Attacking the Sound Barrier 1935-45
Total Page:16
File Type:pdf, Size:1020Kb
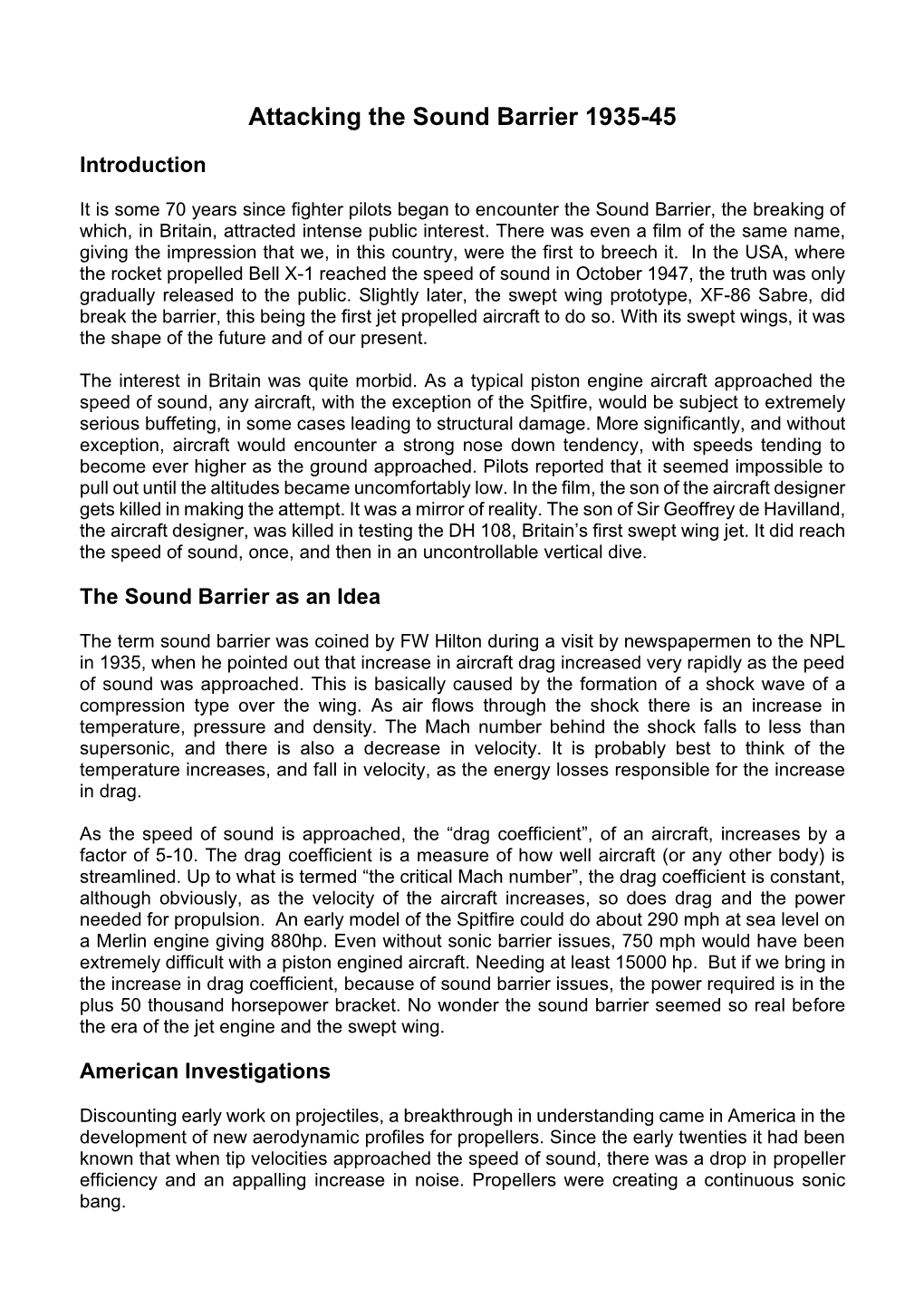
Load more
Recommended publications
-
HISTORICAL PERSPECTIVE a Need for Speed
n HISTORICAL PERSPECTIVE A need for speed Mach 0.8 to 1.2 and above the speed of powerful turbine engine available. To mit- Skystreak taught lots sound, respectively). The U.S. Army Air igate as much risk as possible, the team Forces took responsibility for supersonic kept the design simple, using a conven- about flight near research—which resulted in Chuck Yea- tional straight wing rather than the new ger breaking the sound barrier in the Bell and mostly unproven swept wing. The the sound barrier X-1 on Oct. 14, 1947. That historic event 5,000-lb.-thrust (22-kilonewton) Allison overshadowed the highly successful re- J35-A-11 engine filled the fuselage, leav- BY MICHAEL LOmbARDI search conducted by the pilots who flew ing just enough room to house instrumen- s World War II was coming to a the Douglas D-558-1 Skystreak to the edge tation and a pilot in a cramped cockpit. close, advances in high-speed aero- of the sound barrier while capturing new Because of the lack of knowledge about Adynamics were rapidly progressing world speed records. the survivability of a high-altitude, high- beyond the ability of the wind tunnels of The D-558-1 was developed by the speed bailout, Douglas engineers designed the day, prompting a dramatic expansion Douglas Aircraft Company, today a part a jettisonable nose section that could pro- of flight-test research and experimental of Boeing, at its El Segundo (Calif.) tect the pilot until a safe bailout speed was aircraft. Division. It was designed by a team led reached. -
Airspace: Seeing Sound Grades
National Aeronautics and Space Administration GRADES K-8 Seeing Sound airspace Aeronautics Research Mission Directorate Museum in a BO SerieXs www.nasa.gov MUSEUM IN A BOX Materials: Seeing Sound In the Box Lesson Overview PVC pipe coupling Large balloon In this lesson, students will use a beam of laser light Duct tape to display a waveform against a flat surface. In doing Super Glue so, they will effectively“see” sound and gain a better understanding of how different frequencies create Mirror squares different sounds. Laser pointer Tripod Tuning fork Objectives Tuning fork activator Students will: 1. Observe the vibrations necessary to create sound. Provided by User Scissors GRADES K-8 Time Requirements: 30 minutes airspace 2 Background The Science of Sound Sound is something most of us take for granted and rarely do we consider the physics involved. It can come from many sources – a voice, machinery, musical instruments, computers – but all are transmitted the same way; through vibration. In the most basic sense, when a sound is created it causes the molecule nearest the source to vibrate. As this molecule is touching another molecule it causes that molecule to vibrate too. This continues, from molecule to molecule, passing the energy on as it goes. This is also why at a rock concert, or even being near a car with a large subwoofer, you can feel the bass notes vibrating inside you. The molecules of your body are vibrating, allowing you to physically feel the music. MUSEUM IN A BOX As with any energy transfer, each time a molecule vibrates or causes another molecule to vibrate, a little energy is lost along the way, which is why sound gets quieter with distance (Fig 1.) and why louder sounds, which cause the molecules to vibrate more, travel farther. -
The Mathematical Approach to the Sonic Barrier1
BULLETIN (New Series) OF THE AMERICAN MATHEMATICAL SOCIETY Volume 6, Number 2, March 1982 THE MATHEMATICAL APPROACH TO THE SONIC BARRIER1 BY CATHLEEN SYNGE MORAWETZ 1. Introduction. For my topic today I have chosen a subject connecting mathematics and aeronautical engineering. The histories of these two subjects are close. It might however appear to the layman that, back in the time of the first powered flight in 1903, aeronautical engineering had little to do with mathematics. The Wright brothers, despite the fact that they had no university education were well read and learned their art using wind tunnels but it is unlikely that they knew that airfoil theory was connected to the Riemann conformai mapping theorem. But it was also the time of Joukowski and later Prandtl who developed and understood that connection and put mathematics solidly behind the new engineering. Since that time each new generation has discovered new problems that are at the forefront of both fields. One such problem is flight near the speed of sound. This one in fact has puzzled more than one generation. Everyone knows that in popular parlance an aircraft has "crashed the sonic *or sound barrier" if it flies faster than sound travels; that is, if the speed of the craft q exceeds the speed of sound c or the Mach number, M = q/c > 1. In simple, if perhaps too graphic, terms this means that if you are in the line of flight the plane hits you before you hear it. But it is not my purpose to talk about flight at the speed of sound. -
Aircraft of Today. Aerospace Education I
DOCUMENT RESUME ED 068 287 SE 014 551 AUTHOR Sayler, D. S. TITLE Aircraft of Today. Aerospace EducationI. INSTITUTION Air Univ.,, Maxwell AFB, Ala. JuniorReserve Office Training Corps. SPONS AGENCY Department of Defense, Washington, D.C. PUB DATE 71 NOTE 179p. EDRS PRICE MF-$0.65 HC-$6.58 DESCRIPTORS *Aerospace Education; *Aerospace Technology; Instruction; National Defense; *PhysicalSciences; *Resource Materials; Supplementary Textbooks; *Textbooks ABSTRACT This textbook gives a brief idea aboutthe modern aircraft used in defense and forcommercial purposes. Aerospace technology in its present form has developedalong certain basic principles of aerodynamic forces. Differentparts in an airplane have different functions to balance theaircraft in air, provide a thrust, and control the general mechanisms.Profusely illustrated descriptions provide a picture of whatkinds of aircraft are used for cargo, passenger travel, bombing, and supersonicflights. Propulsion principles and descriptions of differentkinds of engines are quite helpful. At the end of each chapter,new terminology is listed. The book is not available on the market andis to be used only in the Air Force ROTC program. (PS) SC AEROSPACE EDUCATION I U S DEPARTMENT OF HEALTH. EDUCATION & WELFARE OFFICE OF EDUCATION THIS DOCUMENT HAS BEEN REPRO OUCH) EXACTLY AS RECEIVED FROM THE PERSON OR ORGANIZATION ORIG INATING IT POINTS OF VIEW OR OPIN 'IONS STATED 00 NOT NECESSARILY REPRESENT OFFICIAL OFFICE OF EOU CATION POSITION OR POLICY AIR FORCE JUNIOR ROTC MR,UNIVERS17/14AXWELL MR FORCEBASE, ALABAMA Aerospace Education I Aircraft of Today D. S. Sayler Academic Publications Division 3825th Support Group (Academic) AIR FORCE JUNIOR ROTC AIR UNIVERSITY MAXWELL AIR FORCE BASE, ALABAMA 2 1971 Thispublication has been reviewed and approvedby competent personnel of the preparing command in accordance with current directiveson doctrine, policy, essentiality, propriety, and quality. -
7. Transonic Aerodynamics of Airfoils and Wings
W.H. Mason 7. Transonic Aerodynamics of Airfoils and Wings 7.1 Introduction Transonic flow occurs when there is mixed sub- and supersonic local flow in the same flowfield (typically with freestream Mach numbers from M = 0.6 or 0.7 to 1.2). Usually the supersonic region of the flow is terminated by a shock wave, allowing the flow to slow down to subsonic speeds. This complicates both computations and wind tunnel testing. It also means that there is very little analytic theory available for guidance in designing for transonic flow conditions. Importantly, not only is the outer inviscid portion of the flow governed by nonlinear flow equations, but the nonlinear flow features typically require that viscous effects be included immediately in the flowfield analysis for accurate design and analysis work. Note also that hypersonic vehicles with bow shocks necessarily have a region of subsonic flow behind the shock, so there is an element of transonic flow on those vehicles too. In the days of propeller airplanes the transonic flow limitations on the propeller mostly kept airplanes from flying fast enough to encounter transonic flow over the rest of the airplane. Here the propeller was moving much faster than the airplane, and adverse transonic aerodynamic problems appeared on the prop first, limiting the speed and thus transonic flow problems over the rest of the aircraft. However, WWII fighters could reach transonic speeds in a dive, and major problems often arose. One notable example was the Lockheed P-38 Lightning. Transonic effects prevented the airplane from readily recovering from dives, and during one flight test, Lockheed test pilot Ralph Virden had a fatal accident. -
Ping Pong Balls Break the Sound Barrier STEM Lesson Plan / Adaptable for Grades 7–12 Lesson Plan Developed by T
INSIDE SCIENCE TV: Ping Pong Balls Break The Sound Barrier STEM Lesson Plan / Adaptable for Grades 7–12 Lesson plan developed by T. Jensen for Inside Science and the American Institute of Physics About the Video (click here to see video) Purdue University students, led by their mechanical engineering technology professor, designed an hourglass-shaped nozzle like those found in the engine of F-16 fighter planes for their air-cannon. The cannon accelerates a ping-pong ball to supersonic speeds, propelling it with incredible momentum through wood, soda cans, and even denting steel. Related Concepts acceleration energy momentum aerodynamics force sound barrier air pressure linear motion speed continuity equation mass vacuum Bell Ringers Use video to explore students’ prior knowledge, preconceptions, and misconceptions. Have students write or use the prompts to promote critical thinking. Time Video content Students might… 0:00–0:05 Series opening 0:06–0:13 What can travel at Have students make written predictions about supersonic speed and what might travel at supersonic speed and can shatter plywood? blast through plywood. Predictions should be supported with physics concepts. (You can play the video at full screen without the label Ping Pong Balls Break The Sound Barrier showing by keeping your cursor out of the screen.) 0:14–0:25 Purdue mechanical Students might put on their engineering hats and engineering and make annotated drawings that depict how they technology students build would propel a ping-pong ball to supersonic an air-powered cannon. speeds. 0:26–0:32 Students determine how Have students outline the procedure they would fast the ping-pong ball is follow to determine how fast the ping-pong ball traveling and makes was going when it hit the metal grid. -
Chapter Iv What Is the Thrust Ssc?
THRUST SSC ENGLISH 2 – CHAPTER IV WHAT IS THE THRUST SSC? British jet-propelled car Developed by Richard Noble and his 3 asisstants Holds the World Land Speed Record 15. October 1997 First vehicle to break sound barrier DETAILS 16,5 metres long, 3,7 metres high, weights nearly 10 tons Two Rolls Royce engines salvaged from a jet fighter Two engines have a combined power of 55,000 pounds of thrust (110,000 horsepower) Two front and two back wheels with no tyres (disks of forged aluminium) Uses parachutes for breaking SAFETY OF THE CAR There is no ejection system in the car or any other kind of safety mechanisms The emphasis was placed on keeping the car on the ground HOW? Hundreds of sensors to ensure the vehicle to maintain safe path Aerodynamic system is there to keep the vehicle on the ground WORLD LAND SPEED RECORD The record set on 15th October 1997 The record holder is ANDY GREEN (British Royal Air Force pilot) WORLD MOTOR SPORT COUNCIL’S STATEMENT ABOUT THE RECORD The World Motor Sport Council homologated the new world land speed records set by the team ThrustSSC of Richard Noble, driver Andy Green, on 15 October 1997 at Black Rock Desert, Nevada (USA). This is the first time in history that a land vehicle has exceeded the speed of sound. The new records are as follows: Flying mile 1227.985 km/h (763.035 mph) Flying kilometre 1223.657 km/h (760.343 mph) In setting the record, the sound barrier was broken in both the north and south runs. -
Sound Barrier Indexedmaster.Indd
9 CONTENTS Page Chapter 15 1 FIRST FLIGHT 29 2 de HAVILLAND 47 3 NO TAIL 63 4 UNDERSTANDING THE SOUND BARRIER 69 5 SWEPT WINGS 85 6 BIRTH OF THE 108 101 7 YOUNG GEOFFREY 117 8 TESTING 133 9 FALLING LEAVES 147 10 NO WARNING 161 11 THE SHOW GOES ON 183 12 RECORD BREAKER 205 13 TRANSDUNAL TROUGH 216 14 SOUND BARRIER 227 15 FAREWELL HATFIELD 245 16 FARNBOROUGH 253 17 TRAGEDY 269 18 AFTERWARDS 291 APPENDICES Appendix I Discussion of aeroelastic properties of the DH108 II Discussion on the DH108 III Stressing assumptions IV Specification E18/45 V Pilot’s reports VI Meeting to discuss third prototype VII Report by John Wimpenny on flight tests VIII Summary by John Derry of flying DH108 VW120 IX Report by Chris Capper on approach and landing in DH108 TG/283 X Flight test chronology 10 11 INTRODUCTION It was an exciting day for schoolboy Robin Brettle, and the highlight of a project he was doing on test flying: he had been granted an interview with John Cunningham. Accompanied by his father, Ray, Robin knocked on the door of Canley, Cunningham’s home at Harpenden in Hertfordshire and, after the usual pleasantries were exchanged, Ray set up the tape recorder and Robin began his interview. He asked the kind of questions a schoolboy might be expected to ask, and his father helped out with a few more specific queries. As the interview drew to a close, Robin plucked up courage to ask a more personal question: ‘Were you ever scared when flying?’ Thinking that Cunningham would recall some life-or-death moments when under fire from enemy aircraft during nightfighting operations, father and son were very surprised at the immediate and direct answer: ‘Yes, every time I flew the DH108.’ Cunningham, always calm, resolute and courageous in his years as chief test pilot of de Havilland, was rarely one to display his emotions, but where this aircraft was concerned he had very strong feelings, and there were times during the 160 or so flights he made in the DH108 that he feared for his life - and on one occasion came close to losing it. -
Section 7, Lecture 3: Effects of Wing Sweep
Section 7, Lecture 3: Effects of Wing Sweep • All modern high-speed aircraft have swept wings: WHY? 1 MAE 5420 - Compressible Fluid Flow • Not in Anderson Supersonic Airfoils (revisited) • Normal Shock wave formed off the front of a blunt leading g=1.1 causes significant drag Detached shock waveg=1.3 Localized normal shock wave Credit: Selkirk College Professional Aviation Program 2 MAE 5420 - Compressible Fluid Flow Supersonic Airfoils (revisited, 2) • To eliminate this leading edge drag caused by detached bow wave Supersonic wings are typically quite sharp atg=1.1 the leading edge • Design feature allows oblique wave to attachg=1.3 to the leading edge eliminating the area of high pressure ahead of the wing. • Double wedge or “diamond” Airfoil section Credit: Selkirk College Professional Aviation Program 3 MAE 5420 - Compressible Fluid Flow Wing Design 101 • Subsonic Wing in Subsonic Flow • Subsonic Wing in Supersonic Flow • Supersonic Wing in Subsonic Flow A conundrum! • Supersonic Wing in Supersonic Flow • Wings that work well sub-sonically generally don’t work well supersonically, and vice-versa à Leading edge Wing-sweep can overcome problem with poor performance of sharp leading edge wing in subsonic flight. 4 MAE 5420 - Compressible Fluid Flow Wing Design 101 (2) • Compromise High-Sweep Delta design generates lift at low speeds • Highly-Swept Delta-Wing design … by increasing the angle-of-attack, works “pretty well” in both flow regimes but also has sufficient sweepback and slenderness to perform very Supersonic Subsonic efficiently at high speeds. • On a traditional aircraft wing a trailing vortex is formed only at the wing tips. -
Naca Research Memorandum
RM No. L8A28c NACA RESEARCH MEMORANDUM EFFECTS OF SWEEP ON CONTROLS By John G. Lowry, John A. Axelson, and Harold I. Johnson Langley Memorial Aeronautical La 00 ratory Langley Field, Va. NATIONAL ADVISORY COMMITTEE FOR AERONAUTICS WASHINGTON June 3, 1948 Declassified February 10, 1956 NACA PM No. L8A28c NATIONAL ADVISORY COMMITTEE FOR AERONAUTICS RESEARCH MEMORANDUM EFFECTS OF SWEEP ON CONTROLS By John G. Lowry., John A. Axelson, and Harold I. Johnson SUMMARY An analysis of principal results of recent control-surface research pertinent to transonic flight has -been made. Available experimental data on control surfaces of both unswept and sweptback configurations at transonic speeds are used to indiäate the control-surface characteristics in the transonic speed range. A design procedure for controls on swept- back wings based on low-speed experimental data is also discussed. The results indicated, that no serious problems resulting from compressibility effects would be encountered as long as the speeds are kept below the critical speed of the wing and the trailing-edge angle is kept small. Above critical speed, however, the behavior of the' controls depended to a large extent on the wing sweep angle. The design procedures presented for controls on swept wings, although of a preliminary nature, appear to offer a method of estimating the effec- tiveness of flap-type controls on swept wings of normal aspect ratio and taper ratio. INTRODUCTION The design of controls for unswept wings that fly at low speed has been discussed in several papers (references 1 to 7). The design procedures set forth in these papers are adequate to allow for the prediction of control characteristics within small limits. -
Conceptual Design for a Supersonic Advanced Military Trainer
Conceptual Design for a Supersonic Advanced Military Trainer A project presented to The Faculty of the Department of Aerospace Engineering San José State University In partial fulfillment of the requirements for the degree Master of Science in Aerospace Engineering by Royd A. Johansen May 2019 approved by Dr. Nikos Mourtos Faculty Advisor © 2019 Royd A. Johansen ALL RIGHTS RESERVED ABSTRACT CONCEPTUAL DESIGN FOR A SUPERSONIC ADVANCED MILITARY TRAINER by Royd A. Johansen The conceptual aircraft design project is based off the T-X program requirements for an advanced military trainer (AMT). The design process focused on a top-level design aspect, that followed the classic aircraft design process developed by J. Roskam’s Airplane Design. The design process covered: configuration selection, weight sizing, performance sizing, fuselage design, wing design, empennage design, landing-gear design, Class I weight and balance, static longitudinal and directional stability, subsonic drag polars, supersonic area rule applied to supersonic drag polars, V-n diagrams, Class II weight and balance, moments and products of inertia, and cost estimation. Throughout the process other materials and references are consulted to verify or develop a better understanding of the concepts in the Airplane Design series. ACKNOWLEDGEMENTS I would like to express my deep gratitude to Dr. Nikos Mourtos for his support throughout this project and his invaluable academic advisement throughout my undergraduate and graduate studies. I would also like to thank Professor Gonzalo Mendoza for introducing Aircraft Design to me as an undergraduate and for providing additional insights throughout my graduate studies. My thanks are also extended to Professor Jeanine Hunter for helping me develop my theoretical foundation in Dynamics, Flight Mechanics, and Aircraft Stability and Control. -
A Publication of the Southern Museum of Flight Birmingham, Al Historic Happenings
A PUBLICATION OF THE SOUTHERN MUSEUM OF FLIGHT BIRMINGHAM, AL WWW.SOUTHERNMUSEUMOFFLIGHT.ORG HISTORIC HAPPENINGS Lindbergh & WW2 Lindbergh comes to Birmingham uring WW2, Lindbergh was a key n 1927, Charles Lindbergh's D figure in improving the performance I solo transatlantic flight of the P-38 aircraft. Working as a further sparked public interest civilian contractor in the South Pacific in aviation. Local civic during 1944, he was instrumental in boosters, federal initiatives extending the range of the P-38 through through the Department of improved throttle settings, or engine- Spirit of St. Louis leaning techniques, notably by reducing Commerce, and the creation of the airmail system, combined over Birmingham on engine speed to 1,600 rpm, setting the October 5, 1927 carburetors for auto-lean and flying at with public interest, produced a 185 mph. This reduced the P-38s fuel boom in building airports. consumption to 70 gal/h. Following his sensational first solo flight from New York to Paris in May of 1927, 25-year old Lindbergh embarked on a three month flying tour of the United States. Flying his famous plane, Spirit of St. Louis, he touched down in all 48 states, visited 92 cities, gave 147 speeches, and rode 1,290 miles in parades. Airmail usage exploded overnight as a result, and the public began to view airplanes as a viable means of travel. Lindbergh had several Alabama “connections.” He bought his first plane, a “Jenny,” from Glenn Messer Ground crews had noticed that and perhaps soloed for the first time in this plane. He Lindbergh returned from missions with barnstormed Alabama in 1924, and his father had a more fuel than the other pilots based on half-brother, Augustus, who had worked for Frisco the engine settings he employed.