Evaluation of Mechanical Properties of Al-Cu Cold Sprayed And
Total Page:16
File Type:pdf, Size:1020Kb
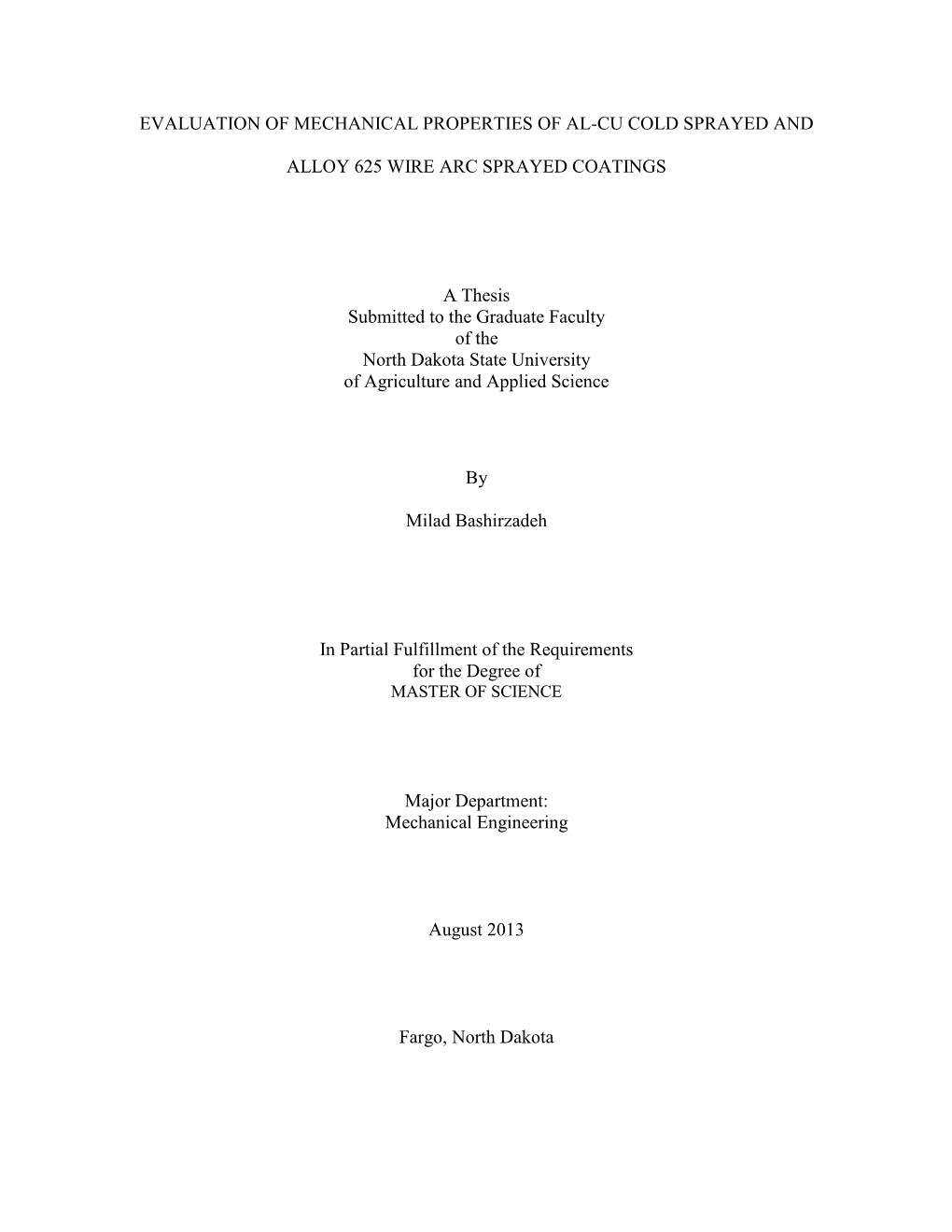
Load more
Recommended publications
-
Investigation of Agglomerated Ceramic Powders Suitable for Cold Spray Geoffrey Celeste, Vincent Guipont, Djamel Missoum-Benziane
Investigation of agglomerated ceramic powders suitable for cold spray Geoffrey Celeste, Vincent Guipont, Djamel Missoum-Benziane To cite this version: Geoffrey Celeste, Vincent Guipont, Djamel Missoum-Benziane. Investigation of agglomerated ceramic powders suitable for cold spray. 2021. hal-03199051 HAL Id: hal-03199051 https://hal-mines-paristech.archives-ouvertes.fr/hal-03199051 Preprint submitted on 15 Apr 2021 HAL is a multi-disciplinary open access L’archive ouverte pluridisciplinaire HAL, est archive for the deposit and dissemination of sci- destinée au dépôt et à la diffusion de documents entific research documents, whether they are pub- scientifiques de niveau recherche, publiés ou non, lished or not. The documents may come from émanant des établissements d’enseignement et de teaching and research institutions in France or recherche français ou étrangers, des laboratoires abroad, or from public or private research centers. publics ou privés. Investigation of agglomerated ceramic powders suitable for cold spray Geoffrey CELESTE*, Vincent GUIPONT, Djamel MISSOUM-BENZIANE Centre des matériaux - CMAT, MINES ParisTech - PSL, UMR CNRS 7633 63 - 65 rue Henri-Auguste Desbruères, 91000 EVRY, France * [email protected] Abstract deposition. The impact behavior of porous agglomerated granules that can adhere with possible beneficial compaction Cold gas spraying is a solid-state deposition process developed of the porous particle has been evidenced in case of HA or for metallic powders as feedstock materials. For ceramic TiO2 powders with nano-sized grains leading to successful materials, such low temperature-high velocity kinetic process build-up of a coating up [13], [14]. The powder could be is still questionable but could have interesting advantages. -
Cold Gas Spraying of a High-Entropy Crfenimn Equiatomic Alloy
coatings Article Cold Gas Spraying of a High-Entropy CrFeNiMn Equiatomic Alloy Joonas Lehtonen 1,* , Heli Koivuluoto 2 , Yanling Ge 1, Aapo Juselius 1 and Simo-Pekka Hannula 1 1 Department of Chemistry and Materials Science, Aalto University, Kemistintie 1, 02150 Espoo, Finland; Yanling.ge@aalto.fi (Y.G.); aapo.juselius@aalto.fi (A.J.); simo-pekka.hannula@aalto.fi (S.-P.H.) 2 Materials Science and Environmental Engineering, Faculty of Engineering and Natural Sciences, Tampere University, Korkeakoulunkatu 6, 33720 Tampere, Finland; heli.koivuluoto@tuni.fi * Correspondence: joonas.m.lehtonen@aalto.fi Received: 30 November 2019; Accepted: 2 January 2020; Published: 8 January 2020 Abstract: Cold gas spraying was used to make a coating from an equiatomic CrFeNiMn high-entropy alloy. This four-component alloy was chosen because it is Co-free, thus allowing application in nuclear industries as a possible replacement of currently used stainless steel coatings. The feedstock material was gas atomized powder with a particle size distribution from 20 to 45 µm. A number of parameters were tested, such as the powder feed rate and gas feed pressure, in order to obtain as dense a coating as possible with nitrogen as the process gas. Spraying was performed using a gas preheating temperature of 1000 ◦C, gas feed pressure ranging from 50 to 60 bar, and two powder feeding rates. The coating thicknesses ranging from 230 to 490 µm and porosities ranging from 3% to 10% were obtained depending on the powder feed rate and gas feed pressure. The hardness of the cross-section of the coating was usually lower than that of the surface. -
On Deposition of Waspaloy Coatings by Cold Spray
On deposition of Waspaloy coatings by cold spray S. Vezzu`*1, S. Rech1, E. Vedelago1, G. P. Zanon2, G. Alfeo2, A. Scialpi2 and R. Huang3 The deposition of pore free and highly adhered Ni and Co superalloy coatings is of great interest for engine design and gas turbine applications, both in case of maintenance repair and overhaul operations as well for mechanical and chemical protection purposes in aeronautics and energy applications. This study would like to give a wide overview about the capability of cold spray technology on this topic: two different commercially available deposition systems, Sulzer-CGT Kinetiks 4000 and Plasma Giken PCS-1000, were compared, and deposition processes with both nitrogen and helium as carrier gas have been explored. Microstructural investigation, microhardness and adhesion results are reported to depict a preliminary scenario of coating properties. Fully dense coatings with thickness .1 mm and adhesion .50 MPa are obtained using helium, while quite porous, 20 MPa adhered coatings are obtained using nitrogen. Finally, general considerations about the potential applicability of those coatings for repair purpose in aerospace applications are pointed out. Keywords: Nickel alloys, Waspaloy, Coating microstructure, MRO, PCS-1000, Kinetiks This paper is part of a special issue on cold spray technology Introduction heat affected zones on precipitation alloys such as the most part of superalloys itself could lead to the Superalloys are traditionally and extensively employed solubilisation or recrystallisation or simply grain growth for the realisation of gas turbine parts and high generally combined with a loss of mechanical properties temperature engines in aeronautic and energy applica- and strength. -
Powders Were Used As Feedstock Material: a Pure Anatase (Hombikat) and Powder P25/20 That Contains up to 20 % Rutile
ITSC’2017 DÜSSELDORF JUNE 7 - JUNE 9, 2017 - 64 exhibitors (twelve countries) - 700 total attendees and visitors - 30 countries represented - 300 papers presented - 35 papers Cold Spray Plenary Lecture P. Sander Airbus Operations GmbH May 7-10, 2018 Orlando, Florida US Gaylord Palms Resort & Convention Center Abstract Due: 2017 September 30, 2017 Final PDF Manuscript Due: February 28, 2018 2 Coldgas Coatings with Adjusted Curie Temperatures for Influencing the Magnetic Susceptibility F. Trenkle, E. Schopp, S. Hartmann obz innovation gmbh, Bad Krozingen, Germany [email protected] OBZ innovation presents the latest developments in the field of induction capable coatings, mainly used for induction cookware on aluminum or copper base material. To offer additional safety and comfort to the customer, a special induction coating was developed with an immanent temperature limitation and uniform heat distribution (Patent T-LIM coating). Pans with as sprayed cold gas “Intelligent” T-Lim induction coating (left) induction coating (left) and after cares for distribution, as the equally machining (right). caramelization process over Conventional induction cookware (right) shows over- and under heated areas, depending on where the induction coil is placed. 3 “Intelligent” induction coating (left) shows in the heat distribution coating (right Temperature and power development Material 2 controls with its Curie for a conventional ferritic chromium point the temperature limitation. cookware and the newly developed T- Furthermore, it cares for a Lim coating. uniform heat distribution over the complete coating area, since the usually not uniformly distributed magnetic field of the induction coil is forced by the alternating magnetic susceptibility (grey = lower and obz developed “coloduct coating” can be black = higher susceptibility) to combined with standard and T-Lim the areas of lower temperatures. -
Formation of Cold-Sprayed Ceramic Titanium Dioxide Layers on Metal Surfaces J.-O
JTTEE5 20:292–298 DOI: 10.1007/s11666-010-9563-3 1059-9630/$19.00 Ó ASM International Formation of Cold-Sprayed Ceramic Titanium Dioxide Layers on Metal Surfaces J.-O. Kliemann, H. Gutzmann, F. Ga¨rtner, H. Hu¨bner, C. Borchers, and T. Klassen Peer Reviewed (Submitted May 10, 2010; in revised form September 16, 2010) Titanium dioxide (TiO2) coatings have potential applications in biomedical implants or as photo-catalytic functional systems. Cold spraying is a well-established method for metal on metal coatings. In cold spraying, the required heat for bonding is provided by plastic deformation of the impacting ductile particles. In contrast, few authors have investigated the impact phenomena and layer formation process for spraying brittle ceramic materials on ductile metal surfaces. In this study, the formation of TiO2 coatings on aluminum, copper, titanium, and steel substrates was investigated by SEM, TEM, XRD, and Raman spectroscopy. The results show that the deposition efficiency depends on spray temperature, powder properties, and in particular on substrate ductility, even for impact of ceramic particles during a second pass over already coated areas. Ceramic particles bond to metallic substrates showing evidence of shear instabilities. High-resolution TEM images revealed no crystal growth or phase transitions at the ceramic/metal interfaces. Keywords bonding mechanism, cold spraying, photocatalytic stresses lead to plastic deformation. Kinetic energy is activity, titanium dioxide converted to thermal energy, which cannot dissipate within the short time frame of the impact (quasi-adiabatic conditions). Metallic materials soften at the boundaries, which leads to more plastic deformation and heat gener- ation, resulting in shear instabilities. -
Critical Review of Corrosion Protection by Cold Spray Coatings
Critical review of corrosion protection by cold spray coatings 1,2 1,2 1∗ S. M. Hassani-Gangaraj , A. Moridi and M. Guagliano Cold spray distribution, surface oxidation15–18 as well as substrate nature and properties.19,20 Cold spray is a high deposition rate coating process, in The exact bonding mechanism is still a matter of which solid powder particles are accelerated to velocities − 1 debate. However, adiabatic shear instability is known as ranging between 300 and 1200 m s through a de the predominant bonding precursor in cold spray. Adia- Laval nozzle, impact and adhere to a substrate or pre- batic shear instability occurs at the particle substrate viously deposited coating. The powder feedstock remains interface during impact. A strong pressure field is intro- well below its melting temperature during deposition. duced as a result of particle impact on the substrate. Con- Therefore, cold spray is categorised among solid state sequently, a shear load is generated, which accelerates the fi deposition methods, and offer signi cant advantages as material laterally. This causes localised shear straining, compared to other traditional thermal spray techniques. which, under critical conditions, leads to adiabatic shear Particles/substrate interaction during high velocity instability. Experimental results show that the minimal impact and the resultant bonding is fundamental, and particle impact velocity needed to produce shear localis- determines physical and mechanical properties of the ation at the particles/substrate interface, correlates quite coating/substrate system. Numerous experimental and well with the critical velocity for particle deposition by computational efforts have been carried out to provide a the cold spray process in a number of metallic materials. -
Cold Spraying of Titanium: a Review of Bonding Mechanisms, Microstructure and Properties T
Key Engineering Materials Online: 2012-12-27 ISSN: 1662-9795, Vol. 533, pp 53-90 doi:10.4028/www.scientific.net/KEM.533.53 © 2013 Trans Tech Publications, Switzerland Cold Spraying of Titanium: A Review of Bonding Mechanisms, Microstructure and Properties T. Hussain1 1 Centre for Energy and Resource Technology (CERT), School of Applied Sciences, Cranfield University, Bedford, MK43 0AL, UK [email protected] Keywords: cold spray, deposits, bonding mechanisms, titanium Abstract. Cold gas dynamic spraying (CGDS) is a relatively new branch of surface engineering that involves modification of the surface of substrates to provide specific engineering advantages, which the substrate alone cannot provide. Cold spraying, as a metal deposition technique, involves spraying of typically 10-40 μm particles which are accelerated by a propellant gas to 300- 1200 m/s at a temperature well below the melting point of material, and upon impact deform and adhere to the substrate. The deposition process in cold spraying occurs in a solid state which results in reduced oxidation and absence of phase changes; whereas, in thermal spraying deposition occurs of molten or semi molten particles. Over the last decade the interest in cold spraying has increased substantially. Considerable effort has been invested in process developments and optimization of coatings like copper. However, bonding in cold spraying is still a matter of some debate. The most prevalent theory is that when a particle travels at a minimum required velocity the particle deforms at a very high strain rate upon impact and during this deformation thermal softening dominates over work hardening in impact zone and a material jet is produced. -
Formation of Cold-Sprayed Ceramic Titanium Dioxide Layers on Metal Surfaces J.-O
View metadata, citation and similar papers at core.ac.uk brought to you by CORE provided by Springer - Publisher Connector JTTEE5 20:292–298 DOI: 10.1007/s11666-010-9563-3 1059-9630/$19.00 Ó ASM International Formation of Cold-Sprayed Ceramic Titanium Dioxide Layers on Metal Surfaces J.-O. Kliemann, H. Gutzmann, F. Ga¨rtner, H. Hu¨bner, C. Borchers, and T. Klassen Peer Reviewed (Submitted May 10, 2010; in revised form September 16, 2010) Titanium dioxide (TiO2) coatings have potential applications in biomedical implants or as photo-catalytic functional systems. Cold spraying is a well-established method for metal on metal coatings. In cold spraying, the required heat for bonding is provided by plastic deformation of the impacting ductile particles. In contrast, few authors have investigated the impact phenomena and layer formation process for spraying brittle ceramic materials on ductile metal surfaces. In this study, the formation of TiO2 coatings on aluminum, copper, titanium, and steel substrates was investigated by SEM, TEM, XRD, and Raman spectroscopy. The results show that the deposition efficiency depends on spray temperature, powder properties, and in particular on substrate ductility, even for impact of ceramic particles during a second pass over already coated areas. Ceramic particles bond to metallic substrates showing evidence of shear instabilities. High-resolution TEM images revealed no crystal growth or phase transitions at the ceramic/metal interfaces. Keywords bonding mechanism, cold spraying, photocatalytic stresses lead to plastic deformation. Kinetic energy is activity, titanium dioxide converted to thermal energy, which cannot dissipate within the short time frame of the impact (quasi-adiabatic conditions). -
On the Influence of Manufacturing Strategy of 3D-Printed Polymer Substrates on Cold Spray Deposition
ESAFORM 2021. MS13 (Additive Manufacturing), 10.25518/esaform21.3003 On the Influence of Manufacturing Strategy of 3D-Printed Polymer Substrates on Cold Spray Deposition Antonio Viscusi, Antonello Astarita, Domenico Borrelli, Antonio Caraviello, Luigi Carrino, Roberta Della Gatta, Valentina Lopresto, Ilaria Papa, Alessia Serena Perna, Raffaele Sansone and Antonino Squillace Antonio Viscusi. Department of Chemical, Materials and Production Engineering, University of Naples Federico II, Piazzale V. Tecchio 80, 80125 Napoli, Italy. Corresponding author: [email protected] Antonello Astarita. Department of Chemical, Materials and Production Engineering, University of Naples Federico II, Piazzale V. Tecchio 80, 80125 Napoli, Italy. Domenico Borrelli. Sòphia High Tech, Via Romani 228, 80048, Sant'Anastasia NA, Italy. Antonio Caraviello. Sòphia High Tech, Via Romani 228, 80048, Sant'Anastasia NA, Italy. Luigi Carrino. Department of Chemical, Materials and Production Engineering, University of Naples Federico II, Piazzale V. Tecchio 80, 80125 Napoli, Italy. Roberta Della Gatta. Department of Chemical, Materials and Production Engineering, University of Naples Federico II, Piazzale V. Tecchio 80, 80125 Napoli, Italy. Valentina Lopresto. Department of Chemical, Materials and Production Engineering, University of Naples Federico II, Piazzale V. Tecchio 80, 80125 Napoli, Italy. Ilaria Papa. Department of Chemical, Materials and Production Engineering, University of Naples Federico II, Piazzale V. Tecchio 80, 80125 Napoli, Italy. Alessia Serena Perna. Department of Chemical, Materials and Production Engineering, University of Naples Federico II, Piazzale V. Tecchio 80, 80125 Napoli, Italy. University of Bergamo, Bergamo, Italy. Raffaele Sansone. Sòphia High Tech, Via Romani 228, 80048, Sant'Anastasia NA, Italy. Antonino Squillace. Department of Chemical, Materials and Production Engineering, University of Naples Federico II, Piazzale V. -
Prezentacja Programu Powerpoint
Les Rencontres Internationales sur la Projection Thermique – RIPT 9 11th to 13th December 2019, Jülich, Germany Preliminary studies of TiO2 coatings deposition onto ABS polymer substrates by low pressure cold spraying M. Winnicki, M. Jasiorski, A. Baszczuk, B. Borak Wroclaw University of Science and Technology Faculty of Mechanical Engineering Lukasiewicza 5, 50-371 Wrocław, e-mail: [email protected] Preliminary studies of TiO2 coatings deposition onto ABS substrates by low pressure cold spraying Outline of presentation • Titanium dioxide – why? • State of art in TiO2 deposition. • Low pressure cold spray operating principle. • Research genesis. • Process parameters. • Materials used in the research. • TiO2 crystalline coatings. • TiO2 amorphous coatings. • TiO2 mixed crystalline - amorphous coatings. • Polyamide – anatase composite coatings. 2 Preliminary studies of TiO2 coatings deposition onto ABS substrates by low pressure cold spraying Titanium dioxide – why? Gas sensors Water and air purification Photocatalysts Self-cleaning agent Antibacterial TiO2 agent Electrochromic Wide gap devices semiconductor Solar oxide cells 3 Preliminary studies of TiO2 coatings deposition onto ABS substrates by low pressure cold spraying Titanium dioxide – why? Rahim T.B.A., Fabrication of Cold Spray Ti-O Coatings Engineered from Agglomerated Powders, 2016, doctoral thesis 4 Preliminary studies of TiO2 coatings deposition onto ABS substrates by low pressure cold spraying State of art in TiO2 deposition TiO2 coating Electro- CVD deposition Magnetron -
Analysis of the Cold Gas Spraying Process and Determination of Selected Properties of Metallic Coatings on Polymers Aleksandra Malachowska
Analysis of the cold gas spraying process and determination of selected properties of metallic coatings on polymers Aleksandra Malachowska To cite this version: Aleksandra Malachowska. Analysis of the cold gas spraying process and determination of selected properties of metallic coatings on polymers. Materials. Université de Limoges; Uniwersytet Wro- clawski, 2016. English. NNT : 2016LIMO0012. tel-01741350 HAL Id: tel-01741350 https://tel.archives-ouvertes.fr/tel-01741350 Submitted on 23 Mar 2018 HAL is a multi-disciplinary open access L’archive ouverte pluridisciplinaire HAL, est archive for the deposit and dissemination of sci- destinée au dépôt et à la diffusion de documents entific research documents, whether they are pub- scientifiques de niveau recherche, publiés ou non, lished or not. The documents may come from émanant des établissements d’enseignement et de teaching and research institutions in France or recherche français ou étrangers, des laboratoires abroad, or from public or private research centers. publics ou privés. UNIVERSITE DE LIMOGES ECOLE DOCTORALE SIMMEA Sciences et Ingénierie en Matériaux, Mécanique, Energétique et Aéronautique Faculté des Sciences et Techniques de Limoges Laboratoire Sciences des Procédés Céramiques et Traitements de Surface Thèse N° [-----] Thèse pour obtenir le grade de DOCTEUR DE L’UNIVERSITÉ DE LIMOGES Discipline / Spécialité : Sciences des Matériaux Aleksandra Małachowska Le 22 mars 2016 Analysis of the cold gas spraying process and determination of selected properties of metallic coatings -
Redalyc.Cold Gas Spray Coatings: Basic Principles, Corrosion
Eclética Química ISSN: 0100-4670 [email protected] Universidade Estadual Paulista Júlio de Mesquita Filho Brasil Santos da Silva, Fernando; Cinca, Núria; Dosta, Sergi; Garcia Cano, Irene; Guilemany, Josep Maria; Benedetti, Assis Vicente Cold gas spray coatings: basic principles, corrosion protection and applications Eclética Química, vol. 42, 2017, pp. 09-32 Universidade Estadual Paulista Júlio de Mesquita Filho Araraquara, Brasil Available in: http://www.redalyc.org/articulo.oa?id=42955131003 How to cite Complete issue Scientific Information System More information about this article Network of Scientific Journals from Latin America, the Caribbean, Spain and Portugal Journal's homepage in redalyc.org Non-profit academic project, developed under the open access initiative Original review iq.unesp.br/ecletica | Vol. 42 | 2017 | Cold gas spray coatings: basic principles, corrosion protection and applications Fernando Santos da Silva 1,2+ , Núria Cinca 2 , Sergi Dosta 2 , Irene Garcia Cano 2 , Josep Maria Guilemany 2 , Assis Vicente Benedetti 1 1 São Paulo State University, Institute of Chemistry, 55 Prof. Francisco Degni St., 14800-060 Araraquara, São Paulo, Brazil 2 Barcelona University, Centre de Projecció Tèrmica, Martí i Franqués 1 St., 08028 Barcelona, Spain + Corresponding authors: Fernando Santos da Silva, phone: +55-16-3301-9649, e-mail address: [email protected] Assis Vicente Benedetti, phone: +55-16-3301-9641, e-mail address: [email protected] ARTICLE INFO Keywords: Article history: 1. cold gas spray (CGS) coatings Received: October 6, 2017 2. feedstock powders Accepted: November 15, 2017 3. spray parameters Published: December 30, 2017 4. corrosion 5. CGS technology applications ABSTRACT : In this review, the beginnings and evolution of the cold gas spray (CGS) technique are described, followed by the main fundamental aspects of the technique together with a description of the several spraying systems up to date.