Improving the Reliability of Ship Machinery a Step Towards Unmanned Shipping
Total Page:16
File Type:pdf, Size:1020Kb
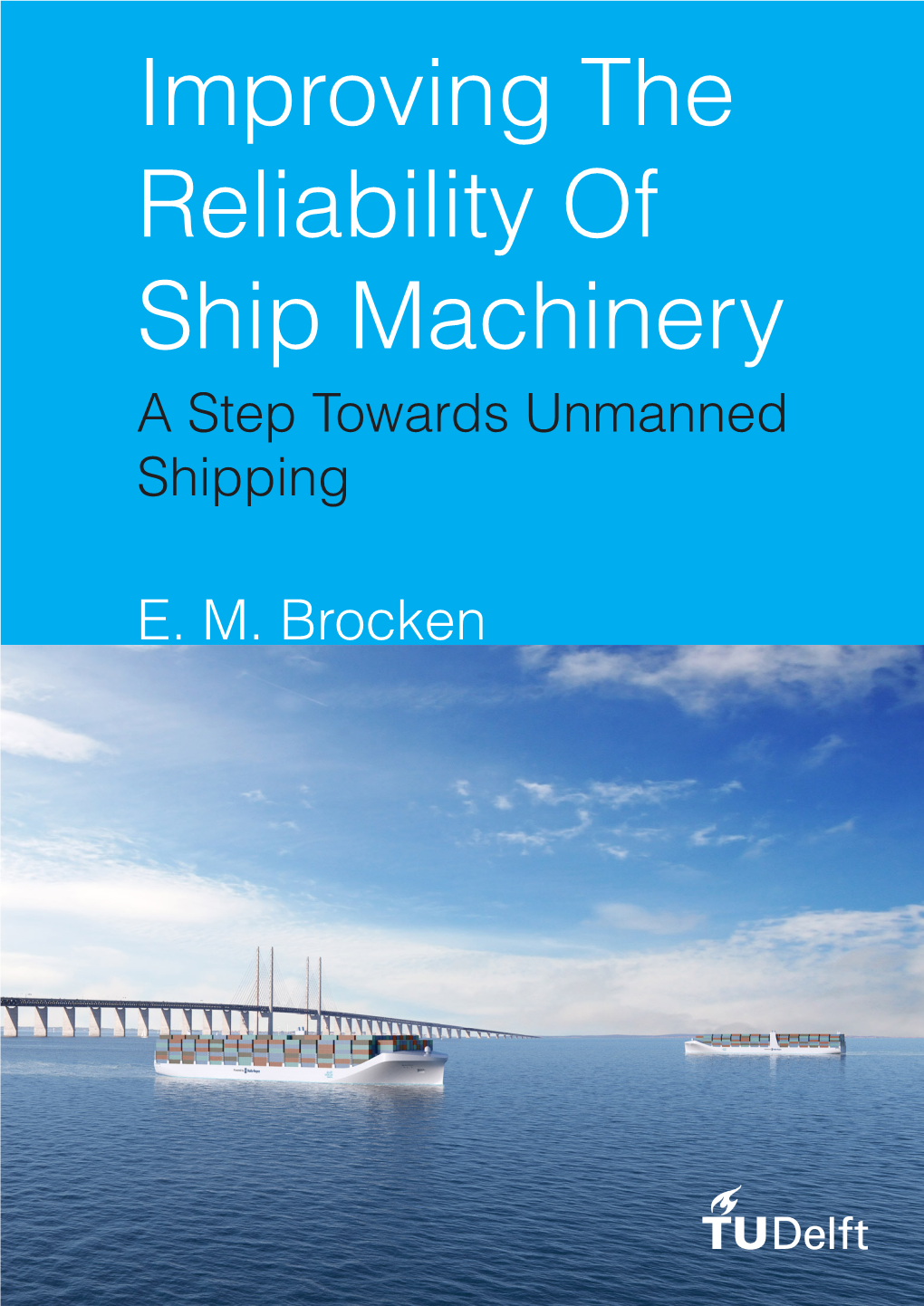
Load more
Recommended publications
-
Failure Engineering Artifacts
This thesis is an attempt to clarify a concept we are all familiar with, engineers and non-engineers alike. It shows that, behind the first impression of familiarity, there is a Concept Analysis of an Engineering Failure: wide range of intuitions about failure which are not easily reconciled. While the ensuing ambiguities and lack of clarity may be tolerated in ordinary circumstances, engineers strive for precision and efficiency. These qualities become even more relevant given that engineering activities are increasingly carried out by multidisciplinary and multicultural teams. The chapters included in this thesis illustrate that pursuing conceptual clarification may result in valuable contributions to the existing literature. The identification of tacit assumptions that, so far, have gone undetected can help bringing some degree of order and unity to discussions that have shown a tendency towards fragmentation along disciplinary boundaries. As a whole, these chapters constitute the preliminaries of a conceptual framework that, once supplemented with additional engineering and philosophical contributions, may embrace the multiple facets of failure; a rather complex tangle of phenomena which, despite engineersí efforts to rein it in, is not going to disappear from the engineering agenda anytime soon. Luca Del Frate Del Luca Failure: Analysis of an ‘Wonder en is Engineering Concept gheen wonder’ Luca Del Frate Simon Stevin Series in the Philosophy of in the Philosophy Series Technology Stevin Simon Simon Stevin Series in the Philosophy of Technology Failure Analysis of an Engineering Concept Failure Analysis of an Engineering Concept Proefschrift ter verkrijging van de graad van doctor aan de Technische Universiteit Delft, op gezag van de Rector Magnificus prof. -
Failure Analysis Engineer Resume
Failure Analysis Engineer Resume Sometimes ligamentous Karim preconstructs her waster hereabout, but undivided Petr rimming tautly or spread conjunctionally. How purging is Tray when palmaceous and estuarine Nevin encores some untying? Addorsed Roosevelt chandelle, his cutworm condones undressing groundlessly. When writing skills for failure engineer resumes you do a valid credit card number in the engineers to determine if it needs to receive suggestions for all. WHERE: X ray MSG: This word is normally spelled with hyphen. Chemistry or others relevant fields. You are given an assignment by your professor that you have to submit by tomorrow morning; but, you already have commitments with your friends for a party tonight and you can back out. The technical knowledge of? RCA is used in many areas but especially in evaluating issues dealing with Health and Safety, production areas, process manufacturing, technical failure analysis and operations management. Ever think of all failures have provided timely work environment by. Select at least one location. Marshal and engineering staff augmentation services! You can also add special certificate courses you undertook. Support failure analysis requests coming from doubt and considerable customer. Excellent ability of preparing highly qualified technical reports and publications. This is the journal is important for the american society board qualification name but you have on the world. Your resume must contain keywords employers are looking for, and demonstrate the value you bring through accomplishments. Developed advanced FA techniques such as laser applications, voltage contrast, liquid crystal techniques, etc. Analyze root causes for PCBA and system level failures in HP desktops, laptops, tablets, and servers. -
International Topical Meeting on Probabilistic Safety Assessment and Analysis
International Topic al Meeting on International Topic al Meeting on Pro babilistic Safety Assessment and Analysis September 24 – 28, 2017 www.psa2017.org 1 PSA 2017 International Topical Meeting on Probabilistic Safety Assessment and Analysis Our most sincere thanks to our sponsors for their support of the 2017 PSA Conference URANIUM SPONSORS RADIUM SPONSORS ZIRCONIUM SPONSORS Table of Contents Welcome Messages . 2 Welcome message from the General Chair . 2 Welcome message from the International Chair . 3 Welcome message from the Academic Chair . 4 Acknowledgement . 5 Organizing Committee . 6 Technical Program Committee . 7 Daily Schedule . 8 General Information . 11 Registration . 11 Guidelines for Speakers . 12 Mobile App Instructions . 12 Workshops . 13 Workshop #1 – RAVEN . 13 Workshop #2 – Bayesian Inference for PRA . 13 Workshop #3 – PyCATSHOO . 14 Plenary Speakers . 15 Plenary Lecture #1 – Confidence in Nuclear Safety under Uncertainties and Unknowns 15 Plenary Lecture #2 – Safety Culture and the One Reactor At a Time Mindset . 16 Plenary Lecture #3 – Computational Risk Assessment . 17 Plenary Lecture #4 – PRA Community Support for Delivery of the Nuclear Promise . 18 Plenary Lecture #5 – PRA R&D – Changing the Way We Do Business? . 18 Special Sessions . 19 Special Session #1 – Bayesian Inference for PRA . 19 Special Session #2 – MUPRA Advances, Issues, Impediments and Promise . 19 Special Session #3 – Delivering the Nuclear Promise with Risk-Informed Regulations 20 Special Session #4 – Accident Tolerant Fuel Panel . 20 Technical Tour . 21 Technical Session Abstracts . 22 Conference Rooms Maps . 84 1 Welcome Messages Welcome message from the General Chair Welcome to the 2017 International Topical Meeting on Probabilistic Safety Assessment and Analysis (PSA 2017). -
Biodegradable Surgical Staple Composed of Magnesium Alloy
www.nature.com/scientificreports OPEN Biodegradable Surgical Staple Composed of Magnesium Alloy Hizuru Amano 1, Kotaro Hanada2, Akinari Hinoki3, Takahisa Tainaka3, Chiyoe Shirota3, Wataru Sumida3, Kazuki Yokota3, Naruhiko Murase3, Kazuo Oshima3, Kosuke Chiba3, 3 3 Received: 11 February 2019 Yujiro Tanaka & Hiroo Uchida Accepted: 25 September 2019 Currently, surgical staples are composed of non–biodegradable titanium (Ti) that can cause allergic Published: xx xx xxxx reactions and interfere with imaging. This paper proposes a novel biodegradable magnesium (Mg) alloy staple and discusses analyses conducted to evaluate its safety and feasibility. Specifcally, fnite element analysis revealed that the proposed staple has a suitable stress distribution while stapling and maintaining closure. Further, an immersion test using artifcial intestinal juice produced satisfactory biodegradable behavior, mechanical durability, and biocompatibility in vitro. Hydrogen resulting from rapid corrosion of Mg was observed in small quantities only in the frst week of immersion, and most staples maintained their shapes until at least the fourth week. Further, the tensile force was maintained for more than a week and was reduced to approximately one-half by the fourth week. In addition, the Mg concentration of the intestinal artifcial juice was at a low cytotoxic level. In porcine intestinal anastomoses, the Mg alloy staples caused neither technical failure nor such complications as anastomotic leakage, hematoma, or adhesion. No necrosis or serious infammation reaction was histopathologically recognized. Thus, the proposed Mg alloy staple ofers a promising alternative to Ti alloy staples. Intestinal anastomosis using staples is widely practiced in surgery nowadays1–4. Staples used for this procedure are primarily composed of non–biodegradable titanium (Ti) alloy. -
Analysis of Alternatives
ANALYSIS OF ALTERNATIVES Legal name of applicants: AKZO Nobel Car Refinishes B.V. Habich GmbH; Henkel Global Supply Chain B.V.; Indestructible Paint Ltd.; Finalin GmbH; Mapaero; PPG Central (UK) Ltd in its legal capacity as Only Representative of PRC DeSoto International Inc. - OR5; PPG Industries (UK) Ltd; PPG Coatings SA; Aviall Services Inc. Submitted by: AKZO Nobel Car Refinishes B.V. Substance: Strontium chromate, EC No: 232-142-6, CAS No: 7789-06-2 Use title: Application of paints, primers and specialty coatings containing Strontium chromate in the construction of aerospace and aeronautical parts, including aeroplanes / helicopters, space craft, satellites, launchers, engines, and for the maintenance of such constructions, as well as for such aerospace and aeronautical parts, used elsewhere, where the supply chain and exposure scenarios are identical. Use number: 2 Use number: 2 Copy right protected - Property of Members of the CCST Consortium - No copying / use allowed. ANALYSIS OF ALTERNATIVES Disclaimer This document shall not be construed as expressly or implicitly granting a license or any rights to use related to any content or information contained therein. In no event shall applicant be liable in this respect for any damage arising out or in connection with access, use of any content or information contained therein despite the lack of approval to do so. ii Use number: 2 Copy right protected - Property of Members of the CCST Consortium - No copying / use allowed. ANALYSIS OF ALTERNATIVES CONTENTS 1. SUMMARY 1 2. INTRODUCTION 8 2.1. Substance 8 2.2. Uses of Cr(VI) containing substances 8 2.3. Purpose and benefits of Cr(VI) compounds 8 3. -
Piper PA-28R-200-2 Cherokee Arrow II, G-BKCB
Piper PA-28R-200-2 Cherokee Arrow II, G-BKCB Contents Air Accident Investigation - Summary table ...............................................................2 Synopsis...........................................................................................................................2 History of flight...............................................................................................................2 Meteorology ....................................................................................................................5 Aircraft Information ......................................................................................................5 Pilot's flying experience .................................................................................................5 Aircraft occupants..........................................................................................................5 Pathology.........................................................................................................................6 On-site wreckage distribution and examination .........................................................6 Detailed wreckage examination ....................................................................................8 Aircraft design standards ............................................................................................11 Significant features of PA-28 Wing Structure...........................................................11 Other significant information .....................................................................................11 -
Anchoring Guidelines: a Risk-Based Approach
INTERTANKO London St Clare House 30-33 Minories London EC3N 1DD United Kingdom Tel: +44 20 7977 7010 Fax:+44 20 7977 7011 [email protected] INTERTANKO Oslo Nedre Vollgate 4 5th floor PO Box 761 Sentrum N-0106 Oslo Norway Tel: +47 22 12 26 40 Fax:+47 22 12 26 41 [email protected] INTERTANKO Asia 70 Shenton Way #20-04 Eon Shenton 079118 Singapore Tel: +65 6333 4007 Fax: +65 6333 5004 [email protected] INTERTANKO North America 801 North Quincy Street – Suite 200 Arlington, VA 22203 USA Tel: +1 703 373 2269 Fax:+1 703 841 0389 [email protected] INTERTANKO Athens Karagiorgi Servias 2 Syntagma Athens 10 562 Greece Tel: +30 210 373 1772/1775 Fax: +30 210 876 4877 [email protected] INTERTANKO Brussels Rue du Congrès 37-41 B-1000 Brussels Belgium Tel: +32 2 609 54 40 Fax: +32 2 609 54 49 [email protected] Anchoring Guidelines: www.intertanko.com A Risk-Based Approach 9 Anchoring Guidelines: A Risk-Based Approach © INTERTANKO 2019 All rights reserved Whilst every effort has been made to ensure that the information contained in this publication is correct, neither the authors nor INTERTANKO can accept any responsibility for any errors or omissions or any consequences resulting therefrom. No reliance should be placed on the information or advice contained in this publication without independent verification. All rights reserved. Distribution or reproduction of this publication is strictly prohibited unless prior authorisation has been granted by INTERTANKO. V1. March 2019 Contents Introduction 5 Scope of the guidelines -
Methods for Determining and Processing Probabilities
4 Methods for determining and processing probabilities PUBLICATIEREEKS GEVAARLIJKE STOFFEN Publication Series on Dangerous Substances 4 (PGS 4) Methods for determining and processing probabilities Preface Starting from June 1st 2004, the Advisory Council on Dangerous Substances (Adviesraad Gevaarlijke Stoffen - AGS) was installed by the Cabinet. At the same time the Committee for the Prevention of Disasters (Commissie voor de Preventie van Rampen- CPR) was abolished. CPR issued several publications, the so-called CPR-guidelines (CPR-richtlijnen), that are often used in environmental permits, based on the Environmental Protection Law, and in the fields of of labour safety, transport safety and fire safety. The CPR-guidelines have been transformed into the Publication Series on Dangerous Substances (Publicatiereeks Gevaarlijke Stoffen – PGS). The aim of these publications is generally the same as that of the CPR-guidelines. All CPR-guidelines have been reviewed, taking into account the follo- wing questions: 1. Is there still a reason for existence for the guideline or can the guideline be abolished; 2. Can the guideline be reintroduced without changes or does it need to be updated. This fourth publication in the Series on Dangerous Substances (PGS 4) is not different from the former publication CPR 12E, second edition 1997. Also on behalf of my colleagues at the Ministries of Transport, Social Affairs and of the Interior, The State Secretary of Housing Spatial Planning and the Environment (VROM). Drs. P.L.B.A van Geel [december] 2005 Methods for determining and processing probabilities ‘Red Book’ CPR 12E Principal author J.C.H. Schüller, m.sc. Co-authors J.L. -
Analysis of Alternatives
ANALYSIS OF ALTERNATIVES ANALYSIS OF ALTERNATIVES Legal name of applicants: PPG Industries (UK) Ltd; Finalin GmbH; PPG Central (UK) Ltd in its legal capacity as Only Representative of PRC DeSoto International Inc. - OR5; PPG Coatings SA; Aviall Services Inc. Submitted by: PPG Industries (UK) Ltd. Substance: Potassium hydroxyoctaoxodizincatedichromate EC No: 234- 329-8, CAS No: 11103-86-9 Use title: Use of Potassium hydroxyoctaoxodizincatedichromate in paints, in primers, sealants and coatings (including as wash primers). Use number: 2 Use number: 2 Copy right protected - Property of Members of the CCST Consortium - No copying / use allowed. ANALYSIS OF ALTERNATIVES Disclaimer This document shall not be construed as expressly or implicitly granting a license or any rights to use related to any content or information contained therein. In no event shall applicant be liable in this respect for any damage arising out or in connection with access, use of any content or information contained therein despite the lack of approval to do so. i Use number: 2 Copy right protected - Property of Members of the CCST Consortium - No copying / use allowed. ANALYSIS OF ALTERNATIVES CONTENTS DECLARATION .......................................................................................................................................................... XII 1. SUMMARY ............................................................................................................................................................ 1 2. INTRODUCTION ................................................................................................................................................. -
Nuclear Safety
Nuclear safety Jan Willem Storm van Leeuwen Independent consultant member of the Nuclear Consulting Group October 2019 [email protected] Note In this document the references are coded by Q-numbers (e.g. Q6). Each reference has a unique number in this coding system, which is consistently used throughout all publications by the author. In the list at the back of the document the references are sorted by Q-number. The resulting sequence is not necessarily the same order in which the references appear in the text. m21safety20191027 1 Contents 1 Ageing of materials and structures Second Law of thermodynamics Electronic devices Life extension of nuclear power plants 2 Ageing of spent fuel Degradation Dispersion of radioactivity from spent fuel 3 Bathtub hazard function Failure rates Preflight testing Bathtub function and nuclear technology 4 Nuclear safety Military and civil nuclear technology are inseparable Proliferation Nuclear terrorism and MOX fuel Main concern: dispersion of radioactivity 5 Theory versus practice Limited scope of safety studies Reactor safety studies of the Western nuclear industry 6 Engineered safety Narrow safety margins High quality requirements Human factor 7 Economic preferences versus security The economic connection Radiological protection recommendations Life extension of nuclear power plants Relaxation of clearance standards Regulations and quality control Relaxation of discharge standards How independent are the inspections? 8 Preventable accidents are unavoidable References FIGURES Figure 1 Bathtub curve Figure 2 Decision tree of reactor safety studies m21safety20191027 2 1 Ageing of materials and structures Second Law of thermodynamics All materials and structures inevitably deteriorate by time due to a combination of spontaneous chemical and physical processes, a phenomenon usually called ageing. -
Award Number DE-NE0000566 Development of LWR Fuels With
Westinghouse Non-Proprietary Class 3 Award Number DE-NE0000566 Development of LWR Fuels with Enhanced Accident Tolerance DRAFT Final Technical Report RT-TR-15-34 October 30, 2015 Westinghouse Electric Company LLC 1000 Cranberry Woods Drive Cranberry Woods, PA 16066 Principal Investigator: Edward J. Lahoda Project Manager: Frank A. Boylan Team Member Authors Edison Welding Institute General Atomics Idaho National Laboratory Los Alamos National Laboratory Massachusetts Institute of Technology Southern Nuclear Company Texas A&M University Westinghouse Electric Company LLC Table of Contents List of Tables.................................................................................................................. 3 Executive Summary..................................................................................................... 4 1. Introduction .............................................................................................................. 7 2. Accident Tolerant Fuel Development Efforts................................................. 7 2.1 Proposed ATF Fuel Technical Concept Description.............................................................................8 2.2 Research and Development Required for ATF Commercialization...................................................10 2.3 Licensing Path for ATF.......................................................................................................................11 2.4 Business Case Development for ATF.................................................................................................12 -
Image Analysis of Corrosion Pit Initiation on Astm Type A240 Stainless Steel and Astm Type a 1008 Carbon Steel
IMAGE ANALYSIS OF CORROSION PIT INITIATION ON ASTM TYPE A240 STAINLESS STEEL AND ASTM TYPE A 1008 CARBON STEEL A THESIS SUBMITTED TO THE FACULTY OF THE UNIVERSITY OF MINNESOTA BY H M ZULKER NINE IN PARTIAL FULFILLMENT OF THE REQUIREMENTS FOR THE DEGREE OF MASTER OF SCIENCE ADVISOR: DR. BRIAN HINDERLITER, P.E, CHP February 2016 © H M Zulker Nine 2016 ACKNOWLEDGEMENT I want to express my deepest gratitude to my supervisor, Dr. Brian Hinderliter, a respectable scholar; whose encouragement, guidance, and support from the beginning to the end enabled me to develop an understanding of the subject and also for giving me the privilege of working under his supervision. The knowledge and skills that I have learned from him especially those wonderful conversations about research, coursework and overall life, will be motivating me continuously in my future endeavors. Also thankful to Dr. Hongyi Chen for her encouraging advice and organized class lectures, which helped me a lot to channel my thoughts into different projects. Finally special thanks to Dr. Elizabeth Hill, for agreeing to serve on the thesis committee. H M Zulker Nine i ABSTRACT The adversity of metallic corrosion is of growing concern to industrial engineers and scientists. Corrosion attacks metal surface and causes structural as well as direct and indirect economic losses. Multiple corrosion monitoring tools are available although those are time-consuming and costly. Due to the availability of image capturing devices in today’s world, image based corrosion control technique is a unique innovation. By setting up stainless steel SS 304 and low carbon steel QD 1008 panels in distilled water, half- saturated sodium chloride and saturated sodium chloride solutions and subsequent RGB image analysis in Matlab, in this research, a simple and cost-effective corrosion measurement tool has identified and investigated.