En Aw-2024 Wrought Aluminum Alloy Processed by Casting with Crystallization Under Pressure
Total Page:16
File Type:pdf, Size:1020Kb
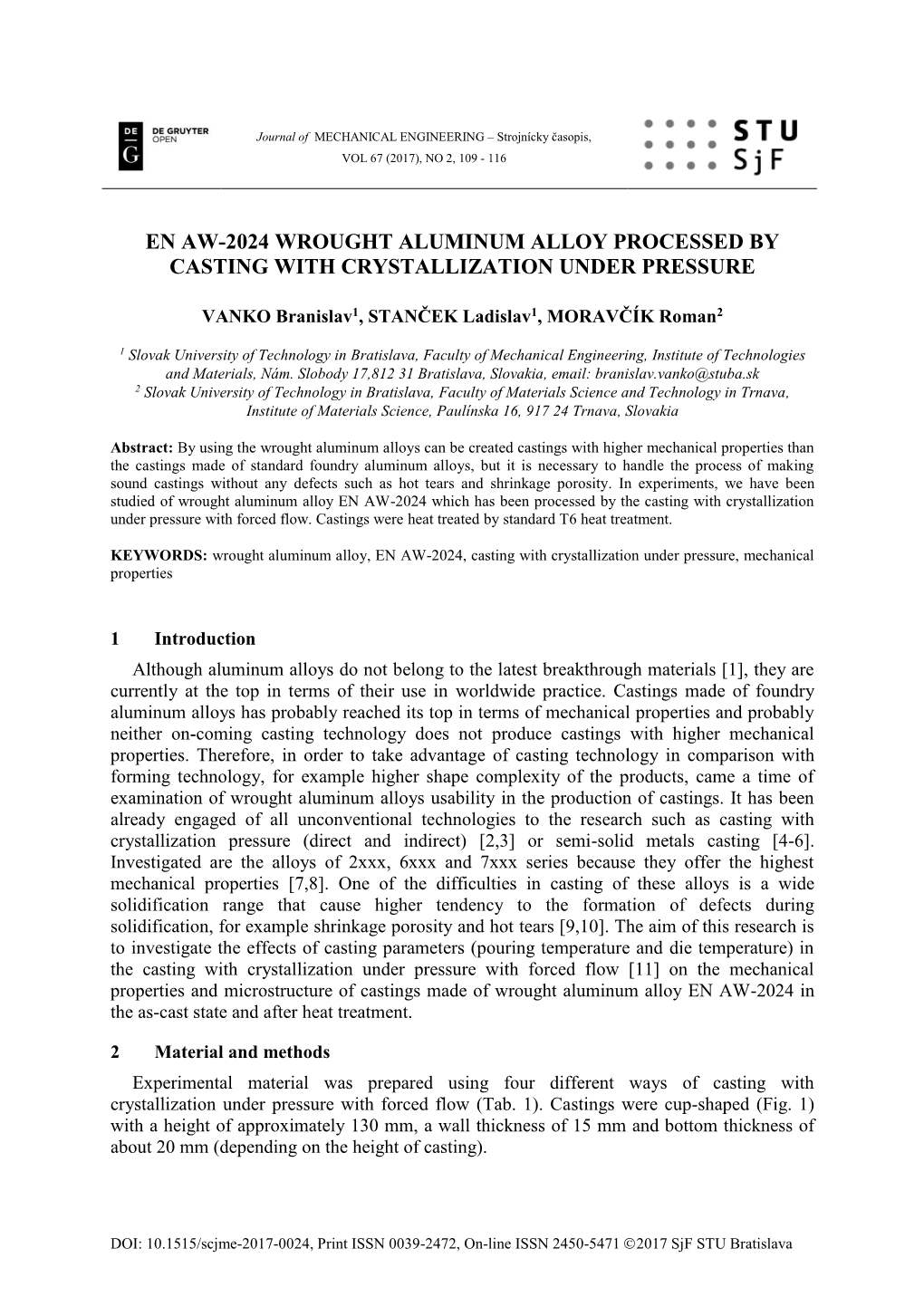
Load more
Recommended publications
-
Stress Corrosion Cracking of Friction Stir-Welded AA-2024 T3 Alloy
materials Article Stress Corrosion Cracking of Friction Stir-Welded AA-2024 T3 Alloy Marina Cabrini 1,2,3 , Sara Bocchi 4 , Gianluca D’Urso 4, Claudio Giardini 4 , Sergio Lorenzi 1,2,3,* , Cristian Testa 1,2,3 and Tommaso Pastore 1,2,3 1 Department of Engineering and Applied Sciences, University of Bergamo, 24044 Dalmine (BG), Italy; [email protected] (M.C.); [email protected] (C.T.); [email protected] (T.P.) 2 National Interuniversity Consortium of Materials Science and Technology (INSTM) Research Unit of Bergamo, 24044 Dalmine (BG), Italy 3 Center for Colloid and Surface Science (CSGI) Research Unit of Bergamo, 24044 Dalmine (BG), Italy 4 Information and Production Engineering, Department of Management, University of Bergamo, 24044 Dalmine (BG), Italy; [email protected] (S.B.); [email protected] (G.D.); [email protected] (C.G.) * Correspondence: [email protected] Received: 2 May 2020; Accepted: 3 June 2020; Published: 8 June 2020 Abstract: The paper is devoted to the study of stress corrosion cracking phenomena in friction stir welding AA-2024 T3 joints. Constant load (CL) cell and slow strain rate (SSR) tests were carried out in aerated NaCl 35 g/L solution. During the tests, open circuit potential (OCP) and electrochemical impedance spectroscopy (EIS) were measured in the different zones of the welding. The results evidenced initial practical nobilty of the nugget lower compared to both heat-affected zone and the base metal. This effect can be mainly ascribed to the aluminum matrix depletion in copper, which precipitates in form of copper-rich second phases. -
Effect of Post Weld Heat Treatment on Aluminium Alloys
ISSN(Online): 2319-8753 ISSN (Print): 2347-6710 International Journal of Innovative Research in Science, Engineering and Technology (A High Impact Factor, Monthly, Peer Reviewed Journal) Visit: www.ijirset.com Vol. 7, Issue 12, December 2018 Effect of Post Weld Heat Treatment on Aluminium Alloys Sanket V Bhosale1, Vijay J Dhembare2, Jaydeep M Khade3, Department of Production Engineering, D Y Patil College of Engineering, Akurdi, Pune, India1,2,3 ABSTRACT:In this paper, the effect of post-weld heat treatment (PWHT) on mechanical properties and change in microstructure of friction stir welded 2024 and 7075 aluminum alloys are studied. Solution heat treatment and various ageing treatments were given to the welded joints. The PWHT procedures caused abnormal coarsening of the grains in the weld zone, which resulted in a drop in micro-hardness at the weld zone compared to the base material of the joints. Another objective of this work is to study effect of Post Weld Heat Treatment on hardness and tensile properties of material. To gate optimum result, hardness and tensile properties of parent material, welded material and heat treated material is compared. Vickers micro hardness test is used to study hardness of samples. KEYWORDS: Friction Stir Welding, Microstructure, aluminium, heat treatment. I. INTRODUCTION Today aluminium alloys are widely used in many manufacturing areas like aerospace, railways, military and automobile sector. Aluminium has low density and good mechanical properties as compared to other metals. Welding is widely used method for joining the alloys of aluminium. But welding of aluminium alloy is big challenge for designers because of oxide layer cavity and hot cracking sensitivity of aluminium alloy. -
Corrosion Behavior of 2024 Aluminum Alloys Structure Produced by Wire Arc Additive Manufacture
Corrosion Behavior of 2024 Aluminum Alloys Structure produced by Wire Arc Additive Manufacture A dissertation submitted to the University of the Manchester for the degree of MSc by Research In the Faculty of Engineering and Physical Sciences 2017 SIHAN TAN School of Materials Corrosion and Protection Centre Table of Contents List of figures ............................................................................................................................. 3 List of tables .............................................................................................................................. 5 Abstract ..................................................................................................................................... 6 Declaration .................................................................................................................................... 7 Copyright Statement ..................................................................................................................... 8 Acknowledgement ........................................................................................................................ 9 1 Introduction ........................................................................................................................ 10 2 Literature review ................................................................................................................. 12 2.1 History of AM ............................................................................................................. -
Influence of the Microstructure on the Corrosion Behaviour of 2024 Aluminium Alloy Coated with a Trivalent Chromium Conversion Layer
OATAO is an open access repository that collects the work of Toulouse researchers and makes it freely available over the web where possible This is an author’s version published in: http://oatao.univ-toulouse.fr/21412 Official URL: https://doi.org/10.1016/j.corsci.2018.07.007 To cite this version: Saillard, Romain and Viguier, Bernard and Odemer, Grégory and Pugliara, Alessandro and Fori, Benoit and Blanc, Christine Influence of the microstructure on the corrosion behaviour of 2024 aluminium alloy coated with a trivalent chromium conversion layer. (2018) Corrosion Science, 142. 119-132. ISSN 0010-938X Any correspondence concerning this service should be sent to the repository administrator: [email protected] Influence of the microstructure on the corrosion behaviour of 2024 aluminium alloy coated with a trivalent chromium conversion layer ⁎ R. Saillarda, B. Viguiera, G. Odemera, A. Pugliaraa, B. Forib, C. Blanca, a CIRIMAT, Université de Toulouse, CNRS, INP-ENSIACET, 4 allée Emile Monso, BP 44362, 31030 Toulouse Cedex 4, France b MECAPROTEC Industries, 34 Boulevard de Joffrery, BP 30204, 31605 Muret Cedex, France ARTICLEINFO ABSTRACT Keywords: The influence of 2024 aluminium alloy microstructure on the protective properties of trivalent chromium A. Aluminium process (TCP) coatings was studied: samples aged at 190 °C were analysed by comparison to a T3 state. The A. Copper surface Cu coverage after deoxidation was higher for long-aged samples because nanometer scale Cu-rich pre- A. Intermetallics cipitates formed during ageing behaved as distinct electrochemical entities and contributed to the formation of A. Metal coatings copper deposits. The growth mechanisms and kinetics of TCP coatings were directly related to the surface Cu B. -
Durability and Corrosion of Aluminium and Its Alloys: Overview, Property Space, Techniques and Developments
Chapter 2 Durability and Corrosion of Aluminium and Its Alloys: Overview, Property Space, Techniques and Developments N. L. Sukiman, X. Zhou, N. Birbilis, A.E. Hughes, J. M. C. Mol, S. J. Garcia, X. Zhou and G. E. Thompson Additional information is available at the end of the chapter http://dx.doi.org/10.5772/53752 1. Introduction Aluminium (Al) is an important structural engineering material, its usage ranking only behind ferrous alloys (Birbilis, Muster et al. 2011). The growth in usage and production of Al continues to increase (Davis 1999). The extensive use of Al lies in its strength:density ratio, toughness, and to some degree, its corrosion resistance. From a corrosion perspec‐ tive, which is most relevant to this chapter, Al has been a successful metal used in a num‐ ber of applications from commodity roles, to structural components of aircraft. A number of Al alloys can be satisfactorily deployed in environmental/atmospheric conditions in their conventional form, leaving the corrosion protection industry to focus on market needs in more demanding applications (such as those which require coating systems, for example, the aerospace industry). Relatively pure aluminium presents good corrosion resistance due to the formation of a bar‐ rier oxide film that is bonded strongly to its surface (passive layer) and, that if damaged, re- forms immediately in most environments; i.e. re-passivation (Davis 1999). This protective oxide layer is especially stable in near-neutral solutions of most non-halide salts leading to excellent pitting resistance. Nevertheless, in open air solutions containing halide ions, with Cl- being the most common, aluminium is susceptible to pitting corrosion. -
Effect of Actual and Accelerated Ageing on Microstructure Evolution and Mechanical Properties of a 2024-T351 Aluminium Alloy
View metadata, citation and similar papers at core.ac.uk brought to you by CORE provided by Open Archive Toulouse Archive Ouverte Open Archive Toulouse Archive Ouverte (OATAO) OATAO is an open access repository that collects the work of Toulouse researchers and makes it freely available over the web where possible. This is an author-deposited version published in: http://oatao.univ-toulouse.fr/ Eprints ID: 18653 To link to this article: DOI:10.1016/j.ijfatigue.2017.10.015 URL: http://dx.doi.org/10.1016/j.ijfatigue.2017.10.015 To cite this version: Prudhomme, Manida and Billy, François and Alexis, Joël and Benoit, Guillaume and Hamon, Florence and Larignon, Céline and Odemer, Grégory and Blanc, Christine and Hénaff, Gilbert Effect of actual and accelerated ageing on microstructure evolution and mechanical properties of a 2024-T351 aluminium alloy. (2018) International Journal of Fatigue, vol. 107. pp. 60-71. ISSN 0142-1123 Any correspondence concerning this service should be sent to the repository administrator: [email protected] Effect of actual and accelerated ageing on microstructure evolution and mechanical properties of a 2024-T351 aluminium alloy M. Prudhommea,b, F. Billya, J. Alexisc, G. Benoita, F. Hamona, C. Larignonb, G. Odemerb, C. Blancb and G. Hénaffa, * a Pprime Institute, UPR 3346 CNRS-ENSMA-Université de Poitiers, ISAE-ENSMA, 1 avenue Clément Ader, 86961 Futuroscope Chasseneuil, France b CIRIMAT, Université de Toulouse, CNRS, INPT, UPS, ENSIACET, 4, allée Emile Monso BP 44362, 31030 Toulouse Cedex 4, France c LGP, ENIT, 47 avenue d'Azereix - BP 1629 - 65016 Tarbes CEDEX, France Abstract Due to the increasing number of civil transport aircrafts that come close to the end of the initial design life, airliners as well as aircraft manufacturers have to face different challenges. -
1. Introduction 2. Materials and Experimental Procedure Effect Of
Materials Research. 2015; 18(2): 328-333 © 2015 DOI: http://dx.doi.org/10.1590/1516-1439.307414 Effect of Quenching Rate and Pre-strain on the Strain Ageing Behaviors of 7075 Aluminum Alloys Ramazan Kaçara*, Kemal Güleryüzb aTechnology Faculty, Manufacturing Engineering Department, Karabük University, 78050, Yüzüncüyıl, Karabük, Turkey bTechnical Education Faculty, Karabuk University, 78050, Yüzüncüyıl, Karabuk, Turkey Received: July 7, 2014; Revised: March 9, 2015 The mechanical properties of aluminum alloys are strongly dependent on the thermo-mechanical process so, the strain ageing behavior of 7075 Al-alloy was investigated in this study. A set of test pieces was solution heat treated at 480 °C for 2 h, water quenched (SHTWQ) then pre-strained for 8% in tension. The test samples were aged at 140 °C for 0.5, 1, 2, 3, 4, 6, 8, 10, 12, 24, 48, 72 and 96 h in a furnace. The other set of test samples were solution heat treated at 480 °C for 2 h, quenched in sand (SHTSQ) then pre-strained for 8% in tension. They were also aged at 140 °C for same intervals. The effect of strain ageing, on the mechanical properties of Al-alloy, was investigated by mean of hardness, and tensile tests. The results shown that, the quenching rate after solution heat treatment, ageing time and temperature, as well as pre-strain, play a very important role in the precipitation- hardening associated with ageing process of the 7075 Al-alloy. Keywords: static strain ageing, Al-alloys, pre-strain, quenching rate, ageing time 1. Introduction 2. Materials and Experimental Procedure 7000 series aluminum alloys have been widely used for The T6 heat treated commercially available 7075 Al-alloy aeronautical applications due to their desirable mechanical used in this study is a plate with a thickness of 10 mm. -
Improved Selective Laser Melting Processing of Aluminium-Silicon
IMPROVED SELECTIVE LASER MELTING PROCESSING OF ALUMINIUM-SILICON-MAGNESIUM ALLOYS Thesis submitted in accordance with the requirements of The University of Liverpool for the degree of Doctor in Philosophy By Donal Lynch February 2019 Abstract This thesis details the investigation of the cracking phenomenon of aluminium alloy AA6061 processed by Selective Laser Melting (SLM) and proposes a modified alloy composition which was proven to eliminate cracking. High strength aluminium alloys are of commercial interest to the aerospace and automotive industries, in order to manufacture lightweight structural components. Current alloys that are regarded as processable through SLM are compromised by low strength, high cost or weight and this has led to an increased interest in developing high-medium strength aluminium alloys specifically for the SLM process. A thorough literature review was conducted to consider how different aluminium systems may perform when processed through SLM and subsequent heat treatments. From this, it was evident that alloys that can achieve appropriate mechanical properties are susceptible to cracking during the SLM process. AA6061 is an alloy within this category and it was selected for investigation due to its suitable mechanical properties, general use and availability in powder form. The potential sources of cracking are addressed in the literature review and a solution was proposed based on welding practices of AA6061. A powder blend of AA6061 powder and AlSi10Mg was made and processed by SLM. This imitates the practice of welding AA6061 with an Al-Si eutectic filler material. The blend ratio was selected to effectively adjust the silicon content of AA6061 by 1% and reflects the cracking susceptibility of binary Al-Mg2Si and Al-Si alloys. -
Effect of Microstructure and Mechanical Properties of Friction Stir Welded Dissimilar Aa5083-Aa6061 Aluminium Alloy Joints
IJRET: International Journal of Research in Engineering and Technology eISSN: 2319-1163 | pISSN: 2321-7308 EFFECT OF MICROSTRUCTURE AND MECHANICAL PROPERTIES OF FRICTION STIR WELDED DISSIMILAR AA5083-AA6061 ALUMINIUM ALLOY JOINTS Buddi Manohar1, Satishkumar. P2, Aruri Devaraju3 1Student (PG), Department of Mechanical Engineering, SR Engineering College, Ananthasagar, Warangal T.S. – 506 371, India 2Associate professor, Department of Mechanical Engineering, SR Engineering College, Ananthasagar, Warangal T.S. – 506 371, India 3Assistant professor, Department of Mechanical Engineering, SR Engineering College, Ananthasagar, Warangal T.S. – 506 371, India Abstract Friction Stir Welding (FSW) is a solid state welding process. In particular, it can be used to join high-strength aerospace aluminum and other metallic alloys that are hard to weld by conventional fusion welding. It was performed on 5mm thicknessAA6061 and AA5083 dissimilar Aluminum alloys. Aluminum alloy light weight, softer, tendency to bend easily, cost effective in terms of energy requirements so aluminum alloy has selected in this FSW technique. In this welding when two metals are joined with the help of heat generated by rubbing metals against each other. The friction stir welding is mostly used for joining aluminum alloys. The main defects occurring in this welding are holes, material flow rate. These defects are mainly caused due to improper selection of welding parameters. In this project the mechanical properties of FSW dissimilar aluminum alloy AA5083 and AA6061has tested with the help of universal testing machine, hardness testing by Vickers hardness at various zones of the welded joints. In this experimental the testing of mechanical properties based on the input parameters such as rotational speed, tool speed and axial force with proper welding parameters. -
University of Cincinnati
UNIVERSITY OF CINCINNATI Date:___________________ I, _________________________________________________________, hereby submit this work as part of the requirements for the degree of: in: It is entitled: This work and its defense approved by: Chair: _______________________________ _______________________________ _______________________________ _______________________________ _______________________________ EFFECT OF AGING ON ABRASIVE WEAR RESISTANCE OF SILICON CARBIDE PARTICULATE REINFORCED ALUMINUM MATRIX COMPOSITE A thesis submitted to the Division of Graduate Studies and Research of the University of Cincinnati In partial fulfillment of the requirement for the degree of MASTER OF SCIENCE in the Department of Chemical and Materials Engineering of the College of Engineering 2007 by Varun Sethi B.Tech, National Institute of Technology, Jamshedpur, 2005 Committee Chair: Dr. R Y. Lin Abstract The effect of aging on the wear resistance of SiC particle reinforced aluminum composites was investigated. The as cast Al/SiCp composite used in this study was purchased from Duralcan with A-356 matrix and 23Vol% of SiC reinforcement. This composite was solutionized at 565ºC and then aged at 180 ºC for different time intervals and changes in hardness and wear resistance were measured using a Rockwell B hardness tester and Pin-on-disc wear tester respectively. For reference purpose an alloy of Al-10wt% silicon was used. Wear resistance of the aged composites was found superior to the as cast composite with the peak aged composite showing the maximum wear resistance and overaging resulted in a decrease in wear resistance. Results also showed that the wear resistance of the composites was greater than the monolithic alloy at all loads and wear rate was found to increase with pressure. -
Use of General Fatigue Data in the Interpretation of Full-Scale Fatigue Tests by W
AGARD-AG-228 oo (S IS 6 Q a: < O AGARDograph No. 228 Use of General Fatigue Data in the Interpretation of Full-scale Fatigue Tests by W. Barrels NORTH ATLANTIC TREATY ORGANIZATION DISTRIBUTION AND AVAILABILITY ON BACK COVER AGARD-AG-228 NORTH ATLANTIC TREATY ORGANIZATION ADVISORY GROUP FOR AEROSPACE RESEARCH AND DEVELOPMENT (ORGANISATION DU TRAITE DE L'ATLANTIQUE NORD) AGARDograph No.228 USE OF GENERAL FATIGUE DATA IN THE INTERPRETATION OF FULL-SCALE FATIGUE TESTS by W. Barrels Retired Military Air Chief Engineer 42, rue Larmeroux 92170 Vanves, France This AGARDograph was sponsored by the Structures and Materials Panel of AGARD. THE MISSION OF AGARD The mission of AGARD is to bring together the leading personalities of the NATO nations in the fields of science and technology relating to aerospace for the following purposes: — Exchanging of scientific and technical information; - Continuously stimulating advances in the aerospace sciences relevant to strengthening the common defence posture; - Improving the co-operation among member nations in aerospace research and development; — Providing scientific and technical advice and assistance to the North Atlantic Military Committee in the field of aerospace research and development; - Rendering scientific and technical assistance, as requested, to other NATO bodies and to member nations in connection with research and development problems in the aerospace field; - Providing assistance to member nations for the purpose of increasing their scientific and technical potential; - Recommending effective ways for the member nations to use their research and development capabilities for the common benefit of the NATO community. The highest authority within AGARD is the National Delegates Board consisting of officially appointed senior representatives from each member nation. -
Effect of Hydrogen on the Wear Resistance of Steels Upon Contact with Plasma Electrolytic Oxidation Layers Synthesized on Aluminum Alloys
metals Article Effect of Hydrogen on the Wear Resistance of Steels upon Contact with Plasma Electrolytic Oxidation Layers Synthesized on Aluminum Alloys Volodymyr Hutsaylyuk 1,* , Mykhailo Student 2, Volodymyr Dovhunyk 2, Volodymyr Posuvailo 2, Oleksandra Student 2, Pavlo Maruschak 3 and Ihor Koval’chuck 2 1 Department of Machine Design, Military University of Technology, Gen. S. Kaliskiego str. 2, 00-908 Warsaw, Poland 2 Karpenko Physico-Mechanical Institute of the National Academy of Sciences of Ukraine, 79060 Lviv, Ukraine; [email protected] (M.S.); [email protected] (V.D.); [email protected] (V.P.); [email protected] (O.S.); [email protected] (I.K.) 3 Department of Industrial Automation, Ternopil National Ivan Pul’uj Technical University, 46001 Ternopil, Ukraine; [email protected] * Correspondence: [email protected]; Tel.: +48-22-261-839-245 Received: 16 January 2019; Accepted: 22 February 2019; Published: 1 March 2019 Abstract: The different nature of the effect of hydrogen on the tribological behavior of two carbon steels (st. 45 and st. U8) upon their contact with super solid plasma electrolytic oxidation (PEO) layers synthesized on two light alloys (AMg-6 and D16T alloys as the analogists of the A 95556 UNS USA and AA2024 ANSI USA alloys correspondently) was investigated in the medium of mineral oil of the I-20 type. To compare the effect of hydrogenation on the tribological properties of the analyzed contact pairs, similar tests were also performed on the same mineral oil with clear water or an aqueous solution of glycerine added to its content.