T Data Center 1 - VXLAN 12:50:00 UTStarcom Microsemi UAR500 TimeProvider 2300 Segment Routing Clocking Core Router Data Center Microwave Access Device Physical Link MPLS/LDP Route Reflector/ Microwave Link SDN Controller & Orchestration Route Server 20 Topology & Orchestration mputation Element (PCE) NETCONF ZTE Spirent Ixia Huawei ZENIC WAN TestCenter IxNetwork NCE(super) Controller Spirent Huawei Delta NE9000- TestCenter AGC7648A 8 Ericsson Juniper MINI-LINK MX104 6693 Cisco Cisco NCS5500 Segment Routing NCS 5500 Core Nokia Ericsson MPLS 7750 SR-7 Router 6371 Cisco ASR 9000 -
PTX5000 and PTX3000 Packet Transport Routers
Data Sheet PTX5000 and PTX3000 Packet Transport Routers Product Overview Product Description Increased interactions between New traffic dynamics like mobility, video, and cloud-based services are transforming people and machines are traditional network patterns and topologies. Stratified, statically designed and manually creating a deluge of traffic, operated networks must evolve to meet demands quickly and economically. Many with increasingly unpredictable operators have seen profitability stagnate and total cost of ownership (TCO) grow under patterns. These dynamics have the burden that growing traffic demands are imposing. Service providers need to become intensified the challenge to meet more agile in order to optimize their existing network resources, shorten planning cycles, growth with traditional network and remove rigid network layers. products and architectures. A new approach, based on both physical • Static scale: The service provider backbone handles the entire weight of the network’s and virtual innovations, is required traffic. Therefore, it is paramount that the core network grows organically, along with to help service providers stay the traffic. The silicon, system, and SDN innovations for the core empower service ahead of growing traffic demands providers to scale faster than the traffic demands themselves in an elegant, elastic, while remaining profitable. Juniper redundant package—without requiring forklift upgrades. Networks PTX Series Packet Transport Routers with custom • Static architecture: Virtualized services and the explosion of cloud-based applications ExpressPlus Silicon, built from are creating traffic patterns that are increasingly unpredictable. To handle this the ground up with SDN in mind, unpredictability, service providers need their architectures to be flexible and dynamic provide service providers with a across all layers. -
Nortel Technology Lens: Analysis and Observations
Nortel Technology Lens: Analysis and Observations Team Members: Peter MacKinnon, Research Associate Peter Chapman, Telecommunications Engineer Hussein Mouftah, Distinguished University Professor School of Electrical Engineering and Computer Science Faculty of Engineering University of Ottawa March 25, 2015 I Table of Contents Executive Summary i - x 1. Introduction 1.1 Preamble 1 1.2 Problem Statement 1 1.3 Summary to Approach & Methodologies 1 1.4 Data & Information Gathering 2 1.5 Principal Findings 3 2. Nortel Technology 2.1 Overview 4 2.2 Technology Environment over the Study Period 5 2.3 Corporate Perspective on Technology 7 2.4 Key Technical & Corporate Milestones 8 2.5 Technology-based Offerings 10 2.6 Nortel’s Right Angle Turn 13 2.7 Skunkworks 15 2.8 Professional Services 16 2.9 The Changing Status of Nortel Technology & Product Offerings 17 2.10 Access Products & Technology 18 2.11 Long-haul Optical 20 2.12 Summary 20 3. Nortel Acquisitions and Strategic Alliances 3.1 Preamble 22 3.2 Acquisitions: An Overview 22 3.3 Selected Acquisitions 25 3.4 Acquisition Summary 31 3.5 Strategic Alliances: A Sample 33 3.6 Sell-off of Assets 34 3.7 Summary 35 4. Technology Management 4.1 Preamble 36 4.2 Time to Market: Some Technical Delays & Missed Opportunities 36 4.3 R&D Expenditures 38 4.4 Research & Development Priorities 39 4.5 Nortel as ‘Definer’ versus ‘Contractor’ 40 4.6 Systems Engineering 42 4.7 Corporate Culture with Respect to R&D and Commercialization 42 4.8 Management Awareness of Nortel Technologies & Technical Strengths 43 4.9 Product Commercialization 43 4.10 Outsourcing & Headcount 44 4.11 Setting the Stage for Unanticipated Troubles 44 4.12 Summary 47 II Table of Contents (cont.) 5. -
Router Configuration Guide Release 20.10.R1
ROUTER CONFIGURATION GUIDE RELEASE 20.10.R1 7450 ETHERNET SERVICE SWITCH 7750 SERVICE ROUTER 7950 EXTENSIBLE ROUTING SYSTEM VIRTUALIZED SERVICE ROUTER ROUTER CONFIGURATION GUIDE RELEASE 20.10.R1 3HE 15827 AAAD TQZZA 01 Issue: 01 October 2020 Nokia — Proprietary and confidential. Use pursuant to applicable agreements. ROUTER CONFIGURATION GUIDE RELEASE 20.10.R1 Nokia is committed to diversity and inclusion. We are continuously reviewing our customer documentation and consulting with standards bodies to ensure that terminology is inclusive and aligned with the industry. Our future customer documentation will be updated accordingly. Nokia is a registered trademark of Nokia Corporation. Other products and company names mentioned herein may be trademarks or tradenames of their respective owners. The information presented is subject to change without notice. No responsibility is assumed for inaccuracies contained herein. © 2020 Nokia. Contains proprietary/trade secret information which is the property of Nokia and must not be made available to, or copied or used by anyone outside Nokia without its written authorization. Not to be used or disclosed except in accordance with applicable agreements. 2 3HE 15827 AAAD TQZZA 01 Issue: 01 ROUTER CONFIGURATION GUIDE RELEASE 20.10.R1 Table of Contents 1 Getting Started..............................................................................11 1.1 About This Guide.......................................................................................11 1.2 Router Configuration Process ...................................................................12 -
IP NGN Backbone Routers for the Next Decade
IP NGN Backbone Routers for the Next Decade Josef Ungerman Consulting SE, CCIE #6167 © 2010 Cisco and/or its affiliates. All rights reserved. Cisco Public 1 • Motivations for IP NGN • Trends is IP/MPLS Core Design • Router Anatomy Trends • Latest Product Updates • Switching Fabric Technologies • Network Processor Technologies © 2010 Cisco and/or its affiliates. All rights reserved. Cisco Public 2 Exponential Growth and Evolving Traffic Mix Video & Multimedia IP traffic will increase 4X 90% Consumer (767 exabytes by 2014) Traffic Mobile Internet 39X Increase in Traffic IT Services via Cloud 2009 Global IP Traffic 2014 300+% Source: Cisco Visual Networking Index—Forecast, 2009-2014 Market Growth • IPv6 and IPv4 Address Exhaustion More Issues:• LTE moving from circuits to packets Very Different • new access technologies – WiFi, FTTX Traffic Profile © 2010 Cisco and/or its affiliates. All rights reserved. Cisco Public 3 Animated slide Monetization Traffic New revenue streams Profitability Revenue Optimization Efficient delivery © 2010 Cisco and/or its affiliates. All rights reserved. Cisco Public 4 Network Architecture Trends © 2010 Cisco and/or its affiliates. All rights reserved. Cisco Public 5 ACCESS AGGREGATION BACKBONE PDH MW SDH/ATM SDH 2G Mobile 3G FMC/ SDH Packet PDH Core ATM SGSN CPE GGSN IGW FR/ATM INTERNET CPE IP/MPLS Internet Metro Ethernet Peering IGW DSLAM Data BRAS MSAN Centers CPE Regional Backbone 1000’s 100’s DWDM 10’s DWDM 1’s © 2010 Cisco and/or its affiliates. All rights reserved. Cisco Public 6 ANY AGGREGATION EDGE CORE ACCESS IP NGN • single multiservice IP/MPLS network CPE • operational hierarchy • Circuits (Pseudowires) and Clouds (IP) PDH MW 2G BACKBONE Internet CarrierE AGGREGATION IP/MPLS Peering 3G IP/MPLS IGW PON CGv6 INTERNET DSLAM Ethernet Data MPLS-TP BRAS Centers MPLS … LTE, WiFI… DWDM 1000’s 100’s 10’s 1’s © 2010 Cisco and/or its affiliates.