Conceptual Launch Vehicle and Spacecract Design for Risk Assessment
Total Page:16
File Type:pdf, Size:1020Kb
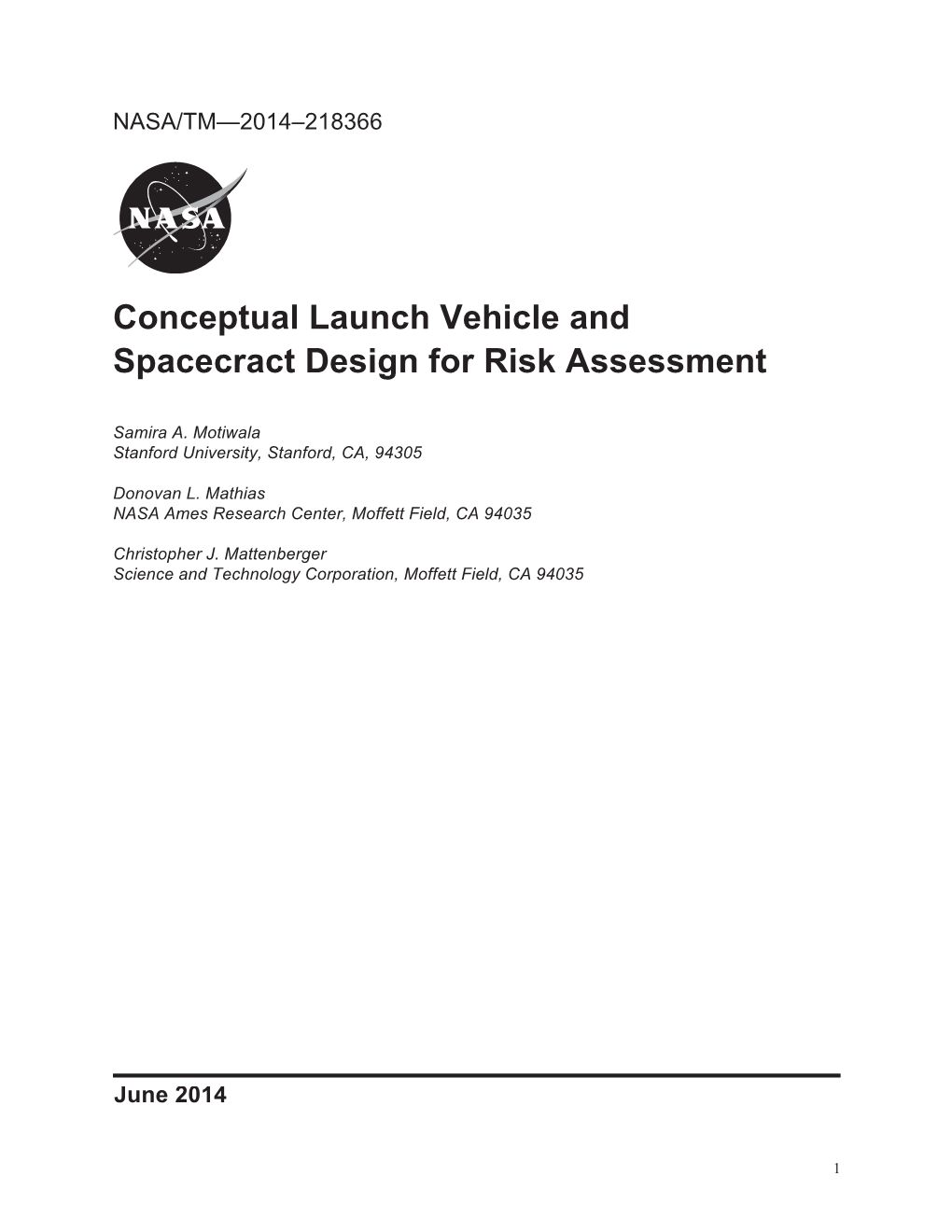
Load more
Recommended publications
-
Conceptual Design and Optimization of Hybrid Rockets
University of Calgary PRISM: University of Calgary's Digital Repository Graduate Studies The Vault: Electronic Theses and Dissertations 2021-01-14 Conceptual Design and Optimization of Hybrid Rockets Messinger, Troy Leonard Messinger, T. L. (2021). Conceptual Design and Optimization of Hybrid Rockets (Unpublished master's thesis). University of Calgary, Calgary, AB. http://hdl.handle.net/1880/113011 master thesis University of Calgary graduate students retain copyright ownership and moral rights for their thesis. You may use this material in any way that is permitted by the Copyright Act or through licensing that has been assigned to the document. For uses that are not allowable under copyright legislation or licensing, you are required to seek permission. Downloaded from PRISM: https://prism.ucalgary.ca UNIVERSITY OF CALGARY Conceptual Design and Optimization of Hybrid Rockets by Troy Leonard Messinger A THESIS SUBMITTED TO THE FACULTY OF GRADUATE STUDIES IN PARTIAL FULFILLMENT OF THE REQUIREMENTS FOR THE DEGREE OF MASTER OF SCIENCE GRADUATE PROGRAM IN MECHANICAL ENGINEERING CALGARY, ALBERTA JANUARY, 2021 © Troy Leonard Messinger 2021 Abstract A framework was developed to perform conceptual multi-disciplinary design parametric and optimization studies of single-stage sub-orbital flight vehicles, and two-stage-to-orbit flight vehicles, that employ hybrid rocket engines as the principal means of propulsion. The framework was written in the Python programming language and incorporates many sub- disciplines to generate vehicle designs, model the relevant physics, and analyze flight perfor- mance. The relative performance (payload fraction capability) of different vehicle masses and feed system/propellant configurations was found. The major findings include conceptually viable pressure-fed and electric pump-fed two-stage-to-orbit configurations taking advan- tage of relatively low combustion pressures in increasing overall performance. -
NEP Paper World Space Congress
IAC-02-S.4.02 PERFORMANCE REQUIREMENTS FOR A NUCLEAR ELECTRIC PROPULSION SYSTEM Larry Kos In-Space Technical Lead Engineer NASA Marshall Space Flight Center MSFC, Alabama, 35812 (USA) E-mail: [email protected] Les Johnson In-Space Transportation Technology Manager Advanced Space Transportation Program/TD15 NASA Marshall Space Flight Center MSFC, Alabama, 35812, (USA) E-mail: [email protected] Jonathan Jones Aerospace Engineer NASA Marshall Space Flight Center MSFC, Alabama, 35812 (USA) E-mail: [email protected] Ann Trausch Mission and System Analysis Lead NASA Marshall Space Flight Center MSFC, Alabama 35812 (USA) E-mail: [email protected] Bill Eberle Aerospace Engineer Gray Research Inc. Huntsville, Alabama 35806 (USA) E-mail: [email protected] Gordon Woodcock Technical Consultant Gray Research Inc. Huntsville, Alabama 35806 (USA) E-mail: [email protected] NASA is developing propulsion technologies potentially leading to the implementation of a nuclear electric propulsion system supporting robotic exploration of the solar system. The mission limitations imposed by the use of today’s predominantly chemical propulsion systems are many: long trip times, minimal science payload mass, minimal power at the destination for science, and the near-impossibility of encountering multiple targets or even orbiting distant destinations. Performance-based mission analysis, comparing a first generation nuclear electric propulsion system with chemical and solar electric propulsion was performed and will be described in the paper. Mission Characteristics and Challenges ________________ Copyright © 2002 by the American Institute of Aeronautics and Europa Lander Astronautics, Inc. No copyright is asserted in the United States under Title 17, U.S. -
Increasing Launch Rate and Payload Capabilities
Aerial Launch Vehicles: Increasing Launch Rate and Payload Capabilities Yves Tscheuschner1 and Alec B. Devereaux2 University of Colorado, Boulder, Colorado Two of man's greatest achievements have been the first flight at Kitty Hawk and pushing into the final frontier that is space. Air launch systems aim to combine these great achievements into a revolutionary way to deliver satellites, cargo and eventually people into space. Launching from an aircraft has many advantages, including the ability to launch at any inclination and from above bad weather, which could delay ground launches. While many concepts for launching rockets from an airplane have been developed, very few have made it past the drawing board. Only the Pegasus and, to a lesser extent, SpaceShipOne have truly shown the feasibility of such a system. However, a recent push for rapid, small payload to orbit launches by the military and a general need for cheaper, heavy lift options are leading to an increasing interest in air launch methods. In order for the efficiency and flexibility of the system to be realized, however, additional funding and research are necessary. Nomenclature ALASA = airborne launch assist space access ALS = air launch system DARPA = defense advanced research project agency LEO = low Earth orbit LOX = liquid oxygen RP-1 = rocket propellant 1 MAKS = Russian air launch system MECO = main engine cutoff SS1 = space ship one SS2 = space ship two I. Introduction W hat typically comes to mind when considering launching people or satellites to space are the towering rocket poised on the launch pad. These images are engraved in the minds of both the public and scientists alike. -
PARAMETRIC ANALYSIS of PERFORMANCE and DESIGN CHARACTERISTICS for ADVANCED EARTH-TO-ORBIT SHUTTLES by Edwurd A
NASA TECHNICAL NOTE -6767 . PARAMETRIC ANALYSIS OF PERFORMANCE AND DESIGN CHARACTERISTICS FOR ADVANCED EARTH-TO-ORBIT SHUTTLES by Edwurd A. Willis, Jr., Wz'llium C. Struck, und John A. Pudratt Lewis Reseurch Center Clevelund, Ohio 44135 NATIONAL AERONAUTICS AND SPACE ADMINISTRATION WASHINGTON, D. C. APRIL 1972 f TECH LIBRARY KAFB, NM I111111 Hlll11111 Ill# 11111 11111 lllllIll1Ill -. -- 0133bOL 1. Report No. 2. Government Accession No. 3. Recipient's Catalog No. - NASA TN D-6767 4. Title and Subtitle PAR I 5. Report Date METRIC NALYSIS OF PERFORMA K! E ND April 1972 DESIGN CHARACTERISTICS FOR ADVANCED EARTH-TO- 6. Performing Organization Code ORBIT SHUTTLES 7. Author(s) 8. Performing Organization Report No. Edward A. Willis, Jr. ; William C. Strack; and John A. Padrutt E-6749 10. Work Unit No. 9. Performing Organization Name and Address 110-06 Lewis Research Center 11. Contract or Grant No. National Aeronautics and Space Administration Cleveland, Ohio 44135 13. Type of Report and Period Covered 12. Sponsoring Agency Name and Address Technical Note National Aeronautics and Space Administration 14. Sponsoring Agency Code Washington, D. C. 20546 ~~ .. ~~ 16. Abstract Performance, trajectory, and design characteristics are presented for (1) a single-stage shuttle with a single advanced rocket engine, (2) a single-stage shuttle with an initial parallel chemical-engine and advanced-engine burn followed by an advanced-engine sustainer burn (parallel-burn configuration), (3) a single-stage shuttle with an initial chemical-engine burn followed by an advanced-engine burn (tandem-burn configuration), and (4)a two-stage shuttle with a chemical-propulsion booster stage and an advanced-propulsion upper stage. -
Aeronautical Engineering
Aeronautical NASA SP-7037 (95) Engineering April 1978 A Continuing NASA Bibliography indexes National Space Administration Aeronautical Engineering Aer ering Aeronautical Engineerin igineerjng Aeronautical Engin ^il Engineering Aeronautical E nautical Engineering Aeronau Aeronautical Engineering Aer ^ring Aeronautical Engineering gineer jng Aeronautical Engirn al Engineering Aeronautical E nautical Engineering Aeronaut Aeronautical Engineering Aerc ring Aeronautical Engineering ACCESSION NUMBER RANGES Accession numbers cited in this Supplement fall within the following ranges: STAR(N-10000 Series) N78-13998—N78-15985 IAA (A-10000 Series) A78-17138—A78-20614 This bibliography was prepared by the NASA Scientific and Technical Information Facility operated for the National Aeronautics and Space Administration by Informatics Information NASA SP-7037(95) AERONAUTICAL ENGINEERING A Continuing Bibliography Supplement 95 A selection of annotated references to unclas- sified reports and journal articles that were introduced into the NASA scientific and tech- nical information system and announced in March 1978m • Scientific and Technical Aerospace Reports (STAR) • International Aerospace Abstracts (IAA) Scientific and Technical Information Office • 1978. National Aeronautics and Space Administration Washington, DC This Supplement is available from the National Technical Information Service (NTIS), Springfield, Virginia 22161, at the price code E02 ($475 domestic, $9 50 foreign) INTRODUCTION Under the terms of an interagency agreement with the Federal Aviation Administration this publication has been prepared by the National Aeronautics and Space Administration for the joint use of both agencies and the scientific and technical community concerned with the field of aeronautical engineering. The first issue of this bibliography was published in September 1970 and the first supplement in January 1971. Since that time, monthly supplements have been issued. -
MARYLAND Orbital Mechanics
Orbital Mechanics • Orbital Mechanics, continued – Time in orbits – Velocity components in orbit – Deorbit maneuvers – Atmospheric density models – Orbital decay (introduction) • Fundamentals of Rocket Performance – The rocket equation – Mass ratio and performance – Structural and payload mass fractions – Multistaging – Optimal ΔV distribution between stages (introduction) U N I V E R S I T Y O F Orbital Mechanics © 2004 David L. Akin - All rights reserved Launch and Entry Vehicle Design MARYLAND http://spacecraft.ssl.umd.edu Calculating Time in Orbit U N I V E R S I T Y O F Orbital Mechanics MARYLAND Launch and Entry Vehicle Design Time in Orbit • Period of an orbit a3 P = 2π µ • Mean motion (average angular velocity) µ n = a3 • Time since pericenter passage M = nt = E − esin E ➥M=mean anomaly E=eccentric anomaly U N I V E R S I T Y O F Orbital Mechanics MARYLAND Launch and Entry Vehicle Design Dealing with the Eccentric Anomaly • Relationship to orbit r = a(1− e cosE) • Relationship to true anomaly θ 1+ e E tan = tan 2 1− e 2 • Calculating M from time interval: iterate Ei+1 = nt + esin Ei until it converges U N I V E R S I T Y O F Orbital Mechanics MARYLAND Launch and Entry Vehicle Design Example: Time in Orbit • Hohmann transfer from LEO to GEO – h1=300 km --> r1=6378+300=6678 km – r2=42240 km • Time of transit (1/2 orbital period) U N I V E R S I T Y O F Orbital Mechanics MARYLAND Launch and Entry Vehicle Design Example: Time-based Position Find the spacecraft position 3 hours after perigee E=0; 1.783; 2.494; 2.222; 2.361; 2.294; 2.328; -
Classifications of Time-Optimal Constant-Acceleration Earth-Mars Transfers
UC Irvine UC Irvine Electronic Theses and Dissertations Title Classifications of Time-Optimal Constant-Acceleration Earth-Mars Transfers Permalink https://escholarship.org/uc/item/4m6954st Author Campbell, Jesse Alexander Publication Date 2014 Peer reviewed|Thesis/dissertation eScholarship.org Powered by the California Digital Library University of California UNIVERSITY OF CALIFORNIA, IRVINE Classifications of Time-Optimal Constant-Acceleration Earth-Mars Transfers THESIS submitted in partial satisfaction of the requirements for the degree of MASTERS OF SCIENCE in Mechanical and Aerospace Engineering by Jesse A. Campbell Thesis Committee: Professor Kenneth D. Mease, Chair Professor Faryar Jabbari Professor Tammy Smecker-Hane 2014 c 2014 Jesse A. Campbell DEDICATION To my family, whose unwavering love and support has guided me through uncertain times my friends, whose unfailing encouragement inspires me to ever greater heights and to anyone else whose personal voyage it is to explore the cosmos. ii TABLE OF CONTENTS Page LIST OF FIGURES iv LIST OF TABLES vi ACKNOWLEDGMENTS vii ABSTRACT OF THE THESIS viii 1 Introduction 1 1.1 Problem Constraints . .2 1.1.1 Coplanar Circular Concentric Orbits . .2 1.1.2 Constant Acceleration . .3 1.1.3 Patched Conics Assumption . .4 2 Problem Formulation and Procedure 7 2.1 Optimal Control Formulation . .9 2.2 Initial Guess Generation Methods . 12 2.2.1 Analytic Solution for µ ≡ 0 ....................... 12 2.2.2 Linear Geometric Continuation (LGC) . 13 2.2.3 Difference Continuation (DC) . 19 2.2.4 Linearized Optimal Difference Continuation (LODC) . 21 3 Results and Classifications 24 3.1 Database Construction . 24 3.2 Database Filtering . 26 3.3 Branching Points . -
The Motion of a Rocket
Prepared for submission to JCAP The motion of a Rocket Salah Nasri aUnited Arab Emirates University, Al-Ain, UAE E-mail: [email protected] Abstract. These are my notes on some selected topics in undergraduate Physics. Contents 1 Introduction2 2 Types of Rockets2 3 Derivation of the equation of a rocket4 4 Optimizing a Single-Stage Rocket7 5 Multi-stages Rocket9 6 Optimizing Multi-stages Rocket 12 7 Derivation of the Exhaust Velocity of a Rocket 15 8 Rocket Design Principles 15 – 1 – 1 Introduction In 1903, Konstantin Tsiolkovsky (1857- 1935), a Russian Physicist and school teacher, published "The Exploration of Cosmic Space by Means of Reaction Devices", in which he presented all the basic equations for rocketry. He determined that liquid fuel rockets would be needed to get to space and that the rockets would need to be built in stages. He concluded that oxygen and hydrogen would be the most powerful fuels to use. He had predicted in general how, 65 years later, the Saturn V rocket would operate for the first landing of men on the Moon. Robert Goddard, an American university professor who is considered "the father of modern rocketry," designed, built, and flew many of the earliest rockets. In 1926 he launched the world’s first liquid fueled rocket. The German scientist Hermann Oberth independently arrived at the same rock- etry principles as Tsiolkovsky and Goddard. In 1929, he published a book entitled "By Rocket to Space", 1 that was internationally acclaimed and persuaded many that the rocket was something to take seriously as a space vehicle. -
Revolutionary Propulsion Concepts for Small Satellites
SSC01-IX-4 Revolutionary Propulsion Concepts for Small Satellites Steven R. Wassom, Ph.D., P.E. Senior Mechanical Engineer Space Dynamics Laboratory/Utah State University 1695 North Research Park Way North Logan, Utah 84341-1947 Phone: 435-797-4600 E-mail: [email protected] Abstract. This paper addresses the results of a trade study in which four novel propulsion approaches are applied to a 100-kg-class satellite designed for rendezvous, reconnaissance, and other on-orbit operations. The technologies, which are currently at a NASA technology readiness level of 4, are known as solar thermal propulsion, digital solid motor, water-based propulsion, and solid pulse motor. Sizing calculations are carried out using analytical and empirical parameters to determine the propellant and inert masses and volumes. The results are compared to an off- the-shelf hydrazine system using a trade matrix “scorecard.” Other factors considered besides mass and volume include safety, storability, mission time, accuracy, and refueling. Most of the concepts scored higher than the hydrazine system and warrant further development. The digital solid motor had the highest score by a small margin. Introduction propulsion concepts to a state-of-the-art (SOTA) hydrazine system, as applied to a notional 100-kg Aerospace America1 recently provided some interesting satellite designed for rendezvous with other objects. data on the number of payloads proposed for launch in the next 10 years. In the year 2000 there was a 68% Basic Description of Concepts increase in the number of proposed payloads weighing less than 100 kg, a 67% increase in the number of Solar Thermal Propulsion (STP) proposed military payloads, and a 92% increase in the number of proposed reconnaissance/surveillance Solar Thermal Propulsion (STP) uses the sun’s energy satellites. -
Technical Report on Different RLV Return Modes' Performances
Formation flight for in-Air Launcher 1st stage Capturing demonstration Technical Report on different RLV return modes’ Performances Deliverable D2.1 EC project number 821953 Research and Innovation action Space Research Topic: SPACE-16-TEC-2018 – Access to space FALCon Formation flight for in-Air Launcher 1st stage Capturing demonstration Technical Report on different RLV return modes’ Performances Deliverable Reference Number: D2.1 Due date of deliverable: 30th November 2019 Actual submission date (draft): 15th December 2019 Actual submission date (final version): 19th October 2020 Start date of FALCon project: 1st of March 2019 Duration: 36 months Organisation name of lead contractor for this deliverable: DLR Revision #: 2 Dissemination Level PU Public X PP Restricted to other programme participants (including the Commission Services) RE Restricted to a group specified by the consortium (including the Commission Services) CO Confidential, only for members of the consortium (including the Commission Services) APPROVAL Title issue revision Technical Report on different RLV return modes’ 2 1 performances Author(s) date Sven Stappert 19.10.2020 Madalin Simioana 21.07.2020 Martin Sippel Approved by Date Sven Stappert 19.10.2020 Martin Sippel FALCon D2.1: RLV Return Mode Performances vers. 19-Oct-20 Page i Contents List of Tables iii List of Figures iii Nomenclature vi 1 Executive Summary ......................................................................................... 1 1.1 Scope of the deliverable ............................................................................................ -
Financial Operational Losses in Space Launch
UNIVERSITY OF OKLAHOMA GRADUATE COLLEGE FINANCIAL OPERATIONAL LOSSES IN SPACE LAUNCH A DISSERTATION SUBMITTED TO THE GRADUATE FACULTY in partial fulfillment of the requirements for the Degree of DOCTOR OF PHILOSOPHY By TOM ROBERT BOONE, IV Norman, Oklahoma 2017 FINANCIAL OPERATIONAL LOSSES IN SPACE LAUNCH A DISSERTATION APPROVED FOR THE SCHOOL OF AEROSPACE AND MECHANICAL ENGINEERING BY Dr. David Miller, Chair Dr. Alfred Striz Dr. Peter Attar Dr. Zahed Siddique Dr. Mukremin Kilic c Copyright by TOM ROBERT BOONE, IV 2017 All rights reserved. \For which of you, intending to build a tower, sitteth not down first, and counteth the cost, whether he have sufficient to finish it?" Luke 14:28, KJV Contents 1 Introduction1 1.1 Overview of Operational Losses...................2 1.2 Structure of Dissertation.......................4 2 Literature Review9 3 Payload Trends 17 4 Launch Vehicle Trends 28 5 Capability of Launch Vehicles 40 6 Wastage of Launch Vehicle Capacity 49 7 Optimal Usage of Launch Vehicles 59 8 Optimal Arrangement of Payloads 75 9 Risk of Multiple Payload Launches 95 10 Conclusions 101 10.1 Review of Dissertation........................ 101 10.2 Future Work.............................. 106 Bibliography 108 A Payload Database 114 B Launch Vehicle Database 157 iv List of Figures 3.1 Payloads By Orbit, 2000-2013.................... 20 3.2 Payload Mass By Orbit, 2000-2013................. 21 3.3 Number of Payloads of Mass, 2000-2013.............. 21 3.4 Total Mass of Payloads in kg by Individual Mass, 2000-2013... 22 3.5 Number of LEO Payloads of Mass, 2000-2013........... 22 3.6 Number of GEO Payloads of Mass, 2000-2013.......... -
Gun-Launched Satellites
GUN-LAUNCHED SATELLITES Gun-Launched Satellites Harold E. Gilreath, Andrew S. Driesman, William M. Kroshl, Michael E. White, Harry E. Cartland, and John W. Hunter This article summarizes and updates a study conducted for the Defense Advanced Research Projects Agency concerning the technical and economic feasibility of using a distributed-injection, light-gas gun to launch small satellites. In principle, a distributed- injection launcher can produce high muzzle velocities at relatively low acceleration levels. The technical feasibility of such a launcher depends on the successful development of fast injector valves and high-temperature, high-pressure hydrogen heat exchangers. Thermal protection, aerodynamic stability, and packaging are significant, but not insurmountable, challenges in designing a launch vehicle that can withstand high-acceleration loads and survive hypersonic flight across the atmosphere. Although many spacecraft components are readily adapted to high g loads, the mass budget of a gun-launched spacecraft is affected substantially by large mass fraction allocations for structure and power subsystems. The results of a financial analysis suggest that a low- volume launch business might provide an attractive total mission cost relative to current systems. (Keywords: Light-gas gun, Small satellites, Space access.) INTRODUCTION Just a few years ago, space was the exclusive province between now and the year 2005, not including replace- of large national governments. Today, more than half ments for failed spacecraft. All of this activity and of international launches consist of commercial pay- planning is increasing the pressure to make space access loads. This rapidly developing space business promises simpler and less costly. Several research and develop- to be very competitive, especially in the telecommuni- ment programs have emerged to develop more econom- cations sector, where more than 20 concepts for low- ical rockets, mainly by emphasizing reusability.