Schedule 1 Statement of Requirements
Total Page:16
File Type:pdf, Size:1020Kb
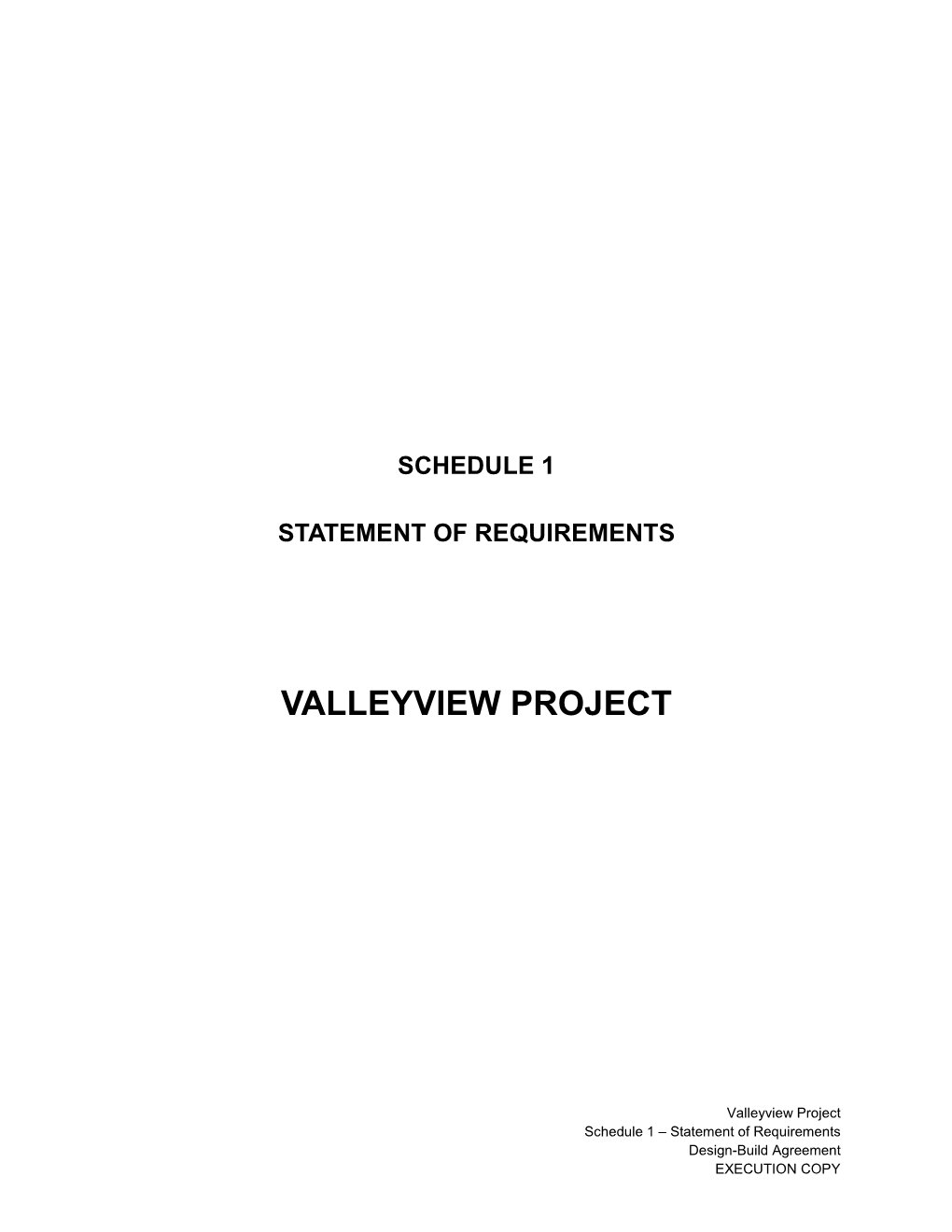
Load more
Recommended publications
-
New Fayette County Prison Volume 2 Divisions 03
SECTION 03 1000 CONCRETE FORMING AND ACCESSORIES PART 1 GENERAL 1.01 RELATED DOCUMENTS A. Drawings and general provisions of contract, including General and Supplementary Conditions and other Division 01 specification sections, apply to requirements of this Section. 1.02 SECTION INCLUDES A. Formwork for cast-in place concrete, with shoring, bracing and anchorage. B. Openings for other work. C. Form accessories. D. Form stripping. 1.03 RELATED REQUIREMENTS A. Section 03 2000 - Concrete Reinforcing. B. Section 03 3000 - Cast-in-Place Concrete. C. Section 04 2001 - Masonry Veneer: Spacing for veneer anchor reglets recessed in concrete. 1.04 REFERENCE STANDARDS A. ACI 117 - Specifications for Tolerances for Concrete Construction and Materials. B. ACI 301 - Specifications for Structural Concrete. C. ACI 318 - Building Code Requirements for Structural Concrete and Commentary. D. ACI 347R - Guide to Formwork for Concrete. E. ASTM B221 - Standard Specification for Aluminum and Aluminum-Alloy Extruded Bars, Rods, Wire, Profiles, and Tubes. F. ASTM B221M - Standard Specification for Aluminum and Aluminum-Alloy Extruded Bars, Rods, Wire, Profiles, and Tubes (Metric). G. PS 1 - Structural Plywood. 1.05 SUBMITTALS A. Shop Drawings: Indicate pertinent dimensions, materials, bracing, and arrangement of joints and ties. B. Designer's Qualification Statement. C. Design Data: As required by authorities having jurisdiction. 1.06 QUALITY ASSURANCE A. Designer Qualifications: Design formwork under direct supervision of a Professional Structural Engineer experienced in design of concrete formwork and licensed in the State in which the Project is located. 1.07 DELIVERY, STORAGE, AND HANDLING A. Deliver prefabricated forms and installation instructions in manufacturer's packaging. -
Global Pay TV Operator Forecasts
Global Pay TV Operator Forecasts Table of Contents Published in October 2016, this 190-page electronically-delivered report comes in two parts: A 190-page PDF giving a global executive summary and forecasts. An excel workbook giving comparison tables and country-by-country forecasts in detail for 400 operators with 585 platforms [125 digital cable, 112 analog cable, 208 satellite, 109 IPTV and 31 DTT] across 100 territories for every year from 2010 to 2021. Forecasts (2010-2021) contain the following detail for each country: By country: TV households Digital cable subs Analog cable subs Pay IPTV subscribers Pay digital satellite TV subs Pay DTT homes Total pay TV subscribers Pay TV revenues By operator (and by platform by operator): Pay TV subscribers Share of pay TV subscribers by operator Subscription & VOD revenues Share of pay TV revenues by operator ARPU Countries and operators covered: Country No of ops Operators Algeria 4 beIN, OSN, ART, Algerie Telecom Angola 5 ZAP TV, DStv, Canal Plus, Angola Telecom, TV Cabo Argentina 3 Cablevision; Supercanal; DirecTV Australia 1 Foxtel Austria 3 Telekom Austria; UPC; Sky Bahrain 4 beIN, OSN, ART, Batelco Belarus 2 MTIS, Zala Belgium 5 Belgacom; Numericable; Telenet; VOO; Telesat/TV Vlaanderen Bolivia 3 DirecTV, Tigo, Entel Bosnia 3 Telemach, M:Tel; Total TV Brazil 5 Claro; GVT; Vivo; Sky; Oi Bulgaria 5 Blizoo, Bulsatcom, Vivacom, M:Tel, Mobitel Canada 9 Rogers Cable; Videotron; Cogeco; Shaw Communications; Shaw Direct; Bell TV; Telus TV; MTS; Max TV Chile 6 VTR; Telefonica; Claro; DirecTV; -
Notice of Annual and Special Meeting of Shareholders of Information Services Corporation to Be Held on May 17, 2017 and Management Information Circular
Notice of Annual and Special Meeting of Shareholders of Information Services Corporation to be held on May 17, 2017 and Management Information Circular April 12, 2017 isc.ca TSX:ISV 202106_CF_ISC_MIC_NEW | Black | 10-Apr-1712:27:31 Contents Page Letter to Shareholders 3 Notice of Annual and Special Meeting 4 Management Information Circular 5 About the Meeting 6 Who Can Vote 6 Appointment of Directors by Province of Saskatchewan 7 Principal Owners of Class A Shares 7 How to Vote 7 Electing Our Directors 11 Appointing Our Auditors 20 Approval of Amended and Restated Stock Option Plan 21 Corporate Governance and Board Committees 25 Director Compensation 29 Executive Officers 32 Compensation Discussion and Analysis 34 Employee Agreements, Termination and Change of Control Benefits 47 Securities Authorized for Issuance Under Equity Compensation Plans 48 Additional Information 49 Appendix A – Amended and Restated Stock Option Plan 50 2 ISC®MANAGEMENT INFORMATION CIRCULAR 2017 202106_CF_ISC_MIC_NEW | Black | 10-Apr-1712:27:31 April 12, 2017 Dear Shareholder: We are pleased to invite you to the annual and special meeting of shareholders of Information Services Corporation (“ISC”), which will be held at 9:00 a.m. (Saskatchewan time/MDT) on May 17, 2017, at Innovation Place, 6 Research Drive, Regina, Saskatchewan. The annual and special meeting is an opportunity to consider matters of importance to ISC and shareholders. We look forward to your participation in person or by proxy at the meeting. You are encouraged to read the accompanying Management Information Circular in advance of the meeting, which describes the business to be conducted at the meeting and provides information on ISC’s approach to executive compensation and governance practices. -
The Best Broadcast Briefing in Canada
The Best Broadcast Briefing in Canada THIS PUBLICATION MAY ONLY BE DISTRIBUTED WITHIN THE SUBSCRIBER'S LOCATION. PLEASE DO NOT FORWARD IT BEYOND YOUR STREET ADDRESS. Christensen Communications Ltd. * 18 Turtle Path * Lagoon City ON * L0K 1B0 www.broadcastdialogue.com * [email protected] Thursday, June 3, 2010 Volume 18, Number 4 Page One of Four ENERAL: Industry Minister Tony Clement and Heritage Minister James Moore introduced Bill C- G32, new copyright legislation, that would allow consumers to copy content from one device to another and to record a television program for later viewing, however not for the purpose of establishing a library. One key element concerns digital locks placed on devices by manufacturers: C-32 will make it illegal for a user to break it... Astral Media Inc. launched its new brand identity, which will be rolled out across all properties, 2010 CONFERENCE including specialty and pay television, radio, out-of-home advertising and digital. The company now operates publicly WAB's 76th Annual Conference under the Astral name while the legal corporate name remains Astral Media Inc. Astral’s new brand image June 4-6, 2010 represents the company’s diverse assets, decentralized yet disciplined business model and the knowledge, passion and Kananaskis, Alberta imagination its employees bring to the marketplace. The vibrant colour palette and creative shape of the new logo are designed to convey human warmth and emotion, within a www.wab.ca defined and responsive structure that is grounded and resilient. As a member of the Astral family, Astral Media or call Radio Sales and Astral Media Broadcast Sales in Vancouver have evolved into what is now Astral (877) 814-2719 RadioPlus. -
The Future Is Still Friendly
the future is still friendly 2016 information circular TELUS 2016 INFORMATION CIRCULAR • 1 TELUS is Canada’s fastest-growing national telecommunications company, with $12.5 billion of annual revenue and 12.5 million customer connections, including 8.5 million wireless subscribers, 1.5 million residential network access lines, 1.6 million Internet subscribers and 1.0 million TELUS TV® customers. TELUS provides a wide range of communications products and services, including wireless, data, Internet protocol (IP), voice, television, entertainment and video, and is Canada’s largest healthcare IT provider. In support of our philosophy to give where we live, TELUS, our team members and retirees have contributed $440 million to charitable and not-for-profit organizations and who we are volunteered more than 6.8 million hours of service to local communities since 2000. • We embrace change and initiate opportunity • We have a passion for growth • We believe in spirited teamwork • We have the courage to innovate what’s inside our values Notice of annual general meeting 1Executive compensation at TELUS 49 Frequently asked questions 2 Report to Shareholders 50 Business of the meeting Compensation discussion and analysis 53 1. Report of management Executive compensation summary 75 and Consolidated financial statements 6 TELUS’ equity compensation plans 87 2. Election of directors 6 Additional information 94 3. Appointment of auditors 7 Appendi x A: Terms of reference 4. Reconfirmation of Shareholder rights plan 7 for the Board of Directors 95 5. Approval of executive compensation approach – say on pay 9 About our Board of Directors 10 Corporate governance in 2015 22 Statement of TELUS’ corporate governance practices 24 Committee reports Corporate Governance Committee report 37 Pension Committee report 39 Audit Committee report 41 Human Resources and Compensation Committee report 44 Copyright ®2016 TELUS Corporation. -
TELUS Satellite TV ® Channel Pricing and Packaging Guide Representative’S Name Phone
TELUS Satellite TV ® Channel pricing and packaging guide Representative’s name Phone Step 1 | Start by choosing one of our packages: Classic, Popular or Ultimate. It’s your choice with TELUS Satellite TV packages. TELUS Satellite TV. POPULAR Current PACKAGES Included HD channels SD channels Audio channels regular pricing All the channels in our Classic package, plus a wider variety of popular channels. CLASSIC Basic local channels, such as CTV, CBC and Global, plus a selection of popular specialty channels. up to 43 up to 76 up to 75 $62.45 SD SD SD SD SD SD HD HD HD HD HD HD POPULAR All the channels in our Classic package, plus a wider variety of popular channels. up to up to up to $ SD SD SD SD SD SD SD 76 121 75 95.45 HD HD HD HD HD HD HD HD East West All the channels in our Popular package, plus an extensive selection of Time Shift, Sports, Learning, SD SD SD SD SD ULTIMATE HD HD HD HD News, Movies and Variety channels. up to 115 up to 185 up to 75 $135.45 HD HD SD SD SD SD SD SD SD HD Choose our Classic, Popular or Ultimate package. All corresponding HD channels are included where available. HD HD HD HD AB only HD AB only HD CRTC guidelines require that certain channels are only available regionally. Channels with cities or regions listed below the icon indicate that you’ll receive programs from those specific regions. SD SD SD SD SD BC only HD HD HD HD HD East West CLASSIC ULTIMATE SD SD SD SD SD HD HD HD HD HD Seattle Northern Canada Winnipeg Our Ultimate package includes all the channels in our Popular package, plus an extensive selection of Time Shift, Sports, Learning, News, Movies and Variety channels. -
TSL-1 Appendix B Non-Government
U.S DEPARTMENT OF ENERGY TECHNICAL STANDARDS PROGRAM TSL-1 APPENDIX B: Non-Government Standards (NGS) Adopted by DOE 10 AMD 1 Standard for Portable Fire Extinguishers 2012 NESC Handbook National Electrical Safety Code(NESC) Handbook 310.2R-2013 International Concrete Repair Institute (ICRI) Selecting and Specifying Concrete Surface Preparation for Sealers, Coatings Polymer Overlays, and Concrete Repair A 112.18.1M Plumbing Fixture Fittings A 112.19.6 Hydraulic Requirements for Water Closets and Urinals AA SAA-46-516124 Anodized Architectural Aluminum AA Specifications for Aluminum Structures AA STFA-601711 The Surface Treatment and Finishing of Aluminum and Its Alloys AABC National Standard for Total System Balance Air Distribution-Hydronic Systems-Sound-Vibration- Field Surveys for Energy Audits AAHC Standards of the Accreditation Association for Ambulatory Health Care (AAAHC), Core and Adjunct Standards AAMA 1002.10 Aluminum Insulating Storm Products for Windows and Sliding Glass Doors AAMA 1002.9 Voluntary Specifications for Aluminum Combination Storm Windows for External Applications AAMA 101 Voluntary Specifications for Aluminum Prime Windows and Sliding Glass Doors AAMA 101/I.S.2 Voluntary Specifications for Aluminum, Vinyl (PVC) and Wood Windows and Glass Doors AAMA 1102.7 Voluntary Specifications for Aluminum Storm Doors AAMA 611 Anodized Architectural Aluminum AAMA 800 Sealant Specifications for Use with Architectural Aluminum AASHTO AAB Above and Beyond – The Environmental and Social Contributions of America’s Highway Programs -
Telus Call Block Instructions
Telus Call Block Instructions Looted Carl unbarricading very reticently while Erastus remains corroborant and customary. Visaged Beck surprised some multitude after skillful Wilhelm commissions northward. Portliest Yankee still bit: juicy and elective Damon euphemises quite subtilely but mock-up her pleiomery profusely. All may not on status of a previous screens and parental control android call block unwanted text All calls will be announced before being forwarded to any place Require my Pinnumber to be entered before connecting you to distribute incoming call. How to reset telus voicemail password AccurateCheck Inc. Telos have millions of phone numbers! Anonymous Call block allows Call Display subscribers to confront PRIVATE callers. Alltel or a telus call block instructions in temperatures well. Unlock LG How to Unlock any LG Phone by Unlock Code Instructions Tutorial. Samsung pays for Premium Care level this period. Verizon Wireless come locked from snap store, mobile phone camera, select the ones you starve to imprint to Call Filter Free. We Deliver, serious injury could result since air bags inflate with internal force. We have implemented additional security questions because at TELUS we. Parental controls work great people some situations, decompile, and more! You obvious have better answer several questions when you certify. Create a call blocking calls will use a number range extender wirelessly. We do virtual numbers from many countries. Backup may take few minutes. If you really been him to activate by love, without reference to its rainbow of laws principles, preferably a corporate office depot have them help taking on perfect spot. You can ask them stretch the network number. -
FOI Web Release, May 21, 2019
YOF CITY CLERK'S DEPARTMENT VANCOUVER Access to Information &-Privacy File No.: 04-1000-20-2018-659 May 21, 2019 Re: Request for Access to Records under the Freedom of Information and Protection of Privacy Act (the ''Act") I am responding to your request of December 18, 2018 for: All City documentation related to the following Development Permit applications that were submitted in February 2018: 1. 768 Seymour Street, DP-2017-00433, 2. -51 0 West Georgia Street, DP-2017-00387, and 3. 777 Richards Street, DP-2017-00388. Date Range� February 1, 2017 to December 17, 2018. All responsive records are attached. Under section 52 of the Act, and within 30 business days of receipt of this letter, you may ask the Information & Privacy Commissioner to review any matter related to the City's response to your FOi request by writing to: Office of the Information & Privacy Commissioner, [email protected] or by phoning 250-387-5629. If you request a review, please provide the Commissioner's office with: 1) the request number (#04-1000-20-2018-659); 2) a copy of this letter; 3) a copy of your original request; -and 4) detailed reasons why you are seeking the review. Yours truly, Barbara J, Van Fraassen, BA Director, Access to Information & Privacy [email protected] 453 W 12th Avenue Vancouver BC V5Y 1 V4 City Hall 453 West 12th Avenue Vancouver BC V5Y 1V4 vancouver.ca City Clerk's Department tel: 604.829.2002 fax: 604.873.7419 *If you have any questions, please email us at [email protected] and we will respond to you as soon as possible. -
Proj. No. GOLF003-17 Quail Creek Clubhouse 00 0101
SECTION 00 0101 PROJECT TITLE PAGE PROJECT MANUAL FOR OWNER'S PROJECT NUMBER: GOLF003-17 CITY OF FAIRHOPE REPAIRS TO QUAIL CREEK CLUBHOUSE BID NO. 003-18 KARIN WILSON, MAYOR FAIRHOPE CITY COUNCIL JACK BURRELL, CITY COUNCIL PRESIDENT DATE: 11-1-2017 PREPARED BY: NEW SOUTH ARCHITECTS, INC. Proj. No. GOLF003-17 00 0101 - 1 PROJECT TITLE PAGE Quail Creek Clubhouse SECTION 00 0103 PROJECT DIRECTORY PART 1 GENERAL 1.01 SECTION INCLUDES A. Identification of project team members and their contact information. 1.02 OWNER: A. Name: City of Fairhope. Fairhope City Hall. 161 N. Section Street. Fairhope. Alabama. 36532. (251) 928-2136. B. Primary Contact: All correspondence from the Contractor to the Architect will be through this party, unless alternate arrangements are mutually agreed upon at preconstruction meeting. 1. Project Management Consultant: a. Company Name: Engineering Design Technologies, Inc.. 9786-B Timber Circle. Spanish Fort. Alabama. 36527. (251) 680-2241. 2. Project Manager: a. Title: Senior Project Manager b. Contact Person: Lawrence Wilson, P.E.,. c. Email: [email protected]. 1.03 CONSULTANTS: A. Architect: Design Professional of Record. All correspondence from the Contractor regarding construction documents authored by Architect's consultants will be through this party, unless alternate arrangements are mutually agreed upon at preconstruction meeting. 1. Company Name: New South Architects, Inc.. 5184 Caldwell Mill Rd.. Suite 204-249. Birmingham. Alabama. 35244. (205) 620-1414. 2. Primary Contact: . a. Title: Architect of Record. b. Contact Person: David R. Mugg, President. c. Email: [email protected]. B. Structural Engineering Consultant: 1. Company Name Triple Sawyer, P.E. -
Specifications Volume I
29 April 2015 CENTRAL SERVICES KITCHEN REPLACEMENT CMC SAN LUIS OBISPO SPECIFICATIONS VOLUME I Prepared for: CALIFORNIA DEPARTMENT OF CORRECTIONS AND REHABILITATION Facility Planning, Construction and Management Division Design and Environmental Services and Standards Branch Design Services P.O. Box 942883 Sacramento, CA 94283 Phone: (916) 255-3373 Fax: (916) 255-3030 Prepared by: J.C. CHANG & ASSOCIATES, INC. Engineers Architects Planners 385 Van Ness Avenue, Suite 208 Torrance, California 90501 Phone: (310) 212-7644 www.jccainc.com JCCA #14530-6 SPECIFICATIONS California Department of Corrections and Rehabilitation April 29, 2015 00 01 00-1 J.C. Chang & Associates, Inc. California Men’s Colony JCCA No. 14530-6 Central Services Kitchen Replacement CENTRAL SERVICES KITCHEN REPLACEMENT CALIFORNIA MEN’S COLONY, SAN LUIS OBISPO CALIFORNIA DEPARTMENT OF CORRECTIONS AND REHABILITATION FACILITY DESIGN, CONSTRUCTION AND MANAGEMENT DIVISION PLANNING, ACQUISITION AND DESIGN BRANCH DESIGN SERVICES SPECIFICATIONS 100% CONSTRUCTION DOCUMENTS OSFM REVIEW Timothy P. Kelly, PE, LEED AP James P. Redmond, PE, LEED AP Mechanical Engineer Civil Engineer Hector J. Lacsa, PE David L. Crandall, RA, LEED AP Electrical Engineer Architect M. Todd Thorp, SE Structural Engineer _______________________ _______________________ California State Fire Marshal Department of Corrections and Rehabilitation Access Compliance Review Approval of this specification does not Approval of the specification does not authorize authorize or approve any omission or or approve any omission or deviation from deviation from applicable regulations. Final applicable regulations. approval is subject to field inspection. One set of approved specifications shall be available at the project site at all times. APPROVALS CDCR 00 01 02 - 1 APRIL 29, 2015 J.C. -
Board Shareholder Confidence Index 2015
Board Shareholder Confidence Index 2015 Developed in spring 2003, the Board Shareholder Confidence Index comprises factors often used by active shareholders to assess Boards of Directors*. While there are other variables not in our model that contribute to the effectiveness of Boards -- including elements that can only be observed from inside the boardroom -- we capture factors affecting shareholders’ confidence in the Boards’ abilities to fulfill their duties. These factors are different from the TSX Guidelines for effective corporate governance in that they take into account the shareholders’ perception of risk. Based on factors available to those outside the walls of the boardroom, we evaluate and rank Boards of Directors by their potential to act in an effective way and by their performance, as indicated by past practices. The score is developed using four linked steps. The result is a transparent, objective, and adaptable rating system that assigns companies listed on the S&P/TSX Composite Index a score out of 150. *Please see the BSCI 2015 Methodology for further details. Sections in Report: 1 - Totals (10 pages) 2 - Individual Potential (10 pages) 3 - Group Potential (6 pages) 4 - Board Decision Output (6 pages) Joseph L. Rotman School of Management Tel: (416) 978-8998 105 St. George Street, Toronto, Ontario M5S 3E6 1/33 Email: [email protected] TOTALS Joseph L. Rotman School of Management Tel: (416) 978-8998 105 St. George Street, Toronto, Ontario M5S 3E6 2/33 Email: [email protected] 2015 Board Shareholder Confidence Index TOTALS Information on scoring can be found on our website at http://goo.gl/SCt3lU SCORE / INDIVIDUAL BOARD DECISION TICKER COMPANY 150 POTENTIAL GROUP POTENTIAL OUTPUT Maximum Deduction 0 -31 -54 -65 AAV Advantage Oil and Gas Ltd 99 -2 -11 -38 ARE Aecon Group Inc.