Comparative Testing of Hydraulic Lime and OPC Mortar Mixes
Total Page:16
File Type:pdf, Size:1020Kb
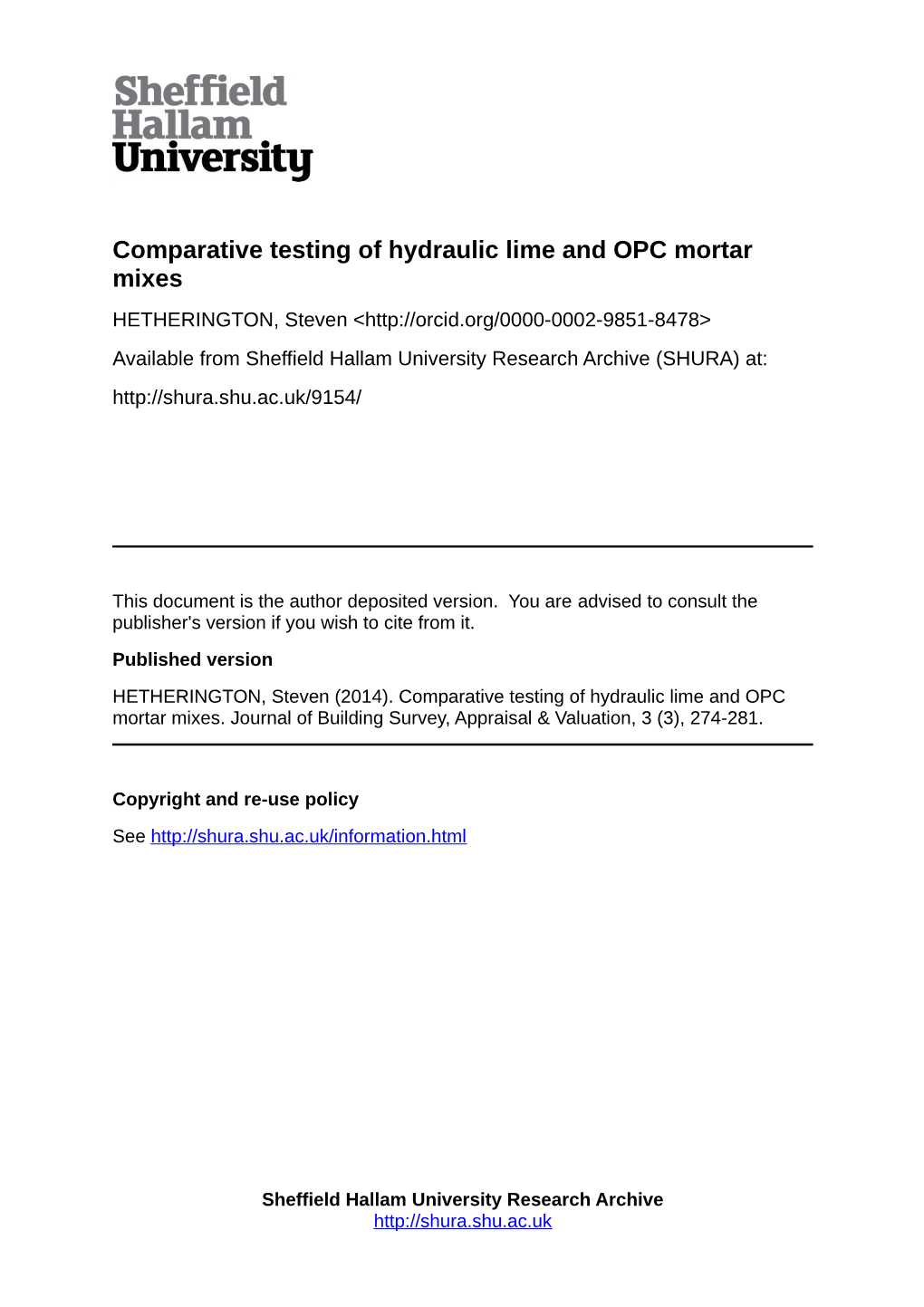
Load more
Recommended publications
-
Different Types of Building Limes
Different types of building limes Natural hydraulic limes are made from limestone that contains impurities such as clay or silicates. Unlike lime putty which is non-hydraulic lime, NHLs can set in damp conditions, indeed they require water for a minimum period of around 72 hours to gain maximum strength. They also have some free lime available for carbonation. There are three European classifications NHL 2, NHL3.5 and NHL5 based on the compressive strength of laboratory mortars after 28 days. These are often somewhat misleadingly termed feebly hydraulic, moderately hydraulic and eminently hydraulic. We generally recommend the use of NHLs where the need for breathability and lower strength is outweighed by the desire for an earlier and harder set such as working on bedding hard masonry, wall copings, chimneys and slate floors. In some circumstances hydraulic lime mortars can be used for rendering or plastering. The strength of a hydraulic lime mortar (HLM) varies depending on the manufacturer of the hydraulic lime as some NHL will be high in the band or low. HLM will also vary depending on the ratio of lime binder to aggregate and the type of aggregate or sand used. Natural Hydraulic Lime (NHL) NHL or Natural Hydraulic Lime, comes from limestone that has natural impurities of clay and other minerals, the amount of impurities within it determines how hard it will set. NHL works by setting in the presence of water, hence the term Hydraulic: Natural hydraulic lime powders come in 3 European grades: GRADE STRENGTH(MPa) EXAMPLES OF USE NHL2 >2 to <7 Pointing internally or with soft masonry, plastering NHL3.5 >3.5 to <10 Bedding, pointing NHL5 >5 to <15 Flooring, below DPC or chimney flaunchings NHL's can be used when speed is essential as it sets much quicker than a Lime Putty based mortar. -
Hot-Mixed Mortars: the New Lime Revival
ALISON HENRY Hot-mixed mortars: the new lime revival Appreciation of the limitations of lime putty mortars and concerns about the strength of natural hydraulic limes have triggered renewed interest in traditional mortars, and in hot mixing. When non-hydraulic lime-putty mortars are used in exposed locations or, as here, for demanding applications such as on wall tops, failure due to frost damage is not uncommon. Quicklime made in The last five years or so have seen a revival in use of hot- traditional kilns often mixed mortar.While many people have welcomed this as contained under- or over- burned limestone which did a way of making more authentic mortars for conservation, not slake when the mortar others are sceptical or even hostile to what they see as a was made, and remained in new fad. Before exploring the pros and cons of hot-mixed the mix as rounded whitish particles, often referred to as mortars, it is worth reflecting on the past 40 years of lime ‘lime lumps’. Fragments of use and how we have arrived at the current situation. black fuel ash from the lime kiln sometimes found their way into the mortar too. The lime revival These are clearly visible in As the damage caused by hard, impervious cement many hot-mixed mortars. mortars became apparent from the mid- 20th century, However, for very high- quality work, quicklime was the revival in use of lime from the 1970s was naturally ‘BHP’ – ‘best hand-picked’ welcomed by conservation practitioners. Emerging – and did not contain lime practice borrowed from materials and methods used lumps or ash. -
Precis of Use of the Natural Hydraulic Lime NHL
ACCURATE OF USE OF THE NATURAL HYDRAULIC LIME Precis of use of the natural hydraulic lime NHL « Or, how to use nature to protect us from its whims ». Olivier Labesse. 1 ACCURATE OS USE OF THE NATURAL HYDRAULIC LIME To my father, a man, i own everything. 2 ACCURATE OF USE OF THE NATURAL HYDRAULIC LIME Preface There has been an on-going renaissance in working with lime throughout Europe during the last twenty years or so. Some countries had abandoned lime completely in favour of cement; when lime was used it was only to increase the workability of cement mortars. Working with lime was all but forgotten, repairs to old buildings were carried our us- ing cement mortars and concrete. As a result problems began to occur. It was realised that old structures originally built with lime were best repaired using lime. In simple terms old buildings needed to breathe in order to stay dry and healthy, and to remain flexible so as not to crack from inevitable minor movement. Working with lime had to be re-learnt again. In some countries nobody still living had worked with lime or only the very old had the dimmest memory of doing so. Written sources were scarce and some- times confusing. Initially mistakes were made but bit by bit knowledge and skills were re-developed. There is still some way to go. France was fortunate not to have abandoned its natural hydraulic lime production, which it has maintained since the 19th century. Today it has a thriving export business because of renewed demand worldwide. -
Development of Bond Strength in Hydraulic Lime Mortared Brickwork
Development of Bond Strength in Hydraulic Lime Mortared Brickwork Submitted by ZHAOXIA ZHOU for the degree of Doctor of Philosophy UNIVERSITY OF BATH Department of Architecture and Civil Engineering January 2012 COPYRIGHT Attention is drawn to the fact that copyright of this thesis rests with its author. A copy of this thesis has been supplied on condition that anyone who consults it is understood to recognise that its copyright rests with the author and that they must not copy it or use material from it except as permitted by law or with the consent of the author. This thesis may be made available for consultation within the University Library and may be photocopied or lent to other libraries for the purposes of consultation. Signature of Author........................................................... ii Acknowledgements The work in the thesis was carried out in the Department of Architecture and Civil Engineering at the University of Bath between January 2006 and January 2009. The author would like to thank Professor Pete Walker and Dr Dina D'Ayala, joint supervisors of this study. They have provided continuous support and professional guidance throughout the duration of the research. Their help, patience and time ensured that the project was completed successfully. The author would like to thank Professor Pete Walker in particular, who has been a great supervisor all the way through this long journey, not only contributing considerable expertise to the research, but also providing endless encouragement and support to help me through this most difficult time in my life. Special mention should be made to Dr Andrew Heath for designing the pneumatic loading system on the bond wrench test apparatus, and all of the laboratory staff in the department, Neil, Brian, Will, Sophie, Graham and Paul, who offered a big hand during the large amount of experimental work. -
Lime and Its Place in the 21St Century: Combining Tradition, Innovation, and Science in Building Preservation∗
International Building Lime Symposium 2005 Orlando, Florida, March 9 -11, 2005 LIME AND ITS PLACE IN THE 21ST CENTURY: COMBINING TRADITION, INNOVATION, AND SCIENCE IN BUILDING PRESERVATION∗ Lauren B. Sickels-Taves, Ph.D.1 Philip D. Allsopp, D.Arch, RIBA2 Abstract Lime is a long-established material in mortars and renders, with its use dating back centuries. Its properties are time-tested, both in-situ and in laboratories. However, lime’s marketability and the increased need for faster building in the 19th and 20th centuries decreased its widespread use. During this period, masonry integrity problems, and, later, sustainability concerns and increased mold risk were introduced into the built environment resulting from the widespread use of impervious materials including Portland cement for mortars and external renders. Evidence shows that lime has always been and remains a practical, sustainable, and healthy alternative to cement worthy of far more widespread deployment across the building industry. ∗ © Copyright NLA Building Lime Group 2005 The views presented in this paper are solely those of the authors. The National Lime Association (NLA) and the Building Lime Group assume no liability or responsibility for any errors, omissions, or other limitations in this paper or for any products, services, or methods presented. This paper is intended for use by professional personnel competent to evaluate the significance and limitations of the information provided and who will accept full responsibility for the application of this information. NLA and the Building Lime Group do not intend to infringe on any patent or other intellectual property right or induce any other party to do so, and thus users of this document are responsible for determining whether any method, technique, or technology described herein is protected by patent or other legal restriction. -
Experimental Study on Lime Mortar Using Flyash and Gallnut As Additives
Special Issue - 2016 International Journal of Engineering Research & Technology (IJERT) ISSN: 2278-0181 SNCIPCE - 2016 Conference Proceedings Experimental Study on Lime Mortar using Flyash and Gallnut As Additives B. Dhilipkumar1 M. Dhivakar Karthick2 Assistant Professor Assistant Professor Department of Civil Engineering Department of Civil Engineering Kongunadu College of Engineering & Technology Kongunadu College of Engineering & Technology Thottiam, Trichy Thottiam, Trichy Abstract— As concern the environmental impacts and high strength and tensile strength of lime mortar have been cost of cement which is widely used, clearly requires alternate studied. protective binder. But in the first civilization, lime is used as II. METHODOLOGY biodegradable binding material which is also composed of additives such as pozzolana and traditional herbs. In the present Lime is a binder which is in general, the purpose of the study lime mortar with composition of flyash as pozzolana binder is to hold the sand particles together and to fill the which enables mortar to set rapidly in the ratio of 1:1:2 voids in between the grains of sand. Hydraulic lime used in (lime:pozzolana:sand) as per IS:4098 – 1983. Also used extracts building construction. Sand is the most common aggregate in of kadukkai (gallnut) and palm’s jaggery in the proportion of 5%, 10% and 15% of the weight of binder. As the result, on mortars. the potable water should be used in appropriate addition of 5% herbal extract in pozzolanic lime mortar amount till attain required consistency. Flyash , kadukkai improves workability and increases tensile strength, also ( Terminalia chebula) and palm’s jaggery are additives of enhanced increased compressive strength about 55% compared lime mortar. -
Hydraulic Lime an Introduction
HYDRAULIC LIME AN INTRODUCTION Hydraulic lime was an important cementitious material before the arrival of Portland cement but it is little used now, except in conservation work. Production of good hydraulic lime is as much a craft as a technology, even more than ordinary lime but, with the decline in use of hydraulic lime, there are few skilled producers left and new producers often need to learn the required skills from scratch. Hydraulic lime hardens partly by reaction with water and so differs from other types of lime which harden by chemical reaction with carbon dioxide in the air. Hydraulic lime has properties intermediate between ordinary lime and Portland cement but is produced in a similar way to ordinary lime. In addition to containing calcium hydroxide, the chemical which makes up ordinary lime, hydraulic lime also contains calcium silicates similar to the main cementitious components of Portland cement. A cement with properties similar to hydraulic lime can also be obtained by mixing ordinary lime with a pozzolanic material. Hydraulic lime can be made stronger than ordinary lime and can be used in some applications for which ordinary lime is not suitable, particularly where water is present. In developing countries hydraulic lime is rarely produced. There is probably considerable potential for increased production in situations where Figure 1: Slaking. Hydrated lime is produced by adding water to quicklime. Portland cement is scarce or very expensive. Chenkumbe Hills Area, Malawi ©Practical However, in general, little mapping of reserves of Action/David Mather raw materials or assessment of their quality has been carried out. -
Potential of Using Wood Biomass Ash in Low-Strength Composites
materials Article Potential of Using Wood Biomass Ash in Low-Strength Composites Ana Bariˇcevi´c 1,* , Ivana Carevi´c 1, Jelena Šantek Bajto 1, Nina Štirmer 1 , Marija Bezinovi´c 1 and Keti Kristovi´c 2 1 Department of Materials, Faculty of Civil Engineering, University of Zagreb, Fra Andrije Kaˇci´caMioši´ca26, 10000 Zagreb, Croatia; [email protected] (I.C.); [email protected] (J.Š.B.); [email protected] (N.Š.); [email protected] (M.B.) 2 Trames Ltd., Šipˇcine2, 20000 Dubrovnik, Croatia; [email protected] * Correspondence: [email protected]; Tel.: +385-1-4639-536 Abstract: Reducing greenhouse gas emissions and dependence on fossil fuels is the cornerstone of all European climate and energy strategies. Consequently, renewable energy sources are becoming more competitive with fossil fuels. The largest source of bioenergy in the European Union is biomass-fired power plants. Therefore, the European coal phase-out strategy led to an increased use of wood biomass as a sustainable fuel, generating large amounts of wood biomass ash (WBA). In the research studies reported so far, WBA has been mainly used in cementitious composites. However, given the similarities between the chemical composition of WBA and hydraulic lime (HL), this research focused on its potential classification as a building lime. Overall, three different sources of fly WBA were considered for the preparation of binders as mixtures of WBA and coal fly ash (CFA) in different ratios. The contribution of each binder mixture on the paste and mortar properties was analyzed based on the chemical composition, setting time, volume stability, and contribution to the mortar strength (compressive and flexural). -
SOIL STABILIZATION USING LIME and FLY ASH N.Krithiga1, D.Pujitha *2,T
SOIL STABILIZATION USING LIME AND FLY ASH N.Krithiga1, D.Pujitha *2,T. Palayam*3 , A.revathy*4 1Assistant Professor(civil Eng),Department of Civil Engineering,Sri Muthukumaran Institute of Technology,*234 UG students, Department of Civil Engineering, ABSTRACT Now a days, inefficient properties of soils are a critical issue in engineering projects. In some cases, improve the characteristic of unsuitable soil is a fundamental step for making construction.Pavement structures on poor soil sub grades show early distress causing the premature failure of the pavement. Clayey soil usually have the potential to demonstrate undesirable engineering behaviour , such as low bearing capacity , high shrinkage and swell characteristics and high moisture susceptibility. Stablilsation of these soil is a usual practice for improving the strength.Soil stabilization performed the use of technique to adding a binder to the soil in order to improve the engineering performance of soil .This study reports the improvement in the strength of a locally available cohesive soil by addition of both lime and fly ash. Researches were illustrated that adding the additives leads to progress in workability and mechanical behaviour of soil after stabilization lime and fly ash as local natural and industrial resources were applied for chemical stabilization. Lime alone has traditionally been used in clay-bearing, highly cohesive soil whereas fly ash has been used to bind non-cohesive soil, granular or poorly cohesive soil. Fly ash is mainly used to stabilize the sub base or base course. 1 1. INTRODUCTION The swelling and shrinkage characteristic of expansive soil depend upon the percentage of moisture content in it. -
Technical Data Sheet Natural Hydraulic Lime (En 459-1)
TECHNICAL DATA SHEET NATURAL HYDRAULIC LIME (EN 459-1) Raw materials: Natural hydraulic lime is a hydraulic binder in powder-form, partially hydrated, that is obtained calcining limestones that contain between 15 and 20% of clay and other impurities, correctly denominated marls. During the calcination (aprox. 1200ºC, lower firing temperature than Portland cement) calcium reacts in the kiln with the clay minerals to produce silicates, aluminates and ferro-aluminates that enable the hydraulic lime to set faster than quicklime or slaked lime and without exposure to air (including under water). Any unreacted calcium is transformed into calcium hydroxide. This part of the lime reacts non-hydraulic, precise water or environmental humidity and carbon dioxide gas of the air, and is responsible for the progressive resistance of the natural hydraulic lime. It varies according to its hydraulic index. Special mortar properties made with natural hydraulic lime, beneficial for RESTORATION AND ECO-BUILDING: Great plasticity (therefore easy to progress), fort adhesion in diverse materials and surfaces, great capacity of water retention, low tendency of cracking (low modulus of elasticity), good durability, good water-impermeability, permeability to water steam, allows buildings to breathe (the less hydraulic the most) and has a good aspect. Lime mortars are up to 34% more insulating than those of cement. Natural hydraulic limes are free of additives and have a low index of radiation. Technical qualities of our NHL 5 NHL 3,5 NHL 3,5 blanca NHL 2 natural -
Mechanical and Durability Performance Improvement of Natural Hydraulic Lime-Based Mortars by Lithium Silicate Solution
materials Article Mechanical and Durability Performance Improvement of Natural Hydraulic Lime-Based Mortars by Lithium Silicate Solution Zijian Song 1,2,*, Zhongyuan Lu 1,* and Zhenyu Lai 1 1 State Key Laboratory for Environment-Friendly Energy Materials, School of Materials Science and Engineering, Southwest University of Science and Technology, Mianyang 621010, China; [email protected] 2 Department of Material Engineering, Mianyang Vocational and Technical College, Mianyang 621000, China * Correspondence: [email protected] (Z.S.); [email protected] (Z.L.) Received: 21 October 2020; Accepted: 19 November 2020; Published: 23 November 2020 Abstract: Natural hydraulic lime (NHL) as a building material has been widely used to restore the historic structure. However, the slow growth rate of strength and durability limits its engineering application. In this work, the NHL-based mortars were pretreated by lithium silicate (LS) solution impregnation and surface spraying. The results show that the compressive strength, surface hardness, and freeze-thaw cycle (FTC) resistance of NHL-based mortar were greatly improved after LS pretreatment. Specifically, the compressive strengths of the sample increased by about 32.7–52.0%. LS was sprayed on the sample’s surface (about 0.2 kg/m2) and the surface hardness increased by up to 10 grades. Compared with the control samples, the weight loss of treated samples decreased by about 31.6–43.8%. A rehydration process to generate the hydrated calcium silicate gel (C-S-H) was observed between calcium hydroxide (CH) and LS, which can decrease the sample’s porosity and form a silicate coating on the surface. With an increase in the concentration of LS, the macropores (50–10,000 nm) content decreased, while the mesopores (10–50 nm) and nanopores (less than 10 nm) increased. -
Influences Affecting Compressive Strength of Modern Non-Hydraulic Lime Mortars Used in Masonry Conservation
Transactions on the Built Environment vol 55, © 2001 WIT Press, www.witpress.com, ISSN 1743-3509 Influences affecting compressive strength of modern non-hydraulic lime mortars used in masonry conservation J. Valek & P.J.M. Bartos Advanced Concrete and Masonry Centre, University of Paisley, Scotland Abstract Non-hydraulic lime based mortars are currently more and more often used for the repair of historic masonry. They are presumed to be compatible with the original mortarlmasonry and their properties are not always evaluated, mainly due to a lack of research into mortars produced in a traditional manner. Influences of curing conditions, quality of mixing and water content on compressive strength of a non-hydraulic lime mortar mix made of lime putty were reviewed and examined. The mortar specimens were prepared with various water contents, cured in outdoor and indoor conditions and tested after 1, 2, 4 and 6 months. Phenolphthalein pH indictor was used to measure the carbonation depth. The strongest mortar specimens were from the indoor ageing condition although the mortar was less carbonated. The addition of water into the fresh mix increased porosity and lowered the compressive strength, however there were other influences which affected this relationship. 1 Introduction In conservation practice there are two main ways to design a new repair mortar. The first one is based on the traditional conservation approach when the new mortar is a copy reproducing the original mortars as close as possible. The second one is more scientifically based, involving a detailed testing of properties of new and original mortars in order to ensure their compatibility.