Multi-Agent Simulation Environment for Logistics Warehouse Design Based on Self-Contained Agents
Total Page:16
File Type:pdf, Size:1020Kb
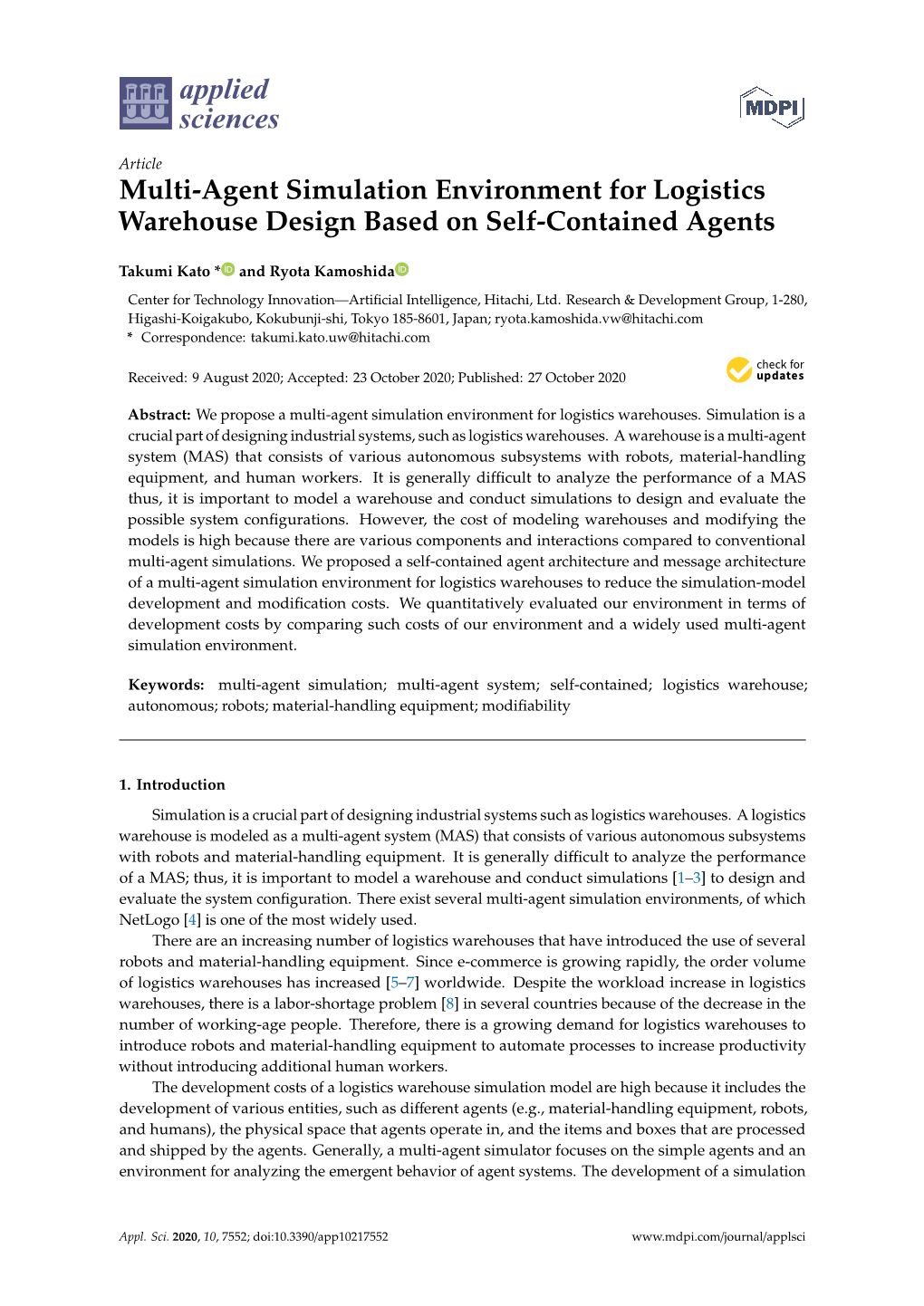
Load more
Recommended publications
-
Coupling Environmental, Social and Economic Models to Understand Land-Use Change Dynamics in the Mekong Delta
ORIGINAL RESEARCH published: 30 March 2016 doi: 10.3389/fenvs.2016.00019 Coupling Environmental, Social and Economic Models to Understand Land-Use Change Dynamics in the Mekong Delta Alexis Drogoul 1, 2*, Nghi Q. Huynh 3, 4 and Quang C. Truong 3, 5 1 UMI 209 UMMISCO, IRD/UPMC/Sorbonne Universités, Paris, France, 2 ICT Lab, University of Science and Technology of Hanoi, Hanoi, Vietnam, 3 PDI-MSC, IRD/UPMC/Sorbonne Universités, Paris, France, 4 CTU/IRD JEAI DREAM, CICT, Can Tho University, Can Tho, Vietnam, 5 CTU/IRD JEAI DREAM, CENRES, Can Tho University, Can Tho, Vietnam The Vietnamese Mekong Delta has undergone in recent years a considerable transformation in agricultural land-use, fueled by a boom of the exportation, an increase of population, a focus on intensive crops, but also environmental factors like sea level rise or the progression of soil salinity. These transformations have been, however, largely misestimated by the 10-year agricultural plans designed at the provincial levels, on the predictions of which, though, most of the large-scale investments (irrigation infrastructures, protection against flooding or salinity intrusion, and so on) are normally Edited by: planned. This situation raises the question of how to explain the divergence between Christian E. Vincenot, Kyoto University, Japan the predictions used as a basis for these plans and the actual situation. Answering it Reviewed by: could, as a matter of fact, offer some insights on the dynamics at play and hopefully Costica Nitu, allow designing them more accurately. The dynamics of land-use change at a scale University Politehnica of Bucharest, Romania of a region results from the interactions between heterogeneous actors and factors at Qing Tian, different scales, among them institutional policies, individual farming choices, land-cover George Mason University, USA and environmental changes, economic conditions, social dynamics, just to name a few. -
An Overview of Simulation Software for Non-Experts to Perform Multi-Robot Experiments
An Overview of Simulation Software for Non-Experts to Perform Multi-Robot Experiments Nur Raihan Ramli1, Sazalinsyah Razali2 Mashanum Osman Robotics and Industrial Automation Research Group Creative Media Lab Center of Excellence for Robotics and Industrial Automation Center for Advanced Computing Technologies Universiti Teknikal Malaysia Melaka Universiti Teknikal Malaysia Melaka 76100 Durian Tunggal, Melaka, Malaysia 76100 Durian Tunggal, Melaka, Malaysia Email: [email protected], [email protected] Email: [email protected] Abstract—Simulation is an initial approach to determine instance, Swarm, Webots, NetLogo, Player/Stage [4], V-REP the experiment feasibility, especially for a complex robotics [5], and Gazebo. environment. This paper give an overview of five simulation software for non-expert developers to quickly perform the multi- robots simulation. In the advanced robotics field, further research II. RELATED WORKS requires simulations, especially which involve multi-robots as to There is a variety of agent-based simulation, and robotics run quickly. There are many robotics simulation software exist. simulation software can be used to perform multi-robot experi- In this paper, we focus only on five simulation software, namely NetLogo, GAMA Platform, Webots, Player/Stage and V-REP. To ments. For agent-based simulation, there are Repast, MASON, distinguish the differences between this five tools, we made a Swarm, and NetLogo. Instead of choosing Repast, MASON, comparison of general information and other criteria. Then, we and Swarm, we choose NetLogo as it is suitable for building rated them based on the criteria and user necessity. Therefore, a multi-agent complex environment. Besides that, Swarm is the users can easily know which software is suitable for them to extremely not easy to install and run successfully, and it is use. -
Application of Model-Driven Engineering to Multi-Agent Systems : a Language to Model Behaviors of Reactive Agents Paulo Pimenta
Application of model-driven engineering to multi-agent systems : a language to model behaviors of reactive agents Paulo Pimenta To cite this version: Paulo Pimenta. Application of model-driven engineering to multi-agent systems : a language to model behaviors of reactive agents. Multiagent Systems [cs.MA]. Université Montpellier, 2017. English. NNT : 2017MONTS031. tel-01905831 HAL Id: tel-01905831 https://tel.archives-ouvertes.fr/tel-01905831 Submitted on 26 Oct 2018 HAL is a multi-disciplinary open access L’archive ouverte pluridisciplinaire HAL, est archive for the deposit and dissemination of sci- destinée au dépôt et à la diffusion de documents entific research documents, whether they are pub- scientifiques de niveau recherche, publiés ou non, lished or not. The documents may come from émanant des établissements d’enseignement et de teaching and research institutions in France or recherche français ou étrangers, des laboratoires abroad, or from public or private research centers. publics ou privés. Délivré par l'Université de Montpellier Préparée au sein de l'école doctorale I2S Et de l'unité de recherche UR GREEN - Cirad Spécialité: Informatique Présentée par Paulo Pimenta Application of Model-driven engineering to multi-agent systems: a language to model behaviors of reactive agents Soutenue le 5 Janvier 2017 devant le jury composé de: M. Jacques Ferber Professseur Université de Montpellier Pres. du Jury M. Jean-Pierre Müller HDR CIRAD Dir. de thèse M. David Hill Professseur Université Blaise-Pascal Rapporteur M. Jean-Michel Bruel Professseur Université de Toulouse Rapporteur M. Mamadou Kaba Traore Mâitre de conference/HDR Université Blaise Pascal Examinateur M. Fabien Michel Mâitre de conference/HDR Université de Montpellier Examinateur M. -
Gamagram: Graphical Modeling with the GAMA Platform Patrick Taillandier
GAMAGraM: Graphical modeling with the GAMA platform Patrick Taillandier To cite this version: Patrick Taillandier. GAMAGraM: Graphical modeling with the GAMA platform. The 4th Interna- tional Conference on Complex Systems and Applications, Jun 2014, France. 6 p. hal-01055569 HAL Id: hal-01055569 https://hal.archives-ouvertes.fr/hal-01055569 Submitted on 13 Aug 2014 HAL is a multi-disciplinary open access L’archive ouverte pluridisciplinaire HAL, est archive for the deposit and dissemination of sci- destinée au dépôt et à la diffusion de documents entific research documents, whether they are pub- scientifiques de niveau recherche, publiés ou non, lished or not. The documents may come from émanant des établissements d’enseignement et de teaching and research institutions in France or recherche français ou étrangers, des laboratoires abroad, or from public or private research centers. publics ou privés. Proceedings of ICCSA 2014 Normandie University, Le Havre, France - June 23-26, 2014 GAMAGRAM: GRAPHICAL MODELING WITH THE GAMA PLATFORM Patrick Taillandier ∗† Abstract. These last years have seen the multiplication of plat- The paper is organized as follows: Section 2 presents forms dedicated to the conception and simulation of agent-based the context of this work, in particular the existing agent- models for studying complex systems. If these platforms allowed based modeling platforms and the graphical modeling lan- to democratize this modeling approach, they are often complex to guages. Section 3 is dedicated to the presentation of the use by non-computer scientists as most of them require to define GAMAGraM plugin. At last, Section 4 concludes and models by writing numerous code lines. -
Thesis Title
Délivré par l'Université de Montpellier Préparée au sein de l'école doctorale I2S Et de l'unité de recherche UR GREEN - Cirad Spécialité: Informatique Présentée par Paulo Pimenta Application of Model-driven engineering to multi-agent systems: a language to model behaviors of reactive agents Soutenue le 5 Janvier 2017 devant le jury composé de: M. Jacques Ferber Professseur Université de Montpellier Pres. du Jury M. Jean-Pierre Müller HDR CIRAD Dir. de thèse M. David Hill Professseur Université Blaise-Pascal Rapporteur M. Jean-Michel Bruel Professseur Université de Toulouse Rapporteur M. Mamadou Kaba Traore Mâitre de conference/HDR Université Blaise Pascal Examinateur M. Fabien Michel Mâitre de conference/HDR Université de Montpellier Examinateur M. Jaime Simao Sichman Mâitre de conference Universidade de São Paulo Invité M. Pierre Bommel Docteur CIRAD Invité iii “Façamos da interrupção um caminho novo. Da queda um passo de dança, do medo uma escada, do sonho uma ponte, da procura um encontro” Fernando Sabino v Abstract Many users of multi-agent systems (MAS) are very commonly disinclined to model and simulate using current MAS platforms. More specifically, modeling the dynamics of a system (in particular the agents’ behaviors) is very often a challenge to MAS users. This issue is more often observed in the domain of socio-ecological systems (SES), because SES domain experts are rarely pro- grammers. Indeed, the majority of MAS platforms were not conceived taking into consideration domain-experts who are non-programmers. Most current MAS tools are not dedicated to SES, or nor do they possess an easily understan- dable formalism to represent the behaviors of agents. -
Towards an Agent-Based Manufacturing Control Strategy: a Simulation Study Mechanical Engineering
Towards an agent-based manufacturing control strategy: a simulation study Guilherme Cordeiro Lopes Thesis to obtain the Master of Science Degree in Mechanical Engineering Supervisors: Prof. João Carlos Prata dos Reis Prof. Susana Margarida da Silva Vieira Examination Committee Chairperson: Prof. Paulo Jorge Coelho Ramalho Oliveira Supervisor: Prof. João Carlos Prata dos Reis Members of the Committee: Prof. João Manuel Gouveia de Figueiredo Prof. Carlos Baptista Cardeira November 2018 ii Aos meus pais, aos meus avos.´ iii iv Acknowledgments To Professor Joao˜ Reis and Susana Vieira, for all the guidance, support and availability throughout the thesis. To my family for always supporting and encouraging me to go further. A special thank you to my parents and grandparents, to whom I dedicate this thesis, for all they have given me so far. They are the base support of my life. To Daniela, all these years always by my side, giving me the strength to overcome the hardest moments and the joy of sharing the happiest ones. To all my friends who helped turning this journey into the best years of my life. v vi Resumo Com o advento de tecnologias emergentes como a Internet das Coisas, redes de sensores sem fios, computac¸ao˜ em nuvem, Internet movel´ e Inteligenciaˆ Artificial, e a sua introduc¸ao˜ no mundo da industria,´ um novo paradigma chegou: a quarta revoluc¸ao˜ industrial. Com o objectivo de usar estas novas tecnolo- gias para alcanc¸ar a fabrica´ inteligente, flex´ıvel e reconfiguravel´ do futuro, capaz de produzir produtos customizados e em pequenos lotes de forma eficiente e rentavel,´ alguns sistemas avanc¸ados de con- trolo de manufactura temˆ sido propostos. -
A Multi-Modal Urban Traffic Agent-Based Framework to Study Individual Response to Catastrophic Events
CORE Metadata, citation and similar papers at core.ac.uk Provided by Open Archive Toulouse Archive Ouverte Open Archive Toulouse Archive Ouverte OATAO is an open access repository that collects the work of Toulouse researchers and makes it freely available over the web where possible This is an author’s version published in: http://oatao.univ-toulouse.fr/22662 Official URL DOI : https://doi.org/10.1007/978-3-030-03098-8_28 To cite this version: Chapuis, Kévin and Taillandier, Patrick and Gaudou, Benoit and Drogoul, Alexis and Daudé, Eric A Multi-modal Urban Traffic Agent-Based Framework to Study Individual Response to Catastrophic Events. (2018) In: 21st International Conference on Principles and Practice of Multi-Agent Systems (PRIMA 2018), 29 October 2018 - 2 November 2018 (Tokyo, Japan). Any correspondence concerning this service should be sent to the repository administrator: [email protected] A multi-modal urban traffic agent-based framework to study individual response to catastrophic events Kevin Chapuis 1,4, Patrick Taillandier 2, Benoit Gaudou 1,3,4, Alexis Drogoul 1,4, and Eric Daud´e 5 1 Sorbonne University, IRD, UMMISCO, F-93143, Bondy, France 2 MIAT, University of Toulouse, INRA, Castanet-Tolosan, France 3 University Toulouse Capitole, IRIT, Toulouse, France 4 USTH - AVAST, ICTLab, Hanoi, Vietnam 5 CNRS, Rouen University, UMR IDEES, Rouen, France Abstract. Urban traffic is made of a variety of mobility modes that have to be taken into account to explore the impact of catastrophic event. From individual mobility behaviors to macroscopic traffic dynam- ics, agent-based modeling provides an interesting conceptual framework to study this question. -
Building, Composing and Experimenting Complex Spatial Models with the GAMA Platform
Open Archive Toulouse Archive Ouverte OATAO is an open access repository that collects the work of Toulouse researchers and makes it freely available over the web where possible This is an author’s version published in: http://oatao.univ-toulouse.fr/22664 Official URL DOI : https://doi.org/10.1007/s10707-018-00339-6 To cite this version: Taillandier, Patrick and Gaudou, Benoit and Grignard, Arnaud and Huynh, Quang-Nghi and Marilleau, Nicolas and Caillou, Philippe and Philippon, Damien and Drogoul, Alexis Building, composing and experimenting complex spatial models with the GAMA platform. (2018) GeoInformatica. 1-24. ISSN 1384-6175 Any correspondence concerning this service should be sent to the repository administrator: [email protected] https://doi.org/10.1007/s10707-018-00339-6 Building, composing and experimenting complex spatial models with the GAMA platform Patrick Taillandier Benoit Gaudou, Arnaud Grignard, Quang-Nghi Huynh Nicolas Marilleau, Philippe Caillou, Damien Philippon, Alexis Drogoul Abstract The agent-based modeling approach is now used in many domains such as geography, ecology, or economy, and more generally to study (spatially explicit) socio-environmental systems where the heterogeneity of the actors and the numerous feedback loops between them requires a modular and incremental approach to modeling. One major reason of this success, besides this conceptual facility, can be found in the support provided by the development of increasingly powerful software platforms, which now allow modelers without a strong background in computer science to easily and quickly develop their own models. Another trend observed in the latest years is the development of much more descriptive and detailed models able not only to better represent complex systems, but also answer more intricate questions. -
Semi-Automatic Program Partitioning
Instituto Tecnológico y de Estudios Superiores de Monterrey Campus Monterrey School of Engineering and Sciences Semi-Automatic Program Partitioning A dissertation presented by Priscila Angulo López Submitted to the School of Engineering and Sciences in partial fulfillment of the requirements for the degree of Doctor of Philosophy In Information Technologies and Communications Major in Computer Science Monterrey, Nuevo León, December 5th, 2017 Declaration of Authorship I, Priscila Angulo López, declare that this dissertation titled, Semi-Automatic Program Partitioning and the work presented in it are my own. I confirm that: • This work was done wholly or mainly while in candidature for a research degree at this University. • Where any part of this dissertation has previously been submitted for a degree or any other qualification at this University or any other institution, this has been clearly stated. • Where I have consulted the published work of others, this is always clearly attributed. • Where I have quoted from the work of others, the source is always given. With the exception of such quotations, this dissertation is entirely my own work. • I have acknowledged all main sources of help. • Where the dissertation is based on work done by myself jointly with others, I have made clear exactly what was done by others and what I have contributed myself. Priscila Angulo López Monterrey, Nuevo León, December 5th, 2017 ©2017 by Priscila Angulo López All rights reserved Dedication A mi amada madre. Acknowledgements This was a long endeavor, accompanied by added trials, as life usually goes. However, the best part is that it allowed me to be the recipient of exceptional encouragement, support and love from a large number of generous and kind persons. -
Experimenting the Impact of Pedestrianisation on Urban Pollution Using Tangible Agent-Based Simulations: Application to Hoan
Experimenting the Impact of Pedestrianisation on Urban Pollution Using Tangible Agent-Based Simulations: Application to Hoan Kiem District, Hanoi, Vietnam Arthur Brugière, Minh Pham, Kevin Chapuis, Alexis Drogoul, Benoit Gaudou, Arnaud Grignard, Nicolas Marilleau, Nguyen-Huu Tri To cite this version: Arthur Brugière, Minh Pham, Kevin Chapuis, Alexis Drogoul, Benoit Gaudou, et al.. Experimenting the Impact of Pedestrianisation on Urban Pollution Using Tangible Agent-Based Simulations: Applica- tion to Hoan Kiem District, Hanoi, Vietnam. Mohd Hafiz Mohd; Md Yushalify Misro; Syakila Ahmad; Doanh Nguyen Ngoc. Modelling, Simulation and Applications of Complex Systems : CoSMoS 2019, Penang, Malaysia, April 8-11, 2019, 359, Springer, Singapore, pp.43-77, 2021, Springer Proceedings in Mathematics & Statistics book series (PROMS), 978-981-16-2628-9. 10.1007/978-981-16-2629-6_4. hal-03258915 HAL Id: hal-03258915 https://hal.archives-ouvertes.fr/hal-03258915 Submitted on 12 Jun 2021 HAL is a multi-disciplinary open access L’archive ouverte pluridisciplinaire HAL, est archive for the deposit and dissemination of sci- destinée au dépôt et à la diffusion de documents entific research documents, whether they are pub- scientifiques de niveau recherche, publiés ou non, lished or not. The documents may come from émanant des établissements d’enseignement et de teaching and research institutions in France or recherche français ou étrangers, des laboratoires abroad, or from public or private research centers. publics ou privés. Experimenting the impact of -
Participatory Modeling and Simulation with the GAMA Platform
OATAO is an open access repository that collects the work of Toulouse researchers and makes it freely available over the web where possible This is an author’s version published in: http://oatao.univ-toulouse.fr/24827 Official URL: https://doi:10.18564/jasss.3964 To cite this version: Taillandier, Patrick and Grignard, Arnaud and Marilleau, Nicolas and Philippon, Damien and Huynh, Quang-Nghi and Gaudou, Benoit and Drogoul, Alexis Participatory Modeling and Simulation with the GAMA Platform. (2019) Journal of Artificial Societies and Social Simulation, 22 (2). ISSN 1460-7425 Any correspondence concerning this service should be sent to the repository administrator: [email protected] Participatory Modeling and Simulation with the GAMA platform Patrick Taillandier!, Arnaud Grignard", Nicolas Marilleau#, Damien Philippon#, Quang-Nghi Huynh$, Benoit Gaudou%, Alexis Drogoul#,& !MIAT, University of Toulouse, INRA, Auzeville, BP !"#"$ %&%"# Cedex Castanet Tolosan, %&'(" France "Media Lab, Massachussets Istitute of Technology, Cambridge, USA #UMI UMMISCO, IRD/UPMC, %" rue Henri Varagnat, )%&(% Bondy Cedex, France &ICTLab, USTH, VAST, Hanoi, Vietnam $DREAM-CICT/IRD, Can Tho University, Cantho, Vietnam %IRIT, University of Toulouse, CNRS, INPT, UPS, UT&, UT"J, " rue du Doyen-Gabriel-Marty, %&'(" Toulouse, France Correspondence should be addressed to [email protected] Abstract: In recent years, agent-based simulation has become an important tool to study complex systems. However, the models produced are rarely used for decision-making support because stakeholders are o0en not involved in the modeling and simulation processes. Indeed, while several tools dedicated to participatory modeling and simulation exist, these are limited to the design of simple KISS models, thus reducing their po- tential impact. -
THESIS Dynamic Multilevel Modeling in the Design of Decision Support
UNIVERSITEPIERREETMARIECURIE´ L’ ECOLE DOCTORALE INFORMATIQUE TELECOMMUNICATIONS ET ELECTRONIQUE THESIS to obtain the degree of DOCTORATE FROM L’UNIVERSITEPIERREET´ MARIE CURIE Presented by NGUYEN Thi Ngoc Anh Defended on 14 November 2014 Dynamic Multilevel Modeling in the design of Decision Support Systems for rescue simulation : combining Agent-based and Mathematical approaches Jury M. Jean Daniel ZUCKER Directeur de Recherche IRD, HDR Supervisor M. NGUYEN Huu Du Professor National University, Vietnam Co-supervisor M.LudovicLECLERCQ DirecteurdeRecherche,HDR Reviewer M.GuillaumeHUTZLER MaˆıtredeConf´erences,HDR Reviewer M. Alexis DROUGOUL Directeur de Recherche IRD, HDR Examinator M.YannCHEVALEYRE ProfesseurdesUniversit´es Examinator M.VincentCORRUBLE MaˆıtredeConf´erences,HDR Examinator M.NGUYEN Hong Phuong Professor of Vietnam Invited academy of sceience and technology Universit´ePierre et Marie Curie, Paris 6 752700, Paris Cedex 06 T´el. Secr´etariat : 01 44 27 28 10 Bureau d accueil, inscription des doctorants T´el. pour les ´etudiants de A `aEL : 01 44 27 28 07 EscG,2`eme´etage T´el.pourles´etudiantsdeEM`aMON:0144272805 15 rue de l ´ecole de m´edecine T´el. pour les ´etudiants de MOO `aZ : 01 44 27 28 02 E-mail : [email protected] Acknowledgements I would like to thank my supervisors Jean Daniel ZUCKER and Nguyen Huu Du for their advises and great kindness. I would also like to thank my husband Tran Thanh Son, my parents Nguyen Dang Loc and Tran Thi Kim Yen, my children Tran Ngoc Van and Tran Hoang Thang whose support and