AIAA-2012-4209 48Th JPC SKB
Total Page:16
File Type:pdf, Size:1020Kb
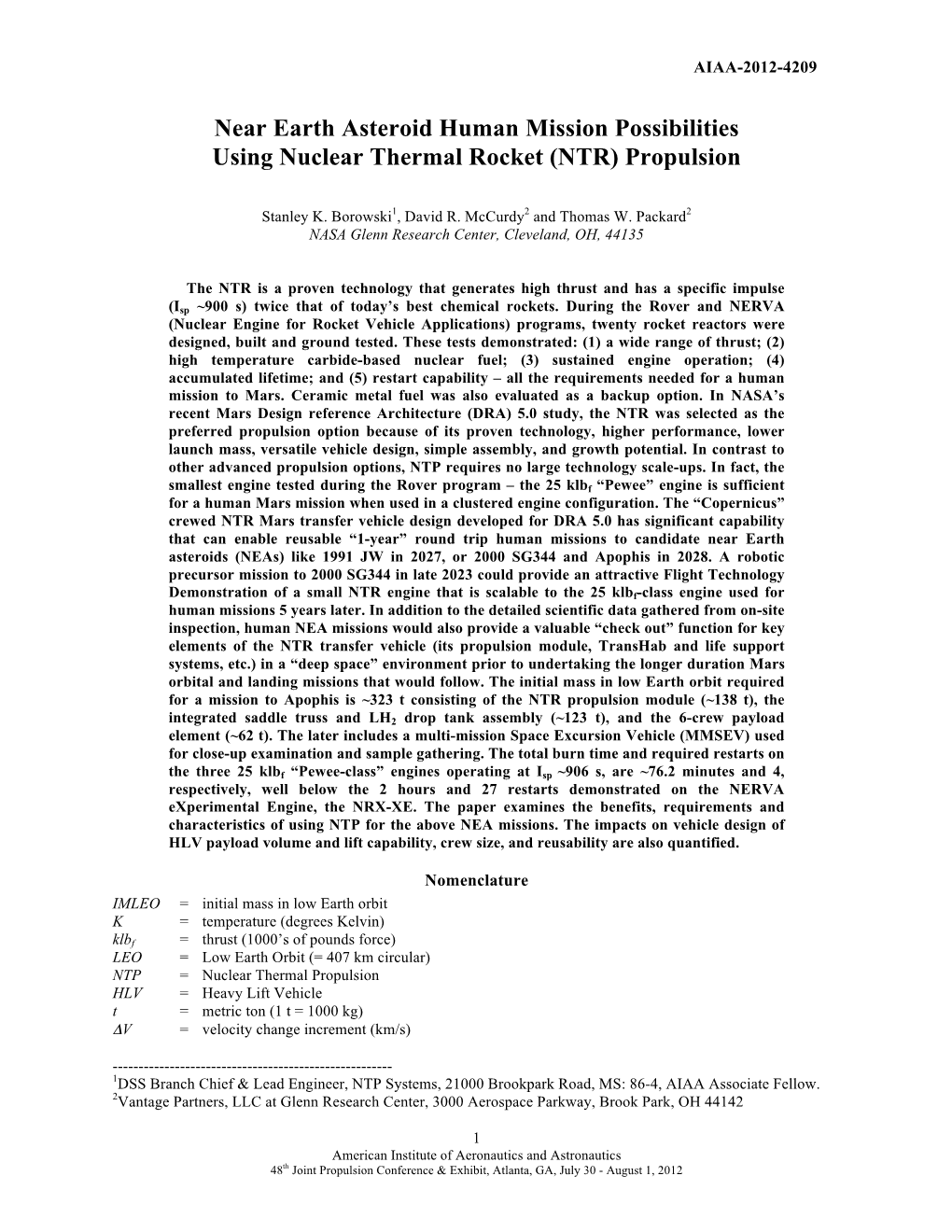
Load more
Recommended publications
-
Asteroid Retrieval Feasibility Study
Publications 4-2-2012 Asteroid Retrieval Feasibility Study John Brophy California Institute of Technology Fred Culick California Institute of Technology Louis Friedman The Planetary Society Pedro Llanos Embry-Riddle Aeronautical University - Daytona Beach, [email protected] et al. Follow this and additional works at: https://commons.erau.edu/publication Part of the Astrodynamics Commons, Space Vehicles Commons, and the The Sun and the Solar System Commons Scholarly Commons Citation Brophy, J., Culick, F., Friedman, L., Llanos, P., & al., e. (2012). Asteroid Retrieval Feasibility Study. , (). Retrieved from https://commons.erau.edu/publication/893 This Report is brought to you for free and open access by Scholarly Commons. It has been accepted for inclusion in Publications by an authorized administrator of Scholarly Commons. For more information, please contact [email protected]. Asteroid Retrieval Feasibility Study 2 April 2012 Prepared for the: Keck Institute for Space Studies California Institute of Technology Jet Propulsion Laboratory Pasadena, California 1 2 Authors and Study Participants NAME Organization E-Mail Signature John Brophy Co-Leader / NASA JPL / Caltech [email protected] Fred Culick Co-Leader / Caltech [email protected] Co -Leader / The Planetary Louis Friedman [email protected] Society Carlton Allen NASA JSC [email protected] David Baughman Naval Postgraduate School [email protected] NASA ARC/Carnegie Mellon Julie Bellerose [email protected] University Bruce Betts The Planetary Society -
An Ongoing Effort to Identify Near-Earth Asteroid Destination
The Near-Earth Object Human Space Flight Accessible Targets Study: An Ongoing Effort to Identify Near-Earth Asteroid Destinations for Human Explorers Presented to the 2013 IAA Planetary Defense Conference Brent W. Barbee∗, Paul A. Abelly, Daniel R. Adamoz, Cassandra M. Alberding∗, Daniel D. Mazanekx, Lindley N. Johnsonk, Donald K. Yeomans#, Paul W. Chodas#, Alan B. Chamberlin#, Victoria P. Friedensenk NASA/GSFC∗ / NASA/JSCy / Aerospace Consultantz NASA/LaRCx / NASA/HQk / NASA/JPL# April 16th, 2013 Introduction I Near-Earth Objects (NEOs) are asteroids and comets with perihelion distance < 1.3 AU I Small, usually rocky bodies (occasionally metallic) I Sizes range from a few meters to ≈ 35 kilometers I Near-Earth Asteroids (NEAs) are currently candidate destinations for human space flight missions in the mid-2020s th I As of April 4 , 2013, a total of 9736 NEAs have been discovered, and more are being discovered on a continual basis 2 Motivations for NEA Exploration I Solar system science I NEAs are largely unchanged in composition since the early days of the solar system I Asteroids and comets may have delivered water and even the seeds of life to the young Earth I Planetary defense I NEA characterization I NEA proximity operations I In-Situ Resource Utilization I Could manufacture radiation shielding, propellant, and more I Human Exploration I The most ambitious journey of human discovery since Apollo I NEAs as stepping stones to Mars 3 NHATS Background I NASA's Near-Earth Object Human Space Flight Accessible Targets Study (NHATS) (pron.: /næts/) began in September of 2010 under the auspices of the NASA Headquarters Planetary Science Mission Directorate in cooperation with the Advanced Exploration Systems Division of the Human Exploration and Operations Mission Directorate. -
1 ABSTRACT Aside from the Exploration of Mars, the Objects That
IAC-07-B3.5.06 INTO THE BEYOND: A CREWED MISSION TO A NEAR-EARTH OBJECT David J. Korsmeyer, NASA Ames Research Center, Intelligent Systems Division, Moffett Field, CA, USA, [email protected] Rob R. Landis, NASA Johnson Space Center, Mission Operations Directorate, Houston, TX, USA [email protected] Paul A. Abell, NASA Johnson Space Center, Astromaterials Research & Exploration Science, Houston, TX, USA [email protected] ABSTRACT utility and opportunities for the developing Aside from the exploration of Mars, the Constellation infrastructure, particularly, the objects that most capture our interest for a Ares Launch vehicles and the Orion crewed new human visit are the Near-Earth Objects spacecraft, to be used for missions that were (NEOs). These objects are ideal candidates not directly in the design specifications (aka for deep space operations and explorations as non-lunar missions). The Ares and Orion we extend the human presence out into the systems are designed to launch 4-6 crew to solar system. The notion of a crewed mission the International Space Station (ISS), and to to a NEO was first discussed in the Apollo eventually take 4 crew back to lunar orbit era. The most recent assessment has been where a lunar lander would take the crew to undertaken by the Advanced Projects Office the surface. within NASA’s Constellation Program. This particular study examined the feasibility of The NASA Constellation Program wanted to sending NASA’s new Orion spacecraft (also understand what are some other feasible, referred to as the Crew Exploration Vehicle, high-value uses of the Orion spacecraft and or CEV) to a NEO. -
Asteroid Retrieval Mission Concept – Trailblazing Our Future in Space and Helping to Protect Us from Earth Impactors
Asteroid Retrieval Mission Concept – Trailblazing Our Future in Space and Helping to Protect Us from Earth Impactors Presented by Dan Mazanek1 Co-authors: John Brophy2 and Gabe Merrill1 1NASA Langley Research Center; 2Jet Propulsion Laboratory April 16, 2013 2013 Planetary Defense Conference Flagstaff, USA Paper No: IAA-PDC13-04-14 1 Background The idea of utilizing asteroidal resources is not new • 1903 – Konstantin Tsiolkovskii included the concept of using asteroids for resources in his most famous publication, The Exploration of Cosmic Space by Means of Reaction Motors • 1977 – NASA’s Dr. Brian O’Leary proposed using mass drivers to move Earth- approaching Apollo and Amor asteroids to Earth’s vicinity • 1997 – Dr. John S. Lewis detailed how we can extract the vast resources available from our solar system in the influential book Mining the Sky: Untold Riches from the Asteroids, Comets, and Planets September 2011 and February 2012 – Asteroid Retrieval Mission (ARM) Study at Caltech’s Keck Institute for Space Studies (KISS) • Examined the feasibility of returning a small (~7 m diameter) near-Earth asteroid (NEA), or part of a large NEA, to cislunar space • Utilize robotic 50 kW-class solar electric propulsion (SEP) vehicle and currently available technologies (40 kW available to the electric propulsion system) • John Brophy (Co-Leader along with Louis Friedman and Fred Culick) and Dan Mazanek were KISS ARM study members 2 Recent Events Recent events have elevated the public’s awareness of the potential of space resources and have -
Why Atens Enjoy Enhanced Accessibility for Human Space Flight
(Preprint) AAS 11-449 WHY ATENS ENJOY ENHANCED ACCESSIBILITY FOR HUMAN SPACE FLIGHT Daniel R. Adamo* and Brent W. Barbee† Near-Earth objects can be grouped into multiple orbit classifications, among them being the Aten group, whose members have orbits crossing Earth's with semi-major axes less than 1 astronomical unit. Atens comprise well under 10% of known near-Earth objects. This is in dramatic contrast to results from recent human space flight near-Earth object accessibility studies, where the most favorable known destinations are typically almost 50% Atens. Geocentric dynamics explain this enhanced Aten accessibility and lead to an understanding of where the most accessible near-Earth objects reside. Without a com- prehensive space-based survey, however, highly accessible Atens will remain largely un- known. INTRODUCTION In the context of human space flight (HSF), the concept of near-Earth object (NEO) accessibility is highly subjective (Reference 1). Whether or not a particular NEO is accessible critically depends on mass, performance, and reliability of interplanetary HSF systems yet to be designed. Such systems would cer- tainly include propulsion and crew life support with adequate shielding from both solar flares and galactic cosmic radiation. Equally critical architecture options are relevant to NEO accessibility. These options are also far from being determined and include the number of launches supporting an HSF mission, together with whether consumables are to be pre-emplaced at the destination. Until the unknowns of HSF to NEOs come into clearer focus, the notion of relative accessibility is of great utility. Imagine a group of NEOs, each with nearly equal HSF merit determined from their individual characteristics relating to crew safety, scientific return, resource utilization, and planetary defense. -
ANIME: the “ASTEROID NODAL INTERSECTION MULTIPLE ENCOUNTERS” CUBESAT MISSION to EXPLORE NEAR-EARTH ASTEROID DIVERSITY. D. Perna1, M
52nd Lunar and Planetary Science Conference 2021 (LPI Contrib. No. 2548) 1106.pdf ANIME: THE “ASTEROID NODAL INTERSECTION MULTIPLE ENCOUNTERS” CUBESAT MISSION TO EXPLORE NEAR-EARTH ASTEROID DIVERSITY. D. Perna1, M. Pajola2, L. Casalino3, S. Ivanovski4, M. Lavagna5, M. Zannoni6, M. Bechini5, A. Capannolo5, A. Colagrossi5, G. Cremonese2, E. Dotto1, A. Lucchetti2, E. Mazzotta Epifani1, J. Prinetto5, E. Simioni2, P. Tortora6 and G. Zanotti5 1INAF – Osservatorio Astronomico di Roma (Italy), [email protected], 2INAF – Osservatorio Astronomico di Padova (Italy), 3DIMEAS – Politecnico di Torino (Italy), 4INAF – Osservatorio Astronomico di Trieste (Italy), 5DAER – Politecnico di Milano (Italy), 6CIRI Aerospace – Università di Bologna (Italy). ANIME in a nutshell: The “Asteroid Nodal positions and velocities. Asteroids 2000 SG344, 2006 Intersection Multiple Encounters” (ANIME) mission HZ51 and 2004 QD14 are selected as ANIME targets concept has been proposed in response to the 2020 due to their pivotal scientific and strategic relevance, Italian Space Agency (ASI) call for ideas for future over a rather large number of suitable alternatives. The CubeSat missions. ANIME aims to explore three near- reference solution (Figure 1) has a total ΔV of 1.05 Earth asteroids (NEAs), selected by virtue of their km/s and a propellant consumption of 1.04 kg (out of peculiar and yet unexplored size and physical regimes, the available 1.5 kg). The ample propellant margin as well as their relevance in terms of planetary guarantees flexibility in terms of: i) departure date protection. Thanks to an optimized trajectory, the changes, ii) strategies for escape from Earth sphere of targets are encountered during their passages through influence (depending on the launch opportunities and their orbital nodes. -
Opportunities for Asteroid Retrieval Missions
Opportunities for Asteroid Retrieval Missions Pre-print proof-reading copy. The final publication is available at: http://link.springer.com/chapter/10.1007/978-3-642-39244-3_21 D. García Yárnoz, J.P. Sanchez, C.R. McInnes Advanced Space Concepts Laboratory, University of Strathclyde, UK. Abstract Asteroids and comets are of strategic importance for science in an effort to uncover the formation, evolution and composition of the Solar System. Near-Earth Objects (NEOs) are of particular interest because of their ac- cessibility from Earth, but also because of their speculated wealth of mate- rial resources. The exploitation of these resources has long been discussed as a means to lower the cost of future space endeavours. In this chapter, we analyze the possibility of retrieving entire objects from accessible helio- centric orbits and moving them into the Earth’s neighbourhood. The aster- oid retrieval transfers are sought from the continuum of low energy trans- fers enabled by the dynamics of invariant manifolds; specifically, the retrieval transfers target planar, vertical Lyapunov and halo orbit families associated with the collinear equilibrium points of the Sun-Earth Circular Restricted Three Body problem. The judicious use of these dynamical fea- tures provides the best opportunity to find extremely low energy transfers for asteroidal material. With the objective to minimise transfer costs, a global search of impulsive transfers connecting the unperturbed asteroid’s orbit with the stable manifold phase of the transfer is performed. A cata- logue of asteroid retrieval opportunities of currently known NEOs is pre- sented here. Despite the highly incomplete census of very small asteroids, the catalogue can already be populated with 12 different objects retrievable with less than 500 m/s of Δv. -
The Comet/Asteroid Impact Hazard: a Systems Approach
THE COMET/ASTEROID IMPACT HAZARD: A SYSTEMS APPROACH Clark R. Chapman and Daniel D. Durda Office of Space Studies Southwest Research Institute Boulder CO 80302 and Robert E. Gold Space Engineering and Technology Branch Johns Hopkins University Applied Physics Laboratory Laurel MD 20723 24 February 2001 The Comet/Asteroid Impact Hazard: Chapman, Durda, and Gold A Systems Approach February 2001 EXECUTIVE SUMMARY The threat of impact on Earth of an asteroid or comet, while of very low probability, has the potential to create public panic and – should an impact happen – be sufficiently destructive (perhaps on a global scale) that an integrated approach to the science, technology, and public policy aspects of the impact hazard is warranted. This report outlines the breadth of the issues that need to be addressed, in an integrated way, in order for society to deal with the impact hazard responsibly. At the present time, the hazard is often treated – if treated at all – in a haphazard and unbalanced way. Most analysis so far has emphasized telescopic searches for large (>1 km diameter) near-Earth asteroids and space-operations approaches to deflecting any such body that threatens to impact. Comparatively little attention has been given to other essential elements of addressing and mitigating this hazard. For example, no formal linkages exist between the astronomers who would announce discovery of a threatening asteroid and the several national (civilian or military) agencies that might undertake deflection. Beyond that, comparatively little attention has been devoted to finding or dealing with other potential impactors, including asteroids smaller than 1 km or long-period comets. -
Manned Mission to NEO Study
National Aeronautics and Space Administration Manned Mission to NEO Study Jerry Condon, NASA/JSC/EG5 Jacob Williams, ESCG Elizabeth Davis, ESCG David Lee, NASA/JSC/EG5 Juan Senent, OSR Sept. 27, 2010 Run Methodology ΔVAD Patch conic assumptions. V∞EI ΔtAE Asteroid Earth departure epoch [1900 Cases]: Departure • Start: Jan 01, 2015 00:00:00 Earth Arrival Step: 5 days • ΔtS • End: Dec 31, 2040 00:00:00 Earth-Asteroid transfer time [72]: ΔVAA • Start: 30 days • Step: 5 days Asteroid Arrival • End: 360 days Asteroid stay time [6]: • Start: 7 days • Step 7 days • End: 42 days Asteroid-Earth transfer time [72]: • Start: 5 days Step: 5 days V∞ED • ΔtEA • End: 360 days 1900x72x6x72 = 59,097,600 cases per asteroid Earth Departure 5766 Asteroids 340,756,761,600 cases total. Run time of ~2 hrs on JSC cluster Pre-Decisional: For NASA Internal Use Only 2 Asteroid Cases JPL Small-Body Database Search Engine: http://ssd.jpl.nasa.gov/sbdb_query.cgi Export CSV file which is read by the program Input parameters: • Object group : NEOs • Object kind: Asteroids Damon Landau 9/1/2010: • Numbered state: All objects Assumed diameter > 50 m • Constraints: H (mag) ≤ 24.2 abs. vis. mag. < 24.2 • 5766 Asteroids in this set (as of 8-26-2010) - Note: without the H constraint, the total number is 7183. Output parameters: • SPK-ID • object fullname • Absolute magnitude: H (mag) • Rotation period: rot_per (h) • Keplerian elements - Epoch of osculation: epoch (MJD) - Semi-major axis: a (AU) - Eccentricity: e - Inclination: i (deg) Assuming these are in - -
Dealing with the Impact Hazard
Chapter for Asteroids III (final draft 06/08/02) book edited by William Bottke, Alberto Cellino, Paolo Paolicchi, and Richard P. Binzel. University of Arizona Press, Tucson (2003) Dealing with the Impact Hazard David Morrison NASA Astrobiology Institute Alan W. Harris NASA Jet Propulsion Laboratory Geoff Sommer RAND Corporation Clark R. Chapman Southwest Research Institute, Boulder Andrea Carusi IAS, Roma Address for correspondence David Morrison NASA Ames 200-7 Mt View CA 94035 [email protected] Abstract The small fraction of the asteroids with Earth-crossing or Earth-approaching orbits is of special interest to us because many will eventually impact our planet. The time-averaged impact flux as a function of projectile energy can be derived from lunar cratering statistics, although we have little information on the possible variability of this flux over time. Alternatively, we can use current observations of Near Earth Asteroids (NEAs) to derive the size distribution and flux of impactors. The effects of impacts of various energies can be modeled, using data from historic impacts (such as the K-T impactor 65 million years ago) and the observed 1994 bombardment of Jupiter by fragments of Comet Shoemaker-Levy 9. Such models confirm that the terrestrial biosphere is highly vulnerable to severe perturbation from impacts, so that even such a small event as the K-T impact (by a projectile 10-15 km in diameter) can lead to a mass extinction. Combining the impact flux with estimates of environmental and ecological effects reveals that the greatest contemporary hazard is associated with impactors near one million megatons energy. -
A Comprehensive Ongoing Survey of the Near-Earth Asteroid Population for Human Mission Accessibility
AIAA Guidance, Navigation, and Control Conference AIAA 2010-8368 2 - 5 August 2010, Toronto, Ontario Canada A Comprehensive Ongoing Survey of the Near-Earth Asteroid Population for Human Mission Accessibility Brent W. Barbee,∗ Timothy Esposito,y Elfego Pi~nonIII,z Sun Hur-Diazx Emergent Space Technologies, Inc., Greenbelt, MD, 20770-6334, USA Ronald G. Mink{ NASA Goddard Space Flight Center, Greenbelt, MD, 20771, USA Daniel R. Adamok Houston, TX, 77059, USA There are currently 7069 known Near-Earth Asteroids (NEAs) and more are being discovered on a continual basis; it is likely that the total NEA population consists of at least hundreds of thousands of objects. NEAs have orbits that bring them into close proximity with Earth's orbit, making them both a unique hazard to life on Earth and a unique opportunity for science and exploration. The current presidential administration has proposed that NASA send humans to an asteroid by the mid-2020s as part of the Flexible Path architecture. A study was therefore undertaken to identify NEAs that are accessible for round-trip human missions using a heavy-lift launch architecture. A fully parametrized, highly efficient algorithm was developed to accomplish this, allowing changes in vehicle parameters to be studied and enabling the accessibility analysis to keep pace with the NEA discovery rate, which is increasing as new telescopes, such as Pan-STARRS, become active. To date, the accessibility analysis algorithm has identified 59 accessible NEAs and 10 marginally inaccessible NEAs. Of the 59 accessible NEAs, 14 offer attractive mission opportunities between 2016 and 2030, with round-trip flight times between 54 and 192 days. -
Easily Retrievable Objects Among the Neo Population
EASILY RETRIEVABLE OBJECTS AMONG THE NEO POPULATION D. García Yárnoz,* J. P. Sánchez,† and C. R. McInnes† DOI: 10.1007/s10569-013-9495-6. Pre-print proof-reading copy. The final publication is available at: http://link.springer.com/article/10.1007/s10569-013-9495-6 Celest Mech Dyn Astr (2013) 116:367–388 ABSTRACT Asteroids and comets are of strategic importance for science in an effort to understand the formation, evolution and composition of the Solar System. Near-Earth Objects (NEOs) are of particular interest because of their accessibility from Earth, but also because of their speculated wealth of material resources. The exploitation of these resources has long been discussed as a means to lower the cost of future space endeavours. In this paper, we consider the currently known NEO population and define a family of so-called Easily Retrievable Objects (EROs), objects that can be transported from accessible heliocentric orbits into the Earth’s neighbourhood at affordable costs. The asteroid retrieval transfers are sought from the continuum of low energy transfers enabled by the dynamics of invariant manifolds; specifically, the retrieval transfers target planar, vertical Lyapunov and halo orbit families associated with the collinear equilibrium points of the Sun-Earth Circular Restricted Three Body problem. The judicious use of these dynamical features provides the best opportunity to find extremely low energy Earth transfers for asteroid material. A catalogue of asteroid retrieval candidates is then presented. Despite the highly incomplete census of very small asteroids, the ERO catalogue can already be populated with 12 different objects retrievable with less than 500 m/s of Δv.