From Ruthenium to Iron for the Catalytic Reduction of Ketones: Catalysis and Mechanistic Insights
Total Page:16
File Type:pdf, Size:1020Kb
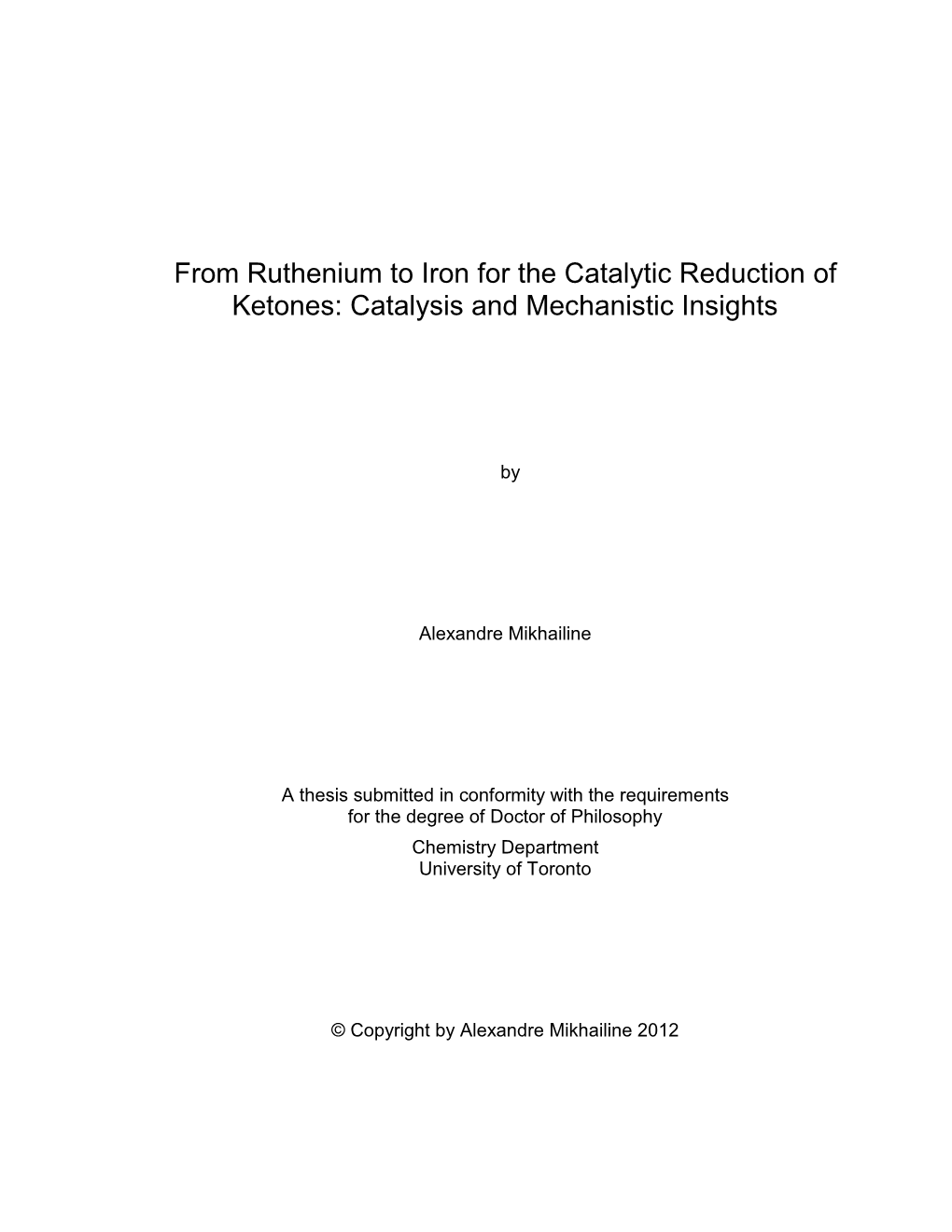
Load more
Recommended publications
-
Modern-Reduction-Methods.Pdf
Modern Reduction Methods Edited by Pher G. Andersson and Ian J. Munslow Related Titles Yamamoto, H., Ishihara, K. (eds.) Torii, S. Acid Catalysis in Modern Electroorganic Reduction Organic Synthesis Synthesis 2008 2006 ISBN: 978-3-527-31724-0 ISBN: 978-3-527-31539-0 Roberts, S. M. de Meijere, A., Diederich, F. (eds.) Catalysts for Fine Chemical Metal-Catalyzed Cross- Synthesis V 5 – Regio and Coupling Reactions Stereo-Controlled Oxidations 2004 and Reductions ISBN: 978-3-527-30518-6 2007 Online Book Wiley Interscience Bäckvall, J.-E. (ed.) ISBN: 978-0-470-09024-4 Modern Oxidation Methods 2004 de Vries, J. G., Elsevier, C. J. (eds.) ISBN: 978-3-527-30642-8 The Handbook of Homogeneous Hydrogenation 2007 ISBN: 978-3-527-31161-3 Modern Reduction Methods Edited by Pher G. Andersson and Ian J. Munslow The Editors All books published by Wiley-VCH are carefully produced. Nevertheless, authors, editors, and Prof. Dr. Pher G. Andersson publisher do not warrant the information Uppsala University contained in these books, including this book, to Department of Organic Chemistry be free of errors. Readers are advised to keep in Husargatan 3 mind that statements, data, illustrations, 751 23 Uppsala procedural details or other items may Sweden inadvertently be inaccurate. Dr. Ian J. Munslow Library of Congress Card No.: Uppsala University applied for Department of Biochemistry and Organic Chemistry Husargatan 3 British Library Cataloguing-in-Publication Data 751 23 Uppsala A catalogue record for this book is available from Sweden the British Library. Bibliographic information published by the Deutsche Nationalbibliothek Die Deutsche Nationalbibliothek lists this publication in the Deutsche Nationalbibliografi e; detailed bibliographic data are available on the Internet at <http://dnb.d-nb.de>. -
MODULAR PHOSPHINOOXAZOLINES: SYNTHESIS and EVALUATION in ALLYLIC SUBSTITUTIONS Dana Madeleine Popa ISBN:978-84-691-8862-0/DL:T-1275-2008
UNIVERSITAT ROVIRA I VIRGILI MODULAR PHOSPHINOOXAZOLINES: SYNTHESIS AND EVALUATION IN ALLYLIC SUBSTITUTIONS Dana Madeleine Popa ISBN:978-84-691-8862-0/DL:T-1275-2008 PhD Thesis MODULAR PHOSPHINOOXAZOLINES: SYNTHESIS AND EVALUATION IN ALLYLIC SUBSTITUTIONS Dana Madeleine Popa Tarragona, July 2008 UNIVERSITAT ROVIRA I VIRGILI MODULAR PHOSPHINOOXAZOLINES: SYNTHESIS AND EVALUATION IN ALLYLIC SUBSTITUTIONS Dana Madeleine Popa ISBN:978-84-691-8862-0/DL:T-1275-2008 UNIVERSITAT ROVIRA I VIRGILI MODULAR PHOSPHINOOXAZOLINES: SYNTHESIS AND EVALUATION IN ALLYLIC SUBSTITUTIONS Dana Madeleine Popa ISBN:978-84-691-8862-0/DL:T-1275-2008 Institut Catalá d’Investigació Química Memoria presentada por Dana Madeleine Popa para optar al título de Doctor por la Universitat Rovira i Virgili. Revisada por Dr. Anton Vidal Dr. Miquel A. Pericàs UNIVERSITAT ROVIRA I VIRGILI MODULAR PHOSPHINOOXAZOLINES: SYNTHESIS AND EVALUATION IN ALLYLIC SUBSTITUTIONS Dana Madeleine Popa ISBN:978-84-691-8862-0/DL:T-1275-2008 UNIVERSITAT ROVIRA I VIRGILI MODULAR PHOSPHINOOXAZOLINES: SYNTHESIS AND EVALUATION IN ALLYLIC SUBSTITUTIONS Dana Madeleine Popa ISBN:978-84-691-8862-0/DL:T-1275-2008 El presente trabajo de investigación ha sido realizado en el Institut Català d`Investigació Química, bajo la dirección de Dr. Anton Vidal y al Dr. Miquel A. Pericàs, a quienes les quiero dar las gracias por la oportunidad que me han ofrecido de formarme como investigadora bajo su supervisión. Quiero agradecer a Dr. Anton Vidal por los consejos y ayuda que me ha ofrecido día a día. Agradezco a Dr. Miquel A. Pericàs por el soporte que me ha proporcionado en todo el momento. Quiero agradecer también a Sergi Rodríguez Escrich por su colaboración en una parte del trabajo de investigación realizado. -
N-Heterocyclic Carbene Ligands for Iridium- Catalysed Asymmetric Hydrogenation
N-Heterocyclic Carbene Ligands for Iridium- Catalysed Asymmetric Hydrogenation Inauguraldissertation zur Erlangung der Würde eines Doktors der Philosophie vorgelegt der Philosophisch-Naturwissenschaftlichen Fakultät der Universität Basel von Steve Nanchen aus Lens / Schweiz Basel 2005 Genehmigt von der Philosophisch-Naturwissenschaftlichen Fakultät auf Antrag von: Prof. Dr. Andreas Pfaltz Prof. Dr. Wolf-Dietrich Woggon Basel, den 20. September 2005 Prof. Dr. Hans-Jakob Wirz Dekan to my wife Annik Acknowledgments I thank Professor Andreas Pfaltz to have given me the opportunity of joining his group, for his help and constant support over the last four years. I also thank Professor Wolf-Dietrich Woggon who agreed to co-examine this thesis. Dr. Valentin Köhler, Dr. William Drury III, Dr. Geoffroy Guillemot and Dr. Benoît Pugin, Solvias AG, are acknowledged for helpful discussions and fruitful collaboration. I am grateful to Markus Neuburger and Dr. Silvia Schaffner for recording numerous X-ray data and for refining X-ray structures. Dr. Klaus Kulicke, Axel Franzke and Dr. Clément Mazet are acknowledged for their countless hours recording 2D NMR spectra and their help on interpretation of data. I thank Björn Gschwend, Dominik Frank and Peter Sommer for their laboratory work contributions. Thanks to Dr. Cara Humphrey, Dr. Geoffroy Guillemot and Dr. Yann Ribourdouille for proof-reading the manuscript. A special thanks goes to the members of the Pfaltz group who have made my stay in Basel an enjoyable time. Thanks to lab 204 for the nice working atmosphere. A big thanks to my friends and family. Their help and presence during these four years was invaluable. Finally, thanks to Annik for all her support and love. -
Sulfenylphosphinoferrocenes: Novel Planar Chiral Ligands in Enantioselective Catalysis*
Pure Appl. Chem., Vol. 78, No. 2, pp. 257–265, 2006. doi:10.1351/pac200678020257 © 2006 IUPAC Sulfenylphosphinoferrocenes: Novel planar chiral ligands in enantioselective catalysis* Silvia Cabrera, Olga García Mancheño, Ramón Gómez Arrayás, Inés Alonso, Pablo Mauleón, and Juan C. Carretero‡ Departamento de Química Orgánica, Facultad de Ciencias, Universidad Autónoma de Madrid, 28049 Madrid, Spain Abstract: Structurally well-defined transition-metal complexes of 1-phosphino-2-sulfenyl- ferrocene (Fesulphos ligands) act as highly efficient catalysts in a variety of mechanistically different transformations. Excellent enantioselectivities were achieved in Pd-catalyzed allylic substitutions, desymmetrization of meso-heterobicyclic alkenes by Pd-catalyzed addition of dialkylzinc reagents, Pd-catalyzed Diels–Alder reaction of cyclopentadiene with N-acryloyl oxazolidinones, and in Cu-catalyzed formal aza-Diels–Alder reaction of Danishefsky diene to N-sulfonyl aldimines. Keywords: sulfenylphosphinoferrocenes; Fesulphos; enantioselective; Pd-catalyzed; allylic substitutions; desymmetrization; Danishefsky diene; N-sulfonyl aldimines; Cu-catalyzed. INTRODUCTION Two main structural concepts have proved to be greatly successful in the design of chiral ligands for asymmetric catalysis: The reduction of the possible diastereomeric transition states by using bidentate C2-symmetrical P/P, N/N, or O/O chiral ligands (e.g., BINAP, bisoxazolines, salen, or BINOL-based ligands) and the use of mixed bidentated ligands equipped with strong and weak donor heteroatom pairs [1]. This second strategy takes advantage of the different electronic properties associated with each heteroatom-metal bond (e.g., the trans influence) which, playing in combination with appropriate steric effects around the metal-coordinating heteroatoms, can create an asymmetric environment capable of inducing high levels of enantiocontrol. Some bidentate P/N chiral ligands such as phosphine–oxazoline systems and QUINAP constitute excellent examples of this strategy [2]. -
Nitrogen-Based Ligands : Synthesis, Coordination Chemistry and Transition Metal Catalysis
Nitrogen-based ligands : synthesis, coordination chemistry and transition metal catalysis Citation for published version (APA): Caipa Campos, M. A. (2005). Nitrogen-based ligands : synthesis, coordination chemistry and transition metal catalysis. Technische Universiteit Eindhoven. https://doi.org/10.6100/IR594547 DOI: 10.6100/IR594547 Document status and date: Published: 01/01/2005 Document Version: Publisher’s PDF, also known as Version of Record (includes final page, issue and volume numbers) Please check the document version of this publication: • A submitted manuscript is the version of the article upon submission and before peer-review. There can be important differences between the submitted version and the official published version of record. People interested in the research are advised to contact the author for the final version of the publication, or visit the DOI to the publisher's website. • The final author version and the galley proof are versions of the publication after peer review. • The final published version features the final layout of the paper including the volume, issue and page numbers. Link to publication General rights Copyright and moral rights for the publications made accessible in the public portal are retained by the authors and/or other copyright owners and it is a condition of accessing publications that users recognise and abide by the legal requirements associated with these rights. • Users may download and print one copy of any publication from the public portal for the purpose of private study or research. • You may not further distribute the material or use it for any profit-making activity or commercial gain • You may freely distribute the URL identifying the publication in the public portal. -
Selective Catalysis by Polymer-Supported Ruthenium
Brigham Young University BYU ScholarsArchive All Theses and Dissertations 2019-03-01 Selective Catalysis by Polymer-Supported Ruthenium NanoparticlesAND New Ligand Design for Cooperative and Bimetallic Catalysis Seyed Hadi Nazari Brigham Young University Follow this and additional works at: https://scholarsarchive.byu.edu/etd BYU ScholarsArchive Citation Nazari, Seyed Hadi, "Selective Catalysis by Polymer-Supported Ruthenium NanoparticlesAND New Ligand Design for Cooperative and Bimetallic Catalysis" (2019). All Theses and Dissertations. 7386. https://scholarsarchive.byu.edu/etd/7386 This Dissertation is brought to you for free and open access by BYU ScholarsArchive. It has been accepted for inclusion in All Theses and Dissertations by an authorized administrator of BYU ScholarsArchive. For more information, please contact [email protected], [email protected]. Selective Catalysis by Polymer-Supported Ruthenium Nanoparticles AND New Ligand Design for Cooperative and Bimetallic Catalysis Seyed Hadi Nazari A dissertation submitted to the faculty of Brigham Young University in partial fulfillment of the requirements for the degree of Doctor of Philosophy David J. Michaelis, Chair Steven L. Castle Joshua L. Price Daniel H. Ess Roger G. Harrison Department of Chemistry and Biochemistry Brigham Young University Copyright © 2019 Seyed Hadi Nazari All Rights Reserved ABSTRACT Selective Catalysis by Polymer-Supported Ruthenium Nanoparticles AND New Ligand Design for Cooperative and Bimetallic Catalysis Seyed Hadi Nazari Department of Chemistry and Biochemistry, BYU Doctor of Philosophy The abstract is the summary of three different projects all centered around the general idea of catalysis which is the general theme of research in the Michaelis laboratory. The first project focuses on development of a new heterogeneous catalyst for selective catalysis. -
Palladium‑Catalyzed Alkylation of Alkenes Using Epoxides. Part II: Palladium‑Catalyzed Asymmetric Wacker‑Type Anti‑Attack of Alkenes
This document is downloaded from DR‑NTU (https://dr.ntu.edu.sg) Nanyang Technological University, Singapore. Part I: Palladium‑catalyzed alkylation of alkenes using epoxides. Part II: Palladium‑catalyzed asymmetric wacker‑type anti‑attack of alkenes Teng, Shenghan 2020 Teng, S. (2020). Part I: Palladium‑catalyzed alkylation of alkenes using epoxides. Part II: Palladium‑catalyzed asymmetric wacker‑type anti‑attack of alkenes. Doctoral thesis, Nanyang Technological University, Singapore. https://hdl.handle.net/10356/146048 https://doi.org/10.32657/10356/146048 This work is licensed under a Creative Commons Attribution‑NonCommercial 4.0 International License (CC BY‑NC 4.0). Downloaded on 08 Oct 2021 15:05:54 SGT PART I: PALLADIUM-CATALYZED ALKYLATION OF ALKENES USING EPOXIDES PART II: PALLADIUM-CATALYZED ASYMMETRIC WACKER-TYPE ANTI-ATTACK OF ALKENES TENG SHENGHAN SCHOOL OF PHYSICAL AND MATHEMATICAL SCIENCES 2020 PART I: PALLADIUM-CATALYZED ALKYLATION OF ALKENES USING EPOXIDES PART II: PALLADIUM-CATALYZED ASYMMETRIC WACKER-TYPE ANTI-ATTACK OF ALKENES TENG SHENGHAN SCHOOL OF PHYSICAL AND MATHEMATICAL SCIENCES A thesis submitted to the Nanyang Technological University in partial fulfilment of the requirement for the degree of Doctor of Philosophy 2020 Statement of Originality I hereby certify that the work embodied in this thesis is the result of original research done by me except where otherwise stated in this thesis. The thesis work has not been submitted for a degree or professional qualification to any other university or institution. I declare that this thesis is written by myself and is free of plagiarism and of sufficient grammatical clarity to be examined. I confirm that the investigations were conducted in accord with the ethics policies and integrity standards of Nanyang Technological University and that the research data are presented honestly and without prejudice. -
Proofreading Experimentally Assigned Stereochemistry Through Q2MM Predictions in Pd- Catalyzed Allylic Aminations
Proofreading Experimentally Assigned Stereochemistry Through Q2MM Predictions in Pd- Catalyzed Allylic Aminations Jessica Wahlers University of Notre Dame Jessica Margalef Stockholm University https://orcid.org/0000-0003-2387-2154 Eric Hansen University of Notre Dame Armita Bayesteh AstraZeneca Paul Helquist University of Notre Dame https://orcid.org/0000-0003-4380-9566 Montserrat Diéguez Rovira i VirgiliUniversity Oscar Pàmies Universitat Rovira i Virgili Olaf Wiest University of Notre Dame https://orcid.org/0000-0001-9316-7720 Per-Ola Norrby ( [email protected] ) AstraZeneca https://orcid.org/0000-0002-2419-0705 Article Keywords: stereochemistry, catalysis, organic chemistry, ligand/substrate combinations Posted Date: June 4th, 2021 DOI: https://doi.org/10.21203/rs.3.rs-579343/v1 License: This work is licensed under a Creative Commons Attribution 4.0 International License. Read Full License Page 1/14 Abstract The palladium-catalyzed enantioselective allylic substitution by carbon or nitrogen nucleophiles is a key transformation that is particularly useful for the synthesis of bioactive compounds. Unfortunately, the selection of a suitable ligand/substrate combination often requires signicant screening effort. Here, we show that a transition state force eld (TSFF) derived by the quantum-guided molecular mechanics (Q2MM) method can be used to rapidly screen ligand/substrate combinations. Testing of this method on 77 literature reactions revealed several cases where the computationally predicted major enantiomer differed -
1 Introduction
University of Huddersfield Repository Walton, Scarlett Maria Catalytic Functionalisation of sp3 Bonds Original Citation Walton, Scarlett Maria (2017) Catalytic Functionalisation of sp3 Bonds. Doctoral thesis, University of Huddersfield. This version is available at http://eprints.hud.ac.uk/id/eprint/34344/ The University Repository is a digital collection of the research output of the University, available on Open Access. Copyright and Moral Rights for the items on this site are retained by the individual author and/or other copyright owners. Users may access full items free of charge; copies of full text items generally can be reproduced, displayed or performed and given to third parties in any format or medium for personal research or study, educational or not-for-profit purposes without prior permission or charge, provided: • The authors, title and full bibliographic details is credited in any copy; • A hyperlink and/or URL is included for the original metadata page; and • The content is not changed in any way. For more information, including our policy and submission procedure, please contact the Repository Team at: [email protected]. http://eprints.hud.ac.uk/ CATALYTIC FUNCTIONALISATION OF SP3 BONDS Scarlett Maria Walton A thesis submitted to the University of Huddersfield in partial fulfilment of the requirements for the degree of Doctor of Philosophy The University of Huddersfield September 2017 Word Count: 33061 Copyright statement i. The author of this thesis (including any appendices and/or schedules to this thesis) owns any copyright in it (the “Copyright”) and s/he has given The University of Huddersfield the right to use such copyright for any administrative, promotional, educational and/or teaching purposes. -
Novel Chiral Chemistries Japan 2009 Pgms RETAIN THEIR PIVOTAL ROLE in ASYMMETRIC CATALYSIS
DOI: 10.1595/147106709X474226 Novel Chiral Chemistries Japan 2009 PGMs RETAIN THEIR PIVOTAL ROLE IN ASYMMETRIC CATALYSIS Reviewed by David J. Ager DSM, PMB 150, 9650 Strickland Road, Suite 103, Raleigh, NC 27615, U.S.A.; E-mail: [email protected] The third Novel Chiral Chemistries Japan simultaneous use of bio- and chemocatalysis to (NCCJapan) Conference and Exhibition was held enable dynamic kinetic resolutions (DKR) to be in Tokyo on 18th and 19th April 2009 (1). The sec- carried out. The initial work was performed with ond meeting had been held in 2007 (2) and the first secondary alcohols. The readily available enzyme, in 2006. All meetings in the series have followed a Candida antarctica lipase B (CALB) (Novozym® similar format, with keynote addresses and sup- 435), which is derived from a yeast, is used to acy- porting lectures, although this time there were late one enantiomer of a secondary alcohol. A some dual presentations in which two speakers ruthenium catalyst then racemises the unreacted from the same company gave complementary talks enantiomer. Initially the Shvo catalyst, 1, was used on slightly different topics within a single time slot. but the racemisation is slow and requires heating to Professor Takao Ikariya (Tokyo Institute of give acceptable reaction rates. Use of the Technology, Japan) and his team, in particular monomeric ruthenium catalyst 2 provides faster Kyoko Suzuki, must be congratulated for the reactions, even at ambient temperatures. excellent job they did to ensure that the conference ran smoothly. As in previous meetings, Professor Ph O O Ph Ikariya put together an exciting mix of speakers H from both academia and industry across the world. -
Inorganic and Coordination Chemistry559595
INORGANIC AND COORDINATION CHEMISTRY559595 doi:10.2533/chimia.2008.595 CHIMIA 2008, 62,No. 7/8 Minisymposium Inorganic and Coordination Chemistry 149 Minisymposium Inorganic and Coordination Chemistry 150 Playing with anions: 1) Fast, environmentally friendlyruthenium- Reticular Chemistry allylation catalystsand 2) Understandingand predicting ion pairing. Omar M. Yaghi Paul S. Pregosin University of California, Los Angeles (UCLA) 607 Charles E. Young Dr. East Los Angeles,CA90095-1569 USA ETH Zurich, 8093Zurich, Switzerland This chemistryisconcernedwithlinkingorganicand inorganic molecular The lecture will consist of two separate but related themes. The opening building units into extended structures usingstrong bonds. These structures section will involve ashort excursioninto how one can synthesize new, and arecrystalline andhaveframeworks in which the inorganic units act as optimize old, rutheniumbased homogeneous allylation catalystssuch that ‘joints’ and the organicunits as ‘struts’ to produce highly porous and robust they are rapid, environmentally friendly and demonstrate exceptional metal-organic frameworks (MOFs) andzeolitic imidazolate frameworks regioselectivity,and then finish with an NMR approach designed to show (ZIFs). This presentationwill outline asimpledesign strategyand synthesis howtorecognize, understand and even predict the extent of ion pairing in a of these materials including their adsorptiveproperties and applicationsto wide variety of inorganic, organic and organometallic salts. clean energy. Inorganic and Coordination -
Nitrogen-Containing Ligands for Asymmetric Homogeneous and Heterogeneous Catalysis
Chem. Rev. 2000, 100, 2159−2231 2159 Nitrogen-Containing Ligands for Asymmetric Homogeneous and Heterogeneous Catalysis Fabienne Fache, Emmanuelle Schulz, M. Lorraine Tommasino, and Marc Lemaire* Laboratoire de Catalyse et Synthe`se Organique, UMR 5622, UCBL, CPE, 43 Bd du 11 Novembre 1918, 69622 Villeurbanne Cedex, France Received December 2, 1999 Contents VIII.4.1. Diels−Alder Reactions 2198 VIII.4.2. 1,3-Dipolar Cycloadditions 2203 I. Introduction 2159 VIII.5. Addition of Nucleophiles to CdC Bonds 2204 II. C−H Bond Formation 2161 VIII.5.1. Michael Additions 2204 II.1. Hydrogen as Reducing Agent 2161 VIII.5.2. Free Radical Conjugate Additions 2206 II.1.1. Homogeneous Systems 2162 VIII.6. Hydroformylation 2206 II.1.2. Heterogeneous Systems 2164 VIII.6.1. Regioselective Hydroformylation 2207 II.2. Borohydride and Other Inorganic Hydrides as 2165 Reducing Agents VIII.6.2. Enantioselective Hydroformylation 2207 II.2.1. Homogeneous Systems 2166 VIII.7. Carbonylation 2208 II.2.2. Heterogeneous Systems 2168 VIII.8. Grignard Cross-Coupling 2210 − II.3. Hydride Transfer Reduction 2169 VIII.9. Carbene Insertion into C H Bonds 2210 d II.3.1. Homogeneous Systems 2169 VIII.10. Addition to C O Bonds 2212 II.3.2. Heterogeneous Systems 2171 VIII.10.1. Aldol Reactions 2212 II.4. Hydrosilylation 2172 VIII.10.2. Nucleophilic Addition of Dialkylzinc 2215 III. C−O Bond Formation 2173 Reagents III.1. Epoxidation of Unfunctionalized Olefins 2173 VIII.10.3. Trimethylsilylcyanation 2218 III.1.1. Homogeneous Catalysis 2173 VIII.10.4. Ene Reaction 2220 d III.1.2. Heterogeneous System 2176 VIII.11.