The LEAN Service Desk from Theory to Prac Ce
Total Page:16
File Type:pdf, Size:1020Kb
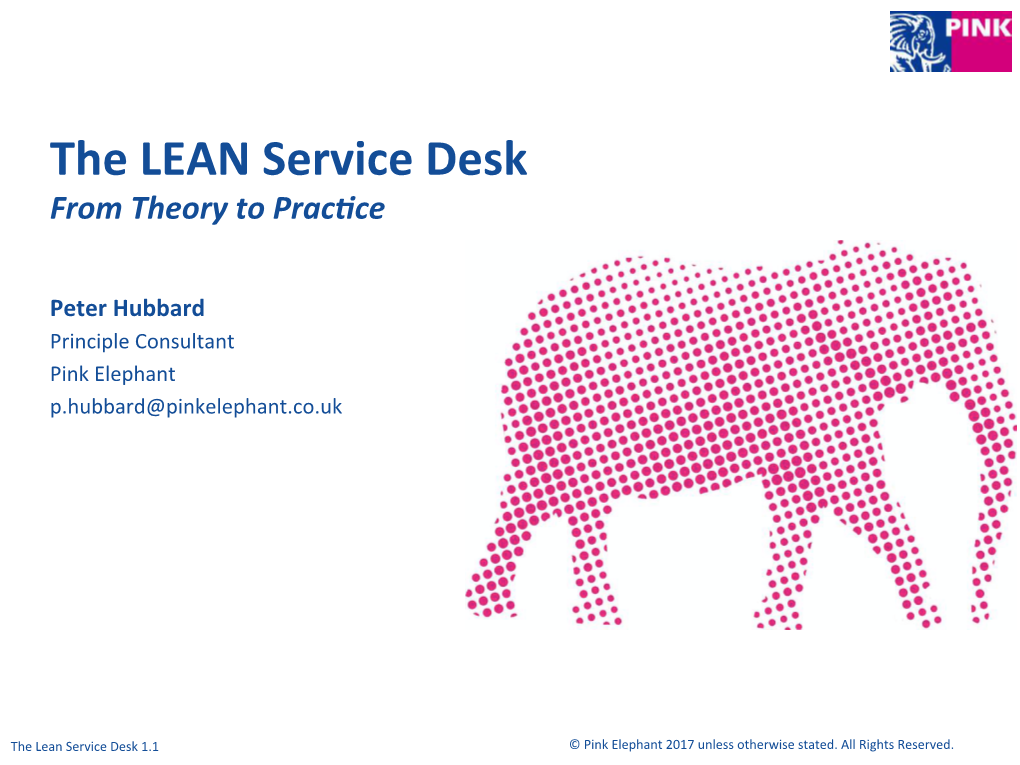
Load more
Recommended publications
-
Lean Process Improvement Assessment
LEAN PROCESS IMPROVEMENT ASSESSMENT INSTRUCTIONS: Read each item, then check a box on the 1-to-5 scale to show how often this occurs in your workplace: If you checked "often" or "very often" then consider: 1 = never 2 = rarely 3 = sometimes 4 = often 5 = very often In my work area, we spend too much time looking for the items we need to do our 5S+ 1 2 3 4 5 1 jobs: files, materials, equipment, and so on. If the physical work area was better 5S+ stands for sort, straighten, shine, standardize, sustain, organized, we’d be more productive and less frustrated. and safety. When we get inputs from customers or from other sources (from paper forms or Poka-Yoke online web forms, for example), we often find that the incoming information is 1 2 3 4 5 From the Japanese term for mistake-proofing, poka-yoke is 2 incomplete or inaccurate. We have to circle back to people to get the information all about putting measures in place to prevent errors from we need. If we received complete information from them the first time around, we’d occurring as a process unfolds. be a lot more efficient. We find ourselves wondering what our customers are thinking. Are we meeting their Voice of the Customer needs and expectations? Are they happy with our work? Are there things we can do 1 2 3 4 5 When it comes to improvement, understanding the 3 to increase their satisfaction? If we had answers to these questions, we could serve customer’s spoken and unspoken requirements is essential. -
Using the DMAIC Process to Direct the Sequencing of Lean/Six Sigma Tools for Successful Project Outcomes
Using the DMAIC Process to Direct the Sequencing of Lean/Six Sigma Tools for Successful Project Outcomes Jim Ellis Certified Master Black Belt J&J Process Excellence Director – US Sales Strategic Accounts [email protected] Intent: Using the DMAIC Process to Direct the Sequencing of Lean/Six Sigma Tools for Successful Project Outcomes The purpose of this presentation is to share with the attendees my experience over the past 5 years using the DMAIC Process how to determine what Lean and/or 6 Sigma tools is the best to use when for assuring successful outcomes of your projects. Learning Objectives: 1.) Clear understanding of DAMIC Process 2.) Clear understanding of which common Lean and 6 Sigma Tools are best used in what stage of DMAIC 3.) Clear understanding of how to assess success for a project and know if you have achieved it. After Attending the attendees will: 1.) Know what the DMAIC process is and how it is applied in project planning 2.) Understand which Lean and 6 Sigma tools are used in what sequence to assure successful project outcomes © 2008 Ortho Clinical Diagnostics The Driving Forces of Change Today’s Healthcare Delivery Challenges… Declining Resources $29.9 Space Vacancy Capital Funds billion Skilled Labor Rates Medicare/Medicaid Reimbursement Laboratory Techs 5.9% Shortfall Imaging Techs 5.9% Pharmacists 8.1% RNs 8.1% Inpatient Admissions2 ED Visits2 Volume New Technology Market Pressures Increasing Pressures © 2008 Ortho Clinical Diagnostics Why are labs changing? “I need to transform my lab!” Why? • 2X Volume • ½ the -
Download Complete Curriculum
L E A N S I X S I G M A G R E E N B E LT C O U R S E T O P I C S Copyright ©2019 by Pyzdek Institute, LLC. LEAN SIX SIGMA GREEN BELT COURSE TOPICS LESSON TOPIC Overview A top-level overview of the topics covered in this course What is Six Sigma? A complete overview of Six Sigma Lean Overview 1 Waste and Value Lean Overview 2 Value Streams, Flow and Pull Lean Overview 3 Perfection Recognizing an Linking your Green Belt activities to the organization’s Opportunity vision and goals Choosing the Project- How to pick a winning project using Pareto Analysis Pareto Analysis Assessing Lean Six Sigma How to carefully assess Lean Six Sigma project candidates Project Candidates to assure success Develop the Project Plan 1 Team selection and dynamics; brainstorming; consensus decision making; nominal group technique Develop the Project Plan 2 Stakeholder analysis, communication and planning, cross functional collaboration, and Force Field Analysis Develop the Project Plan 3 Obtain a charter for your project Develop the Project Plan 4 Work breakdown structures, DMAIC tasks, network diagrams Develop the Project Plan 5 Project schedule management; project budget management Develop the Project Plan 6 Obstacle avoidance tactics and management support strategies High Level Maps 1 L-Maps, linking project charter Ys to L-Map processes High Level Maps 2 Mapping the process from supplier to customer (SIPOC) High Level Maps 3 Product family matrix 2 Voice of the Customer (VOC) 1 Kano Model, getting the voice of the customer using the critical incident technique VOC 2-CTQ Specification Link the voice of the customer to the CTQs that drive it Principles of Variation 1 How will I measure success? Are my measurements trustworthy? Scales of measurement, data types, measurement error principles. -
Methods and Concepts for Lean-Powered Improvement
Methods and Concepts for Lean-Powered Improvement DAILY LEAN “Just do it” Easy improvements found in daily work, walk-throughs, events, etc. Huddles Quick team sessions to check work status, make decisions, problem solve Kanban Boards Visual tool to communicate and optimize the flow of work Scorecards and Scoreboards Prominent visuals showing process performance and other key measures STRUCTURED METHODS Process Mapping A drawing of the workflow showing all steps in a process Standard Work Documented approach (templates, maps, job aids) to ensure consistency A3 Problem Solving Structured tool and process for problem-solving and communication 5S Method for organizing a work area to make it more efficient and orderly Process Walk (Gemba Walk) Walk-through to spot waste and find quick improvement opportunities Six Sigma Statistics-based approach for eliminating defects and variation IMPROVEMENT EVENTS Kaizen Event Structured approach to overhaul a process and plan rollout; 4-5 days Multi-Session PI Event Kaizen event approach but in 2-3 sessions, each lasting 1-3 days Small-Scope PI Event Focuses on a subset process, with rapid rollout; half day to 3 days Value Stream Mapping (VSM) High-level look at processes/systems to find improvement opportunities Lean Process Design Uses Lean concepts to create new processes KEY UNDERLYING CONCEPTS Voice of the Customer Be clear on what creates value from the customer’s perspective Making the Invisible Visible Identify and see all the steps that make up the process Flow Ensure that those value-creating -
Using DMAIC in Improvement of Customer Satisfaction and Facilities Provided at Commuter Stations
International Journal of Academic Research in Business and Social Sciences 2016, Vol. 6, No. 12 ISSN: 2222-6990 Using DMAIC in Improvement of Customer Satisfaction and Facilities provided at Commuter Stations Roslina Mustapha1, Nurul Fadly Habidin2 1Department of Business Management, Faculty of Management and Economics, Universiti Pendidikan Sultan Idris, 35900 Tanjung Malim, Perak, Malaysia 2Department of Management and Leadership, Faculty of Management and Economics, Universiti Pendidikan Sultan Idris, 35900 Tanjong Malim, Perak, Malaysia DOI: 10.6007/IJARBSS/6-i12/2564 URL: http://dx.doi.org/10.6007/IJARBSS/v6-i12/2564 Abstracts This paper discusses the use of six sigma approach to improvement of customer service and facilities at commuter stations. The management of commuter stations should be sensitive to the needs and desires of the passengers. In this study, DMAIC approach taking into accounts the views of the customer (VOC) to the dissatisfaction of commuter services and facilities available at commuter stations. Keywords: Six sigma, DMAIC, customer satisfaction, business management 1. Introduction The performance of a business, whether private or public sector is depends on customer satisfaction. For commuter service almost 20 years of presence in Malaysia, there are still some problems, especially to people with disabilities (PWDs) who want to use the commuter service. Using the six-sigma approach is one way to solve the problem of quality of service. Problem solving is an activity to change what is actually happening to what is supposed to happen (Evans & Lindsay, 2007). People with disabilities are not left behind in the services for commuters as it is one of the convenient public transports, safe and cheap. -
Metrics That Trigger Actionable Discussions: Prioritize Process Improvements Using Gauge R&R and SPC Capability
Metrics That Trigger Actionable Discussions: Prioritize Process Improvements Using Gauge R&R and SPC Capability by Govindarajan (Govind) Ramu If a typical process engineering review meeting at your organization involves engineers staring at scores of presentation slides and feeling overwhelmed, you may want to consider the metrics you’re using. High-level metrics like throughput yield and scrap may seem like logical choices for regular product reviews, and they are useful at a business level; however, they tend not to trigger actionable improvement discussion. In contrast, the same powerful tools that engineers use in their everyday product development and process management applications can have enhanced benefits when put to work for broader decision making about improvements. Integrating tools like failure mode and effects analysis (FMEA), gauge repeatability and reproducibility (GR&R), and statistical process control (SPC) provides a quality improvement framework that organizations can use to monitor process health, prioritize improvements, and assign resources to actions that warrant most attention. Figure 1 shows how FMEA, GR&R, and SPC can be analyzed in the context of relationships between critical to quality (CTQ) and critical to process (CTP) parameters, leading to creation of a “process health card.” In eight steps, you can build your own process health card and begin using it at your engineering review meetings. With your focus strongly on metrics of practical interest to product and process engineers—GR&R results, SPC stability status, and the potential risk to the organization of rejecting good parts or accepting bad parts (misclassification) which impacts the organization’s cost of poor quality—you should find it easier to engage in the actionable discussions that the meeting should foster. -
Chapter 3 Study Guide Tools and Techniques for Quality Design and Control
CHAPTER 3 STUDY GUIDE TOOLS AND TECHNIQUES FOR QUALITY DESIGN AND CONTROL MULTIPLE CHOICE QUESTIONS . Design for Six Sigma consists of four principal activities. Which of the following is not one of them? a. Concept development b. Design development c. Design maximization d. Design verification Answer: C AACSB: Reflective Thinking Page: 102 . In the set of matrices is used to relate the voice of the customer to technical features and production planning and control requirements the following symbols • and Δ are used to denote _____ and _____ respectively. a. a weak relationship; a strong relationship b. a very strong relationship; a weak relationship c. a strong relationship; a weak relationship d. a very strong relationship; a strong relationship Answer: B AACSB: Analytic Page: 107 . Which of the following is not a type of house of quality? a. Technical features deployment matrix b. Process plan and quality control charts c. BCG matrix d. Operating instructions Answer: C AACSB: Analytic Page: 109 . DFMEA stands for: a. design failure mode and effects analysis. b. design function mode and effects analysis c. design failure mode and efficiency analysis d. design feature methods and efficiency analysis Answer: A AACSB: Analytic Page: 109 . The purpose of DFMEA is all of the following except: a. to recommend corrective design actions. b. to estimate the effect and seriousness of the failure. c. to identify all the ways in which a failure can occur. d. to act as the “voice of the customer” in product design. Answer: D AACSB: Reflective Thinking Page: 109 . Which of the following statements is true about various service components: degree of customer contact and interaction, the degree of labor intensity, and the degree of customization? a. -
Operationalizing Voice of the Customer: How Top Performers Create Actionable Insights
Benchmarks & GalaxyTM Vendor Evaluations Series [Type a quote from the document or the summary of an interesting point. You can position the text box anywhere in the document. Use the Drawing Tools tab to change the formatting of the pull quote text box.] Operationalizing Voice of the Customer: How Top Performers Create Actionable Insights ©2012 Hypatia Research, LLC. All Rights Reserved. www.hypatiaresearch.com 781-862-5106 NOTICE: Information contained in this publication has been sourced in good faith from primary, secondary and end-user research and is believed to be reliable based upon our research methodology and analyst’s judgment. Ultimate responsibility for all decisions, use and interpretation of Hypatia research, reports or publications remains with the reader, subscriber or user thereof. Page 1 HYPATIA RESEARCH GROUP LLC. Hereby grants and assigns HYPATIA RESEARCH GROUP LLC. Hereby grants and assigns to IBM and all business units, divisions and subsidiaries thereof, worldwide syndication rights to a report entitled ―OPERATIONALIZING ENTERPRISE VOICE OF THE CUSTOMER SOFTWARE SOLUTIONS.” This license and sales agreement entitles the purchaser, IBM, to all distribution, quote, syndication, translation, and publication rights. Hypatia Research Group, LLC must be credited with proper attribution [©2014 Hypatia Research Group, LLC] in each and every instance of content usage. IBM agrees to take good faith steps to safeguard the Intellectual Property contained in this research study. The trademarked Product MatrixTM chart or GalaxyTM chart may be utilized solely for business development presentations and/or full translations of this study and for report distribution to prospects and/or clients, but may NOT be utilized as part of a press release, slide-share, or any type of public, digital, online or general distribution. -
Lean Six Sigma Black Belt
L E A N S I X S I G M A B L A C K B E LT C O U R S E T O P I C S Copyright ©2019 by Pyzdek Institute, LLC. LEAN SIX SIGMA BLACK BELT COURSE TOPICS LESSON TOPIC Overview A top-level overview of the topics covered in this course What is Six Sigma? A complete top-level overview Lean Overview 1 Waste and Value Lean Overview 2 Value Streams, Flow and Pull Lean Overview 3 Perfection Recognizing an Opportunity Linking your Black Belt activities to the organization’s vision and goals Choosing the Project-Pareto How to pick a winning project using Pareto Analysis Analysis Assessing Lean Six Sigma How to carefully assess Lean Six Sigma project candidates Project Candidates to assure success Develop the Project Plan 1 Team selection and dynamics; brainstorming; consensus decision making; nominal group technique Develop the Project Plan 2 Stakeholder analysis, communication and planning, cross functional collaboration, and Force Field Analysis Develop the Project Plan 3 Obtain a charter for your project Develop the Project Plan 4 Work breakdown structures, DMAIC tasks, network diagrams Develop the Project Plan 5 Project schedule management; project budget management Develop the Project Plan 6 Obstacle avoidance tactics and management support strategies High Level Maps 1 L-Maps, linking project charter Ys to L-Map processes High Level Maps 2 Mapping the process from supplier to customer (SIPOC) High Level Maps 3 Product family matrix 2 Voice of the Customer (VOC) 1 Kano Model, getting the voice of the customer using the critical incident technique VOC 2-Survey Development Using the output of the CIT process to develop and validate surveys VOC 3-Listening to Customers Focus groups and other customer listening posts VOC 4-Analytic Hierarchical How to determine customer importance weights Process (AHP) VOC 5-CTQ Specification Link the voice of the customer to the CTQs that drive it Principles of Variation 1 How will I measure success? Are my measurements trustworthy? Scales of measurement, data types, measurement error principles. -
Lean Six Sigma and Minitab' Page Number Changes for Edition 3 to Edition 4
Lean Six Sigma and Minitab' Page Number changes for Edition 3 to Edition 4 Introduction Edition 3 Edition 4 Notes What is Six Sigma? 1 1 DMAIC – A Logical Approach to Problem Solving 2 2 What is Lean? 3 3 Lean and the Six Sigma DMAIC Structure 4 4 Building a Lean Six Sigma Programme 5 5 Different Types of Lean Six Sigma Projects 7 7 Where do Lean Six Sigma Projects come from? 9 9 Managing Lean Six Sigma Projects 10 10 Minitab – Overview 11 11 Quality Companion – Overview 12 12 How to use this guide – Free data files! 13 13 DEFINE 14 14 Problem Statements 15 15 Goal Statements 17 17 Costs of Poor Quality (COPQ) 18 18 Voice of the Customer (VOC), Kano Analysis 19 19 House of Quality 21 21 Critical to Quality (CTQ) Trees 23 23 Extra page on CTQ Trees. SIPOC – High Level Process Mapping 24 25 Gemba - 26 New tool/page. Project Structure and Project Plans 25 27 Stakeholder Analysis 26 28 Project Working Files 27 29 Facilitation Skills 28 30 Effective Teams and Meetings 29 31 Project Charter 30 32 Define Checklist and Review Questions 31 33 MEASURE 32 34 Key Performance Indicators (KPIs) 33 35 KPI Trees 34 36 Lean Measures (PCE, OEE, Takt Time etc.) 35 37 Statistics for process ‘Position’ / ‘Spread’ 38 40 Operational Definitions 40 42 Data Worlds (Continuous/Count/Attribute Data) 43 45 Data Collection Methods 49 51 Data Collection Plans & Sampling 50 52 Minimum Sample Sizes 51 53 Sampling Frequency 54 56 Contextual Data – the 4th Data World 55 57 Measurement System Analysis – Intro & Routemap 56 58 - Bias and Precision 58 60 - Meausurement System -
Lean Six Sigma Glossary Brought to You By
Lean Six Sigma Glossary Brought To You By: View Online Lean Six Sigma Glossary Including Visuals & Infographics At: https://goleansixsigma.com/glossary/ The web is overflowing with Lean Six Sigma resources. Our glossary provides clear, straight-forward language, organized for quick access so you can easily find and understand terms that you’re searching for. For a better understanding of these terms and an overview of Lean Six Sigma, check out our Green Belt Training & Certification. P300 COPYRIGHT 2015 GOLEANSIXSIGMA.COM. ALL RIGHTS RESERVED. 1 5 Whys: 5 Whys is a simple but effective method of analyzing and solving problems by asking “why” five times, or as many times as needed in order to move past symptoms and determine root cause. This approach is used in tandem with Cause-and-Effect or Fishbone diagrams. 5S: 5S is a workplace organization technique composed for five primary phases: Sort, Set In Order, Shine, Standardize, and Sustain. 8 Wastes (aka Muda): The 8 Wastes; Defects, Overproduction, Waiting, Non-Utilized Talent, Transportation, Inventory, Motion, and Extra- Processing are a list of the most common reasons for excess cycle time in a process. The idea of process improvement is to identify and remove all forms of waste from a process in order to increase efficiency, reduce cost, and provide customer value. A3: On a literal level, A3 refers to a ledger size piece of paper, but in the Lean world it is a one page project report. This one-pager contains the problem, the analysis of the process, the identified root causes, potential solutions and action plan all on a large sheet of paper. -
Step 1 Identify CTQ's
EMGT 835 FIELD PROJECT: Office Supplies Cost Optimization using Six Sigma By Piyachat Kitchaiya Master of Science The University of Kansas Spring Semester 2006 An EMGT Field Project report submitted to the Engineering Management Program and the Faculty of the Graduate School of The University of Kansas in partial fulfillment of the requirements for the degree of Master of Science. ________________________________ Herbert Tuttle Date Committee Chair ________________________________ Dr. Robert Zerwekh Date Committee Member ________________________________ Annette Tetmeyer Date Committee Member Table of Contents Executive Summary............................................................................................................ 1 Acknowledgements............................................................................................................. 2 Introduction......................................................................................................................... 3 The Company’s History.................................................................................................. 3 Management philosophy for continued improvement .................................................... 5 Office Supply Purchasing Process.................................................................................. 6 Off-Contract vs. On-Contract Purchasing....................................................................... 6 Literature Review ..............................................................................................................